This article introduces the paper'Self hardening aluminum alloys for automotive applications' published by Politecnico di Torino.
1. Overview:
- Title: Self hardening aluminum alloys for automotive applications
- Author: Christian Castella
- Publication Year: Not specified in the paper. (Assumed 2014 based on author's publication list)
- Publishing Journal/Academic Society: Politecnico di Torino, Facoltà di Ingegneria, PhD in materials science and technology
- Keywords: Self-hardening aluminum alloys, Automotive applications, Al-Zn-Si-Mg alloys, Knuckle component, Corrosion resistance, Mechanical properties, Heat treatment costs
![Figure 26: Aluminum applications in a car [30].](https://castman.co.kr/wp-content/uploads/image-650-png.webp)
2. Abstracts
This PhD thesis has been carried out in collaboration with Teksid Aluminum, an aluminum foundry situated in Carmagnola near Turin. The research focuses on Self-hardening aluminum alloys (Al-Zn-Si-Mg alloys), an innovative class of light aluminum alloys exhibiting high mechanical properties suitable for various industrial applications, particularly in the transport industry. A key feature is their ability to achieve good performance without heat treatment, undergoing natural ageing at room temperature over 7-10 days. This eliminates heat treatment, reducing production costs, energy consumption, and component deformation risks. The thesis aims to find an alternative to the T6 heat-treated A356 alloy for automotive component production, specifically evaluating the feasibility of self-hardening alloys for a knuckle suspension component. Economical considerations regarding energy saving by avoiding heat treatment are also explored. A significant portion of the thesis investigates the structural features, mechanical properties, and corrosion resistance of self-hardening aluminum alloys, examining the effect of Mg content and cooling rate to define the optimal alloy composition for knuckle suspension component production.
3. Research Background:
Background of the Research Topic:
Aluminum alloys are increasingly utilized in the automotive industry due to their light-weight nature, contributing to reduced vehicle weight and improved fuel efficiency. As stated in the paper, "Aluminum is a light-weight metal and it is one of the most abundant metallic element on earth… The aluminum became a very important economic competitor and the aluminum industry was subjected to an exponential growth [2-3]." This drive for lightweighting is further motivated by the need to "moderate the fuel consumptions of cars and at the same time also the emission of gas, especially CO2".
Status of Existing Research:
Currently, T6 heat-treated A356 alloy is employed for automotive component production, including knuckle components. The paper notes, "The goal of this PhD Thesis was to find an alternative solution to the actually used T6 heat-treated A356 alloy for automotive component production." While heat treatments are commonly used to enhance the mechanical strength of aluminum alloys, they are energy-intensive and can introduce manufacturing complexities. The document mentions that "Generally, heat treatments are widely used in Al foundry to increase the mechanical strength of aluminium alloys. Actually, there is a high tendency to minimize the energy consumption in order to have a minor impact on the environment."
Necessity of the Research:
The research addresses the necessity to reduce energy consumption and production costs in automotive manufacturing while maintaining or improving component performance. Self-hardening aluminum alloys offer a potential solution by eliminating the need for energy-intensive heat treatments. The paper emphasizes that "The possibility to avoid the heat treatment represents an important benefit, contributing to considerably reduce both the production cost of some components and the amount of energy involved in the manufacturing process. Furthermore, without heat treatment the risk of component's deformation during the production is eliminated." This research is crucial for exploring and optimizing self-hardening aluminum alloys as a viable and cost-effective alternative to conventional heat-treated alloys in automotive applications.
4. Research Purpose and Research Questions:
Research Purpose:
The primary research purpose is "to find an alternative solution to the actually used T6 heat-treated A356 alloy for automotive component production." This involves evaluating self-hardening aluminum alloys as a substitute material, specifically for the production of a knuckle suspension component.
Key Research:
The key research areas are:
- "study of the structural features and mechanical properties of the self-hardening aluminum alloys."
- "investigate their corrosion resistance."
- "The effect of the Mg content and of the cooling rate, on the microstructure of three different self-hardening aluminum alloys".
- "aiming to define the optimal alloy composition for knuckle suspension component production."
Research Hypotheses:
While not explicitly stated as formal hypotheses, the research operates under the premise that:
- Self-hardening Al-Zn-Si-Mg alloys can achieve mechanical properties comparable to or sufficient for replacing T6 heat-treated A356 alloy in automotive components.
- The elimination of heat treatment with self-hardening alloys will lead to significant cost and energy savings in manufacturing.
- The microstructure, mechanical properties, and corrosion resistance of self-hardening Al-Zn-Si-Mg alloys can be optimized by adjusting the Mg content and cooling rate during casting.
5. Research Methodology
Research Design:
The research employs a real case study approach, focusing on the "knuckle component" as a representative automotive part. It involves experimental investigation and optimization of "self-hardening" aluminum alloys produced by die-casting.
Data Collection Method:
The following data collection methods were utilized:
- Microstructural Analysis: "Samples for the microstructural analysis have been prepared by standard metallographic technique… then the samples have been investigated, through an optical microscope (OM, MeF4 Reichart-Jung) and a scanning electron microscope (SEM, Leo 1450VP) equipped with energy X-rays dispersive spectroscopy unit (EDS, Oxford microprobe) for the compositional analysis." X-Ray Diffraction was also used, as evidenced by "Figure 56: X-Ray diffractograms for the AlZn10Si8Mg self-hardening alloy."
- Mechanical Properties Testing: Mechanical performance was evaluated through "tensile tests and Brinell hardness tests." Further mechanical characterization included "three point bending test, Charpy test and Vickers hardness test." Fatigue properties were assessed using "fatigue testing machine (TESTRONIC 100K RUMUL)."
- Corrosion Resistance Evaluation: Corrosion resistance was assessed using "salt spray corrosion test, performed according to the ISO 9227 Standard" and "intergranular corrosion test… according to the BS 11846, method B [79]."
Analysis Method:
The analysis involved:
- Quantitative Microstructural Analysis: Measurement of "secondary dendritic arm space (SDAS)" and characterization of silicon particles using "area (A), the roundness (R) and the equivalent diameter (Deq.)."
- Comparison of Mechanical Properties: Obtained mechanical properties were "compared to those of the A356 heat treated alloy, currently used by Teksid, and to those required at the knuckle component."
- Corrosion Behavior Assessment: Visual inspection, SEM analysis, and EDS analysis were used to evaluate corrosion, along with measurements of "corrosion depth" and "weight loss following corrosion" for intergranular corrosion testing.
- Statistical Analysis: Stair case method was used for fatigue limit evaluation.
Research Subjects and Scope:
The research focused on "self-hardening aluminum alloys (Al-Zn-Si-Mg alloys)" with specific compositions: "AlZn10Si8Mg", "AlZn10Si8Mg1", and "AlZn10Si8Mg3". The scope was limited to evaluating these alloys for "automotive application" with a specific focus on the "knuckle component." The effect of "Mg content" (0.3-0.5 wt% up to 3 wt%) and "cooling rate" was investigated.
6. Main Research Results:
Key Research Results:
- Microstructural Evolution: "The main difference revealed between the microstructure in the as cast condition and after seven days of natural ageing regard the secondary dendritic arm space (SDAS) value… After seven days of natural ageing the microstructure appears finer than in the as cast condition." Increased cooling rates resulted in finer microstructures and lower SDAS values. "As Mg content increases, the development of a more accentuated dendritic morphology can be observed."
- Mechanical Properties: "the AlZn10Si8Mg self-hardening alloy mechanical properties are comparable to those of the A356 (AlSi7Mg0.3) aluminum alloy, subjected to a T6 heat treatment." However, "The elongation to fracture A%, of the AlZn10Si8Mg alloy, shows a value which is a little bit different and it is not acceptable for such component." AlZn10Si8Mg1 exhibited the highest flexural stress. Increased Mg content beyond 1wt% (AlZn10Si8Mg3) led to a decrease in flexural stress and impact energy.
- Corrosion Resistance: "These results demonstrate that, even if the studied alloy seems to be a promising candidate, from mechanical point of view, to substitute A356 alloy, do not has an adequate corrosion resistance" for AlZn10Si8Mg. However, "While the AlZn10Si8Mg1 and AlZn10Si8Mg3 alloys seem to be more resistant to the corrosion environment." AlZn10Si8Mg3 showed the best intergranular corrosion resistance, presenting "the lowest values of both the weight loss and of the penetration depth."
- Fatigue Properties: "It can be observed that the AlZn10Si8Mg1 self hardening aluminum alloy has a fatigue limit of about 92 MPa. This fatigue limit value is comparable with that of A356 (AlSi7Mg0.3) alloy subjected to a T6 heat treatment and casting by permanent mold technique [3]."
Analysis of presented data:
The data presented in the paper, including microstructural images, mechanical property graphs, and corrosion test results, consistently indicates a trade-off between mechanical properties and corrosion resistance with varying Mg content and cooling rates in self-hardening Al-Zn-Si-Mg alloys. Higher cooling rates generally refine the microstructure and improve mechanical properties. Increasing Mg content initially enhances strength but can become detrimental at higher levels (3wt%), negatively impacting ductility and impact resistance while improving corrosion resistance. Shrinkage porosities were identified as a recurring defect affecting mechanical performance, particularly fatigue life.
Figure Name List:
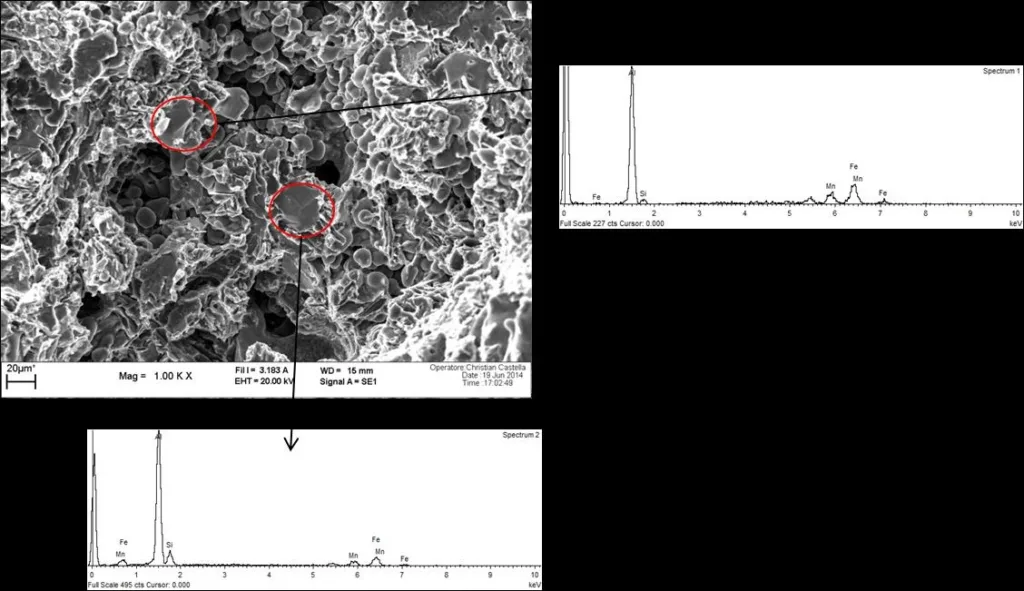
![Figure 25: Components realized with aluminum in a modern car [31].](https://castman.co.kr/wp-content/uploads/image_28-1.webp)
![Figure 27: Relative mass saving, absolute mass saving and market penetration
obtainable with aluminum alloys [32].](https://castman.co.kr/wp-content/uploads/image_30-1024x441.webp)
![Figure 28: Final result of the SLC project based on the "multi-material design" concept
[32].](https://castman.co.kr/wp-content/uploads/image_31-1024x459.webp)
![Figure 44: Car's door panel produced with UNIFONT-90 self-hardening aluminum
alloy [70].](https://castman.co.kr/wp-content/uploads/image_53.webp)
![Figure 49: Knuckle component [71].](https://castman.co.kr/wp-content/uploads/image_58-1024x492.webp)
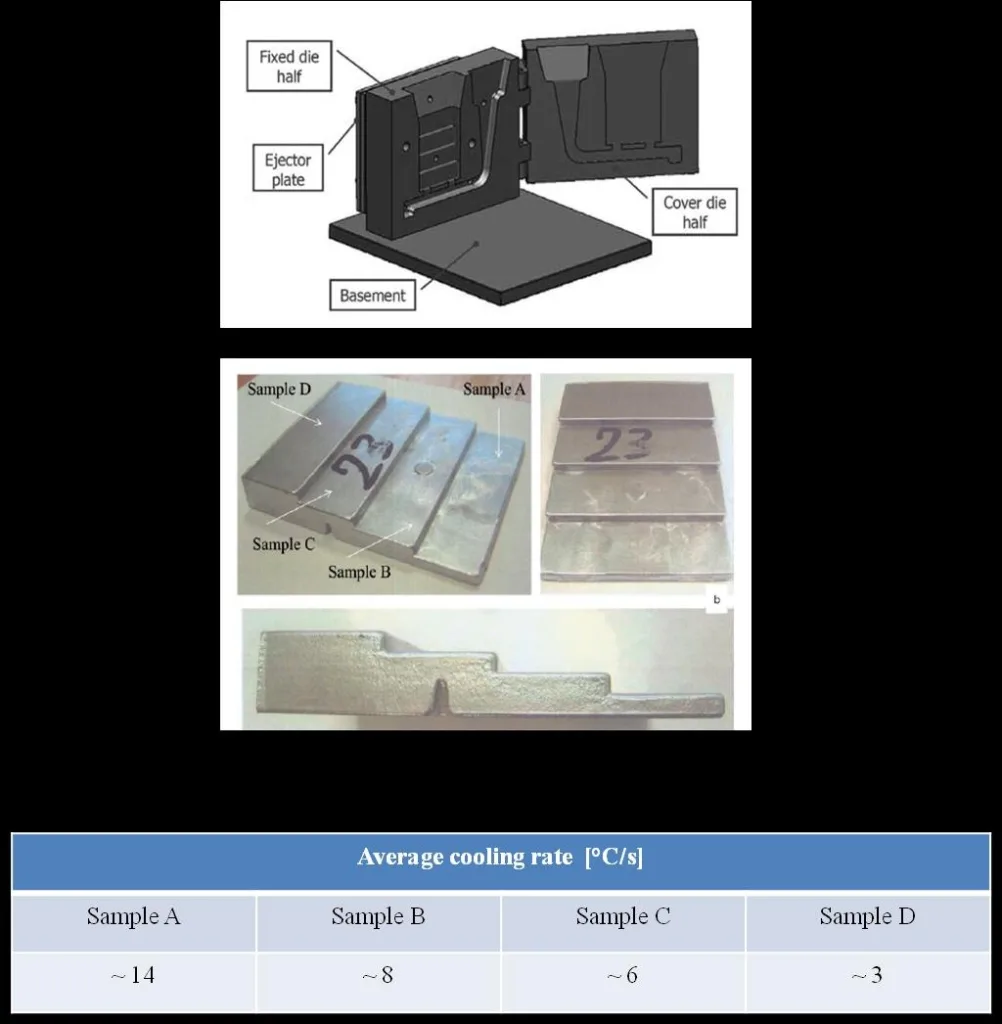
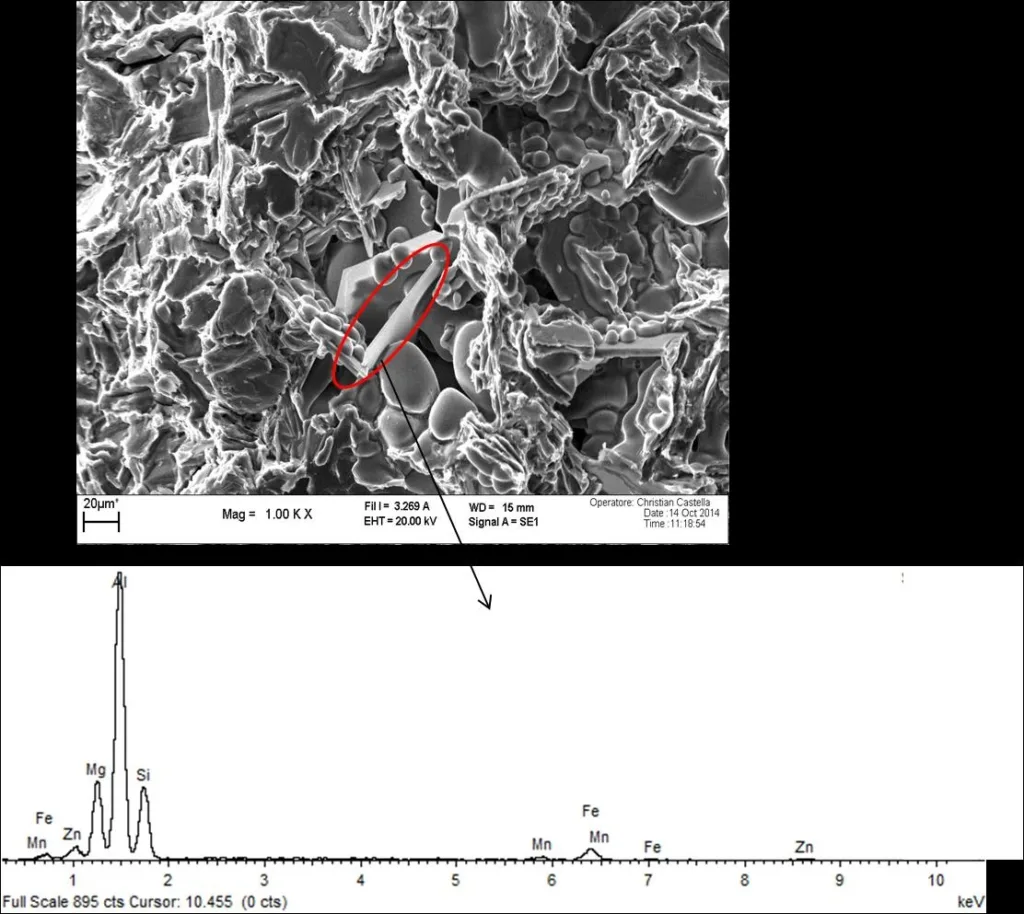
- Figure 1: Microstructures showing: a) the α-Al15(Fe,Mn)3Si2 phase with Chinese script morphology and b) the β-Al5FeSi platelets [7].
- Figure 2: Representation of the mechanisms associated with solution, quench and aging in the case of Al-Cu alloys [12].
- Figure 3: Temperature versus time diagram for: a) conventional and b) uphill quenching processes [15].
- Figure 4: Dislocation bypass precipitates by : a) Friedel effect or b) Orowan mechanism. c) strength versus particle radius diagram [10].
- Figure 5: Strength and hardness as a function of the logarithm of aging time [16].
- Figure 6: Precipitation sequence for Al-Si-Cu alloys [16].
- Figure 7: Hardness-Tensile strength-time curves at different ageing temperatures [16].
- Figure 8: Classification of foundry defects according Cocks [17].
- Figure 9: Classification of foundry defects according Campbell [18].
- Figure 10: Diagram of Sievert's law.
- Figure 11: Gas porosity (courtesy of Teksid Aluminum).
- Figure 12: Shrinkage porosity (courtesy of Teksid Aluminum).
- Figure 13: Shrinkage porosity that act as nucleation site for a fatigue crack (courtesy of Teksid Aluminum).
- Figure 14: Oxide particle (source Teksid Aluminum).
- Figure 15: Creation mechanism of bifilm [26].
- Figure 16: Some bifilm individuated in a A354 aluminum alloy (courtesy of Teksid Aluminum).
- Figure 17: Some bifilm individuated in a A354 aluminum alloy (courtesy of Teksid Aluminum).
- Figure 18: Cold shut revealed in some aluminum components [19].
- Figure 19: Crack individuated in the fractured surface of an aluminum sample (courtesy of Teksid Aluminum).
- Figure 20: Optical microstructure showing β-Al5FeSi, α-Al15(FeMn)3Si2 [28].
- Figure 21: α-Al15(FeMn)3Si2 iron intermetallic compound on the fractured surface of an aluminum sample (courtesy of Teksid Aluminum).
- Figure 22: α-Al15(FeMn)3Si2 iron intermetallic compounds on the fractured surface of an aluminum sample, detected close to a shrinkage porosity (courtesy of Teksid Aluminum).
- Figure 23: Trend of aluminum content in cars in the last 40 years [30].
- Figure 24: Resistance forces to car move [30].
- Figure 25: Components realized with aluminum in a modern car [31].
- Figure 26: Aluminum applications in a car [30].
- Figure 27: Relative mass saving, absolute mass saving and market penetration obtainable with aluminum alloys [32].
- Figure 28: Final result of the SLC project based on the "multi-material design" concept [32].
- Figure 29: Structure of the protective oxide layer forms on aluminum surface [36].
- Figure 30: Pourbaix diagram of Al-H2O system at 25°C [37].
- Figure 31: Polarization curve of pure Al and AA2024-T3 exposed to 0.1M NaCl for 7 days collected at 1mV/s-1 [37].
- Figure 32: Effect of some alloying elements on electrolytic solution potential of aluminum. Potentials are for high-purity binary alloys solution heat treated and quenched. The data are obtained using a solution of 53 g/l NaCl plus 3 g/l H2O2 maintained at 25°C [2].
- Figure 33: Hemispherical pits on aluminum 99.999% in 1.0M NaNO3 solution at E¼1.84 VSHE [39].
- Figure 34: Scheme showing the alloy-solution interphase and the presence of SiO2 particles within the AlOOH/Al2O3 layer [40].
- Figure 35: Scheme of the grain boundary area in a 2xxx aluminum alloy [38].
- Figure 36: Scheme of the grain boundary area in a 7055 aluminum alloy [47].
- Figure 37: Optical micrographs of the surfaces of 7075-T6 aluminum alloy specimens exposed to a deaerated 0.5M NaCl solution at −685mVSCE: (a) as-received specimen and (b), (c) and (d) specimens with grain sizes of 40, 130 and 290 µm, respectively [48].
- Figure 38: Scheme of some theories developed up to now to explain the SCC: a) anodic dissolution; b) hydrogen-induced cracking and c) break of passive film [2].
- Figure 39: Microstructures of 5356-H12 alloy after treatment to produce varying degrees of susceptibility to SCC. a) Cold rolled 20%; highly resistant. b) Cold rolled 20%, then heated 1 year at 100°C; highly susceptible. c) Cold rolled 20%, then heated 1 teat at 150°C; slightly susceptible. d) Cold rolled 20%, then heated 1 teat at 205°C; highly resistant [2].
- Figure 40: Crack propagation rate (v) versus crack tip stress intensity factor (KI) in 3.5 wt% NaCl solution of Al–Zn–Mg–Cu–Zr and Al–Zn–Mg–Cu–Zr–Er–Cr alloys [45].
- Figure 41: Effect of pH on corrosion of 1100-H14 alloy by various chemical solutions [2].
- Figure 42: Effect of temperature on the corrosion of 1100 aluminum alloy in sulfuric acid [2].
- Figure 43: SEM image of a anodizing coating on a piece of extruded AA6060 aluminum alloy [38].
- Figure 44: Car's door panel produced with UNIFONT-90 self-hardening aluminum alloy [70].
- Figure 45: Chassis for robot realized with UNIFONT-90 self-hardening aluminum alloy [70].
- Figure 46: Supports for vibrations dumper fabricated with UNIFONT-94 self hardening aluminum alloy [70].
- Figure 47: Supports for the table of plane's seats produced with UNIFONT-94 self hardening aluminum alloy [70].
- Figure 48: Knuckle component produced by Teksid (courtesy of Teksid Aluminum).
- Figure 49: Knuckle component [71].
- Figure 50: Elements of cost of the heat treatment used for the knuckle component of figure 48 and annual production cost of the heat treatment, used for 400˙000 knuckle components.
- Figure 51: Microstructure of the AlZn10Si8Mg self-hardening aluminum alloy: a) in the as cast condition (100X); b) after seven days of natural ageing (100X); c) in the as cast condition (500X); d) after seven days of natural ageing (500X).
- Figure 52: Aluminum-zinc phase diagram [72].
- Figure 53: SEM micrographs and EDS analysis results of the AlZn10Si8Mg self hardening aluminum alloy in the as cast condition.
- Figure 54: SEM micrographs and EDS analysis results of the AlZn10Si8Mg self hardening aluminum alloy after seven days of natural ageing.
- Figure 55: Partial phase diagrams of Al-Si-Fe system with different amount of Mn: a) 0 wt%; b) 0.1 wt%; c) 0.2 wt% and d) 0.3 wt% [73].
- Figure 56: X-Ray diffractograms for the AlZn10Si8Mg self-hardening alloy.
- Figure 57: Tensile test results: a) ultimate tensile strength; b) yield strength; c) elongation to fracture (A%).
- Figure 58: Brinnel hardness test results.
- Figure 59: Position of the samples inside the batch during salt spray corrosion test.
- Figure 60: Photograph of the samples investigated following the salt spray corrosion test.
- Figure 61: Photograph of the samples subjected to the salt spray corrosion test and the composition of the altered layer, obtained by EDS analysis.
- Figure 62: Step casting geometry: a) general view; b) used geometry for the analysis with side views; c) average cooling rate measured by thermocouples.
- Figure 63: OM micrographs and SDAS values [µm] of the AlZn10Si8Mg self hardening aluminum alloy, as a function of the cooling rate.
- Figure 64: OM micrographs and SDAS values [µm] of the AlZn10Si8Mg1 self hardening aluminum alloy, as a function of the cooling rate.
- Figure 65: OM micrographs and SDAS values [µm] of the AlZn10Si8Mg3 self hardening aluminum alloy, as a function of the cooling rate.
- Figure 66: OM micrographs comparing the microstructure of zone C for all considered alloys.
- Figure 67: OM micrographs of AlZn10Si8Mg self-hardening alloy at different cooling rate: a) Sample D (3 °C/s), b) Sample C (6°C/s), c) Sample B (8°C/s) and d) Sample A (14°C/s) (500x).
- Figure 68: OM micrographs of AlZn10Si8Mg1 self-hardening alloy at different cooling rate: a) Sample D (3 °C/s), b) Sample C (6°C/s), c) Sample B (8°C/s) and d) Sample A (14°C/s) (500x).
- Figure 69: OM micrographs of AlZn10Si8Mg3 self-hardening alloy at different cooling rate: a) Sample D (3 °C/s), b) Sample C (6°C/s), c) Sample B (8°C/s) and d) Sample A (14°C/s) (500x).
- Figure 70: Inverse area of silicon particles for different Mg wt% and cooling rate.
- Figure 71: Roundness of eutectic silicon particles for different Mg wt% and cooling rate.
- Figure 72: Equivalent diameter of silicon particles for different Mg wt% and cooling rate.
- Figure 73: SDAS valued of the alloys.
- Figure 74: a) OM micrographs showing the microstructure of samples of AlZn10Si8Mg, AlZn10Si8Mg1 and AlZn10Si8Mg3 alloys, extracted from zone B and zone D and b) EDS analysis results.
- Figure 75: X-Ray spectra of the studied alloys.
- Figure 76: Dimensions of : a) Mg2Si and b) MgZn2 hardening precipitates, calculated according to the Scherrer formula.
- Figure 77: Flexural stress at break for the alloys investigated: a) after 7 days of natural ageing and b) after10 months of natural ageing.
- Figure 78: Flexural strain at break for the alloys investigated : a) after 7 days of natural ageing and b) after 10 months of natural ageing.
- Figure 79: Charpy test results: a) after 7 days of natural ageing and b) after 10 months of natural ageing.
- Figure 80: Vickers Hardness values obtained: a) after 7 days of natural ageing and b) after 10 months of natural ageing.
- Figure 81: SEM micrographs of the fractured surface.
- Figure 82: SEM images showing some details of the fractured surface: a) shrinkage porosity and b) oxide particle.
- Figure 83: Samples investigated following the salt spray corrosion test.
- Figure 84: Chemical composition of the altered layer individuated on the external surface of AlZn10Si8Mg samples, obtained by EDS analysis.
- Figure 85: Charpy Impact test results: a) before the salt spray corrosion test and b) after the salt spray corrosion test.
- Figure 86:Optical microstructure a), b) and SEM microstructure with EDS analysis results c) of the transverse cross sections of the corroded samples, showing Si particles that act as local cathodes with respect to the eutectic Al matrix.
- Figure 87: SEM microstructure and EDS analysis results of the transverse cross sections of the corroded samples, showing Fe-intermetallic which act as local cathodes with respect to the eutectic Al matrix.
- Figure 88: SEM image a) and FESEM image b) of Al–Fe–Si–Mg compounds.
- Figure 89: a) Weight loss and b) penetration depth, measured after the intergranular corrosion test.
- Figure 90: EDS results of the analysis conducted on the external surface of samples subjected to the intregranular corrosion test.
- Figure 91: Three point bending tests, flexural stress at break results: a) before the intergranular corrosion test and b) after the intergranular corrosion test.
- Figure 92: Three point bending tests, flexural strain at break results: a) before the intergranular corrosion test and b) after the intergranular corrosion test.
- Figure 93: Charpy test results: a) before the integranular corrosion test and b) after the intergranular corrosion test.
- Figure 94: Fatigue test results: a) S-N curve and b) survival probabilities obtained by the stair case method.
- Figure 95: SEM micrographs showing shrinkage porosities that acted as crack initiation site.
- Figure 96: SEM micrograph that shows Fe-Mn intermetallics, which are one of the causes of shrinkage porosity development and EDS analysis results.
7. Conclusion:
Summary of Key Findings:
This PhD thesis concluded that self-hardening Al-Zn-Si-Mg alloys present a viable alternative to T6 heat-treated A356 alloy for automotive component production, particularly for components like knuckle suspensions. "The obtained mechanical properties are perfectly comparable to those of the T6 heat treated A356 (AlSi7Mg0.3) aluminum alloy and they satisfy the properties requirements for the knuckle component." Specifically, AlZn10Si8Mg1 alloy, cast with a cooling rate of approximately 14°C/s, demonstrated a promising balance of mechanical properties, corrosion resistance, and fatigue limit, which is "comparable with that of A356 (AlSi7Mg0.3) alloy subjected to a T6 heat treatment and casting by permanent mold technique [3]." Increased Mg content up to 3wt% (AlZn10Si8Mg3) further improved intergranular corrosion resistance, making it the most corrosion-resistant alloy studied. However, higher Mg content can negatively impact ductility and impact energy. A significant advantage of these alloys is the elimination of heat treatment, leading to potential cost and energy savings.
Academic Significance of the Study:
This study contributes to the academic understanding of self-hardening aluminum alloys, providing detailed insights into the influence of Mg content and cooling rate on their microstructure, mechanical behavior, and corrosion characteristics. The research elucidates the precipitation mechanisms in these alloys and their correlation with observed properties. The findings are valuable for alloy design and optimization strategies for self-hardening aluminum alloys in general.
Practical Implications:
The practical implications of this research are significant for the automotive industry. The study demonstrates the feasibility of using self-hardening Al-Zn-Si-Mg alloys, especially AlZn10Si8Mg1, as a direct substitute for heat-treated A356 alloy in automotive components like knuckle suspensions. This substitution offers the potential for substantial "cost saving realized without the realization of a heat treatment plant [€] 2˙170˙000" and reduced energy consumption by eliminating the heat treatment process. The comparable fatigue limit further supports the practical applicability of these alloys.
Limitations of the Study and Areas for Future Research:
A primary limitation identified is the "elongation to fracture (A%)" of the AlZn10Si8Mg alloy, which "does not satisfy the requirement for the knuckle suspension component." Further research is recommended to address this limitation and improve the ductility of these alloys. The paper also suggests future research directions, including:
- "to increase the value of the elongation to fracture, in order to reach the standard required by the automotive industry for these alloys."
- "Moreover, the fatigue resistance of the most promising alloy will be evaluated at high temperature."
- Further optimization of alloy composition and processing parameters to enhance the overall performance of self-hardening aluminum alloys for automotive applications.
8. References:
- [1] Atlante metallografico delle leghe di alluminio da fonderia, Ettore di Russo, Edimet.
- [2] Corrosion of aluminum and aluminum alloys, edited by J.R.Davis, The materials information society.
- [3] ASM handbook, volume 2 edited by Joseph R. Davis.
- [4]E.A. Starke Jr.; Aluminum alloys: Alloy, Heat Treatment, and Temper Designation; Encyclopedia of Materials: Science and Technology (Second Edition), 2001, Pages 106-107.
- [5] H.A. Elhadari, H.A. Patel, D.L. Chena,W. Kasprzak; Tensile and fatigue properties of a cast aluminum alloy with Ti, Zr and V additions; Materials Science and Engineering A 528 (2011) 8128–8138.
- [6] R. S. Rana, Rajesh Purohit, and S Das; Reviews on the Influences of Alloying elements on the Microstructure and Mechanical Properties of Aluminum; International Journal of Scientific and Research Publications, Volume 2, Issue 6, June 2012 .
- [7] G.Timelli, E.Fiorese, Metodi di neutralizzazione del Fe in leghe Al-Si da fonderia, La Metallurgia Italiana n.3 Marzo (2011) 9-23.
- [8] GUO Hong-min, YANG Xiang-jie; Preparation of semi-solid slurry containing fine and globular particles for wrought aluminum alloy 2024; Trans. Nonferrous Met. SOC. China 17(2007) 799-804.
- [9] D.G. Eskin, Suyitno, L. Katgerman; Mechanical properties in the semi-solid state and hot tearing of aluminium alloys; Progress in Materials Science 49 (2004) 629–711.
- [10] Emma Sjölander, Salem Seifeddine; The heat treatment of Al–Si–Cu–Mg casting alloys; Journal of Materials Processing Technology 210 (2010) 1249–1259.
- [11] M.F. Ibrahim, A.M. Samuel, F.H. Samuel, A preliminary study on optimizing the heat treatment of high strength Al-Cu-Mg-Zn alloys, Materials and Design 57 (2014) 342–350.
- [12] Higgins R.A., Engineering metallurgy, Second Edition, ELBS, ISBN 034018468X, (1986).
- [13] J.S. Robinson, D.A. Tanner, C.E. Truman, A.M. Paradowska, R.C.Wimpory; The influence of quench sensitivity on residual stresses in the aluminium alloys 7010 and 7075; Materials Characterization 65 (2012) 73 – 8 5.
- [14] Jasim M. Salman, Shaymaa Abbas Abd Alsada and Khadim F. Al-Sultani; Improvement Properties of 7075-T6 Aluminum Alloy by Quenching in 30% Polyethylene Glycol and Addition 0.1%B; Research Journal of Material Sciences Vol. 1(6), 12-17, July (2013).
- [15] Diana A. Lados, Diran Apelian, Libo Wang; Minimization of residual stress in heat-treated Al–Si–Mg cast alloys using uphill quenching: Mechanisms and effects on static and dynamic properties; Materials Science and Engineering A 527 (2010) 3159–3165.
- [16] William D. Callister, Jr.; Fundamentals of Materials Science and Engineering; Fifth edition.
- [17] D.L. Cocks, A proposed simple qualitative classification for die-casting defects, Proc. Die-Casting Conference, Montreaux (1996), p. 19/1.
- [18] J. Campbell, R.A. Harding, Casting Technology, in TALAT 2.0 cd-rom, EEA, Brussels (2000).
- [19] Manuale della difettologia nei getti pressocolati, E.Gariboldi – F.Bonollo – P.Parona, Associazione Italiana di Metallurgia.
- [20] S.B. Ghanti, E.A.Druschitz, A.P. Druschitz, J.A.Griffin; The effects of soilidification underpressure on the porosity and mechanical properties of A206-T6 cast aluminum alloy; Paper 11-048 page 1-8 AFS proceedings 2011 America Foundry Society Schaumburg, IL USA.
- [21] H.R. Ammar, A.M. Samuel, F.H. Samuel; Porosity and the fatigue behavior of hypoeutectic and hypereutectic aluminum–silicon casting alloys; International Journal of Fatigue 30 (2008) 1024–1035.
- [22] Bita Ghaffari, George Mozurkewich, Larry A. Godlewski, JacobW. Zindel; Ultrasonic characterization of shrinkage microporosity in aluminum castings; Ultrasonics 41 (2004) 699–707.
- [23] C. Tian, J. Law, J. van der Touw, M. Murray, J.-Y. Yao, D. Graham, D. St. John; Effect of melt cleanliness on the formation of porosity defects in automotive aluminium high pressure die castings; Journal of Materials Processing Technology 122 (2002) 82–93.
- [24] O. Majidi, S.G. Shabestari, M.R. Aboutalebi; Study of fluxing temperature in molten aluminum refining process; Journal of Materials Processing Technology 182 (2007) 450–455.
- [25] Yun Wang, Hu-Tian Li, Zhongyun Fan; Oxidation of Aluminium Alloy Melts and Inoculation by Oxide Particles; Trans Indian Inst Met DOI 10.1007/s12666-012-0194-x.
- [26] J.Campbell, Castings, Butterworth, Oxford, 1991.
- [27] D.Dispinar, J.Campbell, International Journal of cast metal research 17,2004, 280-286.
- [28] Salem Seifeddine, Torsten Sjögren and Ingvar L Svensson; Variations in microstructure and mechanical properties of cast aluminum EN AC 43100 alloy; Metallurgical Science and Technology 12-22.
- [29] J. Hirsch, T. Al-Samman; Superior light metals by texture engineering: Optimized aluminum and magnesium alloys for automotive applications; Acta Materialia 61 (2013) 818–843.
- [30] European Aluminium Association.
- [31] Ju¨rgen Hirsch; Aluminium in Innovative Light-Weight Car Design; Materials Transactions, Vol. 52, No. 5 (2011) pp. 818 to 824.
- [32] Jürgen HIRSCH; Recent development in aluminium for automotive applications; Trans. Nonferrous Met. Soc. China 24(2014) 1995−2002.
- [33]J.Hirsch; Aluminium in innovative light-weight car design; Proc Innovative Development for Lightweight Vehicle Structures; Wolfsburg, Germany: VW, 2009: 101.
- [34] SLC Super Light Car Project [EB/OL]. http://www.superlightcar.com.
- [35] K. Shimizu, R.C. Furneaux, G.E. Thompson, G.C. Wood, A. Gotoh and K. Kobayashi; On the nature of “easy paths” for the diffusion of oxygen in thermal oxide films on aluminium; Oxidation of Metals vol.35, Nos.5/6 pp.427-439, 1991.
- [36] J.R. Davis; Corrosion of aluminum and aluminum alloys; Edited by J.R.Davis ASM International.
- [37] N. L. Sukiman, X. Zhou, N. Birbilis, A.E. Hughes, J. M. C. Mol, S. J. Garcia, X. Zhou and G. E. Thompson; Aluminium Alloys - New Trends in Fabrication and Applications; Edited by Zaki Ahmad, Intech.
- [38] G. M. Scamans, N. Birbilis, R. G. Buchheit; Corrosion of Aluminum and its Alloys; 2010 Elsevier B.V..
- [39] M.G. Alvarez, J.R. Galvele; Pitting Corrosion; Shreir's Corrosion Volume 2, 2010, Pages 772-800.
- [40] M.A. Pech-Canul, M.I. Pech-Canul, P. Bartolo-Pérez, M. Echeverría; The role of silicon alloying addition on the pitting corrosion resistanceof an Al-12 wt.%Si alloy; Electrochimica Acta 140 (2014) 258–265.
- [41] S. Jain; Corrosion and protection of heterogeneous cast Al–Si (356) and Al–Si–Cu–Fe (380) alloys by chromate and cerium inhibitors; The Ohio State University, Ohio, USA, 2006.
- [42] K. Nisancioglu; Electrochemical behavior of aluminum-base intermetallics containing iron; J. Electrochem. Soc. 137 (1990) 69–77.
- [43] K.A. Yasakau, M.L. Zheludkevich, S.V. Lamaka, M.G.S. Ferreira; Role of intermetallic phases in localized corrosion of AA5083; Electrochim. Acta 52 (2007) 7651–7659.
- [44] R. Arrabal, B. Mingo, A. Pardo, M. Mohedano, E. Matykina, I. Rodriguez; Pitting corrosion of rheocast A356 aluminium alloy in 3.5 wt.% NaCl solution; Corrosion Science 73 (2013) 342–355.
- [45] H.C. Fang, H. Chao, K.H. Chen; Effect of recrystallization on intergranular fracture and corrosion of Al–Zn–Mg–Cu–Zr alloy; Journal of Alloys and Compounds 622 (2015) 166–173.
- [46] Fengxuan Song, Xinming Zhang, Shengdan Liu, Qi Tan, Dongfeng Li; The effect of quench rate and overageing temper on the corrosion behaviour of AA7050; Corrosion Science xxx (2013).
- [47] Lanping Huang, Kanghua Chen, Song Li; Influence of grain-boundary pre-precipitation and corrosion characteristics of inter-granular phases on corrosion behaviors of an Al–Zn–Mg–Cu alloy; Materials Science and Engineering B 177 (2012) 862– 868.
- [48] Amjad Saleh El-Amoush; Intergranular corrosion behavior of the 7075-T6 aluminum alloy under different annealing conditions; Materials Chemistry and Physics 126 (2011) 607-613.
- [49] W.J. Liang, P.A. Rometsch, L.F. Cao, N. Birbilis; General aspects related to the corrosion of 6xxx series aluminium alloys:Exploring the influence of Mg/Si ratio and Cu; Corrosion Science 76 (2013) 119–128.
- [50] Starink M.J., Li X M.; A model for electrical conductivity of peak-aged and overaged Al−Zn−Mg−Cu alloys; [J]. Metallurgical and Materials Transactions A, 2003, 34(4): 899−911.
- [51] Chen Song-yi, Chwn Kang-hua, Peng Guo-sheng, Liang Xin, Chen Xue-hai; Effect of quenching rate on microstructure and stress corrosion cracking of 7085 aluminum alloy; [J]. Transactions of Nonferrous Metals Society of China, 2012, 22(1): 47−52.
- [52] Knight S. P., Birbilis N., Muddle B. C., Trueman A. R., Lynch S. P.; Correlations between intergranular stress corrosion cracking, grain-boundary microchemistry, and grain-boundary electrochemistry for Al−Zn−Mg−Cu alloys; [J]. Corrosion Science, 2010, 52(12): 4073−4080.
- [53] Andreatta F., Terryn H., de Wit J. H. W.; Effect of solution heat treatment on galvanic coupling between intermetallics and matrix in AA7075-T6; [J]. Corrosion Science, 2003, 45(8): 1733−1746.
- [54] Zhang Ping, Li Qi, Zhao Jun-jun, Zeng Qing-qiang.; Analysis of secondary phases and measurement of volta potential of 7A52aluminum alloy; [J]. The Chinese Journal of Nonferrous Metals, 2011, 21(6): 1252−1257.
- [55] Venugopal A., Panda R., Manwatkar S., Sreekumar K., Rama Krishna L., Sundararajan G.; Effect of micro arc oxidation treatment on localized corrosion behaviour of AA7075 aluminum alloy in 3.5% NaCl solution; [J]. Transactions of Nonferrous Metals Society of China, 2012, 22(3): 700−710.
- [56] Huan She, Wei Chu, Da Shu, Jun Wang, Bao-de Sun; Effects of silicon content on microstructure and stress corrosion cracking resistance of 7050 aluminum alloy; Trans. Nonferrous Met. Soc. China 24(2014) 2307−2313.
- [57] S. Geng, S. Joshi, W. Pinc, W.G. Fahrenholtz, M.J. O’Keefe, T.J. O’Keefe, P. Yu; Influence of processing parameters on cerium based conversion coatings; in: Proc. Tri-Service Corrosion Conference, Denver, CO, NACE International, 2007,p. 10.
- [58] B. Valdez, S. Kiyota, M. Stoytcheva, R. Zlatev, J.M. Bastidas; Cerium-based conversion coatings to improve the corrosion resistance of aluminium alloy 6061-T6; Corrosion Science 87 (2014) 141–149.
- [59] Peter Plagemann, Joerg Weise, Anja Zockoll; Zinc–magnesium-pigment rich coatings for corrosion protection of aluminum alloys; Progress in Organic Coatings 76 (2013) 616– 625.
- [60] Du Nan, Wang Shuai-xing, Zhao Qing, Shao Zhi-song; Effects of boric acid on microstructure and corrosion resistance of boric/sulfuric acid anodic film on 7050 aluminum alloy; Trans. Nonferrous Met. Soc. China 22(2012) 1655-1660.
- [61] J. Singh-Beemat, J.O. Iroh; Effect of clay on the corrosion inhibition and dynamic mechanical properties of epoxy ester–polyurea–polysiloxane hybrid coatings; Polym. Eng. Sci. (2012).
- [62] J. Singh-Beemat, J.O. Iroh; Characterization of corrosion resistant clay/epoxy ester composite coatings and thin films; Progress in Organic Coatings 74 (2012) 173–180.
- [63] Jaspreet Singh-Beemat, Jude O. Iroh, Linqian Feng; Mechanism of corrosion protection of aluminum alloy substrate byhybrid polymer nanocomposite coatings; Progress in Organic Coatings 76 (2013) 1576– 1580.
- [64] E. Tillová, E. Ďuriníková, M. Chalupová; Structural analysis of secondary AlZn10Si8Mg cast alloy; Acta Metallurgica Slovaca, Vol. 17, 2011, No. 1, p. 4-10.
- [65] E. Tillová, E. Ďuriníková, M. Chalupová; Characterization of phases in secondary AlZn10Si8Mg cast alloy; Materials Engineering - Materiálové inžinierstvo 18 (2011) 1-7.
- [66] http://www.dietermann-guss.de/_pdf-Dateien/IN%20FORM_01_12%20eng.pdf.
- [67] M.Rosso, I.Peter, C.Castella , R.Molina; Investigation on AlZn10Si8Mg alloys for automotive application; Metallurgical Science and Technology Vol. 31-1 - Ed. 2013.
- [68] M.Rosso, I.Peter, C.Castella , R.Molina; Properties of AlZn10Si8Mg Alloys for High Performances Application; Light metals 2014 p.213-218.
- [69] I.Peter, M.Rosso, C.Castella, R.Molina; Self-hardening alloys for automotive application; Materials Science Forum Vols. 794-796 (2014) pp 1221-1226.
- [70] http://www.rheinfelden-alloys.eu/.
- [71] C. Y. Song, J. Lee; Reliability-based design optimization of knuckle component using conservative method of moving least squares meta-models; Probabilistic Engineering Mechanics 26 (2011) 364–379.
- [72] J. L. Murray; The Al-Zn (Aluminum-Zinc) System; Bulletin of Alloy Phase Diagrams Vol. 4 No. 1 1983.
- [73] G.Timelli, E.Fiorese; Metodi di neutralizzazione del Fe in leghe Al-Si da fonderia; La Metallurgia Italiana n.3 Marzo 2011 9-23.
- [74] C. Mascré, Fonderie, 108 (1955), 4330-4334.
- [75] R. Arrabal, B. Mingo, A. Pardo, M. Mohedano, E. Matykina, I. Rodriguez, Pitting corrosion of rheocast A356 aluminium alloy in 3.5 wt.% NaCl solution, Corrosion Science 73 (2013) 342–355.
- [76] Kiryl A. Yasakau, Mikhail L. Zheludkevich ,Sviatlana V. Lamaka, Mario G.S. Ferreira; Role of intermetallic phases in localized corrosion of AA5083; Electrochimica Acta 52 (2007) 7651–7659.
- [77] V.A. Hosseini, S.G. Shabestari, R. Gholizadeh; Study on the effect of cooling rate on the solidification parameters, microstructure, and mechanical properties of LM13 alloy using cooling curve thermal analysis tecjnique; Materials and Design 50 (2013) 7–14.
- [78] Deepak Singla1, S.R. Mediratta; Evaluation of mechanical properties of Al 7075-fly ash composite material; International Journal of Innovative Research in Science, Engineering and Technology Vol. 2, Issue 4, April 201.
- [79] Determination of resistance to IGC of solution heat-treatable aluminium alloys, Standard BS11846:1995, Brithish Standards Institution (1995).
9. Copyright:
- This material is "Christian Castella"'s paper: Based on "Self hardening aluminum alloys for automotive applications".
- Paper Source: [DOI URL]
This material was summarized based on the above paper, and unauthorized use for commercial purposes is prohibited.
Copyright © 2025 CASTMAN. All rights reserved.