This introductory paper is the research content of the paper "High pressure die casting mould repair technologies" published by MTSM2017.
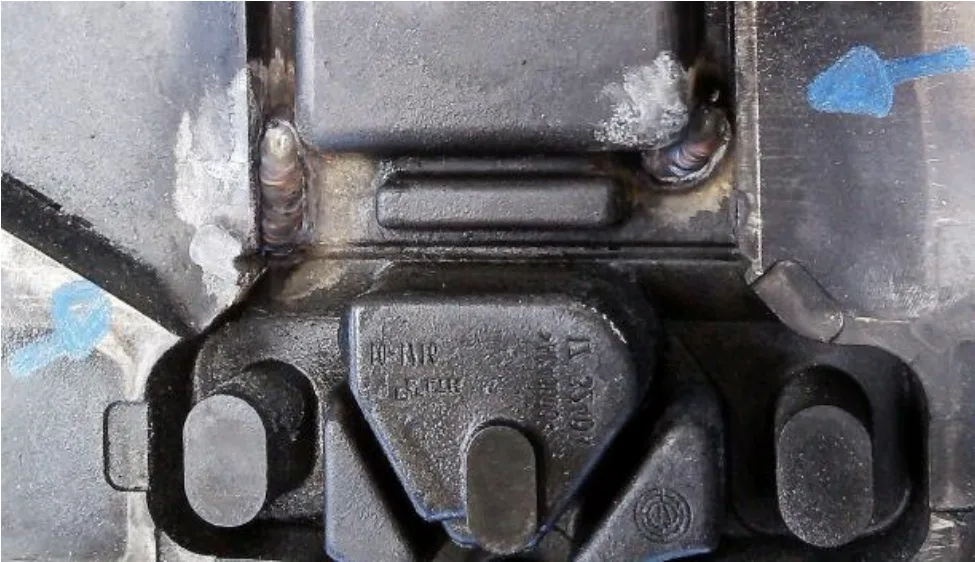
1. Overview:
- Title: High pressure die casting mould repair technologies
- Author: Zvonimir DADIĆ, Dražen ŽIVKOVIĆ, Nikša ČATIPOVIĆ, Josip BILIĆ
- Publication Year: 2017
- Publishing Journal/Academic Society: International conference "Mechanical Technologies and Structural Materials" Split.
- Keywords: Mould wear, Thermal fatigue, Welding, Tool steel
2. Abstracts / Introduction
This paper presents the most commonly used technologies for repairing high-pressure die-cast moulds. High-pressure die casting (HPDC) effectively addresses issues found in conventional casting, such as porosity, surface roughness, long production times, thin-section limitations, and dimensional accuracy. The material commonly used for HPDC permanent molds is highly alloyed hot work tool steel, often H13 (ASTM). During use, the mold surface is damaged, predominantly by thermal cracking. Repair extends the mold's lifespan and reduces production costs.
3. Research Background:
Background of the Research Topic:
The mould is the most complex and expensive component of the HPDC process.
Status of Existing Research:
Prior research indicates that thermal fatigue is the most significant wear mechanism in HPDC molds. The extreme temperature fluctuations during the casting cycle cause surface cracks.
Necessity of the Research:
Because of those aggressive conditions, highly alloyed steel is used as the mould material. Due to the high cost and complexity of HPDC molds, research into repair technologies is crucial for extending mold lifespan and reducing production costs.
4. Research Purpose and Research Questions:
Research Purpose:
To describe the most common technologies for repairing high-pressure die casting molds.
Key Research:
The Key Research of this paper describes:
- Mould material and its treatment.
- Wear mechanisms that damage.
- The technologies use to repair those molds.
5. Research Methodology
Research Design:
This is a review paper, synthesizing existing knowledge and practices.
Data Collection Method:
Literature review and analysis of existing technical documentation.
Analysis Method:
Descriptive analysis and comparison of different repair techniques.
Research Subjects and Scope:
The scope is limited to the repair of high-pressure die casting molds, specifically those made of high-alloyed tool steels like H13.
6. Main Research Results:
Key Research Results:
- The most common mold repair method is Tungsten Inert Gas (TIG) welding, due to the operator's control over the process.
- Other repair methods include manual metal arc welding, laser welding, electro-spark deposition (ESD), and metallization.
- Proper preparation of the welding groove is critical for weld quality.
- Laser welding is show good result.
- Electro-spark deposition (ESD) offer good wear resistence.
Analysis of presented data:
- Table 1: Presents the chemical composition of "W300" (H11) tool steel, a typical mold material. The table lists the percentage by weight of key elements: C (0.38%), Si (1.1%), Mn (0.4%), Cr (5%), Mo (1.3%), and V (0.4%).
- Figure 1: Illustrates the heat treatment process for tool steel. The diagram shows temperature changes over time, including hardening, stress relief, and tempering stages.
- Figure 2: Depicts thermal fatigue cracking on the surface of H11 steel. It visually demonstrates the damage caused by repeated heating and cooling cycles.
- Figure 3: show Example of mould repair by TIG welding.
- Figure 4. show Repair of welding undercuts by LBW.
- Figure 5. show Schematic of ESD process and equipment.
![Figure 1. Heat treatment, [8]](https://castman.co.kr/wp-content/uploads/image-1516-png.webp)
![Figure 2. Thermal fatigue on the surface of H11 steel, [4]](https://castman.co.kr/wp-content/uploads/image-1517-png.webp)
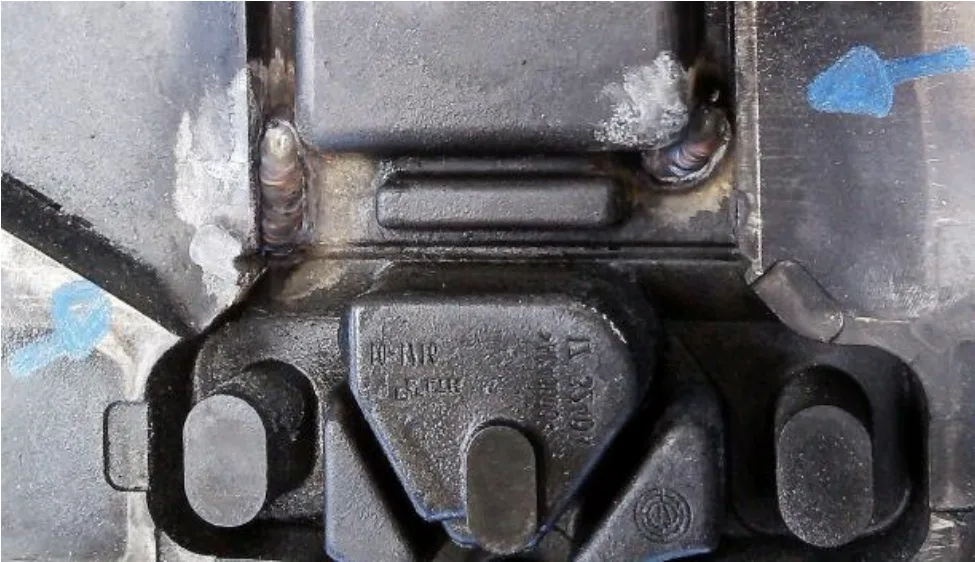
![Figure 4. Repair of undercuts, [24]](https://castman.co.kr/wp-content/uploads/image-1518-png.webp)
![Figure 5. Electro-spark deposition (ESD), [29]](https://castman.co.kr/wp-content/uploads/image-1519-png.webp)
Figure Name List:
- Figure 1. Heat treatment, [8]
- Figure 2. Thermal fatigue on the surface of H11 steel, [4]
- Figure 3. Mould surface repaired by TIG welding
- Figure 4. Repair of undercuts, [24]
- Figure 5. Electro-spark deposition (ESD), [29]
7. Conclusion:
Summary of Key Findings:
HPDC mold repair is essential due to wear, primarily from thermal fatigue. TIG welding is the dominant repair method, but laser welding and ESD offer promising results. Correct surface preparation and controlled welding parameters are crucial for successful repairs.
Academic Significance of the Study:
This review consolidates information on HPDC mold repair, providing a valuable resource for understanding current practices and the challenges involved.
Practical Implications:
The paper highlights the importance of mold repair for cost savings in the HPDC industry. It emphasizes the need for skilled welders and appropriate techniques to maximize mold lifespan.
Limitations of the Study and Areas for Future Research:
As a review, the paper relies on existing research. Further investigation into specific aspects of newer techniques like ESD and laser welding, including long-term performance comparisons, would be beneficial.
8. References:
- [1] Albert Handtmann Metallgusswerk GmbH & Co. KG: High-pressure die casting, www.handtmann.de/en/light-metal-casting/technologies/high-pressure-die-casting/, april 2017.
- [2] C. Mitterer, F. Holler, F. Ustel, D. Heim: Application of hard coatings in aluminium die casting - soldering, erosion and thermal fatigue behaviour, Surface and Coatings Technology 125, 233–239, 2000.
- [3] A. Persson: On Tool Failure in Die Casting, ACTA Universitatis Upsalinensis, Uppsala 2003.
- [4] Z. Dadić, D. Živković, N. Čatipović: Surface wear of steel X38CrMoV5-1 in conditions of die casting, MTSM 2016, Split, 41-45, 2016.
- [5] International Zinc Association: Tooling, http://zinc-diecasting.ionainteractive.com/db-en/HTML/9-3.php, july 2016.
- [6] D. Matiskova, Š. Gašpar, L. Mura: Thermal Factors of Die Casting and Their Impact on the Service Life of Molds and the Quality of Castings, Acta Polytechnica Hungarica Vol. 10, No. 3, 65-78, 2013.
- [7] R. Molina, P. Amalberto: Mechanical characterization of aluminium alloys for high temperature applications Part1: Al-SiCu alloys, Metallurgical Science and Technology, 29(2011)1.
- [8] Böhler: „W300", http://www.bohleredelstahl.com/english/files/W300DE.pdf, april 2014.
- [9] R. Deželić: "Metali 2", Fakultet elektrotehnike strojarstva i brodogradnje, Split, 1987.
- [10] Uddeholm: "Heat treatment of tool steel", http://www.uddeholm.com/files/heattreatment-english.pdf, 2012.
- [11] Assab Singapore: „Assab 8407 supreme", http://www.assab-singapore.com/media/ASSAB_8407_Supreme.pdf, july 2016.
- [12] T. Muhić, J. Tušek, M. Pleterski, D. Bombač: "Problems in repair-welding of duplex-treated tool steels", Metalurgija 48, 2009.
- [13] P.C. Sharma: "A textbook of production technology", S. Chand & Co. Ltd, 2012.
- [14] E. J. Vinarcik: "High integrity die casting processes". John Wiley & Sons, Hoboken, New Jersey, 2003.
- [15] A.H. Mohammed: "Experimental Simulation of Reduction of Erosion Damage in Dies Used in Aluminium Casting", Doktorski rad, 2013.
- [16] J. Tušek, B. Taljat, D. Klobčar: "How to extend the life of die-casting tools", Metalurgija 46, 2007.
- [17] D. Klobčar, A. Muhić, M. Pletenski, J. Tušek: "Thermo-mechanical cracking of a new and laser repair welded die casting die", Metalurgija 51, 2012.
- [18] Unitor®: "Maritime Welding Handbook", https://www.wilhelmsen.com/globalassets/marine-products/welding/documents/wilhelmsen-ships-service---unitor-welding-handbook.pdf, april 2017.
- [19] Uddeholm: "Welding of tool steel", www.uddeholm.com, april 2017.
- [20] S. Thompson: "Handbook of mold, tool and die repair welding", William Andrew Publishing, USA, 1999.
- [21] FSH Welding Group: "Tool and Die Welding", http://www.fsh-welding.com/en/welding-en.htm, preuzeto s interneta 15.4.2017.
- [22] Ellwood Specialty Steel Co, New Castle: "Standard Welding Procedure for ExELL H-13 SMDQ – N, ExEll Tuf Die and ExEll Hot Die", http://ess.elwd.com/wp-content/uploads/2015/04/ESS-H-Steel-Welding-Spec.pdf, preuzeto s interneta 18.4.2017.
- [23] A. Skumavc, J. Tusšek, A. Nagode, Ladislav Kosec: Tungsten heavy alloy as a filler metal for repair, Int. J. Mater. Res. (formerly Z. Metallkd.) 104 (2013) 11.
- [24] J. Tušek, A. Skumavc, K. Pompe, D. Klobčar: "Refurbishment of damaged tools using the combination of GTAW and laser beam welding", Metalurgija 53, 2014.
- [25] A. Skumavc, J. Tušek, M.Mulc, D. Klobčar: "Problems in laser repair welding of polished surfaces", Metalurgija 53, 2014.
- [26] J. Tušek, L. Kosec, A. Lešnjak, T. Muhič: Electrospark deposition for die repair, Metalurgija 51(1), 17-20,2 012.
- [27] R. N. Johnson, G. L. Sheldon: Advances in the electrospark deposition coating process, Journal of Vacuum Science & Technology A 4, 2740 (1986).
- [28] H. Feng, L. Tian, Y. Ma, B. Tang: Tribological Behavior of Molybdenum Alloying layer on H13 Steel by Electrospark Deposition Technique, Advanced Materials Research Vols 97-101 (2010) 1356-1359.
- [29] D.W. Heard, M. Brochu: Development of a nanostructure microstructure in the Al-Ni system using the electrospark deposition process, Journal of Materials Processing Technology, 892-898, 210 (2010).
9. Copyright:
- This material is "Zvonimir DADIĆ, Dražen ŽIVKOVIĆ, Nikša ČATIPOVIĆ, Josip BILIĆ"'s paper: Based on "High pressure die casting mould repair technologies".
- Paper Source: [There is no DOI URL, ResearchGate URL : https://www.researchgate.net/publication/320036239]
This material was created to introduce the above paper, and unauthorized use for commercial purposes is prohibited.
Copyright © 2025 CASTMAN. All rights reserved.