This introductory paper is the research content of the paper ["Effect of Alloying Elements on the Thermal Conductivity and Casting Characteristics of Aluminum Alloys in High Pressure Die Casting"] published by ['Korean Institute of Metals and Materials', 'Chonbuk National University'].
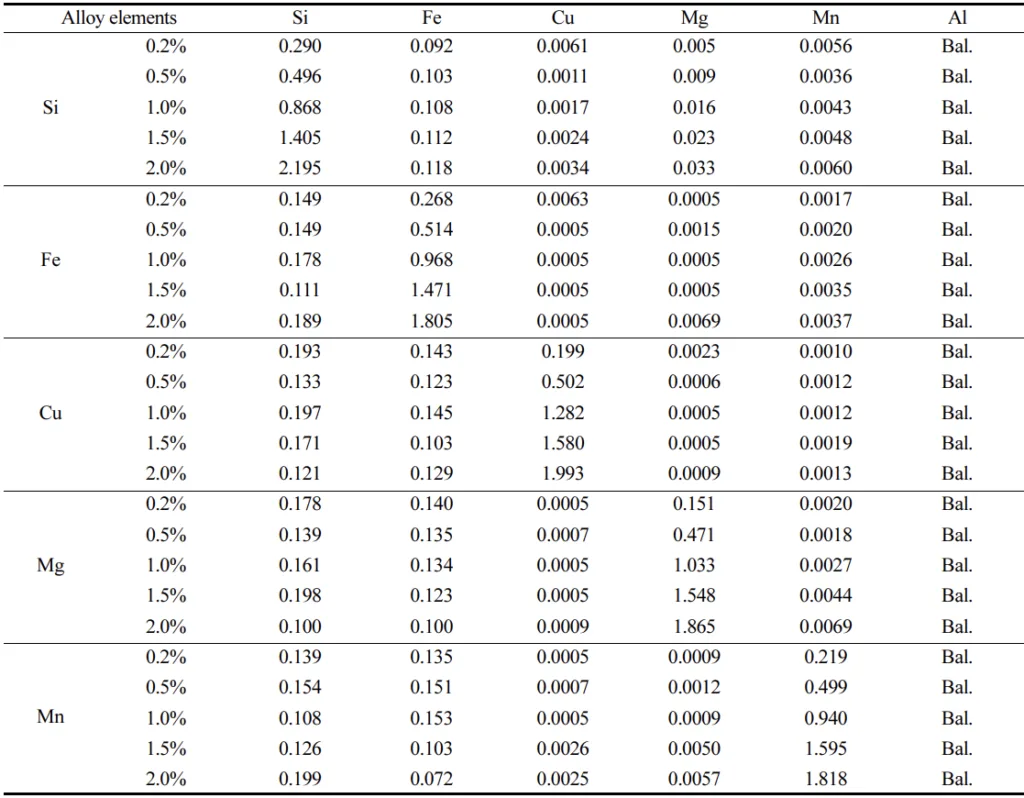
1. Overview:
- Title: Effect of Alloying Elements on the Thermal Conductivity and Casting Characteristics of Aluminum Alloys in High Pressure Die Casting (고압 다이캐스팅용 알루미늄 합금의 열전도성 및 주조성에 미치는 첨가원소의 영향)
- Author: Cheol-Woo Kim, Young-Chan Kim, Jung-Han Kim, Jae-Ik Cho, Min-Suk Oh (김철우, 김영찬, 김정한, 조재익, 오민석)
- Publication Year: 2018
- Publishing Journal/Academic Society: Korean Journal of Metals and Materials (대한금속·재료학회지)
- Keywords: thermal conductivity, heat sink, die-casting, radiation of heat
2. Abstracts / Introduction
Abstract:
High pressure die casting is one of the precision casting methods. It is highly productivity and suitable for manufacturing components with complex shapes and accurate dimensions. Recently, there has been increasing demand for efficient heat dissipation components, to control the heat generated by devices, which directly affects the efficiency and life of the product. Die cast aluminum alloys with high thermal conductivity are especially needed for this application. In this study, the influence of elements added to the die cast aluminum alloy on its thermal conductivity was evaluated. The results showed that Mn remarkably deteriorated the thermal conductivity of the aluminum alloy. When Cu content was increased, the tensile strength of cast aluminum alloy increased, showing 1 wt% of Cu ensured the minimum mechanical properties of the cast aluminum. As Si content increased, the flow length of the alloy proportionally increased. The flow length of aluminum alloy containing 2 wt% Si was about 85% of that of the ALDC12 alloy. A heat dissipation component was successfully fabricated using an optimized composition of Al-1 wt%Cu-0.6 wt%Fe-2 wt%Si die casting alloy without surface cracks, which were turned out as intergranular cracking originated from the solidification contraction of the alloy with Si composition lower than 2 wt%.
Introduction
High pressure die casting is a precision casting method that involves injecting molten metal into precisely machined molds to obtain castings that perfectly match the desired shape. The die casting process is highly productive, enabling mass production of precise and complex shaped components in a short time [1,2]. Recently, in various fields such as automotive and electronics industries, heat generation issues due to increased efficiency and integration of components have become significant. Therefore, the development of components with excellent heat dissipation characteristics is highly demanded to prevent product efficiency degradation and lifespan reduction due to temperature rise in components.
3. Research Background:
Background of the Research Topic:
Recently, heat generation issues have become prominent in the automotive and electronics industries due to the increasing efficiency and integration of components. To prevent product efficiency degradation and lifespan reduction caused by temperature increases, the development of components with excellent heat dissipation characteristics is required. Generally, for components requiring heat dissipation, casting methods using high thermal conductivity wrought aluminum alloys or aluminum with purity of 99 wt% or higher are applied.
Status of Existing Research:
Die-casting Al alloys tend to have lower thermal conductivity due to the small amounts of alloying elements added to improve the castability of the alloy or the physical and chemical properties of the product. For example, Si is added to improve melt fluidity and castability [4], Cu and Mn are added to improve strength and machinability [5-7], and Fe is added to improve die soldering resistance [8]. However, as the amount of these minor alloying elements added to Al increases, the thermal properties of the product deteriorate.
Necessity of the Research:
To develop Al alloys suitable for die casting and exhibiting excellent heat dissipation properties, it is essential to optimize the composition of minor alloying elements. Existing ALDC12 alloy has a thermal conductivity of 99 W/m·k, which is very low compared to pure aluminum (234 W/m·k), making it unsuitable for manufacturing heat dissipation components with existing alloy compositions and manufacturing methods [3]. Therefore, the development of high thermal conductivity Al alloys suitable for high pressure die casting is urgently needed.
4. Research Purpose and Research Questions:
Research Purpose:
The purpose of this study is to evaluate the effect of alloying elements on the thermal conductivity of high pressure die casting Al alloys and to derive the optimal alloy composition for developing Al alloys with excellent heat dissipation properties.
Key Research:
In this study, the effects of varying the composition of added alloying elements on thermal conductivity and fluidity were investigated. Furthermore, heat dissipation components for automotive audio equipment were manufactured using the derived optimal alloy composition, and their performance was comparatively evaluated.
5. Research Methodology
Research Design:
This research is designed as an experimental study to analyze the thermal conductivity, fluidity, mechanical properties, and microstructure of Al alloys while varying the content of added elements (Si, Fe, Cu, Mg, Mn).
Data Collection Method:
- Composition Analysis: Chemical composition analysis of alloys using a Spark emission spectrometer (QUANTRON).
- Thermal Conductivity Measurement: Thermal conductivity measurement using a thermal property analyzer (LFA 477, Netzsch) employing the Laser flash technique.
- Microstructure Observation: Microstructure, precipitates, and microstructural changes analysis using optical microscopy and FE-SEM (JSM-7000F, JEOL) with EDS.
- Mechanical Property Evaluation: Tensile strength and elongation measurement using a tensile tester (AG-IS, SHIMADZU) according to ASTM E8M standards.
- Fluidity Measurement: Measurement of the length of the cast specimen after die casting using a serpentine mold.
Analysis Method:
Thermal conductivity was calculated using measured thermal diffusivity, specific heat, and density. The changes in thermal conductivity, fluidity, mechanical properties, and microstructure were analyzed according to the type and content variation of the added elements. Image analysis was used to measure the area fraction of Al-Cu precipitates.
Research Subjects and Scope:
The research subjects of this study are Al alloys with various additive elements (Si, Fe, Cu, Mg, Mn) each added in amounts of 0.2~2 wt%.
6. Main Research Results:
Key Research Results:
- Mn: Mn was found to significantly deteriorate the thermal conductivity of Al alloys.
- Cu: As the Cu content increased, the precipitation of Al₂Cu intermetallic compounds increased, and the tensile strength increased proportionally. A minimum mechanical property was secured with the addition of 1 wt% Cu.
- Si: As the Si content increased, the fluidity of the Al alloy increased proportionally. The flow length of the Al alloy with 2 wt% Si was about 85% of that of the ALDC12 alloy.
- Optimal Alloy Composition: A heat dissipation component without surface cracks was successfully fabricated using a die casting alloy with an optimized composition of Al-1 wt%Cu-0.6 wt%Fe-2 wt%Si.
Analysis of presented data:
- Thermal Conductivity: Figure 1(d) shows that thermal conductivity decreases as the content of additive elements increases. In particular, Mn addition had the greatest impact on reducing thermal conductivity. The change in thermal conductivity with Si content variation is shown in Figure 8(b), indicating a tendency for thermal conductivity to decrease as Si content increases.
- Mechanical Properties: Figure 2 shows that tensile strength increases and elongation decreases with increasing Cu content.
- Fluidity: Figure 7 shows that flow length increases with increasing Si content. A flow length of about 85% compared to ALDC12 was observed with 2 wt% Si addition.
- Microstructure: Figures 3, 4, and 5 show that Al-Cu precipitates increase with increasing Cu content.
Figure Name List:
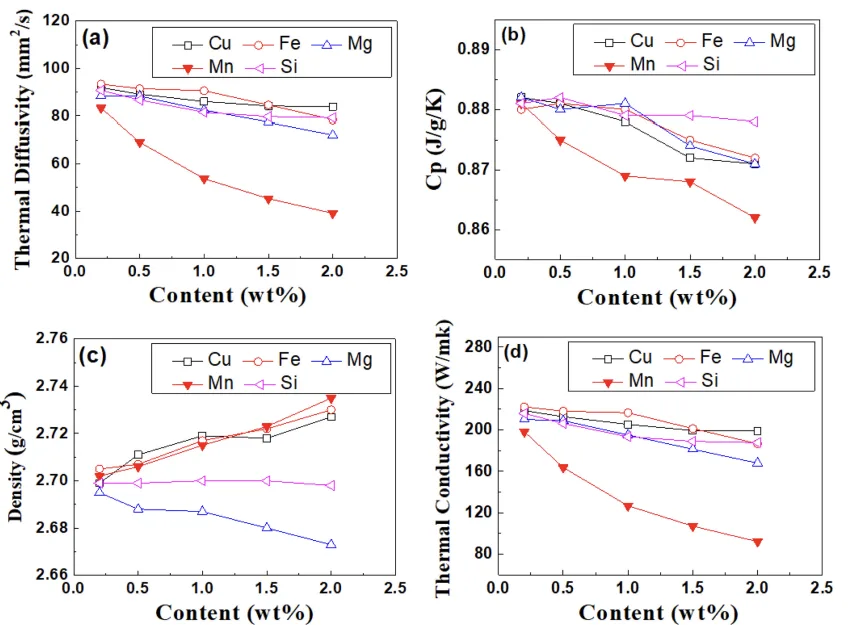
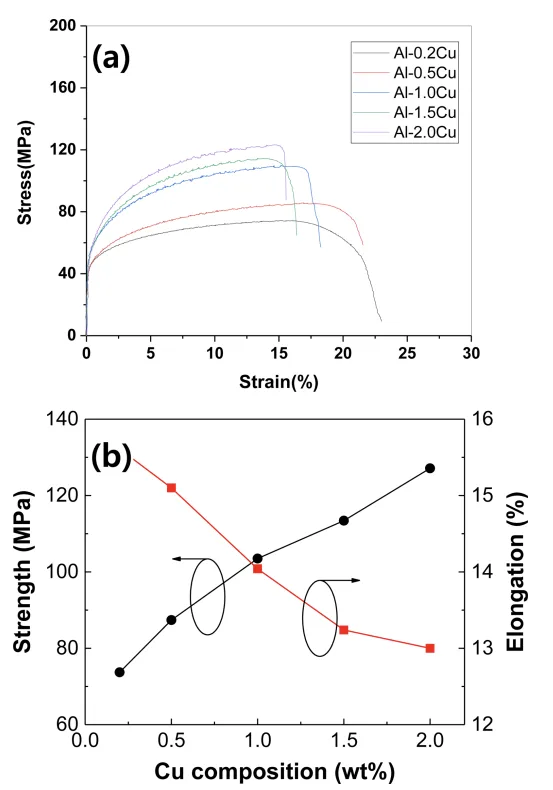
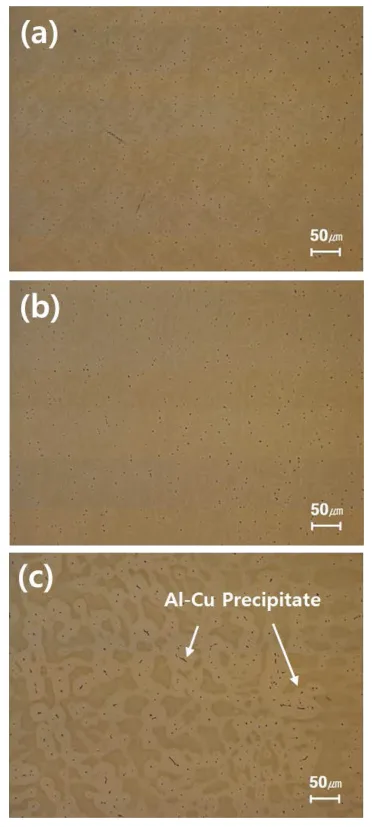
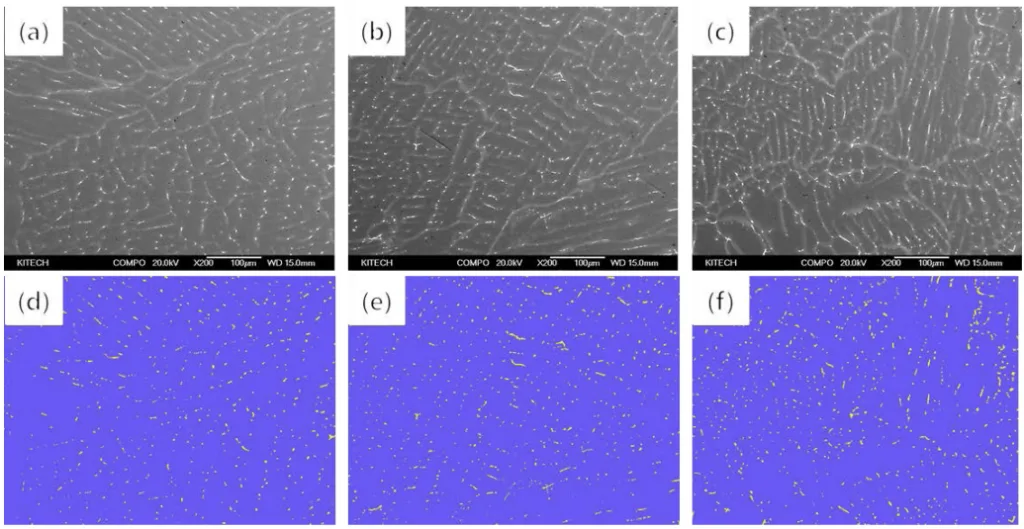
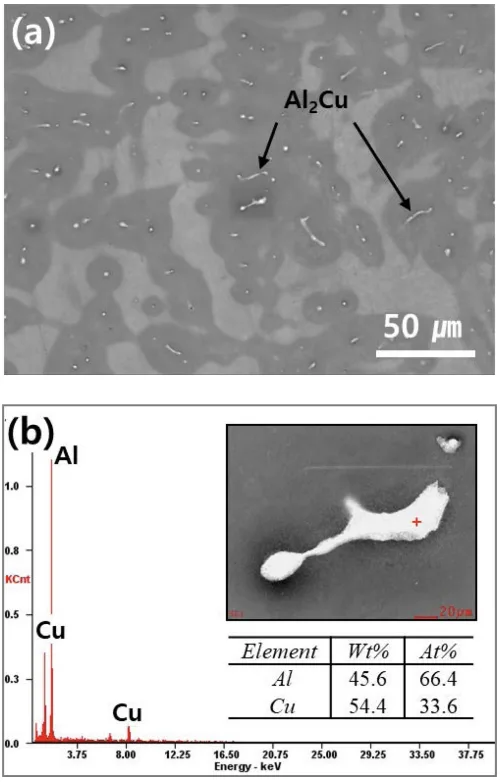
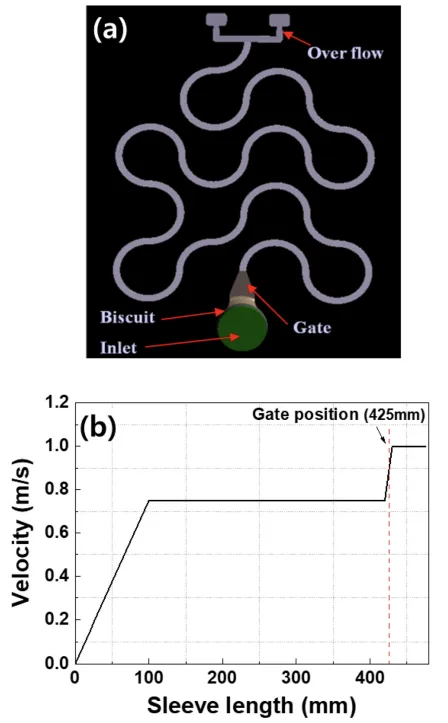
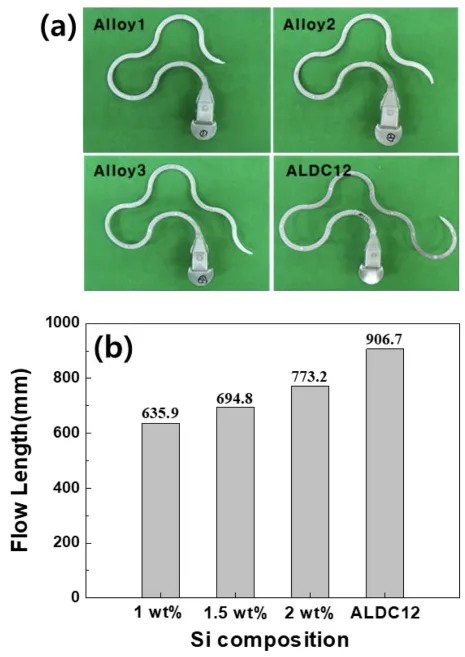
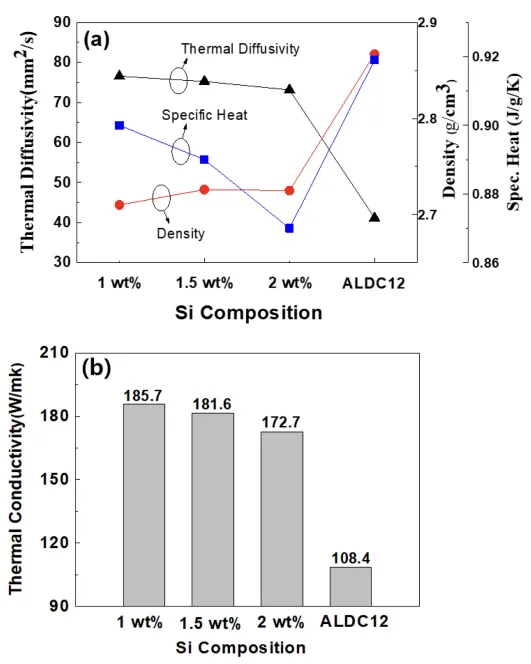
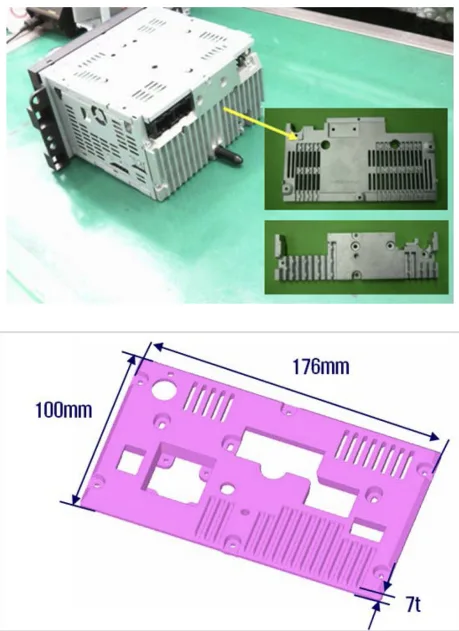
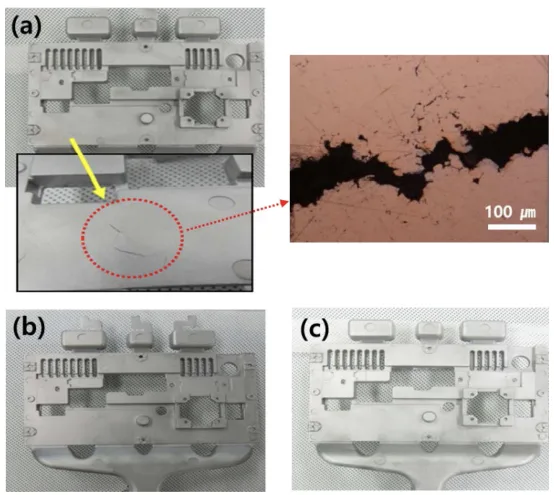
- Fig. 1. Thermal properties of alloys with different additive metals; (a) Thermal diffusivity, (b) Specific heat, (c) Density, (d) Thermal conductivity.
- Fig. 2. (a) Stress-strain curves and (b) change of tensile strength and elongation according to composition of Cu.
- Fig. 3. Microstructure of Al alloys with different Cu composition; (a) Al-1.0wt%Cu, (b) Al-1.5wt%Cu, (c) Al-2.0wt%.
- Fig. 4. SEM image of (a) Al-1wt%Cu, (b) Al-1.5wt%Cu and (c) Al-2wt%Cu (x200) and image analysis data of (d) Al-1wt%Cu, (e) Al-1.5wt%Cu and (f) Al-2wt%Cu (×200).
- Fig. 5. (a) SEM image and (b) EDS results of Al alloy with 2 wt% Cu.
- Fig. 6. (a) Schematic of metal mold and (b) injection speed profile for fluidity test.
- Fig. 7. Results of die casting fluidity test; (a) Schematic of die cast specimens, (b) flow length.
- Fig. 8. (a) Thermal properties and (b) Thermal conductivity of alloys with different additive metals.
- Fig. 9. Die cast heat sink component (car audio heat sink).
- Fig. 10. Diecast car audio heat sink component with various alloy compositions; (a) Al-1.0 wt%Cu-0.6 wt%Fe-1.5 wt%Si), (b) Al-1.0 wt%Cu-0.6 wt%Fe-2.0 wt%Si, (c) Al-2.5 wt%Cu-0.8 wt%Fe-11 wt%Si-0.2 wt%Mg-0.3 wt%Mn (ALDC12).
7. Conclusion:
Summary of Key Findings:
In this study, the effects of alloying elements on the thermal conductivity and castability of high pressure die casting Al alloys were evaluated, and the following conclusions were drawn. Mn significantly reduces the thermal conductivity of Al alloys, Cu increases tensile strength, and Si improves fluidity. The optimal alloy composition derived was Al-1.0 wt%Cu-0.6 wt%Fe-2.0 wt%Si, which exhibits more than twice the thermal conductivity and about 85% fluidity compared to ALDC12 alloy.
Academic Significance of the Study:
This study provides systematic data on the effects of alloying elements on thermal conductivity and castability in high pressure die casting Al alloys, expanding the academic foundation for designing high thermal conductivity die casting alloys.
Practical Implications:
The Al-1.0 wt%Cu-0.6 wt%Fe-2.0 wt%Si alloy developed in this study can be utilized for manufacturing die casting components requiring high heat dissipation performance, such as heat sinks for automotive audio equipment, and can contribute industrially to the development of high-efficiency heat dissipation components.
Limitations of the Study and Areas for Future Research:
This study evaluated the effects of alloying elements within a specific composition range. Further optimization research on alloying elements and process conditions is needed for even superior die casting. In addition, further research on the reliability and durability of the developed alloy is required.
8. References:
- K. P. Keller, IEEE, 10.1109/ITHERM, 112 (1998).
- K. Keller, IEEE, 10.1109/IEMTE, 113 (1998).
- J. R. Davis, ASM, 10.1361/autb, 351 (2001).
- C. R. Loper, Jr., AFS Trans. 533 (1992).
- C. Mascre, Fonderie, 108, 4330 (1995).
- H. Y. Kim, S. W. Han, and H. M. Lee, Mater. Lett. 60, 1880 (2006).
- S. S. Sreeja Kumari, R. M. Pillai, T. P. D. Rajan, and B. C. Pai, Mater. Sci. & Eng. A 460-461, 561 (2007).
- L. A. Naraynan, F. H. Samuel, and J. E. Gruzleski, Metall. Mater. Trans. A 26A, 2161 (2004).
- W. J. Parker, R. J. Jenkins, C. P. Butler, and G. L. Abbott, J. Appl. Phys. 32, 1679 (1961).
- R. D. Cowan, J. Appl. Phys. 34, 926 (1963).
- R. A. Goncalves, Procedia Manuf. 1, 683 (2015).
- L. F. Mondolfo, “Aluminum Alloys: Structure and Properties", Butter Worths (1976).
- H. J. Kim, C. M. Cho, and C. Y. Jeong, J.KFS, 29, 169 (2009).
- D. K. Lews, "Silicon and Its Effect on Fluidity of Aluminum Alloys.", A.S.&R. Co., Inc, Data Sheet.
9. Copyright:
- This material is "Cheol-Woo Kim, Young-Chan Kim, Jung-Han Kim, Jae-Ik Cho, Min-Suk Oh"'s paper: Based on "Effect of Alloying Elements on the Thermal Conductivity and Casting Characteristics of Aluminum Alloys in High Pressure Die Casting".
- Paper Source: DOI: 10.3365/KJMM.2018.56.11.805
This material was created to introduce the above paper, and unauthorized use for commercial purposes is prohibited.
Copyright © 2025 CASTMAN. All rights reserved.