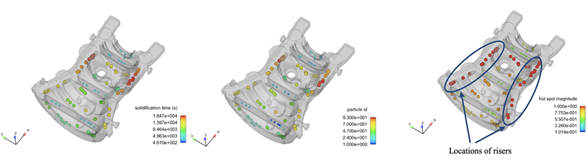
The porosity of die cast parts is one of the primary concerns of buyers and designers. In die casting, porosity refers to the air pockets, small voids, or pores found within a metal part. Too much porosity in a part can be dangerous as it can compromise the structural integrity of the component. Porosity can also cause certain parts to leak, making parts less efficient and causing other problems.
Processing parameters and part design standards can be set to reduce the porosity of the material. Read this post to learn more about what causes porosity in die casting and how to reduce the porosity of your material.
Sources of Porosity in Die Casting
To understand the causes of porosity in die casting, you first need to know about the die casting process. When you start creating the cast part, the mold is closed and the molten metal is injected into the die casting machine under high pressure. In this way, die cast machines and molds hold the molten metal under pressure until it hardens. The water is cast at an optimal speed and passes through a channel to cool the metal.
This process is fast and cost-effective, but porosity can occur when molten metal is poured into the die. The two most common sources of porosity in die casting are:
- Solidification shrinkage: Coagulation shrinkage occurs when a material moves from liquid to solid. This volumetric contraction can open some pores in the material.
- Gas impurities: Gases can come from a variety of sources and can cause impurities in the material. In addition, gases can become trapped in the material and increase the porosity of the material.
How to Control Porosity With Die Casting Processing Parameters
Treatment parameters are measures that monitor a process to see if it is meeting its goals or if there are any issues that need to be adjusted. When creating die casting process parameters, you can continuously measure the porosity of the part and make sure it is at an acceptable level.
Learn about some of the key casting process parameters you can utilize to reduce porosity:
- Mold design: The design of castings and mold parts often affects the overall porosity of the final product. For example, molds with sharp edges and sharp edges can affect porosity. Machining parameters can be set so that the mold is properly designed and has the appropriate hardness.
- Injection speed: Injection speed and machine speed can affect the porosity of the final product. Applying high pressure die casting process parameters can ensure that the injection rate and pressure remain consistent. These parameters also help the machine inject at optimum speed and pressure to reduce porosity.
- Injection temperature: Injection temperature can affect the porosity of parts and components. For example, lower metal temperatures can lead to greater porosity.
- Cleanliness of alloy: Alloy cleanliness can affect the porosity of parts. Contaminants in the alloy can cause more porosity and damage the part. Good machining parameters ensure that the alloy remains as clean as possible, keeping away from potential contaminants.
- Solidification time: The time it takes for a material to move from liquid to solid can affect porosity. Controlling the solidification time and setting parameters can help the material solidify at the best rate for reduced porosity.
Part Design to Reduce Porosity in Die Casting
To reduce porosity in die casting, you need to start with part design. Part designs that do not take into account the die-casting porosity standards or aim to address them may have a greater porosity than those that do not. If you want to reduce porosity, start by working with an engineering team that is die casting savvy and can provide designs for manufacturing insights. It is recommended to perform this step at the beginning of the project.
Companies can also optimize by simulating the die casting process with CFD software. To prevent porosity and protect parts, engineers regularly use overflows, vents, cooling channels, waterways, and runner gates in key locations.
Additionally, if a part needs additional support during the injection process, engineers sometimes use vacuum support to improve the porosity of the casting. High-speed injection of molten alloy meets the resistance and pressure from the air in the die cavity, so porosity is common. By including a vacuum vent, the die cavity can be evacuated more quickly. As a result, the porosity of the part decreases after the molten alloy is injected.
Vacuum casting can also reduce the amount of die lubrication and other residual material before metal is injected into the cavity. This ability to reduce residual material helps prevent excessive gaseous porosity from being created during the solidification process.
Another way a part can be designed to reduce porosity in die casting is to maintain a uniform wall thickness throughout the part. Thin walls tend to have less porosity, while thick walls generally have more shrinkage porosity. Making sure the part is designed with even walls will allow the metal flow to fill the part more and prevent porosity better than if the thin and thick walls were mixed.
How to Predict and Measure Porosity
If you have processing parameters that control porosity, you can better handle the entire die casting process and thus better predict porosity. Low porosity levels can be predicted much more easily by applying die casting porosity standards. In addition, the software can be used to simulate the die casting process, allowing you to better predict the porosity of the part and address the factors that cause the higher porosity before starting die casting.
Several different methods can be used to measure the porosity of a material. One of the common and easy ways to test for excessive porosity of a part is to perform a density or gravimetric measurement. Too much porosity can occur if the part is lighter than expected.
For advanced testing, porosity can be measured using a destructive test or a 3D X-ray machine. Not only does this method provide detailed information about where porosity occurs in a part, it can also more accurately measure the porosity of the part or material under test. Leak tests can also be used with special purpose-built fixtures to check the pressure tightness of the castings.
Contact Premier Engineered Products for Die Casting Services
When you want to control porosity in your parts, you’ll want to turn to the experts. At CASTMAN, we know how to reduce porosity with the proper processing parameters. As a result, we can deliver high-quality parts and components to your business at an affordable cost.
처리 매개 변수로 다공성을 제어하는 방법
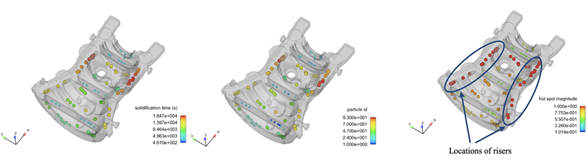
다이 캐스트 부품의 다공성은 구매자와 설계자의 주요 관심사 중 하나입니다. 다이 캐스팅에서 다공성은 금속 부품 내에서 발견되는 공기 주머니, 작은 공극 또는 구멍을 나타냅니다. 부품에 너무 많은 다공성은 구성 요소의 구조적 무결성에 해를 끼칠 수 있으므로 위험 할 수 있습니다. 다공성은 또한 특정 부품의 누출을 유발하여 부품의 효율성을 감소시키고 다른 문제를 일으킬 수 있습니다.
재료의 다공성을 줄이기 위해 처리 매개 변수 및 부품 설계 표준을 설정할 수 있습니다. 이 게시물을 통해 다이 캐스팅의 다공성 원인과 재료에서 다공성을 줄이는 방법에 대해 자세히 알아보십시오.
다이캐스팅의 다공성 원인
다이 캐스팅에서 다공성의 원인을 이해하려면 먼저 다이 캐스팅 공정에 대해 알아야합니다. 주조 부품 생성을 시작할 때 금형을 닫고 용융 금속을 고압으로 다이 캐스트 기계에 주입합니다. 이렇게하면 다이 캐스트 기계와 금형은 압력에 의해 굳을 때까지 용융 금속을 유지합니다. 물은 최적의 속도로 주조하고 금속을 냉각하는데 도움이 되도록 수로를 통과합니다.
이 프로세스는 빠르고 비용 효율적이지만 용융 금속을 다이에 주입하면 다공성이 발생할 수 있습니다. 다이 캐스팅에서 가장 일반적인 두 가지 다공성 원인은 다음과 같습니다.
- 응고 수축 : 응고 수축은 재료가 액체에서 고체로 이동할 때 발생합니다. 이러한 체적 수축으로 인해 재료의 일부 기공이 열릴 수 있습니다.
- 가스 불순물 : 가스는 다양한 소스에서 나올 수 있으며 재료에 불순물을 유발할 수 있습니다. 또한 가스가 재료에 갇혀 재료의 다공성이 높아질 수 있습니다.
다이캐스팅 공정 매개 변수로 다공성을 제어하는 방법
처리 매개 변수는 프로세스가 목표에 도달했는지 또는 조정해야 할 문제가 있는지 확인하기 위해 프로세스를 모니터링하는 측정입니다. 다이캐스팅 공정 매개 변수를 생성할 때 부품의 다공성을 지속적으로 측정하고 허용 가능한 수준인지 확인할 수 있습니다.
다공성을 줄이기 위해 활용할 수 있는 몇 가지 주요 주조 공정 매개 변수에 대해 알아보십시오.
- 금형 설계 : 주조 및 금형 부품의 설계는 종종 최종 제품의 전체 다공성에 영향을 미칩니다. 예를 들어 모서리와 모서리가 날카로운 금형은 다공성에 영향을 미칠 수 있습니다. 금형이 적절하게 설계되고 적절한 경도를 갖도록 가공 매개 변수를 설정할 수 있습니다.
- 주입 속도 : 주입 속도와 기계 속도는 최종 제품의 다공성에 영향을 미칠 수 있습니다. 고압 다이 캐스팅 공정 매개 변수를 적용하면 주입 속도와 압력이 일관되게 유지 될 수 있습니다. 이러한 매개 변수는 기계가 다공성을 줄이기 위해 최적의 속도와 압력으로 주입하는데도 도움이 됩니다.
- 주입 온도 : 주입 온도는 부품 및 구성 요소의 다공성에 영향을 줄 수 있습니다. 예를 들어 낮은 금속 온도는 더 큰 다공성을 초래할 수 있습니다.
- 합금의 청결 : 합금의 청결은 부품의 다공성에 영향을 미칠 수 있습니다. 합금의 오염 물질은 더 많은 다공성을 유발하고 부품을 손상시킬 수 있습니다. 좋은 가공 매개 변수는 합금이 가능한 한 깨끗하게 유지되도록 보장하여 잠재적 인 오염 물질을 멀리합니다.
- 응고 시간 : 재료가 액체에서 고체로 이동하는 데 걸리는 시간은 다공성에 영향을 줄 수 있습니다. 응고 시간을 제어하고 매개 변수를 설정하면 다공성 감소를 위해 재료가 최상의 속도로 응고되는 데 도움이 될 수 있습니다.
다이캐스팅의 다공성을 줄이기위한 부품 설계
다이캐스팅에서 다공성을 줄이려면 부품 설계 부터 시작해야합니다 . 다이캐스팅 다공성 표준을 고려하지 않거나 이를 해결하는 것을 목표로 하는 부품 설계는 그렇지 않은 것보다 더 큰 다공성을 가질 수 있습니다. 다공성을 줄이려면 다이 캐스팅에 정통하고 제조 통찰력을 위한 설계를 제공 할 수 있는 엔지니어링 팀과 협력하여 시작하십시오. 프로젝트 시작시이 단계를 수행하는 것이 좋습니다.
회사는 CFD 소프트웨어를 사용하여 다이 캐스팅 공정을 시뮬레이션하여 최적화 할 수도 있습니다. 다공성을 방지하고 부품을 보호하기 위해 엔지니어는 정기적으로 주요 위치에 오버플로, 통풍구, 냉각 채널, 수로 및 러너 게이트를 사용합니다.
또한 부품이 사출 공정에서 추가 지원이 필요한 경우 엔지니어는 때때로 진공 보조 장치를 사용하여 주조의 다공성을 개선합니다. 용융 된 합금의 고속 주입은 다이 캐비티의 공기로부터 저항과 압력을 충족하기 때문에 다공성이 발생하는 것이 일반적입니다. 진공 벤트를 포함함으로써 다이 캐비티의 공기를 더 빨리 빼낼 수 있습니다. 결과적으로 용융 합금이 주입된 후 부품의 다공성이 줄어 듭니다.
진공 주조는 또한 금속이 캐비티에 주입되기 전에 다이 윤활 및 기타 잔류 물질의 양을 줄일 수 있습니다. 잔류 물질을 줄이는 이 기능은 응고 과정에서 과도한 가스 다공성이 생성되는 것을 방지하는 데 도움이 됩니다.
다이캐스팅의 다공성을 줄이기 위해 부품을 설계 할 수 있는 또 다른 방법은 부품 전체에 균일한 벽 두께를 유지하는 것입니다. 얇은 벽은 다공성이 적은 경향이 있는 반면 두꺼운 벽은 일반적으로 수축 다공성이 더 많습니다. 부품이 균일한 벽으로 설계되었는지 확인하면 얇고 두꺼운 벽이 혼합 된 경우보다 금속 흐름이 부품을 더 많이 채우고 다공성을 더 잘 방지 할 수 있습니다.
다공성 예측 및 측정 방법
다공성을 제어하는 처리 매개 변수가 있으면 전체 다이 캐스팅 공정을 더 잘 처리 할 수 있으므로 다공성을 더 잘 예측할 수 있습니다. 다이캐스팅 다공성 표준을 사용하면 낮은 다공성 수준을 훨씬 쉽게 예측할 수 있습니다. 또한 소프트웨어를 사용하여 다이 캐스팅 프로세스를 시뮬레이션 할 수 있으므로 다이 캐스팅을 시작하기 전에 부품의 다공성을 더 잘 예측하고 다공성을 높이는 요인을 해결할 수 있습니다.
재료의 다공성을 측정하기 위해 몇 가지 다른 방법을 사용할 수 있습니다. 부품의 과도한 다공성을 테스트하는 일반적이고 쉬운 방법 중 하나는 밀도 또는 중량 측정을 수행하는 것입니다. 부품이 예상보다 가벼우면 너무 많은 다공성이 발생할 수 있습니다.
보다 고급 테스트를 위해 해체 테스트 또는 3D X-ray 기계를 사용하여 다공성을 측정 할 수 있습니다. 이러한 방법은 부품에서 다공성이 발생한 위치에 대한 자세한 정보를 제공 할뿐만 아니라 테스트중인 부품 또는 재료의 다공성에 대한보다 정확한 측정을 제공 할 수 있습니다. 주물의 압력 견고성을 확인하려면 특수 목적의 고정 장치를 사용하여 누출 테스트를 사용할 수도 있습니다.
다이캐스팅 서비스를 위해 프리미어 엔지니어링 제품에 문의
부품의 다공성을 제어하려면 전문가에게 문의해야 합니다. 캐스트맨에서는 적절한 처리 매개 변수로 다공성을 줄이는 방법을 알고 있습니다. 결과적으로 우리는 저렴한 비용으로 고품질 부품 및 구성 요소를 비즈니스에 제공 할 수 있습니다.