This article introduces the paper "Phase-Field Modelling of Bimodal Dendritic Solidification During Al Alloy Die Casting" presented in Metals.
1. Overview:
Title: Phase-Field Modelling of Bimodal Dendritic Solidification During Al Alloy Die Casting
Authors: Maryam Torfeh, Zhichao Niu and Hamid Assadi
Publication Year: 2025
Publishing Journal: Metals
Keywords: phase-field modelling; HPDC; interface behaviour
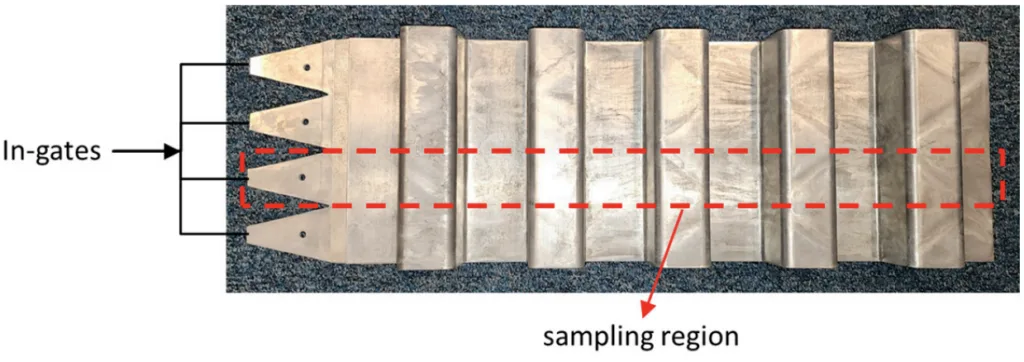
2. Research Background:
High-pressure die casting (HPDC) is a cost-effective method for producing near-net shape components from lightweight aluminium alloys. The final quality of HPDC products is significantly influenced by several process factors. Understanding and controlling the microstructure is paramount to achieving desired mechanical properties, especially in large HPDC components where maintaining uniform microstructure is challenging due to long flow paths.
However, tracking solidification dynamics in HPDC is inherently complex due to rapid solidification rates, fluctuating thermal conditions, and intense turbulence. While numerical simulations have become valuable tools for optimizing casting design and process parameters, most existing studies primarily focus on fluid dynamics and heat transfer, often employing the Finite Element Method (FEM). Predicting microstructure evolution is a more recent focus, typically combining FEM with Cellular Automata (CA). The phase-field method, a powerful technique for modelling solidification, has been underutilized in the context of HPDC. Therefore, there is a clear necessity to investigate dendritic structure evolution in HPDC using advanced modelling techniques like the phase-field method to gain deeper insights into the formation of complex microstructures under rapid solidification conditions.
3. Research Purpose and Research Questions:
Research Purpose:
This study aims to analyse the evolution of dendritic structures during high-pressure die casting (HPDC) using phase-field modelling. The primary goal is to understand how rapid solidification conditions in HPDC lead to the formation of bimodal dendritic microstructures.
Key Research Questions:
The research seeks to answer the following key questions:
- Can a two-dimensional phase-field model effectively simulate the bimodal dendritic solidification process observed in HPDC of Al-Si alloys?
- How do changes in solid-liquid interface properties, reflecting the transition from the shot sleeve to the die cavity, influence the dendritic morphology in the phase-field model?
Research Hypotheses:
While not explicitly stated as hypotheses, the study operates on the premise that by systematically varying solid-liquid interface properties within a phase-field model, it is possible to replicate the microstructural transitions occurring during HPDC, specifically the formation of bimodal dendritic structures resulting from the shift from slower cooling in the shot sleeve to rapid cooling in the die cavity.
4. Research Methodology
Research Design:
This research employed a two-dimensional phase-field model to simulate dendritic solidification. The model is thermodynamically formulated to account for temperature changes from phase transformation heat, thermal boundary conditions, and solute diffusion in both liquid and solid phases.
Data Collection Method:
The study involved both experimental microstructure analysis and numerical simulation.
- Microstructure Study: A hypo-eutectic Al-7% Si alloy casting produced by a 16,000 KN cold chamber HPDC machine was used for microstructure evaluation. Samples were taken from different locations along a ribbed plate casting. Microstructure was observed using optical microscopy after standard metallographic preparation including grinding, polishing, and anodising.
- Numerical Simulation: Phase-field simulations were conducted to model dendritic growth under conditions representative of the shot sleeve and die cavity stages of HPDC.
Analysis Method:
- Microscopic Observation: Optical microscopy was used to analyse the α-Al particle size distribution and segregation band formation at different locations in the HPDC casting.
- Phase-Field Modelling: The phase-field model was used to simulate dendritic solidification, focusing on the impact of varying solid-liquid interface properties (thickness, energy, and mobility) to mimic the transition from shot sleeve to die cavity conditions.
Research Subjects and Scope:
The research focused on the solidification behaviour of a hypo-eutectic Al-7% Si alloy (Al-7% Si) during HPDC. The simulation domain was two-dimensional, using a 500 × 500 cell grid. The study investigated the dendritic solidification process in both the shot sleeve and die cavity stages of HPDC.
5. Main Research Results:
Key Research Results:
The phase-field model successfully demonstrated its ability to:
- Capture the growth of dendrites under shot sleeve cooling conditions.
- Simulate the nucleation and development of new dendrite arms under rapid cooling conditions characteristic of the die cavity.
- Replicate the observed bimodal microstructure by adjusting solid-liquid interface properties to reflect the transition from shot sleeve to die cavity.
Statistical/Qualitative Analysis Results:
- Microstructure Observation: Analysis of the casting microstructure revealed a progressive reduction in the average α-Al particle size from the in-gate to the end of the plate. Specifically, the average size decreased from approximately 21 µm near the in-gate (sample 1) to about 3 µm at the far end (sample 7). Figure 3 shows that approximately 70% of α-Al particles in the middle section of the plate and beyond are in the size range of 0–10 µm, indicating a finer and more uniform particle distribution compared to the in-gate region.
- Segregation Band: A segregation band became more prominent towards the end of the casting, indicating variations in solute distribution along the casting length.
Data Interpretation:
The observed bimodal microstructure in the HPDC casting is attributed to the formation of externally solidified crystals (ESCs) in the shot sleeve, followed by the nucleation and growth of new, finer dendrite arms on these fragmented ESCs upon entering the die cavity with its rapid cooling conditions. The phase-field model effectively captured this transition by adjusting interface properties, demonstrating the model's sensitivity to changes in solidification conditions.
Figure Name List:
- Figure 1. Sampling region on the plate manufactured by HPDC.
- Figure 2. Microstructure evolution at seven sampling locations (S1-S7) along the plate, (a) advent of segregation band at last one-third of the plate shown by red arrows, (b) comparison of α-Al particles.
- Figure 3. Size distribution of a-Al particles along the plate.
- Figure 4. Comparison of a-Al particles along the plate, (a) and (b) near the in-gate, (c) at the end of the plate (the arrows show the new arms nucleated on fragmented dendrites).
- Figure 5. (a) Externally solidified crystals at the in-gate, (b,c) phase-field and Si concentration of dendrites at shot sleeve after 2 ms, (d,e) after 15 ms.
- Figure 6. Comparison of secondary nucleation on a dendrite grew in the shot sleeve for 2 ms and transferred to die cavity (states 1-3 show interface thicknesses of 700–500 nm).
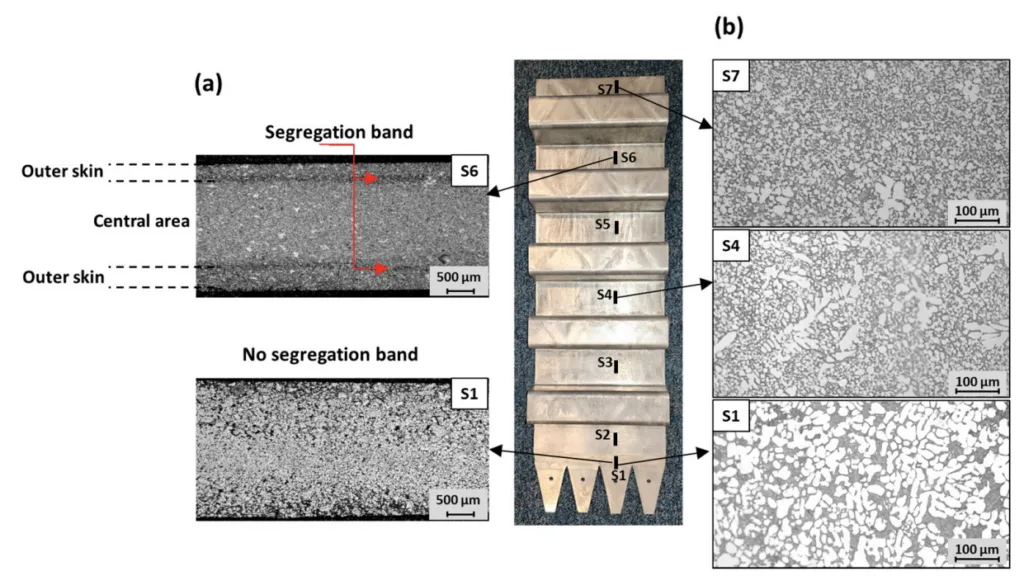
segregation band at last one-third of the plate shown by red arrows, (b) comparison of α-Al particles.
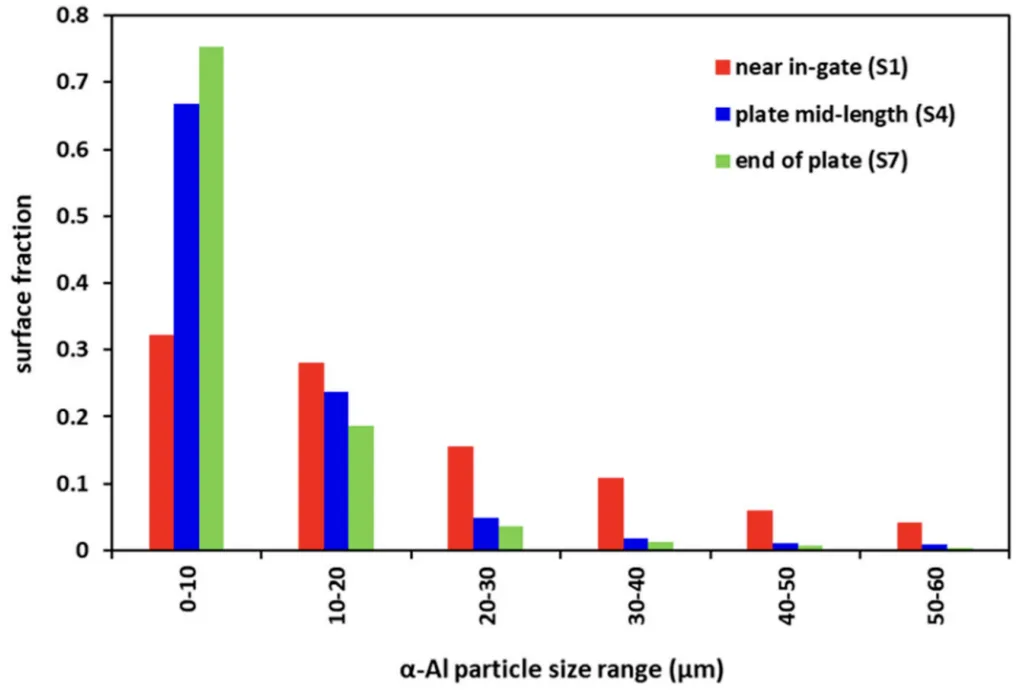
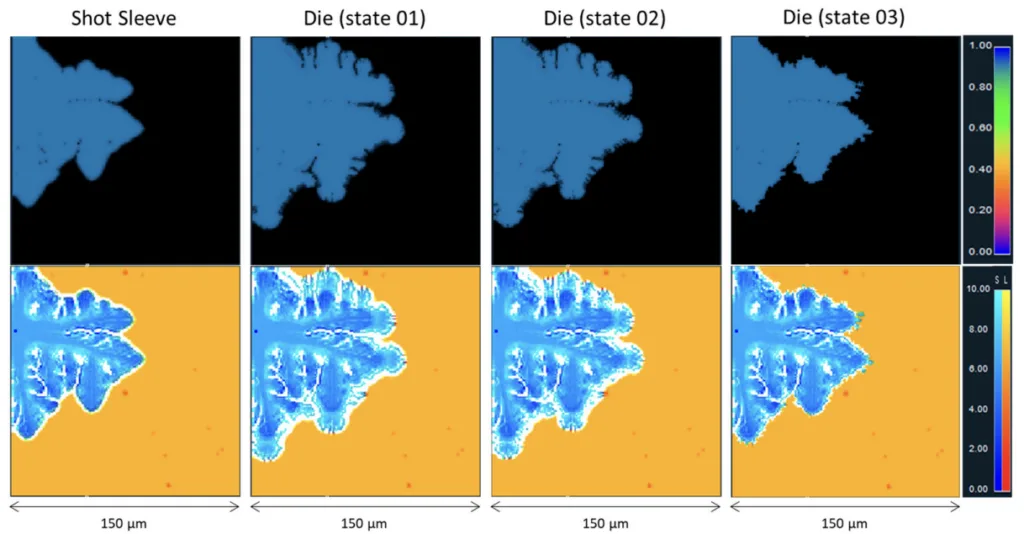
6. Conclusion and Discussion:
Summary of Main Results:
This study successfully employed phase-field modelling to simulate bimodal dendritic solidification during HPDC of Al-Si alloys. The model effectively captured the turbulence-induced fragmentation and subsequent nucleation of new dendrite arms by systematically varying solid-liquid interface properties to represent the changing conditions from the shot sleeve to the die cavity.
Academic Significance of the Research:
This research provides valuable academic insights into the role of turbulence in dendritic solidification within the complex HPDC process. It demonstrates the utility of the phase-field modelling approach for replicating intricate microstructural phenomena observed in die casting.
Practical Implications:
The findings underscore the critical importance of tuning interface properties in phase-field models to accurately represent process-specific conditions in HPDC. This offers a pathway for further optimization of HPDC processes and improved microstructural control in Al-Si alloy castings, potentially leading to enhanced mechanical properties and component performance.
Limitations of the Research:
While the phase-field model effectively captured key aspects of dendritic solidification, it primarily focused on solidification phenomena. The effects of turbulence were inferred indirectly through adjustments to the solid-liquid interface thickness. A more direct incorporation of turbulence effects into the model could further enhance its accuracy and predictive capabilities.
7. Future Follow-up Research:
Directions for Follow-up Research:
Future research should focus on:
- Incorporating a more direct representation of turbulence effects within the phase-field model to enhance simulation accuracy.
- Expanding the model to explore a wider range of HPDC process parameters, such as injection speed, die temperature, and intensification pressure.
- Investigating the solidification behaviour of different Al-Si alloy compositions using the developed phase-field modelling approach.
Areas Requiring Further Exploration:
Further exploration is needed to deepen the understanding of the interplay between kinetic and thermodynamic factors governing dendrite evolution under the complex conditions of HPDC, particularly the influence of turbulence and rapid cooling on interface properties and microstructure formation.
8. References:
- [1] Han, Q.; Zhang, J. Fluidity of Alloys Under High-Pressure Die Casting Conditions: Flow-Choking Mechanisms. Metall. Mater. Trans. B 2020, 51, 1795-1804.
- [2] Mednanský, M.; Bruna, M.; Matejka, M. Electromotor Housing Microstructure Dependence on HPDC Process Parameters. Transp. Res. Procedia 2023, 74, 680-687.
- [3] Niu, Z.; Liu, G.; Li, T.; Ji, S. Effect of High Pressure Die Casting on the Castability, Defects, and Mechanical Properties of Aluminium Alloys in Extra-Large Thin-Wall Castings. J. Mater. Process. Technol. 2022, 303, 117525.
- [4] Zhu, X.; Dong, X.; Blake, P.; Ji, S. Improvement in As-Cast Strength of High-Pressure Die-Cast Al-Si-Cu-Mg Alloys by Synergistic Effect of Q-Al5Cu2Mg8Si6 and 0-Al2Cu Phases. Mater. Sci. Eng. A 2021, 802, 140612.
- [5] Laukli, H.I.; Gourlay, C.M.; Dahle, A.K.; Lohne, O. Effects of Si Content on Defect Band Formation in Hypoeutectic Al-Si Die Castings. Mater. Sci. Eng. A 2005, 413–414, 92-97.
- [6] Helenius, R.; Lohne, O.; Arnberg, L.; Laukli, H.I. The Heat Transfer during Filling of a High-Pressure Die-Casting Shot Sleeve. Mater. Sci. Eng. A 2005, 413, 52-55.
- [7] Ji, S.; Wang, Y.; Watson, D.; Fan, Z. Microstructural Characteristics of Diecast AlMgSiMn Alloy. Mater. Sci. Forum 2014, 783, 234-239.
- [8] Zheng, H.; Jiang, Y.; Liu, F.; Zhao, H. Synergistic Effect of Externally Solidified Crystals and Fe-Rich Intermetallic on the Fracture Behavior of HPDC Alloy. J. Mater. Res. Technol. 2023, 27, 2822-2832.
- [9] Xie, H.; Wang, J.; Li, Y.; Song, J.; Hu, H.; Qin, L.; Zhao, H.; Li, C.; Cui, Y.; Tan, Z.; et al. Fast Shot Speed Induced Microstructure and Mechanical Property Evolution of High-Pressure Die Casting Mg-Al-Zn-RE Alloys. J. Mater. Process. Technol. 2024, 331, 118523.
- [10] Li, J.; Yu, W.; Sun, Z.; Zheng, W.; Zhang, L.; Xue, Y.; Liu, W.; Xiong, S. Influence of Introducing Zr, Ti, Nb and Ce Elements on Externally Solidified Crystals and Mechanical Properties of High-Pressure Die-Casting Al–Si Alloy. Int. J. Miner. Metall. Mater. 2025, 32, 147-153.
- [11] Zhu, X.; Yang, H.; Dong, X.; Ji, S. The Effects of Varying Mg and Si Levels on the Microstructural Inhomogeneity and Eutectic Mg2Si Morphology in Die-Cast Al-Mg-Si Alloys. J. Mater. Sci. 2019, 54, 5773–5787.
- [12] Yang, Q.; Wu, X.; Qiu, X. Microstructural Characteristics of High-Pressure Die Casting with High Strength-Ductility Synergy Properties: A Review. Materials 2023, 16, 1954.
- [13] Gu, C.; Lu, Y.; Cinkilic, E.; Miao, J.; Klarner, A.; Yan, X.; Luo, A.A. Predicting Grain Structure in High-Pressure Die Casting of Aluminum Alloys: A Coupled Cellular Automaton and Process Model. Comput. Mater. Sci. 2019, 161, 64-75.
- [14] El-Mahallawy, N.A.; Taha, M.A.; Pokora, E.; Klein, F. On the influence of process variables on the thermal conditions and properties of high pressure die-cast magnesium alloys. J. Mater. Process. Technol. 1998, 73, 125-138.
- [15] Kwon, H.J.; Kwon, H.K. Computer aided engineering (CAE) simulation for the design optimization of gate system on high pressure die casting (HPDC) process. Robot. Comput.-Integr. Manuf. 2019, 55, 147-153.
- [16] Sharifi, P.; Jamali, J.; Sadayappan, K.; Wood, J.T. Grain size distribution and interfacial heat transfer coefficient during solidification of magnesium alloys using high pressure die casting process. J. Mater. Sci. Technol. 2018, 34, 324-334.
- [17] Dou, K.; Lordan, E.; Zhang, Y.J.; Jacot, A.; Fan, Z.Y. A complete computer aided engineering (CAE) modelling and optimization of high pressure die casting (HPDC) process. J. Manuf. Process. 2020, 60, 435-446.
- [18] Assadi, H. A Phase-Field Model for Non-Equilibrium Solidification of Intermetallics. Acta Mater. 2007, 55, 5225-5235.
- [19] Li, B.; Xu, Q.Y.; Liu, B.C. Numerical Modeling of Microstructure Evolution and Dendrite Growth for Al-Si Alloy Casting during Low Pressure Die Casting. Mater. Sci. Forum 2007, 561–565, 1787-1792.
- [20] Belov, N.A.; Eskin, D.G.; Aksenov, A.A. Multicomponent Phase Diagrams: Applications for Commercial Aluminum Alloys; Elsevier: Amsterdam, The Netherlands, 2005; p. 48.
- [21] Dey, A.K.; Poddar, P.; Singh, K.K.; Sahoo, K.L. Mechanical and Wear Properties of Rheocast and Conventional Gravity Die Cast A356 Alloy. Mater. Sci. Eng. A 2006, 435-436, 521-529.
- [22] Zheng, H.; Jiang, Y.; Liu, F.; Zhao, H. Microstructure Heterogeneity Optimization of HPDC Al-Si-Mg-Cu Alloys by Modifying the Characteristic of Externally Solidified Crystals. J. Alloys Compd. 2024, 976, 173167.
- [23] Otarawanna, S.; Gourlay, C.M.; Laukli, H.I.; Dahle, A.K. Microstructure Formation in High Pressure Die Casting. Trans. Indian Inst. Met. 2009, 62, 499-503.
- [24] Laukli, H.I.; Gourlay, C.M.; Dahle, A.K. Migration of Crystals during the Filling of Semi-Solid Castings. Metall. Mater. Trans. A 2005, 36, 805-818.
- [25] Hao, Y.Z.; Zhao, H.D.; Shen, X.; Wang, X.L.; Zheng, H.T. Simulation of a-Al Grain Formation in High Vacuum Die-Casting Al-Si-Mg Alloys with Multi-Component Quantitative Cellular Automaton Method. China Foundry 2022, 19, 99–108.
- [26] Han, Q.; Xu, H. Fluidity of Alloys under High Pressure Die Casting Conditions. Scr. Mater. 2005, 53, 7-10.
- [27] Reyes, A.E.S.; Guerrero, G.A.; Ortiz, G.R.; Gasga, J.R.; Robledo, J.F.G.; Flores, O.L.; Costa, P.S. Microstructural, Microscratch and Nanohardness Mechanical Characterization of Secondary Commercial HPDC AlSi9Cu3-Type Alloy. J. Mater. Res. Technol. 2020, 9, 8266-8282.
- [28] Zhang, H.; Li, D.; Wang, Q.; Fan, Z.; Luo, M.; Midson, S.P.; Zhu, Q. Effect of Primary a-Al Morphology in Slurry on Segregation during 357 Semi-Solid Die Casting. Solid State Phenom. 2019, 285, 398-402.
- [29] Gourlay, C.M.; Laukli, H.I.; Dahle, A.K. Segregation Band Formation in Al-Si Die Castings. Metall. Mater. Trans. A 2004, 35, 2881-2891.
9. Copyright:
This material is Maryam Torfeh, Zhichao Niu and Hamid Assadi's paper: Based on Phase-Field Modelling of Bimodal Dendritic Solidification During Al Alloy Die Casting.
Paper Source: https://doi.org/10.3390/met15010066
This material was summarized based on the above paper, and unauthorized use for commercial purposes is prohibited.
Copyright © 2025 CASTMAN. All rights reserved.