This article introduces the paper ["INVESTIGATION ON THE EFFECTS OF INNOVATIVE MELT TREATMENTS ON MICROSTRUCTURE AND MECHANICAL BEHAVIOUR OF DIECAST AL ALLOYS"] published by ['UNIVERSITÀ DEGLI STUDI DI PADOVA and AALEN HOCHSCHULE FÜR TECHNIK UND WIRTSCHAFT'].
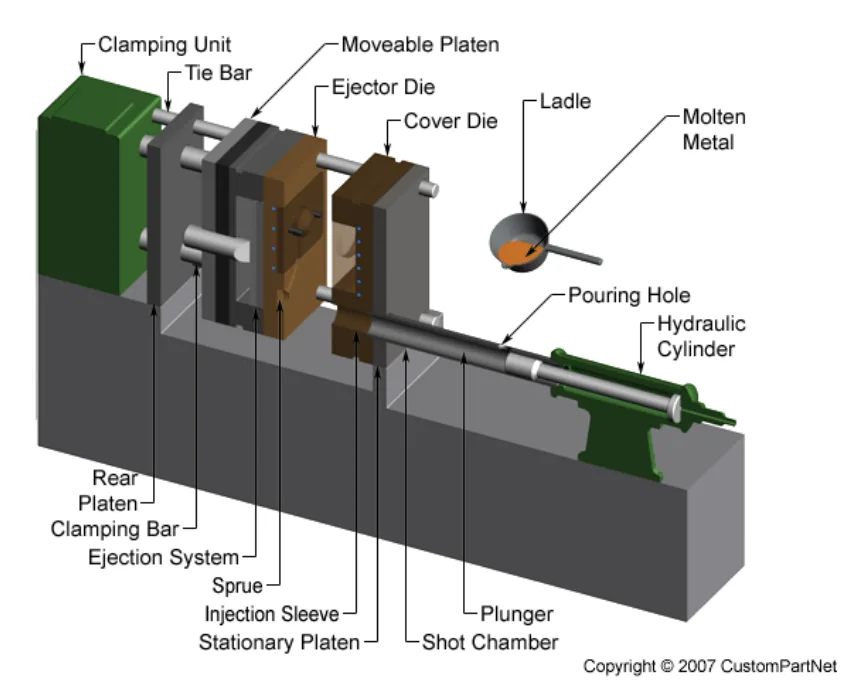
1. Overview:
- Title: INVESTIGATION ON THE EFFECTS OF INNOVATIVE MELT TREATMENTS ON MICROSTRUCTURE AND MECHANICAL BEHAVIOUR OF DIECAST AL ALLOYS
- Author: Alberto Dal Maso, Prof. Dr. Ing. Lothar H. Kallien, Prof. Ing. Franco Bonollo
- Publication Year: Academic year 2011 – 2012
- Publishing Journal/Academic Society: UNIVERSITÀ DEGLI STUDI DI PADOVA, CORSO DI LAUREA MAGISTRALE IN INGEGNERIA DELL’INNOVAZIONE DEL PRODOTTO
- Keywords: die casting, aluminum alloys, melt treatment, microstructure, mechanical behaviour, Al2O3 particles, in-situ process
2. Abstracts or Introduction
The research on innovative materials with enhanced performance is pivotal across numerous sectors. A common strategy for improving material characteristics involves combining complementary materials to achieve superior performance, a principle underlying composite material research. Metal-matrix composites (MMC) are particularly interesting due to their performance and processing versatility. This study investigates an innovative melt treatment on molten aluminium to produce aluminum oxide (Al2O3) particles in situ, aiming to disperse them within the melt and incorporate them into the solidified metal. The use of Al2O3 as reinforcement is explored for its dual benefits: mechanical reinforcement, enhancing hardness, strength, and elastic modulus of aluminum alloys, and as a grain refining agent, improving alloy performance through a finer microstructure. The research examines the treatment's effect on pure aluminum and Al-Cu alloys, tested in both permanent mold and high-pressure die casting (HPDC). The HPDC process, crucial for producing Al, Mg, and Zn alloy components, involves high-pressure injection of molten alloy into steel dies. Recent advancements in HPDC, such as vacuum and semi-solid metal casting, have improved casting quality. Al-Cu alloys, known for their strength and ductility, are widely used in both wrought and cast forms, benefiting from precipitation hardening. However, they exhibit hot cracking susceptibility and corrosion issues. The melt treatment, involving argon and oxygen injection into molten aluminum, aims to form and disperse Al2O3 particles to enhance alloy properties and microstructure.
3. Research Background:
Background of the Research Topic:
The development of innovative materials is crucial in engineering, with metal-matrix composites (MMCs) gaining prominence due to their enhanced properties and versatile processing. Aluminum alloys, particularly Al-Cu alloys, are essential in both wrought and cast applications, offering high strength and toughness. High Pressure Die Casting (HPDC) is a vital process for manufacturing components from alloys based on Al, Mg, or Zn, especially for automotive and other high-volume industries. Improving the mechanical properties and reducing defects in die-cast aluminum alloys are ongoing areas of research.
Status of Existing Research:
Existing research in material science focuses on enhancing material properties through methods like combining materials in composites. Metal matrix composites, especially those reinforced with ceramic phases like Al2O3, are well-documented for improved strength, hardness, and high-temperature performance. Prior studies have explored Al2O3 reinforced MMCs produced via in-situ and ex-situ methods. Research also indicates that Al2O3 particles can act as grain refiners in Al-Cu alloys, potentially reducing hot cracking. Innovations in HPDC, such as vacuum-assisted and semi-solid HPDC, aim to reduce defects and improve part quality. However, challenges remain in producing cost-effective and industrially scalable methods for creating and dispersing nanoscale reinforcements in metal matrices.
Necessity of the Research:
Despite advancements in HPDC and Al-Cu alloys, limitations such as hot cracking susceptibility, porosity, and corrosion resistance persist. Producing metal matrix nanocomposites (MMNCs) with improved mechanical properties and overcoming limitations like low fracture toughness and machinability is a key area. Many existing methods for producing MMCs are costly and complex for conventional production environments. There is a need for affordable and effective methods to enhance the properties of die-cast aluminum alloys, particularly through in-situ generation and dispersion of reinforcing particles like Al2O3, which can improve strength, refine microstructure, and potentially reduce hot cracking susceptibility in processes like HPDC. This research addresses the need for innovative, cost-effective melt treatments to improve the performance of die-cast aluminum alloys, making them suitable for more demanding structural applications.
4. Research Purpose and Research Questions:
Research Purpose:
The primary research purpose is to investigate the feasibility of an innovative melt treatment to generate Al2O3 particles in-situ within molten aluminum and to evaluate the effects of this treatment on the microstructure and mechanical behavior of die-cast aluminum alloys. This includes assessing whether the generated Al2O3 particles are retained in the solidified metal and how they influence the mechanical properties.
Key Research:
- Can an innovative melt treatment, involving the injection of argon and oxygen gas mixture into molten aluminum, effectively produce Al2O3 particles in-situ?
- Does this melt treatment lead to a dispersion of Al2O3 particles within the molten aluminum that are retained upon solidification?
- What is the influence of this in-situ melt treatment on the microstructure of pure aluminum and Al-Cu alloys?
- How does the melt treatment affect the mechanical properties (tensile strength, yield strength, elongation) of die-cast pure aluminum and Al-Cu alloys produced in both permanent mold and HPDC?
- Can this melt treatment be a viable method for enhancing the properties of die-cast aluminum alloys without significantly increasing production costs or complexity?
5. Research Methodology
Research Design:
The research employed an experimental design to evaluate the effects of an innovative melt treatment on aluminum alloys. The melt treatment involved injecting a mixture of argon and oxygen gas into molten aluminum while stirring. The experiment was conducted in small and large-scale setups, utilizing induction furnaces and degassing units. Different treatment times, gas flow rates, impeller sizes, and casting methods (permanent mold and HPDC) were systematically varied to assess their impact.
Data Collection Method:
- Mechanical Testing: Tensile tests were performed on specimens cast in permanent molds and machined from die-cast plates to evaluate ultimate tensile strength (UTS), yield strength (YS), and elongation (A).
- Microscopy: Optical microscopy was used to analyze the microstructure of the alloys, examining grain structure and phase distribution.
- Computed Tomography (CT): CT scanning was employed to assess porosity content and distribution within the cast specimens.
- Density Measurement: Archimedes’ balance was used to measure the density of specimens, providing another measure of porosity.
- Chemical Composition Analysis: Spark optical emission spectrometry (S-OES) was used to verify the chemical composition of the alloys.
Analysis Method:
- Quantitative Analysis: Tensile test data were statistically analyzed to determine the effects of melt treatment and casting methods on mechanical properties. Porosity measurements from CT scans and density tests were correlated with mechanical property data.
- Qualitative Analysis: Microstructural analysis from optical microscopy and CT images were used to qualitatively assess the impact of melt treatment on grain refinement, phase distribution, and porosity morphology.
- Comparative Analysis: The mechanical properties of treated and untreated alloys, as well as alloys cast using different methods (permanent mold vs. HPDC), were compared to evaluate the effectiveness of the melt treatment and casting processes. The results were also compared against the specifications of standard alloys like EN AC-21100 and AA 206.0 T4.
Research Subjects and Scope:
The research subjects were four different aluminum alloys:
- Alloy 1: Commercially pure aluminum.
- Alloy 2: AlCu4.6 (Al-4.6Cu).
- Alloy 3: AlCu5MnMg (Al-5Cu-0.45Mn-0.37Mg).
- Alloy 4: AlCu5MnMg with Zn and Ti addition (Al-5Cu-0.42Mn-0.27Mg-0.1Zn-0.023Ti).
The scope of the study included:
- Melt Treatment: In-situ generation of Al2O3 particles in molten aluminum using argon and oxygen gas injection.
- Casting Methods: Permanent mold casting and High Pressure Die Casting (HPDC).
- Heat Treatments: Solution heat treatment and natural aging for Alloy 4 HPDC specimens.
- Mechanical Properties: Tensile strength, yield strength, and elongation.
- Microstructural Characterization: Optical microscopy and CT porosity analysis.
6. Main Research Results:
Key Research Results:
- Melt Treatment and Al2O3 Formation: The melt treatment process consistently produced a foamy slag on the melt surface, indicating the formation of oxides, presumably Al2O3. However, microstructural analysis did not reveal Al2O3 particles dispersed within the aluminum matrix in any of the alloys.
- Mechanical Properties of Alloy 1 (Pure Aluminum): The melt treatment with Ar or Ar + O2 did not significantly alter the mechanical properties of pure aluminum. Variations in tensile strength and elongation were attributed to porosity and mold temperature fluctuations rather than the melt treatment itself.
- Mechanical Properties of Alloy 2 (AlCu4.6): The addition of copper significantly increased the strength of Alloy 2 compared to Alloy 1. HPDC Alloy 2 exhibited higher strength and elongation than permanent mold castings, attributed to a finer microstructure from faster cooling. Both casting methods showed a "saw-toothed" stress-strain curve, possibly due to the CuAl2 phase.
- Mechanical Properties of Alloy 3 (AlCu5MnMg): Alloy 3 showed further increased strength but reduced elongation compared to Alloy 2. HPDC Alloy 3 had slightly higher strength than permanent mold castings. The "saw-toothed" behavior was not observed in Alloy 3.
- Mechanical Properties of Alloy 4 (AlCu5MnMg with Zn and Ti): Alloy 4, in the as-cast HPDC condition, showed stable yield strength and higher UTS compared to permanent mold castings. Heat treatment (T4) significantly improved the strength of HPDC Alloy 4, achieving properties comparable to AA 206.0 T4 alloy, although elongation remained lower.
- Porosity: Porosity was a significant factor influencing mechanical properties across all alloys and casting methods. CT analysis revealed varying porosity levels and distributions, affecting tensile strength and elongation.
Analysis of presented data:
- Figure 5.1, 5.2, 5.3, 5.4, 5.5, 5.6, 5.7: These figures show the mechanical properties (Rm, Ag) of Alloy 1 under different melt treatments (Ar, Ar+O2) and impeller sizes (Ø 72 mm, Ø 185 mm) over time. The data indicates no significant strengthening effect from the melt treatment, with variations likely due to porosity and mold conditions.
- Figure 5.8, 5.9, 5.10: These figures present CT images and porosity measurements for Alloy 1, showing porosity variations and suggesting a correlation between porosity and mechanical property variability.
- Figure 5.16, 5.20, 5.21: These figures compare the mechanical properties of Alloy 2 cast in permanent mold and HPDC. HPDC samples show higher strength and elongation. Figure 5.21 compares casting processes for Alloy 2, highlighting the improved properties of HPDC.
- Figure 5.19, 5.22: These figures show stress-strain curves for Alloy 2, illustrating the "saw-tooth" behavior, more pronounced in permanent mold castings.
- Figure 5.26, 5.30: These figures present the mechanical properties of Alloy 3 cast in permanent mold and HPDC. Alloy 3 exhibits higher strength but lower elongation than Alloy 2.
- Figure 5.35, 5.36, 5.38, 5.39: These figures show the mechanical properties of Alloy 4 in permanent mold, as-cast HPDC, and heat-treated HPDC conditions. Heat treatment significantly improves the strength of HPDC Alloy 4.
Figure Name List:
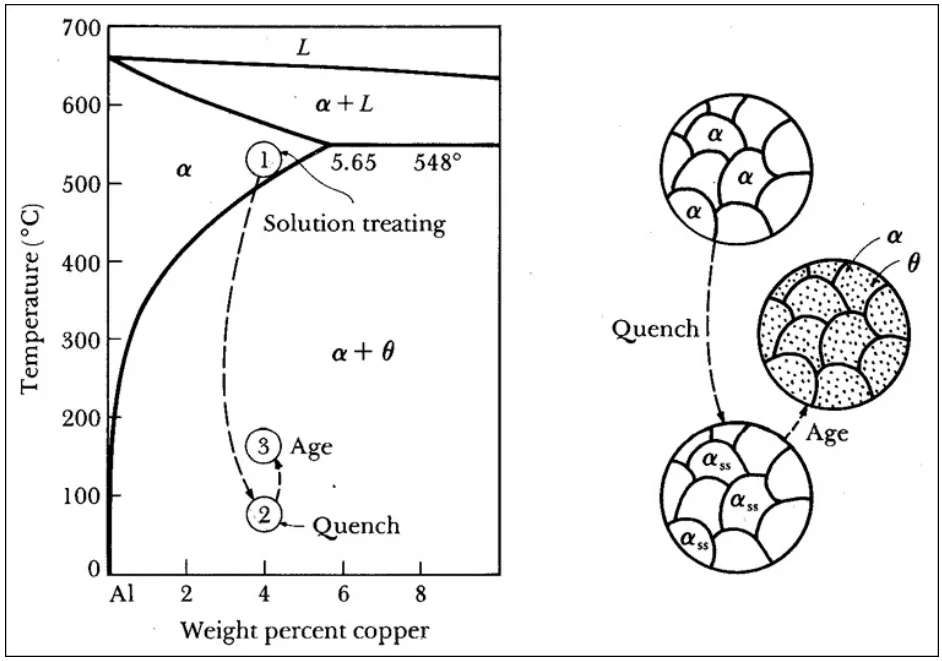
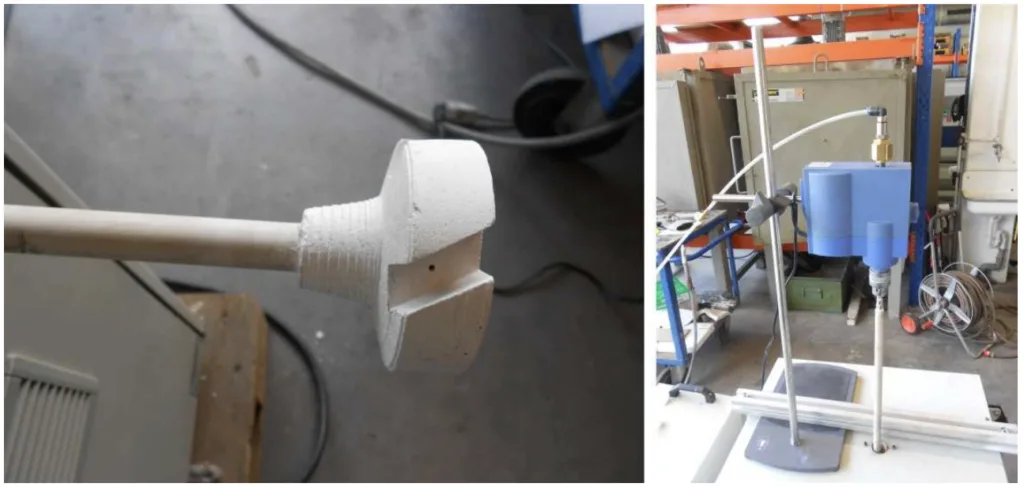
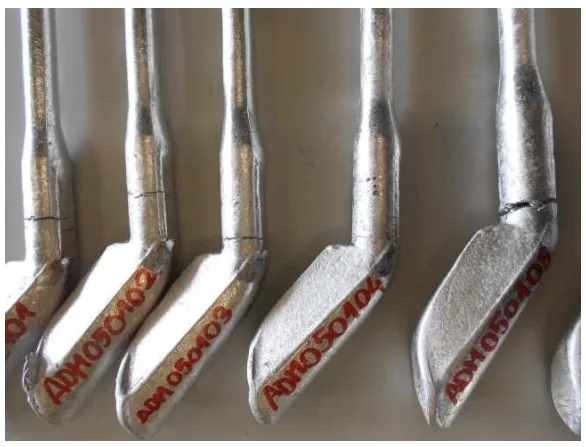
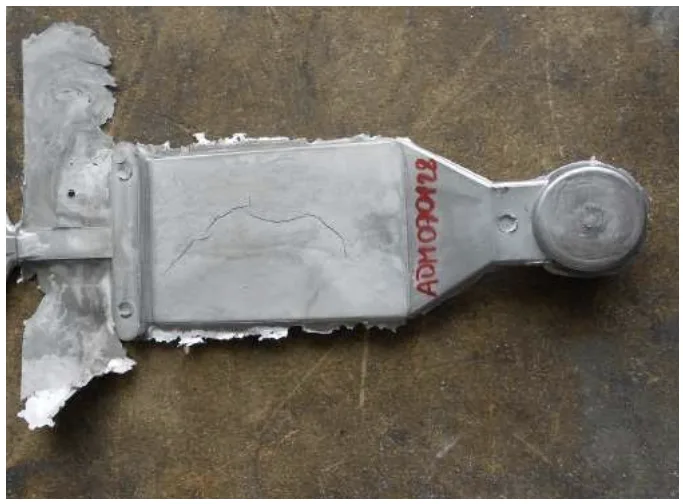
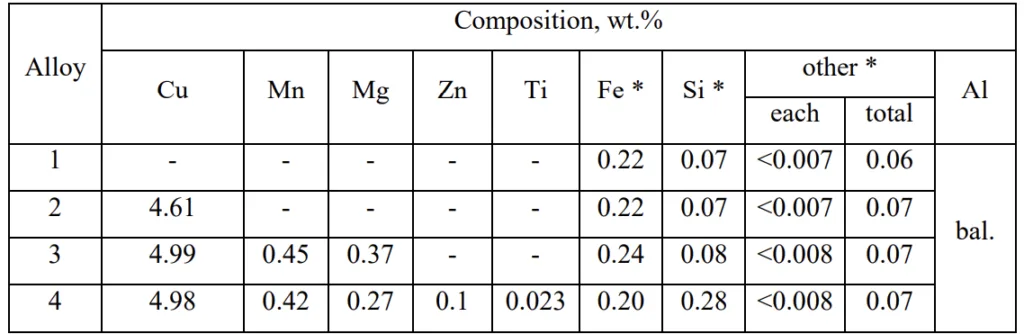
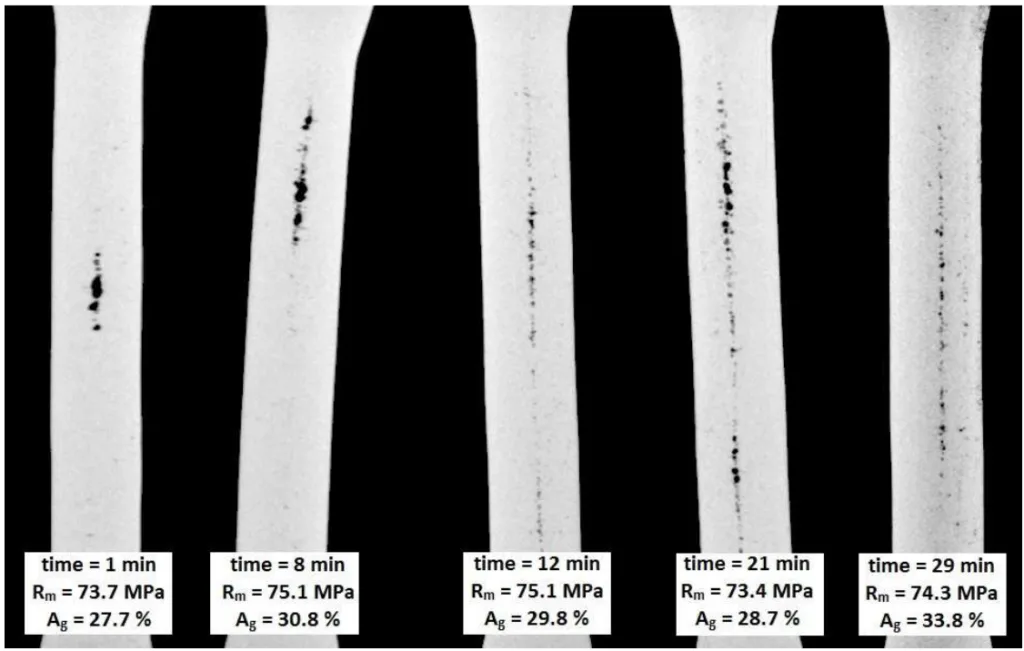
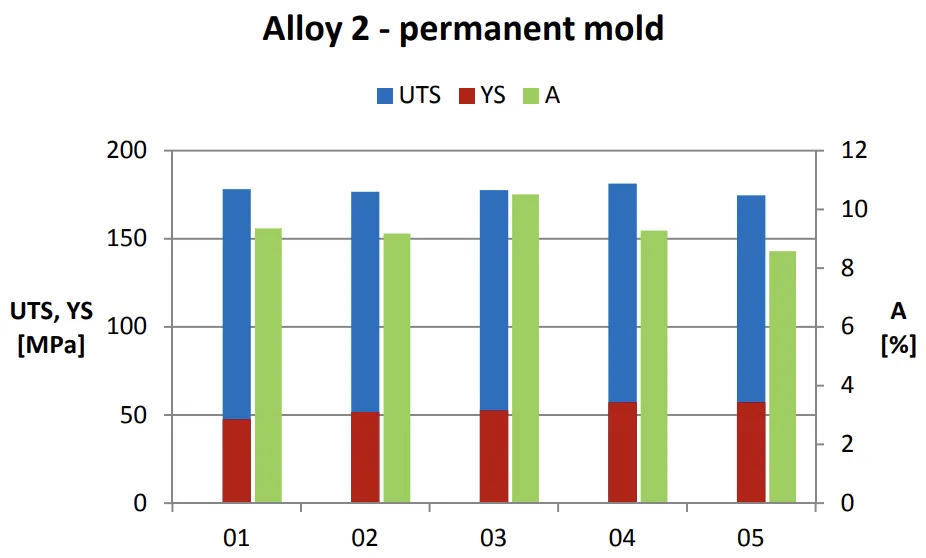
- Figure 1: rappresentazione in sezione di una macchina da pressocolata
- Figure 2: illustrazione del processo di rafforzamento per precipitazione
- Figure 3: girante e miscelatore utilizzati nell'impianto più piccolo
- Figure 4: scoria formatasi sulla superficie del bagno fuso di alluminio fuso
- Figure 5: piasta ottenuta per pressocolata con evidenti segni di criccatura a caldo
- Figure 6: proprietà meccaniche della lega 1 - iniezione di Ar + O2 - girante da Ø 72 mm
- Figure 7: proprietà miccaniche della lega 1 - iniezione di Ar + O2 - girante da Ø 185 mm
- Figure 8: microstruttura della lega 1 dopo trattamento con iniezione di Ar + O2
- Figure 9: distribuzione dei punti di rottura dei provini di lega 2 pressocolata
- Figure 10: proprietà meccaniche della lega 4 dopo invecchiamento
- Figure 2.1: parts produced with HPDC: a dental chair component (a), a medical imager side wall (b), an engine base bracket (c) and a transaxle housing (d).
- Figure 2.2: layout of a hot-chamber HPDC machine
- Figure 2.3: layout of a cold-chamber HPDC machine
- Figure 2.4: main components of a die assembly
- Figure 2.5: a vacuum system for extracting air both from the shot sleeve and the die cavity
- Figure 2.6: StatVac equipment by Electronics GmbH
- Figure 2.7: layout of a Vacural HPDC machine
- Figure 2.8: microstructure comparison between a convetional and a semi solid die cast alloy
- Figure 3.1: Alfred Wilm (1869–1937)
- Figure 3.2: Duralumin was adopted in airplanes and airships for its stength, toughtness and lightness
- Figure 3.3: Al-CuAl2 phase diagram
- Figure 3.4: solidification of an Al-Cu alloy
- Figure 3.5: the precipitation hardening process
- Figure 3.6: two mechanisms of overcoming precipitates
- Figure 3.7: influence of precipitate radius on the stress σy
- Figure 3.8: changes in behaviour due to different age hardening conditions
- Figure 3.9: solvuses of Al-Cu phases
- Figure 3.10: a hot crack originate on a die cast component
- Figure 4.1: a block of boron nitride and the impeller machined
- Figure 4.2: two phases of the gluing process
- Figure 4.3: the stirrer installed on the furnace
- Figure 4.4: scheme of the gas mixing circuit
- Figure 4.5: the big scale setup during the treatment
- Figure 4.6: the Ø 185 mm impeller
- Figure 4.7: slag solidified around the impeller and the oxide powder on the crucible
- Figure 4.8: slag wrapped around the graphite tube
- Figure 4.9: slag removed from the surface of melt
- Figure 4.10: permanent mold cast tensile specimens
- Figure 4.11: Weingarten GDK 200 HPDC machine
- Figure 4.12: die employed for the production of die cast plates
- Figure 4.13: hot cracks in permanent mold cast specimens
- Figure 4.14: hot cracks on a die cast plate
- Figure 4.15: mark of the ejector pin on the overflow of a die cast plate
- Figure 4.16: blisters on the surface of a heat treated die cast plate
- Figure 4.7: slag solidified around the impeller and the oxide powder on the crucible
- Figure 5.1: mechanical properties of alloy 1 – melt treatment with Ar + O2 – Ø 72 mm impeller setup
- Figure 5.2: ultimate tensile strength of alloy 1 − melt treatment with Ar − Ø185 mm impeller setup
- Figure 5.3: permanent elongation at maximum load of alloy 1 − melt treatment with Ar – Ø 185 mm impeller setup
- Figure 5.4: ultimate tensile strength of alloy 1 − melt treatment with Ar and O2 – Ø 185 mm impeller
- Figure 5.5: elongation at maximum load of alloy 1 − melt treatment with Ar and O2 – Ø 185 mm impeller
- Figure 5.6: Rm comparison between alloy 1 treated with Ar and alloy 1 treated with Ar + O2
- Figure 5.7: comparison of Rm and Ag variability in alloy 1 after trend-filtering of Ag values − melt treatment with Ar + O2 – Ø 185 mm impeller
- Figure 5.8: CT images showing the internal porosity of some of the tensile specimens of alloy 1
- Figure 5.9: porosity content of tensile specimens of alloy 1 − melt treatment with Ar + O2 – Ø 185 mm impeller
- Figure 5.10: CT images of the grip sections of tensile specimens of alloy 1 − melt treatment with Ar + O2 – Ø 185 mm impeller
- Figure 5.11: microstructure of alloy 1 − no melt treatment − 100x
- Figure 5.12: microstructure of alloy 1 − no melt treatment − 1000x
- Figure 5.13: microstructure of alloy 1 − melt treatment with Ar + O2 – Ø 72 mm impeller setup − 1000x
- Figure 5.14: microstructure of alloy 1 − melt treatment with Ar + O2 – Ø 185 mm impeller – 100x
- Figure 5.15: microstructure of alloy 1 − melt treatment with Ar + O2 – Ø 185 mm impeller − 1000x
- Figure 5.16: mechanical properties of permanent mold cast alloy 2
- Figure 5.17: CT images of permanent mold cast specimens of alloy 2
- Figure 5.18: porosity content of alloy 2 specimens cast in permanent mold
- Figure 5.19: a stress-strain curve of permanent mold cast alloy 2, showing the "saw-tooth" behaviour
- Figure 5.20: distribution of failure points of die cast alloy 2 specimens
- Figure 5.21: mechanical properties of alloy 2 - comparison of casting processes
- Figure 5.22: stress-strain curve of die cast alloy 2, showing the same “saw-tooth” behaviour as for permanent mold cast specimens
- Figure 5.23: microstructure of alloy 2 − permanent mold casting − 100x
- Figure 5.24: microstructure of alloy 2 − permanent mold casting − 500x
- Figure 5.25: microstructure alloy 2 – HPDC − 100x
- Figure 5.26: mechanical properties of permanent mold cast alloy 3
- Figure 5.27: CT images of permanent mold cast alloy 3
- Figure 5.28: porosity content of the specimens of permanent mold cast alloy 3
- Figure 5.29: x-ray images of die cast alloy 3 specimens, showing hot cracks inside the two samples in the middle
- Figure 5.30: mechanical properties of die cast alloy 3
- Figure 5.31: comparison of the yielding behaviour of permanent mold and die cast alloy 3
- Figure 5.32: microstructure of alloy 3 − permanent mold casting − 100x
- Figure 5.33: microstructure of alloy 3 − permanent mold casting − 1000x
- Figure 5.34: microstructure of alloy 3 – HPDC − 100x
- Figure 5.35: mechanical properties of permanent mold cast alloy 4
- Figure 5.36: mechanical properties of HPDC alloy 4 without heat treatment
- Figure 5.37: comparison of the yielding behaviour of permanent mold and die cast alloy 4
- Figure 5.38: mechanical properties of die cast alloy 4 after HT1
- Figure 5.39: mechanical properties of die cast alloy 4 after HT2
- Figure 5.40: microstructure of alloy 4 − permanent mold casting − 100x
- Figure 5.41: microstructure of alloy 4 - permanent mold casting - 1000x
- Figure 5.42: microstructure of alloy 4 − HPDC − no heat treatment − 100x
- Figure 5.43: microstructure of alloy 4 − HPDC − no heat treatment − 500x
- Figure 5.44: microstructure of alloy 4 − HPDC − HT1 − 100x
- Figure 5.45: microstructure of alloy 4 - HPDC - HT2 - 100x
7. Conclusion:
Summary of Key Findings:
The innovative melt treatment, involving argon and oxygen injection, consistently produced slag, but did not result in Al2O3 particle reinforcement within the aluminum matrix. Mechanical properties of pure aluminum (Alloy 1) were not improved by the treatment. Copper addition (Alloy 2) significantly increased strength, with HPDC showing superior properties over permanent mold casting. Alloys 3 and 4, with Mn and Mg additions, further increased strength but reduced elongation. Heat treatment (T4) substantially enhanced the strength of HPDC Alloy 4, reaching properties comparable to AA 206.0 T4. Porosity significantly influenced mechanical property variability across all alloys and casting methods.
Academic Significance of the Study:
This study provides a comprehensive investigation into an innovative in-situ melt treatment for generating Al2O3 particles in aluminum alloys. The findings demonstrate that while the treatment effectively produces oxides evidenced by slag formation, it does not achieve the desired dispersion of Al2O3 reinforcement within the aluminum matrix using the tested parameters. The research contributes to the understanding of melt treatment limitations and the complex interplay between processing parameters, microstructure, and mechanical properties in die-cast aluminum alloys, particularly Al-Cu based alloys. It highlights the challenges in implementing in-situ reinforcement strategies in conventional die casting processes.
Practical Implications:
The results suggest that the investigated melt treatment, in its current form, is not a practically viable method for enhancing the mechanical properties of die-cast aluminum alloys through Al2O3 particle reinforcement. The study underscores the importance of optimizing casting parameters, such as mold temperature and cooling rate, to manage porosity and hot cracking, especially in Al-Cu alloys. The findings reinforce the effectiveness of heat treatments, particularly T4 temper, in significantly improving the strength of HPDC Al-Cu alloys like Alloy 4, making them comparable to established high-performance alloys such as AA 206.0 T4.
Limitations of the Study and Areas for Future Research:
The primary limitation is the failure to achieve in-situ Al2O3 particle dispersion within the aluminum matrix, despite oxide formation. Future research should explore modifications to the melt treatment process, such as:
- Optimizing Gas Injection Parameters: Varying gas mixture ratios, flow rates, and injection methods to promote Al2O3 nucleation and dispersion.
- Impeller Design and Stirring Conditions: Refining impeller geometry and stirring speed to enhance turbulence and oxide particle distribution while minimizing slag formation and melt surface disruption.
- Alternative In-situ Reactions: Investigating different reactive gas mixtures or precursors that might facilitate Al2O3 formation and dispersion more effectively.
- Nanoparticle Stabilization: Exploring methods to stabilize and prevent agglomeration of Al2O3 nanoparticles during melt treatment and casting.
- Process Scalability and Cost-Effectiveness: Focusing on developing melt treatment methods that are industrially scalable and economically feasible for mass production of reinforced die-cast components.
- Further investigation on hot cracking: Further research is needed to understand the hot cracking mechanism in Al-Cu alloys and to develop effective strategies for its mitigation in HPDC, potentially through microstructure control or alloy modification.
8. References:
- [1] K.U. Kainer, Basics of Metal Matrix Composites
- [2] C. Borgonovo, Aluminum Nano-composites for Elevated Temperature Applications, Worcester Polytechnic Institute, Worcester, USA
- [3] C. Borgonovo, Makhlouf M. Makhlouf, Synthesis of die-castable nano-particle reinforced aluminium matrix composite materials by in-situ gas-liquid reactions, Worcester Polytechnic Institute, Worcester, USA
- [4] A.A. Hamid, P.K. Ghosh, S.C. Jain, S. Ray, Processing, Microstructure, and Mechanical Properties of Cast In-Situ Al(Mg,Ti)-Al2O3(TiO2) Composite, Metallurgical and Materials Transactions A, vol. 37A, Feb. 2006
- [5] North American Die Casting Association - www.diecasting.org
- [6] CustomPartNet – www.custompartnet.com/wu/die-casting#equipment
- [7] ASM Handbook, ASM International, vol. 2
- [8] UC RUSAL – www.aluminiumleader.com/en/around/transport
- [9] I. J. Polmear, Aluminium Alloys - A century of age hardening, Materials Forum Vol. 28 – 2004
- [10] J.R. Greer, Handout AlCu, www.jrgreer.caltech.edu
- [11] Prof. F. Bonollo, Leghe di alluminio: approfondimenti metallurgici – Trattamenti termici, Dipartimento di Tecnica e Gestione dei Sistemi Industriali - Università di Padova, Vicenza, Italy
- [12] Alcan AA206 Primary Foundry Alloys, Alcan Primary Products Corporation Inc.
- [13] S. Li, Hot Tearing in Cast Aluminium Alloys: Measures and Effects of Process Variables, Worcester Polytechnic Institute, Worcester, USA
- [14] S. Bao, K. Tang, A. Kvithyld, M. Tangstad, Wettability of Aluminum on Alumina, Metallurgical and Materials Transactions B, vol. 42B, Dec. 2011
- [15] E.G. Fuchs, A Roósz, TTD-Diagrams for the Homogenization of As-Cast Structures, Z. Metallkunde, Vol. 63, pp. 211-214 (1972)
- [16] Prof. F. Bonollo, Prodotti Metallurgici Innovativi e Multifunzionali, Dipartimento di Tecnica e Gestione dei Sistemi Industriali - Università di Padova, Vicenza, Italy
- [17] www.matweb.com
- [18] www.keytometals.com
- [19] www.aviometal.com
- [20] www.wikipedia.org
9. Copyright:
- This material is "Alberto Dal Maso"'s paper: Based on "INVESTIGATION ON THE EFFECTS OF INNOVATIVE MELT TREATMENTS ON MICROSTRUCTURE AND MECHANICAL BEHAVIOUR OF DIECAST AL ALLOYS".
- Paper Source: [No DOI available in the document]
This material was created to introduce the above paper, and unauthorized use for commercial purposes is prohibited.
Copyright © 2025 CASTMAN. All rights reserved.