This article introduces the paper "Front Aluminum Subframe of High Level Vacuum Die-casting," published in Transactions of KSAE, Vol. 20, No. 4, pp.52-59 (2012). This paper details the development of an aluminum subframe using high level vacuum die casting to reduce weight and enhance performance compared to traditional steel subframes.
1. Overview:
- Title: Front Aluminum Subframe of High Level Vacuum Die-casting
- Author: Younggun Cho, Taeseong Lim, Sang-gil Jang, Cheol-hwan Cho
- Publication Year: 2012
- Publishing Journal/Academic Society: Transactions of the Korean Society of Automotive Engineers (KSAE)
- Keywords: High level vacuum die-casting (고진공 다이캐스팅), Aluminum subframe (알루미늄 서브프레임), Rib (리브), Sound level (음향 수준), Roll rod (롤 로드)

2. Research Background:
- Social/Academic Context of the Research Topic:
- Increasing demand for improved fuel efficiency through vehicle lightweighting due to rising oil prices and stricter carbon dioxide emission regulations.
- Growing importance of lightweight materials in automotive design.
- Aluminum is gaining prominence as a lightweight material for structural parts like suspension systems, beyond engine components, due to its high specific strength and versatile forming processes.
- Aluminum subframes are becoming increasingly common, especially in large vehicles globally.
- Limitations of Existing Research:
- Traditional subframes are typically manufactured using stamped steel, which is heavier.
- Conventional die casting of aluminum, while cost-effective, suffers from high gas content in products (10~30cc/100gAl), leading to lower mechanical properties and limitations in heat treatment and welding, making it unsuitable for high-strength structural components.
- Necessity of the Research:
- Need to develop lightweight aluminum subframes to meet fuel efficiency demands.
- Necessity to overcome the limitations of conventional die casting by employing high level vacuum die-casting to minimize gas content and improve material properties for structural applications.
- Aim to reduce weight compared to steel subframes while managing material cost increases through process optimization.
3. Research Purpose and Research Questions:
- Research Purpose:
- To develop an aluminum front subframe using high level vacuum die-casting technology.
- To achieve weight reduction compared to steel subframes while maintaining or improving structural performance.
- To optimize the design and manufacturing process to minimize cost increases associated with material changes.
- Key Research Questions:
- Can high level vacuum die-casting effectively produce aluminum subframes with reduced gas content and improved material properties?
- How much weight reduction can be achieved by replacing a steel subframe with an aluminum subframe manufactured using high level vacuum die-casting?
- What is the structural performance of the developed aluminum subframe in terms of mounting stiffness, noise and vibration (NVH), and endurance compared to steel subframes?
- How does the design of ribs in the aluminum subframe affect its NVH performance and structural integrity?
- Research Hypotheses:
- High level vacuum die-casting will result in an aluminum subframe with lower gas content and superior mechanical properties compared to conventional die-casting methods.
- The aluminum subframe will achieve a significant weight reduction compared to the steel subframe.
- Optimized rib design in the aluminum subframe will enhance stiffness and NVH performance, making it comparable to or better than steel subframes.
4. Research Methodology:
- Research Design:
- Development and comparative study.
- Design and manufacturing of an aluminum subframe using high level vacuum die-casting.
- Comparison of the aluminum subframe's properties and performance against a steel subframe.
- Data Collection Method:
- Material Property Testing: Mechanical property tests (tensile strength, yield strength, elongation) on aluminum alloy produced by high level vacuum die-casting. Chemical composition analysis of the aluminum alloy.
- X-Ray Inspection: X-ray testing to evaluate porosity and casting quality of the manufactured aluminum subframe.
- NVH Evaluation: Modal analysis and booming tests to assess vibration and noise characteristics. Sound level measurements in a vehicle equipped with the aluminum subframe.
- Durability and Strength Testing: Durability tests under various load conditions (for and backward, lateral, up and down). Strength tests to evaluate structural integrity under static loads.
- Stiffness Analysis: Measurement of roll rod mounting stiffness.
- Analysis Method:
- Comparative Analysis: Comparing material properties, weight, stiffness, NVH performance, and durability of the aluminum subframe with the steel subframe.
- Finite Element Analysis (FEA): Using HyperWorks Pre and Radioss Solver for modal analysis to simulate NVH performance with different rib designs.
- Statistical Analysis: Averaging material property test results and analyzing X-ray inspection grades.
- Research Subjects and Scope:
- Material: Aluminum alloy (Silafont 36) produced by high level vacuum die-casting and stamped steel for subframe.
- Component: Front subframe for automotive application.
- Manufacturing Process: High level vacuum die-casting for aluminum subframe.
- Performance Evaluation: Mounting stiffness, NVH (noise, vibration), endurance, and strength.
5. Main Research Results:
- Key Research Results:
- Weight Reduction: The aluminum subframe achieved a weight reduction of 4kg compared to the steel subframe.
- Material Properties: High level vacuum die-casting produced aluminum with mechanical properties comparable to high-grade aluminum alloys. Table 1 shows the mechanical properties of Silafont 36 aluminum alloy compared to steel:
- Silafont 36: Elastic modulus 71 GPa, Elongation 4.1%, Y.S 162 MPa, U.T.S 247 MPa.
- Steel: Elastic modulus 206 GPa, Elongation 32%, Y.S 343 MPa, U.T.S 465 MPa.
- NVH Performance Improvement: NVH evaluation showed a reduction in sound level by 8dB at 140Hz (around 4,200rpm engine speed) with the aluminum subframe. Modal analysis indicated increased frequencies for key modes in the aluminum subframe compared to steel, except for the torsion mode.
- Stiffness: Roll rod mounting stiffness was enhanced in the aluminum subframe, particularly in the fore-aft direction (increased from 6,920 kgf/mm in steel to 8,405 kgf/mm in aluminum). Vertical stiffness of the roll rod mounting was measured at 1,108 kgf/mm for the aluminum subframe.
- Durability and Strength: The aluminum subframe successfully passed durability tests under various load conditions and met strength requirements without failure (fracture or buckling).
- Casting Quality: X-ray inspection revealed porosity levels generally below grade 3 (except for some thicker sections), indicating good casting quality, comparable to or better than international standards (porosity level around 2cc/100g, target < 4cc/100g, and achieved level ~2cc/100g).
- Statistical/Qualitative Analysis Results:
- Table 3 shows the stiffness of roll rod mounting for different rib designs (Rib A, Rib B, Rib C). Rib C demonstrated the highest vertical stiffness (Z direction) at 1,108 kgf/mm.
- Table 4 presents global mode frequencies for steel and aluminum subframes. Aluminum subframe showed higher frequencies for bending and lateral bending modes compared to steel.
- Table 6 and Fig. 8 show X-ray inspection results, indicating acceptable casting quality with porosity mostly within grade 3.
- Table 7 summarizes measured material properties of the cast aluminum alloy, showing average Yield Strength of 235 MPa, Ultimate Tensile Strength of 265 MPa, and Elongation of 5.6%.
- Fig. 9 shows modal testing results comparing frequency response functions of aluminum and steel subframes.
- Fig. 10 shows booming test results at the front seat, indicating NVH improvement with the aluminum subframe.
- Fig. 12 presents strength test results, confirming the structural integrity of the aluminum subframe.
- Data Interpretation:
- The use of high level vacuum die-casting enabled the production of a lightweight aluminum subframe with enhanced structural and NVH performance.
- Optimized rib design (Rib C) contributed to improved stiffness, particularly in the vertical direction.
- The aluminum subframe achieved significant weight reduction and NVH improvement while meeting durability and strength requirements.
- Casting quality achieved through high level vacuum die-casting is comparable to high standards for automotive components.
- Figure Name List:
- Fig. 1 High level vacuum die-casting
- Fig. 2 Subframe shape (top view)
- Fig. 3 Subframe shap (bottom view)
- Fig. 4 Results of normal mode analysis
- Fig. 5 Results of strength analysis
- Fig. 6 Mold structure of high level vacuum die-casting
- Fig. 7 Phography of manufactured subframe
- Fig. 8 X-ray testing
- Fig. 9 Modal testing of aluminium and steel subframe
- Fig. 10 Booming testing at front seat
- Fig. 11 Testing facilities
- Fig. 12 Strength test results

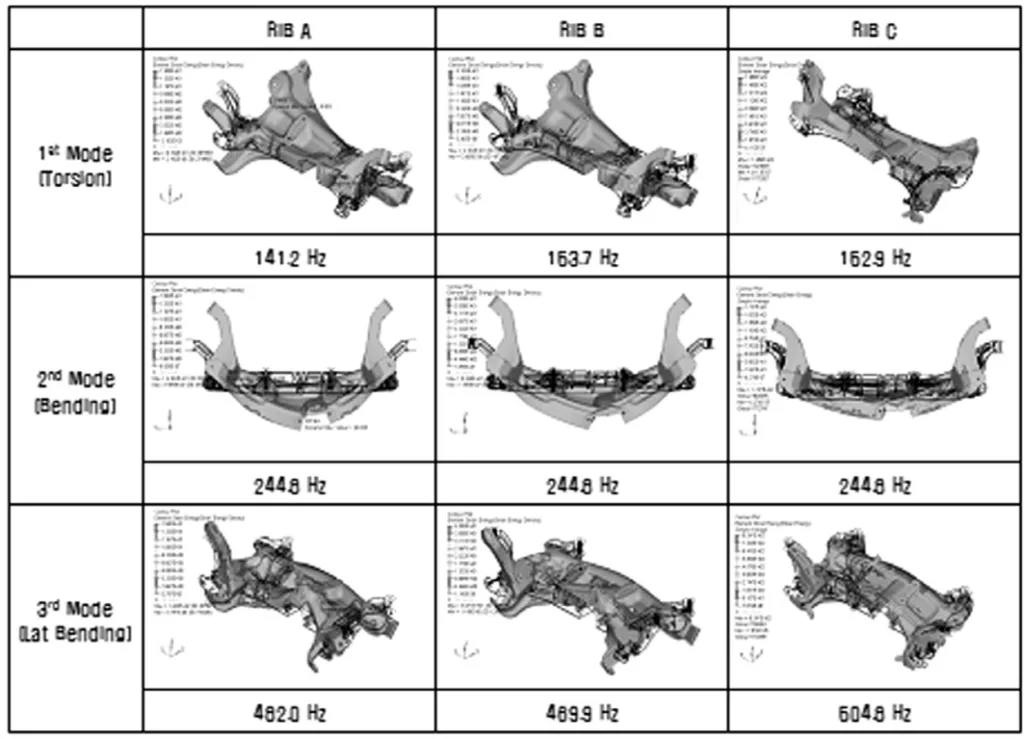
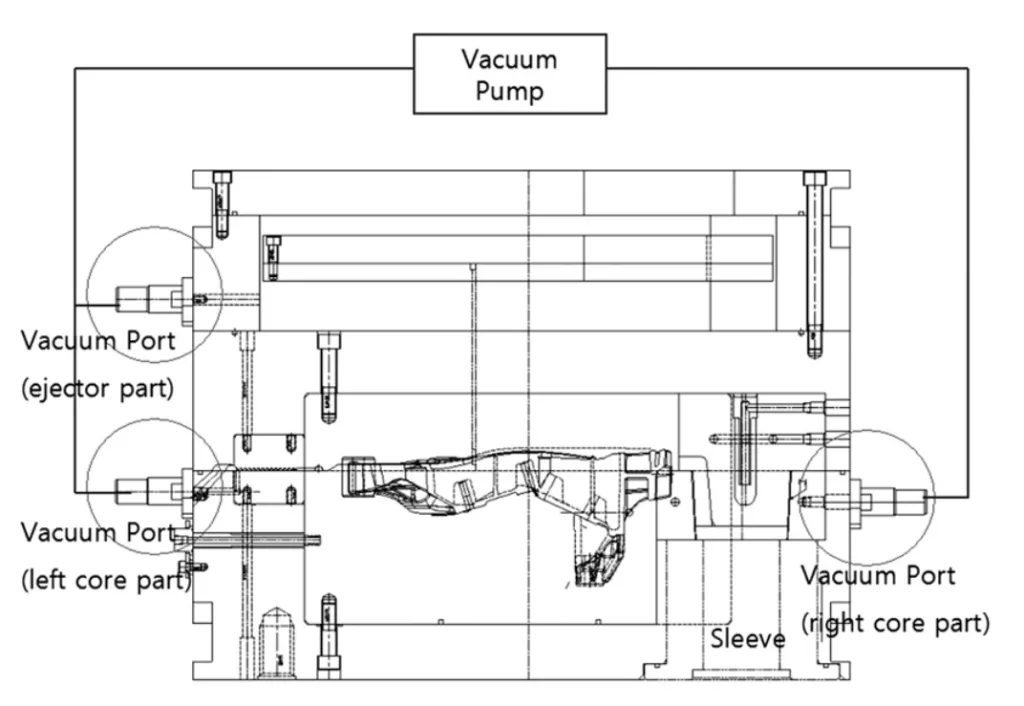
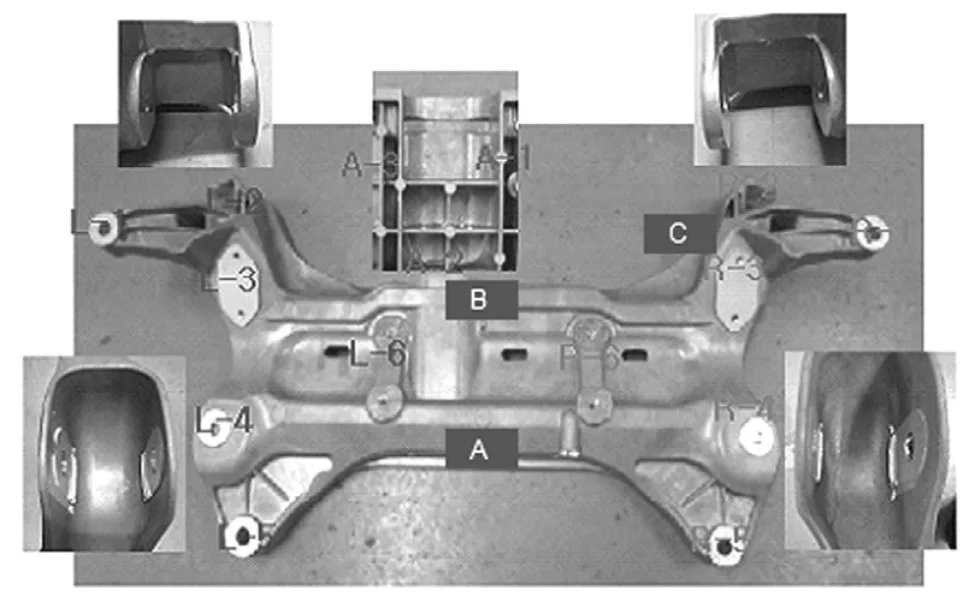
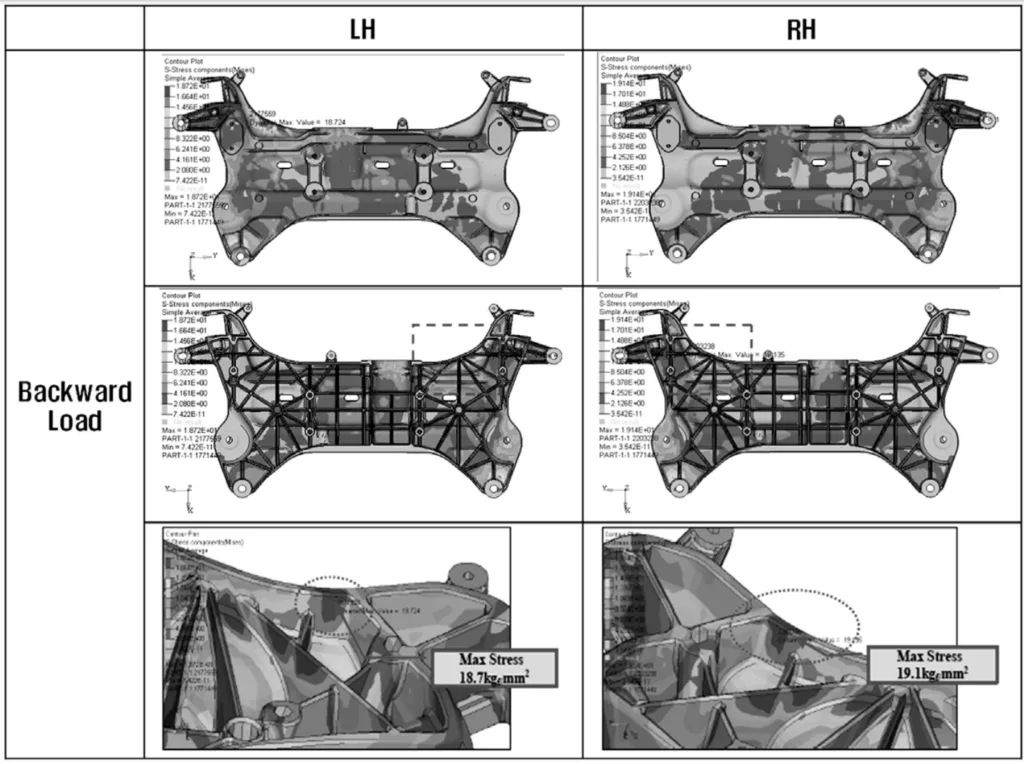
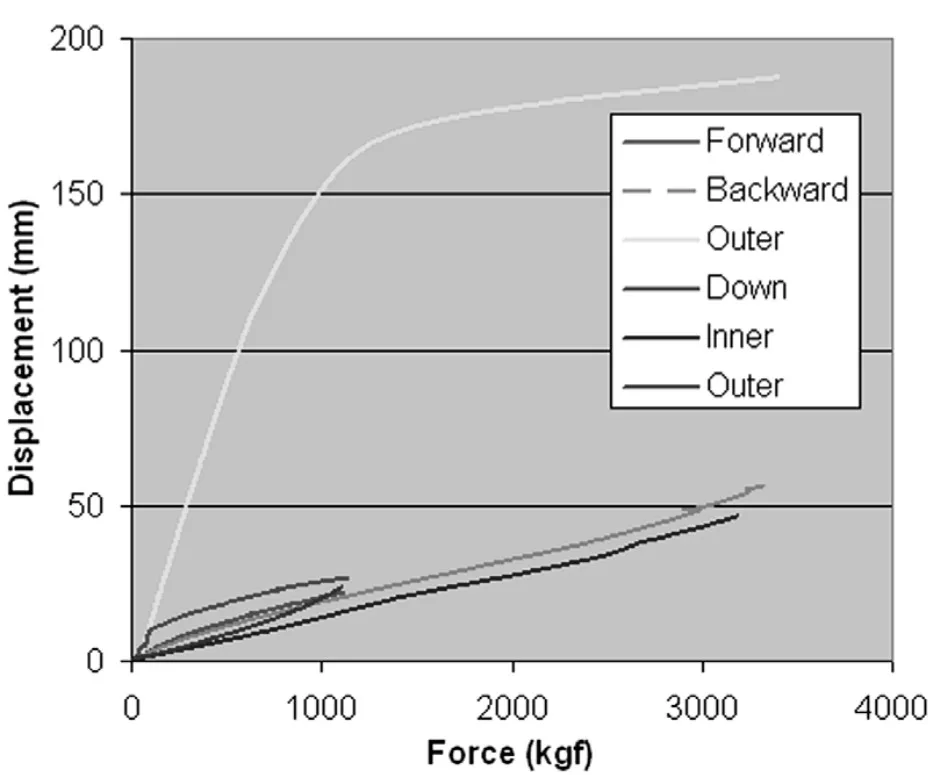
6. Conclusion and Discussion:
- Summary of Main Results:
- Successfully developed an aluminum front subframe using high level vacuum die-casting for the first time in Korea.
- Achieved a 4kg weight reduction compared to the steel subframe.
- Optimized rib structure (honeycomb-like) to enhance vertical stiffness of the roll rod mounting, reaching over 1,108kgf/mm.
- Demonstrated NVH performance improvement, with an 8dB reduction in sound level at 140Hz.
- Confirmed that the aluminum subframe meets durability and strength standards, comparable to or exceeding steel subframe performance.
- Achieved casting quality with porosity levels comparable to leading international automotive standards.
- Academic Significance of the Research:
- Demonstrates the successful application of high level vacuum die-casting for manufacturing large structural automotive components like subframes.
- Provides valuable data on the material properties, structural performance, and NVH characteristics of aluminum subframes produced by this advanced casting method.
- Contributes to the body of knowledge on lightweighting strategies in automotive engineering.
- Practical Implications:
- Offers a viable solution for automotive manufacturers to reduce vehicle weight and improve fuel efficiency through aluminum subframe implementation.
- High level vacuum die-casting can be adopted for mass production of complex aluminum structural parts with improved quality and performance.
- The developed aluminum subframe design and manufacturing process can be directly applied to vehicle production.
- Limitations of the Research:
- The study focused on a specific front subframe design and aluminum alloy (Silafont 36).
- The long-term durability and performance under real-world driving conditions were not extensively evaluated beyond the laboratory tests.
- Cost-effectiveness of mass production using high level vacuum die-casting compared to steel subframe manufacturing was not explicitly analyzed in detail within this paper.
7. Future Follow-up Research:
- Directions for Follow-up Research:
- Further optimization of the aluminum subframe design and rib structure for enhanced performance and weight reduction.
- Exploration of other aluminum alloys suitable for high level vacuum die-casting with potentially improved mechanical properties or cost-effectiveness.
- Comprehensive long-term durability testing and real-world vehicle performance evaluation of the aluminum subframe.
- Detailed cost analysis and process optimization for mass production of aluminum subframes using high level vacuum die-casting.
- Investigation of joining technologies for aluminum subframes in vehicle assembly.
- Areas Requiring Further Exploration:
- Refinement of casting parameters to further minimize porosity and improve casting quality consistency.
- Detailed analysis of fatigue performance and crashworthiness of the aluminum subframe.
- Environmental impact assessment of aluminum subframe production and lifecycle compared to steel subframes.
8. References:
- 1) D. Triantos and M. Michaels, "Design and Fabrication of an Aluminum Engine Crandle for a General Motors Vehicle," SAE 1999-01-0659, 1999.
- 2) A. Mikuni, O. Itagaki and M. Suzuki, “Development of Aluminum Vacuum Die CastSub-frame," JSAE Autumn Conference, JSAE, 20045658, 2004.
- 3) T. Gakamoto, K. Kira and H. Kambe, “Development of Automotive Suspension Part by High Vacuum Die Casting," Journal of Japan Foundry Engineering Society, Vol.76, No.4, pp.283-288, 2004.
- 4) M. Tashiro, K. Kudoh, Y. Konno and K. Takagi, "Development of Nissan Innovative Casting System for Aluminum Casting Suspension Parts," Nissan Technical Review, No.49, 2001.
- 5) A. Mikuni, O. Itagaki and M. Suzuki, “Development of Aluminum Vacuum Die Cast Sub-frame," JSAE Annual Congress, JSAE, No.81-04, 2004.
- 6) G.-M. Yoon, D.-H. Kang, Y.-J. Ko and J.-D. Lim, "Application of High Level Vacuum Die-casting for the Automotive Parts,” Annual Conference Proceedings, KSAE, pp.1540-1546, 2009.
- 7) S.-Y. Park, D.-C. Park, K.-S. Yoon and M.-S. Lee, "A Study of Front Subframe System Optimization for Improving Vehicle NVH Performance," SAE 2009-01-2097, 2009.
- 8) M.-S. Kim, T.-S. Li, K.-M. Yoon, Y.-J. Ko, J.-M. Kim and K.-H. Kwak, “Development of Cast-forged Knuckle Using High Strength Aluminum Alloy,” Spring Conference Proceedings, KSAE, pp.1048-1055, 2010.
9. Copyright:
- This material is Younggun Cho, Taeseong Lim, Sang-gil Jang, Cheol-hwan Cho's paper: Based on Front Aluminum Subframe of High Level Vacuum Die-casting.
- Paper Source: DOI http://dx.doi.org/10.7467/KSAE.2012.20.4.052
This material was summarized based on the above paper, and unauthorized use for commercial purposes is prohibited.
Copyright © 2025 CASTMAN. All rights reserved.