용탕단조 시 저온염코어 적용 가압력의 영향
- Lee, Jun-Ho (R & D Division for Hyundai Motor Co. & Kia Motors Corp.) ;
- Moon, J.H. (R & D Center, Dong Yang Piston Co., LTD.) ;
- Lee, Dock-Young (Division of Materials, Korea Institute of Science and Technology)
Abstract
A new concept of salt core, a melting temperature of which is lower than the solidus temperature of cast alloy, was introduced to produced an integrated casting part having a complicated inner shape or requiring under-cut in high pressure die casting or squeeze casting process. The main goal of this study is to develop a new integrated net-shape forming technology using fusible core of lower melting temperature than that of a casting alloy. This integrated net-shape forming technology would be very successful and cost-effective for producing the integrated products having a complicated inner shape or requiring under-cut. The technology for measuring and evaluating a various property of fusible core such as a thermal conductivity and thermal expansion coefficient, melting temperature was established. Also, the work space can be cleaned without a pollution inducing products.
서 론
최근 알루미늄 주물과 마그네슘 주물의 제조에 다이캐스팅, 저압주조, 및 용탕단조 등 압력을 이용하는 주조법의 적용이 크게 증가 하고 있다. 이러한 주조 방법은 중력주조에 비하여 용탕의 주입 및 금형에 충진을 임의로 제어하고 기계화할 수 있어 생산성 향상과 불량률 감소 및 치수정밀성 향상이 그 주 요한 장점들이다. 저온염 용융 코어 적용 복합주조기술은 일체화성형부품의 경 량화와 모듈화를 위한 핵심기반기술이다.
용융코어제조 및 특성평가의 목적으로는 고물성 용융코어재료 를 개발하여 합금과 코어사이의 최적화 방안을 세우는데 의미 가 있다. 특히 여러 개의 부품을 모듈화나 일체화시키면 복잡 한 내부 형상의 일체화 부품으로 되는 경우가 많이 발생하게 된다. 또한 품질이 다른 재료를 일체화하면 일체화된 부품은 고품질의 특성을 유지하여야 한다. 따라서 내부형상이 복잡한 고품질의 일체화 부품을 제조할 수 있는 주조기술의 개발이 요구되고 있다.
현재까지 복잡한 내부형상을 구현하기 위하여 대부분 쉘(shell)코어를 사용해 왔다. 그러나 쉘코어는 강도가 약해 취급시 쉽게 부서지거나, 결합제로 사용되는 레진 냄새와 재활용이 쉽지 않아 작업장 환경과 원가절감에 커다란 문제를 안고 있다. 또한 코어표면이 미려하지 않아 중력주조제품 생산 에만 사용되고, 고압주조시 코어표면으로 용탕침투가 일어나기 때문에 원가절감과 고품질에 유리한 다이캐스팅이나 용탕단조제 품에는 사용이 불가능하다.
한편 자동차용 주철주물제품들은 최 근 부품 경량화와 고성능화 요구에 부응하기 위해서 알루미늄 제품으로 개발되고 있다. 용융코어(fusible core)는 기존의 코어와는 다르게 융점이 270~520o C 정도인 저융점 화학염(salt)을 기본소재로 사용하며, 세라믹입자를 첨가하여 강도와 코어물성을 향상시킨다. 이들 코 어는 용융금속이 저속/고속으로 주입되어도 코어가 파괴되거나, 용융금속이 코어내부로 침투되지 않는 장점을 가진다.
이는 열 전도계수가 금형재질인 특수강의 약 1/400정도로 매우 낮아서 코어가 열적 변형이 되기 전에 용융금속의 표면응고층을 형성 시킬 수 있기 때문에 다이캐스팅을 하여도 코어의 파괴는 없 고, 코어의 복잡한 형상을 그대로 구현할 수 있다. 또한 코어 제거방법도 종래의 방법과 달리 성형제품을 코어의 용융온도보 다 20~30o C 이상의 온도에서 1~2분 가열하면 코어는 액체상 태가 되어 추출이 가능하고, 액체상태의 코어재료는 다시 재활 용이 가능하여 환경오염이나 산업폐기물이 발생되지 않는다.
본 실험에 적용한 용탕단조법(Squeeze casting)은 금형에 용 융금속을 주입한 후 유압장치를 이용하여 기계적 고압력을 용 탕에 가하여 정해진 금형공간을 충진 시킴과 동시에 50~ 200 MPa 가압하에서 응고 완료시키는 주조공정으로서 전반은 중력주조와 같고 후반은 형단조와 같아서 용탕단조법이라 칭하 며 치밀한 조직이 얻어지고 기계적 특성도 다른 주조품보다 우수한 것으로 보고[1-3]되어 있다.
현재까지의 고압응고 및 용 탕단조법에 대한 연구[4-7]들은 주로 알루미늄과 동합금의 응고 조직과 기계적 성질들에 대한 가압력과 가압조건등의 영향을 실험적으로 조사하고 그 특성들을 살펴보는 것이었다. 이러한 연구는 용탕단조에 의해 고품질제품 제조 가능성을 제시하여 실용화면에서 연구를 많이 하게 하였고 실제 기본원리가 되는 응고현상에 미치는 가압력의 영향에 관해서는 연구가 거의 없 는 실정이다.
본 연구에서는 저융점 코어를 용탕단조에 적용하여 가압력(중 력, 1000 kg/cm2 ) 증가에 따라서 용탕과 용융코어의 적합성을 평가하였다. 펀치의 가압력이 증가함에 따라서 열전달계수가 변 하는 것을 측정하였다. 가압된 용탕의 미세조직을 관찰하여 비 교 분석하였다.
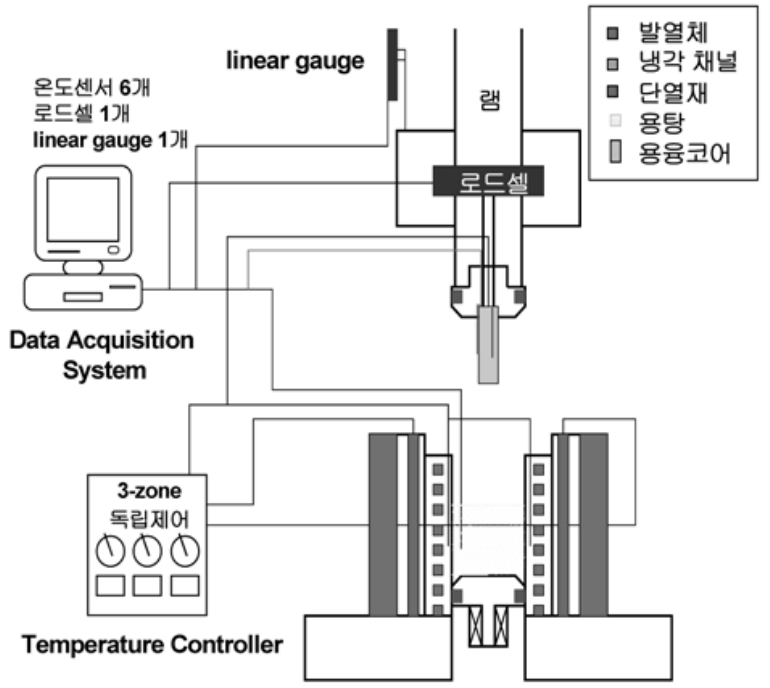
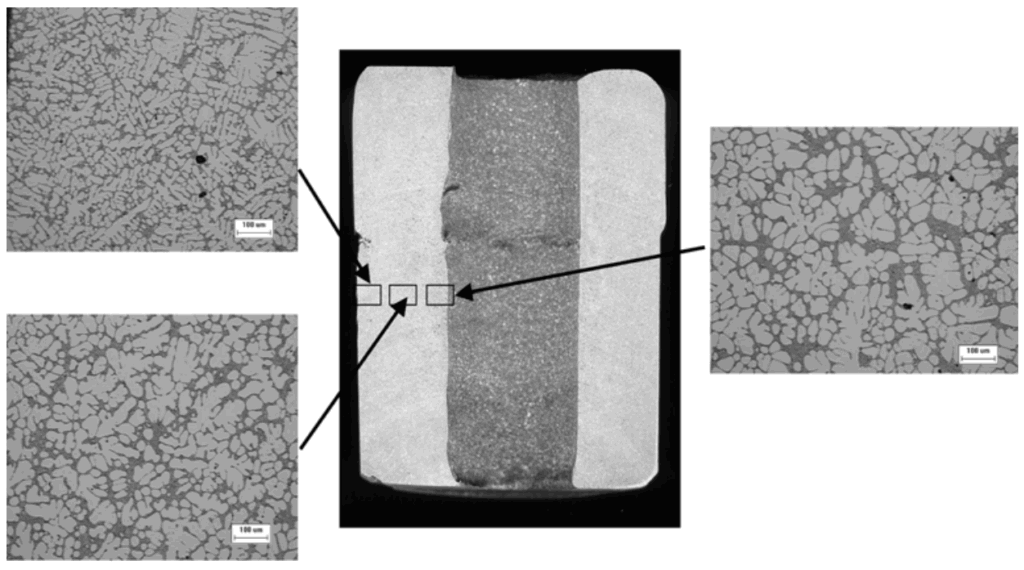
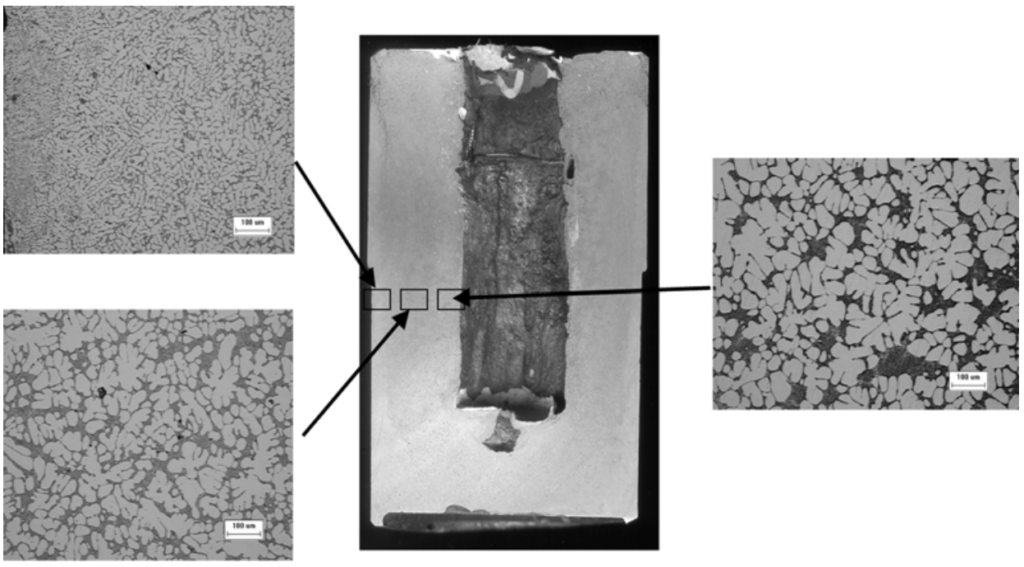
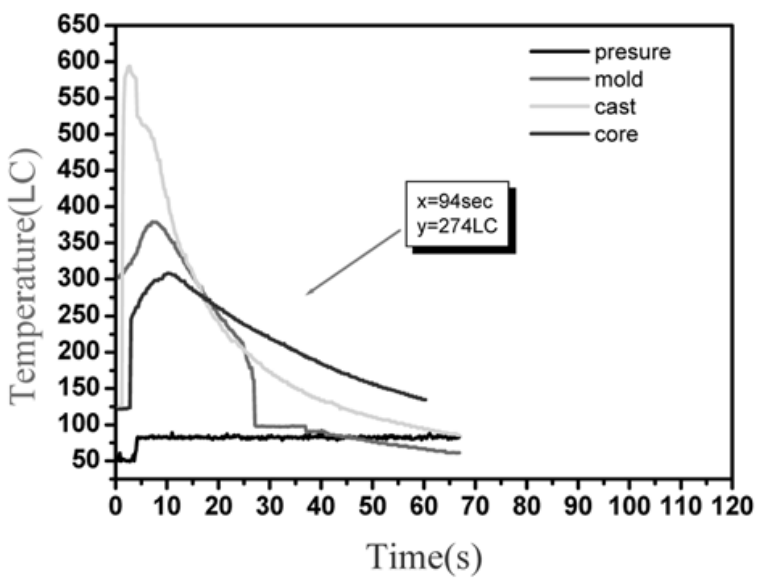
Keywords
Salt core;Squeeze casting;High pressure die casting;Net-shape forming
References
- Fatih Cay, S. Can Kurnaz, Mater. & Design, "Hot tensile and fatigue behaviour of zinc-aluminum alloys produced by gravity and squeeze casting", 26 (2005) 479-485 https://doi.org/10.1016/j.matdes.2004.07.023
- T. M. Yue, Jour. of Mater. Process. Tech., "Squeeze casting of high-strength aluminium wrought alloy AA7010", 66 (1997) 179-185 https://doi.org/10.1016/S0924-0136(96)02516-2
- Z.W. Chen, W.R. Thorpe, Mater Sci. and Eng. A, "The effect of squeeze casting pressure and iron content on the impact energy of Al-7Si-0.7Mg alloy", 221 (1996) 143-153 https://doi.org/10.1016/S0921-5093(96)10496-2
- M.A. Sava , S. Altinta , Mater. Sci. and Eng. A, "Effects of squeeze casting on the wide freezing range binary alloys", 173 (1993) 227-231 https://doi.org/10.1016/0921-5093(93)90220-9
- P.V. Evans, R. Keyte, R.A. Ricks, Mater. &Design, "Squeeze casting of aluminium alloys for near net shape manufacture", 14 (1993) 65-67 https://doi.org/10.1016/0261-3069(93)90050-6
- A Bloyce, J.C Summers, Mater. Sci. and Eng. A, "Static and dynamic properties of squeeze-cast A357-SiC particulate Duralcan metal matrix composite", 135 (1991) 231-263 https://doi.org/10.1016/0921-5093(91)90568-8
- M. R. Ghomashchi, K. N. Strafford, Jour. of Mater. Process. Tech., "Factors influencing the production of high integrity aluminium/silicon alloy components by die and squeeze casting processes", 38 (1993) 303-326 https://doi.org/10.1016/0924-0136(93)90204-J