This introduction paper is based on the paper "Evaluation of Microstructure and Mechanical Property of a Novel Ceramic Salt Core" published by "Journal of the Korean Foundrymen's Society".
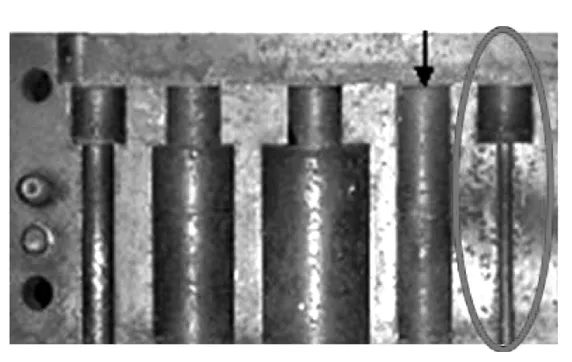
1. Overview:
- Title: Evaluation of Microstructure and Mechanical Property of a Novel Ceramic Salt Core
- Author: Jun-Ho Lee and Dock-Young Lee
- Year of publication: 2008
- Journal/academic society of publication: Journal of the Korean Foundrymen's Society (한국주조공학회지)
- Keywords: Salt core, Ceramic, Compression strength, Casting.
2. Abstract:
This study deals about the development of fusible core with low melting temperature by addition of ceramic particles. A new concept of salt core was introduced to produce an integrated casting part having a complicated inner shape or requiring under-cut in high pressure die casting or squeeze casting process. The mechanical properties of fusible core were improved due to the addition of ceramic particles which helped to produce fine microstructure. The new technology for the preparation of new fusible core materials which possess high compression strength was established. Addition of ceramics particles increased the mechanical properties of fusible core materials. There was an increasing relationship between percentage of ceramic particles and mechanical strength was existed up to 60%.
3. Introduction:
In die casting methods, various cores like metal cores, coated shells, and high-melting point cores are used. However, these methods suffer from drawbacks such as melt infiltration, core breakage due to low strength, and difficulty in post-casting removal. A new type of fusible core is introduced, distinct from conventional cores, utilizing a low-melting point chemical salt (melting point 270-520°C) as the base material, enhanced with ceramic particles to improve strength and core properties [1, 2]. These cores resist fracture and melt infiltration even during low/high-speed injection of molten metal. This is attributed to their very low thermal conductivity (approximately 1/400th of mold steel), which allows a solidified layer to form on the molten metal surface before the core undergoes significant thermal deformation, thus preserving complex core shapes even in die casting.
This study evaluates the necessary characteristics of these fusible cores for casting and assesses their mechanical properties. Die casting [3-6] and squeeze casting involve injecting molten metal into a mold and applying high pressure (50-200 MPa) via hydraulics to fill the cavity and solidify the metal [7-13]. Under such pressure, the fusible core must maintain its strength without fracturing or collapsing. The newly developed fusible core uses low-melting salt (270-520°C) as a base. Its low thermal conductivity prevents core fracture during die casting and allows complex shapes to be realized. However, the low melting point poses a risk of the core melting before the casting solidifies, especially for complex internal features. This research aims to leverage the advantage of complex shape realization while mitigating the melting issue by applying these cores to the die casting process, investigating suitable manufacturing methods, and analyzing the change in mechanical strength (specifically, compression strength) by varying the content of ceramic particles added to the low-melting salt.
4. Summary of the study:
Background of the research topic:
Die casting and squeeze casting processes often require cores to create complex internal geometries or undercuts in cast parts. Traditional core methods face challenges like breakage, melt infiltration, and removal difficulties. Fusible cores based on low-melting point salts offer potential advantages but need sufficient mechanical strength to withstand high casting pressures and thermal stability to avoid premature melting.
Status of previous research:
The paper introduces a new concept of salt core enhanced with ceramic particles. While general core technologies exist [3-13] and properties of molten salts are known [1], this study focuses on the novel combination of low-melting salt and ceramic additives to improve mechanical properties specifically for high-pressure die casting and squeeze casting applications. The limitations of existing cores and the potential issues with basic low-melting salt cores necessitate this investigation into enhanced materials.
Purpose of the study:
The purpose is to develop and evaluate a novel fusible core material by adding ceramic particles to a low-melting point salt base. The study aims to establish a manufacturing technology for these new fusible cores, improve their mechanical properties (specifically compression strength) for suitability in high-pressure die casting and squeeze casting, and understand the relationship between the amount of added ceramic particles and the resulting core strength.
Core study:
The core of the study involved manufacturing fusible core samples using a base of low-melting point salt mixed with varying weight percentages (20 wt.%, 40 wt.%, 50 wt.%, and 60 wt.%) of ceramic particles. The mechanical properties, specifically room temperature compression strength, of these different core compositions were measured. Additionally, the microstructure of the fractured core surfaces was analyzed using SEM to understand how the addition of ceramic particles influences the core's internal structure and relates to its mechanical strength.
5. Research Methodology
Research Design:
The study employed an experimental design to compare the mechanical properties and microstructure of fusible cores made with different compositions. The independent variable was the weight percentage of ceramic particles (0, 20, 40, 50, 60 wt.%) added to a constant base amount of salt. The dependent variables were the compression strength and the observed microstructure.
Data Collection and Analysis Methods:
- Core Manufacturing: Fusible cores were prepared using salt and ceramic powder. For compression test samples (50 mm diameter, 150 mm length), four compositions were made:
- Sample 1: 200g salt + 50g ceramic (20 wt.% ceramic)
- Sample 2: 200g salt + 133g ceramic (40 wt.% ceramic)
- Sample 3: 200g salt + 200g ceramic (50 wt.% ceramic)
- Sample 4: 200g salt + 300g ceramic (60 wt.% ceramic)
The salt was melted at 370°C in a stainless steel crucible (300mm diameter, 300mm height). The specified amount of ceramic powder was added, and the mixture was heated and stirred for 1 hour to ensure homogeneity. The molten mixture (at 370°C) was then gravity poured into an SKD61 steel mold (Fig. 1), preheated to 250°C, to produce the core samples (Fig. 2).
- Compression Testing: Room temperature compression tests were conducted using a Thermecmastor_Z Exhaust System (Fuji Electronic Industrial Co., LTD). Tests were performed on pure salt samples and salt cores with 20, 40, 50, and 60 wt.% ceramic content. The deformation rate was 1 mm/min. Stress-strain curves were recorded (Fig. 3, Fig. 4, Fig. 5, Fig. 6), and the compressive strength (UCS) was determined based on the upper yield point, plotted as a function of ceramic weight % (Fig. 7).
- Microstructure Analysis: Fractured surfaces of the compression-tested cores were examined using Scanning Electron Microscopy (SEM) to analyze the microstructure (Fig. 8, Fig. 9).
Research Topics and Scope:
The research focused on manufacturing low-melting point salt-based fusible cores with varying ceramic particle content (20, 40, 50, 60 wt.%). The scope included measuring the room temperature compression strength of these cores, analyzing their fracture surfaces via SEM to observe microstructural changes, and determining the feasibility limit of ceramic addition for core manufacturing (tested up to 70 wt.%).
6. Key Results:
Key Results:
- Room temperature compression tests showed that the strength of the fusible cores increased as the weight percentage of added ceramic particles increased from 20% to 60% (Fig. 3 - Fig. 7). The upper yield point, considered critical for maintaining dimensional accuracy under load in casting environments, consistently rose with higher ceramic content.
- Analysis of fracture surfaces using SEM (Fig. 8 for 40% ceramic, Fig. 9 for 50% ceramic) revealed that the microstructure of the core material became finer as the ceramic content increased.
- This microstructural refinement is attributed to the significantly higher thermal conductivity of the ceramic particles compared to the salt base material. This difference leads to an increased cooling rate during the manufacturing (solidification) of the fusible core.
- The resulting finer and denser microstructure contributed to the observed increase in compression strength. Furthermore, the ceramic particles act as a reinforcement phase within the salt matrix, creating a composite material effect that enhances strength.
- It was possible to successfully manufacture core samples with up to 60 wt.% ceramic particles. An attempt to add 70 wt.% ceramic resulted in a mixture with excessively high viscosity, making it impossible to form the core samples by pouring.
Figure Name List:
- Fig. 1. Mold for fusible core preparation.
- Fig. 2. Fusible core samples.
- Fig. 3. Stress-strain curve of fusible core; salt-wt20% ceramic.
- Fig. 4. Stress-strain curve of fusible core; salt-40wt% ceramic.
- Fig. 5. Stress-strain curve of fusible core; salt-50wt% ceramic.
- Fig. 6. Stress-strain curve of fusible core; salt-60wt% ceramic.
- Fig. 7. Compressive stress of fusible core as a function of ceramic weight.
- Fig. 8. Fractured surface analysis of fusible core; salt-40% ceramic.
- Fig. 9. Fractured surface analysis of fusible core; salt-50% ceramic.
7. Conclusion:
Compression tests were conducted to evaluate the core's ability to withstand external forces encountered during die casting and other high-pressure casting processes. Cores with 20, 40, 50, and 60 wt.% ceramic added to salt were tested. The following conclusions were drawn:
- Room temperature compression strength analysis showed that the strength of the fusible core increased as the ceramic content increased through the range of 20, 40, 50, and 60 wt.%. This indicates an improved ability to resist deformation under casting pressures.
- Fracture surface analysis (SEM) revealed that the microstructure became finer with increasing ceramic content. This is attributed to the higher thermal conductivity of the ceramic particles compared to the salt, causing faster cooling during core production. The resulting denser structure, along with the composite effect of ceramic particles reinforcing the salt matrix, contributed to the observed increase in strength.
8. References:
- [1] Tatsuhico Ejima, J. of the Korean Inst. of Metals "Thermo-physical Properties of Molten Salts", Vol.25. (1987) 368-377
- [2] J. Kor. Foundrymen's Soc.," Microstructural evolution of electromagnetically stirred Al alloy billet during isothermal reheating at the solid-liquid state", Vol.28.No.3,(2008),129-135
- [3] C. P. Hong, T. Umeda and Y. Kimura, Metall. Trans., "Numerical Models for Solidification: Part 1 & Part 2", 15B, p. 91-101, p. 103-113, (1984)
- [4] K. Ohsasa and T. Takahashi, "Radial Contraction Behavior of Solidifying Shell for Cylindrical Al-3%Si Al-3%Si Alloy Ingot", J. Japan Inst. Metals, 52(12), (1988) 1012-1019,
- [5] S. Engler, D. Boenisch and B. Kohler, "Metal and Mold Wall Movement during Solidification of Cast Iron", AFS Cast Metals Research Journal, 3 (1973) 20-30
- [6] N. Chvorinov, "Theorie der Erstarrung von Gubtucken”, Giesseri, 27 (1940) 177-186 201-208, 222-225
- [7] T. M. Yue, Jour. of Mater. Process. Tech., "Squeeze casting of high-strength aluminium wrought alloy AA7010", 66 (1997) 179-185
- [8] Z.W. Chen, W.R. Thorpe, Mater Sci. and Eng. A, "The effect of squeeze casting pressure and iron content on the impact energy of Al-7Si-0.7Mg alloy", 221 (1996) 143-153
- [9] Fatih ay, S. Can Kurnaz, Mater. & Design, "Hot tensile and fatigue behaviour of zinc-aluminum alloys produced by gravity and squeeze casting", 26 (2005) 479-485
- [10] A Bloyce, J.C Summers, Mater. Sci. and Eng. A, "Static and dynamic properties of squeeze-cast A357-SiC particulate Duralcan metal matrix composite", 135 (1991) 231-263
- [11] M. R. Ghomashchi, K. N. Strafford, Jour. of Mater. Process. Tech., "Factors influencing the production of high integrity aluminium/silicon alloy components by die and squeeze casting processes", 38 (1993) 303-326
- [12] P.V. Evans, R. Keyte, R.A. Ricks, Mater. &Design, "Squeeze casting of aluminium alloys for near net shape manufacture", 14 (1993) 65-67
- [13] M.A. Sava, S. Altinta, Mater. Sci. and Eng. A, "Effects of squeeze casting on the wide freezing range binary alloys", 173 (1993) 227-231
9. Copyright:
- This material is a paper by "Jun-Ho Lee and Dock-Young Lee". Based on "Evaluation of Microstructure and Mechanical Property of a Novel Ceramic Salt Core".
- Source of the paper: [DOI URL Not Found]
This material is summarized based on the above paper, and unauthorized use for commercial purposes is prohibited.
Copyright © 2025 CASTMAN. All rights reserved.