This article introduces the paper "Effect of Artificial Aging Treatment on the Mechanical Properties and Regulation of Precipitated Phase Particles of High-Pressure Die-Cast Thin-Wall AlSi10MnMg Longitudinal Carrier" presented at Materials, MDPI
1. Overview:
- Title: Effect of Artificial Aging Treatment on the Mechanical Properties and Regulation of Precipitated Phase Particles of High-Pressure Die-Cast Thin-Wall AlSi10MnMg Longitudinal Carrier
- Author: Xu Zhao, Ping Wang, Yang Yang, Song Wang, Qiang Zhao, and Jingying Sun
- Publication Year: 2023
- Publishing Journal/Academic Society: Materials, MDPI
- Keywords: single-stage aging; double-stage aging; AlSi10MnMg alloy; microstructure; mechanical properties
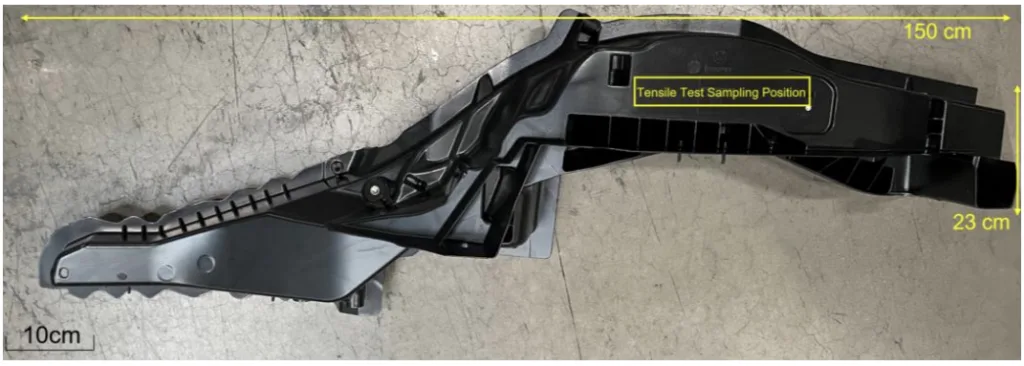
2. Research Background:
- Social/Academic Context of the Research Topic: The increasing demand for lightweight construction in the automotive industry, driven by the burgeoning sales of electric vehicles, highlights the importance of aluminum alloys. Die-cast aluminum alloys, particularly high-quality AlSi10MnMg alloys used in automotive structural components like longitudinal carriers, are gaining prominence. Age-hardening heat treatments are crucial for enhancing the strength of these alloys.
- Limitations of Existing Research: While AlSi10MnMg alloy exhibits good tensile strength and hardness after T6 solution aging, further enhancement, especially in elongation, is needed. Existing research provides limited insight into the mechanical properties and precipitate phases of AlSi10MnMg alloy after double-stage aging.
- Necessity of the Research: To optimize the performance of die-cast AlSi10MnMg alloy for automotive structural applications, a deeper understanding of the double-stage aging mechanism is necessary. This research aims to investigate and optimize the double-stage aging process to achieve a superior balance of strength, hardness, and ductility in this alloy.
3. Research Purpose and Research Questions:
- Research Purpose: To investigate the effects of single-stage and double-stage artificial aging processes on the mechanical properties and microstructure of die-cast AlSi10MnMg aluminum alloy. The study aims to identify the optimal aging process and elucidate the underlying micromechanisms that enhance the alloy's performance.
- Key Research Questions:
- How do single-stage and double-stage aging treatments affect the microstructure and mechanical properties (tensile strength, hardness, elongation) of die-cast AlSi10MnMg alloy?
- What are the optimal parameters for single-stage and double-stage aging to maximize strength and ductility?
- What are the micromechanisms, particularly related to precipitate phases, responsible for the changes in mechanical properties during single-stage and double-stage aging?
- Research Hypotheses: The study hypothesizes that double-stage aging can lead to superior mechanical properties compared to single-stage aging by controlling the precipitation and growth of secondary phases in the AlSi10MnMg alloy.
4. Research Methodology
- Research Design: Experimental study employing single-stage and double-stage artificial aging treatments on die-cast AlSi10MnMg alloy. Orthogonal experimental design (L9(3^4) table) was used for double-stage aging parameter optimization.
- Data Collection Method:
- Chemical Composition Analysis: Optical Emission Spectroscopy (OES)
- Tensile Testing: Universal testing machine (Z150) at room temperature, strain rate of 1 mm·min⁻¹, using DIN50125-E5 specimens.
- Hardness Testing: Brinell hardness measurements using a microhardness tester (62.5 kgf load, 30 s loading time).
- Microstructural Analysis: Optical Microscopy (OM) and Scanning Electron Microscopy (SEM) with Energy-Dispersive Spectroscopy (EDS).
- Phase Analysis: X-ray Diffraction (XRD) using monochromatic Cu-Kα radiation.
- Precipitate Phase Measurement: Image pro plus software.
- Analysis Method:
- Range analysis and orthogonal analysis using SPSS software to determine the influence of aging parameters in double-stage aging.
- Analysis of variance in mechanical properties and microstructure with varying aging parameters.
- Correlation of microstructure features (precipitate size, distribution, phases) with mechanical properties.
- Research Subjects and Scope: Die-cast thin-wall AlSi10MnMg longitudinal carrier samples provided by Brilliance BMW Ltd. Samples underwent solution treatment at 520 °C for 2 h, followed by single-stage aging (165 °C, 180 °C, 195 °C for 1h, 3h, 5h) and double-stage aging (orthogonal design parameters).
5. Main Research Results:
- Key Research Results:
- Single-Stage Aging: Peak strength for single-stage aging was achieved at 180 °C × 3 h, yielding a tensile strength of 332.5 MPa, Brinell hardness of 133.0 HB, and elongation of 5.56%. Tensile strength and hardness initially increased and then decreased with aging time, while elongation showed an inverse trend.
- Double-Stage Aging: Optimal double-stage aging process identified as first-stage aging at 100 °C × 3 h and second-stage aging at 180 °C × 3 h. Range analysis indicated the influence of parameters on mechanical properties in the order: first-stage aging time > first-stage aging temperature > second-stage aging time > second-stage aging temperature.
- Microstructure: The amount of secondary phase particles at grain boundaries increased with aging temperature and holding time, stabilizing as aging progressed and eventually coarsening. Double-stage aging resulted in more compact and uniformly distributed precipitates compared to single-stage aging.
- Fracture Surface: Fracture surfaces exhibited mixed fracture characteristics, including ductile dimples and brittle cleavage steps.
- Statistical/Qualitative Analysis Results:
- Range analysis of orthogonal experiments showed that first-stage aging time is the most influential factor on the strength-toughness index (Q value).
- XRD analysis confirmed the precipitation of Mg₂Si phase in aged samples, with variations in peak sharpness and area correlating with aging conditions and mechanical properties.
- Data Interpretation:
- Single-stage aging at 180 °C for 3 h provides a good balance of strength and hardness.
- Double-stage aging, with optimized parameters, further enhances mechanical properties by controlling precipitate morphology and distribution. The initial low-temperature aging step promotes the formation of stable G.P. zones, which then facilitate finer and more uniform precipitation during the subsequent high-temperature aging.
- Figure Name List:
- Figure 1. Shape specifications of longitudinal carrier and sampling position of tensile sample.
- Figure 2. Dimensions of tensile specimen.
- Figure 3. Optical micrograph of AlSi10MnMg longitudinal carrier after single-stage aging.
- Figure 4. Mechanical properties of AlSi10MnMg longitudinal carrier under different aging time.
- Figure 5. Mechanical properties of AlSi10MnMg longitudinal carrier under different aging temperatures.
- Figure 6. Tensile fracture surfaces SEM images of AlSi10MnMg longitudinal carrier.
- Figure 7. Effect of double-stage aging parameters on the Q index of die-cast AlSi10MnMg longitudinal carrier.
- Figure 8. Optical micrograph of AlSi10MnMg longitudinal carrier after single-stage aging and double-stage aging.
- Figure 9. SEM images and EDS surface scanning results of AlSi10MnMg longitudinal carrier after single-stage aging and double-stage aging.
- Figure 10. XRD test result of AlSi10MnMg longitudinal carrier.
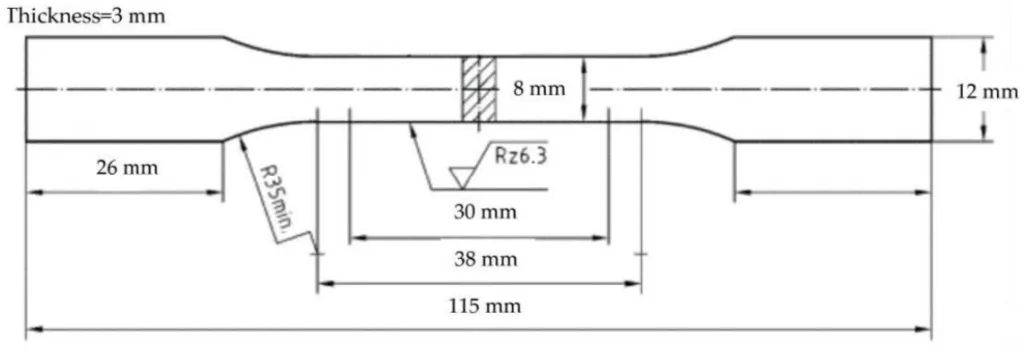
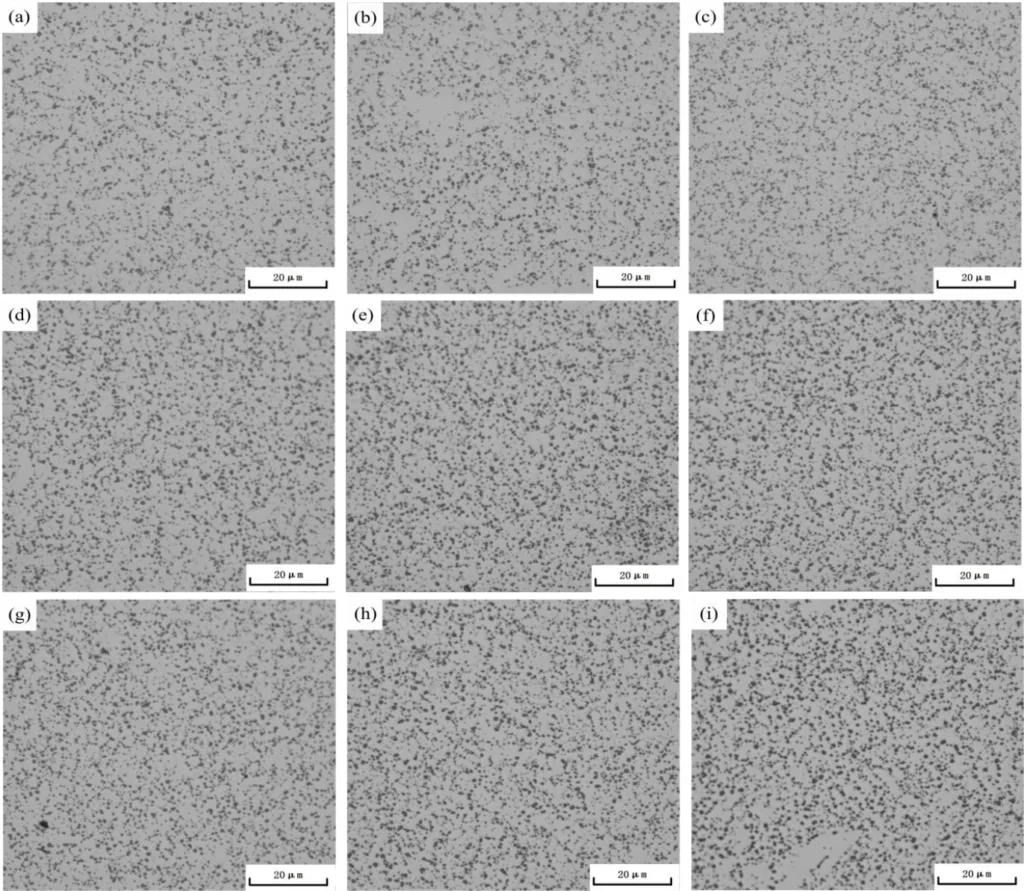
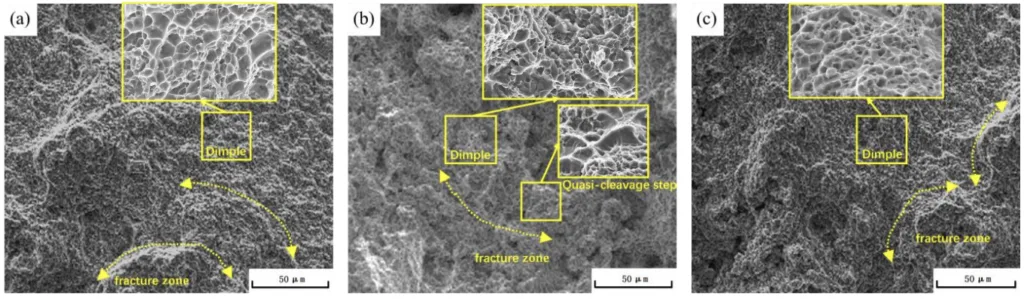
6. Conclusion and Discussion:
- Summary of Main Results: The study successfully optimized both single-stage and double-stage artificial aging processes for die-cast AlSi10MnMg alloy. Single-stage aging at 180 °C × 3 h yielded peak strength. Double-stage aging, with optimal parameters of 100 °C × 3 h + 180 °C × 3 h, further improved the strength-toughness balance. Microstructural analysis and XRD confirmed the role of precipitate phases in influencing mechanical properties.
- Academic Significance of the Research: This research provides a comprehensive understanding of the aging behavior of die-cast AlSi10MnMg alloy, particularly under double-stage aging conditions. It elucidates the relationship between aging parameters, microstructure evolution, and mechanical properties, contributing to the fundamental knowledge of age-hardening mechanisms in this alloy system.
- Practical Implications: The optimized double-stage aging process identified in this study offers a practical approach to enhance the mechanical performance of AlSi10MnMg die-cast components, such as longitudinal carriers in automobiles. This can lead to lighter and stronger automotive structures, contributing to improved fuel efficiency and performance of electric vehicles. The optimal single-stage aging condition also provides a valuable reference for simpler heat treatment processes.
- Limitations of the Research: The study focused on specific aging temperatures and times. Further investigation could explore a wider range of parameters and their interactions. The research is limited to laboratory-scale experiments; industrial-scale validation of the optimized processes is recommended.
7. Future Follow-up Research:
- Directions for Follow-up Research:
- Investigate the effect of a broader range of first-stage and second-stage aging parameters to further refine the optimal double-stage aging process.
- Explore the impact of trace elements and casting process variations on the aging response of AlSi10MnMg alloy.
- Conduct in-situ studies of precipitate evolution during double-stage aging to gain deeper insights into the transformation kinetics.
- Evaluate the fatigue and corrosion performance of AlSi10MnMg alloy subjected to optimized double-stage aging.
- Areas Requiring Further Exploration:
- The long-term stability of the mechanical properties achieved through double-stage aging.
- The economic feasibility and scalability of implementing double-stage aging in industrial die-casting processes.
- Modeling and simulation of the precipitation process in AlSi10MnMg alloy to predict and optimize aging treatments.
8. References:
- Dhara, S.; Das, A. Impact of ultrasonic welding on multi-layered Al–Cu joint for electric vehicle battery applications: A layer-wise
microstructural analysis. Mater. Sci. Eng. A Struct. Mater. Prop. Microstruct. Process. 2020, 791, 139795. [CrossRef] - Dunn, J.; Gaines, L.; Kelly, J.; James, C.; Gallagher, K. The significance of Li-ion batteries in electric vehicle life-cycle energy and
emissions and recycling’s role in its reduction. Energy Environ. Sci. 2015, 8, 158–168. [CrossRef] - De Leon, M.; Shin, H. Review of the advancements in aluminum and copper ultrasonic welding in electric vehicles and
superconductor applications. J. Mater. Process. Technol. 2022, 307, 117691. [CrossRef] - Sadeghian, A.; Iqbal, N. A review on dissimilar laser welding of steel-copper, steel-aluminum, aluminum-copper, and steel-nickel
for electric vehicle battery manufacturing. Opt. Laser Technol. 2022, 146, 107595. [CrossRef] - Camargos, P.; Santos, P.; Santos, I.; Ribeiro, G.; Caetano, R. Perspectives on Li-ion battery categories for electric vehicle applications:
A review of state of the art. Int. J. Energy Res. 2022, 46, 19258–19268. [CrossRef] - Popescu, M.; Goss, J.; Staton, D.; Hawkins, D.; Chong, Y.; Boglietti, A. Electrical Vehicles-Practical Solutions for Power Traction
Motor Systems. IEEE Trans. Ind. Appl. 2018, 54, 2751–2762. [CrossRef] - Battaglia, E.; Bonollo, F.; Ferro, P.; Fabrizi, A. Effect of Heat Treatment on Commercial AlSi12Cu1(Fe) and AlSi12(b) Aluminum
Alloy Die Castings. Metall. Mater. Trans. A Phys. Metall. Mater. Sci. 2018, 49, 1631–1640. [CrossRef] - Dash, S.; Li, D.; Zeng, X.; Li, D.; Chen, D. Low-cycle fatigue behavior of Silafont®-36 automotive aluminum alloy: Effect of
negative strain ratio. Mater. Sci. Eng. A Struct. Mater. Prop. Microstruct. Process. 2022, 852, 143701. [CrossRef] - Zhang, J.; Cinkilic, E.; Huang, X.; Wang, G.; Liu, Y.; Weiler, J.; Luo, A. Optimization of T5 heat treatment in high pressure die
casting of Al–Si–Mg–Mn alloys by using an improved Kampmann-Wagner numerical (KWN) model. Mater. Sci. Eng. A Struct.
Mater. Prop. Microstruct. Process. 2023, 865, 144604. [CrossRef] - Schwankl, M.; Himmler, D.; Urban, M.; Körner, C. Optimization of Mechanical Properties of Al–Al-Compound Castings by
Adapted Heat Treatment. Adv. Eng. Mater. 2018, 20, 1800400. [CrossRef] - Shi, J.; Pries, H.; Stammen, E.; Dilger, K. Chemical pretreatment and adhesive bonding properties of high-pressure die cast
aluminum alloy: AlSi10MnMg. Int. J. Adhes. Adhes. 2015, 61, 112–121. [CrossRef] - Mazahery, A.; Shabani, M.O. Experimental Investigation on the Aging Response, Hardness and Total Impact Energy Absorption
of Sr-Modified Heat-Treatable Cast Automotive Aluminum Alloys. Trans. Indian Inst. Met. 2014, 67, 753–759. [CrossRef] - Jiao, X.; Zhang, Y.; Wang, J.; Nishat, H.; Liu, Y.; Liu, W.; Xiong, S. Characterization of externally solidified crystals in a highpressure die-cast AlSi10MnMg alloy and their effect on porosities and mechanical properties. J. Mater. Process. Technol. 2021,
298, 117299. [CrossRef] - Niklas, A.; Orden, S.; Bakedano, A.; Da Silva, M.; Nogués, E.; Fernández-Calvo, A. Effect of solution heat treatment on gas
porosity and mechanical properties in a die cast step test part manufactured with a new AlSi10MnMg(Fe) secondary alloy. Mater.
Sci. Eng. A Struct. Mater. Prop. Microstruct. Process. 2016, 667, 376–382. [CrossRef] - Huang, L.; Peng, L.; Mi, X.; Zhao, G.; Huang, G.; Xie, H.; Zhang, W. Effect of Cold Working on the Properties and Microstructure
of Cu-3.5 wt% Ti Alloy. Materials 2022, 15, 8042. [CrossRef] [PubMed] - Kapil, A.; Lee, T.; Vivek, A.; Cooper, R.; Hetrick, E.; Daehn, G. Spot impact welding of an age-hardening aluminum alloy: Process,
structure and properties. J. Manuf. Process. 2019, 37, 42–52. [CrossRef] - Tao, K.; Xu, J.; Zhang, D.; Zhang, A.; Su, G.; Zhang, J. Effect of Final Thermomechanical Treatment on the Mechanical Properties
and Microstructure of T Phase Hardened Al-5.8Mg-4.5Zn-0.5Cu Alloy. Materials 2023, 16, 3062. [CrossRef] - Liu, F.; Yu, F.; Zhao, D. Aging Behavior and Precipitates Analysis of Wrought Al-Si-Mg Alloy. Materials 2022, 15, 8194. [CrossRef]
- Szlancsik, A.; Kincses, D.; Orbulov, I. Mechanical properties of AlSi10MnMg matrix syntactic foams filled with lightweight
expanded clay particles. IOP Conference Series. Mater. Sci. Eng. 2020, 903, 12045. - Nishiwaki, Y.; Takekawa, T. Forensic Comparison of Automotive Aluminum Wheel Fragments Using Synchrotron Radiation
X-ray Fluorescence with 18- and 116-keV Excitation X-rays. J. Forensic Sci. 2019, 64, 1034–1039. [CrossRef] - Srivastava, M.C.; Lohne, O. Effects of Heat Treatment on the Microstructure and Mechanical Properties of Ductile AlSi9MgMn
Die Castings. Inter. Metalcast. 2016, 10, 556–565. [CrossRef] - Birol, Y.; Karlik, M. The interaction of natural ageing with straining in a twin-roll cast AlMgSi automotive sheet. Scr. Mater. 2006,
55, 625–628. [CrossRef] - Wang, W.; Pan, Q.; Wang, X.; Sun, Y.; Ye, J.; Lin, G.; Liu, Y. Non-isothermal aging: A heat treatment method that simultaneously
improves the mechanical properties and corrosion resistance of ultra-high strength Al-Zn-Mg-Cu alloy. J. Alloys Compd. 2020,
845, 156286. [CrossRef] - Wu, C.; Feng, D.; Ren, J.; Zang, Q.; Li, J.; Liu, S.; Zhang, X. Effect of non-isothermal retrogression and re-ageing on throughthickness homogeneity of microstructure and properties of Al-8Zn-2Mg-2Cu alloy thick plate. J. Cent. South Univ. 2022, 29,
960–972. [CrossRef] - Zheng, X.; Yang, Y.; Tang, J.; Han, B.; Xu, Y.; Zeng, Y.; Zhang, Y. Influence of Retrogression Time on the Fatigue Crack Growth
Behavior of a Modified AA7475 Aluminum Alloy. Materials 2023, 16, 2733. [CrossRef] - Anijdan, S.M.; Kang, D.; Singh, N.; Gallerneault, M. Precipitation behavior of strip cast Al-Mg-0.4Sc-0.15Zr alloy under single and
multiple-stage aging processes. Mater. Sci. Eng. A 2015, 640, 275–279. [CrossRef] - Santhosh, R.; Geetha, M.; Saxena, V.K.; Nageswararao, M. Studies on single and duplex aging of metastable beta titanium alloy
Ti-15V-3Cr-3Al-3Sn. J. Alloys Compd. 2014, 605, 222–229. [CrossRef] - Oh-ishi, K.; Hono, K.; Shin, K.S. Effect of pre-aging and Al addition on age-hardening and microstructure in Mg-6wt% Zn alloys.
Mater. Sci. Eng. A 2008, 496, 425–433. [CrossRef] - Antunes, P.; Silva, C.; Correa, E.; Tavares, S. Influence of the heat input and aging treatment on microstructure and mechanical
properties of AISI 317 L steel weldments using 0020 robotic–pulsed GMAW. Int. J. Adv. Manuf. Technol. 2019, 105, 5151–5163.
[CrossRef] - Zhu, S.Z.; Luo, T.J.; Yang, Y.S. Improving mechanical properties of age-hardenable Mg-6Zn-4Al-1Sn alloy processed by double
aging treatment. J. Mater. Sci. Technol. 2017, 33, 1249–1254. [CrossRef] - Shaeri, M.; Taheri, K.; Taheri, A.; Shaeri, M. Influence of heat treatment and aging on microstructure and mechanical properties of
Mg-1.8Zn-0.7Si-0.4Ca alloy. Mater. Werkst. 2019, 50, 187–196. [CrossRef] - Abdelaziz, M.; Samuel, A.; Doty, H.; Songmene, V.; Samuel, F. Mechanical Performance and Precipitation Behavior in Al-Si-Cu-Mg
Cast Alloys: Effect of Prolonged Thermal Exposure. Materials 2022, 15, 2830. [CrossRef] [PubMed] - Ammar, H.; Moreau, C.; Samuel, A.; Samuel, F.; Doty, H. Influences of alloying elements, solution treatment time and quenching
media on quality indices of 413-type Al–Si casting alloys. Mater. Sci. Eng. A Struct. Mater. Prop. Microstruct. Process. 2008, 489,
426–438. [CrossRef] - Xu, J.; Pan, Y.; Lu, T.; Bo, B. Synergistic effects of composition and heat treatment on microstructure and properties of vacuum die
cast Al-Si-Mg-Mn alloys. China Foundry 2018, 15, 117–123. [CrossRef] - Vissers, R.; Van Huis, M.; Jansen, J.; Zandbergen, H.; Marioara, C.; Andersen, S. The crystal structure of the β
0 phase in Al–Mg–Si
alloys. Acta Mater. 2017, 55, 3815–3823. [CrossRef] - Lazi´c, M.M.; Lazi´c, M.; Milašin, J.; Popovi´c, D.; Majeriˇc, P.; Rudolf, R. In Vitro Evaluation of the Potential Anticancer Properties of
Cu-based Shape Memory Alloys. Materials 2023, 16, 2851. [CrossRef] - Ninive, P.; Strandlie, A.; Gulbrandsen-Dahl, S.; Lefebvre, W.; Marioara, C.; Andersen, S.; Løvvik, O. Detailed atomistic insight
into the β” phase in Al–Mg–Si alloys. Acta Mater. 2014, 69, 126–134. [CrossRef]
9. Copyright:
- This material is "Xu Zhao, Ping Wang, Yang Yang, Song Wang, Qiang Zhao, and Jingying Sun"'s paper: Based on "Effect of Artificial Aging Treatment on the Mechanical Properties and Regulation of Precipitated Phase Particles of High-Pressure Die-Cast Thin-Wall AlSi10MnMg Longitudinal Carrier".
- Paper Source: https://doi.org/10.3390/ma16124369
This material was summarized based on the above paper, and unauthorized use for commercial purposes is prohibited.
Copyright © 2025 CASTMAN. All rights reserved.