This article introduces the paper ['Mg Casting Alloys for the Aerospace Challenge'] presented at the ['JOURNAL OF METALS']
1. Overview:
- Title: Mg Casting Alloys for the Aerospace Challenge
- Author: A. Stevenson
- Publication Year: May 1987
- Publishing Journal/Academic Society: JOURNAL OF METALS / The Minerals, Metals & Materials Society (TMS)
- Keywords: magnesium alloys, aerospace, casting alloys, high strength alloys, elevated temperature, foundry techniques, grain refining, zirconium alloys, rare earth alloys, fluxless melting, dry sand processes
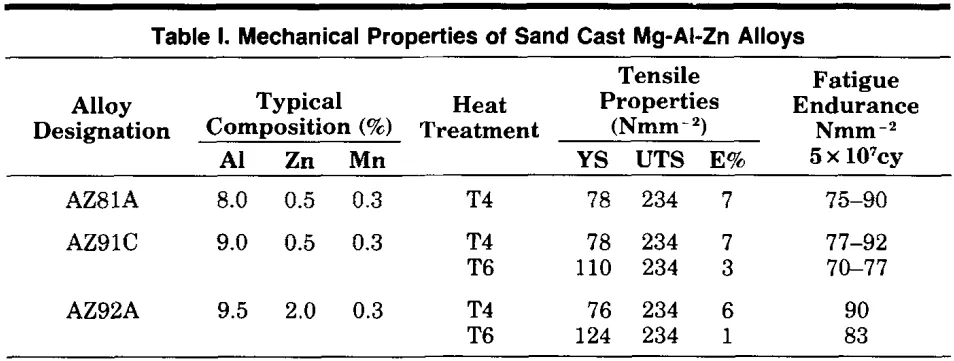
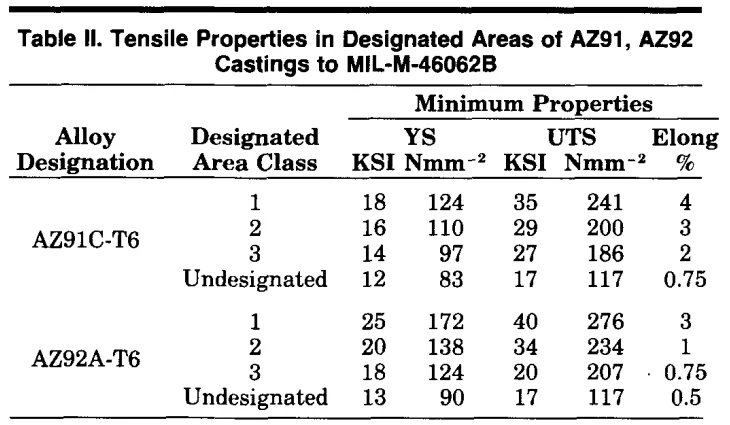
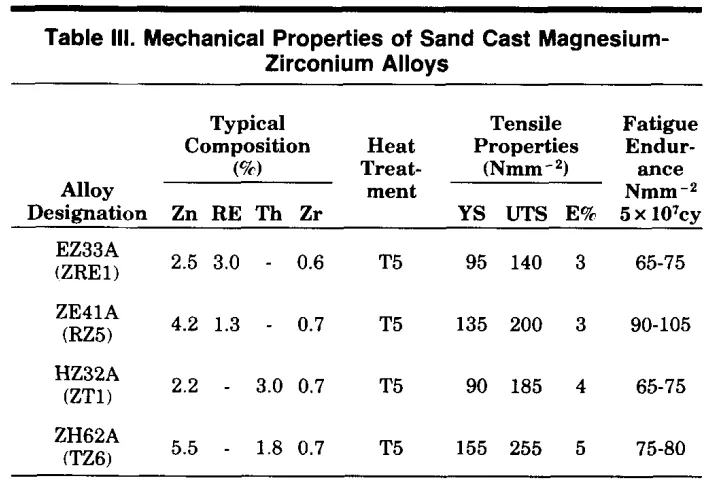
2. Research Background:
Background of the Research Topic:
The utilization of magnesium alloys in aerospace applications has been driven by their inherent advantages, coupled with continuous advancements in alloy development and foundry practices. Initially a laboratory curiosity after its isolation in 1808, magnesium became industrially relevant in the early 1920s with the advent of practical melting and refining techniques. This progress facilitated the development of approximately 30 commercially viable casting alloys. Modern aerospace magnesium alloys are primarily derived from two major alloy series: Mg/Al/Zn and Mg/Zn/Zr systems.
Status of Existing Research:
Early research and development efforts concentrated on Mg/Al/Zn alloys, with compositions ranging from 6-10% Al and 0.5-3.0% Zn. Alloys such as AZ81, AZ91, and AZ92 emerged as prominent casting alloys within this series, and remain in use, particularly where cost-effectiveness is paramount in commercial aerospace applications. These alloys, maximized for strength in the T6 heat treatment condition, exhibit increased yield strength but decreased ductility with higher aluminum content. However, these Mg/Al/Zn alloys are susceptible to microshrinkage, stress corrosion cracking above 50% of their yield strength, and their mechanical properties degrade significantly above approximately 250°F (120°C). Another significant research direction explored the grain refining effect of zirconium in magnesium alloys, known since the late 1930s, leading to the development of Mg-Zn-Zr based alloys. Further advancements included the discovery that rare earth (misch metal) and thorium additions to Mg/Zn/Zr alloys eliminated hot cracking and improved weldability.
Necessity of the Research:
The aerospace sector demands materials with superior performance characteristics, including enhanced ambient and elevated temperature capabilities, to meet stringent user requirements. This necessitates ongoing research and development of magnesium alloys that can deliver high strength and maintain useful properties at elevated temperatures, such as up to 570°F (299°C). Furthermore, advancements in foundry techniques are crucial to produce larger, more complex, and thinner-walled castings with closer tolerances, thereby maximizing weight savings, a critical factor in aerospace design.
3. Research Purpose and Research Questions:
Research Purpose:
This paper aims to review the spectrum of magnesium alloys currently available to the aerospace industry. It seeks to evaluate their technical advantages and disadvantages, and to describe specific alloys engineered to provide improved performance at both ambient and elevated temperatures, catering to the specific demands of aerospace applications.
Key Research:
The key research areas explored in this paper encompass:
- Characterization of Mg-Al-Zn alloys (AZ81A, AZ91C, AZ92A) and their mechanical properties in sand cast conditions.
- Examination of tensile properties in designated areas of AZ91 and AZ92 castings according to MIL-M-46062B specifications.
- Analysis of mechanical properties of sand cast magnesium-zirconium alloys, including ZE41A, EZ33A, HZ32A, and ZH62A.
- Investigation of the effect of temperature on tensile properties of silver-containing alloys EQ21 and QE22, and WE54 in comparison to high-temperature aluminum alloys RR350 and A356.
- Evaluation of tensile properties of hydrided ZE63A-T6 and ZE41A-T5 at ambient temperatures.
- Assessment of fatigue properties of magnesium alloys WE54 and QE22A.
- Discussion of advancements in casting processes, including dry sand processes and fluxless melting techniques.
Research Hypotheses:
The paper implicitly posits that through strategic alloying and the refinement of foundry techniques, magnesium alloys can be tailored to satisfy the rigorous demands of aerospace applications. This includes achieving high strength, maintaining structural integrity at elevated temperatures, and enabling the production of complex, lightweight components with enhanced performance characteristics. The development of alloys like WE54 suggests a hypothesis that specific alloying strategies (e.g., Mg-Y-Nd-Zr system) can significantly improve elevated temperature performance compared to existing magnesium alloys and even approach the performance of established high-temperature aluminum alloys.
4. Research Methodology
Research Design:
This paper adopts a review-based research design, synthesizing existing knowledge and data pertaining to magnesium casting alloys in the aerospace industry. It is adapted from a presentation at the 1987 TMS Annual Meeting, indicating a compilation of established research, industrial practices, and alloy development trends up to that period. The paper leverages published literature and experimental findings to provide a comprehensive overview.
Data Collection Method:
The data presented in this paper are primarily collected from existing literature, specifications, and experimental studies on magnesium alloys. Mechanical property data, such as tensile strength, yield strength, elongation, fatigue endurance, and creep resistance, are compiled and presented in tabular and graphical formats. Alloy compositions and heat treatments are also documented as reported in prior research and alloy specifications.
Analysis Method:
The analysis method employed is comparative and descriptive. The paper compares the mechanical properties of different magnesium alloy systems (Mg-Al-Zn, Mg-Zn-Zr, Mg-Ag-Nd-Zr, Mg-Y-Nd-Zr) and assesses their suitability for aerospace applications based on property benchmarks and operational temperature requirements. Graphical analysis is used to illustrate the effect of temperature and exposure time on alloy performance. The paper also describes the advancements in foundry techniques and their impact on casting quality and complexity.
Research Subjects and Scope:
The research focuses on magnesium casting alloys specifically designed or considered for aerospace applications. The scope encompasses a range of alloy systems, heat treatments (T4, T5, T6), and casting methods (sand, investment, permanent mold). The paper examines the alloys' performance characteristics, including mechanical properties at ambient and elevated temperatures, castability, weldability, and corrosion resistance, within the context of aerospace industry needs. The scope also extends to advancements in magnesium foundry technology, specifically dry sand processes and fluxless melting.
5. Main Research Results:
Key Research Results:
- Mg-Al-Zn Alloys (AZ Series): These alloys (AZ81A, AZ91C, AZ92A) are widely used due to their cost-effectiveness and versatility in various casting techniques (sand, investment, permanent mold, die casting). Table I summarizes their mechanical properties in sand cast conditions, showing that maximum strength is achieved in the T6 heat treated condition, with yield strength increasing and ductility decreasing with higher Al content. However, they are prone to microshrinkage and stress corrosion cracking, and their mechanical properties degrade above 250°F (120°C).
- Mg-Zn-Zr Alloys (ZE, ZH, EZ, HZ Series): These alloys, particularly with rare earth additions, offer improved elevated temperature properties and weldability. ZE41 and ZH62 are structural alloys for temperatures up to 300°F (150°C), while EZ33A and HZ32 are designed for creep strength at temperatures up to 480°F (250°C) and 660°F (350°C), respectively. Table III details their mechanical properties.
- Silver-Containing Alloys (QE22A, QH21, EQ21): Alloys like QE22A, QH21, and EQ21 represent a significant advancement, with room temperature properties approaching those of high-strength aluminum alloys A356 and A357. Figure 1 demonstrates that EQ21 exhibits better temperature stability at elevated temperatures than QE22A.
- Hydrided ZE63A: Solution treatment of Mg/Zn/RE/Zr alloys in a hydrogen atmosphere led to the development of ZE63A, which, in the "hydrided" condition (ZE63A-T6), exhibits excellent tensile and fatigue properties (Tables IV and V).
- WE54 Alloy (Mg-Y-Nd-Zr): This newly developed alloy demonstrates superior elevated temperature properties compared to existing magnesium alloys and favorably compares with RR350 aluminum alloy up to 572°F (300°C) (Figure 2 and 3). Creep testing at 480°F (250°C) also shows WE54's superiority (Figure 4).
- Foundry Technology Advancements: The adoption of dry sand processes (CO2-silicate, cold-set, air-set systems) and fluxless melting techniques has significantly improved casting quality, dimensional accuracy, surface finish, and enabled the production of more complex and thinner-walled magnesium castings.
Data Interpretation:
- Table I, II, III, IV, V, VI: These tables provide quantitative data on the mechanical properties of various magnesium alloys under different conditions (heat treatments, temperatures). They allow for direct comparison of alloy performance in terms of tensile strength, yield strength, elongation, fatigue endurance, and fracture toughness.
- Figure 1, 2, 3, 4: These figures graphically illustrate the effect of temperature and exposure time on the tensile and creep properties of selected alloys (EQ21, QE22, WE54, RR350, QH21A, QE22A). They visually demonstrate the superior elevated temperature performance of newer alloys like EQ21 and WE54.
- Figure 5: This figure presents critical crack lengths for different magnesium alloys as a function of percentage design stress, indicating their fracture toughness characteristics.
Figure Name List:
- Figure 1. Effect of temperature on tensile properties of EQ21 vs. QE22.
- Figure 2. Effect of temperature on tensile properties of WE54 vs. the high temperature Al alloys RR350 and A356.
- Figure 3. Effect of exposure time on tensile properties of 482°F (250°C) for WE54X compared with QH21A and Al casting alloy RR350.
- Figure 4. Stress/strain relationship for WE54 vs. QH21A and QE22A at 482°F (250°C).
- Figure 5. Critical crack lengths as a function of percentage design stress for various magnesium alloys.
- Figure 6. This casting, produced in ZE41, weighs 620 lbs. and is the main gearbox for the Westland WG34 helicopter.
- Figure 7. Shown is a sectioned gearbox casting, revealing cored passageways.
- Table I. Mechanical Properties of Sand Cast Mg-Al-Zn Alloys
- Table II. Tensile Properties in Designated Areas of AZ91, AZ92 Castings to MIL-M-46062B
- Table III. Mechanical Properties of Sand Cast Magnesium-Zirconium Alloys
- Table IV. Tensile Properties of ZE63A-T5, ZE41A-T5 at Ambient Temperature
- Table V. Mechanical Properties of ZE63A-T6 (Hydrided) vs. ZE41-T5 at Ambient Temperatures
- Table VI. Fatigue Properties of Magnesium Alloys WE54, QE22A
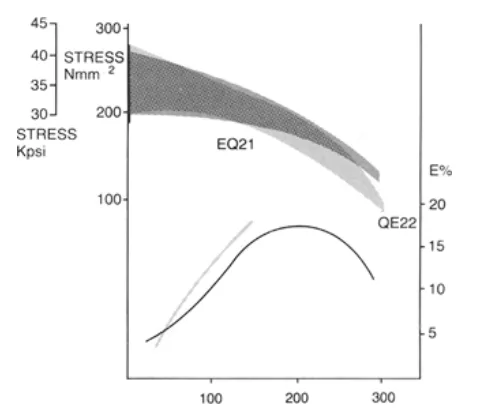
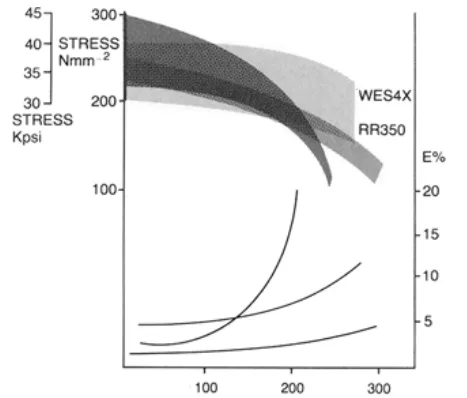
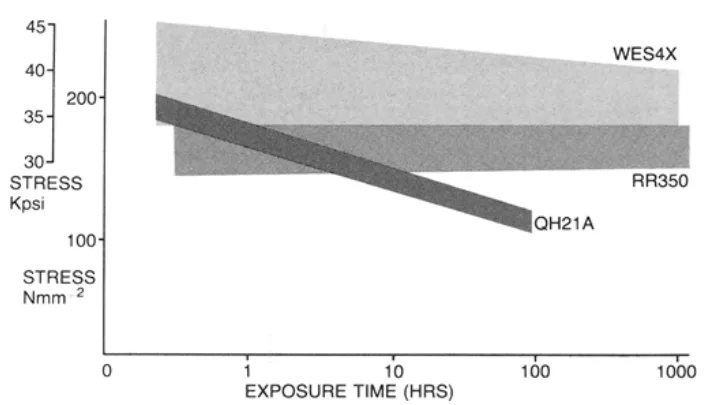
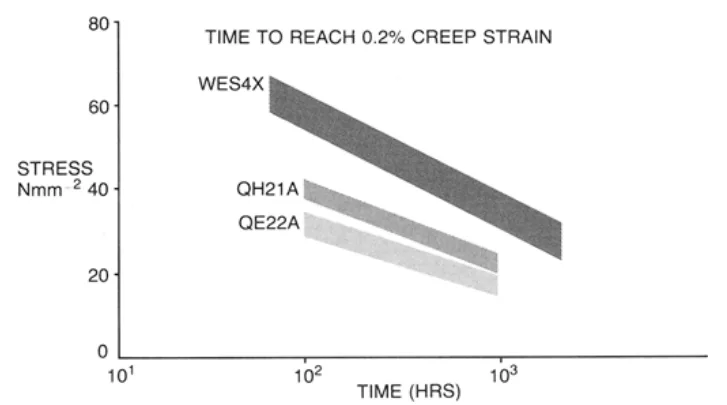
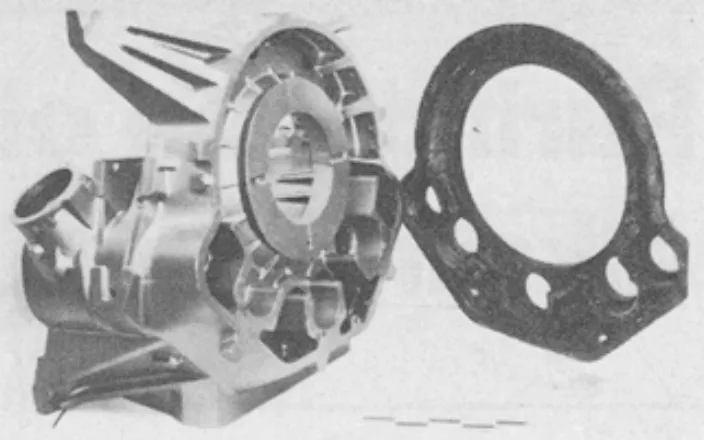
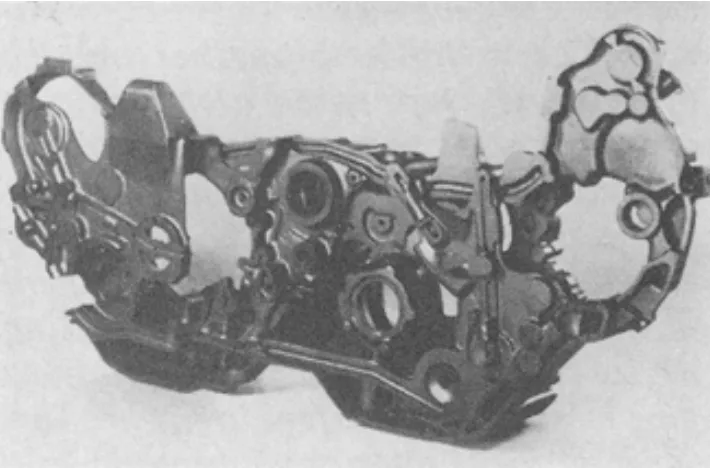
6. Conclusion:
Summary of Main Results:
Magnesium casting alloys have undergone significant advancements to meet the evolving demands of the aerospace industry. While Mg-Al-Zn alloys remain relevant for cost-sensitive applications, Mg-Zn-Zr alloys and silver-containing alloys like QE22A, QH21, and EQ21 offer superior high-temperature performance and strength. The WE54 alloy (Mg-Y-Nd-Zr) represents a notable breakthrough, exhibiting exceptional elevated temperature properties, even comparable to high-temperature aluminum alloys. Concurrently, innovations in foundry technologies, such as dry sand processes and fluxless melting, have enhanced casting precision, complexity, and overall quality, enabling the production of advanced magnesium components for aerospace applications.
Academic Significance of the Research:
This paper provides a valuable handbook-level review of magnesium casting alloys for aerospace, documenting the progression of alloy development and foundry practices. It underscores the critical role of alloying strategies and processing innovations in tailoring magnesium alloys to achieve specific performance criteria. The paper serves as a consolidated resource for understanding the material science and engineering advancements that have expanded the applicability of magnesium in demanding aerospace environments.
Practical Implications:
The development and characterization of advanced magnesium alloys and foundry techniques have significant practical implications for the aerospace industry. These advancements enable the design and manufacture of lighter, more intricate, and higher-performance aerospace components. The enhanced elevated temperature capabilities of alloys like WE54 and the improved casting precision afforded by new foundry methods translate to potential weight savings, improved fuel efficiency, and enhanced operational capabilities for aerospace vehicles.
Limitations of the Research:
As a review paper based on a 1987 presentation, this work primarily summarizes the state of knowledge up to that time. It does not present novel experimental data or analysis beyond the cited references. The paper acknowledges limitations inherent in specific alloy systems, such as the microshrinkage susceptibility of Mg-Al-Zn alloys and the lengthy hydriding process required for ZE63A. Furthermore, the performance data and alloy developments discussed reflect the technology available in the mid-1980s, and subsequent advancements in magnesium alloy technology and foundry practices are not covered.
7. Future Follow-up Research:
- Directions for Follow-up Research
Future research directions should focus on: - Optimizing melting and casting techniques, particularly for advanced alloys like WE54, to enhance production efficiency and reduce costs.
- Continued exploration of novel alloy compositions within the Mg-Y-Nd-Zr system and other alloy families to further improve elevated temperature strength, creep resistance, and other critical properties.
- Streamlining and shortening the hydriding treatment process for alloys like ZE63A to broaden their industrial applicability.
- Areas Requiring Further Exploration
Areas requiring further exploration include: - Expanding the industrial application of high-performance alloys like WE54 in aerospace structures and engine components, leveraging their superior elevated temperature capabilities.
- Promoting the wider adoption of pressure hydriding techniques for ZE63A to overcome limitations associated with long hydriding times.
- Further refining dry sand processes and fluxless melting techniques to extend their application across a broader range of magnesium alloys and casting complexities, and to improve process economics and environmental sustainability.
8. References:
- R.J.M. Payne and N. Bailey, J. Inst. Metals, Vol. 88, Pt. 10, 1959/60, pp. 417-427.
- British Patent 1,463,610.
- K.G. Gradwell, "Precipitation in a High Strength Magnesium Casting Alloy," Ph.D. Thesis, University of Manchester, 1972.
- British patent 1,463,608.
- P.A. Fisher, P.C. Meredith and P.E. Thomas, Foundry, August 1967, pp. 68-72.
- British Patent 1,465,687.
- U.S. Patent 4,401,621.
- W. Unsworth and J.F. King, Proceedings of the AFS/ CMI Conference "Recent Advances in Magnesium Technology," June 1985, pp. 43-57.
- Ibid.
- R.L. Naro and J.F. Hart, Trans. AFS 1980, Vol. 55, pp. 57-66.
- W. Ellinghaus, Giesserei 68, Nr. 6 (1981), 16th March, pp. 135-143.
- I. Strachan and H.J. Proffitt, Modern Casting, December 1981, pp. 42-43.
- J.W. Freuhling and J.D. Hanawalt, Trans. AFS 1969, Vol. 77, p. 59.
- S.L. Couling et al., Proc. International Magnesium Association, Oslo, 1979.
- H.J. Proffitt, Proc. International Magnesium Association, Houston 1981, pp. 53-58.
9. Copyright:
- This material is "A. Stevenson"'s paper: Based on "Mg Casting Alloys for the Aerospace Challenge".
- Paper Source: JOURNAL OF METALS, May 1987
This material was summarized based on the above paper, and unauthorized use for commercial purposes is prohibited.
Copyright © 2025 CASTMAN. All rights reserved.