This article introduces the paper 'High Pressure Die Casting of Aluminium and Magnesium Alloys - Grain Structure and Segregation Characteristics' published by 'Norwegian University of Science and Technology (NTNU)'.
1. Overview:
- Title: High Pressure Die Casting of Aluminium and Magnesium Alloys - Grain Structure and Segregation Characteristics
- Author: Hans Ivar Laukli
- Publication Year: April 2004
- Publishing Journal/Academic Society: Norwegian University of Science and Technology (NTNU)
- Keywords: Not explicitly listed in the provided document, keywords can be inferred from the title and abstract as: High Pressure Die Casting, Aluminium Alloys, Magnesium Alloys, Grain Structure, Segregation Characteristics, Solidification.
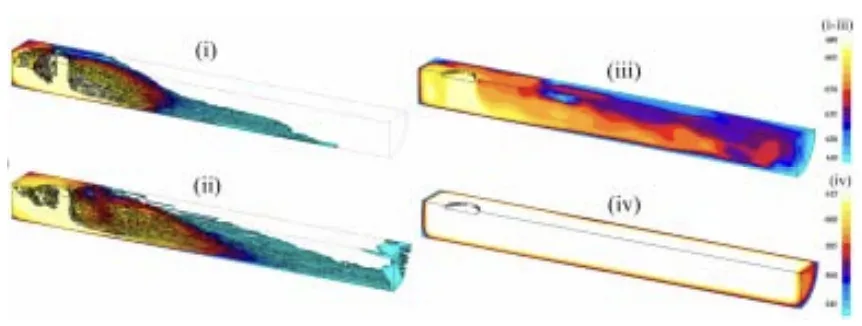
2. Abstracts or Introduction
Cold chamber high pressure die casting, (HPDC), is an important commercial process for the production of complex near net shape aluminium and magnesium alloy castings. The work presented in the thesis was aimed at investigating the microstructure formation in this type of casting.
The solidification characteristics related to the process and the alloys control the formation of grains and defects. This again has a significant impact on the mechanical properties of the castings. The investigations were carried out mainly using the AM60 magnesium alloy and the A356 aluminium alloy. Two different casting arrangements were used: the cold chamber HPDC and the gravity die casting methods, which allowed for different flow and solidification conditions.
The microstructures in the castings were investigated using optical microscopy, image analysis, scanning electron microscopy, electron back scatter diffraction measurements and electron probe microanalysis. In the HPDC experiments, the shot sleeve solidification conditions were investigated primarily by changing the melt superheat on pouring.
This significantly affected the microstructures in the castings. The fraction of externally solidified crystals (ESCs) was consistently found to be largest near the gate in both the AM60 and the A356 die castings. This was attributed to the inherent shot sleeve solidification conditions and the flow set up by the plunger movement. When the superheat was increased, a lower fraction of ESCs was found in the castings.
Furthermore, a high superheat gave ESCs with branched dendritic/elongated trunk morphology whilst a low superheat generated coarser and more globular ESCs, both in the AM60 and the A356 castings. The ESCs typically segregated towards the central region of the cross sections at further distances from the gate in the die castings.
When a thin layer of thermal insulating coating was applied on the shot sleeve wall in the production of AM60 die castings, it nearly removed all ESCs in the castings. Using an A356 alloy, (and no shot sleeve coating), with no Ti in solution gave a significantly lower fraction of ESCs, whereas AlTi5B1 grain refiner additions induced an increase in the fraction of ESCs and a significantly finer grain size in the castings.
The formation of globular ESCs was enhanced when AlTi5B1 grain refiner was added to the A356 alloy. In controlled laboratory gravity die casting experiments, typical HPDC microstructures were created by pouring semi-solid metal into a steel die: The ESCs were found to segregate/migrate to the central region during flow, until a maximum packing, (fraction of ESCs of ~35-40%), was reached.
The extent of segregation is determined by the fraction of ESCs, and the die temperature affects the position of the ESCs. The segregation of ESCs was explained to occur during flow as a result of lift forces. The formation of banded defects has also been studied: the position of the bands was affected by the die temperature and the fraction of ESCs.
Based on the nature of the bands and their occurrence, a new theory on the formation of defect bands was proposed: During flow the solid distribution from the die wall consists of three regions: 1) a solid fraction gradient at the wall; 2) a low solid fraction region which carries (3) a network of ESCs. A critical fraction solid exists where the deformation rate exceeds the interdendritic flow rate.
When the induced stress exceeds the network strength, deformation can occur by slip, followed by liquid flow. The liquid flow is caused by solidification shrinkage, hydrostatic pressure on the interior ESC network, and gaps forming which draw in liquid.
3. Research Background:
Background of the Research Topic:
The research addresses the critical area of microstructure formation in High Pressure Die Casting (HPDC), a commercially vital process for producing complex, near net shape aluminium and magnesium alloy castings. The paper highlights the challenge of inconsistent mechanical properties in HPDC components compared to wrought products, often attributed to process parameter variations but lacking sufficient documentation. This inconsistency hinders the broader application of HPDC, particularly in demanding sectors like the automotive industry where crashworthiness and fatigue resistance are paramount.
Status of Existing Research:
Existing research acknowledges the influence of process parameters on HPDC quality, but systematic investigations, especially concerning shot sleeve conditions and their impact on microstructure, were deemed insufficient. The preface mentions that documentation of process parameter variations and their effects is often "unsatisfactory". The introduction refers to the need for "scientific comprehension of the process and metal behavior" to improve crashworthiness and fatigue properties for extended automotive applications.
Necessity of the Research:
The research is necessitated by the need to improve the mechanical property consistency of HPDC components. The project was initiated because "documentation is often unsatisfactory" regarding the link between process parameters and casting quality. Norsk Hydro's installation of a state-of-the-art HPDC machine provided the opportunity for "more systematic investigations of the HPDC process and the effect of different parameters". The doctorate work was specifically started to analyze "shot sleeve conditions and analysis of the effects on the microstructure in the castings caused by the metal fed into the die." This indicates a clear necessity to understand and control the initial solidification stages in the shot sleeve to enhance the final casting microstructure and properties.
4. Research Purpose and Research Questions:
Research Purpose:
The primary research purpose is to investigate the microstructure formation in High Pressure Die Casting (HPDC) of aluminium and magnesium alloys. Specifically, the thesis aims to understand how solidification characteristics, influenced by process parameters and alloy composition, control grain formation and defects, and consequently, the mechanical properties of HPDC castings.
Key Research:
The key research areas explored in this study are:
- Shot Sleeve Solidification Conditions: Investigating the impact of shot sleeve conditions, particularly melt superheat, on microstructure.
- Externally Solidified Crystals (ESCs): Analyzing the formation, morphology, and segregation of ESCs in HPDC castings.
- Grain Size Distribution: Examining the distribution of grain sizes and the role of ESCs in creating bimodal grain structures.
- Banded Defects: Studying the formation mechanisms of banded defects, including segregation and porosity bands.
- Effect of Grain Refiners: Evaluating the influence of grain refiner additions (AlTi5B1) on grain structure and ESC formation in A356 alloy.
- Crystal Migration: Investigating the migration and segregation of crystals during semi-solid flow in gravity die casting experiments simulating HPDC conditions.
Research Hypotheses:
While not explicitly stated as formal hypotheses, the research operates under the following implicit hypotheses:
- Shot sleeve solidification conditions, particularly melt superheat, significantly influence the formation and characteristics of ESCs and the overall microstructure in HPDC castings.
- ESCs play a crucial role in determining grain size distribution and the formation of defects like banded structures.
- Grain refiner additions can modify ESC formation and refine the grain structure in HPDC aluminium alloys.
- Segregation of ESCs in HPDC castings is driven by flow dynamics and lift forces acting on solidifying crystals.
- Banded defects in HPDC are related to the interplay of solid fraction gradients, ESC migration, and rheological properties of the semi-solid metal during die filling.
5. Research Methodology
Research Design:
The research employs a combination of experimental studies using both industrial-scale HPDC and controlled laboratory gravity die casting, coupled with analytical modeling and microstructural characterization techniques. The HPDC experiments focused on manipulating process parameters like melt superheat and shot sleeve coating, while gravity die casting experiments were designed to simulate HPDC microstructures under controlled conditions.
Data Collection Method:
Data collection methods include:
- HPDC Experiments: Casting of AM60 magnesium alloy and A356 aluminium alloy box-shaped components using a state-of-the-art HPDC machine. Process parameters were systematically varied, including melt superheat and shot sleeve coating.
- Gravity Die Casting Experiments: Controlled laboratory experiments involving pouring semi-solid A356 aluminium alloy into a steel die to mimic HPDC microstructures and investigate ESC segregation and banded defect formation.
- Interrupted Die Filling Tests: Stopping the HPDC process at different stages of die filling to observe metal flow patterns and microstructure evolution.
- Temperature Measurements: Infrared thermographic measurements of shot sleeve temperature and thermocouple measurements of melt temperature.
Analysis Method:
Analysis methods used in the research include:
- Microscopy: Optical microscopy, Scanning Electron Microscopy (SEM), and Electron Backscatter Diffraction (EBSD) were used to characterize the microstructure, grain size distribution, and ESC morphology.
- Image Analysis: Quantitative image analysis was employed to measure the area fraction of ESCs and eutectic phases.
- Electron Probe Microanalysis (EPMA): EPMA was used to analyze the chemical composition of different microstructural features, particularly silicon and titanium distribution.
- Analytical Modeling: Development and application of analytical models to understand solidification in the shot sleeve and predict fraction solid.
- Numerical Simulations: Numerical simulations were used to model shot sleeve filling, temperature evolution, and fluid flow behavior.
Research Subjects and Scope:
- Materials: AM60 magnesium alloy and A356 aluminium alloy were the primary materials investigated.
- Casting Methods: Cold chamber High Pressure Die Casting (HPDC) and gravity die casting.
- Focus: Grain structure, segregation characteristics, and defect formation in thin-walled castings.
- Scale: Industrial HPDC machine and laboratory-scale gravity die casting setup.
6. Main Research Results:
Key Research Results:
- Shot Sleeve Solidification: Shot sleeve conditions significantly impact microstructure. Lower melt superheat and colder shot sleeves lead to a higher fraction of ESCs. Thermal insulating shot sleeve coatings nearly eliminate ESCs in AM60 castings.
- ESC Morphology: Melt superheat influences ESC morphology. Low superheat results in coarser, globular ESCs, while high superheat leads to branched, dendritic/elongated ESCs.
- Grain Refinement Effects: AlTi5B1 grain refiner additions in A356 alloy enhance globular ESC formation and refine grain size. Ti in solution increases ESC fraction, while AlTi5B1 additions further enhance globular ESCs.
- ESC Segregation: ESCs consistently segregate towards the gate region in HPDC castings and migrate to the central region during flow in gravity die casting experiments, reaching a maximum packing fraction (~35-40%). Segregation is attributed to lift forces during flow.
- Banded Defects Formation: Banded defects are influenced by die temperature and ESC fraction. A new theory proposes that defect bands form due to deformation and liquid flow in a low solid fraction region carrying an ESC network, driven by solidification shrinkage and hydrostatic pressure.
Analysis of presented data:
- Melt Superheat and ESCs: Increased melt superheat reduces ESC fraction and alters morphology from globular to dendritic. This is attributed to reduced nucleation and increased remelting of ESCs at higher temperatures.
- Grain Refiners and ESCs: Grain refiners, particularly AlTi5B1, promote globular ESC formation and finer grain size, suggesting enhanced heterogeneous nucleation.
- ESC Segregation Mechanism: Gravity die casting experiments confirm ESC segregation during flow, reaching a packing limit. Lift forces are proposed as the driving mechanism for ESC migration towards the central region.
- Banded Defects Theory: The proposed three-region model for solid distribution during flow explains banded defect formation as a consequence of deformation and liquid segregation in specific solid fraction zones.
Figure Name List:
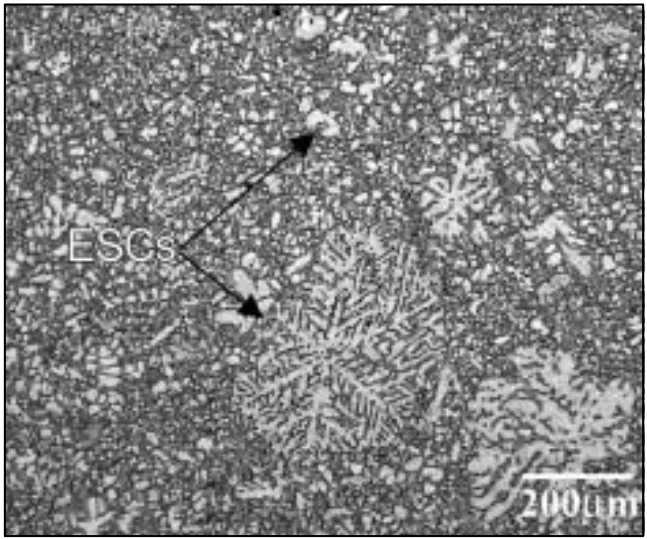
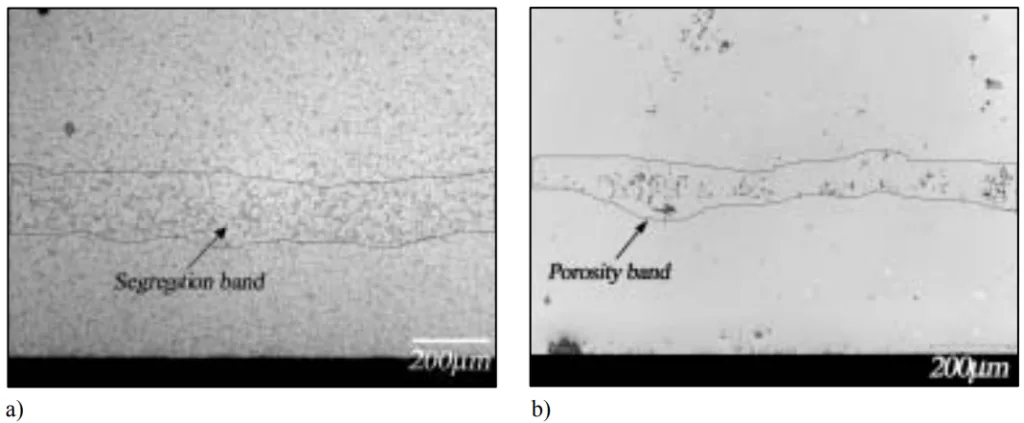
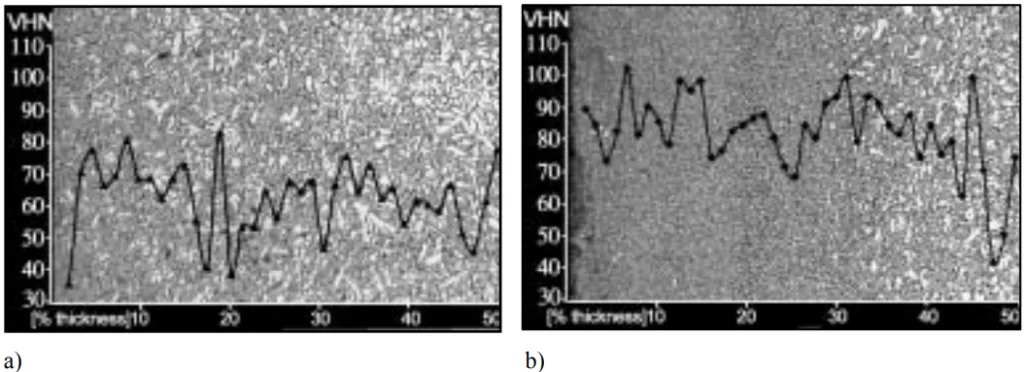
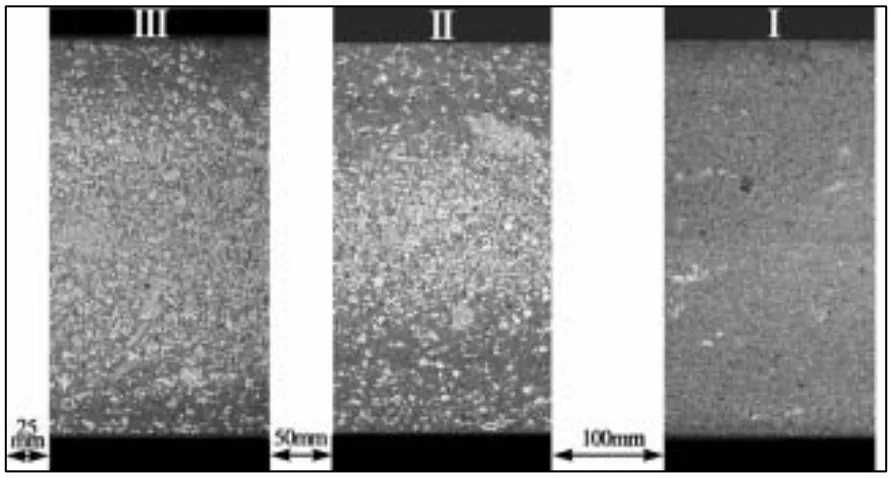
- Figure 1: Illustration of cold chamber high pressure die casting.
- Figure 2: Nucleation is feasible in the thermally undercooled region adjacent to the die wall when the melt undercooling, ΔTt, exceeds the required nucleation undercooling ΔTn.
- Figure 3: Illustration of the principles for constitutional undercooling in constrained growth.
- Figure 4: The low-solute parts of the Al-Si, (black lines), and Mg-Al, (blue lines), binary phase diagrams.
- Figure 5: Measurements of the shear strength of the material as a function of fraction solid, (fs), for the two extremes in crystal morphology; large dendritic crystals and small globular crystals.
- Figure 6: a) Simulation of the filling of an A380 aluminium alloy. b) Simulation of particle position during filling.
- Figure 7: Simulation of the melt temperature evolution in the shot sleeve, (longitudinal cross section), for an A356 aluminium alloy.
- Figure 8: a) Cross sectional micrograph from the biscuit. b) Magnification of the microstructure near the plunger.
- Figure 9: Cross sectional micrograph from an A380 aluminium alloy die casting which shows large cold flakes embedded in the microstructure.
- Figure 10: Optical micrograph from an industrially produced HPDC AM60 instrument panel.
- Figure 11: Shot profile from an AM60 magnesium alloy die casting.
- Figure 12: Surge wave, with velocity vw, ahead of plunger tip, with velocity vp.
- Figure 13: Simulation of slow shot plunger movement and simultaneous metal flow and fraction solid distribution.
- Figure 14: At approximately 70% plunger movement photographs of: a) The fragmented flow front; b) A location where the metal has frozen through the thickness during die filling, (marked with arrow).
- Figure 15: a) Segregation band in an A356 die casting; b) A porosity band in an AM60 die casting.
- Figure 16: Illustration of: a) The fraction solid profile; b) The corresponding strength profile; c) The resulting microstructure where the central region facilitates deformation by slip along the segregated shear plane.
- Figure 17: a) Segregation bands in an A356 aluminium alloy die casting. b) Typical HPDC microstructure.
- Figure 18: Measurements of microhardness (VHN), (10g indentation load), from the surface to the centre in half of the cross sections of thin walled, (2.5mm), AM60 magnesium alloy die castings: a) Large fraction of ESCs ~evenly distributed, with an average VHN 63; b) The ESCs are only located in the central region.
- Figure 19: Cross sectional micrographs from tensile tested specimens taken from AM60 magnesium alloy die castings: a) Near the gate, typical elongation: 3-10%; b) Farther from the gate, typical elongation: 15-25%.
- Figure 20: Schematic illustration of the plunger movement and corresponding qualitative description of fraction solid distribution.
- Figure 21: The solidification and metal flow in the shot sleeve results in microstructures with different thermal histories in the casting.
- Figure 22: Schematic illustration of the packing of ESCs in the central region.
7. Conclusion:
Summary of Key Findings:
This research provides a comprehensive investigation into the microstructure formation in HPDC aluminium and magnesium alloys, emphasizing the role of shot sleeve solidification, ESCs, and process parameters. Key findings include the significant influence of melt superheat and shot sleeve conditions on ESC formation and morphology, the effectiveness of grain refiners in modifying ESC characteristics and grain size, the segregation behavior of ESCs driven by flow dynamics, and a new theory explaining banded defect formation based on semi-solid rheology.
Academic Significance of the Study:
The study contributes significantly to the fundamental understanding of solidification phenomena in HPDC, particularly concerning the formation and behavior of ESCs. The research provides valuable insights into the complex interplay of process parameters, alloy composition, and microstructure evolution in this high-speed casting process. The proposed theory for banded defect formation and the detailed analysis of ESC segregation mechanisms advance the scientific knowledge base in die casting metallurgy.
Practical Implications:
The findings have direct practical implications for the die casting industry. The research highlights strategies for controlling ESC formation and distribution through melt superheat management and shot sleeve design modifications, including thermal insulating coatings. The study also demonstrates the effectiveness of grain refiners in improving microstructure and potentially enhancing mechanical properties. This knowledge can be used to optimize HPDC processes for improved casting quality, reduced defects, and enhanced mechanical performance, particularly ductility.
Limitations of the Study and Areas for Future Research:
The study acknowledges limitations in fully capturing the complex, dynamic nature of the HPDC process in laboratory simulations. Further research is suggested in the following areas:
- Investigating the effects of different alloys on ESC formation, segregation, and banded defect characteristics.
- Further exploring the nucleation mechanisms of ESCs, particularly the formation of globular crystals and the role of crystal remelting/dissolution.
- Conducting more detailed experiments measuring temperature evolution in the shot sleeve during pouring and die filling.
- Developing more refined computer models incorporating two-phase flow, heat transfer, and non-isothermal melt conditions in the shot sleeve to improve process simulation and defect prediction.
- Further investigation into the lift mechanisms responsible for ESC segregation and the influence of different die geometries and flow rates on defect band formation.
- Exploring the impact of grain refinement on magnesium alloys in HPDC, as it is less established compared to aluminium alloys.
8. References:
- [1] E.J. Vinarcik, High Integrity Die Casting Processes, John Wiley & Sons, Inc., 2003.
- [2] L.J.D. Sully, Metals Handbook, 15, 286-295.
- [3] M. M. Avedesian, H. Baker, Magnesium and Magnesium Alloys, ASM International, 1999.
- [4] A. Kaye, A. Street, Die Casting Metallurgy, Butterworth scientific, 1982.
- [5] N. Fantetti, O. Holta, J.B. R¯nhaug, D. Albright, NADCA Trans., 1997, 19, T97-054.
- [6] Melting and handling magnesium for die casting, Hydro Magnesium Data Sheet, 2002.
- [7] Introduction to Die Casting, NADCA, 1997.
- [8] A.D. Figueredo, Science and Technology of Semi-Solid Metal Processing, NADCA, 2001.
- [9] Die Casting - Process Optimization, B¸hler Druckguss, 2001.
- [10] L. B‰ckerud, C. Chai, J. Tamminen, Solidification Characteristics of Aluminium Alloys, AFS/Skanaluminium, 2, 1990.
- [11] W.G. Walkington, Die Casting Defects - Causes and Solutions, NADCA, 1997.
- [12] M.C. Flemings, Solidification Processing, McGraw-Hill, 1974.
- [13] W. Kurz, D.J. Fisher, Fundamentals of Solidification, Trans Tech Publications, 1998.
- [14] P.A. T¯ndel, PhD thesis, Norwegian Institute of Technology (Trondheim), 1994.
- [15] D.A. Porter, K.E. Easterling, Phase Transformations in Metals and Alloys, Chapman & Hall, 1997.
- [16] J. Campbell, Castings, Butterworth-Heinemann, 1997.
- [17] A. Ohno, Solidification - The Separation Theory and its Practical Applications, Springer Verlag, 1987.
- [18] B. Chalmers, J. Aust. Inst. of Metals, 1963, 8, 255-263.
- [19] R.T. Southin, Trans. AIME, 1966, 239, 220-225.
- [20] W.C. Winegard, B. Chalmers, Trans. ASM, 1954, 46, 1214-1224.
- [21] I. Maxwell, A. Hellawell, Acta Met., 1975, 23, 229-237.
- [22] K.A. Jackson, J.D. Hunt, D.R. Uhlmann, T.P. Seward, Trans. AIME, 1966, 236, 149-158.
- [23] E.F. Emley, Principles of Magnesium Technology, Pergamon Press Ltd., 1966.
- [24] A.W. Woods, J. Fluid Mech., 1992, 239, 429-448.
- [25] G. Hansen, A. Hellawell, S.Z. Lu, R.S. Steube, Met. Mat. Trans. A, 1996, 27A, 569-581.
- [26] Die Cast Magnesium Alloys, Hydro Magnesium Data Sheet, 2001.
- [27] J.R. Davis, Aluminum and Aluminum Alloys, ASM International, 1993.
- [28] A. Hellawell, 4th Int. Conf. on Semi-Solid Proc. Alloys Comp., 1996, 60-65.
- [29] Q. Han, A. Hellawell, Met. Mat. Trans. B, 1997, 28B, 169-173.
- [30] A.K. Dahle, D.H. StJohn, Acta Mat., 1998, 47, 31-41.
- [31] A.K. Dahle, L. Arnberg, J. of Met., 1996, 48, 34-37.
- [32] L. Wang, T. Nguyen, G. Savage, C.J. Davidson, Int. J. C.Met.R., 2003, 16, 409-417.
- [33] L. Wang, T. Nguyen, M. Murray, NADCA Trans., 2001, 21, T01-014.
- [34] H.T. Haaland, PhD thesis, Norwegian University of Science and Technology (Trondheim), 2000.
- [35] F.M. White, Fluidmechanics, McGraw-Hill, 1999.
- [36] S. Sannes, 2003. Personal communication.
- [37] H. Iwahori, M. Nakamura, K. Tozawa, Y. Yamamoto, NADCA Trans., 1985, 13, 1-9.
- [38] P. Paliani, L. Zalewski, J. Barreto, N. Tsumagari, J. Brevick, C. Mobley, NADCA Trans., 1995, 18, 149-155.
- [39] S. Sannes, Fill Tests - Simulations and Microstructures in U-profile Castings, Hydro Aluminium, Porsgrunn, 2003, 03P_BN2.doc.
- [40] P. Schmidt, PhD thesis, Royal Institute of Technology (Stockholm), 1994.
- [41] W. Sequeira, PhD thesis, The University of Queensland (Brisbane), 2000.
- [42] S. Sannes, H. Gjestland, H. Westengen, H.I. Laukli, Proc. Int. Conf. Mg. Alloys & Appl., 2003, 6, 725-731.
- [43] R. Chatfield, P.W. Rohan, ADCA Die Casting Conf., 2000, paper15; 11-15.
- [44] N. Tsumagari, T. Liang, J. Brevick, C. Mobley, NADCA Trans., 2001, 21, 251-256.
- [45] M. Gershenzon, P.W. Rohan, M.T. Murray, NADCA Trans., 1999, 20, 305-315.
- [46] T. Abbott, M. Easton, Mat. Forum, 2001, 25, 181-201.
- [47] D. StJohn, A.K. Dahle, T. Abbott, M.D. Nave, M. Qian, Proc. Magnesium Techn., 2003, 95-100.
- [48] S. Sannes, H. Gjestland, 2004. Personal communication.
- [49] P. Koch, Die Casting Eng., 1974, 18, 44-46.
- [50] L.W. Garber, Die Casting Eng., 1982, 26, 14-22.
- [51] J. Brevick, M. Duran, Y. Karni, NADCA Trans., 1991, 15, 399-404.
- [52] OSU Center for Die Casting, Effects of ESP on wave celerity and die cast products - 2D athermal model, 2002, http://www.mse.eng.ohio-state.edu/~mobley/diecasting/.
- [53] E.A. Herman, Heat Flow in the Die Casting Industry, NADCA, 1997.
- [54] A. Bowles, PhD thesis, The University of Queensland (Brisbane), 2002.
- [55] Z.W. Chen, Mat. Sci. Eng. A, 2003, 348, 145-153.
- [56] T.B. Hill, BNF Guide to Better Magnesium Die Casting, BNF Metals Technology Centre, 1976.
- [57] S. Sannes, H. Westengen, Proc. Int. Conf. Mg. Alloys & Appl., 1998, 4, 223-228.
- [58] P.D.D. Rodrigo, V. Ahuja, Proc. Int. Conf. Mag. Sci. Techn., 2000, 97-104.
- [59] C. Pitsaris, T. Abbott, C.J. Davidson, Light Met. Techn., 2003, 223-226.
- [60] H. Cao, M. Wessen, 11th Mg Autom.End User Sem., 2003, 1-22.
- [61] G.K. Batchelor, Theoretical and Applied Mechanics, Elsevier Science publishers, 1989, 27-40.
- [62] G.E. Dieter, Mechanical Metallurgy, McGraw-Hill, 1988.
- [63] C. Pitsaris, T. Abbott, C.H.J. Davies, G. Savage, Proc. Int. Conf. Mg. Alloys & Appl., 2003, 6, 694-699.
- [64] C. D¯rum, O.S. Hopperstad, O.-G. Lademo, M. Langseth, Int. J. Sol. Struct., 2004, submitted.
- [65] C. D¯rum, 2004. Personal communication.
- [66] H. Gjestland, 2004. Personal communication.
9. Copyright:
- This material is "Hans Ivar Laukli"'s paper: Based on "High Pressure Die Casting of Aluminium and Magnesium Alloys - Grain Structure and Segregation Characteristics".
- Paper Source: https://doi.org/N/A (DOI URL Not Available in the document)
This material was summarized based on the above paper, and unauthorized use for commercial purposes is prohibited.
Copyright © 2025 CASTMAN. All rights reserved.