This introductory paper is the research content of the paper "Local stress/strain field analysis of die-casting Al alloys via 3D model simulation with realistic defect distribution and RVE modelling" published by [Publisher is not included in the paper].
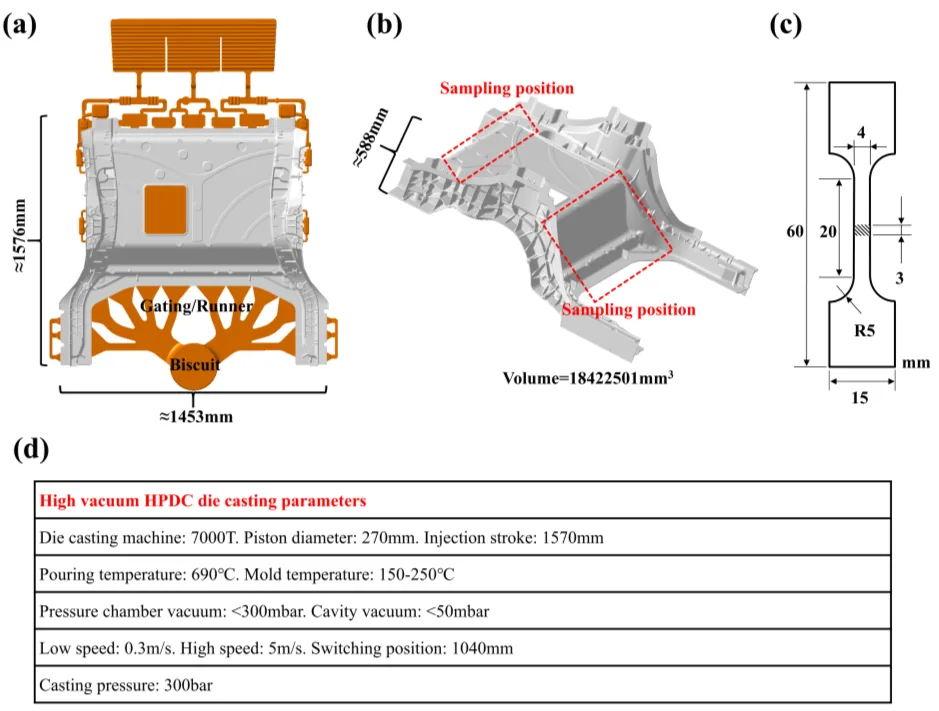
1. Overview:
- Title: Local stress/strain field analysis of die-casting Al alloys via 3D model simulation with realistic defect distribution and RVE modelling
- Author: Jian Yang, Bo Liu, Dongwei Shu, Qin Yang, Tiegang Hu
- Publication Year: 2024
- Published Journal/Society: Preprint.
- Keywords: Die-casting; Aluminium alloy; Representative volume element; X-ray computed tomography; Automotive lightweighting.
2. Abstract
The deformation and fracture behavior of die-casting aluminium (Al) alloys is very complex. Due to local variations in properties, the microstructure and mechanical behavior of materials are highly anisotropic. In this paper, an attempt has been made to quantitatively study the defect characteristics of high pressure cast Al alloy parts using experimental and finite element calculation methods, and to analysis the effect of local porosity and pore size on plasticity. Three-dimensional solids with real defect distribution are obtained by using 3D X-ray computed tomography, and used as an input for building a finite element model. The damage initiation of cast Al alloys under complex stress states is analyzed from micro to macro scales. Crack propagation occurs through two modes of microporous agglomeration: aggregated pores produce cracks from internal necking and stress concentration. Then, they expand in the same direction, agglomerate in a specific direction and eventually fracture. Subsequently, the effect of porosity on non-homogeneity was elucidated by obtaining local stress/strain behavior through digital image correlation measurements. Additionally, a theoretical framework of elasto-plastic deformation of microstructures and a 3D representative volume element model are developed to simulate the deformation and damage processes under cyclic boundary conditions of materials. The simulation results show that the local stress/strain around the pores evolves gradually with deformation. During the die casting process, the method demonstrates the ability to predict the mechanical behavior of Al alloys.
3. Research Background:
Background of the research topic:
Die-casting aluminium (Al) alloys are used for lightweighting in the automotive and aerospace industries[1]. High pressure die-casting (HPDC) is a key manufacturing process for Al alloy parts[2, 3]. However, porosity-type defects can affect the mechanical properties of the product[4, 5]. The presence of porosity leads to microstructural discontinuities, which increase the possibility of localised stress concentrations[6-8].
Status of previous research:
Many researchers have used a combination of experimental and finite element simulation to investigate the effect of microscopic defects with macroscopic mechanical properties[12].
- Sun[13] investigated the effect of microporosity on the tensile properties and fracture behavior of AM50 alloys.
- Jiang[14] investigated the relationship between porosity and mechanical properties of HPDC AZ91 magnesium alloy.
- Zhang[7] developed a 3D finite element model based on real defects.
- Zhang[16] verified the deformation and fracture behaviour of non-uniform structures using numerical simulations and DIC testing.
- Zhang[17] investigated the spatial distribution and morphological characteristics of porosity in Al-10 Si-0. 3 Mg parts and its effect on plasticity.
- Sun[20] simulated the influence of porosity, pore size and distribution on the damage effect under different working conditions.
- Ma[21] established the constitutive equations of die-casting Al alloys.
- Numerous studies have shown that microstructure inhomogeneity is a key factor influencing the damage initiation behavior of materials[22-26].
Need for research:
The accuracy of the finite element simulation needs to be improved due to boundary conditions and macroscopic factors.
4. Research purpose and research question:
Research purpose:
This study focuses on the damage initiation cracking of cast Al alloys under complex stress states, and proposes a framework that combines experimental analysis and computational modelling.
Core research:
- Quantitative study of the three-dimensional characteristics of the pores of HPDC parts is carried out in this study using X-ray CT technique.
- The effects of local porosity, pore size and location on plasticity are analyzed.
- Inverse modelling is performed based on images of the internal pores captured by X-ray CT technology.
- Numerical results from models based on real defect distributions are compared with local stress/strain behaviour obtained from DIC measurements.
- The theoretical framework of elastic-plastic deformation of 3D microstructures and the RVE model are established to simulate the deformation and damage processes under the cyclic boundary conditions.
5. Research methodology
The research framework is presented in Fig. 1. The research is divided into three main parts:
- Defect Analysis: X-ray CT scanning is used to quantitatively analyze the size and spatial distribution of defects.
- Inverse Modeling and Simulation: 3D images of internal pores (from X-ray CT) are used to create a solid model with a realistic defect distribution. The relationship between defects and mechanical properties is explored through simulation, elucidating fracture mechanisms.
- RVE Modeling: An RVE model is built to simulate deformation and damage processes under cyclic boundary conditions.
Experimental Methods:
- Materials Selection: Non-heat treatment die-casting Al alloy (Al-9Si, Al-7Si) was selected. The chemical composition was determined using an inductively coupled plasma emission spectrometer (PerkinElmer Optima 8300) (Table 1).
- HPDC Experiment: A YIZUMI LEAP 7000T horizontal cold chamber die casting machine was used. Process parameters are detailed in Fig. 2.
- X-ray CT Scanning and Inverse Modeling: X-ray CT (XPloreVista 2000 4D) was used to explore pore size, morphology, and location, following standards ASTM E505, ASTM E2422, and CASE 301-2023. The inverse modeling process is described in Fig. 3, involving steps in AVIZO and ABAQUS software.
- Tensile Test and DIC Test: Tensile tests were performed using an MTS C45.305EEEY machine. A HAYTHAM DV 1200-32 system was used for displacement measurement. Digital Image Correlation (DIC) was used to correlate strain distribution with pore deformation.
- Elastic plastic material behavior law:
The J2 isotropic elasto-plastic model was used to investigate the intrinsic behavior of the Al matrix.
According to Eq. (1), a value of n of 0.15 and a value of K of 356 can be fitted.
6. Key research results:
Key research results and presented data analysis:
- Porosity Characterization: X-ray CT scanning revealed the spatial distribution and morphology of defects (Fig. 5). Defects were classified as gas pores, shrinkage pores, and gas-shrinkage pores[32-34] based on volume and sphericity (Eq. 2). Most defects were identified as gas pores. Relationships between volume and sphericity, and volume and projected area, are shown in Fig. 6.
- Plastic Deformation Analysis with Real Defects: A volumetric mesh with realistic pore characteristics was used in finite element simulations. Fig. 7 shows the simulation flow chart and results. The simulation model accurately predicted the matrix brittle fracture mode.
- Comparison of Simulation and Experiment: Simulated and experimental fracture results were compared (Table 2, Fig. 8). The CAE model with real defect distribution showed improved accuracy compared to a model without defects.
- Deformation and Microcrack Formation Mechanism: The deformation of gas pores and the mechanism of microcrack formation are shown in Fig. 9. Crack extension occurs through two modes of microporosity aggregation.
- Relationship between Pore Characteristics and Local Strain: DIC analysis showed localized areas of high strain, correlating with defect distribution (Fig. 10).
- 3D microscale RVE model development:
3D RVE models of cast Al alloys were generated using Digimat software. The setup parameters of the RVE model are given in Fig. 11(a). - Representative volume element predictions:
The RVE models and simulation results with different pore volume fractions are shown in Fig. 13.
Fig. 14 shows a schematic diagram of pore deformation and damage at different volumetric porosities.
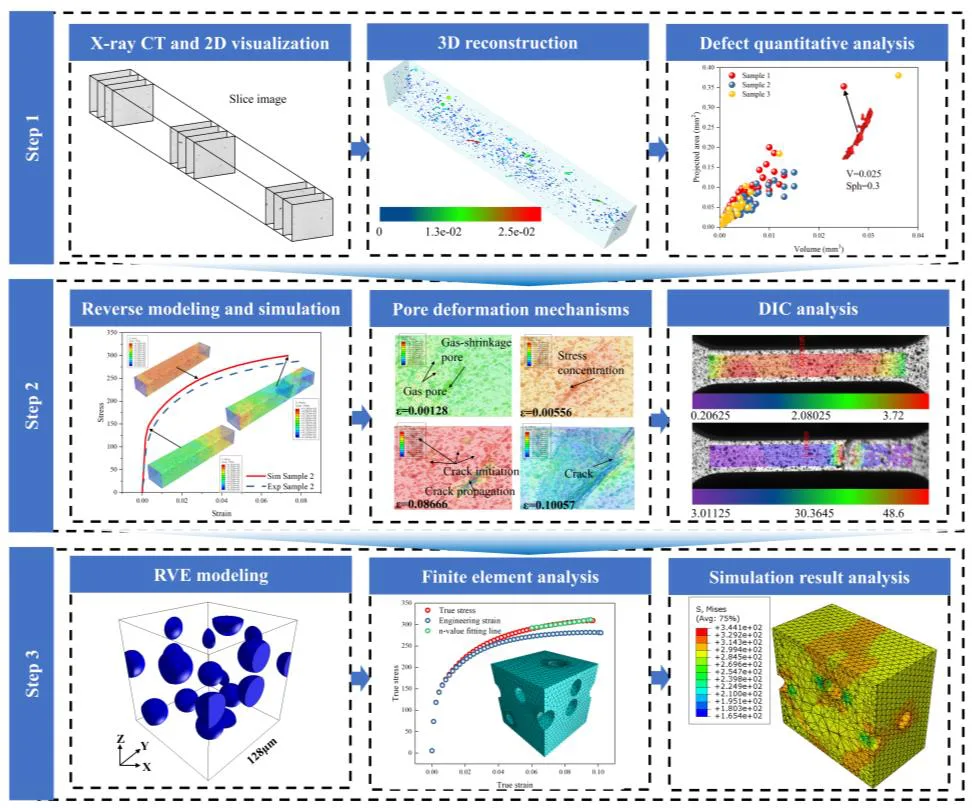
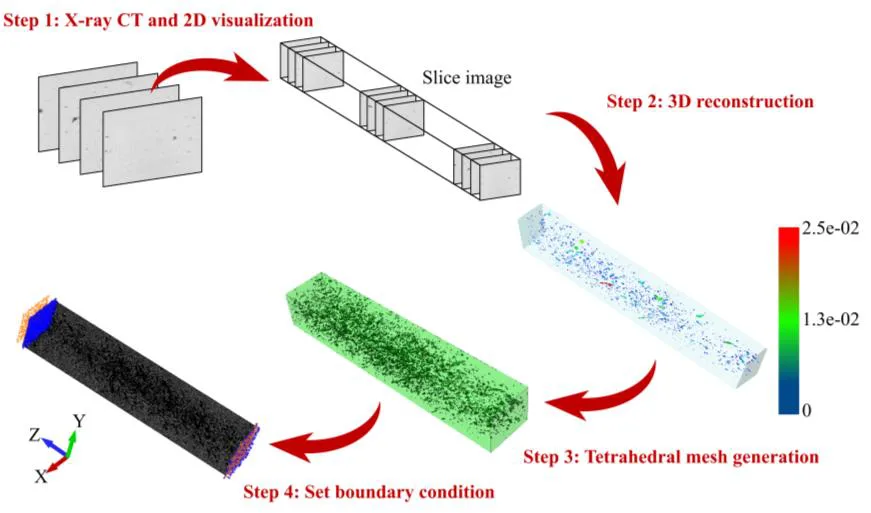
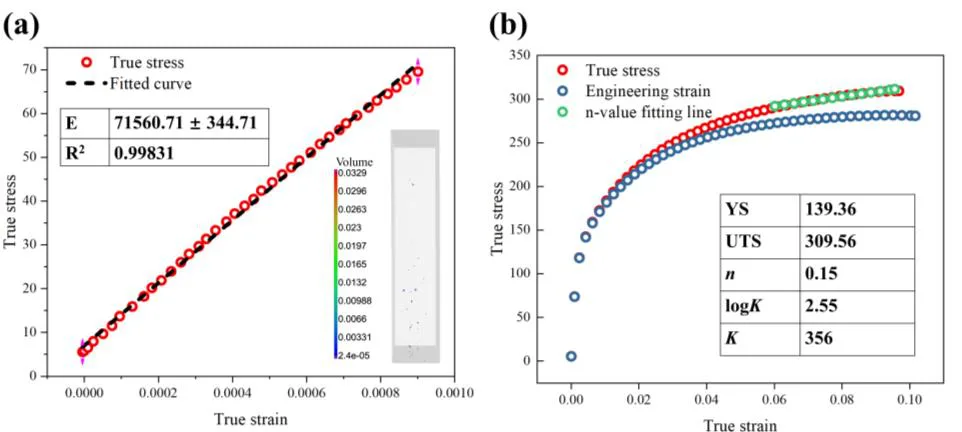
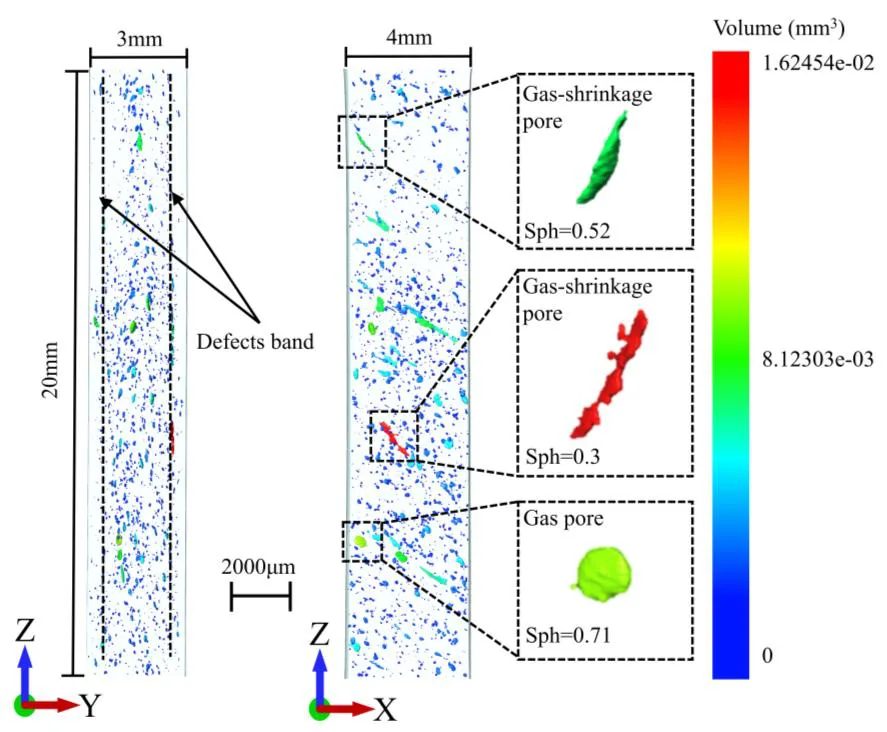
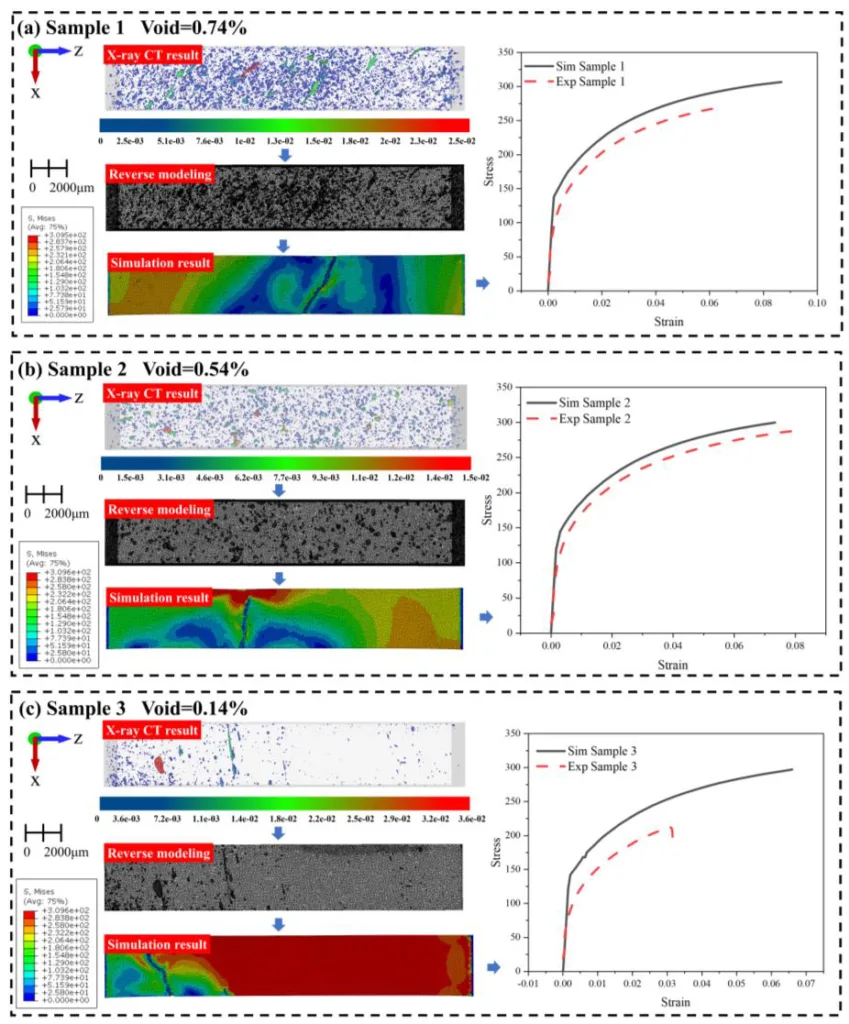
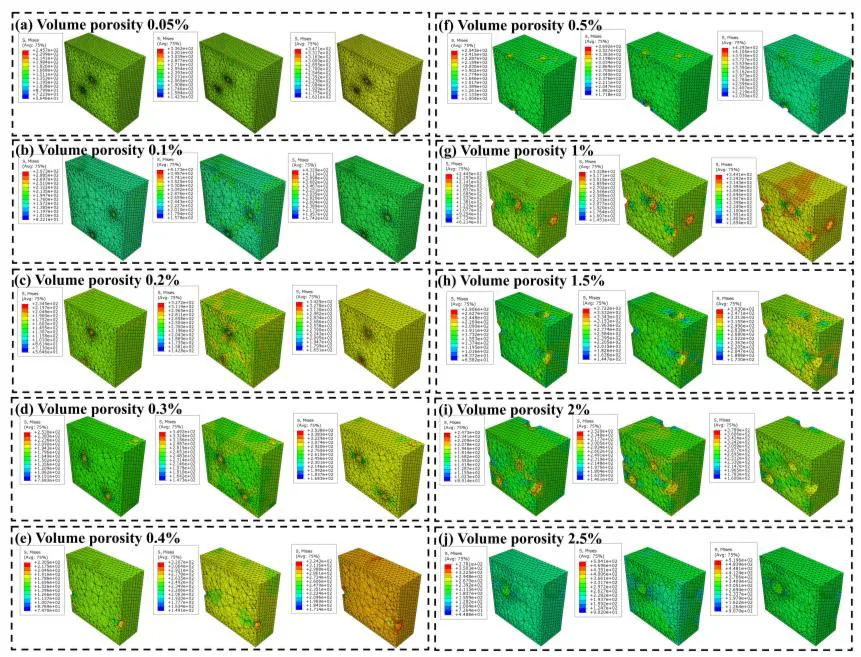
List of figure names:
- Figure 1: Research idea framework for this study.
- Figure 2: Part structure, dimensions and process parameters.
- Figure 3: Inverse modelling method for finite element volumetric meshing and method of setting boundary conditions.
- Figure 4: Elastic-plastic material behavior law.
- Figure 5: Spatial distribution and morphological characteristics of defects
- Figure 6: Quantitative statistical analysis of defects.
- Figure 7: Inverse modelling steps and simulation analysis results.
- Figure 8: Mechanical property data and statistical results.
- Figure 9: Deformation and microcrack formation mechanism of gas pores.
- Figure 10: Simulation, tensile experiment and DIC analysis.
- Figure 11: Setting parameters of the RVE model.
- Figure 12: Schematic representation of the periodic boundary conditions.
- Figure 13: RVE models with different porosities and simulation results.
- Figure 14: Schematic representation of porosity deformation and damage at different porosities.
7. Conclusion:
Summary of key findings:
- A 3D model with real pore morphology was obtained using X-ray CT and inverse modeling. Simulation accuracy was significantly improved compared to a model without defects.
- The simulation model accurately predicted the matrix brittle fracture mode during tensile fracture. Aggregated porosity produces cracks from internal necking and stress concentrations.
- A 3D RVE model was developed and integrated with a finite element elasto-plastic deformation framework. When porosity increases, there is an abnormal accumulation of plastic strain in the local region.
- The method provides significant advantages for the study of pore sprouting mechanisms, fracture modes and macroscopic property prediction of die-casting Al alloys.
8. References:
- [1] J. Allison, M. Li, C. Wolverton, and X. Su, "Virtual aluminum castings: an industrial application of ICME," Jom, vol. 58, pp. 28-35, 2006.
- [2] S. Dash, D. Li, X. Zeng, and D. Chen, "Heterogeneous microstructure and deformation behavior of an automotive grade aluminum alloy," Journal of Alloys and Compounds, vol. 870, p. 159413, 2021.
- [3] T. Li et al., "Progress and prospects in Mg-alloy super-sized high pressure die casting for automotive structural components," Journal of Magnesium and Alloys, 2023.
- [4] X. Hu and L. Xie, "FEA Simulations of Temperature Changes of Castings When Solidified and Cooled in Mould," in Advances in Computer Science and Education Applications: International Conference, CSE 2011, Qingdao, China, July 9-10, 2011. Proceedings, Part II, 2011: Springer, pp. 178-183.
- [5] Q. Pan, L. Zheng, Y. Sang, Y. Li, L. Zhou, and H. Zhang, "Effect of casting temperature on microstructure in a directionally solidified Ni-44Ti-5Al-2Nb-1Mo alloy," Rare Metals, vol. 30, pp. 349-353, 2011.
- [6] Y. Tijani, A. Heinrietz, T. Bruder, and H. Hanselka, "Quantitative evaluation of fatigue life of cast aluminum alloys by non-destructive testing and parameter model," International journal of fatigue, vol. 57, pp. 73-78, 2013.
- [7] Y. Zhang et al., "Analysis of local stress/strain fields in an HPDC AM60 plate containing pores with various characteristics," Engineering Failure Analysis, vol. 127, p. 105503, 2021.
- [8] G. Nicoletto, R. Konečná, and S. Fintova, "Characterization of microshrinkage casting defects of Al-Si alloys by X-ray computed tomography and metallography," International journal of fatigue, vol. 41, pp. 39-46, 2012.
- [9] Y. Zhang et al., "The gradient microstructure and deformation heterogeneity in HPDC AM60 alloy," Materials Science and Engineering: A, vol. 792, p. 139647, 2020.
- [10] J. H. Forsmark, J. W. Zindel, L. Godlewski, J. Zheng, J. E. Allison, and M. Li, "Using quality mapping to predict spatial variation in local properties and component performance in Mg alloy thin-walled high-pressure die castings: an ICME approach and case study," Integrating Materials and Manufacturing Innovation, vol. 4, pp. 81-118, 2015.
- [11] G. Hahn and A. Rosenfield, "Metallurgical factors affecting fracture toughness of aluminum alloys," Metallurgical Transactions A, vol. 6, pp. 653-668, 1975.
- [12] M. Luetje, M. Wicke, I. Bacaicoa, A. Brueckner-Foit, A. Geisert, and M. Fehlbier, "3D characterization of fatigue damage mechanisms in a cast aluminum alloy using X-ray tomography," International Journal of Fatigue, vol. 103, pp. 363-370, 2017.
- [13] X. Sun, Z. Cao, H. Liu, W. Jiang, and L. Liu, "Predicting the influence of microporosity on the mechanical properties and fracture behavior of high-pressure die-cast AM50 magnesium alloy," Applied Mechanics and Materials, vol. 670, pp. 90-94, 2014.
- [14] W. Jiang, Z. Cao, X. Sun, and H. Liu, "Three-dimensional microstructure reconstruction and finite element simulation of gas pores in the high-pressure die-casting AZ91 Mg alloy," Microscopy and Microanalysis, vol. 21, no. 6, pp. 1420-1425, 2015.
- [15] Y. Zhang et al., "Porosity quantification for ductility prediction in high pressure die casting AM60 alloy using 3D X-ray tomography," Materials Science and Engineering: A, vol. 772, p. 138781, 2020.
- [16] Y. Zhang et al., "Ductility prediction of HPDC aluminum alloy using a probabilistic ductile fracture model," Theoretical and Applied Fracture Mechanics, vol. 119, p. 103381, 2022.
- [17] Y. Zhang et al., "Quantitative analysis of 3D pore characteristics effect on the ductility of HPDC Al-10Si-0.3 Mg alloy through X-ray tomography," Journal of Materials Research and Technology, vol. 26, pp. 8079-8096, 2023.
- [18] S. Isavand and A. Assempour, "Strain localization and deformation behavior in ferrite-pearlite steel unraveled by high-resolution in-situ testing integrated with crystal plasticity simulations," International Journal of Mechanical Sciences, vol. 200, p. 106441, 2021.
- [19] S. Isavand and A. Assempour, "Effects of microstructural morphology on formability, strain localization, and damage of ferrite-pearlite steels: experimental and micromechanical approaches," Metallurgical and Materials Transactions A, vol. 52, pp. 711-725, 2021.
- [20] D. Z. Sun, Y. S. Ma, and F. Andrieux, "Modeling of the influence of pore morphology on damage behavior of an aluminum die casting alloy," in Materials Science Forum, 2014, vol. 794: Trans Tech Publ, pp. 319-324.
- [21] Y.-S. Ma, D.-Z. Sun, F. Andrieux, and K.-S. Zhang, "Influences of initial porosity, stress triaxiality and Lode parameter on plastic deformation and ductile fracture," acta mechanica solida sinica, vol. 30, pp. 493-506, 2017.
- [22] J. Lian, H. Yang, N. Vajragupta, S. Münstermann, and W. Bleck, "A method to quantitatively upscale the damage initiation of dual-phase steels under various stress states from microscale to macroscale," Computational materials science, vol. 94, pp. 245-257, 2014.
- [23] Y. Abdin, S. Lomov, A. Jain, G. Van Lenthe, and I. Verpoest, "Geometrical characterization and micro-structural modeling of short steel fiber composites," Composites Part A: Applied Science and Manufacturing, vol. 67, pp. 171-180, 2014.
- [24] S. A. H. Motaman, F. Roters, and C. Haase, "Anisotropic polycrystal plasticity due to microstructural heterogeneity: A multi-scale experimental and numerical study on additively manufactured metallic materials," Acta Materialia, vol. 185, pp. 340-369, 2020.
- [25] S. J. Wolff, S. Lin, E. J. Faierson, W. K. Liu, G. J. Wagner, and J. Cao, "A framework to link localized cooling and properties of directed energy deposition (DED)-processed Ti-6Al-4V," Acta Materialia, vol. 132, pp. 106-117, 2017.
- [26] S. Isavand, M. Kardan-Halvaei, and A. Assempour, "Crystal plasticity modeling and experimental characterization of strain localization and forming limits in ferrite-pearlite steels," International Journal of Solids and Structures, vol. 233, p. 111205, 2021.
- [27] R. Liu et al., "Influence of pore characteristics and eutectic particles on the tensile properties of Al-Si-Mn-Mg high pressure die casting alloy," Materials Science and Engineering: A, vol. 783, p. 139280, 2020.
- [28] T. Li et al., "Anisotropic cyclic deformation behavior of an extruded Mg-3Y alloy sheet with rare earth texture," Journal of Magnesium and Alloys, vol. 10, no. 6, pp. 1581-1597, 2022.
- [29] Y. Xia et al., "The ductility variation of high-pressure die-cast AE44 alloy: the role of inhomogeneous microstructure," Metallurgical and Materials Transactions A, vol. 52, pp. 2274-2286, 2021.
- [30] Z. Li et al., "Characterization on the formation of porosity and tensile properties prediction in die casting Mg alloys," Journal of Magnesium and Alloys, vol. 10, no. 7, pp. 1857-1867, 2022.
- [31] E. Fiorese, F. Bonollo, G. Timelli, L. Arnberg, and E. Gariboldi, "New classification of defects and imperfections for aluminum alloy castings," International Journal of Metalcasting, vol. 9, pp. 55-66, 2015.
- [32] D. Cocks, "A proposed simple qualitative classification for die-casting defects," in Proc. Diecasting Conference, Montreaux, 1996, p. 19.
- [33] J. Campbell, Castings. Elsevier, 2003.
- [34] W. G. Walkington, Die casting defects.. Causes and solutions. NADCA, 1997.
- [35] M. Avalle, G. Belingardi, M. P. Cavatorta, and R. Doglione, "Casting defects and fatigue strength of a die cast aluminium alloy: a comparison between standard specimens and production components," International journal of Fatigue, vol. 24, no. 1, pp. 1-9, 2002.
- [36] S. G. Lee and A. M. Gokhale, "Formation of gas induced shrinkage porosity in Mg-alloy high-pressure die-castings," Scripta Materialia, vol. 55, no. 4, pp. 387-390, 2006.
- [37] E. Lordan et al., "On the probabilistic nature of high-pressure die casting," Materials Science and Engineering: A, vol. 817, p. 141391, 2021.
- [38] Y.-T. Yang et al., "Al-enabled properties distribution prediction for high-pressure die casting Al-Si alloy," Advances in Manufacturing, pp. 1-12, 2024.
- [39] M. M. Thakur, N. A. Henningsson, J. Engqvist, P.-O. Autran, J. P. Wright, and R. C. Hurley, "On mesoscale modeling of concrete: Role of heterogeneities on local stresses, strains, and representative volume element," Cement and Concrete Research, vol. 163, p. 107031, 2023.
- [40] W. Zhang, H. Jing, L. Xu, L. Zhao, Y. Han, and C. Li, "Numerical investigation of creep crack initiation in P92 steel pipes with embedded spherical defects under internal pressure at 650° С," Engineering Fracture Mechanics, vol. 139, pp. 40-55, 2015.
- [41] V. Poroshin and A. Shlishevsky, "The forecasting of deformational and strength properties of metals with uniformly scattered defects in form of spherical hollows at single and cyclic loading," Materials Today: Proceedings, vol. 11, pp. 58-65, 2019.
- [42] F. Klein and P. Wimmer, "Experimental Determination of the Influence of Casting Conditions on the Solidifaction of Zinc Die Castings," in Materials Science Forum, 1996, vol. 215: Trans Tech Publ, pp. 409-414.
- [43] J. Weiler and J. Wood, "Modeling the tensile failure of cast magnesium alloys," Journal of alloys and compounds, vol. 537, pp. 133-140, 2012.
- [44] S. Mohd, Y. Mutoh, Y. Otsuka, Y. Miyashita, T. Koike, and T. Suzuki, "Scatter analysis of fatigue life and pore size data of die-cast AM60B magnesium alloy," Engineering Failure Analysis, vol. 22, pp. 64-72, 2012.
- [45] F. Nichols, "Plastic instabilities and uniaxial tensile ductilities," Acta metallurgica, vol. 28, no. 6, pp. 663-673, 1980.
- [46] J. Lian and J. Chen, "Plastic instability and strain to fracture for damaged materials," Materials Science and Engineering: A, vol. 131, no. 1, pp. 9-15, 1991.
- [47] C. Hamilton, "Superplasticity," in Strength of Metals and Alloys (ICSMA 7): Elsevier, 1986, pp. 1831-1857.
- [48] I. Serrano-Munoz, J.-Y. Buffiere, C. Verdu, Y. Gaillard, P. Mu, and Y. Nadot, "Influence of surface and internal casting defects on the fatigue behaviour of A357-T6 cast aluminium alloy," International Journal of Fatigue, vol. 82, pp. 361-370, 2016.
- [49] Z. Xu, W. Wen, and T. Zhai, "Effects of pore position in depth on stress/strain concentration and fatigue crack initiation," Metallurgical and Materials Transactions A, vol. 43, pp. 2763-2770, 2012.
- [50] Y. Zhang et al., "Microstructure-property relationships in HPDC Aural-2 alloy: Experimental and CP modeling approaches," Materials Science and Engineering: A, vol. 848, p. 143364, 2022.
- [51] P. M. Carneiro, P. V. Gamboa, C. Baudín, and A. P. Silva, "Modelling of elastic modulus of a biphasic ceramic microstructure using 3D representative volume elements," Journal of the European Ceramic Society, vol. 40, no. 3, pp. 901-910, 2020.
- [52] G. Chen, A. Bezold, and C. Broeckmann, "Influence of the size and boundary conditions on the predicted effective strengths of particulate reinforced metal matrix composites (PRMMCs)," Composite Structures, vol. 189, pp. 330-339, 2018.
- [53] Q. Sun, S. Asqardoust, A. Sarmah, and M. K. Jain, "Elastoplastic analysis of AA7075-0 aluminum sheet by hybrid micro-scale representative volume element modeling with really-distributed particles and in-situ SEM experimental testing," Journal of Materials Science & Technology, vol. 123, pp. 201-221, 2022.
- [54] A. Moumen, M. Jammoukh, L. Zahiri, and K. Mansouri, "Numerical modeling of the thermo mechanical behavior of a polymer reinforced by horn fibers," Int. J, vol. 9, no. 4, 2020.
- [55] V. Felli, B. Noris, and R. Ognibene, "Eigenvalues of the Laplacian with moving mixed boundary conditions: the case of disappearing Dirichlet region," Calculus of Variations and Partial Differential Equations, vol. 60, pp. 1-33, 2021.
- [56] E. Totry, C. González, and J. LLorca, "Failure locus of fiber-reinforced composites under transverse compression and out-of-plane shear," Composites Science and Technology, vol. 68, no. 3-4, pp. 829-839, 2008.
- [57] Q. Sun et al., "Failure criteria of unidirectional carbon fiber reinforced polymer composites informed by a computational micromechanics model," Composites Science and Technology, vol. 172, pp. 81-95, 2019.
- [58] S. L. Kramer et al., "The third Sandia Fracture Challenge: predictions of ductile fracture in additively manufactured metal," International Journal of Fracture, vol. 218, pp. 5-61, 2019.
- [59] D. P. Naragani, J.-S. Park, P. Kenesei, and M. D. Sangid, "Void coalescence and ductile failure in IN718 investigated via high-energy synchrotron X-ray tomography and diffraction," Journal of the Mechanics and Physics of Solids, vol. 145, p. 104155, 2020.
- [60] O. West, J. Lian, S. Münstermann, and W. Bleck, "Numerical determination of the damage parameters of a dual-phase sheet steel," ISIJ international, vol. 52, no. 4, pp. 743-752, 2012.
- [61] V. Brinnel, J. Langenberg, F. Kordtomeikel, Y. Di, and S. Münstermann, "Numerical derivation of strain-based criteria for ductile failure: Discussions on sensitivity and validity," Engineering Fracture Mechanics, vol. 148, pp. 421-440, 2015.
9. Copyright:
- This material is a paper by "Jian Yang, Bo Liu, Dongwei Shu, Qin Yang, Tiegang Hu": Based on "Local stress/strain field analysis of die-casting Al alloys via 3D model simulation with realistic defect distribution and RVE modelling".
- Source of paper: https://ssrn.com/abstract=4968855
This material was created to introduce the above paper, and unauthorized use for commercial purposes is prohibited. Copyright © 2025 CASTMAN. All rights reserved.