This article introduces the paper 'Improved tensile properties of a new aluminum alloy for high pressure die casting' published by 'Materials Science and Engineering A'.
1. Overview:
- Title: Improved tensile properties of a new aluminum alloy for high pressure die casting
- Author: Peng Zhang, Zhenming Li, Baoliang Liu, Wenjiang Ding, Liming Peng
- Publication Year: 2015
- Publishing Journal/Academic Society: Materials Science and Engineering A
- Keywords: Al-5Mg-0.6Mn aluminum alloy; high pressure die casting; tensile properties; strain rate; high temperature
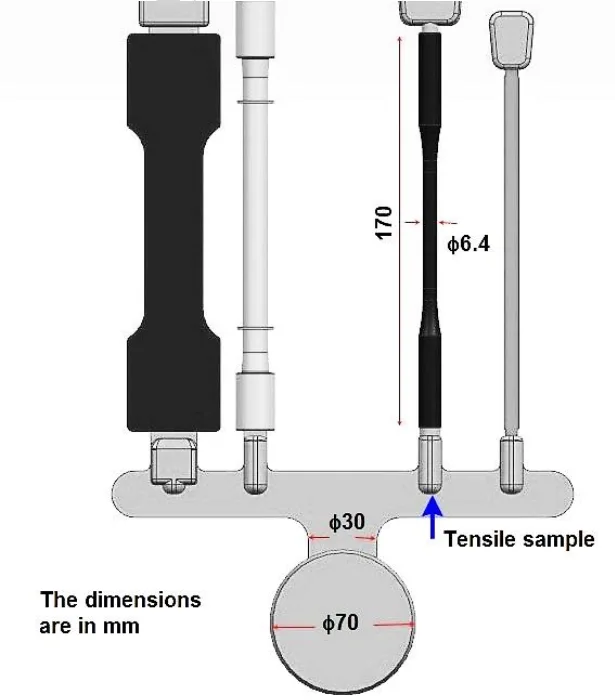
2. Abstracts or Introduction
Abstract
This paper investigates the effects of strain rate and test temperature on the tensile properties and deformation behavior of a recently developed high-ductility cast aluminum alloy Al-5Mg-0.6Mn. The as-cast alloy tested at room temperature and the lowest strain rate of ~1.67 × 10⁻⁴ s⁻¹ shows the highest yield yield strength of ~212 MPa, ultimate tensile strength of ~357 MPa and elongation (~17.6%). Increasing strain rate reduces the ultimate tensile strength and ductility of the as-cast alloy. With the increasing of test temperature, the as-cast alloy shows significantly decreases in tensile strengths and improvements improvements in elongation. The tensile failure of the alloy is mainly originated from the cracking and debonding ding eutectic particles. The Portevin-Le Chatelier effect occurs in the alloy tested at RT. Strain rate in current study ranges does not significantly affect the work-hardening behavior of the alloy. Increasing test temperature apparently reduces the strain-hardening exponent and coefficient. For the alloy tested at RT, all tensile failures occur prior to global instability, indicating the existence of localized damage. In contrast, for the alloy tested at HT, the global instability occurs at strains below the logarithmic fracture strains, suggesting that there is still a postnecking damage.
3. Research Background:
Background of the Research Topic:
Die cast aluminum alloys are increasingly utilized in automotive, aerospace, and transportation industries due to their light weighting and enhanced performance. High pressure die casting (HPDC) is favored for mass production because of its high productive efficiency, capacity for intricate shapes, thin-walled components, dimensional accuracy, surface finish, and mechanical properties. However, the rapid filling speed and cooling rate in HPDC can trap gases within the cavity, leading to casting defects like pores and oxide inclusions. These defects can act as stress concentration sites, reducing the mechanical properties of castings, especially at elevated temperatures where gas expansion in pores can cause surface bubbling and further deteriorate mechanical properties. A key challenge is that aluminum alloy die castings with pores generally cannot undergo heat treatment and are unsuitable for high-temperature applications.
Status of Existing Research:
While component structure and mold design are crucial, the selection of appropriate alloys is paramount for high-pressure die casting to achieve excellent die cast productions. The increasing demand for cast aluminum components necessitates alloys with high tensile strength, elongation, and fatigue properties. Current commercial aluminum alloys (such as Al-Si-Mg, Al-Si-Cu-Mg and Al-Si-Cu) often lack sufficient ductility (δ< 5%) for structural applications in modern automobiles and aerospace. Heat treatment is a recognized method to improve tensile properties of cast aluminum alloys, but rectification works are often needed after heat treatment for large, thin-walled components due to size changes caused by treatment technologies. This highlights the need for new die cast aluminum alloys that do not require heat treatment to broaden their practical applications.
Necessity of the Research:
Developing new die-cast aluminum alloys without heat treatment is crucial for widening the practical applications of these materials. The basic requirements for die casting aluminum alloys include: (1) excellent fluidity for cavity filling and good surface quality; (2) superior mechanical properties at both room and high temperatures for larger, complex, thin-walled castings; (3) a narrow crystallization temperature range to minimize shrinkage and enhance product quality; and (4) low interaction tendency between the alloy and mold cavity to reduce die-sticking. Al-Mg aluminum alloys are attractive for structural components due to their good corrosion resistance and high mechanical properties, but their fluidity and oxidation behavior are generally inferior to Al-Si based alloys, posing challenges in die casting. Therefore, research and development of new Al-Mg based alloys for high pressure die casting are needed. A newly developed die-casting alloy, Al-5Mg-0.6Mn, shows promise for automotive powertrain and structural applications due to its high strength, ductility, and resistance without requiring heat treatment.
4. Research Purpose and Research Questions:
Research Purpose:
The primary purpose of this research is to investigate the tensile properties and deformation behavior of a newly developed high-ductility cast aluminum alloy, Al-5Mg-0.6Mn, specifically focusing on the effects of strain rate and test temperature. This study aims to assess the suitability of this alloy for high-pressure die casting applications, particularly in automotive and aerospace industries, by characterizing its mechanical response under varying conditions.
Key Research:
The key research questions addressed in this paper are:
- How do different strain rates affect the tensile properties (yield strength, ultimate tensile strength, and elongation) of the as-cast Al-5Mg-0.6Mn alloy at room temperature?
- How do varying test temperatures influence the tensile properties of the as-cast Al-5Mg-0.6Mn alloy at a constant strain rate?
- What are the underlying deformation and fracture mechanisms of the Al-5Mg-0.6Mn alloy under different strain rates and test temperatures?
- How does strain rate and test temperature affect the strain-hardening behavior of the alloy, and is there a Portevin-Le Chatelier (PLC) effect present?
- What are the implications of tensile instability and fracture characteristics of this alloy for its application in high-pressure die casting components?
Research Hypotheses:
The research implicitly hypothesizes that:
- Increasing strain rate will negatively impact the tensile strength and ductility of the Al-5Mg-0.6Mn alloy.
- Increasing test temperature will reduce the tensile strength but improve the elongation of the Al-5Mg-0.6Mn alloy.
- The Portevin-Le Chatelier effect may be observed at room temperature, influencing the strain-hardening behavior.
- Microstructural features, such as eutectic particles and defect bands, will play a significant role in the fracture mechanism under different testing conditions.
- The Al-5Mg-0.6Mn alloy, despite being a cast alloy, can exhibit improved tensile properties compared to traditional Al-Mg alloys, making it suitable for HPDC applications without heat treatment.
5. Research Methodology
Research Design:
The research employs an experimental design to evaluate the tensile properties of the as-cast Al-5Mg-0.6Mn aluminum alloy under varying strain rates and test temperatures. The study involves preparing tensile samples from the alloy and subjecting them to uniaxial tensile testing under controlled conditions. Fractographic analysis and microstructural characterization are conducted to understand the deformation and fracture mechanisms. Numerical flow simulation is used to analyze defect band formation during die casting.
Data Collection Method:
- Material Preparation: The Al-5Mg-0.6Mn alloy was prepared from high purity Al and master alloys using an electrical resistance furnace and cast into a metal mold using a LK400S 4000KN HPDC machine. Die casting parameters are shown in Fig. 1. Standard tensile samples were prepared according to ASTM B557-06.
- Tensile Testing: Uniaxial tensile tests were performed using a Zwick/Roell-20kN tensile machine with a high-temperature furnace. Stress-strain curves were recorded using a knife-edge extensometer. Tests were conducted at five different strain rates (1.67 × 10⁻⁴ s⁻¹ (B₁), 3.33 × 10⁻⁴ s⁻¹ (B₂), 6.67 × 10⁻⁴ s⁻¹ (B₃), 1.33 × 10⁻³ s⁻¹ (B₄), and 2.67 × 10⁻³ s⁻¹ (B₅)) at room temperature (RT~20°C). Additionally, tests were performed at five temperatures (20°C (C₁), 120°C (C₂), 150°C (C₃), 185°C (C₄), and 220°C (C₅)) at a constant strain rate of 6.67 × 10⁻⁴ s⁻¹. At least four tests were conducted for each condition.
- Microstructural Characterization: Microstructure was examined using a JEOL JSM-6460 scanning electron microscope (SEM) with energy dispersive spectroscope (EDS). X-ray diffraction (XRD) was performed using a D/MAX-IIIA X-ray diffractometer to identify phases. Metallographic samples were prepared and etched for SEM observation.
- Numerical Simulation: Mold filling process simulation was conducted using Flow 3D analysis software to investigate defect band formation.
Analysis Method:
- Tensile Data Analysis: Yield strength (YS), ultimate tensile strength (UTS), and elongation (A) were determined from the stress-strain curves. The effects of strain rate and test temperature on these properties were analyzed.
- Fractographic Analysis: Fracture surfaces were examined using SEM to identify fracture modes and damage mechanisms, such as dimples, particle cracking, and debonding.
- Microstructural Analysis: EDS and XRD analyses were used to identify the composition and phases present in the alloy, including intermetallic compounds and porosities. Defect bands were characterized using SEM.
- Strain-Hardening Behavior Analysis: The Portevin-Le Chatelier (PLC) effect was analyzed from the stress-strain curves. Strain-hardening exponent (n) and coefficient (k) were determined by fitting the Hollomon equation to the true stress-logarithmic plastic strain data. Tensile instability was assessed by comparing the strain-hardening rate and flow curves.
Research Subjects and Scope:
The research subject is a newly developed high-ductility cast aluminum alloy with a nominal composition of Al-5Mg-0.6Mn. The scope of the study is limited to:
- Investigating the tensile properties under quasi-static tensile loading conditions.
- Examining the effects of strain rates ranging from 1.67 × 10⁻⁴ s⁻¹ to 2.67 × 10⁻³ s⁻¹ at room temperature.
- Evaluating the influence of test temperatures from 20°C to 220°C at a constant strain rate of 6.67 × 10⁻⁴ s⁻¹.
- Characterizing the microstructure and fracture behavior of the as-cast alloy.
- Analyzing the strain-hardening behavior and tensile instability under these conditions.
6. Main Research Results:
Key Research Results:
- Tensile Properties:
- The as-cast Al-5Mg-0.6Mn alloy exhibited a high yield strength of ~212 MPa, ultimate tensile strength of ~357 MPa, and elongation of ~17.6% when tested at room temperature and a strain rate of ~1.67 × 10⁻⁴ s⁻¹.
- Increasing strain rate led to a decrease in ultimate tensile strength and ductility.
- Increasing test temperature resulted in a significant reduction in tensile strengths but an improvement in elongation. At 220°C, elongation reached ~23.9%.
- Microstructure and Fracture:
- The microstructure consisted of an α-aluminum matrix and hard eutectic phase compounds (Al₁₂Mg₁₇). Massive Alₓ(Fe, Mn)ᵧSi<0xE2><0x96><0x9A> intermetallic phases and porosities were also observed.
- Tensile failure originated from cracking and debonding of eutectic particles.
- Fractographic analysis showed dimples on fracture surfaces at both room and high temperatures, with macroscopic shear fracture at RT and necking with large dimples at HT (220°C).
- Strain-Hardening Behavior:
- The Portevin-Le Chatelier (PLC) effect was observed at room temperature.
- Strain rate did not significantly affect work-hardening behavior.
- Increasing test temperature reduced both the strain-hardening exponent and coefficient.
- Tensile Instability:
- At room temperature, tensile failure occurred prior to global instability, indicating localized damage.
- At high temperatures, global instability occurred at strains below logarithmic fracture strains, suggesting postnecking damage.
Analysis of presented data:
- Strain Rate Effects (Fig. 7, Table 2): Yield strength remained relatively constant across different strain rates, averaging around 210 ± 3 MPa. However, ultimate tensile strength and ductility decreased with increasing strain rate. The highest UTS (~357 MPa) and elongation (17.6%) were achieved at the lowest strain rate (1.67 × 10⁻⁴ s⁻¹).
- Temperature Effects (Fig. 8, Table 3): Both yield strength and ultimate tensile strength decreased as temperature increased. At 220°C, YS reduced to 163 MPa and UTS to 191 MPa. Conversely, elongation significantly increased with temperature, reaching ~23.9% at 220°C, a ~100% increase compared to RT (~12.1%).
- Fractography (Fig. 9): SEM images revealed dimpled fracture surfaces at all tested temperatures, indicating ductile fracture. Dimple size appeared related to the size of phase particles. Shear fracture was dominant at RT, while necking and larger dimples were observed at 220°C.
- PLC Effect (Fig. 10, 11): True stress-logarithmic strain curves showed serrations indicative of the PLC effect at room temperature. Analysis of stress drop and reloading times (Fig. 11) provided quantitative characteristics of the PLC effect.
- Strain Hardening (Fig. 12, 13, 14, 15): Strain-hardening rate decreased with increasing strain. Increasing test temperature reduced both strain-hardening exponent (n) and coefficient (k), as shown by the fitted Hollomon equation parameters.
- Tensile Instability (Fig. 16, 17): The ratio of tensile instability strain to fracture strain (εᵢ/ε<0xE2><0x9F><0x82>) indicated localized fracture at RT (εᵢ/ε<0xE2><0x9F><0x82> ≥ 1) and more uniform damage accumulation at HT (εᵢ/ε<0xE2><0x9F><0x82> < 1).
Figure Name List:
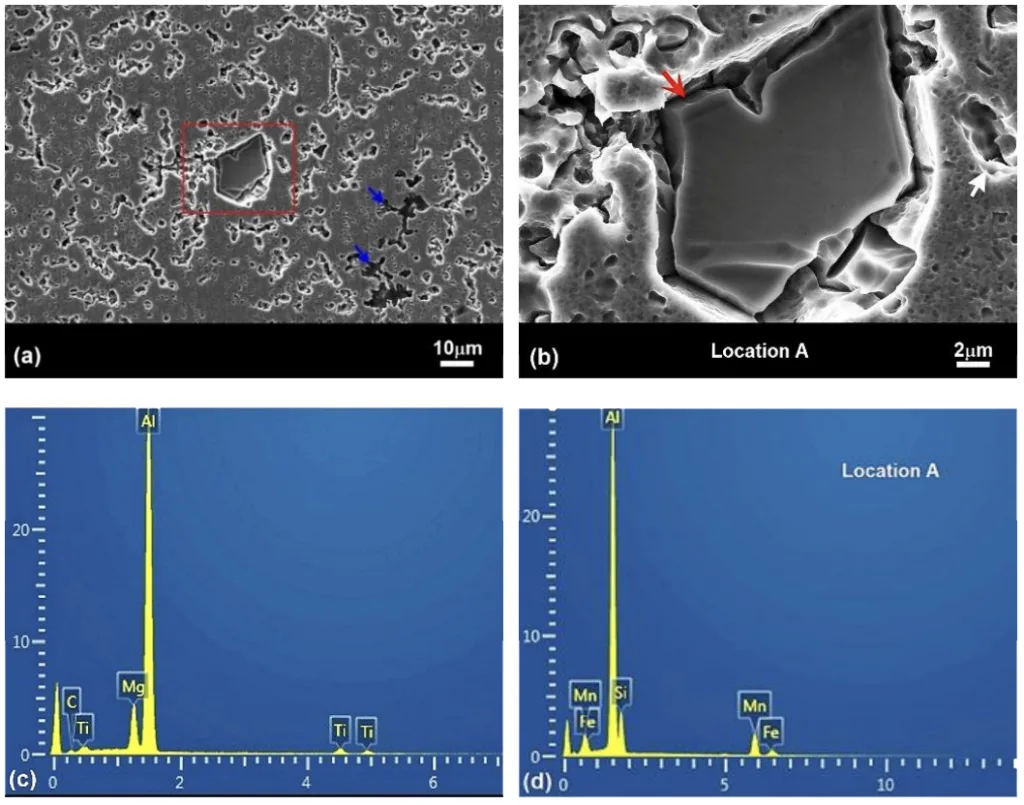
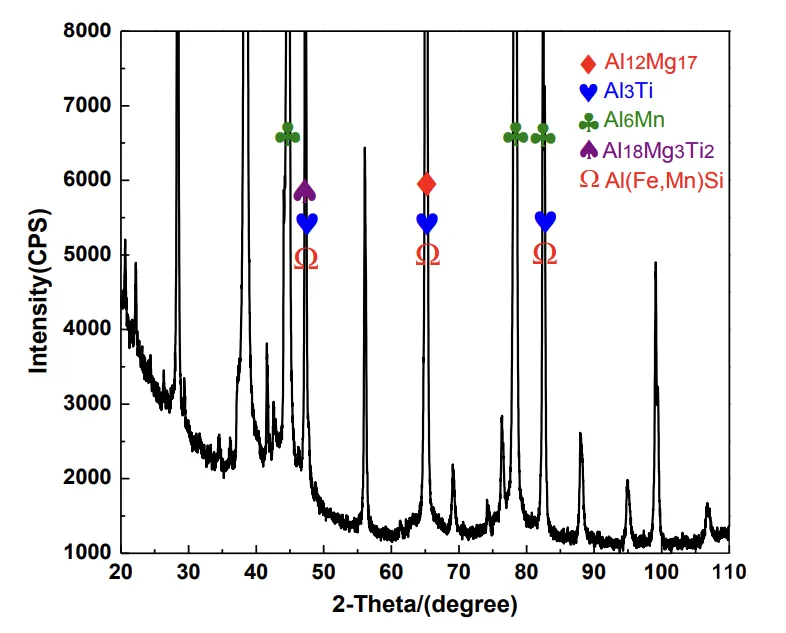
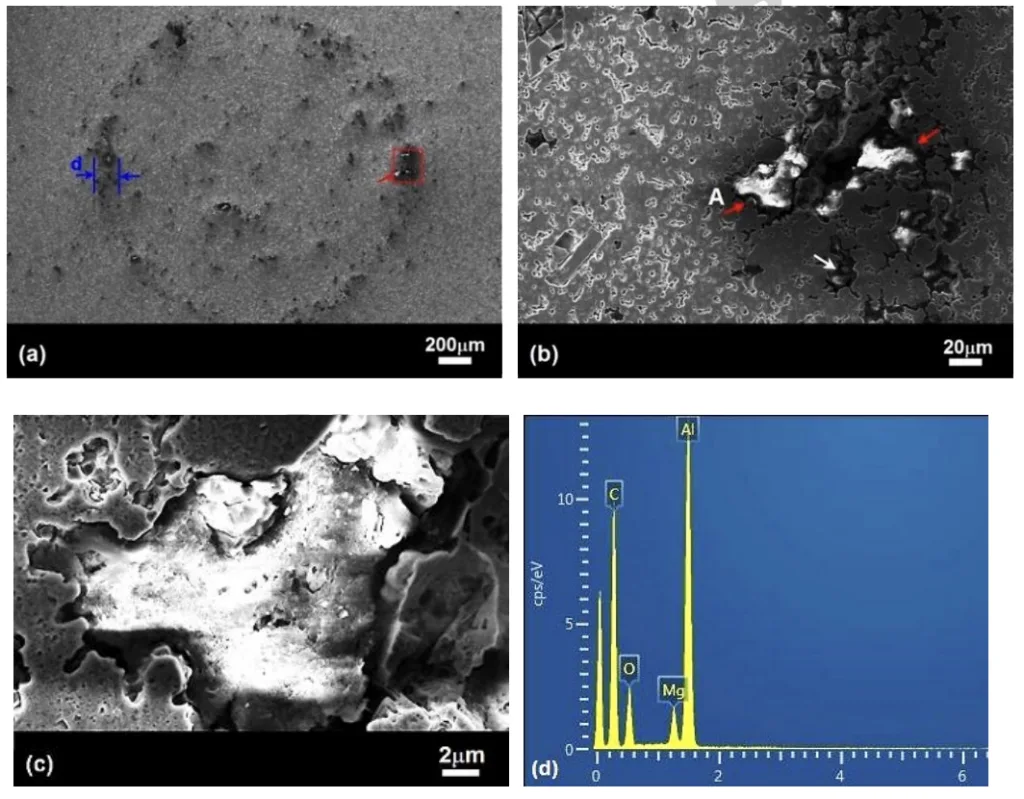
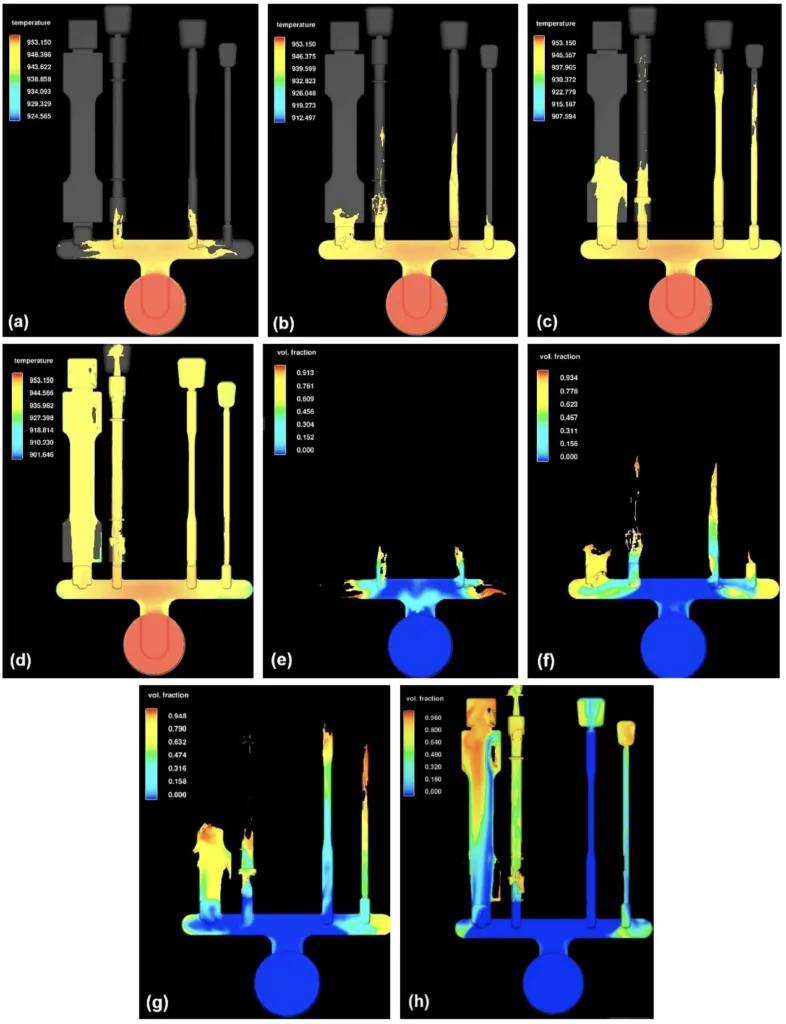
- Fig. 1. Die Casting parameters including filling speed (mm/s) and filling time (s) at different stages.
- Fig. 2. Diagram of die casting for the standard tensile testing samples of cast aluminum alloy according to the specification defined in ASTM B557-06.
- Fig. 3. (a) Secondary SEM image of the microstructure from the grip section of the as-cast Al-5Mg-0.6Mn alloy sample. (b) Location A. (c) Energy dispersive spectroscope (EDS) showing the Al-Mg phases. (d) Energy dispersive spectroscope (EDS) of the phase in location A.
- Fig. 4. XRD curve of the Al-5Mg-0.6Mn alloy.
- Fig. 5. (a) Microstructure observation of the as-cast Al-5Mg-0.6Mn alloy showing defect bands. (b) Location of image (b). (c) High magnification image of the inclusions in image b. (d) Energy dispersive spectroscope spectrum of the inclusions in figure b (location A).
- Fig. 6. Numerical flow simulation images about (a, b, c, d) thermal field and (e, f, g, h) volume fraction of entrained air based on Flow-3D analysis software showing defect bands formation process.
- Fig. 7. Effect of strain rate on tensile properties of the as-cast Al-5Mg-0.6Mn alloy.
- Fig. 8. Effect of test temperature on tensile properties of the as-cast Al-5Mg-0.6Mn alloy.
- Fig. 9. SEM fractographs showing the effect of test temperature on the fracture in the as-cast Al-5Mg-0.6Mn alloy: (a, b) 20°C; (c, d) 120°C; (e, f) 150°C; and (g, h) 220°C.
- Fig. 10. (a) Effect of strain rate on true stress-logarithmic strain curves of the as-cast Al-5Mg-0.6Mn alloy. (b) Magnified curve of location A in figure 9a. (c) True stress-logarithmic plastic strain curves showing the effect of strain rate on flow behavior of the as-cast alloy.
- Fig. 11. (a) σ₁, (b) 62, (c) 63, (d) 62 +63 and (e) t1, (f) t2, (h) t3, (g) t2 + t3 in figure 9b, as a function of logarithmic strain for the as-cast Al-5Mg-0.6Mn alloys.
- Fig. 12. (a) Strain-hardening rate measured at a plastic strain of 0.0015, as function of strain rate for the as-cast Al-5Mg-0.6Mn alloy. (b) Determination of n and K values for the alloys tested at different strain rates. (c) Strain-hardening exponent n and (d) strain-hardening coefficients k measured at a logarithmic plastic strain range from about 0.01 up to instability.
- Fig. 13. (a) Effect of test temperature on true stress-logarithmic strain curves of the as-cast Al-5Mg-0.6Mn alloy. (b) Logarithmic strain corresponding to the transition site between the two regions and the maximum true stress. (c) The ratio of strain at the transition site (ɛt) to fracture strain (ɛf) and the ratio of strain at maximum flow stress (Em) to fracture strain (ɛf). (d) True stress-logarithmic plastic strain curves showing the effect of test temperature on flow behavior of the as-cast alloy.
- Fig. 14. (a) Strain-hardening rate measured at a plastic strain of 0.0015, as function of test temperatures for the as-cast Al-5Mg-0.6Mn alloy. (b) Determination of n and K values for the alloys tested at different test temperatures. (c) Strain-hardening exponent n and (d) strain-hardening coefficients k measured at a logarithmic plastic strain range from about 0.01 up to instability.
- Fig. 15. (a) Strain-hardening exponent n and (b) strength coefficient k (at different logarithmic plastic strain ranges) of the as-cast Al-5Mg-0.6Mn alloy, as a function of different test temperature.
- Fig. 16. Tensile instability plots for the as-cast Al-5Mg-0.6Mn alloy tested at different strain rate and test temperature: (a) B₁-1.67 × 10⁻⁴, B₂-3.33 × 10⁻⁴, B₃-6.67 × 10⁻⁴, B₄-1.33 × 10⁻³ and B₅-2.67 × 10⁻³; (b) C₁-20°C, C₂-125°C, C₃-150°C, C₃-185°C and C₄-220°C.
- Fig. 17. The ratio of tensile instability strain ɛ¡ to fracture strain ɛf of the as-cast Al-5Mg-0.6Mn alloy tested at different strain rates (a) and test temperatures (b).
- Fig. 18. Macroscpic tensile fracture features of the as-cast Al-5Mg-0.6Mn alloy tested at different temperatures (C₁-20°C and C₄-220°C).
7. Conclusion:
Summary of Key Findings:
This study comprehensively evaluated the tensile properties of a novel as-cast Al-5Mg-0.6Mn aluminum alloy produced by high-pressure die casting, focusing on the influence of strain rate and test temperature. Key findings indicate that the alloy exhibits promising tensile performance, particularly at lower strain rates and room temperature, achieving a yield strength of ~212 MPa, an ultimate tensile strength of ~357 MPa, and an elongation of ~17.6% under optimal conditions. Increasing strain rate negatively affects tensile strength and ductility, while elevated temperatures reduce tensile strengths but enhance elongation. The tensile failure mechanism is primarily attributed to the cracking and debonding of eutectic particles. The Portevin-Le Chatelier effect is observed at room temperature, and strain-hardening behavior is influenced by test temperature but not significantly by strain rate within the studied ranges. Tensile instability analysis suggests localized damage at room temperature and postnecking damage at higher temperatures.
Academic Significance of the Study:
This research contributes to the academic understanding of the mechanical behavior of Al-Mg-Mn alloys produced by HPDC. It provides detailed insights into the effects of strain rate and temperature on the tensile properties, deformation mechanisms, and fracture characteristics of this alloy system. The identification of the Portevin-Le Chatelier effect and the analysis of strain-hardening and tensile instability behaviors add to the fundamental knowledge of aluminum alloy deformation physics. The study also highlights the role of microstructural features, such as eutectic particles and defect bands, in determining the alloy's mechanical response.
Practical Implications:
The findings have significant practical implications for the application of Al-5Mg-0.6Mn alloy in high-pressure die casting. The alloy's high tensile strength and ductility, especially at room temperature and low strain rates, suggest its potential for structural components in automotive, aerospace, and other transportation industries, particularly where lightweighting is critical. The fact that this performance is achieved in the as-cast condition, without the need for heat treatment, offers significant manufacturing advantages in terms of cost and processing time. However, the reduction in tensile strength at higher temperatures and strain rates should be considered in application design, especially for components operating under elevated temperature or dynamic loading conditions.
Limitations of the Study and Areas for Future Research:
This study is limited to quasi-static tensile testing and specific ranges of strain rates and temperatures. Further research is recommended to explore:
- The fatigue and creep properties of the Al-5Mg-0.6Mn alloy, which are critical for many structural applications.
- The impact properties and fracture toughness of the alloy to assess its resistance to sudden impact loads.
- The corrosion behavior in various environments to ensure long-term durability.
- The optimization of die casting parameters to minimize defect band formation and further enhance mechanical properties.
- The effect of heat treatment on the alloy's properties, even though the current study emphasizes as-cast performance.
- Modeling and simulation of the alloy's deformation and fracture behavior to predict performance under complex loading conditions.
8. References:
- [1] A.I. Taub, P.E. Krajewski, A.A. Luo, J.N. Owens, JOM 59(2) (2007) 48-57.
- [2] S.X. Ji, D. Watson, Z.Y. Fan, M. White, Mater. Sci. Eng. A 556(2012) 824-833.
- [3] Z.Q. Hu, L. Wan, S.L. Lü, P. Zhu, S.S. Wu, Mater. Design. 55(2014) 353-360.
- [4] S. Farahany, A. Ourdjini, T.A.A. Bakar, M.H. Idris, Thermochim. Acta 575(2014) 179-187.
- [5] V.S. Zolotorevsky, N.A. Belov, M.V. Glazoff, Casting Aluminum Alloys, Elsevier, Oxford, 2007.
- [6] S.X. Ji, F. Yan, Z.Y. Fan, Mater. Sci. Eng. A 626(2015) 165-174.
- [7] S.X. Ji, Z.Y. Fan, Metall. Mater. Trans. A 33(11)(2002) 3511-3520.
- [8] V.D. Tsoukalas, Mater. Design. 29(10) (2008) 2027-2033.
- [9] S.G. Lee, A.M. Gokhale, Scripta Mater. 55(4)(2006) 387-390.
- [10] H.D. Zhao, F. Wang, Y.Y. Li, W. Xia, J. Mater. Process Tech. 209(9)(2009) 4537-4542.
- [11] M. Avalle, G. Belingardia, M.P. Cavatora, R. Doglione, Int. J. Fatigue 24(1)(2002) 1-9.
- [12] H. Mayer, M. Papakyriacou, B. Zettl, S.E. Stanzl-Tschegg, Int. J. Fatigue 25(2003) 245-256.
- [13] Z. Ma, A.M. Samuel, F.H. Samuel, H.W. Doty, S. Valtierra, Mater. Sci. Eng. A 490(1-2)(2009) 36-51.
- [14] R. Sharma, Anesh, D.K. Dwivedi, Mater. Sci. Eng. A 408(1-2)(2005) 274-280.
- [15] B. Lin, W.W. Zhang, Z.H. Lou, D.T. Zhang, Y.Y. Li, Mater. Design. 59(2014) 10-18.
- [16] I.A. Luna, H.M. Molinar, M.J.C. Román, J.C.E. Bocardo, M.H. Trejo, Mater. Sci. Eng. A 561(20)(2013) 1-6.
- [17] Y. Han, A.M. Samuel, H.W. Doty, S. Valtierra, F.H. Samuel, Mater. Design. 58(2014) 426-438.
- [18] Z.X. Wang, H. Li, F.F. Miao, B.J. Fang, R.G. Song, Z.Q. Zheng, Mater. Sci. Eng. A 607(2014) 313-317.
- [19] S.F. Radtke, D.C. Herrschaft, Inter. J. Mater. Eng. Appl. 1(4)(1979) 209-226.
- [20] A.A. Luo, J. Magnes. Alloys 1(1)(2013) 2-22.
- [21] F. Casarotto, A.J. Franke, R. Franke, in: J. Rowe (ed.), Advanced Materials in Automotive Engineering, Woodhead Publishing limited, Cambridge, 2012, pp.109-149.
- [22] L. Kramer, M. Phillippi, W.T. Tack, C. Wong, J. Mater. Eng. Perform. 21(2012) 1025-1029.
- [23] R.H. Jones, D.R. Baer, M.J. Danielson, J.S. Vetrano, Metall. Mater. Trans. A 32(2001) 1699-1711.
- [24] J.L. Searles, P.I. Gouma, R.G. Buchheit, Metall. Mater. Trans. A 32(2001) 2859-2867.
- [25] C.Y. Meng, D. Zhang, C. Hua, L.Z. Zhuang, J.S. Zhang, J. Alloys Comp. 617(2014) 925-932.
- [26] G. Timelli, B. Franco, Mater. Sci. Eng. A 528(2010) 273-282.
- [27] X.W. Hu, F.G. Jiang, F.R. Ai, H. Yan, J. Alloys Comp. 538(2012) 21-27.
- [28] Q.L. Li, T.D. Xia, Y.F. Lan, W.J. Zhao, L. Fan, P.F. Li, J. Alloys Comp. 562(2013) 25-32.
- [29] W.H. Yuan, Z.Y. Liang, C.Y. Zhang, L.J. Wei, Mater. Design. 34(2012) 788-792.
- [30] Y.L. Duan, G.F. Xu, D. Xiao, L.Q. Zhou, Y. Deng, Z.M. Yin, Mater. Sci. Eng. A 624(2015) 124-131.
- [31] M.M. Sharma, J.D. Tomedi, T.J. Weigley, Mater. Sci. Eng. A 619(2014) 35-46.
- [32] A.C. Magee, L. Ladani, Mater. Sci. Eng. A 582(2013) 276-283.
- [33] H. Toda, Z.A.B. Shamsudin, K. Shimizu, K. Uesugi, A. Takeuchi, Y. Suzuki, M. Nakazawa, Y. Aoki, M. Kobayashi, Acta Mater. 61(2013) 2403-2413.
- [34] S. Banerjee, P.S. Robi, A. Srinivasan, L.P. Kumar, Mater. Sci. Eng. A 527(2010) 2498-2503.
- [35] G. Han, W.Z. Zhang, G.H. Zhang, Z.J. Feng, Y.J. Wang, Mater. Sci. Eng. A 633(2015) 161-168.
- [36] Y.Y. Li, W.H. Wang, Y.F. Hsu, S. Trong, Mater. Sci. Eng. A 497(2008) 10-17.
- [37] Q.G. Wang, Metall. Mater. Trans. A 35A(2004) 2707-2718.
- [38] S. Murali, K.S. Raman, K.S.S. Murthy, Mater. Sci. Eng. A 190A(1995) 165-172.
- [39] G. Davignon, A. Serneels, B. Verlinden, L. Delaey, Metall. Mater. Trans. A 27A(1996) 3357-3361.
- [40] X. Fang, G. Shao, Y.Q. Liu, Z. Fan, Mater. Sci. Eng. A 445-446(2007) 65-72.
- [41] H.I. Laukli, C.M. Gourlay, A..K. Dahle, O. Lohne, Mater. Sci. Eng. A 413-414(2005) 92-97.
- [42] A.K. Dahle, S. Sannes, D.H.S. John, H. Westengen, J. Light Met. 1(2001) 99-103.
- [43] C.M. Gourlay, H.I. Laukli, A.K. Dahle, Metall. Mater. Trans. A 38(2007) 1833-1844.
- [44] S. Otarawanna, C.M. Gourlay, H.I. Laukli, A.K. Dahle, Metall. Mater. Trans. A 40(2009) 1645-1659.
- [45] E. Fiorese, F. Bonollo, G. Timelli, L. Arnberg, E. Gariboldi, Int. J. Metalcast 9(1) (2015) 55-66.
- [46] W.G. Walkington, Die casting defects – causes and solutions, North American Die Casting Association, 1997.
- [47] E. Gariboldi, F. Bonollo, M. Rosso, La Metallurgia Italiana 99(2007) 39-46.
- [48] Aluminium and aluminium alloys-Classification of defects and imperfections in high Pressure, Low Pressure and Gravity Die Cast Products, CEN/TR 16749, 2014.
- [49] Q.G. Wang, C.H. Cáceres, J.R. Griffiths, Metall. Mater. Trans. A 34A(2003) 2901-2912.
- [50] B. Kondori, R. Mahmudi, Metall. Mater. Trans. A 40A(2009) 2007-2015.
- [51] F. Kabirian, R. Mahmudi, Metall. Mater. Trans. A 40A(2009) 116-127.
- [52] C.D. Lee, Mater. Sci. Eng. A 464(1-2) (2007) 249-254.
- [53] C.D. Lee, K.S. Shin, Mater. Sci. Eng. A 599(2014) 223-232.
- [54] H.R. Ammar, A.M. Samuel, F.H. Samuel, Inter. J. Fatigue 30(6)(2008) 1024-1035.
- [55] Y.X. Gao, J.Z. Yi, P.D. Lee, T.C. Lindler, Fatigue Fract. Eng. Mater. Struct. 27(7) (2004) 559-570.
- [56] Q.G. Wang, D. Apelian, D.A. Lados, J. Light Met. 1(2001) 73-84.
- [57] M.A. Le Chatelier, Revue de Metallurgie 6 (1909) 914.
- [58] A. Portevin, F. Le Chatelier, Comptes Rendus Acad. Sci. Paris 176(1923) 507-509.
- [59] Q.G. Wang, M. Praud, A. Needleman, K.S. Kim, J.R. Griffiths, C.J. Davidson, C.H. Cáceres, A.A. Benzerga, Acta Mater. 58(2010) 3006-3013.
- [60] M. Niinomi, T. Kobayashi, K. Ikeda, J. Mater. Sci. 5(9)(1986) 847-848.
- [61] H.S. Rosenbaum, D. Turnbull, Acta Metall. Mater. 6(1958) 653-659.
- [62] J. Coër, P.Y. Manach, H. Laurent, M.C. Oliveira, L.F. Menezes, Mech. Res. Commun. 48(2013) 1-7.
- [63] S. Zhang, P.G. Mccormick, Y. Estrin, Acta Mater. 49(2001) 1087-1094.
- [64] H.F. Jiang, Q.C. Zhang, X.D. Chen, Z.J. Chen, Z.Y. Jiang, X.P. Wu, J.H. Fan, Acta Mater. 55(2007) 2219-2228.
- [65] T.A. Lebedkina, M.A. Lebyodkin, Acta Mater. 56(2008) 5567-5574.
- [66] A.H. Cottrell, Dislocations and plastic flow in crystals, Oxford University Press, London, 1953, pp. 134.
- [67] Y. Estrin, L.P. Kubin, J. Mech. Behav. Mater. 2(1989) 255.
- [68] C. Fressengeas, A.J. Beaudoin, M. Lebyodkin, L.P. Kubin, Y. Estrin, Mater. Sci. Eng. A 400-401(2005) 226-300.
- [69] L.P. Kubin, Y. Estrin, J. Phys. III France 1(1991) 929-943.
- [70] A. Nortmann, C.H. Schwink, Acta Mater. 45(1997) 2043-2051.
- [71] A. Nortmann, C.H. Schwink, Acta Mater. 45(5)(1997) 2051-2058.
- [72] R.A. Mulford, U.F. Kocks, Acta Metall. Mater. 27(7)(1979) 1125-1134.
- [73] P.G. McCormick, Acta metall. Mater. 20(1972) 351-354.
- [74] L.P. Kubin, Y. Estrin, Acta Metall. Mater. 33(1985) 397-407.
- [75] A. van den Beukel, Physica status. solidi. (a) 30(1975) 197-206.
- [76] P. Rodriguez, S. Venkadesans, Solid State Phenom. 42-43(1995) 257-266.
- [77] C.H. Cáceres, J.R. Griffiths, P. Reiner, Acta Mater. 44(1996) 15-23.
- [78] L.M. Brown, W.M. Stobbs, Phil. Mag. 23(1971) 1185-1199.
- [79] L.M. Brown, W.M. Stobbs, Phil. Mag. 23(1971) 1201-1233.
- [80] S.F. Corbin, D.S. Wilkinson, Acta Metall. Mater. 42(4)(1994) 1311-1318.
- [81] Q.G. Wang, Metall. Mater. Trans. A 35A(2004) 2707-2718.
9. Copyright:
- This material is "Peng Zhang"'s paper: Based on "Improved tensile properties of a new aluminum alloy for high pressure die casting".
- Paper Source: https://dx.doi.org/10.1016/j.msea.2015.10.127
This material was summarized based on the above paper, and unauthorized use for commercial purposes is prohibited.
Copyright © 2025 CASTMAN. All rights reserved.