This article introduces the paper 'Optimizing Lightweight Material Selection in Automotive Engineering: A Hybrid Methodology Incorporating Ashby's Method and VIKOR Analysis' published by Preprints.org.
1. Overview:
- Title: Optimizing Lightweight Material Selection in Automotive Engineering: A Hybrid Methodology Incorporating Ashby's Method and VIKOR Analysis
- Author: Edoardo Risaliti, Francesco Del Pero, Gabriele Arcidiacono, Paolo Citti
- Publication Year: 2024
- Publishing Journal/Academic Society: Preprints.org
- Keywords: Lightweighting; Redesign; VIKOR; ashby; automotive; material selection; environmental impact; MCDA methods
![Table 1. IRV coefficient calculated by geographical relevance (NO: Norway, EU28: 28-country
European average, PL: Poland) and standard driving cycle (NEDC: New European Driving Cycle,
WLTC: Worldwide harmonized Light vehicles Test Cycles, ALDC: All-Long Driving Cycle) [65] [66].](https://castman.co.kr/wp-content/uploads/image-850-1024x387.webp)
2. Abstracts or Introduction
The automotive industry is facing increasing pressure to reduce greenhouse gas (GHG) emissions. Lightweighting is a key strategy, and material selection plays a crucial role in achieving mass reduction, thereby decreasing fuel consumption and enhancing vehicle performance. This paper introduces an innovative methodology for material selection in the automotive sector, integrating the Ashby approach and VIKOR (Vise Kriterijumska Optimizacija I Kompromisno Resenje) analysis. The Ashby method is utilized as an initial filter based on mechanical performance coefficients, followed by the VIKOR method to rank materials considering multiple criteria, including mechanical behavior, cost, manufacturing process availability, and environmental impact assessed via Life Cycle Assessment (LCA). The proposed hybrid methodology aims to provide a balanced and sustainable approach to material selection, validated through a re-design case study of a motor bracket for a C-segment passenger electric car.
3. Research Background:
Background of the Research Topic:
The automotive industry is a significant contributor to greenhouse gas emissions, accounting for approximately 20% in Europe. To meet stringent GHG emission reduction targets, lightweighting has emerged as a critical design strategy. Mass reduction in vehicles leads to decreased fuel consumption and exhaust emissions, alongside improvements in vehicle performance, safety, and handling. Selecting materials that offer superior structural properties with reduced weight compared to traditional materials like steel is a significant challenge.
Status of Existing Research:
Current lightweighting strategies encompass three major approaches: utilizing lightweight materials such as aluminum [15][18], titanium [18], magnesium [19], High-Strength Steels (HSS) [20], and composites [21]; employing innovative manufacturing processes like additive manufacturing [27], advanced sheet compression molding [28], and injection molding [29]; and optimizing component design through topology optimization [33][34]. The Ashby theory [40][41][42] is a widely recognized method for material selection in automotive engineering, particularly for its effectiveness in selecting materials based on mechanical and structural integrity requirements. Multi-Criteria Decision Analysis (MCDA) methods are also increasingly applied to address the complexities of material selection involving multiple design criteria [45]. Common MCDA methods include TOPSIS, VIKOR, COPRAS, PROMETHEE, ELECTRE, and MOORA.
Necessity of the Research:
While the Ashby method is valuable for initial material screening based on performance indices, it has limitations in handling numerous selection criteria and lacks inherent material ranking capabilities. Furthermore, it does not comprehensively address trade-offs between technical, economic, and environmental aspects [43]. Existing applications of MCDA methods in material selection often rely on arbitrarily chosen parameters dictated by designer experience and may not systematically evaluate the underlying physical phenomena [44]. Therefore, there is a need for a more holistic and structured approach that integrates objective performance criteria with cost and environmental considerations for sustainable material selection in automotive lightweighting.
4. Research Purpose and Research Questions:
Research Purpose:
The primary research purpose is to explore and validate an innovative methodology for material selection in the automotive industry that promotes both lightweighting and sustainability. This methodology aims to overcome the limitations of traditional approaches by integrating the objective material performance criteria of the Ashby theory with the multi-criteria decision-making capabilities of the VIKOR method.
Key Research:
The key research focus is on the development and application of a hybrid methodology that combines the Ashby approach for initial material filtering based on mechanical performance indices with the VIKOR method for comprehensive material ranking. This integration allows for the simultaneous consideration of design, cost, and environmental aspects in the material selection process. The methodology is designed to emphasize the interaction between selection criteria and environmental impact, offering a holistic approach to material choice.
Research Hypotheses:
While not explicitly stated as formal hypotheses, the research operates under the premise that:
- Integrating the Ashby method and VIKOR analysis will provide a more robust and comprehensive methodology for material selection compared to using either method in isolation.
- The proposed hybrid methodology will enable a more balanced consideration of mechanical performance, cost-efficiency, and environmental footprint in automotive material selection.
- Applying the VIKOR method with Design Index, Cost Index, and Environmental Index derived from Ashby theory and LCA will lead to the identification of optimal and sustainable lightweight material solutions for automotive components.
5. Research Methodology
Research Design:
The research employs a hybrid methodology design, integrating two established methods: the Ashby method and the VIKOR method. The Ashby method is used for initial screening of materials based on performance indices related to mechanical properties. Subsequently, the VIKOR method is applied to rank the pre-selected materials based on multiple criteria, including Design Index (mass), Cost Index (production cost), and Environmental Index (Life Cycle Climate Change impact).
Data Collection Method:
The study utilizes data from the Granta Selector Database [64] for material properties, industrial process parameters, and environmental impact data. A case study from existing literature [68], concerning the re-design of a motor bracket of a C-segment electric car, is adopted to validate the proposed methodology. Impact Reduction Values (IRV) for the use phase environmental impact are calculated based on geographical relevance and driving cycles, using data from [65] and [66].
Analysis Method:
The VIKOR method is the primary analysis method. It ranks design solutions by calculating a single score (Qi) based on group utility (Si) and individual regret (Ri). These scores are derived from normalized values of the Design Index, Cost Index, and Environmental Index. Weighting criteria are applied to prioritize cost, design, and sustainability aspects. The Design Index is calculated using Ashby performance indices to estimate component mass. The Cost Index is calculated considering raw material cost, manufacturing process costs, and tooling costs [Equation 16]. The Environmental Index is calculated using LCA principles, encompassing raw material acquisition, use phase, and End-of-Life (EoL) stages [Equation 17].
Research Subjects and Scope:
The research focuses on material selection for automotive components, specifically a motor mounting bracket for a C-segment electric car. The scope is limited to the selection of materials and primary manufacturing processes for lightweight re-design, considering design performance, production cost, and environmental impact (Climate Change). The analysis considers a range of materials, including steels, aluminum alloys, and cast irons, and compatible industrial processes available in the Granta Selector Database.
6. Main Research Results:
Key Research Results:
The application of the hybrid Ashby-VIKOR methodology to the motor bracket case study resulted in a ranked list of 1316 viable lightweight design solutions. The top-ranked solution is a low alloy steel (AISI 9255) processed by press forming. This solution achieves a 44% mass reduction, 75% cost saving, and 61% reduction in Climate Change impact compared to the reference AISI 304 stainless steel bracket. Wrought steels, particularly low alloy steels produced by press forming, dominate the top rankings due to their favorable balance of mechanical properties and cost-effectiveness. Aluminum solutions offer greater mass reduction but are ranked lower due to higher raw material costs and embodied energy, leading to a less significant overall environmental benefit in this specific case study. Cast iron alternatives, while offering substantial cost reduction, are limited by their lower mechanical properties and mass reduction potential.
Analysis of presented data:
Figure 1 illustrates Ashby diagrams used for initial material screening, plotting material index ratios relevant to tensile/compression and torque bending loads. These diagrams visually represent the material database and facilitate the selection of materials meeting initial performance criteria. Figure 2 presents a comparison of the Design Index, Cost Index, and Environmental Index ratios for the top 20 ranked solutions relative to the baseline design. This visualization highlights the trade-offs between different design solutions in terms of mass reduction, cost, and environmental impact. The analysis reveals that for the top-ranked solutions (low alloy steels), all three indices are relatively aligned, indicating a balanced improvement across all criteria. For aluminum solutions, the Design Index is lower (better mass reduction), but Cost and Environmental Indices are higher, reflecting the cost and environmental trade-offs associated with aluminum.
Figure Name List:
![Figure 1. Ashby diagrams used for material selection: ferrous metal alloys are represented in green, non-ferrous metal alloys in purple and red, plastics in blue, and composite materials with both plastic and metal matrices in brown and orange. The black lines are the maximum deterioration of parameters [53].](https://castman.co.kr/wp-content/uploads/image-847-837x1024.webp)
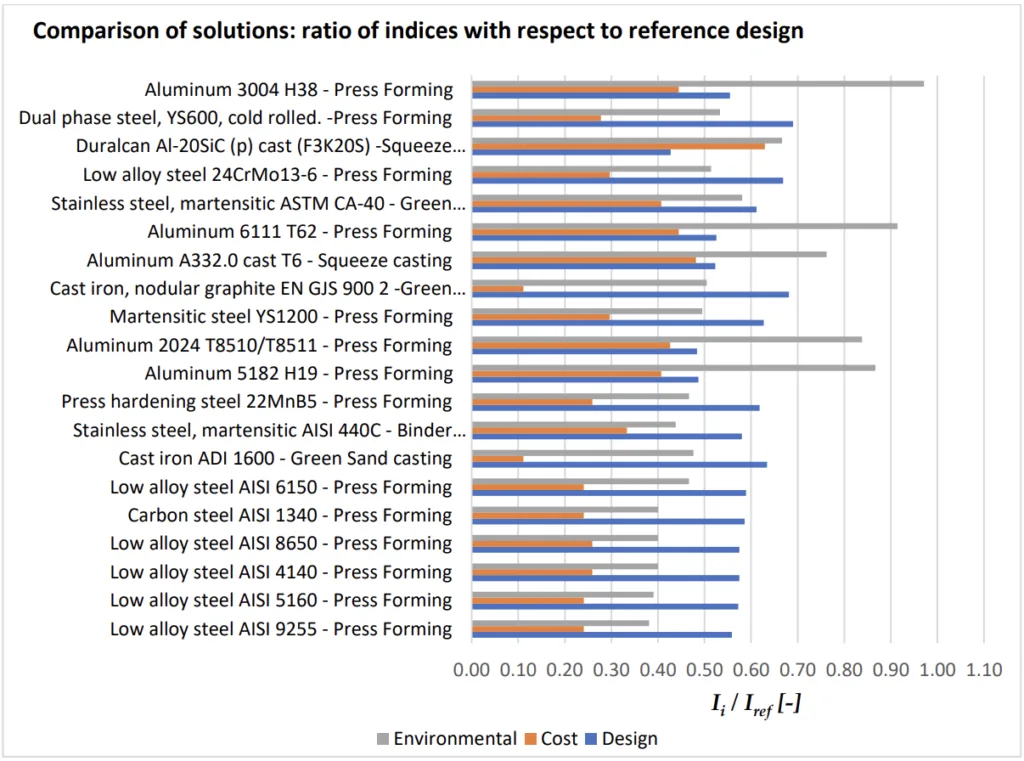
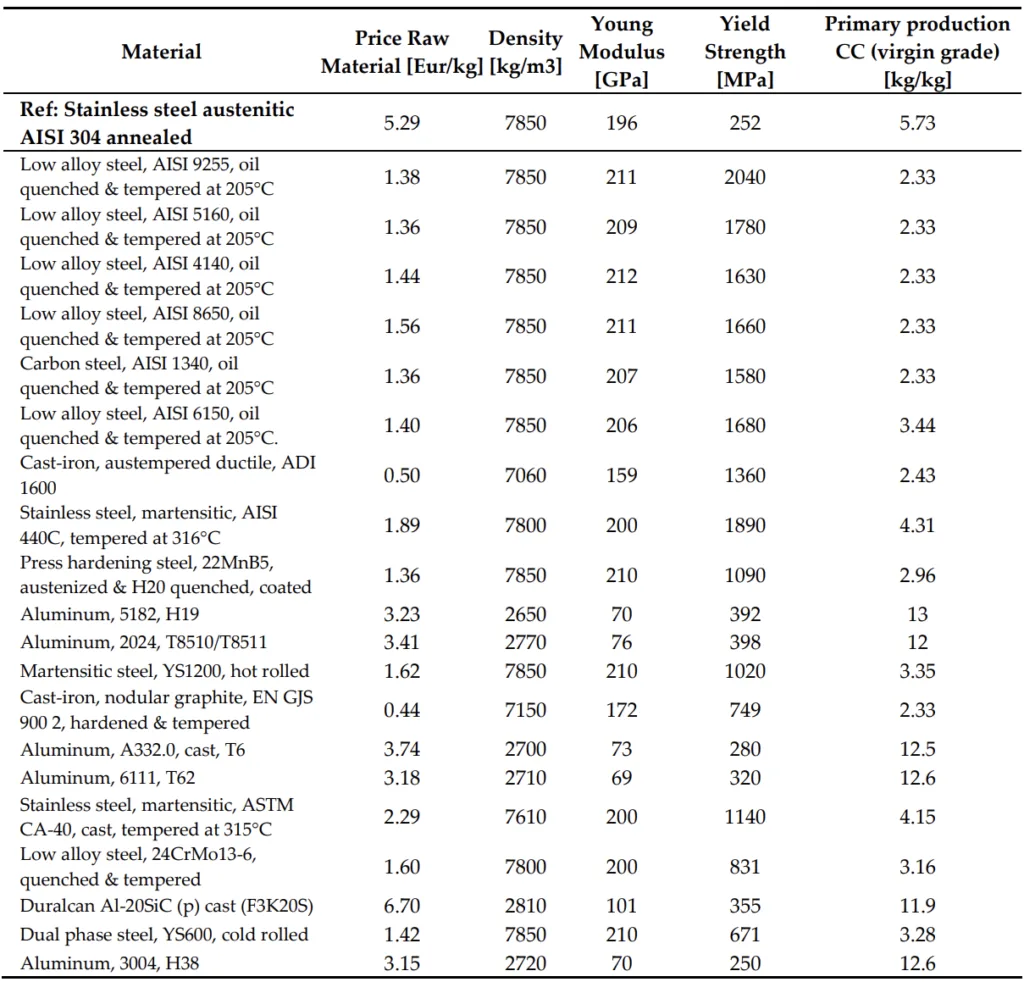
7. Conclusion:
Summary of Key Findings:
This study successfully developed and validated a hybrid methodology for material selection in automotive lightweighting by integrating the Ashby method and VIKOR analysis. The methodology was applied to a motor bracket re-design case study, demonstrating its ability to identify optimal lightweight solutions considering structural integrity, cost, and environmental sustainability. Low alloy steel processed by press forming emerged as the top-ranked material for the case study, offering significant improvements in mass, cost, and environmental impact compared to the baseline stainless steel design.
Academic Significance of the Study:
The research contributes to the field of material selection methodology by providing an innovative approach that bridges traditional performance-based selection with contemporary sustainability considerations. The integration of Ashby theory and VIKOR analysis offers a structured and objective framework for navigating complex material choices in eco-design. This hybrid methodology addresses the limitations of individual methods and provides a more holistic perspective on material selection in automotive engineering.
Practical Implications:
The developed methodology provides a valuable tool for automotive engineers and designers in the early stages of component re-design for lightweighting. It enables a systematic and data-driven approach to material selection, facilitating the identification of solutions that optimize not only component performance but also cost and environmental footprint. The methodology can be readily implemented using material databases and LCA tools, supporting informed decision-making in sustainable automotive design.
Limitations of the Study and Areas for Future Research:
The study is limited to the material selection phase and does not incorporate detailed design optimization. Future research could explore the integration of topological optimization with the proposed methodology to further enhance lightweighting potential and refine component design. Additionally, the economic and environmental analysis is limited to primary manufacturing processes and Climate Change impact; expanding the scope to include secondary processes, End-of-Life treatments in more detail, and a broader range of environmental impact categories would provide a more comprehensive assessment.
8. References:
- [1] IEA. CO2 Emissions in 2022. IEA 2023, Paris.
- [2] V.Ferreira et al. Technical and environmental evaluation of a new high performance material based on magnesium alloy reinforced with submicrometre-sized TiC particles to develop automotive lightweight components and make transport sector more sustainabl. J. Mater. Res. Technol. 2019, 8, pp. 2549-2564.
- [3] Commission European. White Paper: Roadmap to a Single European Transport Area-Towards a Competitive and Resource Efficient Transport System. European Commission: Brussels, Belgium. 2011, /* COM/2011/0144 final */.
- [4] Brooke L.; Evans H., Lighten up!, Automot. Eng., 2009, 117, pp. 16-22
- [5] M. Goede. Super Light Car-Lightweight construction thanks to a multi-material design and function integration. Eur. Transp. Res. Rev., 2009, 1, pp. 5-10.
- [6] V. Ferreira et al. Lightweight automotive components based on nano-diamond-reinforced aluminium alloy: A technical and environmental evaluation. Diam. Relat. Mater, 2019, 92, pp. 174-186.
- [7] Kelly J.C.; Sullivan J.L.; Burnham A.; Elgowainy A. Impacts of vehicle weight reduction via material substitution on life-cycle greenhouse gas emissions. Environ. Sci. Technol, 2015, 49, pp. 12535-12542.
- [8] JAGUAR LAND ROVER USING AEROSPACE TECHNOLOGY TO DEVELOP FUTURE LIGHTWEIGHT VEHICLES. https://media.jaguarlandrover.com/news/2020/10/jaguar-land-rover-using-aerospace-technology-develop-future-lightweight-vehicles. 22 October 2020.
- [9] The lightweight New A8 Unique mix of materials used in the next Audi milestone. https://press.audi.co.uk/en-gb/releases/52#:~:text=Picture%20caption,A8%20for%20the%20first%20time. 5 April 2017.
- [10] Stellantis Fosters Circular Economy Ambitions with Dedicated Business Unit to Power New Era of Sustainable Manufacturing and Consumption. https://www.stellantis.com/en/news/press-releases/2022/october/stellantis-fosters-circular-economy-ambitions-with-dedicated-business-unit-to-power-new-era-of-sustainable-manufacturing-and-consumption. 11 October 2022
- [11] C. Koffler, K. Rohde-Brandenburger. On the Calculation of Fuel Savings Through Lightweight Design in Automotive Life Cycle Assessments. Int. J. Life Cycle Assess., 2010, 15, pp. 128-135.
- [12] H.C. Kim, T.J. Wallington. Life Cycle Assessment of Vehicle Lightweight-ing: A Physics-Based Model to Estimate Use-Phase Fuel Consumption of Electrified Vehicles. Environ. Sci. Technol.,2016, 50, pp. 11226-11233.
- [13] L. Kroll et al. Lightweight Components for Energy-Efficient Machine Tools. CIRP J. Manuf. Sci. Technol., 2011, 4, pp. 148-160.
- [14] R. Neugebauer et al. Structure Principles of Energy Efficient Machine Tools. CIRP J. Manuf. Sci. Technol., 2011, 4, pp. 136-147.
- [15] Zhang W.; Xu J., Advanced lightweight materials for Automobiles: A review. Materials & Design, 2022, 221.
- [16] Mascarin A.; Hannibal T.; Raghunathan A.; Ivanic Z.; Francfort J. Vehicle Lightweighting: 40% and 45% Weight Savings Analysis: Technical Cost Modeling for Vehicle Lightweighting. United States: N. p.: s.n., 2015.
- [17] Tisza M.; Czinege I. Comparative study of the application of steels and aluminium in lightweight production of automotive parts. Int. J. Lightweight Mater. Manuf.,2018, 1, pp.229-238.
- [18] Mallick P.K.; Materials, Design and Manufacturing for Lightweight Vehicles; 2nd Edition., 2020.
- [19] Kumar D.; Kumar R.P.; Thakur L. A review on environment friendly and lightweight Magnesium-Based metal matrix composites and alloys. Materials Today: Proceedings, 2021, 38, pp.359-364.
- [20] Galán J. et al. Advanced high strength steels for automotive industry. Revista de metalurgia, 2012, 48,118.
- [21] Wazeer A.; Das A.; Abeykoon C.; Sinha A.; Karmakar A. Composites for electric vehicles and automotive sector: A review. Green Energy and Intelligent Transportation, 2023, 2.
- [22] Bourmaud A.; Fazzini M.; Renouard N.; Behlouli K.; Ouagne P. Innovating routes for the reused of PP-flax and PP-glass non woven composites: A comparative study. Polymer Degradation and Stability, 2018, 152, 259-271.
- [23] Elmarakbi A.; Azoti W. State of the Art on Graphene Lightweighting Nanocomposites for Automotive Applications. Experimental Characterization, Predictive Mechanical and Thermal Modeling of Nanostructures and their Polymer Composite; Marotti de Sciarra, F., Russo, P., 2018, pp. 1-23.
- [24] La Rosa A.D. et al; Biobased versus traditional polymer composites. A life cycle assessment perspective. J. Clean. Prod., 2014, 74, pp.135-144.
- [25] M. Schönemann, C. Schmidt, C. Herrmann, S. Thiede. Multi-level modeling and simulation of manufacturing systems for lightweight automotive components. Procedia CIRP, 2016, 41, pp. 1049-1054.
- [26] M.A. Iadicola, A.A. Creuziger, W.E. Luecke, D.K. Banerjee, T.H. Gnaupel-Herold. Automotive Lightweighting. NIST, 2008. Available online: https://www.nist.gov/programs-projects/automotive-lightweighting (accessed on 22 October 2020).
- [27] P.C. Priarone, A.R. Catalano, L. Settineri. Additive manufacturing for the automotive industry: on the life-cycle environmental implications of material substitution and lightweighting through re-design. Prog. Addit. Manuf., 2023, 8, pp. 1229-1240.
- [28] Dattilo, C.A.; Zanchi, L.; Del Pero, F.; Delogu, M. Sustainable design: an integrated approach for lightweighting components in the automotive sector. SDM-2017: 4th International Conference on Sustainable Design and Manufacturing, 2017.
- [29] Simoes, C.L.; Figueiredo de Sà, R.; Ribeiro, C.J.; Bernardo, P.; Pontes, A.J.; Bernardo, C.A. Environmental and economic performance of a car component: assessing new materials, processes and designs. J. Clean. Prod. 2016, 118, pp.105-117.
- [30] Delogu, M.; Zanchi, L.; Maltese, S.; Bonoli, A.; Pierini, M. Environmental and economic life cycle assessment of a lightweight solution for an automotive component: a comparison between talc-filled and hollow glass microspheres-reinforced polymer composites. J. Clean. Prod. 2016, 139, pp.548-560
- [31] Vita, A.; Castorani, V.; Germani, M.; Marconi, M. Comparative life cycle assessment of low-pressure RTM, compression RTM and high-pressure RTM manufacturing processes to produce CFRP car hoods. Procedia CIRP, 2019, 80, pp.352-357.
- [32] Zanchi, L.; Delogu, M.; Ierides, M.; Vasiliadis, H. Life cycle assessment and life cycle costing as supporting tools for EVs lightweight design. Sustain. Des. Manuf. 2016, 52, pp.335-348
- [33] Fiebig, S.; Sellschopp, J.; Manz, H.; Vietor, T.; Axmann, J.K.; Schumacher, A. Future challenges for topology optimization for the usage in automotive lightweight design technologies. 11th World Congress on Structural and Multidisciplinary Optimisation, Sydney, Australia, June 2015.
- [34] Işık, M. et al. Topology optimization and manufacturing of engine bracket using electron beam melting. J. Addit. Manuf. Technol., 2021, 1, pp.583.
- [35] Puri, P.; Compston, P.; Pantano, V. Life Cycle assessment of Australian automotive door skins. Int. J. Life Cycle Assess., 2009, 14, pp.420-428.
- [36] Delogu, M.; Del Pero, F.; Romoli, F.; Pierini, M. Life cycle assessment of a plastic air intake manifold. Int. J. Life Cycle Assess., 2015, 20, pp.1429-1443.
- [37] Poulikidou, S.; Jerpdal, L.; Björklund, A.; Åkermo, M. Environmental performance of self-reinforced composites in automotive applications. Case study on a heavy truck component. Mater. Des., 2016, 103, pp.321-329.
- [38] Inti, S.; Sharma, M.; Tandon, V. An approach for performing life cycle impact assessment of pavements for evaluating alternative pavement designs. Int. Conf. on Sust. Des., Eng. and Const, 2016,145, pp. 964-971.
- [39] Mayyas, A.T.; Qattawi, A.; Mayyas, A.R.; Omar, M.A. Life cycle assessment-based selection for a sustainable lightweight body-in-white design. Energy, 2012, 39, pp.412-425.
- [40] Ashby, M.F.; Johnson, K. Materials and Design: The Art and Science of Material Selection in Product Design, 2nd ed.; Butterworth-Heinemann: Oxford, UK, 2013.
- [41] Camargo, D.Z. et al. Selection of Materials for Weight Reduction in Sports Cars. Adv. Mater. Res., 2019, 1152, pp.73-82.
- [42] Ashby, F.; Multi-Objective Optimization in Material Design and Selection. Acta Mater. 2000, 48, pp.359-369.
- [43] Lewis, G.M. et al. Green Principles for Vehicle Lightweighting. Environ. Sci. Technol., 2019, 53, pp.4063-4077.
- [44] Rao, R.V.; Patel, B.K. A subjective and objective integrated multiple attribute decision making method. Mater. Des., 2010, 37, pp.4738-4747.
- [45] Stojčić, M., et al. Application of MCDM Methods in Sustainability Engineering: A Literature Review 2008-2018. Symmetry, 2019, 11, 3.
- [46] Hwang, C.L.; Yoon, K. Methods for Multiple Attribute Decision Making. In: Multiple Attribute Decision Making. Lecture Notes in Economics and Mathematical Systems, vol. 186. Springer, Berlin, Heidelberg, 1981.
- [47] Opricovic, S. Multicriteria optimization of civil engineering systems. Faculty of Civil Engineering: Belgrade, Serbia, 1998; pp. 5-21.
- [48] Chatterjee, P.; Chakraborty, S. A comparative analysis of VIKOR method and its variants. Decis. Sci. Lett., 2016, 5, pp.469-486.
- [49] Zavadskas, E.K.; Kaklauskas, A.; Šarka, S. The new method of multicriteria evaluation of projects. Tech. and Economic Dev. of Ec., 1996, 1(3), pp.131–139.
- [50] Mousavi-Nasab, S.H.; Sotoudeh-Anvari, A. A comprehensive MCDM-based approach using TOPSIS, COPRAS, and DEA as an auxiliary tool for material selection problems. Mater. Des., 2017, 121, pp.237-253.
- [51] Brans, J.P.; Nadeau, R.; Landry, M. L'ingénierie de la décision. Elaboration d'instruments d'aide à la décision. La méthode PROMETHEE. In: L'Aide à la Décision: Nature, Instruments et Perspectives d'Avenir, 1982, pp.183-213.
- [52] Brans, J.P.; De Smet, Y. PROMETHEE Methods. In: Greco, S.; Ehrgott, M.; Figueira, J. (eds) Multiple Criteria Decision Analysis. International Series in Operations Research & Management Science, vol. 233. Springer, New York, NY, 2016.
- [53] Roy, B. Classement et choix en présence de points de vue multiples. Rev. Fr. Inf. Rech. Opér., 1968, 2(8), pp.57-75.
- [54] Figueira, J.R.; Mousseau, V.; Roy, B. ELECTRE Methods. In: Greco, S.; Ehrgott, M.; Figueira, J. (eds) Multiple Criteria Decision Analysis. International Series in Operations Research & Management Science, vol. 233. Springer, New York, NY, 2016.
- [55] Brauers, W.K.M. Optimization Methods for a Stakeholder Society. A Revolution in Economic Thinking by Multiobjective Optimization. Kluwer Academic Publishers, Boston, 2004.
- [56] Chakraborty, S. Applications of the MOORA method for decision making in manufacturing environment. Int. J. Adv. Manuf. Technol., 2011, 54, pp.1155–1166.
- [57] Kumar, R.; Ray, A. Selection of material for optimal design using multi-criteria decision making. Procedia Mater. Sci., 2014, 6, pp.590-596.
- [58] Giorgetti, A.; Cavallini, C.; Arcidiacono, G.; Citti, P. A mixed C-VIKOR fuzzy approach for material selection during design phase: a case study in valve seats for high performance engine. Int. J. Appl. Eng. Res., 2017, 12, pp.3117-3129.
- [59] Jahan, A.; Mustapha, F.; Ismail, M.; Sapuan, S.; Bahraminasab, M. A comprehensive VIKOR method for material selection. Mater. Des., 2011, 32, pp.1215-1221.
- [60] Manalo, M.V.; Magdaluyo, E.R. Integrated DLM-COPRAS method in material selection of laminated glass interlayer for a fuel-efficient concept vehicle. World Congress on Engineering, London, UK, 2018; Vol. 2.
- [61] Gul, M.; Celik, E.; Gumus, A.; Guneri, A. A fuzzy logic based PROMETHEE method for material selection problems. Beni-Suef Univ. J. Basic Appl. Sci., 2018, 7, 68-79.
- [62] Aziz, C.; Taleb, M.; Zakia, R.; Rajaa, B.; El Haji, M. Electre multicriteria analysis for choosing material concerned by the corrosion problem. J. Appl. Sci. Environ. Stud., 2020, 3, pp.132-146.
- [63] Sen, B.; Bhattacharjee, P.; Mandal, U. A comparative study of some prominent multi criteria decision making methods for connecting rod material selection. Perspect. Sci.,2016, 8, pp.547-549.
- [64] ANSYS. Available online: https://www.ansys.com/it-it/products/materials/granta-selector (accessed on 17 July 2024).
- [65] Del Pero, F.; Berzi, L.; Antonacci, A.; Delogu, M. Automotive Lightweight Design: Simulation Modeling of Mass-Related Consumption for Electric Vehicles. Machines ,2020, 8, 3.
- [66] Antonacci, A.; Del Pero, F.; Baldanzini, N.; Delogu, M. Holistic eco-design tool within automotive field. IOP Conf. Ser. Mater. Sci. Eng. 2022, 1214
- [67] Więckowski, J.; Sałabun, W. How the normalization of the decision matrix influences the results in the VIKOR method? Procedia Comput. Sci., 2020, 176, pp.2222-2231.
- [68] Celik, H.K. et al. Strength-Based Design Analysis of a Damaged Engine Mounting Bracket Designed for a Commercial Electric Vehicle. J. Fail. Anal. Prev., 2021, 21, pp.1315-1322.
- [69] Del Pero, F.; Berzi, L.; Dattilo, C.A.; Delogu, M. Environmental sustainability analysis of Formula-E electric motor. Proc. Inst. Mech. Eng. Part D: J. Automob. Eng., 2021, 235, pp.303-332.
- [70] Ecoinvent. Available online: https://ecoinvent.org/ (accessed on 17 July 2024).
9. Copyright:
- This material is Edoardo Risaliti, Francesco Del Pero, Gabriele Arcidiacono, Paolo Citti's paper: Based on "Optimizing Lightweight Material Selection in Automotive Engineering: A Hybrid Methodology Incorporating Ashby's Method and VIKOR Analysis".
- Paper Source: doi: 10.20944/preprints202411.1992.v1
This material was summarized based on the above paper, and unauthorized use for commercial purposes is prohibited.
Copyright © 2025 CASTMAN. All rights reserved.