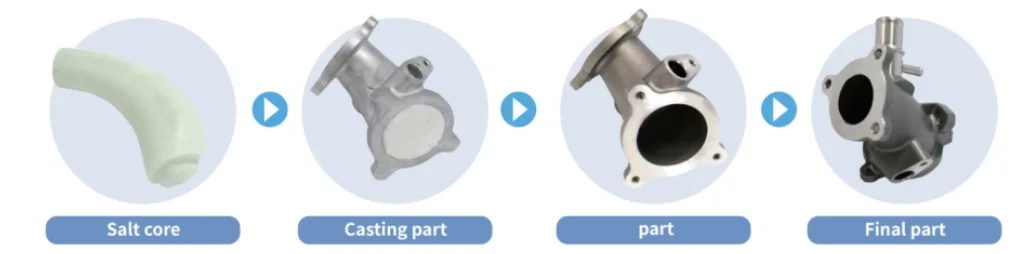
Aluminum high-pressure die casting is a widely used manufacturing process known for its high efficiency and precision. However, producing parts with undercut shapes—features that interfere with the mold opening direction—poses significant challenges. Traditional solutions, such as slide cores or multi-part molds, increase complexity, costs, and limit design flexibility.
Application of Salt Core Technology for Undercut Shapes
Salt core technology is an innovative solution that addresses the challenges of producing undercut shapes in aluminum die casting. This process involves using a soluble salt material as a core to create complex internal geometries, including undercuts.
Technical Process
- Salt Core Production:
- A salt core is manufactured using a specialized die casting method, ensuring heat resistance and precise geometry.
- The salt material can be molded into highly intricate and accurate shapes.
- Core Insertion and Casting:
- The salt core is placed inside the die cavity.
- Molten aluminum alloy is injected at high pressure, forming the external structure of the part while leaving the salt core intact.
- Salt Core Removal:
- After casting, the salt core is dissolved in water or a solvent, leaving behind the desired undercut or internal geometry.
Advantages of Salt Core Technology
- Enables Complex Undercut Geometries:
- Overcomes the limitations of traditional die casting, allowing the creation of intricate internal structures and undercut features.
- Minimizes Post-Processing:
- Eliminates the need for additional machining or assembly, reducing production time and costs.
- Increases Design Flexibility:
- Allows engineers to focus on optimizing part functionality and weight without being constrained by mold design limitations.
- Improves Precision and Consistency:
- Salt cores offer high dimensional accuracy, ensuring consistent quality across production batches.
- Prevents Reverse Engineering:
- The salt core dissolves after casting, making it difficult for competitors to analyze or replicate the internal features of the part.
Conclusion
Salt core technology is a game-changing solution for producing aluminum die-cast parts with undercut shapes. By offering greater design freedom, enhanced efficiency, and higher precision, it has become an essential method for automotive, aerospace, and other industries requiring complex, high-performance components.
Key Applications of Salt Core Technology
- Automotive Components:
- Turbocharger housings, differential housings, exhaust manifolds, transmission channels, and other parts with complex internal geometries.
- Aerospace Parts:
- Lightweight and precise internal channels for jet engines and cooling systems.
- Electronics and Heat Management Systems:
- Heat sinks and cooling channels with intricate designs for optimized thermal performance.
Automotive Components
1. Turbocharger Housing Internal Structures
Traditional High-Pressure Die Casting Challenges:
- Creating intricate internal passages for airflow often requires multi-part assemblies or post-casting machining due to undercut shapes.
Advantages of Salt Core Process:
- Improved Design Freedom: Enables the creation of complex internal geometries in a single casting step.
- Enhanced Performance: Optimized airflow paths improve engine efficiency and reduce turbo lag.
- Lightweight and Strong: Internal voids reduce weight without compromising structural integrity.
2. Exhaust Manifold
Traditional High-Pressure Die Casting Challenges:
- Undercut geometries for exhaust flow pathways require complex cores or multi-piece assemblies, increasing cost and reducing durability.
Advantages of Salt Core Process:
- Seamless Integration: Single-piece casting eliminates the need for assembly or welding.
- Thermal Efficiency: Accurate internal geometry ensures even thermal distribution, reducing hot spots.
- Durability: Eliminates weak points from weld seams, improving high-temperature resistance.
3. Engine Block Internal Oil Channels
Traditional High-Pressure Die Casting Challenges:
- Internal channels for oil flow are difficult to achieve due to undercuts, often requiring additional machining.
Advantages of Salt Core Process:
- Precision Channels: Enables the creation of smooth, precisely shaped oil channels for optimized lubrication.
- Cost Efficiency: Eliminates the need for additional machining or drilling.
- Improved Engine Performance: Ensures consistent oil flow, reducing friction and improving engine life.
4. Transmission Housing
Traditional High-Pressure Die Casting Challenges:
- The undercut sections for fluid flow and gear compartments require intricate machining or inserts.
Advantages of Salt Core Process:
- Integrated Fluid Passages: Salt cores enable the creation of complex internal fluid channels in one casting.
- Reduced Weight: Hollow sections reduce the overall weight while maintaining structural strength.
- Leakage Prevention: A single-piece casting minimizes the risk of fluid leakage from joints or seals.
5. Cooling System Components
Traditional High-Pressure Die Casting Challenges:
- Undercut geometries for coolant channels are difficult to form, often requiring brazing or additional parts.
Advantages of Salt Core Process:
- Thermal Optimization: Facilitates the creation of complex cooling channels that enhance heat dissipation.
- Streamlined Production: Reduces the need for additional assembly steps, increasing production efficiency.
- Improved Reliability: Single-piece designs are more resistant to leaks or failures under pressure.
6. Suspension Components
Traditional High-Pressure Die Casting Challenges:
- Suspension parts with hollow or intricate internal structures face challenges due to undercut sections.
Advantages of Salt Core Process:
- Lightweight Design: Internal voids reduce weight while maintaining the required mechanical strength.
- Increased Durability: The absence of seams or welds enhances resistance to fatigue and dynamic stresses.
- Enhanced Geometry Flexibility: Allows the production of innovative, performance-enhancing designs.
7. Brake Caliper
Traditional High-Pressure Die Casting Challenges:
- Internal hydraulic passages with undercuts are difficult to form in a single piece.
Advantages of Salt Core Process:
- Integrated Hydraulic Channels: Salt cores allow precise, smooth internal passages for improved braking performance.
- Weight Reduction: Hollow sections lower the weight without compromising braking efficiency.
- Enhanced Reliability: A single-piece design reduces the risk of hydraulic fluid leaks.
8. Fuel Injector Housing
Traditional High-Pressure Die Casting Challenges:
- Small, intricate internal pathways for fuel flow require additional machining or inserts, complicating production.
Advantages of Salt Core Process:
- Precision Fuel Flow: Enables accurate shaping of internal channels, enhancing fuel atomization and efficiency.
- Compact and Lightweight: Reduces the size and weight of the housing without sacrificing strength.
- Improved Consistency: Single-step casting ensures consistent quality and performance.
9. Differential Housing
Traditional High-Pressure Die Casting Challenges:
- Internal voids or undercut shapes for gear compartments are challenging to achieve with conventional methods.
Advantages of Salt Core Process:
- Enhanced Strength: Single-piece casting eliminates weak points at joints or seams.
- Optimized Weight: Hollow interiors reduce weight while ensuring structural integrity.
- Noise Reduction: Improved geometry allows better noise and vibration dampening.
10. Electric Vehicle Battery Module Case
Traditional High-Pressure Die Casting Challenges:
- Cooling channels and internal compartments often involve undercuts, making them complex to manufacture with standard techniques.
Advantages of Salt Core Process:
- Thermal Management: Facilitates the integration of complex cooling channels to enhance heat dissipation.
- Structural Integrity: One-piece casting ensures robust housing to protect battery cells.
- Weight Efficiency: Hollow designs reduce weight, crucial for extending EV range.
Summary of Benefits for Undercut Components:
- Design Flexibility: Salt core processes enable the production of complex geometries in one step.
- Cost Savings: Reduces or eliminates secondary machining, welding, or assembly.
- Performance Enhancement: Improves fluid flow, heat dissipation, and overall mechanical performance.
- Weight Reduction: Allows for lighter designs without sacrificing strength or durability.
- Production Efficiency: Streamlines manufacturing processes, increasing output and consistency.
The salt core process is a transformative solution for addressing the challenges of undercut geometries in automotive parts, enabling manufacturers to achieve higher performance and cost efficiency.