This introductory paper is the research content of the paper ["EFFECTS OF THERMOMECHANICAL TREATMENTS ON THE CHEMICAL AND MECHANICAL PROPERTIES OF Al-Cu Alloy"] published by [International Journal of Materials, Methods and Technologies].
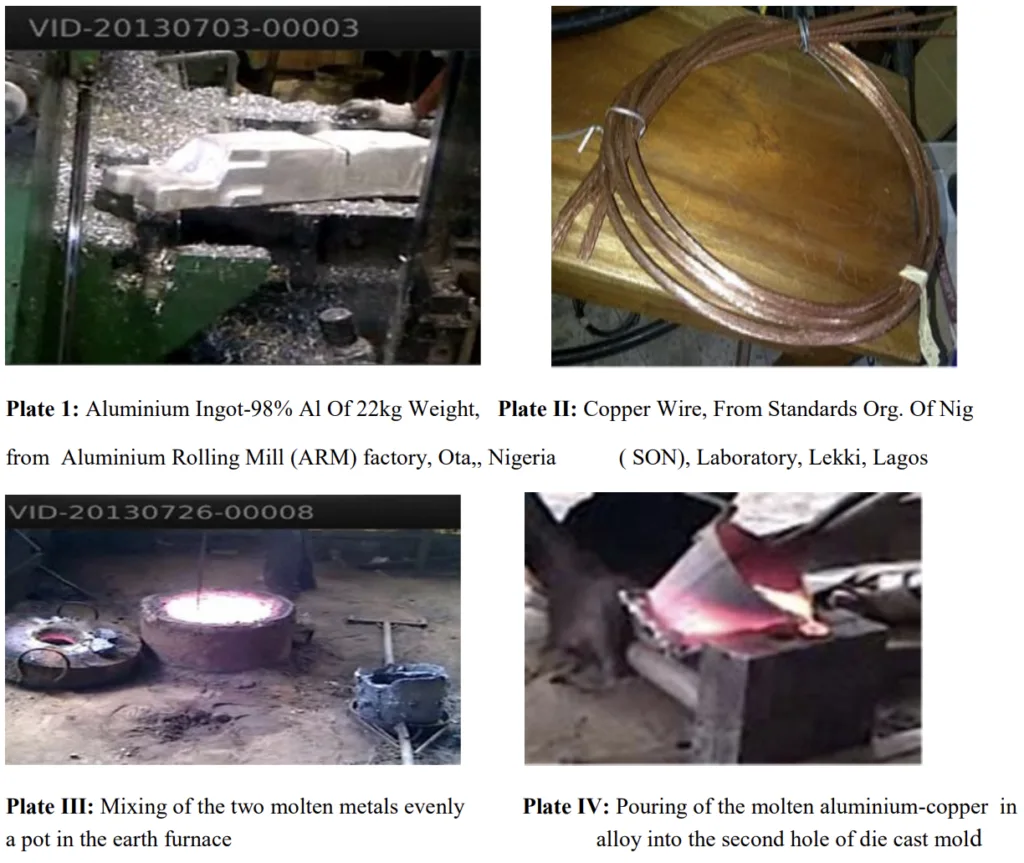
1. Overview:
- Title: EFFECTS OF THERMOMECHANICAL TREATMENTS ON THE CHEMICAL AND MECHANICAL PROPERTIES OF Al-Cu Alloy
- Author: Adegbola Adekunle Amos, Olapade Julius, Aderounmu Mudashiru, Salawu Ismaila, Alabi Ismaila, Kareem Mutiu, Omotoyinbo Joseph Ajibade and Olaniran Oladayo
- Publication Year: January 2014
- Publishing Journal/Academic Society: International Journal of Materials, Methods and Technologies, Vol. 2, No. 1, PP: 1-11, ISSN: 2327-0322 (Online)
- Keywords: Al-9.37Cu, metallography, precipitates, thermomechanical, deformation, INSTRON, over-ageing ductility and Hardnesss
2. Abstracts / Introduction
This research paper investigates the development of Al-9.37Cu alloy characterized through metallographic examinations. The alloy, cast using Die-Casting, underwent treatments including solution treatment, water quenching, air-quenching, and over-ageing. The study revealed that rolling and ageing significantly enhanced the strength of Al-9.37Cu due to the growth of large precipitates along aluminum grain boundaries, impeding dislocation movement during yielding. However, heating the alloy beyond 200°C (500°C) led to a decline in tensile values due to the formation of an equilibrium tetragonal phase, which is fully in-coherent and exhibits low strengthening effect from fibrous structures.
The introduction highlights the role of copper as an alloying element in aluminum to enhance strength, while acknowledging the trade-off with corrosion resistance. It emphasizes the importance of uniform alloying element distribution in lightweight metals like aluminum for homogenous material properties. The text also provides a brief historical context of aluminum production and discusses the solubility of copper in aluminum at different temperatures, referencing the Al-Cu equilibrium phase diagram (Fig.1). The introduction concludes by stating the research aims to explore the influence of thermomechanical ageing on Al-Cu alloy, focusing on the effects of internal stresses and strains during overheating.
3. Research Background:
Background of the Research Topic:
The research addresses the challenge of enhancing the mechanical strength of aluminum while retaining its lightweight and corrosion-resistant properties. Aluminum's inherent low density and corrosion resistance make it ideal for various applications, particularly in the transport industry. Alloying with copper is a common method to improve strength, but the effects of thermomechanical treatments on the resulting Al-Cu alloy's properties require detailed investigation to optimize performance. The study focuses on understanding how different heat treatments and deformation processes affect the microstructure and, consequently, the mechanical properties of a die-cast Al-9.37Cu alloy.
Status of Existing Research:
Existing research, as cited in the introduction, indicates that the solubility of copper in aluminum is temperature-dependent, influencing the formation of different phases and microstructures. The Al-Cu equilibrium phase diagram (Fig.1) is referenced to illustrate the solid solubility limits and the formation of intermetallic compounds like θ (Al2Cu). Prior studies, referenced as (Kacer et al 2003) and (Ashby and Jones, 2006), have explored the fundamental aspects of aluminum alloys and their metallurgical developments. However, this paper delves deeper into the specific effects of thermomechanical treatments, including die-casting, solution treatment, quenching, ageing, and warm-working, on the properties of Al-9.37Cu alloy.
Necessity of the Research:
The research is necessary to optimize the processing parameters for Al-Cu alloys used in die casting. Understanding the impact of thermomechanical treatments on the microstructure and mechanical properties is crucial for producing high-performance components. The study aims to provide insights into achieving a balance between strength and ductility in Al-Cu alloys through controlled heat treatments and deformation, addressing the limitations of pure aluminum's strength and the potential for property degradation due to improper processing. The research seeks to contribute to the development of alternative non-ferrous alloy products with improved corrosion resistance and high strength-to-weight ratio, capable of withstanding significant deformation.
4. Research Purpose and Research Questions:
Research Purpose:
The primary research purpose is to investigate the influence of thermomechanical treatments on the chemical and mechanical properties of Al-Cu alloy, specifically Al-9.37Cu. This involves characterizing the effects of die-casting, solution treatment, quenching (water and air), ageing (natural and artificial), and warm-working on the alloy's microstructure, tensile strength, hardness, and ductility. The study aims to optimize these treatments to enhance the alloy's mechanical performance.
Key Research:
The key research questions addressed in this paper are:
- How do different thermomechanical treatments (solution treatment, quenching, ageing, warm-working) affect the microstructure of die-cast Al-9.37Cu alloy?
- What is the impact of these treatments on the tensile strength, hardness (HRB), and ductility of the Al-9.37Cu alloy?
- How does over-ageing at elevated temperatures influence the mechanical properties and microstructure of the alloy?
- Can optimized thermomechanical treatments enhance the strength-to-weight ratio and overall performance of die-cast Al-Cu alloys for structural applications?
5. Research Methodology
Research Design:
The research employs an experimental design to investigate the effects of thermomechanical treatments on Al-9.37Cu alloy. The study involves casting the alloy using die-casting, followed by subjecting the cast samples to various heat treatments and warm-working processes. Mechanical testing, including tensile tests and hardness measurements, along with metallographic examinations, are conducted to evaluate the resulting properties and microstructural changes.
Data Collection Method:
Data was collected through the following methods:
- Chemical Analysis: Spectrometry was used to determine the chemical composition of the cast Al-Cu alloy (Table I).
- Tensile Testing: INSTRON Tensile Testing Machine was used to measure the tensile strength, yield strength, and elongation of the treated samples (Plate VIII, IX).
- Hardness Testing: Brinell Hardness Testing Machine was used to measure the hardness of the samples (Plate VII).
- Metallographic Examination: Optical microscopy was used to examine the microstructure of the alloy samples under different treatment conditions (Plate X, XI, XII, XIII, XIV, XV).
Analysis Method:
The collected data was analyzed using:
- Quantitative Analysis: Tensile strength, hardness, and elongation values were compared across different treatment conditions to assess the effects of each treatment.
- Qualitative Analysis: Metallographic images were analyzed to correlate microstructural features (grain size, precipitates, phases) with the observed mechanical properties. Stress-strain curves (Fig. 2, 3, 4, 5) and graphs of UTS and Hardness variations (Fig. 6, 7) were used to visualize and compare the results. Pie chart (Fig. 8) was used to show impact values variation.
Research Subjects and Scope:
The research subject is Al-9.37Cu alloy, prepared from 98% Aluminium ingot and Copper wires. The scope of the study is limited to:
- Material: Al-9.37Cu alloy produced by die casting.
- Treatments: Solution treatment at 550°C, water and air quenching, natural and artificial ageing (at 165°C and 200°C for varying durations), annealing at 350°C, and warm-working at 300°C.
- Characterization: Chemical composition, tensile properties, hardness, and microstructure.
6. Main Research Results:
Key Research Results:
- Enhanced Strength through Rolling and Ageing: Rolling and ageing significantly increased the strength of Al-9.37Cu alloy due to the growth of precipitates at grain boundaries, hindering dislocation movement.
- Strength Reduction at High Temperatures: Heating the alloy beyond 200°C (500°C) decreased tensile strength due to the formation of an in-coherent equilibrium tetragonal phase (CuAl2) with low strengthening effect.
- Microstructural Changes: Metallographic examinations revealed dendritic structures in as-cast samples (Plate X), recrystallized grains in annealed samples (Plate XI), precipitates in water-quenched samples (Plate XII), and grain boundary precipitation in air-quenched samples (Plate XIII). Artificially aged samples at 200°C showed further microstructural evolution (Plate XIV), and over-aged samples at 500°C exhibited grain coarsening (Plate XV).
- Optimal Ageing Temperature: Ageing at 200°C for 6 hours resulted in a tensile strength of 177.67 MPa and impact energy of 2.82 J, indicating improved mechanical properties compared to as-cast condition (119 MPa).
- Influence of Quenching Medium: Water quenching and air quenching resulted in different cooling rates and precipitate distributions, affecting the final mechanical properties (Fig. 3).
Analysis of presented data:
- Stress-Strain Curves (Fig. 2, 3, 4, 5): These curves illustrate the variation in tensile behavior of Al-Cu alloy under different thermomechanical treatments. Fig. 2 shows the as-cast condition, Fig. 3 compares air and water quenching, Fig. 4 shows ageing at different times, and Fig. 5 shows annealing at 350°C.
- UTS and Hardness Variation (Fig. 6, 7): Fig. 6 shows the variation of Ultimate Tensile Strength (UTS) with different heat treatments (Normalising, Water Quenched, Aged, Annealed). Fig. 7 shows the variation of Hardness (HRB) with the same treatments. These figures visually compare the effectiveness of different treatments on strength and hardness.
- Impact Values Variation (Fig. 8): Pie chart in Fig. 8 illustrates the impact values variation for different heat treatment processes, showing the percentage distribution across Aged conditions (2hr, 4hr, 6hr), Air Quenched, Annealed, and Water Quenched.
- Over-ageing Effect (Fig. 9): Fig. 9 demonstrates the effect of over-ageing on tensile strength at different temperatures, showing a decrease in tensile values with increasing temperature beyond optimal ageing conditions.
- Microstructure Images (Plate X-XV): These plates provide visual evidence of microstructural changes resulting from different treatments, supporting the interpretation of mechanical property variations.
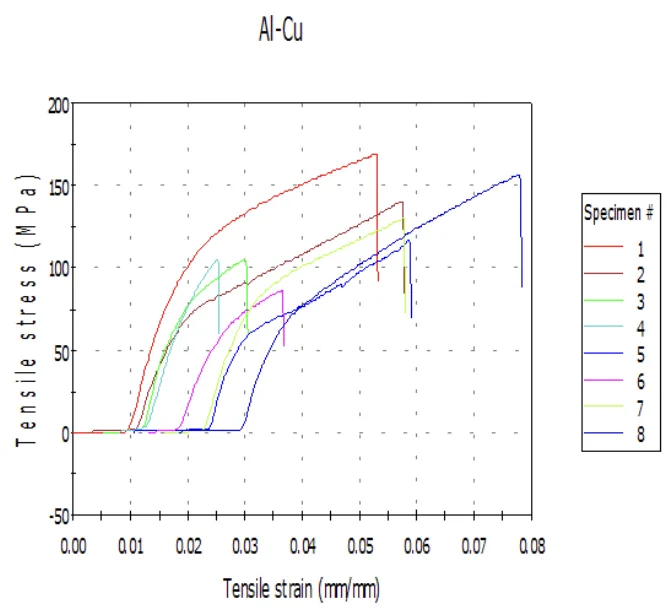
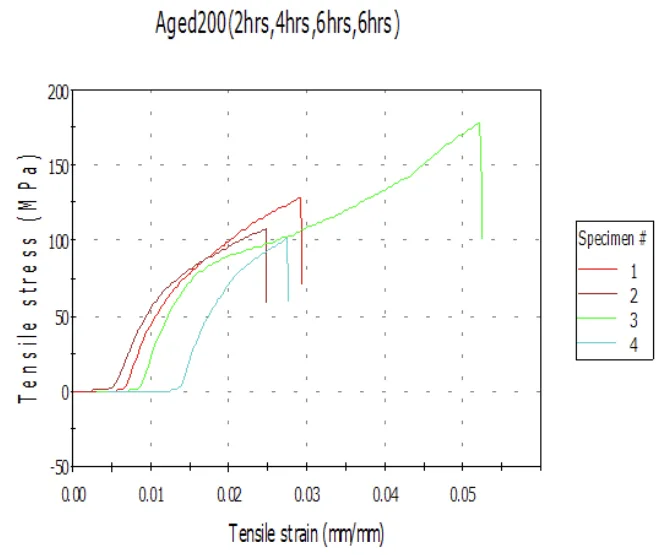
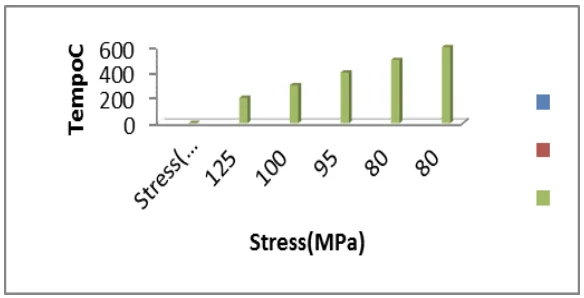
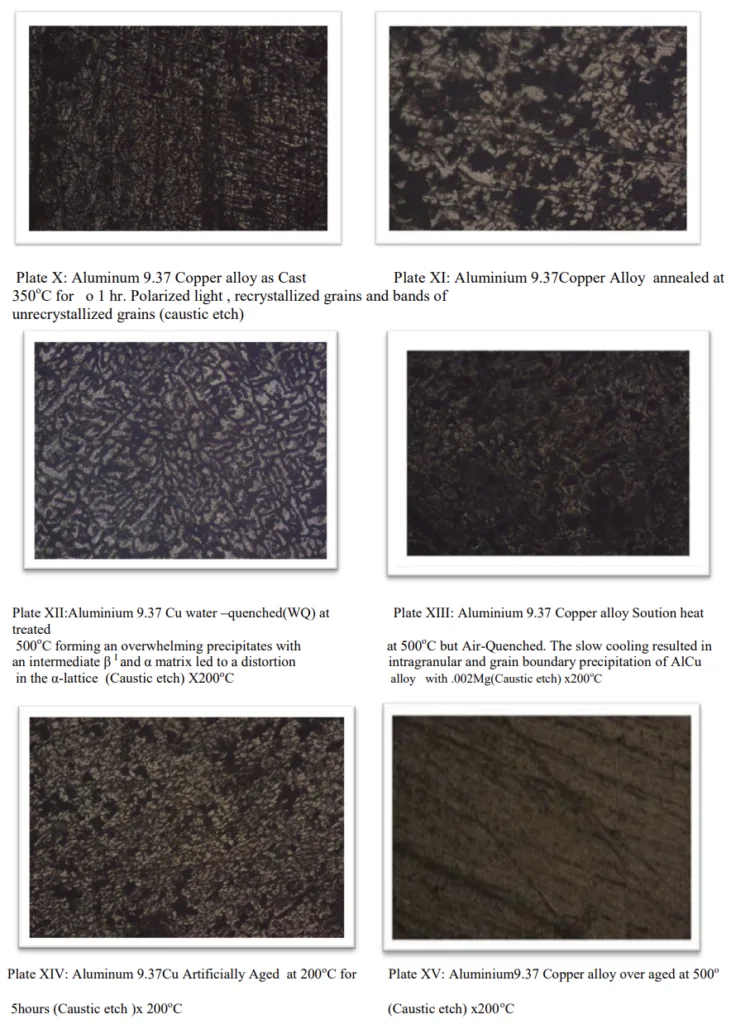
Figure Name List:
- Fig.1: The Al-9.37%Cu alloy equilibrium phase diagram
- Fig.2: Stress (MPa) - Strain (mm/mm) variation of cast Al-Cu alloy before heat treated.
- Fig.3: Stress (MPa) - Strain (mm/ mm) variation of cast Al-Cu alloy after heat treated and cooled at different medium (Air- Water Quench).
- Fig.4: Stress (MPa) - Strain (mm/mm) variation of cast variation of cast Al-Cu alloy after ageing at different time
- Fig. 5: Stress (MPa) - Strain (mm/mm) Al-Cu alloy after annealled at 350°C for 1hr
- Fig.6: Variation of UTS(MPa) with Heat Treatment
- Fig.7: Variation of Hardness(HRB) with Treatment Processes
- Fig.8: Pie Chart showing impact values variation Heat Treatment Processes
- Fig. 9: The effect of Over-ageing on the Tensile Values (MPa) for different Hours of heat treatment processes
- Plate 1: Aluminium Ingot-98% Al Of 22kg Weight, from Aluminium Rolling Mill (ARM) factory, Ota,, Nigeria
- Plate II: Copper Wire, From Standards Org. Of Nig (SON), Laboratory, Lekki, Lagos
- Plate III: Mixing of the two molten metals evenly a pot in the earth furnace
- Plate IV: Pouring of the molten aluminium-copper in alloy into the second hole of die cast mold
- Plate V: Solidified Al-9.37Cu rods
- PlateVI: Aluminum alloy samples loaded inturn inside the Heat treatment oven at Obafemi Awolowo University, Ile-Ife, Nigeria
- Plate VII: Digital Hardness Testing (Brinell Machine under the
- Plate VIII:Mounting of Aluminium Alloy Sample INSTRON Tensile Testing Machine at Center for Energy, Obafemi Awolowo, Ile-Ife, Nigeria
- Plate IX: The interface of tensile tests for aged, Air-Quenched, and Water Quenched samples
- Plate X: Aluminum 9.37 Copper alloy as Cast 350°C for o 1 hr. Polarized light , recrystallized grains and bands of unrecrystallized grains (caustic etch)
- Plate XI: Aluminium 9.37Copper Alloy annealed at
- Plate XII:Aluminium 9.37 Cu water -quenched(WQ) at treated 500°C forming an overwhelming precipitates with an intermediate β¹ and a matrix led to a distortion in the a-lattice (Caustic etch) X200°C
- Plate XIII: Aluminium 9.37 Copper alloy Soution heat at 500°C but Air-Quenched. The slow cooling resulted in intragranular and grain boundary precipitation of AlCu alloy with.002Mg(Caustic etch) x200°C
- Plate XIV: Aluminum 9.37Cu Artificially Aged at 200°C for 5hours (Caustic etch )x 200°C
- Plate XV: Aluminium9.37 Copper alloy over aged at 500° (Caustic etch) x200°C
7. Conclusion:
Summary of Key Findings:
The study concludes that the mechanical properties of die-cast Al-9.37Cu alloy are significantly influenced by thermomechanical treatments. Rolling and ageing enhance strength, while over-ageing at high temperatures reduces it. Solution treatment followed by water quenching and ageing at room temperature for 6 hours optimizes the alloy's strength and hardness, making it suitable for applications requiring a high strength-to-weight ratio. The microstructure analysis confirms that precipitate formation and distribution are critical factors determining the mechanical properties.
Academic Significance of the Study:
This study contributes to the fundamental understanding of phase transformations and precipitation behavior in Al-Cu alloys under various thermomechanical conditions. It provides valuable insights into the relationship between processing parameters, microstructure evolution, and mechanical properties. The research highlights the importance of controlled heat treatments in optimizing the performance of die-cast aluminum alloys, adding to the body of knowledge in materials science and metallurgy.
Practical Implications:
The findings have practical implications for the die casting industry, particularly in the production of Al-Cu alloy components. The study provides a processing guideline for achieving enhanced mechanical properties in Al-9.37Cu alloy through optimized solution treatment, quenching, and ageing. This can lead to the manufacturing of lighter and stronger components for automotive, aerospace, and other engineering applications, potentially improving fuel efficiency and structural performance. Specifically, the research suggests that for applications requiring high strength-weight ratio, a solution treatment at 500°C followed by water-quenching and ageing at room temperature (32°C) for a maximum of 6 hours is recommended.
Limitations of the Study and Areas for Future Research:
The study is limited to Al-9.37Cu alloy and specific thermomechanical treatments. Further research could explore:
- The effects of varying copper content on the thermomechanical behavior of die-cast Al-Cu alloys.
- Optimization of ageing parameters (temperature and time) for different Al-Cu compositions.
- Investigation of other quenching media and their impact on microstructure and properties.
- Detailed analysis of precipitate characteristics (size, distribution, type) using advanced microscopy techniques (e.g., TEM).
- Evaluation of corrosion resistance and fatigue properties of optimally treated Al-Cu alloys.
- Application of these findings to other die-casting alloys and processes.
8. References:
- [1] Aaronson H.I. (1992), Handbook on Metallography and Microstructures, the Materials Information Company, Vol.9, 9th Edition, ISBN 0-87170-007-7 (v. 1)
- [2] Adegbola A., Omotoyinbo J.A, Olaniran O. Ghazali A. and Fashina O. E (2013), Conference Proceedings on Light Metals, TMS, Texas, USA, pp. 481-486, John Wiley & Sons
- [3] Ashby, M.F and Jones, D.R.H (2006),Engineering Materials 2, Second Editon, Butterworth Heineman, Oxford. pp 104-109
- [4] Askeland D.R and Phule P.P (2003), The Science and Engineering of Materials, Thomson Books Inc. USA
- [5] Gayle F.W and Goodway M. (1994), Science. 266(5187): 1015
- [6] Higgins R.A (1980)Engineering Metallurgy, Edward Arnold Publishers, London
- [7] Huda Z, Saufi, Shaifulazaur J.(2006) Industrial Technology 15(2):127
- [8] John V.B (1990) Engineering Materials, Macmillan Press, London
- [9] Kacer H, Atik E, and Meric C (2003) Journal of Materials Processing Tech. 142(3):762
- [10] Lacombe .P, and Moufland. M (1953), Les applications de la Micrographic en Couleurs par Formation des Pellicules Minces Epitaxiques a Teintes d'interference a l'Etude de l'Aluminium, du fer et du Cuivre' Edtions Metaux Saint Germain en Laye; extract from Metaux (Corrosion Ind). Vol.28 (No 340)
9. Copyright:
- This material is "Adegbola Adekunle Amos, Olapade Julius, Aderounmu Mudashiru, Salawu Ismaila, Alabi Ismaila, Kareem Mutiu, Omotoyinbo Joseph Ajibade and Olaniran Oladayo"'s paper: Based on "EFFECTS OF THERMOMECHANICAL TREATMENTS ON THE CHEMICAL AND MECHANICAL PROPERTIES OF Al-Cu Alloy".
- Paper Source: http://ijmmt.com/index.php/ijmmt/article/view/48
This material was created to introduce the above paper, and unauthorized use for commercial purposes is prohibited.
Copyright © 2025 CASTMAN. All rights reserved.