The content of this introduction paper is based on the article "Mechanism of die soldering during aluminum die casting" published by "China Foundry".
![Figure 1: Schematic illustration showing possible aluminum composition and temperature profiles at the die surface, and the resulting phases for the case of pure aluminum cast in an iron die. Three regions at the die surface can be identified. Soldering occurs in Region I [4].](https://castman.co.kr/wp-content/uploads/image-1853-png.webp)
1. Overview:
- Title: Mechanism of die soldering during aluminum die casting
- Author: Q. Han
- Year of publication: 2015
- Journal/academic society of publication: China Foundry, vol. 12, no. 2, pp. 136-143.
- Keywords: Soldering, die sticking, aluminum alloys, and die casting
2. Abstract:
Soldering is a unique casting defect associated with die casting or metal mold casting of aluminum alloys. It occurs when molten aluminum sticks or solders the surface of the die steel and remains there after the ejection of the casting, causing surface defect and dimensional inaccuracy of the castings and increased machine downtime. Soldering occurs easily when a bare die steel mold is used for die casting of aluminum alloys. When molten aluminum comes in contact with the die steel at a temperature higher than a critical temperature, the iron and aluminum atoms diffuse into each other, forming a series of intermetallic phases and a liquid aluminum-rich fcc phase. This liquid phase exists between intermetallic phases. On cooling the liquid fcc phase solidifies on the intermetallic phases and grows into the casting, resulting in soldering. The critical temperature is the eutectic temperature near the aluminum corner of the phase diagram. If the die is protected using a nonreactive ceramic coating, soldering starts at locations where local coating failure occurs. Molten aluminum comes into contact with die steel through the coating failure locations and eats into the steel matrix, forming small pits. As these small pits grow, the coating is gradually removed and soldering becomes more severe. Details of step for die soldering on a bare steel die and on a coated die material are discussed.
3. Introduction:
Die casting, or high pressure die casting (HPDC), is a century old process of injecting molten metal into a steel die using high pressure. This cost effective process is capable of producing net-shape products at a rapid production rate and with a high metal yield per mold. No other metal casting processes allow for a greater variety of shapes, fine intricacy of design or closer dimensional tolerance. Today, the die casting process is used to produce over one-third of the all metal castings, most of them are aluminum castings [1].
One major issue limiting the productivity of aluminum die castings is die soldering. Soldering or die sticking is a phenomenon in which molten aluminum “welds” to the die surface. Under severe conditions, die soldering occurs after just a few casting cycles, resulting in increased machine downtime, scrap that is related to surface quality and pressure or leak tightness of a casting, and costs since the dies are generally expensive and downtime results in lost production. Die soldering is also associated with other metal mold casting processes including low pressure permanent mold casting.
Small features on a metal die that are surrounded by molten metal are prone to soldering formation because such features are usually heated to higher temperatures than the bulk of the die during each run of die casting process. Core pins, used for forming small holes in casting, are such features on a metal die that are prone to soldering during the die casting process. The use of core pins reduces the requirement for drilling the holes on castings, making the casting process more cost effective. A typical die casting machine uses about 10 to 100 pins. The die casting industry uses H-13 steel for making dies and core pins due to the fact that H-13 steel resists to heat checking and wear.
Two types of soldering are claimed by the diecasting industry. One occurs at high temperatures due to a chemical/metallurgical reaction between the molten aluminum alloy and the die [2], the other occurs at low temperatures due to mechanical interaction [3]. Limited systematic study has been carried out to investigate die soldering until in 1990s when the North American diecasting industry faced strong international competition. It became vital for die casters to minimize downtime and to increase their productivity in order to survive but most die casters in North America are small business companies that are lack of resource for research. As a result, research on die soldering has been sponsored by industrial organizations and by governmental agencies. Significant progress has been made in understanding die soldering that occurs due to a chemical reaction. Little is understood on soldering due to mechanical interactions.
This article discusses die soldering as a result of chemical interaction. It is generally acknowledged that this type of soldering is closely related to the “washout” of a protective film on the die surface [2]. Washout occurs when the molten aluminum alloy destroys the protective film (coating or lubricant) on the die. The molten aluminum then comes into contact with the die surface and react with the die material, usually H-13 steel. Die lubricant can be easily destroyed by the molten metal but a coating, especially a coating made using the physical vapor deposition (PVD) process, can stay on the mold for many casting cycles. When a large portion of the die lubricant is removed, soldering is controlled by a direct chemical reaction between the molten metal and the bare die steel. In case there is a strong PVD coating on a die, soldering is controlled by the local failure of the coating. This article describes soldering on a bare steel mold and on a coated die or core pin.
4. Summary of the study:
Background of the research topic:
Die soldering, where molten aluminum adheres to the die surface, is a significant impediment to productivity in aluminum high-pressure die casting (HPDC). It leads to casting defects (surface imperfections, dimensional inaccuracy), increased machine downtime for die maintenance, higher scrap rates, and increased costs associated with expensive dies and lost production. Features like core pins, made typically from H-13 steel, are particularly susceptible due to higher operating temperatures.
Status of previous research:
Systematic investigation into die soldering was limited until the 1990s. Research distinguishes between high-temperature soldering due to chemical/metallurgical reactions and low-temperature soldering from mechanical interaction. Significant progress has been achieved in understanding the chemical reaction mechanism, often linked to the "washout" or destruction of protective films (lubricants or coatings) by the molten aluminum alloy [2]. The role of durable coatings, such as PVD coatings, in mitigating soldering is acknowledged, but soldering can still occur upon local coating failure. Understanding of mechanical soldering remains limited.
Purpose of the study:
This study aims to elucidate the mechanism of die soldering that occurs as a result of chemical interaction between molten aluminum alloys and die steel (specifically H-13). It details the process for both bare steel surfaces and surfaces protected by a nonreactive ceramic coating, focusing on the conditions leading to soldering and the progression of die damage.
Core study:
The core of the study analyzes the fundamental mechanism of die soldering based on chemical reactions. For bare steel dies, it investigates the diffusion of aluminum into the steel and iron into the aluminum, leading to the formation of intermetallic phases. A critical aspect is the formation of a liquid aluminum-rich fcc phase when the die surface temperature exceeds a critical temperature (Tc), identified as the eutectic temperature (655°C for pure Al-Fe). This liquid phase facilitates the bonding between the casting and the die upon solidification. For coated dies, the study outlines a five-step failure mechanism: (1) local coating failure (cracking/detachment), (2) pit formation via reaction at the exposed steel, (3) in-depth and lateral growth of pits involving intermetallic and Al-rich fcc phase formation, (4) connection of adjacent pits, and (5) formation of negative draft or undercut due to erosion in the failed areas. Experimental dipping tests were conducted to validate the critical temperature concept for pure aluminum and A380 alloy. Microstructural analysis of used core pins provided evidence for the proposed mechanism on coated surfaces.
5. Research Methodology
Research Design:
The research employed a combination of theoretical analysis based on phase diagrams (Al-Fe system) and metallurgical principles (diffusion, reaction kinetics, phase transformations) alongside experimental validation. Two primary scenarios were investigated: soldering on bare steel surfaces and soldering initiation and progression on coated steel surfaces (specifically core pins).
Data Collection and Analysis Methods:
- Bare Steel Analysis:
- Simple dipping and dip-coating tests were performed using mild steel cylinders (12 mm diameter, 25 mm length) immersed in molten pure aluminum and A380 aluminum alloy.
- Sample surface temperature was monitored using a welded thermocouple and controlled (±3°C) by adjusting immersion in the melt or holding in a furnace.
- Tests were conducted at various surface temperatures above and below the respective melting points/liquidus temperatures (Pure Al: 630°C to 740°C; A380: 500°C to 680°C) for different durations (Table 1).
- Post-test samples were presumably sectioned and examined metallographically (implied by Figure 3) to assess the presence and nature of soldering, including the formation of intermetallic layers and metallurgical bonds.
- Results were correlated with the Al-Fe phase diagram (Figure 1) to identify critical temperatures for liquid phase formation.
- Coated Die/Core Pin Analysis:
- Core pins used in industrial die casting machines for various durations were collected.
- Scanning Electron Microscopy (SEM) was utilized to examine the surfaces of these pins.
- SEM imaging documented various stages of soldering: initial coating failure modes (cracking, detachment - Figure 4), pit formation and growth (Figure 5), morphology of established soldered areas (Figure 6a, Figure 7), and evidence of undercutting (Figure 8).
- Energy Dispersive X-ray Spectroscopy (EDS) line scans (implied by Figure 6b, 6c) were used to analyze the elemental distribution (Al, Fe, Si, Cr, Cu) across the H-13 matrix, reaction zones (intermetallics), and Al alloy regions within the pits, allowing for phase identification and understanding of diffusion processes.
Research Topics and Scope:
The research focused exclusively on the mechanism of die soldering in aluminum die casting resulting from chemical/metallurgical interactions. The scope included:
- Defining the conditions (critical temperature) for soldering initiation on bare steel surfaces for pure aluminum and A380 alloy.
- Characterizing the intermetallic phases formed and the role of the liquid Al-rich fcc phase.
- Detailing the sequential steps involved in soldering development on ceramic-coated H-13 steel core pins, starting from local coating failure and progressing to severe die damage (undercut).
- Investigating the microstructural evolution and elemental diffusion associated with pit formation and growth on coated surfaces.
- The study did not investigate soldering caused by mechanical interaction.
6. Key Results:
Key Results:
- Die soldering on bare steel occurs when the die surface temperature (TD) exceeds a critical temperature (Tc), enabling the formation of an aluminum-rich liquid fcc phase within the Fe-Al intermetallic reaction layer (Region I, Figure 1). Solidification of this liquid phase creates a metallurgical bond between the casting and the die (Figure 2).
- For pure aluminum cast against iron/steel, the critical temperature Tc corresponds to the Al-Fe eutectic temperature, 655°C. Experimental dipping tests confirmed soldering occurred at surface temperatures ≥ 661°C, but not ≤ 643°C (Table 1, Figure 3).
- For A380 alloy cast against steel, the critical temperature for soldering is suggested to be related to either the dendrite coherency temperature (approx. 560°C) or the liquidus temperature (575°C). Experiments showed soldering at 575°C but not at 550°C (Table 1).
- On ceramic-coated H-13 steel dies/core pins, soldering initiates at sites of local coating failure, such as cracks or areas where the coating has detached from the substrate (Figure 4).
- Molten aluminum penetrates these failure sites and reacts with the underlying H-13 steel, forming small pits or reaction regions containing iron aluminides (Figure 5).
- These pits grow laterally, undermining the adjacent coating, and also grow in-depth into the steel matrix. This growth involves the formation of complex iron aluminides (e.g., Al12Fe6Si5, Al15Fe6Si5, Al4FeSi) and an Al-rich fcc phase, particularly at the outer edge of the reaction zone (Figure 6).
- The Al-rich fcc phase, which can be liquid at die casting temperatures (if Al content > 61.5 wt% and T > 655°C), facilitates further erosion of intermetallics and enhances diffusion, accelerating pit growth.
- Adjacent pits eventually connect, forming larger, continuous soldered areas often exhibiting a zigzag morphology (Figure 7).
- In severely affected regions where the coating is completely removed, continued erosion and dissolution of the steel matrix by the impinging molten aluminum can lead to the formation of negative draft or undercuts on the die surface (Figure 8), severely hindering casting ejection and potentially causing damage.
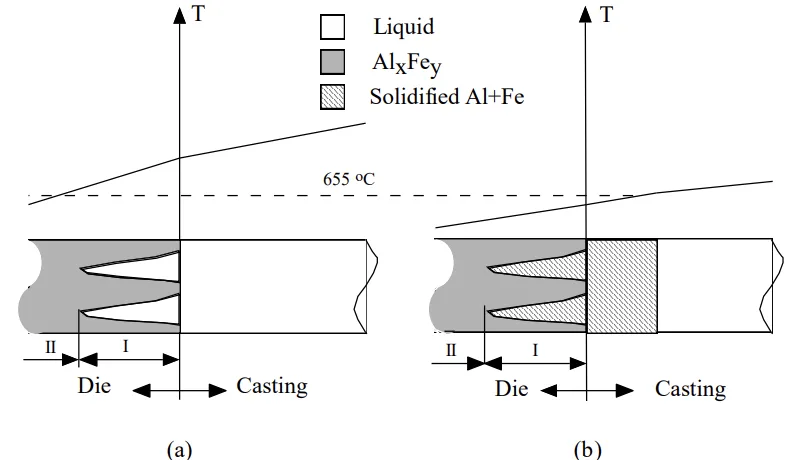
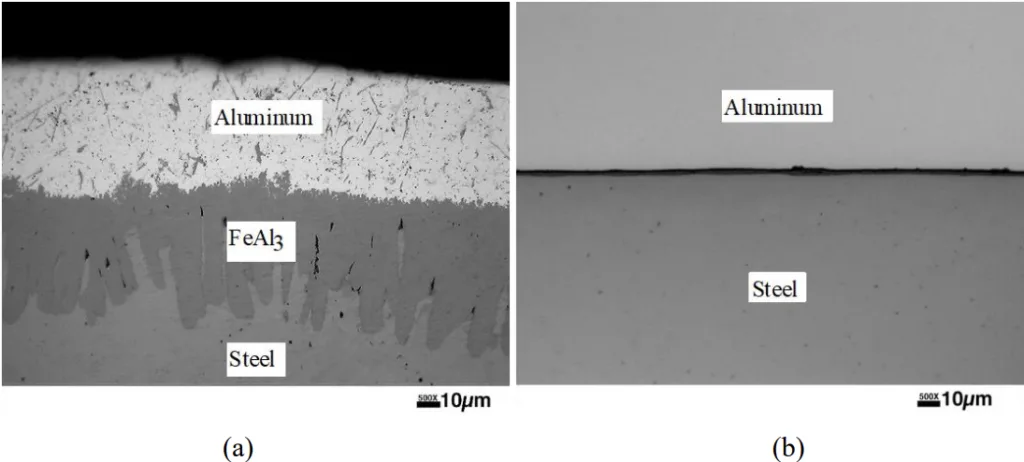
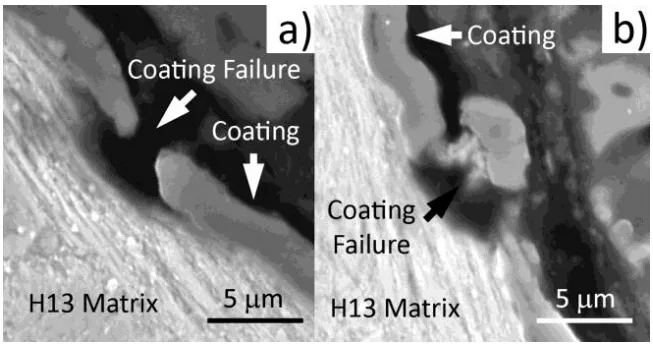
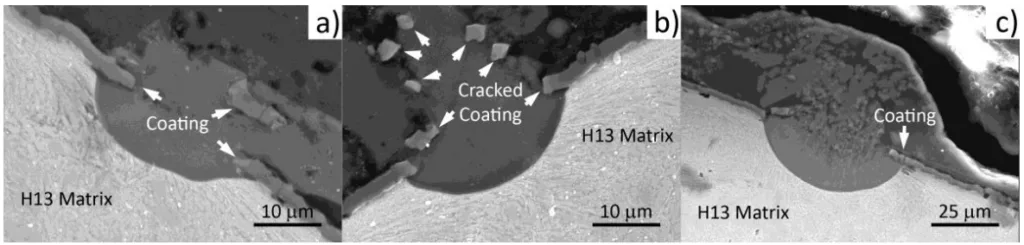
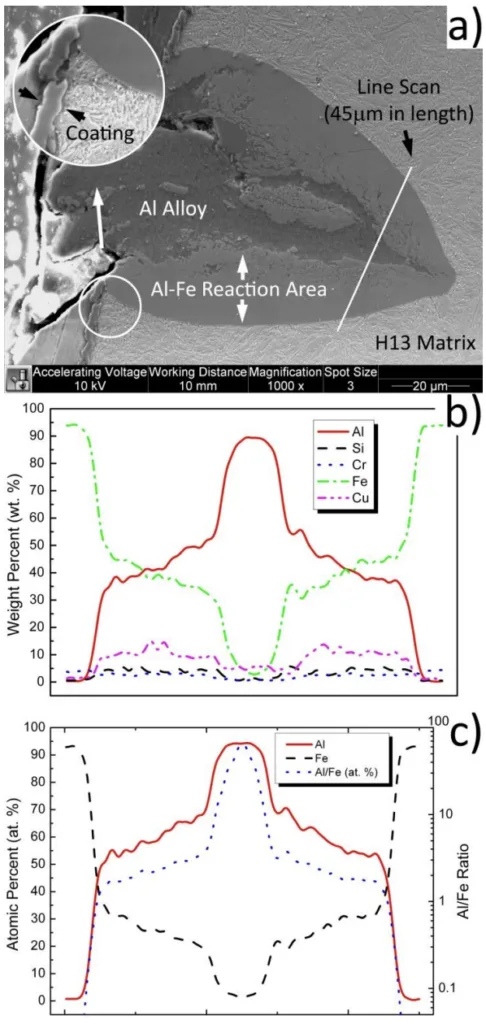
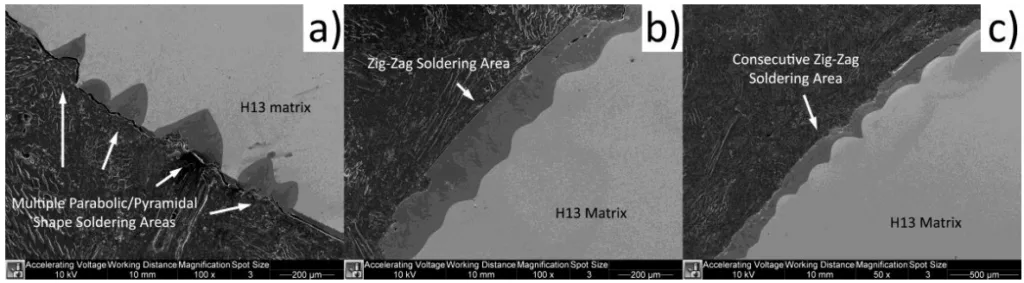
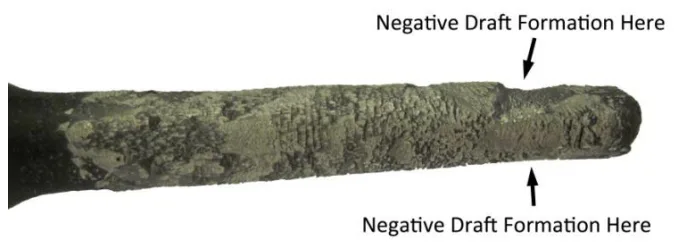
Figure Name List:
- Figure 1: Schematic illustration showing possible aluminum composition and temperature profiles at the die surface, and the resulting phases for the case of pure aluminum cast in an iron die. Three regions at the die surface can be identified. Soldering occurs in Region I [4].
- Figure 2. Schematic illustration of the mechanism of die soldering, indicating (a) the presence of liquid at the die surface when the temperature at the surface is higher than a critical temperature, 655°C, and (b) the formation of a joint between the casting and the die on solidification of this liquid phase.
- Figure 3. Typical microstructures observed at the die surface for three cases: (a) metallurgical bond resulting in soldering, and (b) absence of reaction between steel and aluminum.
- Figure 4: SEM images illustrating coating failure in two ways: (a) cracked and (b) detached.
- Figure 5 SEM images of the reaction areas: (a) coating broken by lateral growth in soldering area, (b) coating cracked and migrated away, and (c) coating washed out.
- Figure 6: Typical pit or soldering area with parabolic/pyramidal shape: (a) the SEM image and line scan location, (b) weight percentage curves of five elements along the scanned line and (c) atomic percentage curves and the ratio of Al/Fe curve.
- Figure 7: SEM images of soldering area: (a) multiple pits of parabolic/pyramidal shape, (b) and (c) two views of soldering area with a consecutive zigzag shape.
- Figure 8: Schematic of negative draft or undercut formation on a core pin (arrow showed).
7. Conclusion:
Die soldering in aluminum die casting, driven by chemical interaction, occurs when the die surface temperature surpasses a critical threshold (Tc), leading to the formation of an Al-rich liquid phase within the Fe-Al intermetallic layer at the die-casting interface. This liquid phase solidifies and bonds the casting to the die. For pure aluminum against steel, Tc is the Al-Fe eutectic temperature (655°C). For alloys like A380, Tc is related to the liquidus or dendrite coherency temperature. On bare steel, the process involves diffusion and reaction leading directly to this liquid formation above Tc. On coated dies (e.g., ceramic on H-13 steel), soldering follows a progressive failure mechanism initiated by localized coating defects (cracks, detachment). Molten aluminum reacts with the exposed steel, forming pits that grow both laterally and in-depth. This growth involves the formation of iron aluminides and an Al-rich fcc phase, which, if liquid, accelerates erosion and further reaction. Pits eventually coalesce, and severe erosion can lead to undercuts or negative draft, hindering part ejection. The presence and behavior of the Al-rich fcc phase are central to the soldering mechanism in both bare and coated scenarios.
(Note: The original paper includes a heading "4. Conclusions" but provides no text under it. This conclusion is synthesized from the abstract and the main findings presented throughout the paper.)
8. References:
- [1] NADCA website, http://www.diecasting.org/].
- [2] Y.L. Chu, P.S. Cheng and R. Shivpuri, Transactions (Rosemont, Illinois: North American Die Casting Association, 1993), pp.361-371
- [3] D. Argo, R.J. Barnhurst, and W. Walkington, “NADCA Sponsored Research: The cause of Soldering in Zinc Die Casting,” Transactions (Rosemont, Illinois: North American Die Casting Association, 1997), pp. 77-82
- [4] Q. Han and S. Viswanathan, “Analysis of the Mechanism of Die Soldering in Aluminum Die Casting," Metall. Mater. Trans., 2003, 34A, pp. 139-46.
- [5] H. Baker et al. (Eds), ASM Handbook, vol.3, Alloy Phase Diagrams (Materials Park, OH: ASM International), 1992.
- [6] W. Kajoch and A. Fajkiel, “Testing the Soldering Tendencies of Aluminum Die Casting Alloys," Transactions (Rosemont, Illinois: North American Die Casting Association, 1991), pp.67-74.
- [7] S. Shankar and D. Apelian, "Die Soldering – A Metallurgical Analysis of the Molten Aluminum/Die Interface Reactions,” Transactions (Rosemont, Illinois: North American Die Casting Association, 1997), pp. 243-251.
- [8] V.G. Rivlin and G.V. Raynor, “Critical Evaluation of Constitution of Aluminum-Iron-Silicon System,” Int. Met. Rev., 26 (1981) pp. 133-152.
- [9] R.W. Richards, R.D. Jones, P.D. Clements and H. Clarke, “Metallurgy of Continuous Hot Dip Aluminizing,” Int. Mat. Rev., 39 (1994) pp. 191-212.
- [10] J. Wallace, D. Schwam, Y. Zhu, S. Birceanu, “Soldering Characteristics of Die Materials and the Effect on Cooling Link Placement on Die Life,” Transactions of the North American Die Casting Association, Rosemont, IL, 2002, T03-041.
- [11] G. Engleman, S. Viswanathan, C.A. Blue, Q. Han, and N.B. Dahotre, “High Density Infrared Coatings for Soldering Resistance,” Transactions of the North American Die Casting Association, Rosemont, IL, 2002, T02-43.
- [12] J. Moore, S. Carrera, J. Lin, O. Salas, B. Mishra, G. Mustoe, and P. Ried, “The Development of Surface Engineered Coating Systems for Aluminum Pressure Die Casting Dies: An Evaluation of Six Commercial Coatings,” Transactions of the North American Die Casting Association, Rosemont, IL, 2003, T03-025.
- [13] L. Arnberg, L. Bäckerud, and G. Chai, Solidification Characteristics of Aluminum Alloys, vol.3, Dendrite Coherency (American Foundrymen's Society, Inc., 1996), 115
- [14] Z. W. Chen and M. Z. Jahedi, Die Erosion and Its Effect on Soldering Formation in High Pressure Die Casting of Aluminum Alloys, Materials and Design, 1999, vol. 20, pp.303-309.
- [15] J. Song, T. Denouden, and Q. Han, “Mechanisms of Soldering Formation on Coated Core Pins," Metall Mater Trans, 2012, 43A, pp. 415-421.
- [16] S. Shankar, and D. Apelian, “Die Soldering: Mechanism of the Interface Reaction between Molten Aluminum Alloy and Tool Steel,” Metall. Mater. Trans., 2002, 33B, pp. 466-476.
- [17] J. V. Skoff, "A New Approach to the Cause of High Pressure Die Steel Erosion, Pitting and Breakout", NADCA Transactions, 2010, pp. T10-051.
9. Copyright:
- This material is a paper by "Q. Han". Based on "Mechanism of die soldering during aluminum die casting".
- Source of the paper: https://doi.org/10.1007/s41230-015-1116-6
This material is summarized based on the above paper, and unauthorized use for commercial purposes is prohibited.
Copyright © 2025 CASTMAN. All rights reserved.