This article introduces the paper 'New Die Casting Alloy with High Ductility in As Cast State for Automotive Structural Components' published by 'Journal of the Korea Foundry Society'.
1. Overview:
- Title: New Die Casting Alloy with High Ductility in As Cast State for Automotive Structural Components
- Author: Shiichiro Watanabe and Rüdiger Franke
- Publication Year: January 2008
- Publishing Journal/Academic Society: Journal of the Korea Foundry Society
- Keywords: Die Casting Alloy, High Ductility, As Cast State, Automotive Structural Components, Al-Si-Mg alloy, Ageing behavior, Self piercing rivet
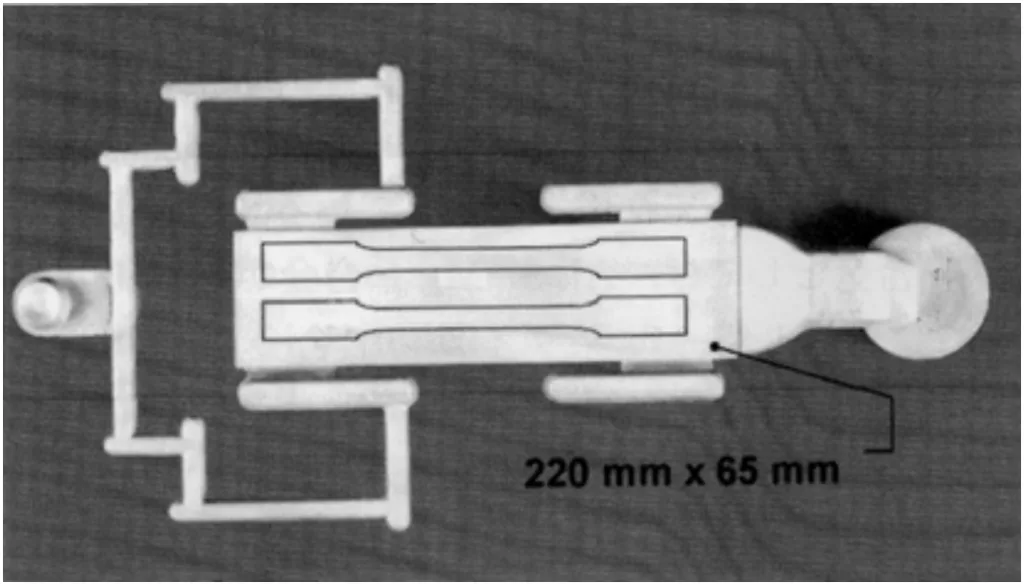
2. Abstracts or Introduction
In the pursuit of mitigating global warming, the automotive industry is persistently challenged to enhance fuel efficiency by reducing vehicle weight. A pivotal strategy in achieving this objective is the substitution of ferrous materials with lightweight aluminum alloys, thereby facilitating vehicle weight reduction [1,2]. Recent advancements in high-quality die casting technologies, including vacuum die casting [3], coupled with the development of high-performance die casting alloys exhibiting both high strength and ductility, have enabled the adoption of large die-cast components as structural elements in passenger vehicles [4,5]. Among high-quality die casting alloys, Al-Si-Mg systems are predominantly utilized. These Al-Si-Mg die casting alloys offer a versatile range of mechanical properties through precise control of magnesium content and heat treatment, effectively meeting the diverse performance requirements of various automotive structural components [6].
However, the widespread application of high-quality die casting alloys in automotive body structures has brought forth inherent limitations and new demands. For instance, conventional Al-Si-Mg die casting alloys necessitate solution heat treatment post-casting to achieve the requisite high ductility, specifically an elongation exceeding 10%, crucial for structural components. This heat treatment introduces process complexities and potential distortions, necessitating additional straightening operations, which pose significant manufacturing challenges. Consequently, the industry demands alloys capable of delivering high ductility in the as-cast condition, eliminating the need for heat treatment. Furthermore, the increasing power output of modern engines, particularly diesel engines, leads to elevated operating temperatures due to engine heat radiation. This thermal exposure can induce changes in the mechanical properties of Al-Si-Mg die casting components over prolonged service periods, raising concerns about long-term reliability. Additionally, advancements in automotive assembly necessitate the development of robust joining technologies, including methods for joining dissimilar materials.
In response to these evolving demands from the automotive industry, and considering the thermal exposure from engine heat, this research endeavors to develop a die casting alloy that exhibits minimal age hardening and achieves high elongation in the as-cast state. Simultaneously, the alloy is designed to possess excellent castability. Furthermore, the study explores the feasibility of self-piercing rivet joining as a potential technique for joining this alloy with dissimilar materials.
3. Research Background:
Background of the Research Topic:
The automotive sector is under constant pressure to improve fuel efficiency and reduce CO2 emissions, primarily driven by global warming concerns. Lightweighting of vehicles through material substitution, specifically replacing steel components with aluminum alloys, is a key strategy to achieve these goals [1,2].
Status of Existing Research:
Al-Si-Mg alloys are established materials for high-quality die casting in automotive structural applications [4,5,6]. However, these alloys typically require solution heat treatment to attain the desired high ductility (elongation > 10%) for structural integrity. This heat treatment step adds complexity, cost, and potential distortion issues to the manufacturing process. Moreover, the operational environment in engine compartments exposes these alloys to elevated temperatures, leading to concerns about long-term property degradation due to aging of the Al-Si-Mg system.
Necessity of the Research:
To address the limitations of current Al-Si-Mg die casting alloys, there is a critical need for a novel alloy that can provide:
- High ductility in the as-cast condition, eliminating the need for costly and complex heat treatments.
- Stability of mechanical properties under elevated temperature service conditions, resisting age hardening.
- Excellent castability to produce complex automotive structural components with thin walls.
- Compatibility with advanced joining techniques, such as self-piercing riveting, for multi-material assemblies.
4. Research Purpose and Research Questions:
Research Purpose:
The primary objective of this research is to develop a new die casting alloy tailored for automotive structural components that exhibits:
- High ductility in the as-cast state (Elongation > 10%).
- Moderate yield strength (Yield Strength > 120 MPa).
- No long-term age hardening behavior under elevated temperature exposure.
- Good castability for complex designs with thin wall sections.
Furthermore, the research aims to investigate the applicability of self-piercing rivet (SPR) joining for this newly developed alloy.
Key Research:
To achieve the research purpose, the following key investigations were conducted:
- Effect of Magnesium (Mg) Content on Ageing Behavior: Systematically varying Mg content in Al-Si-Mg alloys to evaluate its influence on long-term aging and mechanical property changes at elevated temperatures.
- Effect of Transition Element Addition (Mn, Mo, Zr) on Mechanical Properties: Exploring the impact of adding transition elements, specifically Manganese (Mn), Molybdenum (Mo), and Zirconium (Zr), on enhancing the yield strength of the alloy while maintaining high ductility in the as-cast state.
- Characterization of Developed Alloy in As-Cast Condition: Analyzing the mechanical properties (tensile strength, elongation) and microstructure of the optimized alloy in the as-cast state, considering the effect of die casting thickness (cooling rate).
- Castability Assessment in Practical Die Casting: Evaluating the castability of the developed alloy in a practical die casting environment, focusing on achieving uniform mechanical properties across complex shapes.
- Feasibility Study of Self Piercing Rivet (SPR) Joining: Investigating the feasibility and optimal conditions for joining the developed as-cast alloy using self-piercing rivet technology, particularly for joining with dissimilar materials like aluminum sheet alloys.
Research Hypotheses:
- Mg Content and Age Hardening: Age hardening in Al-Si-Mg alloys is primarily attributed to the precipitation of Mg₂Si. Reducing Mg content will minimize age hardening and improve property stability at elevated temperatures.
- Transition Element Strengthening: The addition of transition elements like Mo and Zr will enhance the yield strength of the Al-Si-Mg alloy through mechanisms such as precipitation hardening or grain refinement, without significantly compromising ductility.
- As-Cast High Ductility Alloy Development: By carefully controlling the alloy composition, particularly limiting Mg content and incorporating Mo and Zr, a die casting alloy can be developed that achieves high ductility in the as-cast state, eliminating the need for solution heat treatment.
- SPR Joining Feasibility: With optimized die and process parameters, self-piercing rivet joining is a viable method for joining components made from the developed as-cast die casting alloy, enabling multi-material design solutions.
5. Research Methodology
Research Design:
This research employed an experimental design focused on alloy development and characterization. The study systematically investigated the effects of compositional variations and processing parameters on the mechanical properties and microstructure of Al-Si-Mg die casting alloys.
Data Collection Method:
- Tensile Testing: Mechanical properties, specifically yield strength and elongation, were evaluated using tensile tests on die-cast specimens. At least 10 specimens were tested for each condition, and average values were reported.
- Microstructural Analysis: Scanning Electron Microscopy (SEM) was utilized to characterize the microstructure of the alloys, focusing on the morphology and distribution of eutectic silicon and intermetallic phases.
- Initial Bubble Test: Melt quality was assessed using the initial bubble test to ensure low gas content in the molten metal prior to die casting. The target gas content was below 1 ml/100g Al.
- Die Casting Trials: Experimental alloys with varying compositions (Mg, Mn, Mo, Zr content) were produced using a 3900 kN Buhler B-machine high-pressure die casting machine. Die casting plates with thicknesses of 2, 3, 4, and 6 mm were cast to investigate the effect of cooling rate. Practical die casting trials were also conducted using a 20MN high vacuum die casting machine to produce complex shaped components for castability assessment.
- Self-Piercing Rivet (SPR) Joining Trials: SPR joining experiments were performed using as-cast plates of the developed alloy and AA5052 aluminum alloy sheets to evaluate joining feasibility and optimize process parameters.
Analysis Method:
The collected data were analyzed using comparative methods. Mechanical property data (yield strength, elongation) were compared across different alloy compositions, aging conditions, and die casting thicknesses to determine the effects of these variables. Microstructural observations were correlated with mechanical property data to understand the underlying mechanisms influencing alloy performance. Castability was assessed based on the uniformity of mechanical properties in practical die casting components and the absence of casting defects. The success of SPR joining was evaluated based on visual inspection for defects and joint integrity.
Research Subjects and Scope:
The research focused on experimental Al-Si-Mg based die casting alloys with systematic variations in:
- Magnesium (Mg) content: Ranging from 0.003% to 0.1% to investigate aging behavior.
- Manganese (Mn) content: Ranging from 0.39% to 1.17% to assess its effect on mechanical properties.
- Molybdenum (Mo) and Zirconium (Zr) content: Added individually and in combination (up to 0.21% and 0.15% respectively) to evaluate their impact on yield strength.
- Die casting thickness: Varied from 2 mm to 6 mm to study the effect of cooling rate on mechanical properties.
- Joining materials: Developed alloy as-cast plates were joined with AA5052 aluminum alloy sheets in SPR joining trials.
6. Main Research Results:
Key Research Results:
- Magnesium Content and Ageing: The study revealed that Mg content significantly influences the age hardening behavior of Al-Si-Mg alloys. Increasing Mg content up to 0.1% resulted in a notable increase in yield strength after aging at 393K for 1000 hours, indicating age hardening due to Mg₂Si precipitation (Fig. 2). To minimize age hardening for components exposed to engine heat, Mg content should be limited to 0.04% or less.
- Transition Element Addition (Mo and Zr): The addition of Mn alone (up to 1.2%) did not significantly improve yield strength (Fig. 3). However, the combined addition of Molybdenum (Mo) and Zirconium (Zr), each at 0.15%, to the Al-10%Si-0.5%Mn alloy resulted in a 10% increase in yield strength without compromising elongation (Fig. 4). This synergistic effect of Mo and Zr was more effective than individual additions.
- Developed Alloy Properties: The optimized alloy composition (Al-10%Si-0.5%Mn-0.15%Mo-0.15%Zr-0.015%Sr) achieved a high elongation of 12-13% and a yield strength exceeding 120 MPa in the as-cast state. This alloy composition effectively meets the target requirements for high ductility and moderate strength without heat treatment.
- Castability and Elongation Distribution: Practical die casting trials demonstrated that the developed alloy exhibits excellent castability, producing components with uniform and high elongation values across different locations, including the final filling areas (Table 7). This indicates reduced susceptibility to casting defects and improved melt fluidity compared to conventional Al-Si-Mg alloys.
- Self-Piercing Rivet (SPR) Joining Feasibility: SPR joining of the developed as-cast alloy with AA5052 aluminum sheets was successfully achieved by optimizing the rivet die design and process parameters (Fig. 8). Using a flat die with a cone-shaped side (taper die) for the rivet die and adjusting the die depth for the upper plate (die casting material) enabled successful SPR joining without cracking.
Analysis of presented data:
- Figure 2. Influence of Magnesium content on long term ageing of Al-10%Si-0.5% Mn alloy die casting. This figure illustrates that increasing Mg content leads to a greater increase in yield strength after aging, indicating age hardening. However, the change in elongation is minimal with varying Mg content.
- Figure 3. Effect of Manganese content on mechanical prooerty of Al-10%Si-Mn alloy die casting. This figure shows that increasing Mn content up to 1.2% does not significantly improve the yield strength of the Al-10%Si-Mn alloy.
- Figure 4. Effect of Molybdenum and Zirconium content on mechanical prooerty of Al-10%Si-0.5%Mn alloy die casting. This figure demonstrates that the combined addition of Mo and Zr effectively increases the yield strength of the Al-10%Si-0.5%Mn alloy.
- Figure 5. Microstructure of Strontiun modified Al-Si-Mg alloy and developed alloy die casting. This figure compares the microstructure of a conventional Sr-modified Al-Si-Mg alloy with the developed alloy. The developed alloy exhibits a finer eutectic silicon structure, attributed to the reduced Mg content and Sr modification.
- Figure 6. Scanning electron microstructure of eutectic silicon. SEM images further illustrate the finer eutectic silicon morphology in the developed alloy compared to the conventional Al-Si-Mg-Mg alloy.
- Figure 7. Mechanical property of developed alloy die casting in as cast state versus wall thickness. This figure shows the effect of die casting wall thickness (cooling rate) on mechanical properties. Yield strength increases with decreasing wall thickness (faster cooling), while elongation shows a slight increase with increasing wall thickness.
- Figure 8. Self pierce riveting trial of developed alloy plate in as cast state. This figure demonstrates the successful self-piercing rivet joining of the developed as-cast alloy plate (4mm) and an AA5052 aluminum alloy sheet (1.5mm) without cracking.
Figure Name List:
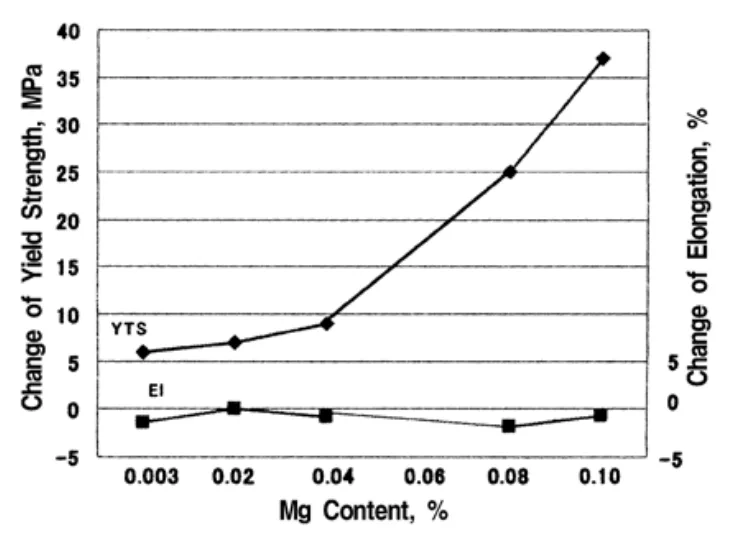
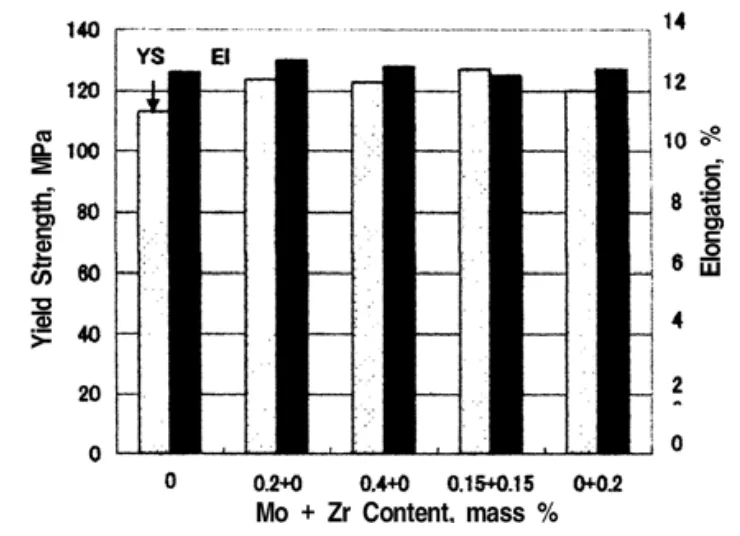
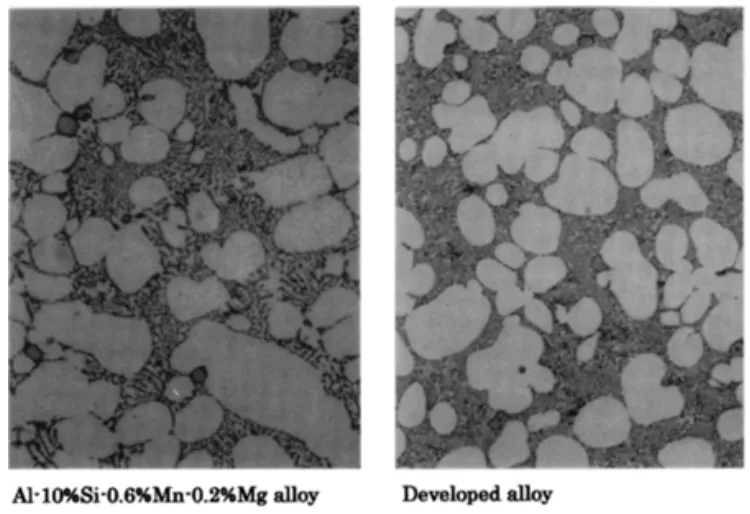
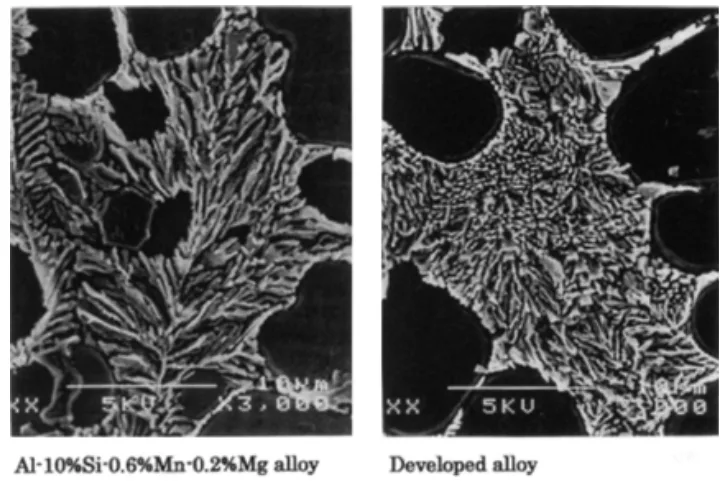
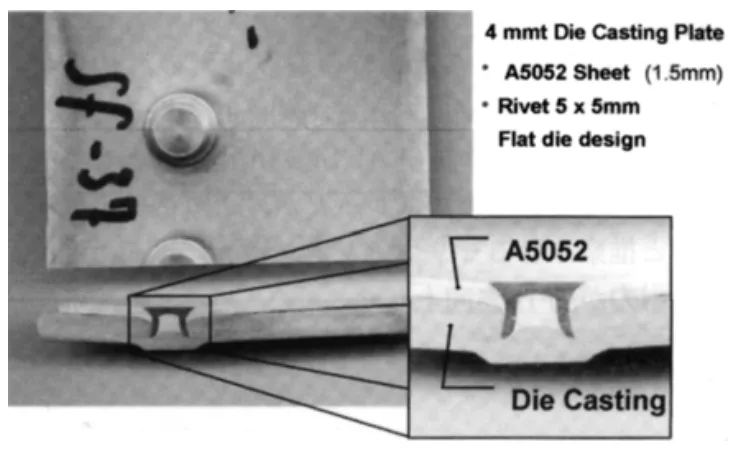
- Fig. 1. High pressure die casting plate for tensile test.
- Fig. 2. Influence of Magnesium content on long term ageing of Al-10%Si-0.5% Mn alloy die casting.
- Fig. 3. Effect of Manganese content on mechanical prooerty of Al-10%Si-Mn alloy die casting.
- Fig. 4. Effect of Molybdenum and Zirconium content on mechanical prooerty of Al-10%Si-0.5%Mn alloy die casting.
- Fig. 5. Microstructure of Strontiun modified Al-Si-Mg alloy and developed alloy die casting.
- Fig. 6. Scanning electron microstructure of eutectic silicon.
- Fig. 7. Mechanical property of developed alloy die casting in as cast state versus wall thickness.
- Fig. 8. Self pierce riveting trial of developed alloy plate in as cast state.
7. Conclusion:
Summary of Key Findings:
This research successfully developed a new high-ductility die casting alloy for automotive structural components. The key features of this alloy are:
- Composition: Al-10%Si-0.5%Mn-0.15%Mo-0.15%Zr-0.015%Sr, characterized by a limited Mg content (<0.04%) and the addition of Mo and Zr.
- Mechanical Properties: Achieves high elongation (>10%) and moderate yield strength (>120 MPa) in the as-cast state, eliminating the need for solution heat treatment.
- Ageing Resistance: Exhibits minimal age hardening and stable mechanical properties under elevated temperature exposure, suitable for engine compartment applications.
- Castability: Demonstrates excellent castability, producing uniform and high-quality die castings with complex shapes and thin walls.
- Joinability: Enables self-piercing rivet joining with dissimilar materials, facilitating multi-material automotive designs.
Academic Significance of the Study:
This study contributes to the field of die casting metallurgy by demonstrating the feasibility of developing high-ductility as-cast aluminum alloys through strategic compositional design. The research provides valuable insights into:
- The critical role of Mg content in controlling age hardening in Al-Si-Mg alloys.
- The synergistic strengthening effect of Mo and Zr additions in enhancing yield strength without sacrificing ductility.
- The microstructure-property relationships in as-cast die casting alloys, particularly the influence of eutectic silicon morphology.
Practical Implications:
The developed die casting alloy offers significant practical benefits for the automotive industry:
- Reduced Manufacturing Costs: Eliminating the solution heat treatment process simplifies production, reduces energy consumption, and lowers manufacturing costs.
- Improved Component Performance: High as-cast ductility enhances energy absorption and crashworthiness of structural components. Ageing resistance ensures long-term reliability in demanding thermal environments.
- Enabling Lightweighting and Multi-Material Design: The alloy facilitates the production of lightweight automotive structures and enables the use of self-piercing rivet joining for efficient assembly of multi-material components.
Limitations of the Study and Areas for Future Research:
While this study successfully developed a promising new alloy, some limitations and areas for future research exist:
- Microstructural Characterization of Mo and Zr Phases: The exact nature and distribution of Mo and Zr-containing phases in the microstructure require further investigation to fully understand their strengthening mechanisms. Advanced techniques like TEM analysis could be employed.
- Optimization of SPR Joining Process: Further research is needed to optimize the SPR joining process parameters for a wider range of joint configurations and material thicknesses.
- Exploration of Other Joining Technologies: Investigating the suitability of the developed alloy for other advanced joining technologies, such as adhesive bonding or friction stir welding, would broaden its application potential.
- Long-Term Performance Evaluation: Extended long-term performance evaluations under real-world automotive operating conditions are necessary to fully validate the alloy's durability and reliability.
8. References:
9. Copyright:
- This material is "Rüdiger Franke"'s paper: Based on "New Die Casting Alloy with High Ductility in As Cast State for Automotive Structural Components".
- Paper Source: https://www.researchgate.net/publication/264061492
This material was summarized based on the above paper, and unauthorized use for commercial purposes is prohibited.
Copyright © 2025 CASTMAN. All rights reserved.