This article introduces the paper ['Modeling alloy and energy utilization in high volume die casting'] published by ['Springer-Verlag Berlin Heidelberg'].
1. Overview:
- Title: Modeling alloy and energy utilization in high volume die casting
- Author: Jerald R. Brevick, Austin F. Mount-Campbell, Clark A. Mount-Campbell, Alan J. Horn
- Publication Year: 2014
- Publishing Journal/Academic Society: Clean Techn Environ Policy
- Keywords: Aluminum, Automobile industry, Energy consumption, Material selection, Process model
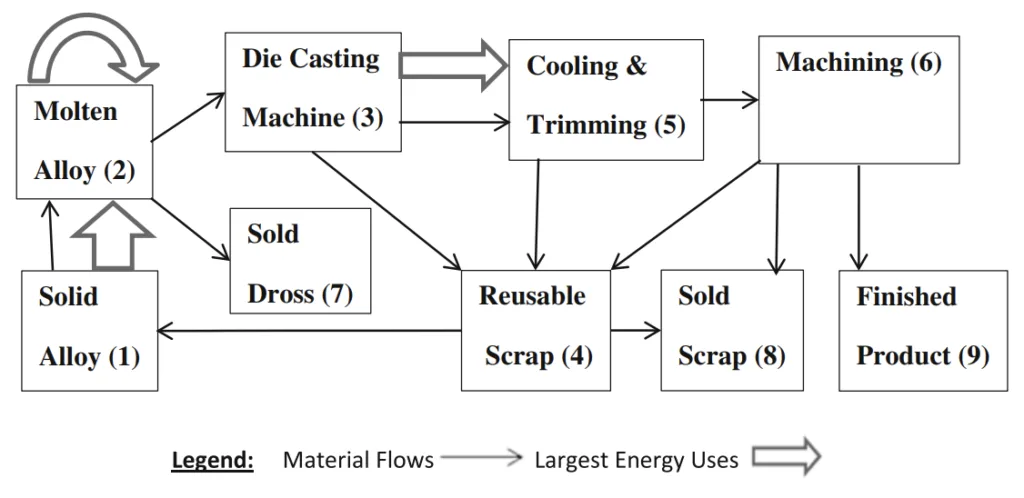
2. Abstracts or Introduction
Die casting is recognized as a high-technology manufacturing process characterized by significant capital and energy investment. While die casting presents notable economic and environmental advantages, its inherent high energy consumption necessitates careful examination. Operational and design decisions within the die casting process exert considerable influence over total energy utilization and the emission of equivalent carbon dioxide. To address this, an absorbing-state Markov chain (ASMC) model is proposed to represent the material flow and quantify resource consumption in the most energy-intensive stages of the process. This model is designed to aid decision-makers in evaluating design options, investment strategies, and operational adjustments, including equipment procurement. The paper specifies the data elements required for model implementation and the necessary reference data for analyzing energy-related emissions. The practical application of the model is demonstrated through a historical case study focusing on a specific product design decision. Furthermore, the prescriptive applications of the model, derived from this case study, are explored, highlighting the model's versatility in supporting diverse analyses.
This article concentrates on high-volume, low-mix die casting operations, prevalent in sectors like the automotive industry, where foundries typically maintain continuous operation with minimal changeovers. Die cast components are ubiquitous, found in "90% of manufactured products in the United States (NADCA 2012)". The die casting process offers numerous benefits, including environmental advantages such as the long service life and recyclability of castings. A significant portion of waste metal within die casting operations is reutilized through remelting. Aluminum alloys are the predominant die cast metals, with "a majority of the aluminum used in American die casting operations is post-consumer recycled (NADCA 2012)". The capacity to reliably produce high-volume, high-quality products using recycled materials underscores the enduring prominence of die casting in manufacturing.
However, these advantages are counterbalanced by substantial energy costs. Die casting operations are notably energy-intensive, primarily due to the high temperatures required for alloy melting and the considerable pressure needed for injecting the alloy into the die. Injection pressures typically range "between 14,000 and 140,000 kPa (Groover 2004)". In 2002, die casting processes in the United States consumed an estimated "100 trillion kJ of energy (Eppich and Naranjo 2007)", an energy quantity comparable to the annual energy consumption of all residential and commercial buildings in Philadelphia. This high energy consumption, coupled with substantial capital equipment costs, underscores the critical importance of strategic investment and operational decisions in die casting.
3. Research Background:
Background of the Research Topic:
Die casting is a manufacturing process recognized for its high energy intensity. The significant energy consumption associated with die casting operations is a critical concern, necessitating strategies for optimization. Given the widespread application of die casting, particularly in industries like automotive manufacturing, there is a pressing need to address and mitigate its energy footprint.
Status of Existing Research:
Prior research acknowledges the substantial energy demands of die casting processes. Existing studies have focused on quantifying energy consumption within die casting and identifying areas for potential energy reduction. However, the complexity and interconnectedness of die casting operations necessitate a system-wide perspective for effective decision-making.
Necessity of the Research:
To effectively evaluate the impact of operational and design choices on energy consumption within die casting, a comprehensive, system-wide model is essential. Traditional experimental approaches are often impractical due to the scale and complexity of these operations. Therefore, a modeling approach is required to compare different operating conditions and assess the consequences of various decisions. This research addresses this need by introducing an absorbing-state Markov chain (ASMC) model, representing the first peer-reviewed application of ASMC methodology to die casting operations, offering a novel tool for systematic analysis and optimization.
4. Research Purpose and Research Questions:
Research Purpose:
The primary research purpose is to develop and demonstrate an absorbing-state Markov chain (ASMC) model tailored to die casting processes. This model aims to analyze alloy and energy utilization within high-volume die casting settings. Ultimately, the research seeks to provide a decision-support tool for stakeholders to evaluate the implications of various design, investment, and operational decisions on energy consumption and material efficiency.
Key Research:
The key research endeavors include:
- Formulation of an ASMC model to accurately represent the die casting process.
- Identification of critical parameters and data elements necessary for effective model implementation and operation.
- Validation and illustration of the model's utility through a real-world case study derived from the automotive industry.
- Application of the model to analyze energy consumption patterns and associated emissions within the die casting process.
Research Hypotheses:
While not explicitly stated as formal hypotheses, the research is guided by the implicit assumptions that:
- An ASMC model can provide a valid and effective representation of the complex dynamics of a die casting process.
- The developed model can be effectively utilized to quantify and analyze energy consumption and alloy utilization throughout the die casting lifecycle.
- The insights derived from the model can offer valuable support for informed decision-making in the context of die casting operations, leading to process optimization and resource efficiency.
5. Research Methodology
Research Design:
The research employs a model-based approach centered on the development of an absorbing-state Markov chain (ASMC) model. To demonstrate the practical applicability and utility of this model, a case study methodology is adopted. The research design involves analyzing both baseline operational scenarios and alternative scenarios through the lens of the ASMC model to assess and compare their performance.
Data Collection Method:
Data for this study is sourced from a case study originally documented by Butler (2008), supplemented by data collected directly from die casting operations. The dataset encompasses critical parameters such as alloy loss percentages, scrap rates (platform and reusable), alloy quantity per shot, casting weights (after trimming and finished), machining rejection rates, energy consumption metrics, and various operational parameters pertinent to die casting. Data sources include prior publications by Butler (2008) and Brevick et al. (2004), industry reports like Kim et al. (2010), and environmental datasets from the EPA.
Analysis Method:
The core analytical method is Markov chain analysis, utilizing matrix-based calculations. This involves computing the expected number of visits to each state within the ASMC model. Based on these calculations, estimations are derived for alloy consumption, energy utilization, and associated emissions. The analysis further includes a comparative assessment of different operational scenarios—baseline versus alternatives—to quantify the impact of changes on energy and material efficiency.
Research Subjects and Scope:
The research focuses on high-volume, low-mix die casting operations, with a particular emphasis on applications within the automotive sector. The scope is further defined by considering die casting processes involving aluminum and magnesium alloys. The illustrative case study specifically examines the production of cam covers for a four-cylinder automotive engine, providing a concrete example within the defined scope.
6. Main Research Results:
Key Research Results:
The research successfully developed an ASMC model comprising nine distinct states that effectively represent the die casting process flow, as depicted in "Fig. 1 Process flow of die casting operation". Key transition probabilities within the model were identified and quantified, along with the necessary data inputs for model parameterization. The model's practical application was demonstrated through a case study comparing the production of aluminum and magnesium cam covers. Alternative operational scenarios, including the use of a new cover gas for magnesium and the implementation of molten alloy supply for aluminum, were analyzed using the model. The analysis quantified energy consumption and ECO2 emissions for each scenario, revealing that the adoption of alternative cover gases and molten alloy supply can lead to significant reductions in ECO2 emissions.
Analysis of presented data:
The ASMC model facilitates the calculation of expected visits to each defined state, enabling the quantification of alloy usage, energy consumption, and emissions. "Equations (1) and (2)" in the paper define the transition probability matrix and the method for calculating expected visits. "Tables 2 and 3" detail the data requirements for the model and the calculations for transition probabilities. "Tables 4 and 5" present the baseline scenario data and the corresponding resource consumption and emissions for both magnesium and aluminum die casting. The results highlight the substantial environmental impact associated with the SF6 cover gas used in magnesium die casting. Furthermore, the analysis indicates that molten alloy supply offers a notable reduction in both energy consumption and emissions, particularly for aluminum die casting operations.
Figure Name List:
- Fig. 1 Process flow of die casting operation
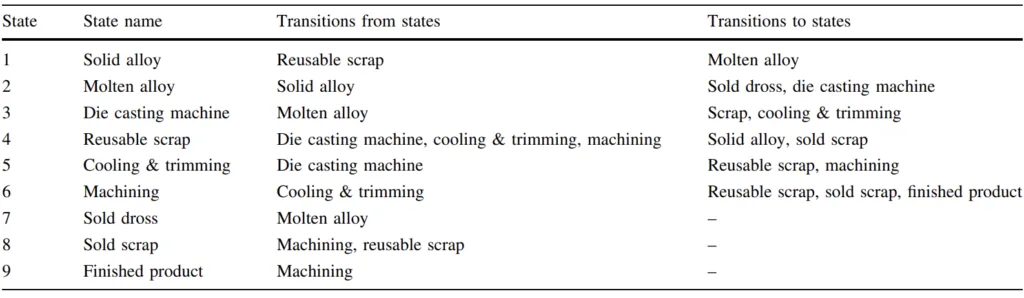
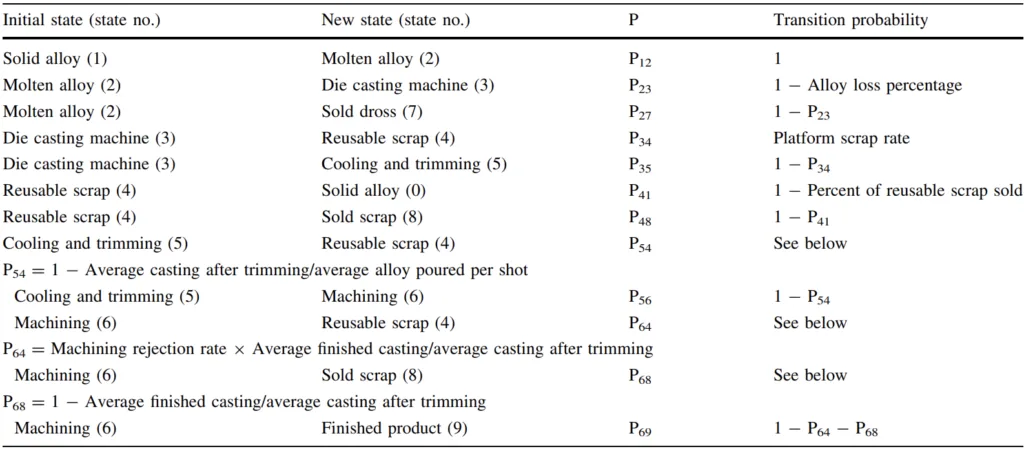
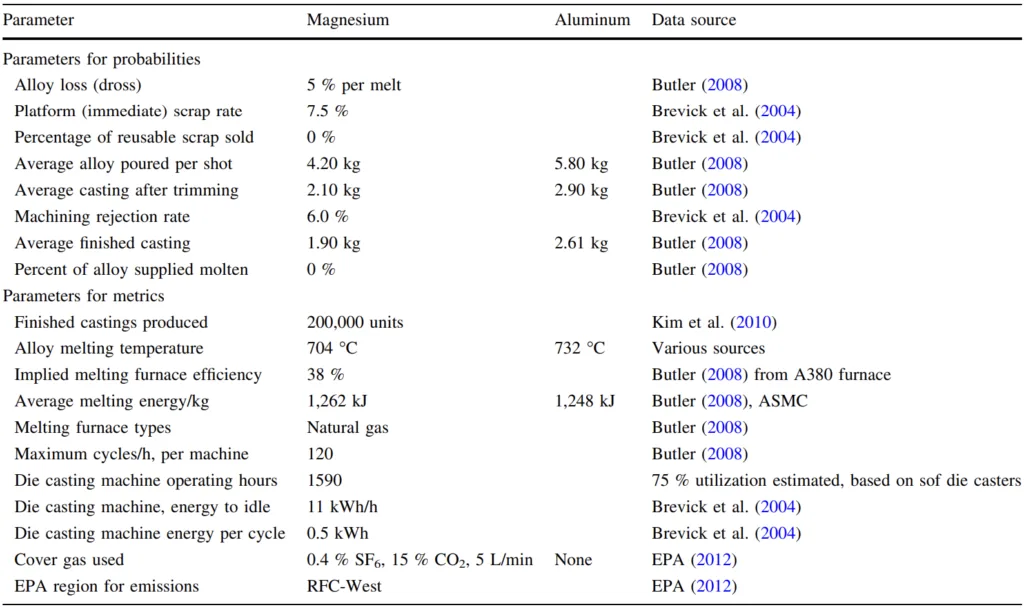
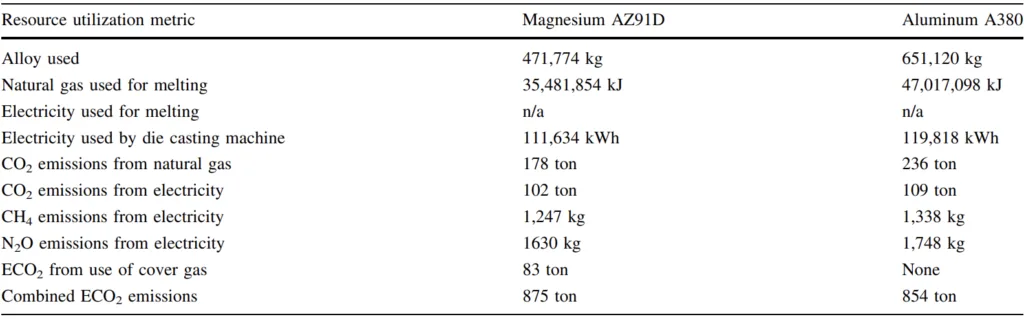
7. Conclusion:
Summary of Key Findings:
The absorbing-state Markov chain (ASMC) model developed in this research effectively represents the operational dynamics of die casting processes. The model accurately estimates energy consumption and ECO2 emissions based on readily available operating data. Its utility lies in enabling the analysis of various alternative operational scenarios and configurations within die casting, facilitating informed decision-making. The case study underscores the significant impact of material selection, cover gas choice, and alloy supply strategies on energy consumption and emissions. Notably, the use of SF6 cover gas in magnesium die casting contributes substantially to overall emissions, while molten alloy supply emerges as a promising strategy for reducing both energy use and environmental impact.
Academic Significance of the Study:
This study presents the first peer-reviewed application of an ASMC model to represent and analyze die casting operations. It contributes to the academic field by providing a system-wide modeling framework for understanding the complexities of energy and material flows in die casting. The research advances the methodological toolkit for analyzing manufacturing processes and offers a novel approach for assessing environmental impacts.
Practical Implications:
The ASMC model provides a valuable tool for die casting practitioners to evaluate and optimize their operations. It supports data-driven decision-making regarding process design, technology investments, and operational adjustments. By enabling the quantification of energy and environmental consequences of different choices, the model assists in identifying and implementing strategies to enhance energy efficiency, reduce environmental footprint, and improve resource utilization in die casting. The findings specifically highlight the practical importance of cover gas selection in magnesium die casting and the potential benefits of adopting molten alloy supply chains.
Limitations of the Study and Areas for Future Research:
The current model has limitations in explicitly estimating energy consumption for certain ancillary processes such as alloy holding, transfer, trimming, and machining, although potential model extensions to incorporate these aspects are discussed. The case study, while illustrative, is specific to cam cover production, suggesting a need for further validation and application of the model across a broader range of die casting contexts and product types. Future research directions include expanding the model's scope to encompass a wider spectrum of environmental impacts beyond energy and emissions, as well as integrating financial analysis capabilities. Further refinement of data collection methodologies and model parameterization techniques could also enhance the model's accuracy and applicability.
8. References:
- Brevick J, Mount-Campbell CA, Mobley C (2004) Energy consumption of die casting operations, Grant/Contract No. OSURF Project No. 739022: US Department of Energy
- Butler W (2008) The "carbon footprint" of aluminum and magnesium die casting compared to injection molded components. North American Die Casting Association
- Cheah L, Heyword J, Kirchain R (2009) Aluminum stock and flows in U. S. passenger vehicles and implications for energy use. J Ind Ecol 13(5):718-734
- City of Philadelphia (2012) www.phila.gov. May 2012
- Eppich RE, Naranjo RD (2007) Implementation of metal casting best practices, The U.S. Department of Energy-Office of Energy Efficiency and Renewable Energy (DOE-EERE), Industrial Technologies Program (ITP) Grant. BCS, Incorporated: The U.S. Department of Energy
- Groover MP (2004) Fundamentals of modern manufacturing, 2nd edn. Wiley, New York, p 228
- Kim H, Keoleian GA, Skerlos SJ (2010) Economic assessment of greenhouse gas emissions by lightweighting using aluminum and high-strength steel. J Ind Ecol 16(1):64-80
- Luenberger DG (1979) Introduction to dynamic systems: theory, models, and applications. Wiley 1979:242
- North American Die Casting Association (NADCA) (2012) www.diecasting.org. May 2012
- Ross SM (1993) Introduction to probability models, 5th edn. Academic, San Diego, p 140
- Street AC (1986) The die casting book, 2nd edn. Portcullis, Surrey
- U. S. Environmental Protection Agency (EPA) (2012) www.epa.gov. May 2012
9. Copyright:
- This material is "Jerald R. Brevick"'s paper: Based on "Modeling alloy and energy utilization in high volume die casting".
- Paper Source: DOI 10.1007/s10098-013-0604-8
This material was summarized based on the above paper, and unauthorized use for commercial purposes is prohibited.
Copyright © 2025 CASTMAN. All rights reserved.