This article introduces the paper ['Increasing the lifespan of high-pressure die cast molds subjected to severe wear'] published by ['Surface & Coatings Technology'].
1. Overview:
- Title: Increasing the Lifespan of High-Pressure Die Cast Molds Subjected to Severe Wear
- Author: V. Nunes, F.J.G. Silva, M.F. Andrade, R. Alexandre, A.P.M. Baptista
- Publication Year: 2017
- Publishing Journal/Academic Society: Surface & Coatings Technology
- Keywords: Wear, Abrasion, Erosion, High-pressure die casting, Mold wear, Wear mechanisms, Mold lifespan
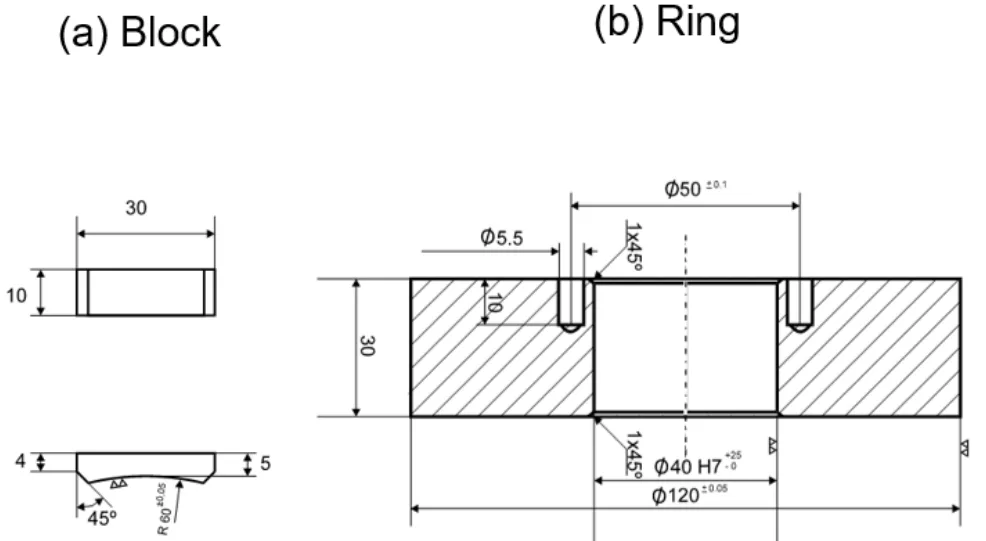
2. Abstracts or Introduction
Regardless of the increasing incorporation of composite materials on vehicle components, high pressure die casting still remains one of the most useful manufacturing techniques to obtain automotive parts with a complex shape in a cost effective way. It is well known that automotive industry requires high production cadence as well as high products quality. Thus, systematic approaches are permanently being done leading to optimize all the production and management aspects.
The aluminum alloys commonly used in automotive parts such as fuel pumps bodies, throttle bodies, EGR valves, support brackets and so on usually contain Silicon which presents high abrasively. The aluminum flow at high temperature and high speed into the mold induces severe wear, sometimes due to a combination of abrasion and erosion effects.
In this study, two molds with typical severe wear problems were selected and the wear mechanisms involved were deeply studied. After that, a careful selection of the best coating for this purpose was done and some of the most critical parts of the mold were coated in order to test possible effective advantages of the coating application, analyzing the wear resistance behavior and wear mechanisms involved. In parallel, tribological tests were also carried out in order to study if a correlation between laboratory and industrial tests can be drawn. Scanning Electron Microscopy (SEM) and Energy Dispersive Spectroscopy were intensively used to characterize the coatings and the wear mechanisms observed. Laboratory tribological tests have involved ball scattering and block-on-ring tests, trying to impose low and medium loads on the contact, respectively. Promising results were obtained allowing conclude that certain coatings present a better behavior than other ones in this field of application.
3. Research Background:
Background of the Research Topic:
Regardless of the increasing incorporation of composite materials on vehicle components, high pressure die casting still remains one of the most useful manufacturing technique to obtain automotive parts with a complex shape in a cost effective way. However, the molds that are used to produce those parts are constantly exposed to highly severe conditions, such as high pressure, rapid temperature fluctuations and erosion from fast-moving molten metal. The following steps can be deemed in the high-pressure die-casting process: filling the shot sleeve, high-velocity cavity filling, application of a supplementary high pressure, cooling and solidification, mold opening and part ejection, die cooling and corresponding lubrication for a new injection cycle [1]. The usual molten metal input speed is comprised between 20-60 m/s and the temperature, depending on aluminum alloy type is around 700°C [2]. The maintenance or replace of these molds require a huge cost which implies that producers need to find the best solution to increase their lifespan. The industrial environmental and working conditions increase the capacity to induce some failure mechanisms on hot work tool steel, such as erosion, corrosion, wear and thermal fatigue [3].
Status of Existing Research:
Over the last years, some researches have been developed to understand the different types of failure mechanisms [2, 4-7]. The aluminum injection into the die consists on one of the most severe processes due to aluminum soldering mechanisms. The molten aluminum creates chemical reactions with the die surface and leads to failure mechanisms on aluminum die casting [4, 8]. For this reason, a large number of studies have been developed to build coatings to prevent the mechanisms that decrease the mold lifespan [1, 3, 9-16]. Ceramic coatings are usually used to avoid some failure mechanisms, in particular, heat checking occurrence. However, other coatings can also contribute to improve the mold lifespan and the cost may not be the most relevant factor in this kind of application [11].
In 1997, Wang [14] presented an extensive work about how coatings can improve the mold lifespan, having studied current coatings at that time, namely TiN, TiAlN and CrN, using different hot work tool steel and maraging steels, analyzing different strands such as molten aluminum corrosion, toughness resistance, hardness and heat changes. The study allows realizing that TiN is not a good solution due to its low oxidation temperature, concluding as well that H13 or Marlok steel, when coated, can be considered for high-pressure injection molding, mainly if an improvement of the impact toughness and corrosion and erosion behaviors are desired. This study was corroborated by Park and Kim [16], who conclude that TiN starts to oxidize at 500°C, while other studied coatings (TiAlN and TiSiN) showed a much better oxidation resistance up to 700°C. Furthermore, it is well-known that TiN tends to dissociate at temperatures above 600°C [17, 18]. These last coatings exhibited as well good mechanical properties, but the TiSiN is better for medium temperatures, being the TiAlN coating the best for higher temperatures. However, tests carried out by Dobrzanski et al. [10] allowed state that TiN coating led achieving a wear resistance five times greater than X37CrMoV5-1 type hot work tool steel under the same pin-on-disc test conditions at room temperature, as well as in the same tests carried out at 500°C. Similar studies were also performed by Tentardini et al. [8] with the same TiN and CrN coatings regarding the aluminum die casting, but this time using H13 steel and Anviloy® 1150 as substrates. These researchers found that CrN coating presented a better behavior than TiN one regarding soldering mechanisms with the aluminum alloy in the casting process. Moreover, Guzilia et al. [1] had also investigated soldering phenomenon, concluding that the use of TiN, CrN and TiCn coatings avoid soldering between the aluminum alloy and the steel mold, being possible to observe a built-up layer of cast aluminum alloy, which causes less damages to the mold, avoiding its rapid degradation, because the coatings act as a physical barrier that prevents any reaction between the molten aluminum and the mold steel surface. Furthermore, Heim et al. [12] also studied the soldering phenomenon in aluminum die casting, concluding as well that coatings such as TiN, TiCN, TiBN and TiAlCN prevent that nefarious problem.
Based yet on the same coatings, some new coating architecture has been tested, namely using multi-layered coatings [19]. The different layers intended to assume different roles such as thermal barrier (outer layer – rare earth oxide coating), a diffusion barrier (middle layer – TiAlN coating) and thin adhesive layer (inner layer Ti coating). By this way, thermal fatigue resistance of the substrate was significantly improved, as can be observed after 4000 thermal cycles with liquid aluminum. A similar approach was carried out by Bobzin et al. [20], testing a multilayered CrN/AlN/Al2O3 coating on AISI H11 steel substrate, being the Al2O3 the top layer. Also, two industrial coatings were used in that study under the same test conditions, including industrial tests with 5884 aluminum shots in an aluminum die casting machine. The CrN/AlN/Al2O3 showed an interesting behavior comparatively to the other coatings, improving significantly the mold lifespan. Phase transformations in the coating were reported being attributed to the temperature reached in the mold. However, a slightly different approach was also studied by Muller [15], who used a plasma nitriding pre-treatment of the mould surface, followed by PVD or PACVD coatings such as TiBN, CrN and W-C:H films, concluding that plasma nitriding pre-treatment improves the surface macro-hardness and critical load relatively to surfaces just doted of the same PVD or PACVD coatings. On the other hand, Rodríguez-Baracaldo [21] studied a combination of nitriding pre-treatments with (Ti0.7Al0.3)N coating, comparing it with two nitriding pre-treated steel and other steel just provided with (Ti0.6Al0.4)N coating, carrying out the wear tests at room and high temperature (600°C). While at room temperature there were no significant differences regarding the wear behavior, the same is not true at elevated temperature, where the nitriding pre-treated steel provided with the (Ti0.6Al0.4)N coating showed the best wear behavior, comparatively to the pre-treated steel and not pre-treated steel coated with (Ti0.6Al0.4)N coating, being the last one that performed the worst wear behavior. Also, a different approach was investigated by Tomaslewski et al. [22], co-depositing Mo together with TiAlN using AISI M2 equivalent high-speed steel as substrates. The quasi-multilayer obtained is TiAlN/(TiAl)1-x - MoxN giving way to a Mo content of about 8%, improving the friction coefficient relative to steel from 0.8 to 0.5 and decreasing the wear rate to values below 1015 m³/N·m. This work was preceded by similar approaches carried out by other authors regarding pure multilayered systems based on distinct layers of TiAlN interspersed with Mo ones [23-25]. More recently, another study was performed by Reenwinkel et al. [26] regarding the elastic properties of TiAlN-WNx coatings using different concentrations of TiAlN and WNx. This study showed that the higher is the concentration of W, the lower is Young's modulus, what can be extrapolated to wear behavior.
More recently, other advanced coatings have been investigated regarding the improvement of the wear resistance property. Park et. al. [27] studied the influence of nitriding pre-treatment of H13 steel before the deposition of TiB2. They concluded that the adhesion of the coating to the substrate increased to values higher than 30 N by this nitriding process but the hardness decreased to values between 20-30 GPa. However, this pre-treatment cannot be applied to coatings with high hardness (>60 GPa) due to the difference between the hardness of this coating and the substrate, thus, the adhesion is difficult to improve for high coating hardness. TiB2 similar coatings have been also studied by other authors [28], concluding that these coatings present a very good adhesion and wear resistance properties regarding the test conditions used in that work (micro-abrasion wear test configuration). Moreover, Maaza et al. [29, 30] also tried to decrease the diffusion of some other elements or compounds such as Ni and B4C on Ti by using different surface treatments regarding the its use on some surface multilayered systems in other applications.
Molds for plastic injection also represents some challenges for coating science, mainly those are used for Glass-Fiber Reinforced Plastics (GFRP) injection, taking into account the abrasion promoted by the glass-fiber tips. However, in these cases, there are not the same problems as in the aluminum injection because the temperatures usually used to melt aluminum alloys are significantly higher comparatively to plastic materials [31]. In this field, other more complex coatings have been also investigated using micro-abrasion wear tests, such as TiAlSiN [32] and TiAlCrSiN [33], showing promising properties in terms of adhesion and wear resistance. However, in these cases the working temperature was not a concern take into account.
Necessity of the Research:
Based on the existing research, there is a clear necessity to explore and optimize coatings for high-pressure die casting molds to enhance their lifespan and performance under severe wear conditions. This study focuses on comparing two different TiAlN coatings to address this need.
4. Research Purpose and Research Questions:
Research Purpose:
In this work, two different TiAlN coatings have been investigated (Ti0.4Al0.6N and Ti0.5Al0.5N) regarding their possible application on high-pressure die casting molds mobile parts and cavities. These films were deeply characterized and tested in order to evaluate their ability to resist to wear under different conditions.
Key Research:
- Characterization of two different TiAlN coatings (Ti0.4Al0.6N and Ti0.5Al0.5N).
- Evaluation of wear resistance of these coatings under conditions simulating high-pressure die casting.
- Comparison of the performance of the two TiAlN coatings in both laboratory and industrial settings.
- Analysis of wear mechanisms and material transfer between aluminum alloys and coated molds.
Research Hypotheses:
The paper does not explicitly state research hypotheses. However, implicitly, the research aims to test the hypothesis that different compositions of TiAlN coatings will exhibit varying wear resistance and performance in high-pressure die casting applications, and that TiAlN coatings can improve the lifespan of die casting molds.
5. Research Methodology
Research Design:
The research employed a comparative experimental design, evaluating two different TiAlN coatings (Ti0.4Al0.6N and Ti0.5Al0.5N) against each other and against uncoated mold steel in both laboratory and industrial settings.
Data Collection Method:
- Laboratory Tribological Tests: Block-on-ring tribometer tests were conducted to simulate wear and friction behavior.
- Industrial Tests: Core pins coated with TiAlN were tested in a real die-casting process over 30,000 injection cycles.
- Materials Characterization:
- Scanning Electron Microscopy (SEM) and Energy Dispersive Spectroscopy (EDS) for morphology, thickness, and composition analysis.
- Ultra-Micro Hardness Test (Fisherscope H100) for hardness and Young's modulus.
- Scratch-test (CSM REVETEST) for adhesion evaluation.
- Profilometer (MAHR PERTHOMETER M2) and Atomic Force Microscopy (AFM) for surface roughness characterization.
Analysis Method:
- Quantitative analysis: Measurement of coating thickness, hardness, adhesion strength, surface roughness, friction coefficient, and wear volume.
- Qualitative analysis: SEM and EDS analysis of wear scars, material transfer, and wear mechanisms.
- Comparative analysis: Comparison of the performance of the two TiAlN coatings and correlation between laboratory and industrial test results.
Research Subjects and Scope:
- Substrate Material: AISI H13 steel (DIN X40CrMoV5-1).
- Coating Materials: Ti0.4Al0.6N and Ti0.5Al0.5N coatings deposited by PVD.
- Aluminum Alloys: A380 (AlSi9Cu3(Fe)) and A13 (AlSil2Cul(Fe)) aluminum-silicon-copper alloys.
- Scope: Evaluation of TiAlN coatings for high-pressure die casting molds, focusing on wear resistance and lifespan improvement.
6. Main Research Results:
Key Research Results:
- Coating Characterization: Ti40Al60N and Ti50Al50N films were deposited as monolayer thin films with thicknesses around 3 µm and 2 µm, respectively. Both coatings were homogenous.
- Surface Morphology: Ti50Al50N coating was found to be smoother than Ti40Al60N.
- Roughness Analysis: After PVD deposition, roughness decreased slightly compared to the substrate. Ti50Al50N showed a lower roughness value (0.02 µm reduction) than Ti40Al60N (0.066 µm reduction).
- Adhesion: Both coatings showed good adhesion. Ti50Al50N exhibited slightly higher critical loads for cohesive (33 N) and adhesive (49 N) failures compared to Ti40Al60N (31 N and 47 N, respectively).
- Hardness and Young's Modulus: Ti40Al60N showed higher hardness (33.63 GPa) and Young's modulus (469.88 GPa) than Ti50Al50N (23.57 GPa and 320.05 GPa, respectively).
- Tribological Behavior: In laboratory tests, Ti40Al60N exhibited lower friction coefficients than Ti50Al50N against both A380 and A13 aluminum alloys.
- Industrial Tests: Core pins coated with Ti40Al60N showed less wear after 30,000 injection cycles compared to Ti50Al50N. Ti50Al50N core pins showed evidence of coating failure and more severe wear.
Analysis of presented data:
- SEM and EDS analysis of wear tracks revealed material transfer of aluminum alloy to the coating surface in both Ti40Al60N and Ti50Al50N coatings.
- Ti50Al50N showed a more intense transfer of A13 aluminum alloy compared to A380, suggesting higher metallurgical affinity.
- Ti40Al60N, despite having a rougher surface, demonstrated better wear resistance and lower friction, attributed to its higher hardness and Young's modulus.
- Industrial tests corroborated laboratory findings, indicating that Ti40Al60N performed better in real die-casting conditions.
Figure Name List:
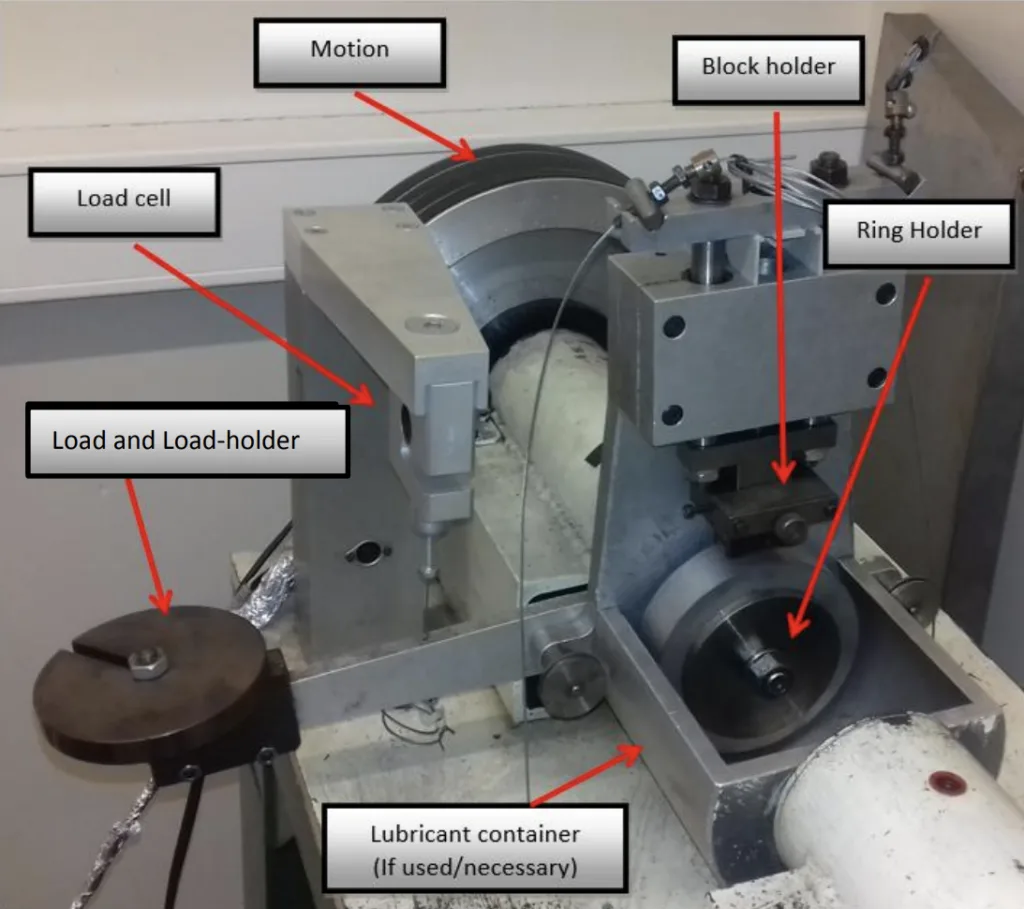

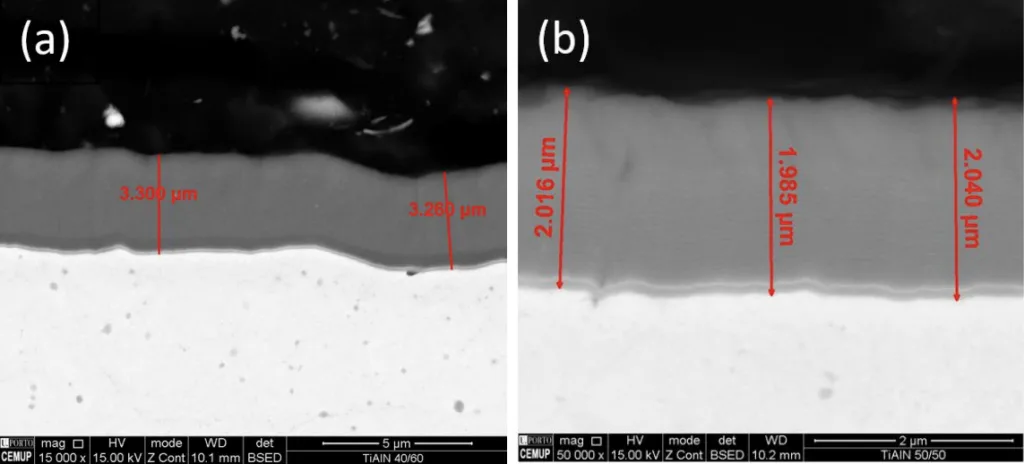
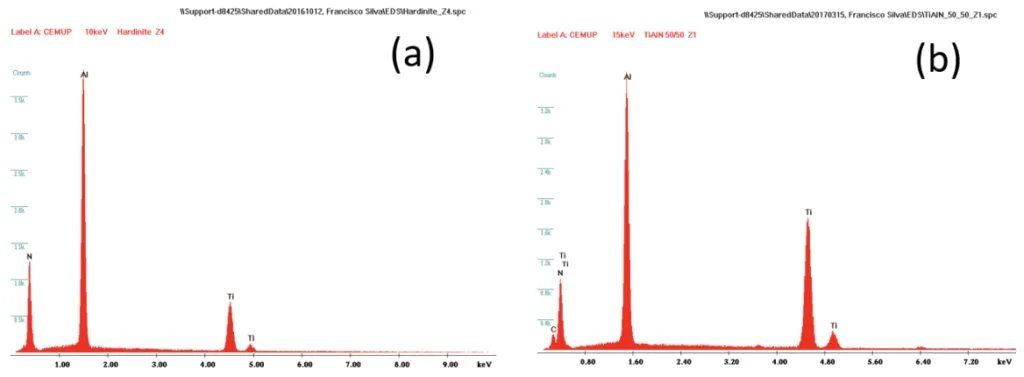
𝑇𝑖40𝐴𝑙60𝑁 and (b) 𝑇𝑖50𝐴𝑙50N
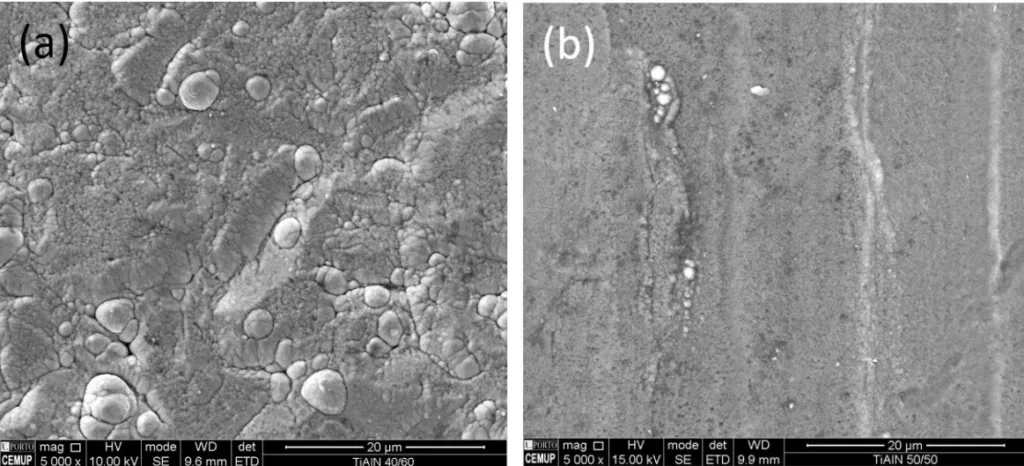
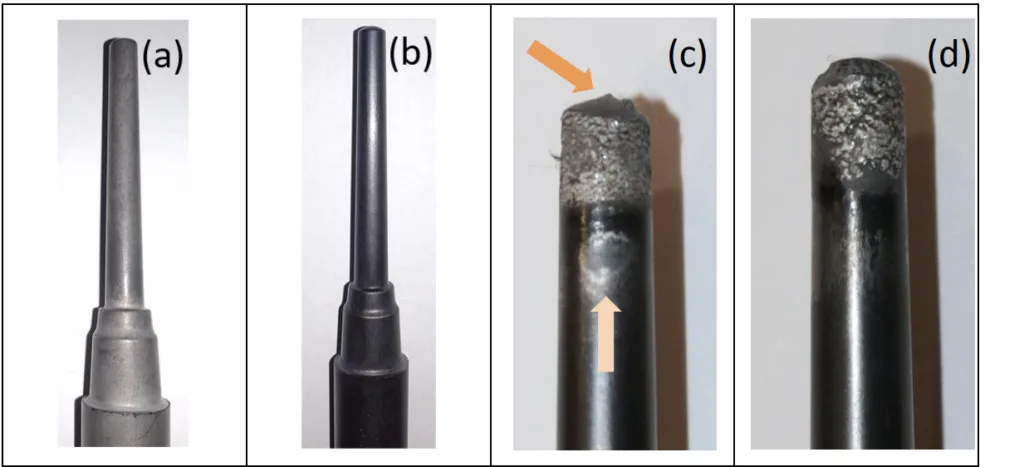
- Figure 1 - Block (a) and ring (b) samples geometry
- Figure 2 - View of the block on ring tribometer used in tribological tests
- Figure 3 - View of the mold where the core pins were assembled for industrial tests
- Figure 4 - Cross-section views of the coatings (Ti40Al60N (a) and Ti50Al50N (b)) allowing measure the coatings thickness
- Figure 5 - EDS spectra collected during SEM observations allowing confirm the composition coatings: (a) Ti40Al60N and (b) Ti50Al50N
- Figure 6 - Coatings morphological characterization (a) Ti40Al60N and (b) Ti50Al50N (top view)
- Figure 7 - AFM topography analysis on Ti40Al60N (a) and Ti50Al50N (b) coated ring surface
- Figure 8 - Scratch-test critical loads (a) cohesive and (b) adhesive failure events on Ti40Al60N coating
- Figure 9 - Scratch-test critical loads (a) cohesive and (b) adhesive failure events on Ti50Al50N coating
- Figure 10 - SEM images collected of Ti40Al60N coated ring surface in contact with different aluminum alloy ((a) A380 and (b) A13) after wear tribological tests on block on ring tribometer. Sliding direction represented by arrows
- Figure 11 - SEM images collected of Ti50Al50N coated ring surface in contact with different aluminum alloy ((a) A380 and (b) A13) after wear tribological tests on block on ring tribometer. Sliding direction represented by arrows
- Figure 12 - SEM observation and spectra of transferred A13 aluminum alloy from the block to Ti40Al60N coated ring surface (a, b, c). Sliding direction represented by arrow
- Figure 13 - SEM observation and spectra of transferred A380 aluminum alloy on Ti40Al60N coated ring surface (a, b, c). Sliding direction represented by arrow
- Figure 14 - SEM observation and spectra of transferred A13 aluminum alloy on Ti50Al50N coated ring surface (a, b, c). Sliding direction represented by arrow
- Figure 15 - SEM observation and spectra of transferred A13 aluminum alloy on Ti50Al50N coated ring surface (a, b, c). Sliding direction represented by arrow
- Figure 16 - Core pin samples used on die-casting mold (a) uncoated pin, (b) Ti40Al60N coated pin, (c) after 30,000 shots with Ti50Al50N coating, (d) after 30,000 shots with Ti40Al60N coating
7. Conclusion:
Summary of Key Findings:
This study compared two TiAlN coatings, Ti40Al60N and Ti50Al50N, for high-pressure die casting molds. Ti40Al60N demonstrated superior wear resistance in both laboratory and industrial tests, exhibiting lower friction and less wear on core pins after 30,000 injection cycles. While Ti50Al50N showed good wear resistance in laboratory settings, it exhibited poorer performance in industrial tests with evidence of coating failure and greater aluminum adhesion. Ti40Al60N's higher hardness and Young's modulus, despite a slightly rougher surface, contributed to its better performance.
Academic Significance of the Study:
This study contributes to the understanding of the relationship between TiAlN coating composition, microstructure, and wear performance in high-pressure die casting applications. It highlights the importance of considering both laboratory and industrial testing to validate coating performance. The research provides valuable insights into the wear mechanisms and material transfer phenomena occurring in coated die casting molds.
Practical Implications:
The findings suggest that Ti40Al60N coating is a more effective solution for increasing the lifespan of high-pressure die casting molds compared to Ti50Al50N. This has practical implications for the die casting industry, offering a potential coating solution to reduce mold wear, decrease maintenance costs, and improve productivity. The study supports the use of Ti40Al60N for inserts or movable parts of molds subjected to severe wear.
Limitations of the Study and Areas for Future Research:
The study was limited to two specific TiAlN compositions and two aluminum alloys. Future research could explore a broader range of coating compositions, multilayer coatings, and different aluminum alloys to further optimize coating performance. Longer duration industrial tests beyond 30,000 cycles are needed to fully assess the lifespan limit of the coatings. Further investigation into the specific wear mechanisms and the role of surface roughness in coating performance would also be beneficial.
8. References:
- [1] S. Gulizia, M.Z. Jahedi, E.D. Doyle, Performance evaluation of PVD coatings for high pressure die casting, Surf. Coatings Technol., 140(3) (2001) 200–205. DOI: 10.1016/S0257-8972(01)01037-4.
- [2] A. Persson, S. Hogmark, J. Bergström, Thermal fatigue cracking of surface engineered hot work tool steels, Surf. Coatings Technol., 191(2-3) (2005) 216–227. DOI: 10.1016/j.surfcoat.2004.04.053.
- [3] I. Peter, M. Rosso, and F.S. Gobber, Study of protective coatings for aluminum die casting molds, Appl. Surf. Sci., 358 (2015) 563–571. DOI: 10.1016/j.apsusc.2015.08.013.
- [4] Z.W. Chen, M.Z. Jahedi, Die erosion and its effect on soldering formation in high-pressure die casting of aluminum alloys, Mater. Des., 20(6) (1999) 303–309. DOI: 10.1016/S0261-3069(99)00035-7.
- [5] A. Persson, S. Hogmark J. Bergström, Simulation and evaluation of thermal fatigue cracking of hot work tool steels, Int. J. Fatigue, 26(10) (2004) 1095–1107. DOI: 10.1016/j.ijfatigue.2004.03.005.
- [6] D. Klobčar, J. Tušek, Thermal stresses in aluminum alloy die casting dies, Comput. Mater. Sci., 43(4) (2008) 1147–1154. DOI: 10.1016/j.commatsci.2008.03.009.
- [7] D. Klobčar, L. Kosec, B. Kosec, J. Tušek, Thermo fatigue cracking of die casting dies, Eng. Fail. Anal., 20 (2012) 43-53. DOI: 10.1016/j.engfailanal.2011.10.005.
- [8] E.K. Tentardini, A.O. Kunrath, C. Aguzzoli, M. Castro, J.J. Moore, and I.J.R. Baumvol, Soldering mechanisms in materials and coatings for aluminum die casting, Surf. Coatings Technol., 202(16) (2008) 3764-3771. DOI: 10.1016/j.surfcoat.2008.01.019.
- [9] O. Knotek, F. Löffler B. Bosserhoff, PVD coatings for diecasting moulds, Surf. Coatings Technol., 62(1-3) (1993) 630-634. DOI: 10.1016/0257-8972(93)90310-K.
- [10] L.A. Dobrzanski, M. Polok, P. Panjan, S. Bugliosi, M. Adamiak, Improvement of wear resistance of hot work steels by PVD coatings deposition, J. Mater. Process. Technol., 155-156(1-3) (2004) 1995-2001. DOI: 10.1016/j.jmatprotec.2004.04.405.
- [11] B. Navinšek, P. Panjan, I. Urankar, P. Cvahte, F. Gorenjak, Improvement of hot-working processes with PVD coatings and duplex treatment, Surf. Coatings Technol., 142-144 (2001) 1148-1154. DOI: 10.1016/S0257-8972(01)01098-2.
- [12] D. Heim, F. Holler, C. Mitterer, Hard coatings produced by PACVD applied to aluminium die casting, Surf. Coatings Technol., 116–119 (1999) 530-536. DOI: 10.1016/S0257-8972(99)00104-8.
- [13] C. Mitterer, F. Holler, F. Üstel, D. Heim, Application of hard coatings in aluminium die casting - soldering, erosion and thermal fatigue behaviour, Surf. Coatings Technol., 125(1-3) (2000) 233-239. DOI: 10.1016/S0257-8972(99)00557-5.
- [14] Y. Wang, A study of PVD coatings and die materials for extended die-casting die life, Surf. Coatings Technol., 94-95(97) (1997) 60-63. DOI: 10.1016/S0257-8972(97)00476-3.
- [15] K.B. Müller, Deposition of hard films on hot-working steel dies for aluminium, J. Mater. Process. Technol., 130-131 (2002) 432-437. DOI: 10.1016/S0924-0136(02)00715-X.
- [16] I.-W. Park, K.H. Kim, Coating materials of TiN, Ti-Al-N, and Ti-Si-N by plasma-enhanced chemical vapor deposition for mechanical applications, J. Mater. Process. Technol., 130-131 (2002) 254-259. DOI: 10.1016/S0924-0136(02)00807-5.
- [17] N.J.M Carvalho, E. Zoestbergen, B.J Kooi, J.Th.M De Hosson, Stress analysis and microstructure of PVD monolayer TiN and multilayer TiN/(Ti,Al)N coatings, Thin Solid Films, 429(1-2) (2003)179-189. DOI: 10.1016/S0040-6090(03)00067-1.
- [18] J. Musil, H. Hrubý, Superhard nanocomposite Til-xAlxN films prepared by magnetron sputtering, Thin Solid Films, 365 (2000) 104-109. DOI: 10.1016/S0040-6090(00)00653-2.
- [19] A. Srivastava, V. Joshia, R. Shivpuria, R. Bhattacharya, S. Dixit, A multilayer coating architecture to reduce heat checking of die surfaces, Surf. Coatings Technol., 163-164 (2003) 631-636. DOI: 10.1016/S0257-8972(02)00690-4.
- [20] K. Bobzin, T. Brögelmann, U. Hartmann, N.C. Kruppe, Analysis of CrN/AlN/Al2O3 and two industrially used coatings deposited on die casting cores after application in an aluminum die casting machine, Surf. Coatings Technol., vol. 308 (2016) 374-382. DOI: 10.1016/j.surfcoat.2016.09.040.
- [21] R. Rodríguez-Baracaldo, J.A. Benito, E.S. Puchi-Cabrera, M.H. Staia, High temperature wear resistance of (TiAl)N PVD coating on untreated and gas nitrided AISI H13 steel with different heat treatments, Wear, 262 (2007) 380-389. DOI: 10.1016/j.wear.2006.06.010.
- [22] Ł. Tomaszewski, W. Gulbinski, A. Urbanowicz. T. Suszko, A. Lewandowski, W. Gulbinski, TiAlN based wear resistant coatings modified by molybdenum addition, Vacuum 121 (2015) 223-229. DOI: 10.1016/j.vacuum.2015.08.027.
- [23] C.J. Tavares, L. Rebouta, M. Andritschky, F. Guimaraes, A. Cavaleiro, Mechanical and surface analysis of Ti0.4A10.6N/Mo multilayers, Vacuum 60 (2001) 339-346. DOI: 10.1016/S0042-207X(00)00413-9.
- [24] C.J. Tavares, L. Rebouta, J.P. Rivière, J. Pacaud, H. Garem, K. Pischow, Z. Wang, Microstructure of superhard (Ti,Al)N/Mo multilayers, Thin Solid Films, 398-399 (2001) 397-404. DOI: 10.1016/S0040-6090(01)01349-9.
- [25] C.J. Tavares, C. Vidrago, L. Rebouta, J.P. Rivière, E. Le Bourhis, M.F. Denanot, Optimization and thermal stability of TiAlN/Mo multilayers, Surf. Coat. Technol. 200 (2005) 288-292. DOI: 10.1016/j.surfcoat.2005.02.099.
- [26] T. Reeswinkel, D.G. Sangiovanni, V. Chirita, L. Hultman, J.M. Schneider, Structure and mechanical properties of TiAlNeWNx thin films, Surf. Coat. Technol. 205 (2011) 4821-4827. DOI: 10.1016/j.surfcoat.2011.04.066.
- [27] B. Park, D.-H. Jung, H. Kim, K.-C. Yoo, J.-J. Lee, J. Joo, Adhesion properties of TiB2 coatings on nitrided AISI H13 steel, Surf. Coat. Technol. 200 (2005) 726-729. DOI: 10.1016/j.surfcoat.2005.01.064.
- [28] F.J.G. Silva, R.C.B. Casais, R.P. Martinho, A.P.M. Baptista, Mechanical and Tribological Characterization of TiB2 Thin Films, J. Nanosci. Nanotechnol., 12 (2012) 9187–9194. DOI: 10.1166/jnn.2012.6759.
- [29] M. Mâaza, C. Sella, J. P. Ambroise, M. Kâabouchi, M. Milôche, F. Wehling and M. Groos, Determination of diffusion coefficient D and activation energy Qa of nickel into titanium in Ni-Ti multilayers by grazing-angle neutron reflectometry, J. Appl. Cryst. 26 (1993) 334-342. DOI: 10.1107/S0021889892010355.
- [30] M. Mâaza. A. Menelle. J.P. Chauvineau. B. Pardo. A. Raynal. F. Bridou. C. Sella. T. Megademini. Monochromation and anodization with Ti-B4C multilayers in neutron optics, Physica B, 198(1-3) (1994) 231-234. DOI: 10.1016/0921-4526(94)90167-8.
- [31] K. Bobzin, T. Brögelmann, R.H. Brugnara, N.C. Kruppe, S. Chromy, Influence of HPPMS pulse parameters on the reactive gas N2 and on the properties of (Cr, Al)N coatings, Surf. Coat. Technol. 293 (2016) 28-34. DOI: 10.1016/j.surfcoat.2015.12.072.
- [32] M.F.C. Andrade, R.P. Martinho, F.J.G. Silva, R.J.D. Alexandre, A.P.M. Baptista, Influence of the abrasive particles size in the microabrasion wear tests of TiAlSiN thin coatings, Wear 267 (2009) 12–18. DOI: 10.1016/j.wear.2008.12.114.
- [33] R.P. Martinho, M.F.C. Andrade, F.J.G. Silva, R.J.D. Alexandre, A.P.M. Baptista, Microabrasion wear behaviour of TiAlCrSiN nanostructured coatings, Wear 267 (2009) 1160-1165. DOI: 10.1016/j.wear.2008.12.063.
- [34] Francisco J. G. Silva, Revestimentos duros ultra-finos executados por P.V.D. (in Portuguese), Master Thesis, Faculty of Engiineering, University of Porto, Porto, 1997.
- [35] Arnaldo M. G. Pinto, Influência do Comportamento Dinâmico da Máquina de Ensino nos Resultados de Atrito e Desgaste, (in Portuguese), Master Thesis, Faculty of Engineering, University of Porto, Porto, 2001.
- [36] F. Silva, A. T. Ribeiro, L. A. Ferreira, A comparative study of the tribological behaviour of TiN and ZrN PVD coatings, Lubrication at the frontier, D. Dowson et al. (Eds), Tribology Series, Elsevier, Amsterdan, pp 141-147.
- [37] P. Terek, L. Kovacevic, A. Miletic, P. Panjan, S. Balos, B. Skoric, Effects of die core treatments and surfaces finishes on the sticking and galling tendency of Al-Si alloy casting during ejection, Wear, 356-357 (2016) 122-134. DOI: 10.1016/j.wear.2016.03.016.
- [38] E. Lugscheider, C. Barimani, S. Guerreiro, K. Bobzin, Corrosion tests of PVD coatings with die lubricant used for Al high-pressure die-casting dies, Surf. Coat. Technol., 108-109 (1998) 408-412. DOI: 10.1016/S0257-8972(98)00624-6.
- [39] J.L. Mo, M.H. Zhu, B. Lei, Y.X. Leng, N. Huang, Comparison of tribological behaviours of AlCrN and TiAlN coatings - Deposited by physical vapor deposition, Wear, 263 (2007) 1423-1429. DOI: 10.1016/j.wear.2007.01.051.
- [40] A. Drnovsek, P. Panjan, M. Panjan, M. Cekada, The influence of growth defects in sputter-deposited TiAlN hard coatings on their tribological behavior, Surf. Coat. Technol., 288 (2016) 171-178. DOI: 10.1016/j.surfcoat.2016.01.021.
- [41] B. Wang, G.R. Bourne, A.L. Korenyi-Both, A.K. Monroe, S.P. Midson, M.J. Kaufman, Method to evaluate the adhesion behavior of aluminum-based alloys on various materials and coatings for lube-free die casting, J. Mater. Process. Technol., 237 (2016) 386-393. DOI: 10.1016/j.jmatprotec.2016.06.031.
9. Copyright:
- This material is "V. Nunes, F.J.G. Silva, M.F. Andrade, R. Alexandre, A.P.M. Baptista"'s paper: Based on "Increasing the lifespan of high-pressure die cast molds subjected to severe wear".
- Paper Source: doi:10.1016/j.surfcoat.2017.05.098
This material was summarized based on the above paper, and unauthorized use for commercial purposes is prohibited.
Copyright © 2025 CASTMAN. All rights reserved.