This article introduces the paper['PROGRESS IN DUCTILE ALUMINIUM HIGH PRESSURE DIE CASTING ALLOYS FOR THE AUTOMOTIVE INDUSTRY'] published by ['la metallurgia italiana'].
1. Overview:
- Title: PROGRESS IN DUCTILE ALUMINIUM HIGH PRESSURE DIE CASTING ALLOYS FOR THE AUTOMOTIVE INDUSTRY
- Author: R. Franke, D. Dragulin, A. Zovi, F. Casarotto
- Publication Year: 2007
- Publishing Journal/Academic Society: la metallurgia italiana
- Keywords: high-pressure die casting alloys, ductility in the as-cast state, automotive, ductile al-alloys
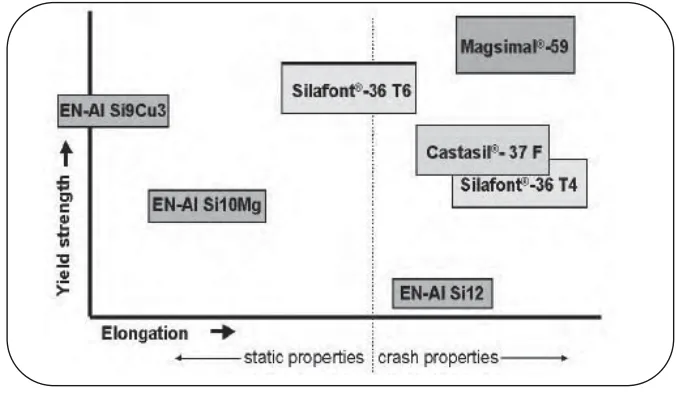
2. Abstracts or Introduction
The modern die casting process is increasingly utilized for manufacturing components demanding high quality, such as engine cradles, cross members, and nodes for space frame constructions. This trend necessitates the development of design alloys exhibiting superior mechanical properties. For crash-relevant automotive parts where high ductility (elongation > 12 %) is a critical requirement, two primary approaches are considered. The first involves heat treating low iron Al-Si alloys to T4 or T7 tempers. However, this method can induce part distortion and blistering, leading to increased production costs. The second approach employs Al-Mg alloy types, which inherently meet ductility requirements in the as-cast state, but these alloys present challenges in casting process. Consequently, research efforts have been directed towards leveraging the easily castable Al-Si alloy system to achieve high elongation (> 12 %) and yield-strength (> 120 MPa) in temper F, without long term aging behavior. This paper elucidates the technical advancements initiated in the early 1990s, which gained prominence with the advent of the first series space frame Aluminum car, and have continued with structural components applied in the as-cast condition, moving towards a future characterized by an increasing utilization of lightweight components replacing steel and heat treated Aluminum designs.
3. Research Background:
Background of the Research Topic:
The automotive industry serves as the primary driving force behind the innovation and production of novel die casting alloys. From a technical standpoint, the application domain of standard aluminium alloys is constrained. These conventional alloys are predominantly used for components with basic requirement profiles, typically focusing on low weight and a certain yield strength. As qualitatively assessed in Fig. 1, standard alloys exhibit inherent limitations in fulfilling advanced mechanical demands.
Status of Existing Research:
Currently, Al Si9Cu3-type (226) alloys are predominantly employed for parts where ductility or high corrosion resistance are not critical requirements. Al Si12-alloy offers a degree of ductility when cast in permanent molds, but it lacks significant yield strength. Therefore, achieving an optimal balance of properties often necessitates compromises among these existing alloy systems.
Necessity of the Research:
There is a pressing need for aluminum alloys suitable for high-pressure die casting that can deliver enhanced ductility and yield strength in the as-cast state. This eliminates the need for costly and potentially distorting heat treatments, particularly for complex automotive structural components. The development of such alloys is crucial for expanding the application of die casting in automotive industry, especially for safety-critical and lightweighting initiatives.
4. Research Purpose and Research Questions:
Research Purpose:
The primary purpose of this paper is to discuss the technical progress in the development and application of ductile aluminium high-pressure die casting alloys for the automotive industry, tracing advancements from the early 1990s to present applications.
Key Research:
The key research areas explored in this paper are centered around the development and characterization of specific ductile aluminium alloys for high-pressure die casting, namely Silafont®-36, Magsimal®-59, and Castasil®-37. These alloys are designed to address the increasing demands for mechanical performance, corrosion resistance, and castability in automotive structural components.
Research Hypotheses:
The research implicitly operates on the hypothesis that through careful alloy design and process optimization, aluminium alloys can be tailored to achieve:
- High ductility and adequate yield strength in the as-cast temper (F) for Al-Si based alloys like Silafont®-36 and Castasil®-37, thereby avoiding heat treatment.
- Superior corrosion resistance and mechanical properties in the as-cast temper for Al-Mg-Si based alloys like Magsimal®-59, suitable for demanding structural applications.
- Improved performance and weight reduction in automotive components by utilizing these advanced die casting alloys compared to traditional materials and processes.
5. Research Methodology
Research Design:
This paper adopts a descriptive and application-oriented approach, showcasing the evolution and implementation of specific ductile aluminium die casting alloys in the automotive sector. It presents case studies and alloy characterizations to illustrate the progress in the field.
Data Collection Method:
The paper relies on the presentation of mechanical property data, chemical compositions, and microstructural analyses of the discussed alloys. This data is presented through figures and tables, presumably derived from experimental testing and industrial applications.
Analysis Method:
The analysis is primarily qualitative and comparative, focusing on:
- Ranking and comparing the mechanical properties of different aluminium alloys, including standard and specialized alloys like Silafont®-36, Magsimal®-59, and Castasil®-37 (Fig. 1, Fig. 3, Fig. 5, Fig. 8).
- Microstructural examination to understand the effect of alloying elements and processing on the resulting properties (Fig. 2, Fig. 7).
- Case study analysis of automotive component applications, demonstrating the practical implementation and benefits of these alloys (Fig. 4, Fig. 6, Fig. 9).
Research Subjects and Scope:
The research focuses on ductile aluminium alloys specifically developed for high-pressure die casting in the automotive industry. The scope encompasses alloy design, property characterization, processing considerations, and application examples for structural and crash-relevant components. The alloys discussed are primarily Silafont®-36, Magsimal®-59, and Castasil®-37, along with comparisons to standard aluminium alloys.
6. Main Research Results:
Key Research Results:
- SILAFONT®-36: Introduced in 1994 by Aluminium Rheinfelden as the first ductile aluminium alloy for high-pressure die-casting. It is based on the Al-Si system and designed for high ductility in temper F, achievable through T4 or T7 heat treatments for demanding applications, or T5 or T6 for high yield strength needs (Fig. 3).
- MAGSIMAL®-59: Launched in 1996, this AlMgSi-type alloy exhibits exceptional corrosion resistance and superior mechanical properties in temper F. Its fine microstructure, resulting from rapid solidification, contributes to enhanced mechanical and fatigue properties (Fig. 5).
- CASTASIL®-37: Developed for complex designs requiring high ductility and medium yield strength in temper F. This Al-Si alloy is designed to be easily castable and avoids long-term aging. It achieves at least 12% elongation and 120 MPa yield strength in temper F, making it suitable for intricate automotive structural parts (Fig. 8).
Analysis of presented data:
- Figure 1 ranks aluminium alloys based on yield strength and elongation, highlighting the positioning of Silafont®-36 and Castasil®-37 relative to standard alloys like EN-Al Si9Cu3 and EN-Al Si12.
- Figure 2 compares the microstructure of standard Al Si10Mg material with Silafont®-36, demonstrating the finer, Sr-modified eutectic structure in Silafont®-36, which contributes to improved elongation.
- Figure 3 illustrates the range of mechanical properties achievable with Silafont®-36 through different heat treatments (T4, T5, T6, T7), showing the trade-off between yield strength and elongation.
- Figure 5 shows the mechanical properties of Magsimal®-59 as a function of wall thickness, indicating that thinner walls result in higher yield strength and elongation due to finer microstructure.
- Figure 8 presents the mechanical properties of Castasil®-37 in temper F as a function of wall thickness, showing a slight decrease in yield strength and a stable elongation with increasing wall thickness.
Figure Name List:
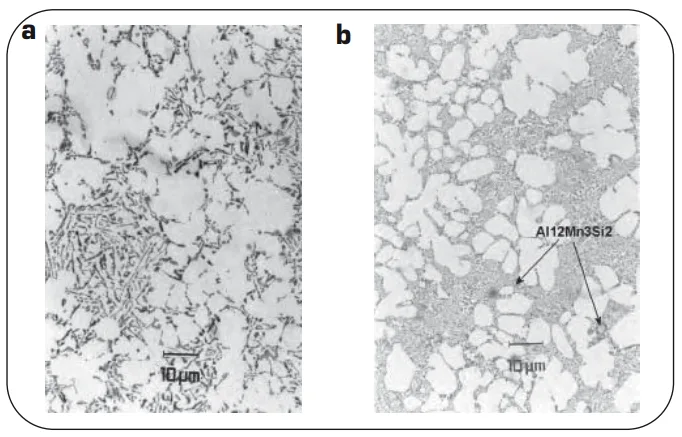
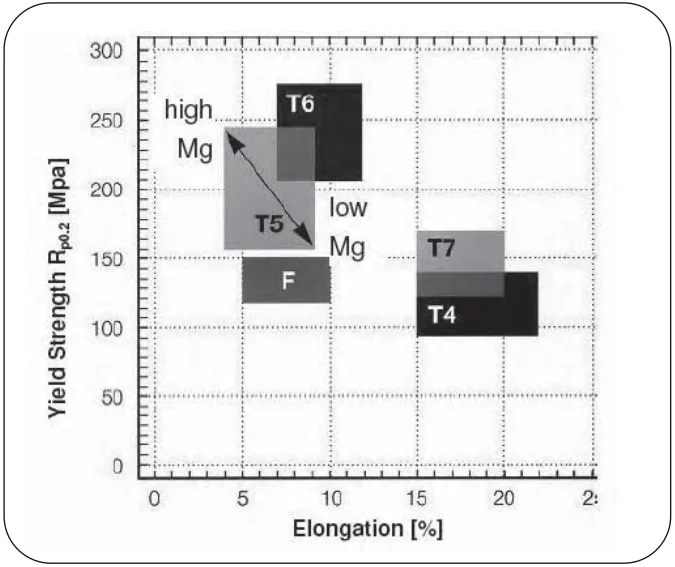

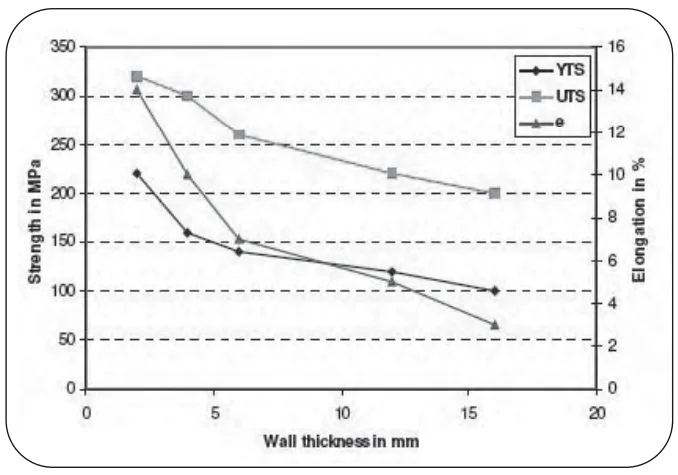
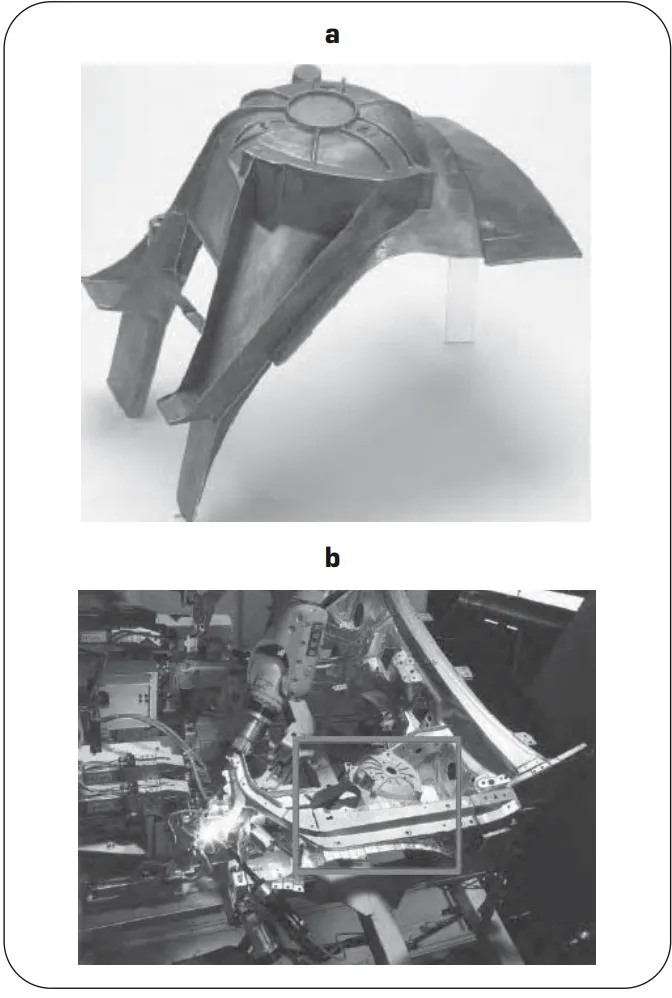
- Fig. 7 Microstructures of an AlSi9Mg standard material and Castasil®-37.
- Fig. 8 Mechanical properties of Castasil®-37 in temper F.
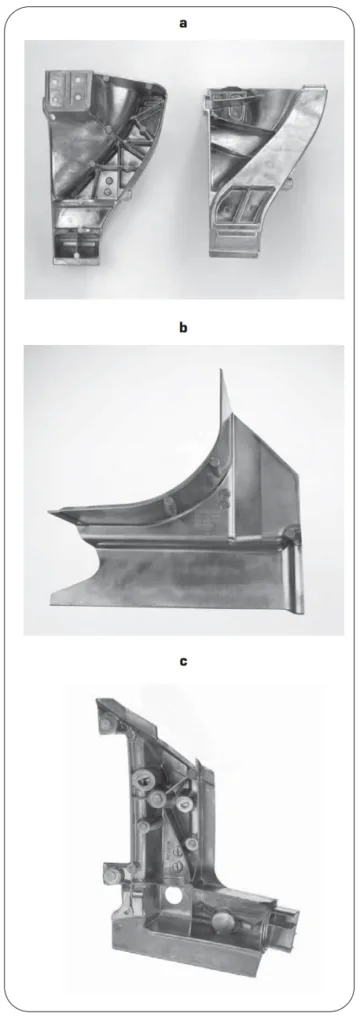
7. Conclusion:
Summary of Key Findings:
This paper highlights the progress in developing ductile aluminium high-pressure die casting alloys for the automotive industry. It introduces three key alloys: Silafont®-36, Castasil®-37, and Magsimal®-59, each designed to meet specific performance requirements. Silafont®-36 and Castasil®-37, based on the Al-Si system, offer high ductility in the as-cast state, with Castasil®-37 specifically tailored for complex geometries. Magsimal®-59, an Al-Mg-Si alloy, provides excellent corrosion resistance and mechanical strength. These alloys collectively address the automotive sector's demand for lightweight, high-performance structural components, enabling the replacement of steel and heat-treated aluminium in various applications.
Academic Significance of the Study:
The study demonstrates the significant advancements in aluminium die casting alloy technology, showcasing how alloy design can be strategically employed to achieve specific mechanical property profiles. It underscores the importance of understanding the interplay between alloy composition, processing parameters, and resulting microstructure in optimizing material performance for demanding applications like automotive structural components.
Practical Implications:
The development and application of Silafont®-36, Magsimal®-59, and Castasil®-37 offer practical solutions for automotive engineers seeking to utilize high-pressure die casting for structural and safety-critical parts. These alloys provide options for achieving weight reduction, enhanced mechanical performance, and improved corrosion resistance, while potentially simplifying manufacturing processes by reducing or eliminating the need for heat treatments and straightening operations. Examples like engine cradles, space frame nodes, and shock towers illustrate the successful implementation of these alloys in real-world automotive applications.
Limitations of the Study and Areas for Future Research:
This paper primarily presents a review of alloy development and applications, rather than in-depth experimental research. While it effectively showcases the progress in the field, it does not delve into detailed parametric studies or process optimizations. Future research could focus on:
- Further optimization of the compositions and processing of Silafont®-36, Castasil®-37, and Magsimal®-59 alloys to enhance specific properties or tailor them for new applications.
- Exploration of novel alloy systems and processing techniques to further improve the performance of ductile aluminium die casting alloys.
- Investigating the long-term performance and durability of these alloys in various automotive operating environments.
- Developing advanced simulation and modeling tools to aid in the design and optimization of die casting processes for these complex alloys and components.
8. References:
- 1) Koch H., Hielscher U., Sternau H.; Franke A. J., "Silafont®TM-36, the new lowiron high-pressure die-casting alloy", TMS, Light Metals 1995, 1011-1018
- 2) Koch H., Hielscher U., Sternau H.; Franke A. J.,"Magsimal™-59, an Al MgMnSi-Type Squeeze-Casting Alloy designed for temper F", TMS, Light Metals 1996, 933-937
9. Copyright:
- This material is "R. Franke, D. Dragulin, A. Zovi, F. Casarotto"'s paper: Based on "PROGRESS IN DUCTILE ALUMINIUM HIGH PRESSURE DIE CASTING ALLOYS FOR THE AUTOMOTIVE INDUSTRY".
- Paper Source: la metallurgia italiana >> maggio 2007
This material was summarized based on the above paper, and unauthorized use for commercial purposes is prohibited.
Copyright © 2025 CASTMAN. All rights reserved.