This article introduces the paper ['Manufacturing Processes of Car Alloy Wheels'] published by ['HAL open science'].
1. Overview:
- Title: Manufacturing Processes of Car Alloy Wheels
- Author: Mohsen Soori
- Publication Year: 2022
- Publishing Journal/Academic Society: HAL open science (Preprint)
- Keywords: Alloy wheels, Casting, CNC machining operations, Finite Element Method, Optimization
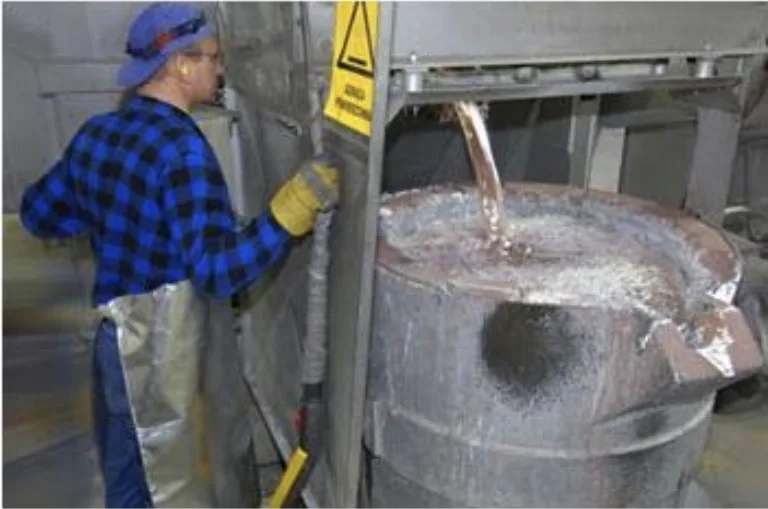
2. Abstracts
Passenger cars are using the alloy wheels due to lighter wheels in order to reduce fuel consumption. The alloy wheels are usually made from light and strong alloys such as aluminum and magnesium which can improve the performances of braking system to increase safety of the driving. They are produced by casting, machining and forging operations. The production process can be analyzed and modified to increase efficiency of part production.
Finite element analysis can be used to find the static and dynamic stress of the wheel in actual working conditions. Process of machining operations using turning machine tools can also be analyzed to be modified. The optimization process can be used to increase rigidity of the produced alloy wheels. New alloys properties can be tested using virtual simulation to increase performances of the alloy wheels. To increase quality of produced parts, thermal model of the low-pressure die-cast in alloy wheel production process is analyzed. So, more added value in manufacturing process of alloy wheels can be achieved.
Keywords: Alloy wheels, Casting, CNC machining operations, Finite Element Method, Optimization
3. Research Background:
Background of the Research Topic:
The automotive industry's pursuit of fuel efficiency has driven the adoption of alloy wheels in passenger cars, primarily due to their reduced weight compared to steel wheels. These alloy wheels, typically composed of light and robust materials such as aluminum and magnesium, not only contribute to fuel economy but also enhance braking system performance, thereby improving driving safety. The manufacturing of alloy wheels encompasses several key processes, including casting, machining, and forging operations.
Status of Existing Research:
Current research in alloy wheel manufacturing focuses on analyzing and refining production processes to maximize part production efficiency. Finite Element Analysis (FEA) is employed to evaluate static and dynamic stresses within the wheel under operational conditions. Machining operations utilizing turning machine tools are subject to analysis and modification for optimization. Furthermore, optimization techniques are applied to enhance the rigidity of manufactured alloy wheels. Virtual simulation is utilized to assess novel alloy properties and improve overall wheel performance. Thermal modeling of the low-pressure die-casting process is also investigated to elevate the quality of produced components.
Necessity of the Research:
This research is necessitated by the ongoing demand for enhanced efficiency and quality in alloy wheel manufacturing. By analyzing and modifying existing production methodologies, the aim is to achieve increased added value in the manufacturing process of alloy wheels, addressing critical aspects such as performance, safety, and structural integrity.
4. Research Purpose and Research Questions:
Research Purpose:
The primary purpose of this study is to present a comprehensive overview of the alloy wheel production process and to analyze recent research endeavors aimed at advancing and optimizing these manufacturing techniques.
Key Research:
This paper reviews recent scholarly works concerning the development of alloy wheel production, with a focus on the following key areas:
- Computer Simulation of Casting Process of Aluminum Wheels
- Casting defects in low-pressure die-cast aluminum alloy wheel
- Process capability improvement for aluminum alloy wheel machining
- Analysis of Static Stress in an Alloy Wheel of the Passenger car
- Optimization of Rigidity of Aluminum Alloy Wheels
- Analysis of Alloy properties for the Manufacture of Automotive Wheels
- Simulation of Inner Rim Compression Test of Aluminum Alloy Wheels
- Analysis of the forging processes for 6061 aluminum-alloy wheels
- Development of a 3-D thermal model of the low-pressure die-cast (LPDC) process of A356 aluminum alloy wheels
- Precision forging technology for aluminum alloy
- Finite element simulation and experimental validation of the cracking phenomenon in aluminum alloy wheels
- Effect of Cooling Process on Porosity in the Aluminum Alloy Automotive Wheel During Low-Pressure Die Casting
Research Hypotheses:
While not explicitly stated as formal hypotheses, the reviewed research implicitly investigates the premise that the application of advanced analytical and simulation techniques, such as FEA, thermal modeling, and optimization algorithms, can significantly contribute to the improvement of alloy wheel manufacturing processes across various stages, from casting and machining to forging and quality control.
5. Research Methodology
Research Design:
This study adopts a literature review design, systematically examining and synthesizing existing research publications relevant to the manufacturing processes of car alloy wheels.
Data Collection Method:
The data for this review were collected through a comprehensive search and analysis of peer-reviewed journal articles, conference proceedings, and scholarly publications focusing on alloy wheel manufacturing technologies.
Analysis Method:
The analysis method employed is descriptive summarization. Each selected research paper is analyzed and summarized to extract key findings, methodologies, and conclusions. The summaries are then synthesized to provide an overview of recent advancements and trends in the field.
Research Subjects and Scope:
The research subjects encompass various aspects of alloy wheel manufacturing, including casting, machining, forging, material properties, process optimization, and defect analysis. The scope is limited to research and development activities aimed at enhancing the production processes of alloy wheels, primarily focusing on aluminum alloys and related manufacturing techniques.
6. Main Research Results:
Key Research Results:
This paper summarizes and synthesizes the findings of recent research across several critical areas of alloy wheel manufacturing:
- Computer Simulation of Casting Process: Hsu and Yu [22] utilized casting simulation software to iteratively model the aluminum wheel casting process until mold temperature stabilization. They introduced a "shrinkage index" (SI) to quantify casting quality, correlating well with leakage test results and enabling optimization of casting parameters.
- Casting Defects in Low-Pressure Die-Cast Aluminum Alloy Wheel: Zhang et al. [23] investigated casting-related defects in low-pressure die-cast aluminum wheels, identifying macro- and micro- porosity, entrained oxide films, and exogenous oxide inclusions as key challenges affecting wheel cosmetics, air-tightness, and mechanical performance.
- Process Capability Improvement for Aluminum Alloy Wheel Machining: Sharma et al. [24] applied the DMAIC (Define-Measure-Analyze-Improve-Control) approach to enhance the process capability of A356 aluminum alloy wheel machining. Utilizing Ishikawa diagrams and process failure mode analysis, they achieved significant improvements in process capability indices (Cp, Cpk, Cpm).
- Analysis of Static Stress in an Alloy Wheel of the Passenger car: Nallusamy et al. [25] employed static stress analysis to improve the quality and safety of alloy wheels, using A356 alloy and T6 heat treatment. Their work focused on optimizing the dynamic cornering fatigue test to enhance testing productivity.
- Optimization of Rigidity of Aluminum Alloy Wheels: Kocaturk et al. [26] presented optimization procedures for rigidity parameters of aluminum alloy wheels, utilizing ANSYS Workbench for finite element simulations and Minitab for statistical analysis. Their study aimed to maximize rigidity while minimizing mass increase.
- Analysis of Alloy properties for the Manufacture of Automotive Wheels: Kaba et al. [27] analyzed alloy properties, comparing AlSi7Mg0.3 and AlSi5Mg0.3 alloys. They found that while AlSi5Mg0.3 exhibits smaller grains, AlSi7Mg0.3 offers superior mechanical properties and fluidity, favoring it for industrial applications.
- Simulation of Inner Rim Compression Test of Aluminum Alloy Wheels: Kara and Daysal [28] developed simulations for inner rim compression tests using ABAQUS, comparing simulation results with experimental data to assess fracture and failure behavior, crucial for ensuring wheel safety.
- Analysis of the forging processes for 6061 aluminum-alloy wheels: Kim et al. [29] analyzed forging processes for 6061 aluminum alloy wheels using finite element methods, incorporating thermo-mechanical models and rigid visco-plasticity to simulate metal forming at elevated temperatures and optimize process conditions.
- Development of a 3-D thermal model of the low-pressure die-cast (LPDC) process of A356 aluminum alloy wheels: Zhang et al. [30] developed a 3-D thermal model for the LPDC process using ABAQUS, validated with extensive temperature measurements. The model identified complex heat flow paths and hot spots, aiding in process optimization for increased production capacity.
- Precision forging technology for aluminum alloy: Deng et al. [31] reviewed precision forging technologies for aluminum alloys, highlighting advanced techniques like closed die forging and isothermal die forging to overcome challenges related to deformation characteristics and achieve precision shapes.
- Finite element simulation and experimental validation of the cracking phenomenon in aluminum alloy wheels: Otarawanna et al. [32] used finite element analysis to predict cracking phenomena during wheel impact tests, validating FEA models against experimental results to reduce design time and costs.
- Effect of Cooling Process on Porosity in the Aluminum Alloy Automotive Wheel During Low-Pressure Die Casting: Sui et al. [33] investigated the effect of cooling processes on porosity in low-pressure die casting. Numerical simulation and experiments demonstrated that strategic cooling and insulation can reduce microporosity defects in critical areas.
Analysis of presented data:
The reviewed studies collectively underscore the increasing reliance on computational simulation and analysis tools to optimize and enhance alloy wheel manufacturing processes. From casting and forging to machining and material selection, Finite Element Analysis, thermal modeling, and process simulation are instrumental in identifying and mitigating defects, improving process efficiency, and ensuring product quality and safety. The data presented highlight the multifaceted approach researchers are taking to address challenges in alloy wheel production, leveraging both numerical and experimental methodologies.
Figure Name List:
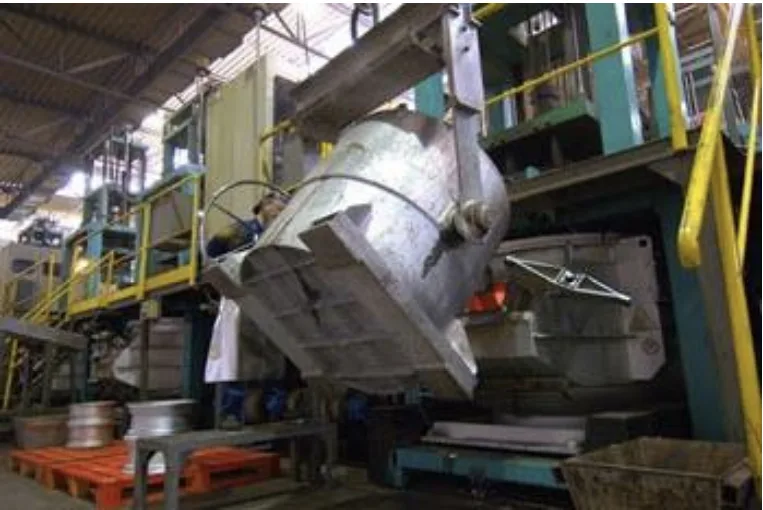
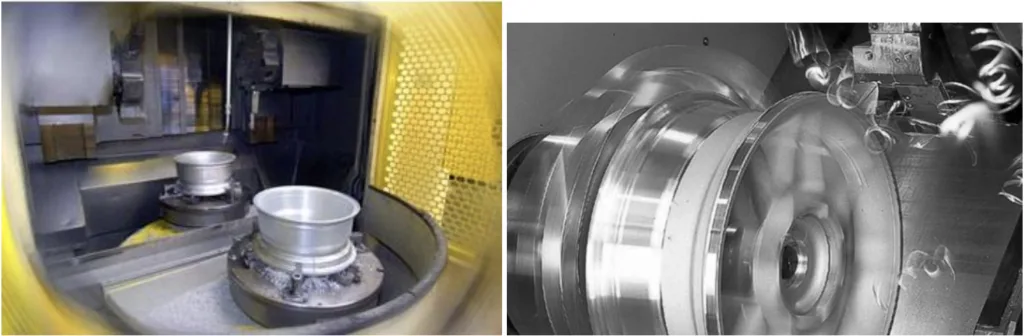
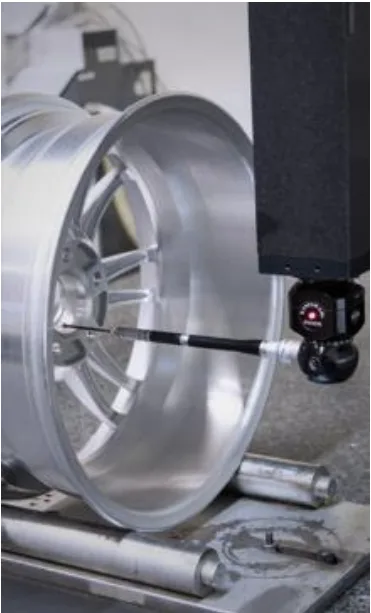
![Fig. 5. CAD models of casting molds for an aluminum disc wheel [22]](https://castman.co.kr/wp-content/uploads/image-655-png.webp)
![Fig. 6. The finite element model of an aluminum wheel and its molds [22].
Temperature distributions of mold during the casting process is shown in the figure 5.](https://castman.co.kr/wp-content/uploads/image-656-1024x377.webp)
![Fig. 7. Temperature distributions of mold during the casting process [22].](https://castman.co.kr/wp-content/uploads/image-657-png.webp)
![Fig. 8. Alloy wheel machining drawing with center hole diameter of ø50.000 (±0.050) [24].](https://castman.co.kr/wp-content/uploads/image-658-1024x551.webp)
![Fig. 12. Contour of the von Mises stress obtained from the simulation without the tire at 850 kg. Arrows mark the location where the von Mises stress is maximum (ignoring the direct impact region) [32].](https://castman.co.kr/wp-content/uploads/image-659-1024x545.webp)
![Fig. 13. Effect of the cooling and insulation process in removing the macroporosity defects in the junctions of prodcuced alloy wheels [33].](https://castman.co.kr/wp-content/uploads/image-660-1024x295.webp)
- Fig. 1. Providing the molten alloys for the casting operation.
- Fig. 2. Casting operation of wheel alloys.
- Fig. 3. Machining operations of wheel alloys.
- Fig. 4. Quality control of produced alloy wheels using the CMM.
- Fig. 5. CAD models of casting molds for an aluminum disc wheel [22].
- Fig. 6. The finite element model of an aluminum wheel and its molds [22].
- Fig. 7. Temperature distributions of mold during the casting process [22].
- Fig. 8. Alloy wheel machining drawing with center hole diameter of ø50.000 (±0.050) [24].
- Fig. 9. Wheel configuration just after forging [29].
- Fig. 10. 30° section mesh of a wheel and die (wheel differentiated by fine mesh size compared to die) [30].
- Fig. 11. Contour plot of temperatures in the (a) wheel and (b) die prior to die-open [30].
- Fig. 12. Contour of the von Mises stress obtained from the simulation without the tire at 850 kg. Arrows mark the location where the von Mises stress is maximum (ignoring the direct impact region) [32].
- Fig. 13. Effect of the cooling and insulation process in removing the macroporosity defects in the junctions of prodcuced alloy wheels [33].
7. Conclusion:
Summary of Key Findings:
This study comprehensively reviewed the manufacturing processes of alloy wheels, emphasizing recent research aimed at process optimization and enhancement. The findings consistently highlight the pivotal role of computer simulation and analysis in advancing alloy wheel production. Research efforts are significantly directed towards mitigating defects in automotive aluminum alloy casting, improving machining efficiency, ensuring structural integrity through static stress analysis, optimizing wheel rigidity, and exploring advanced alloy materials. Thermal modeling of low-pressure die-casting and advancements in forging technologies are also critical areas of focus. Cooling methodologies in low-pressure die casting are identified as crucial for enhancing the quality of produced parts.
Academic Significance of the Study:
This review provides a valuable synthesis of current academic research trends in alloy wheel manufacturing. It underscores the academic community's focus on leveraging virtual simulation and analytical techniques to address manufacturing challenges and improve process understanding. The study serves as a consolidated resource for researchers seeking to understand the state-of-the-art and identify potential future research directions in this domain.
Practical Implications:
The practical implications of the reviewed research are substantial for the alloy wheel manufacturing industry. The studies offer actionable insights and methodologies for manufacturers to refine their production processes, enhance product quality, and improve operational efficiency. The emphasis on virtual simulation and optimization techniques provides cost-effective and time-saving approaches for process development and quality control, potentially leading to significant improvements in manufacturing outcomes.
Limitations of the Study and Areas for Future Research:
As a review paper, this study is inherently limited by its reliance on existing published research and does not include original experimental validation. Future research should focus on the industrial implementation and validation of the summarized techniques in real-world manufacturing environments. Further exploration of novel optimization algorithms, advanced simulation methodologies, and the integration of Industry 4.0 technologies in alloy wheel manufacturing are also recommended areas for future investigation.
8. References:
- 1. Soori M, Arezoo B, Habibi M (2017) Accuracy analysis of tool deflection error modelling in prediction of milled surfaces by a virtual machining system. International Journal of Computer Applications in Technology 55 (4):308-321
- 2. Soori M, Arezoo B, Habibi M (2014) Virtual machining considering dimensional, geometrical and tool deflection errors in three-axis CNC milling machines. Journal of Manufacturing Systems 33 (4):498-507
- 3. Soori M, Arezoo B, Habibi M (2013) Dimensional and geometrical errors of three-axis CNC milling machines in a virtual machining system. Computer-Aided Design 45 (11):1306-1313
- 4. Soori M, Arezoo B, Habibi M (2016) Tool deflection error of three-axis computer numerical control milling machines, monitoring and minimizing by a virtual machining system. Journal of Manufacturing Science and Engineering 138 (8)
- 5. Soori M, Arezoo B (2020) Virtual Machining Systems for CNC Milling and Turning Machine Tools: A Review. International Journal of Engineering and Future Technology 18 (1):56-104
- 6. Soori M, Arezoo B A Review in Machining-Induced Residual Stress.
- 7. Soori M, Arezoo B (2022) NURBS Interpolation Algorithm to Minimize Chord Error in 5-Axis CNC Milling Operations of Turbine Blades.
- 8. Soori M (2019) Virtual product development. GRIN Verlag,
- 9. Dastres R, Soori M (2021) Advances in Web-Based Decision Support Systems. International Journal of Engineering and Future Technology
- Dastres R, Soori M (2021) A Review in Recent Development of Network Threats and Security Measures. International Journal of Computer and Information Engineering 15 (1):75-81
- Dastres R, Soori M (2021) Artificial Neural Network Systems. International Journal of Imaging and Robotics (IJIR) 21 (2):13-25
- Dastres R, Soori M (2021) A Review in Advanced Digital Signal Processing Systems. International Journal of Electrical and Computer Engineering 15 (3):122-127
- Soori M, Asmael M, Solyalı D (2020) Recent Development in Friction Stir Welding Process: A Review. SAE International Journal of Materials and Manufacturing (5):18
- Soori M, Asmael M (2021) Virtual Minimization of Residual Stress and Deflection Error in Five-Axis Milling of Turbine Blades. Strojniski Vestnik/Journal of Mechanical Engineering 67 (5):235-244
- Soori M, Asmael M (2021) Cutting temperatures in milling operations of difficult-to-cut materials. Journal of New Technology and Materials 11 (1):47-56
- Soori M, Asmael M, Khan A, Farouk N (2021) Minimization of surface roughness in 5-axis milling of turbine blades. Mechanics Based Design of Structures and Machines:1-18. doi:10.1080/15397734.2021.1992779
- Soori M, Asmael M (2021) MINIMIZATION OF DEFLECTION ERROR IN FIVE AXIS MILLING OF IMPELLER BLADES. Facta Universitatis, series: Mechanical Engineering. doi:10.22190/FUME2108220695
- Soori M, Asmael M (2022) A Review of the Recent Development in Machining Parameter Optimization. Jordan Journal of Mechanical & Industrial Engineering 16 (2):205-223
- Dastres R, Soori M, Asmael M (2022) RADIO FREQUENCY IDENTIFICATION (RFID) BASED WIRELESS MANUFACTURING SYSTEMS, A REVIEW. Independent Journal of Management & Production 13 (1):258-290
- Dastres R, Soori M (2021) Advances in Web-Based Decision Support Systems. International Journal of Engineering and Future Technology 19 (1):1-15
- Dastres R, Soori M (2021) The Role of Information and Communication Technology (ICT) in Environmental Protection. International Journal of Tomography and Simulation 35 (1):24-37
- Hsu Y-L, Yu C-C (2006) Computer simulation of casting process of aluminium wheels-a case study. Proceedings of the Institution of Mechanical Engineers, Part B: Journal of Engineering Manufacture 220 (2):203-211
- Zhang B, Cockcroft S, Maijer D, Zhu J, Phillion A (2005) Casting defects in low-pressure die-cast aluminum alloy wheels. Jom 57 (11):36-43
- Sharma G, Rao PS, Babu BS (2018) Process capability improvement through DMAIC for aluminum alloy wheel machining. Journal of Industrial Engineering International 14 (2):213-226
- Nallusamy S, Prabu NM, Balakannan K, Majumdar G Analysis of Static Stress in an Alloy Wheel of the Passengercar. In: International Journal of Engineering Research in Africa, 2015. Trans Tech Publ, pp 17-25
- Kocaturk O, Elagoz FY, Kara A Optimization of Rigidity of Aluminum Alloy Wheels. In: Fracture, Fatigue and Wear, 2018. Springer, pp 814-819
- Kaba M, Donmez A, Cukur A, Kurban A, Cubuklusu H, Birol Y (2018) AlSi5Mg0. 3 Alloy for the manufacture of automotive wheels. International Journal of Metalcasting 12 (3):614-624
- Kara A, Daysal O Simulation of Inner Rim Compression Test of Aluminum Alloy Wheels. In: Key Engineering Materials, 2018. Trans Tech Publ, pp 379-384
- Kim Y, Ryou T, Choi H, Hwang B (2002) An analysis of the forging processes for 6061 aluminum-alloy wheels. Journal of Materials Processing Technology 123 (2):270-276
- Zhang B, Maijer D, Cockcroft S (2007) Development of a 3-D thermal model of the low-pressure die-cast (LPDC) process of A356 aluminum alloy wheels. Materials Science and Engineering: A 464 (1-2):295-305
- Deng L, Wang X, Jin J, Xia J (2018) Precision forging technology for aluminum alloy. Frontiers of Mechanical Engineering 13 (1):25-36
- Otarawanna S, Uttamung P, Malatip A Finite element simulation and experimental validation of the cracking phenomenon in aluminium alloy wheels during the impact test. In: AIP Conference Proceedings, 2018. vol 1. AIP Publishing LLC, p 020303
- Sui D, Cui Z, Wang R, Hao S, Han Q (2016) Effect of cooling process on porosity in the aluminum alloy automotive wheel during low-pressure die casting. International Journal of Metalcasting 10 (1):32-42
9. Copyright:
- This material is "Mohsen Soori"'s paper: Based on "Manufacturing Processes of Car Alloy Wheels".
- Paper Source: https://hal.science/hal-03740879v1
This material was summarized based on the above paper, and unauthorized use for commercial purposes is prohibited.
Copyright © 2025 CASTMAN. All rights reserved.