This article introduces the paper ['Effects of microstructure and casting defects on the fatigue behavior of the high-pressure die-cast AlSi9Cu3(Fe) alloy'] presented at the ['Procedia Structural Integrity']
1. Overview:
- Title: Effects of microstructure and casting defects on the fatigue behavior of the high-pressure die-cast AlSi9Cu3(Fe) alloy
- Author: L. Lattanzi, A. Fabrizi, A. Fortini, M. Merlin, G. Timelli
- Publication Year: 2017
- Publishing Journal/Academic Society: Procedia Structural Integrity
- Keywords: die cast aluminum alloy; casting defects; microstructure.
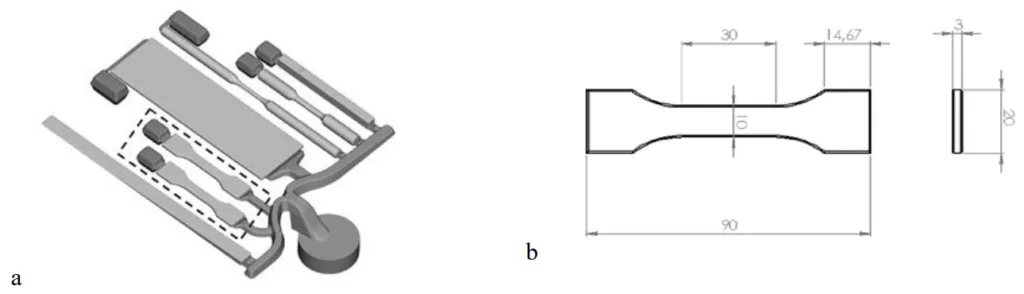
2. Research Background:
Background of the Research Topic:
High-pressure die-cast (HPDC) components are increasingly utilized due to their "good flexibility and high productivity", making them suitable for mass production, particularly in the automotive sector. However, the HPDC process, characterized by "rapid filling of the die and high cooling rate", inherently leads to the formation of "a wide variety of defects, such as porosity and oxide films" and "cold joints", as defined by "PD CEN/TR 16749:2014 standard and proposed by Fiorese et al. 2015". These casting defects are known to negatively impact mechanical properties, potentially acting as "starting points for fatigue cracks and thus deteriorating the fatigue behavior of the casting". Therefore, understanding the fatigue behavior of die-cast aluminum alloys is crucial for assessing the performance of complex castings in automotive applications.
Status of Existing Research:
While the static mechanical properties of die-cast aluminum alloy components have been extensively studied, "very few studies have examined the role of high pressure die casting defects on the fatigue properties". Existing research indicates that casting defects influence static strength differently in each case, with significant variations observed in elongation at rupture. Avalle et al. 2002 reported a decrease in static characteristics of HPDC AlSi9Cu3(Fe) with increasing porosity. Fatigue studies by Avalle et al. 2002 and Mayer et al. 2003 highlighted the role of pores and cold joints in fatigue strength reduction and crack initiation at porosities in HPDC AlSi9Cu3(Fe) and Mg alloys. Hu et al. 2014's research on AlMg5Si2Mn alloy showed that permanent mold specimens have shorter fatigue limits compared to HPDC specimens. Studies on sand casting, permanent mold casting, and low-pressure die casting also confirm that defects reduce fatigue strength, with defect size and location influencing fatigue life. These investigations primarily utilized fracture surface analysis and metallographic characterization to study defect influence on fatigue behavior.
Necessity of the Research:
Despite existing research on casting defects and fatigue, there is a need for a more detailed understanding of how microstructure interacts with fatigue crack initiation and propagation in HPDC AlSi9Cu3(Fe) alloy. The current study aims to address this gap by describing the microstructure's effect on fatigue behavior in this specific alloy produced by HPDC, utilizing microstructural characterization and fatigue testing to identify crack initiation sites and the role of defects in fatigue failure.
3. Research Purpose and Research Questions:
Research Purpose:
The primary goal of this research is "to describe how the microstructure affects the fatigue crack initiation and propagation" in high-pressure die-cast AlSi9Cu3(Fe) aluminum alloy. This is achieved through preliminary microstructural characterization and fatigue testing, followed by detailed fracture surface analysis.
Key Research:
The key research focuses on:
- Characterizing the microstructure of HPDC AlSi9Cu3(Fe) alloy specimens.
- Performing uniaxial fatigue tests under load control to assess fatigue behavior.
- Investigating fracture surfaces and profiles to identify crack initiation sites.
- Studying the influence of casting defects, particularly microstructure, on fatigue crack initiation and propagation and overall fatigue failure.
Research Hypotheses:
While not explicitly stated as hypotheses, the research implicitly investigates the following:
- Casting defects, inherent in the HPDC process, act as primary initiation sites for fatigue cracks in AlSi9Cu3(Fe) alloy.
- Microstructural features, influenced by the HPDC process parameters, significantly affect the fatigue behavior of the alloy.
- The location and type of casting defects (e.g., porosity, oxide films, cold joints, intermetallic compounds, segregation bands) directly correlate with fatigue crack initiation and propagation mechanisms.
4. Research Methodology
Research Design:
This research employs an experimental design involving material production, microstructural characterization, mechanical testing, and fractographic analysis. Die cast AlSi9Cu3(Fe) specimens were produced using a specifically designed die and characterized for microstructure. Uniaxial fatigue tests were conducted, and subsequently, fracture surfaces were analyzed to correlate microstructure and defects with fatigue behavior.
Data Collection Method:
- Material Production: Die cast AlSi9Cu3(Fe) specimens were produced using a cold-chamber die casting machine with specific parameters (locking force 2.9 MN, die temperature ~230 °C, fill fraction 0.28, plunger velocities 0.2 m·s⁻¹ and 2.7 m·s⁻¹, intensification pressure 40 MPa). The chemical composition of the alloy is provided in "Table 1".
- Microstructural Characterization: Preliminary microstructural investigations were performed using "optical (OM) and scanning electron microscopy (SEM)". Phase identification was conducted using "X-ray diffraction (XRD) technique". Grain size and texture evaluation were performed using "electron back-scattered diffraction (EBSD) investigations".
- Fatigue Testing: Uniaxial fatigue tests were performed on "LM10 Italsigma testing machine" under load control with a frequency of "50 s⁻¹" and a stress amplitude of "80 MPa". A stress ratio of "R = 0.1" was used. Fatigue life (number of cycles to failure) was recorded for three specimens.
- Fractographic Analysis: After fatigue tests, fracture surfaces and profiles were examined using "optical and scanning electron microscopy" to identify crack initiation sites, propagation areas, and the role of defects in fatigue failure.
Analysis Method:
- Microstructural Analysis: OM, SEM, XRD, and EBSD were used to characterize grain size, morphology, phase distribution, intermetallic compounds, and casting defects (porosity, oxide films, cold joints, segregation bands). "EDS spectra and elemental maps" were used to identify intermetallic phases.
- Fatigue Data Analysis: Fatigue life data (number of cycles to failure) was recorded and analyzed to assess the scatter in fatigue performance.
- Fractographic Analysis: SEM micrographs of fracture surfaces were analyzed to identify crack initiation sites, propagation regions (stable and static fracture), and associated defects. Fracture profiles were examined using optical microscopy to characterize the crack path and transition zones.
Research Subjects and Scope:
The research subjects were specimens made of "Die cast AlSi9Cu3(Fe) (EN AC-46000) alloy". The scope of the study is limited to:
- Fatigue behavior under uniaxial loading conditions with a stress ratio of R=0.1 and a single stress amplitude level of 80 MPa.
- Microstructural and fractographic analysis of fatigue-tested specimens.
- Investigation of the influence of microstructure and casting defects on fatigue crack initiation and propagation in this specific HPDC aluminum alloy.
5. Main Research Results:
Key Research Results:
- Microstructure: The microstructure of the alloy exhibited "a rosette-like morphology" of α-Al dendrites, typical of a globular grain structure. Grain size and secondary dendrite arm spacing (SDAS) were similar at the core region. "Table 2" shows average values of grain size ("17 ± 8 µm") and SDAS ("12 ± 2 µm"). The d/SDAS ratio was less than 1.6, indicating spherical or globular grain morphology. "Fig. 3b" shows no preferential grain orientation. Intermetallic phases identified included "β-Al5FeSi", "θ-Al2Cu", and blocky "α-Al(Fe,Mn, Cr)Si (sludge)" phases. "Fig. 4b" depicts sludge phases. A "eutectic segregation band" was observed, indicating "positive macro-segregation" and localized Al-Si eutectic enrichment. "Fig. 6a" shows the eutectic segregation region. "Fig. 6b" shows gas porosity concentration in the segregation band region.
- Fatigue Life: Fatigue life of die-cast specimens exceeded "4×10⁴ cycles" at 80 MPa stress level, with failures at "8.7×10⁴ cycles, 4.4×10⁴ cycles, and 10×10⁴ cycles". Data scatter suggests fatigue life dependence on die-cast defects.
- Fractography: Fatigue cracks initiated at section sharp corners, often from a single site. "Fig. 7a" shows the crack initiation region. Fracture surfaces showed a "limited bright area" (stable crack propagation) and an "irregular surface region" (static fracture). Initiation sites were associated with "oxide films and cold joints" at section corners, as seen in "Fig. 7b". "Sludge particles and gas porosities" were observed in the irregular region ("Fig. 8a and Fig. 8b"). Fracture profiles showed a smooth region corresponding to stable propagation and a rough region for static failure ("Fig. 9").
Data Interpretation:
- The globular grain structure and absence of preferential texture suggest uniform solidification, but the presence of a segregation band and gas porosities, induced by the HPDC process, significantly influence dynamic mechanical properties.
- The scatter in fatigue life indicates that casting defects play a dominant role in controlling crack propagation and thus fatigue behavior. Crack initiation, however, appears to be influenced by geometrical characteristics (sharp corners).
- Oxide films and cold joints at sharp corners act as primary crack initiation sites. These defects create material discontinuities, facilitating fatigue crack initiation.
- Sludge particles and gas porosities contribute to the irregular static fracture region, indicating their role in the final failure process after crack propagation.
- The fracture path follows both interdendritic eutectic regions and crosses dendrites during propagation, while static failure follows the dendritic structure profile, suggesting failure of interdendritic constituents promotes fracture propagation.
Figure Name List:
- Fig. 1. (a) Geometry of the die casting, the investigated specimens are indicated by the dashed line rectangle; (b) technical design of the tensile specimen.
- Fig. 2. Typical OM micrograph of a specimen: (a) near the surface; (b) at the center.
- Fig. 3. (a) α-Al grain size dimension distribution; (b) EBSD orientation map obtained in the central cross-section of the specimen.
- Fig. 4. Analyses of secondary phases: (a) XRD spectrum; (b) SEM micrograph of blocky sludge phases.
- Fig. 5. SEM image of the specimen cross-section.
- Fig. 6. (a) eutectic segregation region in the specimen cross-section; (b) porosity in the tensile specimen cross-section.
- Fig. 7. SEM images of the specimen that failed at 8.7×10⁴ cycles: (a) crack initiation region. The red arrow indicates the crack initiation site while the dashed line highlights the transition region; (b) particular of the crack origin site.
- Fig. 8. SEM images of surface features: (a) gas porosity; (b) fractured sludge particles.
- Fig. 9. Fracture profile of the specimen that failed at 8.7×10⁴ cycles. (a) the red arrow indicates the crack initiation point and the dashed arrow indicates the transition region; (b) crack propagation region at high magnification; (c) static failure region at high magnification.
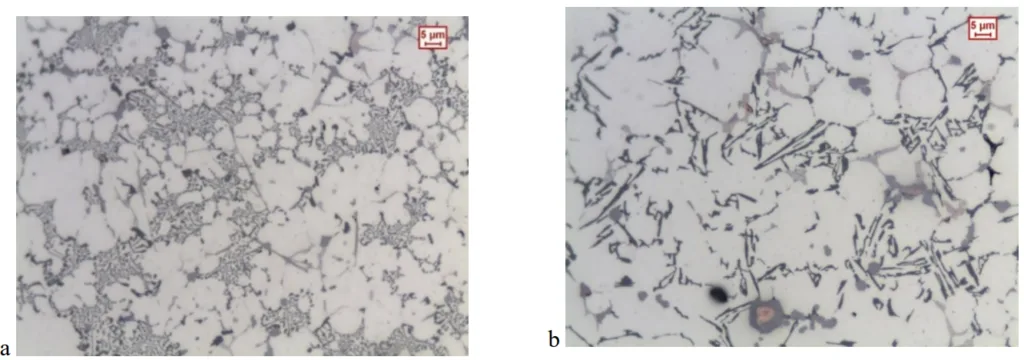
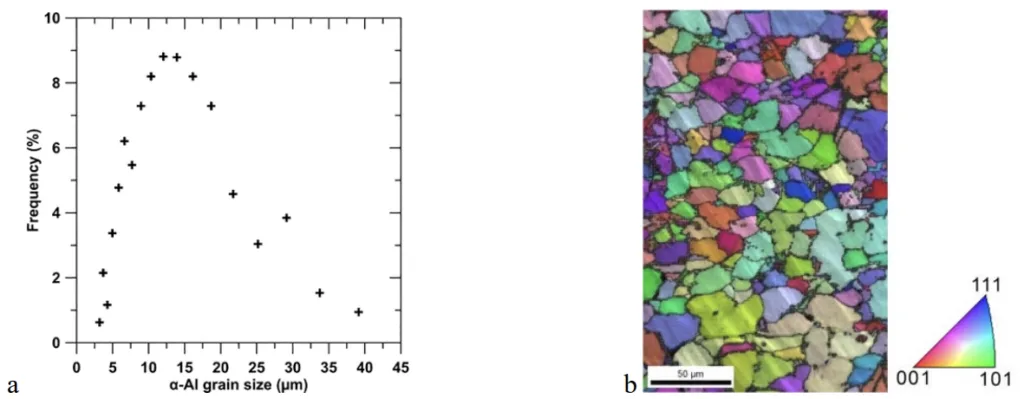
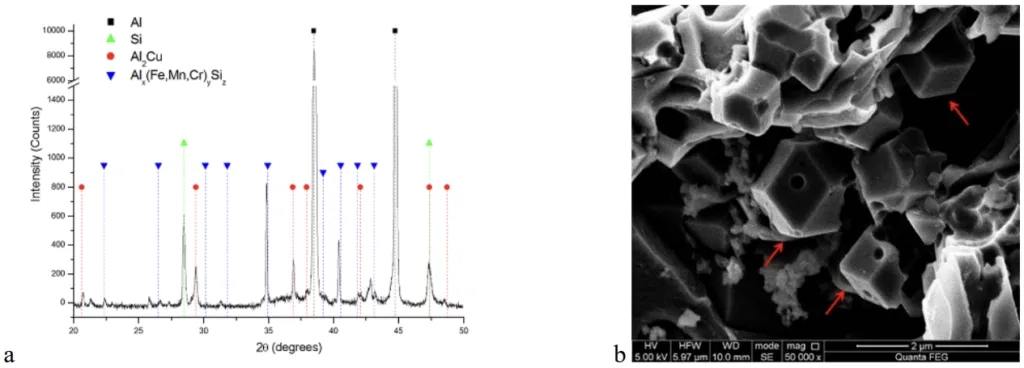

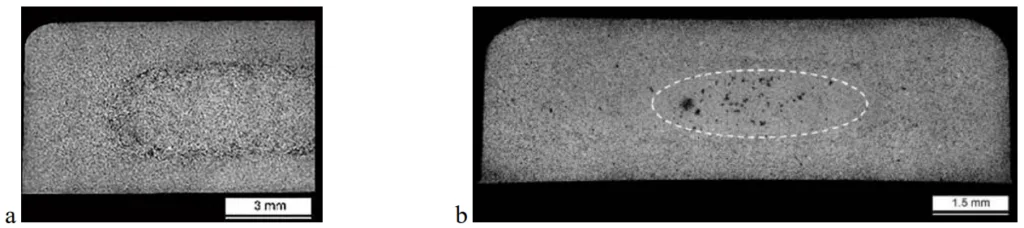
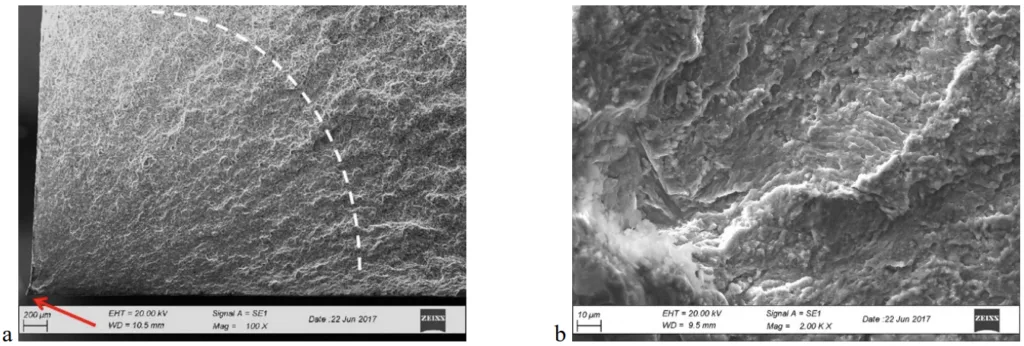
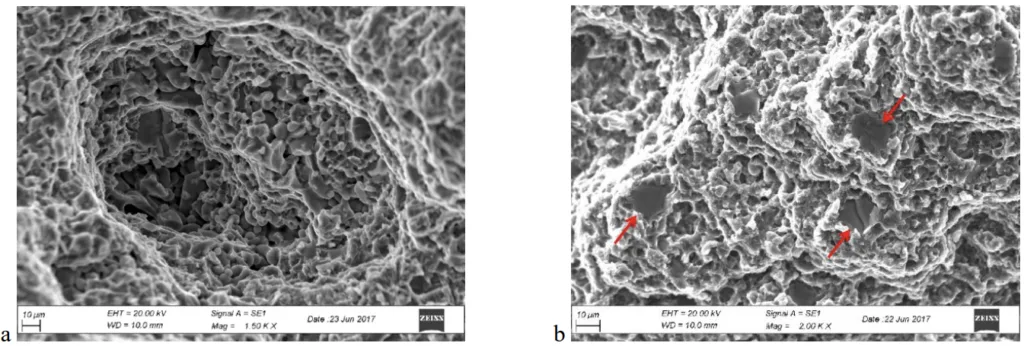
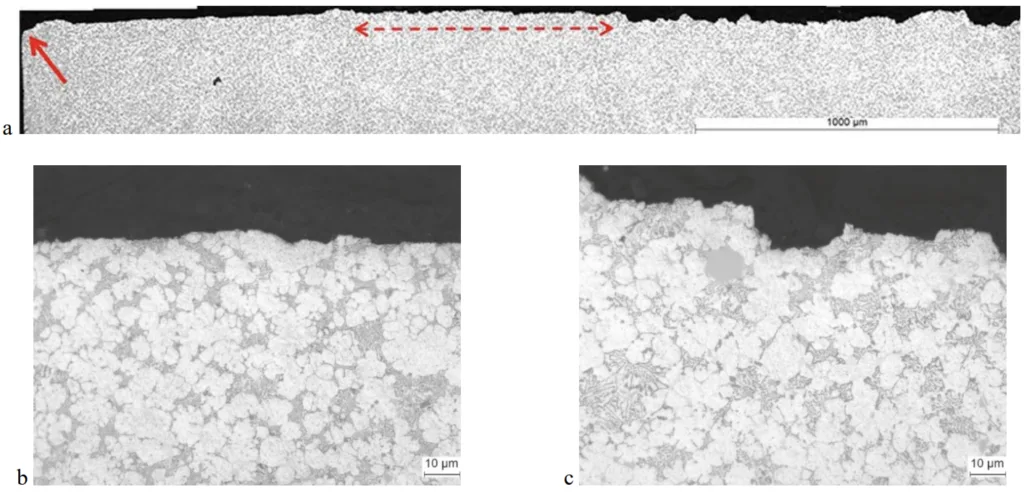
6. Conclusion:
Summary of Main Results:
This study investigated the effects of microstructure and casting defects on the fatigue behavior of HPDC EN AC 46000 alloy. Uniaxial fatigue tests and microstructural/fractographic analyses revealed that:
- A segregation band and gas porosity are present due to the HPDC process.
- Fatigue life exhibits scatter, indicating defect-controlled crack propagation.
- Crack initiation occurs at oxide films and cold joints located at sharp corners.
- Fracture surfaces consist of stable propagation and static fracture regions, with sludge particles and gas porosities in the latter.
- Fracture profiles distinguish smooth (propagation) and rugged (static failure) portions of the crack path.
Academic Significance of the Research:
This research contributes to the fundamental understanding of fatigue behavior in HPDC aluminum alloys by directly linking microstructure and casting defects to fatigue crack initiation and propagation mechanisms. It provides detailed characterization of defect types and their locations, offering insights into how HPDC process-induced defects influence fatigue performance. The study also highlights the importance of considering both geometrical features and material defects in fatigue design for die-cast components.
Practical Implications:
The findings have practical implications for the die casting industry, particularly in automotive applications. Understanding the role of oxide films, cold joints, segregation bands, and porosity in fatigue failure can guide process optimization to minimize defect formation and improve component reliability. Specifically, controlling die filling and cooling rates to reduce segregation and porosity, and optimizing die design to minimize cold joint formation at critical locations like sharp corners, can enhance the fatigue performance of HPDC AlSi9Cu3(Fe) alloy components.
Limitations of the Research
This study is a "preliminary study" with limitations including:
- Fatigue tests were conducted at a single stress amplitude level and stress ratio, limiting the generalizability of the fatigue life data across a wider range of loading conditions.
- The number of fatigue specimens tested (three) is small, which limits the statistical significance of the fatigue life scatter and the quantitative correlation between defect characteristics and fatigue life.
- The study focused on a specific alloy and HPDC process parameters; results may not be directly transferable to other alloys or casting conditions.
7. Future Follow-up Research:
- Directions for Follow-up Research
Future research should "be deepened in order to investigate the role of microstructural constituents" more comprehensively. "Moreover, a higher number of fatigue tests will be performed in order to enable a statistical evaluation of the defects influence on the number of cycles to failure." This includes:- Conducting fatigue tests at multiple stress levels to generate S-N curves and assess fatigue strength.
- Performing statistical analysis with a larger dataset to quantify the relationship between defect characteristics (size, type, location) and fatigue life.
- Investigating the influence of different HPDC process parameters on microstructure, defect formation, and fatigue behavior.
- Exploring advanced non-destructive testing methods for defect characterization and quality control in HPDC components.
- Areas Requiring Further Exploration
Further exploration is needed in:- The precise mechanisms of fatigue crack initiation at oxide films and cold joints.
- The role of different types of intermetallic phases in fatigue crack propagation.
- The interaction between segregation bands, porosity, and fatigue performance.
- Developing predictive models for fatigue life based on microstructure and defect characteristics in HPDC components.
8. References:
- Ammar H.R., Samuel A.M., Samuel F.H., 2008. Porosity and the fatigue behavior of hypoeutectic and hypereutectic aluminum-silicon casting alloys. International Journal of Fatigue 30, 1024-1035.
- Avalle M., Belingardi G., Cavatorta M.P., Doglione R., 2002. Casting defects and fatigue strength of a die cast aluminium alloy: a comparison between standard specimens and production components. International Journal of Fatigue 24, 1-9.
- Fabrizi A., Ferraro S., Timelli G., 2013. The influence of Sr, Mg and Cu addition on the microstructural properties of a secondary AlSiCu3(Fe) die casting alloy. Materials Characterization 85, 13-25.
- Fiorese E., Bonollo F., Timelli G., Arnberg L., Gariboldi E., 2015. New classificationof defects and imperfections for aluminum alloy castings. International Journal of Metalcasting 9, 55-66.
- Hu Z., Wan L., Lu S., Zhu P., Wu S., 2014. Research on the microstructure, fatigue and corrosion behavior of permanent mold and die cast aluminum alloy. Materials and Design 55, 353-360.
- Mayer H., Papakyriacou M., Zettl B., Stanzl-Tschegg S.E., 2003. Influence of porosity on the fatigue limit of die cast magnesium and aluminium alloys. International Journal of Fatigue 25, 245-256.
- Meneghetti G., Susmel L., Tovo R., 2007. High-cycle fatigue crack paths in specimens having different stress concentration features. Engineering Failure Analysis 14, 656-672.
- Mu P., Nadot Y., Nadot-Martin C., Chabod A., Serrano-Munoz I., Verdu C., 2014. Influence of casting defects on the fatigue behavior of cast aluminum AS7G06-T6. International Journal of Fatigue 63, 97-109.
- Serrano-Munoz I., Buffiere J.-Y., Verdu C., Gaillard Y., Mu P., Nadot Y., 2016. Influence of surface and internal casting defects on the fatigue behaviour of A357-T6 cast aluminium alloy. International Journal of Fatigue 82, 361-370.
- Timelli G., Ferraro S., Grosselle F., Bonollo F., Voltazza F., Capra L., 2011. Caratterizzazione meccanica e microstrutturale di leghe di alluminio pressocolate. La Metallurgia Italiana 1, 5-17.
- Wang Q.G., Apelian D., Lados D.A., 2001. Fatigue behavior of A356-T6 aluminum cast alloys. Part I. Effect of casting defects. Journal of Light Metals 1, 73-84.
9. Copyright:
- This material is "The Authors"'s paper: Based on "Effects of microstructure and casting defects on the fatigue behavior of the high-pressure die-cast AlSi9Cu3(Fe) alloy".
- Paper Source: 10.1016/j.prostr.2017.11.119
This material was summarized based on the above paper, and unauthorized use for commercial purposes is prohibited.
Copyright © 2025 CASTMAN. All rights reserved.