This article introduces the paper ['Fluidity of Pure Aluminum in a Narrow Channel Die Gap during Die Casting'] presented at the ['Metals, MDPI']
1. Overview:
- Title: Fluidity of Pure Aluminum in a Narrow Channel Die Gap during Die Casting
- Author: Toshio Haga and Hiroshi Fuse
- Publication Year: 2024
- Publishing Journal/Academic Society: Metals, MDPI
- Keywords: pure aluminum; die casting; fluidity; narrow die gap; die temperature; plunger speed

2. Research Background:
Background of the Research Topic:
The increasing demand for lightweight heat sinks with excellent heat dissipation has driven interest in pure aluminum due to its superior thermal conductivity compared to conventional die casting alloys like JIS ADC12 [1]. Producing thin-finned heat sinks necessitates understanding the fluidity of pure aluminum in narrow die gaps during the die casting process. However, the influence of casting parameters on the fluidity of pure aluminum in such conditions remains inadequately explored.
Status of Existing Research:
Extensive research has been conducted on factors influencing the fluidity of aluminum alloys. These factors encompass solidification mode [2-7], metal composition [8-18], melt superheating [5,12-14,19-23], viscosity [3,24-26], surface tension [27-29], mold materials [30-32], mold temperature [33-40], plunger speed [13,34-38,40,41], mold gap [13,40,41], and mold vibration [42,43]. Generally, fluidity in aluminum alloys is known to improve with increasing die temperature, die gap, and plunger speed. However, these investigations primarily focused on aluminum alloys and wider die gaps. The applicability of these findings to pure aluminum within narrow die gaps in die casting remains unclear.
Necessity of the Research:
It is crucial to elucidate the specific effects of casting conditions on the fluidity of pure aluminum (99.9%Al and 99.7%Al) when die casting in narrow 0.5 mm die gaps. Specifically, the roles of plunger speed and die temperature, which are pivotal casting parameters affecting fluidity, require detailed investigation. Furthermore, it is essential to determine if the established correlation between aluminum purity and flow length [2–6] is maintained in narrow die gap scenarios and to assess the impact of iron (Fe) as an impurity on the flow length of pure aluminum under these conditions.
3. Research Purpose and Research Questions:
Research Purpose:
The primary research purpose is to elucidate the effect of die casting conditions on the fluidity of 99.9%Al and 99.7%Al when cast into a narrow 0.5 mm die gap. This study aims to provide a deeper understanding of the flow behavior of pure aluminum in constrained geometries during die casting.
Key Research:
This research focuses on the following key areas:
- Investigating the effects of die temperature and plunger speed on the flow length of pure aluminum in a 0.5 mm narrow die gap.
- Comparing the flow length characteristics of pure aluminum with those of ADC12 alloy under identical narrow die gap conditions.
- Examining the influence of iron (Fe) content as an impurity on the flow length of pure aluminum in a narrow die gap.
Research Hypotheses:
This study challenges the conventional hypothesis that fluidity consistently increases with die temperature and plunger speed in die casting. It explores an alternative hypothesis that in narrow die gaps, particularly for pure aluminum, the relationship between fluidity and these parameters may deviate from conventional expectations due to factors such as solidified layer behavior.
4. Research Methodology
Research Design:
The research employed an experimental design utilizing a 500 kN cold chamber die casting machine (HC 50F, Hishinuma Machinery, Ranzan, Japan). A spiral die, schematically illustrated in Figure 1, with a channel width of 7 mm and channel gaps of 0.5 mm and 1.0 mm was used for fluidity tests.
Data Collection Method:
Flow length measurements were obtained from cast spiral specimens. Twelve test pieces were cast under each condition, and the average flow length was recorded. Chemical compositions of the alloys (99.9%Al, 99.7%Al, ADC12, and Al-X%Fe) were determined using optical emission spectroscopy (PDA-500, SIMADZU, Kyoto, Japan). Optical microscopy (ECLIPSE LV150, Nikon, Tokyo, Japan) was used to capture images of the die surface and cast specimens.
Analysis Method:
The collected flow length data were analyzed to assess the effects of die temperature (30 °C and 150 °C) and plunger speed (0.2, 0.4, 0.6, and 0.8 m/s) on the fluidity of pure aluminum and other alloys in both 0.5 mm and 1.0 mm die gaps. The results were interpreted based on the proposed mechanism of peeling and re-melting of the solidified layer at the die surface.
Research Subjects and Scope:
The study investigated the fluidity of commercially pure aluminum (99.9%Al and 99.7%Al), aluminum alloy ADC12, and a series of Al-X%Fe alloys (X = 0.3, 0.5, 0.7, 0.9 and 1.1%). The scope was limited to die casting experiments using a spiral die with channel gaps of 0.5 mm and 1.0 mm, die temperatures of 30 °C and 150 °C, and plunger speeds ranging from 0.2 to 0.8 m/s.
5. Main Research Results:
Key Research Results:
- Narrow Die Gap (0.5 mm):
- Counter to conventional expectations, the fluidity of 99.9%Al and 99.7%Al was superior at a die temperature of 30 °C and a plunger speed of 0.2 m/s compared to conditions of 150 °C and 0.8 m/s. Similar trends were observed for ADC12 and Al-X%Fe alloys.
- At a die temperature of 30 °C, the fluidity of 99.9%Al, 99.7%Al, ADC12, and Al-X%Fe decreased as plunger speed increased.
- Wider Die Gap (1.0 mm):
- Flow length increased with increasing plunger speed, aligning with conventional die casting principles.
- At a die temperature of 30 °C, the flow length of 99.7%Al was less than that of 99.9%Al.
- At a die temperature of 150 °C, flow lengths for 99.7%Al and 99.9%Al were comparable.
- Effect of Fe Content (0.5 mm gap):
- At 30 °C and 0.2 m/s, Al-0.5%Fe and Al-0.7%Fe exhibited longer flow lengths than 99.9%Al and 99.7%Al.
- For other conditions, the flow length of Al-X%Fe alloys tended to decrease with increasing Fe content, consistent with conventional understanding.
Data Interpretation:
The unexpected enhancement of fluidity at lower die temperatures (30 °C) and plunger speeds (0.2 m/s) in narrow die gaps is attributed to the phenomenon of solidified layer peeling. Under these specific conditions, reduced contact between the molten metal and the die surface may lead to diminished heat transfer. This, in turn, can decrease the solidification rate, prolonging the solidification process and resulting in increased flow length. Conversely, at higher die temperatures and plunger speeds, improved adhesion and heat transfer dominate, leading to conventional fluidity behavior.
Figure Name List:
- Figure 1. Schematic illustration of spiral die. Units: mm. (a) Shape, (b) dimensions.
- Figure 2. Schematic diagrams of casters used in this study. (a) Melt spinning single roll caster, (b) melt drag single roll caster, (c) vertical type high-speed twin roll caster.
- Figure 3. Effects of plunger speed and die temperature on flow length for 99.9%Al and 99.7%Al. Die gap: 0.5 mm.
- Figure 4. Effects of plunger speed and die temperature on flow length for 99.7%Al and 99.9%Al. Die gap: 1 mm.
- Figure 5. Effects of plunger speed, die temperature, and die gap on flow length for JIS ADC12. (a) Die gap: 0.5 mm; die temperature: 30 and 150 °C. (b) Die gap: 1 mm; die temperature: 30 and 150 °C.
- Figure 6. Effects of Fe content, plunger speed, and die temperature on flow length for pure aluminum and Al-Fe alloys listed in Table 1. Die gap is 0.5 mm.
- Figure 7. Effect of die temperature and plunger speed on surface conditions of spiral die-cast specimens of 99.7%Al. (a) Surface of spiral die, (b) surfaces of spiral die-cast specimens.
- Figure 8. Effect of roll temperature on adhesion length for 99.9%Al to roll. Roll speed: 24 m/s.
- Figure 9. Effect of slit gap on adhesion length for 99.7%Al foil to roll for same foil thickness in melt-spinning single-roll caster. Roll speed: 55 m/s, foil thickness: 32 µm.
- Figure 10. Effects of roll temperature and molten metal speed on adhesion length to roll during melt spinning.
- Figure 11. Schematic diagram showing the effects of die temperature and plunger speed on solidification and flow length for molten metal. (a) Die temperature: 30 °C, plunger speed: 0.2 m/s. (b) Die temperature: 150 °C; plunger speed: 0.8 m/s.
- Figure 12. Schematic diagram showing effects of die temperature and plunger speed on solidified layer thickness with 1 mm die gap. (a) Die temperature: 30 °C, plunger speed: 0.2 m/s. (b) Die temperature: 150 °C, plunger speed: 0.8 m/s.
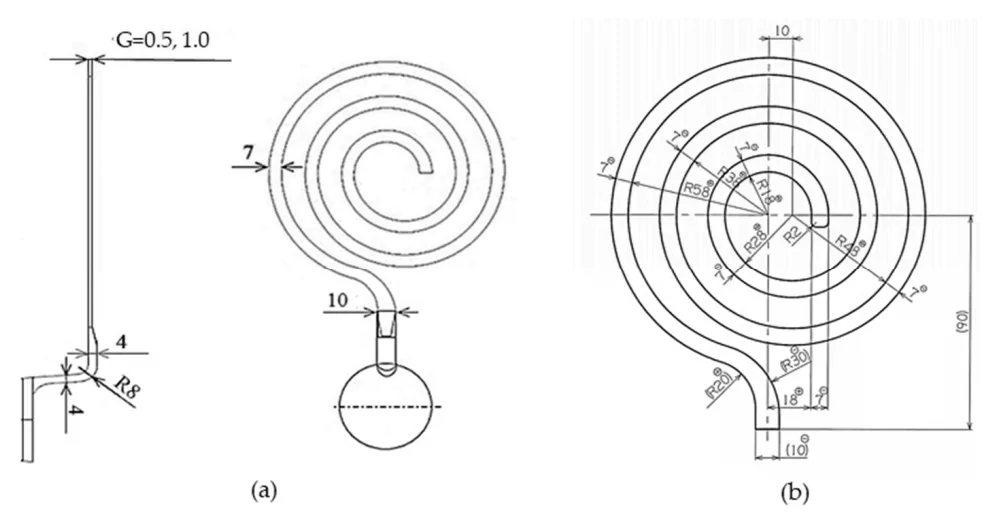
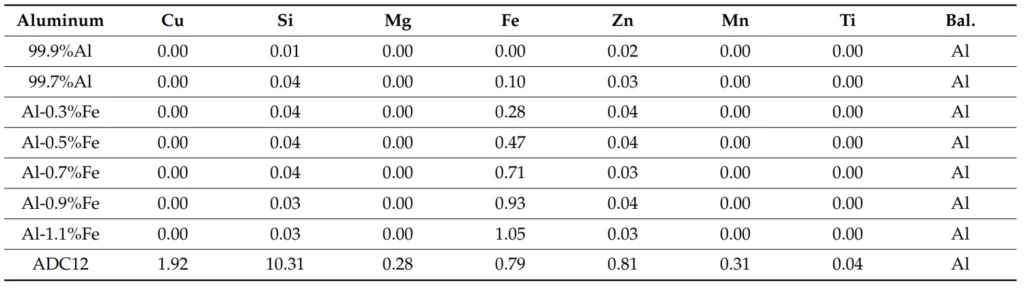
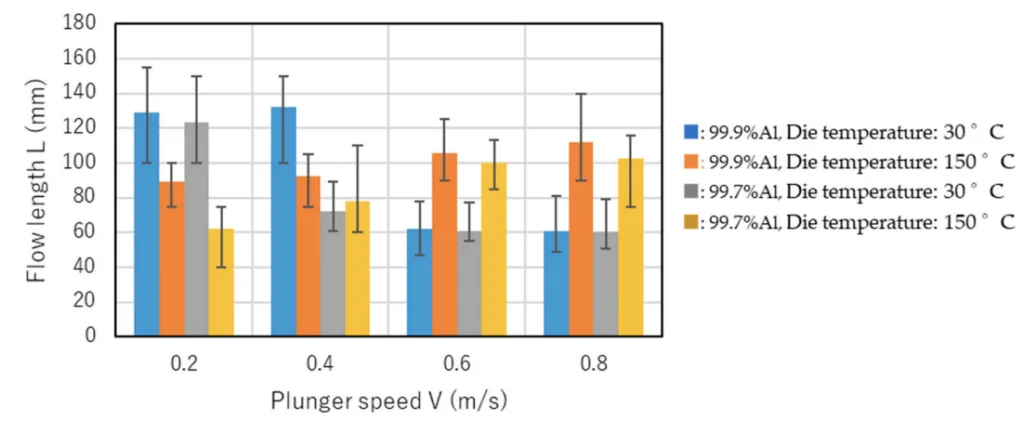
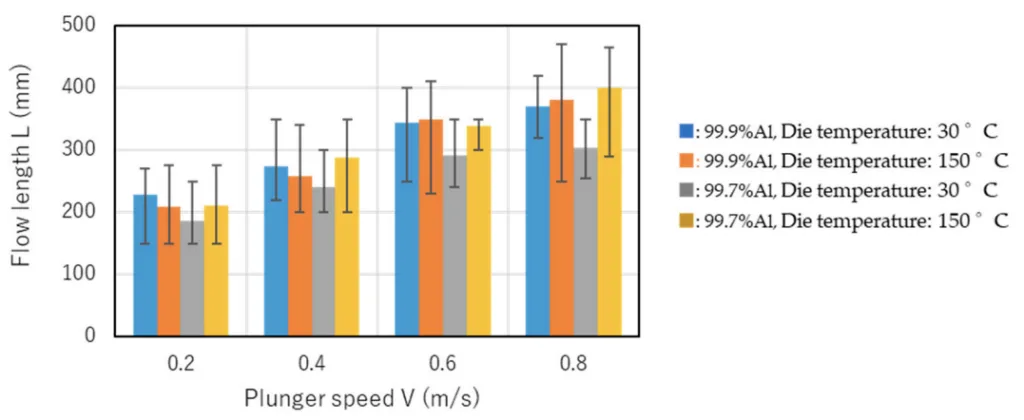

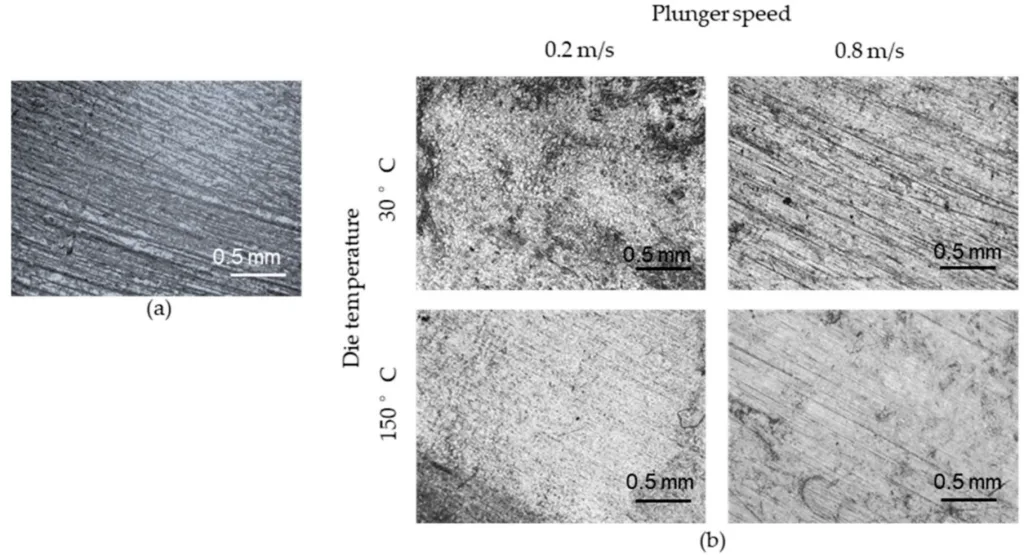
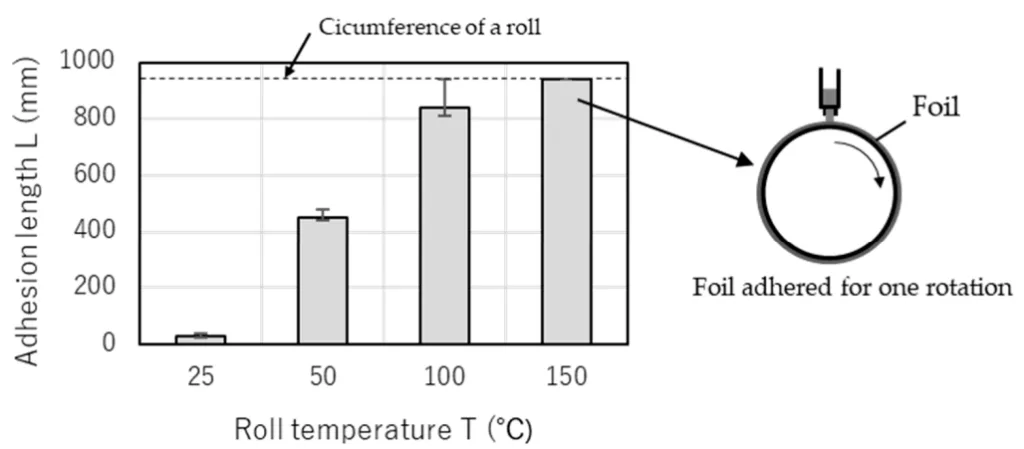
6. Conclusion:
Summary of Main Results:
This study demonstrated that in die casting pure aluminum (99.9%Al and 99.7%Al) and ADC12 into narrow 0.5 mm die gaps, lower die temperatures (30 °C) and slower plunger speeds (0.2 m/s) can paradoxically lead to enhanced fluidity, contrary to conventional die casting expectations. This phenomenon is attributed to the peeling of the solidified layer from the die surface, which reduces heat transfer and delays solidification.
Academic Significance of the Research:
This research challenges the traditional understanding of fluidity in die casting, particularly for pure aluminum in confined geometries. It highlights the significant role of solidified layer peeling as a critical factor influencing fluidity under specific casting conditions, offering a new perspective on metal flow behavior in narrow die gaps.
Practical Implications:
The findings suggest that for die casting thin-walled components from pure aluminum, employing lower die temperatures and plunger speeds might be advantageous to enhance fluidity in narrow sections. This insight is valuable for optimizing die casting processes for intricate pure aluminum parts, such as heat sinks with thin fins.
Limitations of the Research
The study is primarily focused on pure aluminum and ADC12 alloys, and the conclusions are drawn from experiments using a specific spiral die geometry with a 0.5 mm narrow gap. Further research is needed to validate these findings across a broader range of alloys, die designs, and die gap dimensions to generalize the observed phenomena.
7. Future Follow-up Research:
- Directions for Follow-up Research:
Future research should focus on a more detailed investigation of the solidified layer peeling mechanism, including its kinetics and influencing factors. Exploring the effects of other casting parameters, such as injection pressure and gate design, and examining a wider range of alloy compositions on solidified layer peeling and fluidity in narrow die gaps are crucial next steps. - Areas Requiring Further Exploration:
Further exploration should include developing computational models to simulate the peeling and re-melting process of the solidified layer to predict fluidity in narrow die gaps. Optimizing die casting parameters specifically for thin-walled pure aluminum components, considering the solidified layer peeling mechanism, is an area requiring further investigation for practical applications.
8. References:
- [1] JIS H 5032: 2006(E); Aluminum Alloy Die Castings. Japanese Industrial Standards Committee: Tokyo, Japan, 2006.
- [2] Flemings, M.C.; Niyama, E.; Tayor, H.F. Fluidity of Aluminum alloys. An experimental and qualitative evaluation. AFS Trans. 1961, 69, 566-576.
- [3] Kayama, N.; Murai, K.; Kiguchi, S.; Satoh, H. Effect of formation of primary crystals on fluidity and viscosity in nearly stages of solidification. Rep. Cast. Res. Lab. Waseda Univ. 1976, 27, 1-8.
- [4] Dahle, A.K.; BæcKerund, L.; Arnberg, L. Castability of Aluminum foundry alloys. Int. J. Cast Met. Res. 1996, 9, 103-112. [CrossRef]
- [5] Timelli, G.; Bonollo, F. Fluidity of aluminium die castings alloy. Int. J. Cast Met. Res. 2007, 20, 304-311. [CrossRef]
- [6] Hans, E.; Xu, H. Fluidity of alloys under high pressure die casting conditions. Scr. Mater. 2005, 53, 7–10.
- [7] Han, Q.; Zhang, J. Fluidity of alloys under high-pressure die casting conditions: Flow-choking mechanisms. Metall. Mater. Trans. B 2020, 51, 1795-1804. [CrossRef]
- [8] Mollard, F.R.; Flemings, M.C.; Niyama, E.F. Understanding aluminum fluidity: The key to advanced cast products. AFS Trans. 1987, 95, 647-652.
- [9] Sheshadri, M.R.; Ramachandran, A. Casting fluidity and fluidity of aluminium and its alloys. Mod. Cast. 1965, 21, 110–122.
- [10] Gowri, S.; Samuel, F.H. Effect of alloying element on the solidification characteristic and microstructure of Al-Si-Cu-Mg-Fe 380 alloy. Metall. Mater. Trans. A 1994, 25, 437-448. [CrossRef]
- [11] Behera, R.; Chatterjee, D.; Sutradhar, G. Effect of reinforcement particles on the fluidity and solidification behavior of the stir cast aluminum. Am. J. Mater. Sci. 2012, 2, 53–61. [CrossRef]
- [12] Adefuye, O.A. Casting fluidity of commercially pure Al-Si casting alloys. Trans. J. Sci. Technol. 2014, 4, 16–30.
- [13] Erzi, E.; Yüksel, Ç.; Gürsoy, Ő.; Çolak, M.; Dispinar, D. Characterisation of aluminum alloys by octopus fluidity test. J. Polytech. 2024, 27, 21-25. [CrossRef]
- [14] Chen, G.C.; Li, X. Effect of TiC nano-treating on the fluidity and solidification behavior of aluminum alloy 6063. J. Mater. Process. Technol. 2024, 324, 118241. [CrossRef]
- [15] Shah, A.W.; Ha, S.H.; Kim, B.H.; Yoon, Y.O.; Lim, H.K.; Kim, S.K. Effect of Si addition flow behavior in Al-Mg and Al-Mg-Si molten alloys. Metall. Mater. Trans. A 2020, 51, 6670-6678. [CrossRef]
- [16] Mao, G.; Wu, Z.; Liu, S.; Zhong, L.; Gao, W. The fluidity of A357 alloy with scandium (Sc) and zirconium (Zr) addition. J. Mater. Res. Technol. 2020, 9, 13570–13574. [CrossRef]
- [17] Durmuş, M.; Dispinar, D.; Gavgali, M.; Uslu, E.; Çolak, M. Evaluation of Fe content on the fluidity of A356 aluminum alloy by new fluidity index. Int. J. Metalcast. 2024. [CrossRef]
- [18] Guo, T.; Wang, B.; Zhang, Z.; Sun, Q.; Jin, Y.; Ding, W. Effect of micro-scale Er on the microstructure and fluidity of ZL205A alloy. Materials 2019, 12, 1688. [CrossRef]
- [19] Niesse, J.E.; Flemings, M.C.; Taylor, H.F. Applications of Theory in Understanding Fluidity of Metals. AFS Trans. 1959, 67, 685-697.
- [20] Sahoo, K.L.; Sivaramakrishnan, C.S. Some studies on Al–8.3Fe–0.8V-0.9Si alloy for near net shape casting. J. Mater. Process. Technol. 2002, 135, 253-257. [CrossRef]
- [21] Bang, H.S.; Kwon, H.I.; Chung, S.B.; Kim, D.U.; Kim, M.S. Experimental investigation and numerical simulation of the fluidity of A356 aluminum alloy. Metals 2022, 12, 1986. [CrossRef]
- [22] Šolc, M.; Blaško, P.; Pentrík, J.; Gimanová, L.; Blašková, A.; Małyea, T.; Furman, J.; Socha, V. Simulation Models in a Fluidity Test of the Al-Si Alloy. Metals 2024, 14, 456. [CrossRef]
- [23] Köse, S.; Süküroğlu, E.S. Investigation of the effects of filling speed, casting temperature and metallurgical quality on fluidity of lamellars graphite cast iron at different section thickness. Int. J. Metalcast. 2024. [CrossRef]
- [24] Kayama, N. Viscosity and Fluidity in the Early Stages of Solidification of Metals, Quality Control of Engineering Alloys and the Role of metals Science; Delft University of Technology: Delft, The Netherlands, 1978; pp. 103–119.
- [25] Niu, G.; Mao, J.; Wang, J. Effect of Ce addition on fluidity of casting aluminum alloy A356. Metall. Mater. Trans. A 2019, 50, 5935-5944. [CrossRef]
- [26] Heidazadeh, A.; Emamy, M.; Rhimzadeh, A.; Soufi, R.; Sohrabi Baba Heidary, D.; Nasibi, S. The effect of copper addition on the fluidity and viscosity of an Al-Mg-Si alloy. J. Mater. Eng. Perform. 2014, 23, 469-476. [CrossRef]
- [27] Campbell, J. Thin wall castings. Mater. Sci. Technol. 1988, 4, 194–204. [CrossRef]
- [28] Emamy, M.; Abbasi, S.; Kaboli, S.; Vampbell, J. Fluidity of Al based metal matrix composites containing Al2O3 and SiC par-ticles. Int. J. Cast Met. Res. 2009, 22, 430-437. [CrossRef]
- [29] Rosandi, R.; Masnur, D. Influence of pouring temperatures to fluidity of aluminum scrap cans with investment casting using natural clays as mold materials. JOM FTEKNIK 2016, 3, 1–3.
- [30] Niyama, E.; Anzai, K.; Funakubo, T.; Hiratsuka, S. Some basic research for thin wall casting technology. J. Mater. Process. Technol. 1997, 63, 779-783.
- [31] Tiryakioglu, M.; Askeland, D.R.; Ramsay, C.W. The fluidity of 319 and A356: An experimental design approach. AFS Trans. 1994, 102, 17-25.
- [32] Borouni, M.; Niroumand, N.; Fathi, M.H. Effect of a nano-ceramic mold coating on the fluidity length of thin wall castings in Al4-1 alloy gravity sand casting. Mater. Technol. 2014, 4, 473-477.
- [33] Nishi, N. Characteristics of Fluid Flow for Thin Wall Aluminum Alloy Die Castings. Imono 1995, 67, 918–923.
- [34] Komazaki, T.; Asada, J.; Watanabe, K.; Sasaki, H.; Nishi, N. Effects of Casting Conditions on Flow Length of Thin-Walled Diecasting for ADC 10 Alloy. Imono 1995, 67, 689–695.
- [35] Brenji, R.V. Effectof reinforcement amount, mold temperature, superheat, and mold thickness on fluidity of in-situ Al-Mg2Si compisites. China Foundry 2018, 15, 66-74. [CrossRef]
- [36] Kim, M.-G.; Sung, S.-Y.; Kim, Y.-J. Microstructure, metal mold reaction and fluidity of investment Cast-TiAl alloys. Mater. Trans. 2004, 45, 536-541. [CrossRef]
- [37] Haga, T.; Fuse, H. Semisolid casting of product with thin fins by using Al-25%Si. Key Eng. Mater. 2015, 651–653, 1551–1556. [CrossRef]
- [38] Haga, T.; Fuse, H.; Terao, M. Fabrication thin heat sink by the die casting of semisolid Al-25%Si. Solid State Phenom. 2018, 285, 423-428. [CrossRef]
- [39] Masnur, D.; Rosandi, R.; Nawangsari, P. Effect of mold temperature and cavity thickness on the fluidity of the liquid aluminum beverage cans in the clay mold. AIP Conf. Proc. 2024, 3053, 020017. [CrossRef]
- [40] Asan, Y.E.; Çolak, M. Modeling the effect of pour height, casting and mold heating conditions for the analysis of fluidity of different section thickness in die mold casting of Al12Si alloy. J. Sci. Technol. 2022, 15, 14–27. [CrossRef]
- [41] Fuse, H.; Imamura, S.; Terao, M.; Haga, T. Semisolid die casting of hypereutectic Al-25%Si alloy. Mater. Trans. 2020, 61, 993–999. [CrossRef]
- [42] Han, Z.; Wang, Z.; Sun, Z.; Zhang, B.; Rao, W. Influence of non-uniform ultrasonic vibration on casting fluidity of liquid aluminum alloy. Res. Dev. 2022, 19, 380–386. [CrossRef]
- [43] Al-Mallak, A.A.; Doos, Q.M. Fluidity of Al-Si alloy in metal mold casting under vibration. IOP Conf. Ser. Mater. Sci. Eng. 2021, 1090, 012081. [CrossRef]
- [44] Available online: https://hishinuma.jp/menu/2013/09/hc50f.html (accessed on 29 May 2024).
- [45] Zhang, G.; Wang, Z.; Niu, J.; Xu, H.; Ren, X. Enhanced Fluidity of ZL205A Alloy with the Combined Addition of Al-Ti-C and La. Materials 2021, 14, 6169. [CrossRef] [PubMed]
- [46] Zou, G.; Chai, Y.; Shen, Q.; Cheng, T.; Zhang, H. Analysis of the Fluidity and Hot Tearing Susceptibility of AlSi3.5Mg0.5Cu0.4 and A356 aluminum alloys. Int. J. Metalcast. 2022, 16, 909-923. [CrossRef]
- [47] Available online: https://hishinuma.jp/menu/cat/cat132/cat1/ (accessed on 29 May 2024).
- [48] Motomura, M.; Haga, T.; Sakurai, Y. Design and assembling of single roll apparatus for rapid solidification and characteristics of wide Al-Si eutectic alloy foils solidified. J. Jpn. Inst. Light Met. 1988, 38, 528–533. [CrossRef]
- [49] Haga, T.; Ishihara, K.; Katayama, T.; Nishiyama, T. Effect of contacting condition between molten metal and roll on Al-12%Si alloy strip cast by melt drag method. Keikinzoku 1998, 48, 613–617.
- [50] Haga, T. Development of a twin roll caster for light metals. J. Achiev. Mater. Manuf. Eng. 2010, 43, 393–402.
9. Copyright:
- This material is "Toshio Haga and Hiroshi Fuse"'s paper: Based on "Fluidity of Pure Aluminum in a Narrow Channel Die Gap during Die Casting".
- Paper Source: https://doi.org/10.3390/met14101133
This material was summarized based on the above paper, and unauthorized use for commercial purposes is prohibited.
Copyright © 2025 CASTMAN. All rights reserved.