모터 성능 향상을 위한 다이캐스트 구리 로터
Authors
J.G. CowieCopper Development Association Inc., New York, NY, USAD.T. BrenderCopper Development Association Inc., New York, NY, USA
Abstract
Aluminum has been the common conductor material for the squirrel cage of the induction motor largely because of ease of manufacturing by pressure die casting. Short die life in die casting the higher melting copper resulting in high production cost has prevented the copper rotor from attaining a place in integral horsepower motors. Because of its higher electrical conductivity, copper in the rotor reduces energy losses. Data presented in this paper show that in addition to reduced rotor losses and improvement in overall electrical energy efficiency, an important derivative benefit is reduced motor operating temperature which will lead to longer motor life and reduced maintenance costs in high duty cycle motors. Overall motor losses as measured in laboratory dynamometer tests using IEEE Specification 112B were reduced by 14 to 23% in copper rotors compared to aluminum counterparts. Other performance characteristics of copper rotor equipped motors are described. A short summary of tests of high temperature die materials and their use in die casting copper is presented.
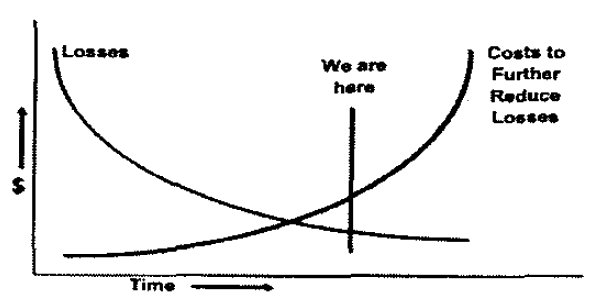
Keywords
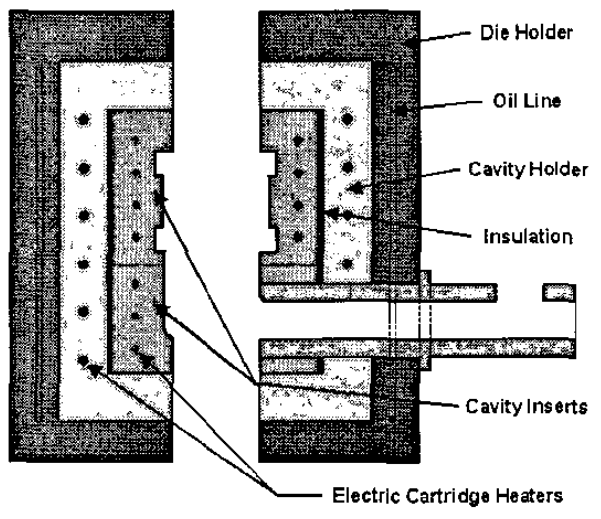
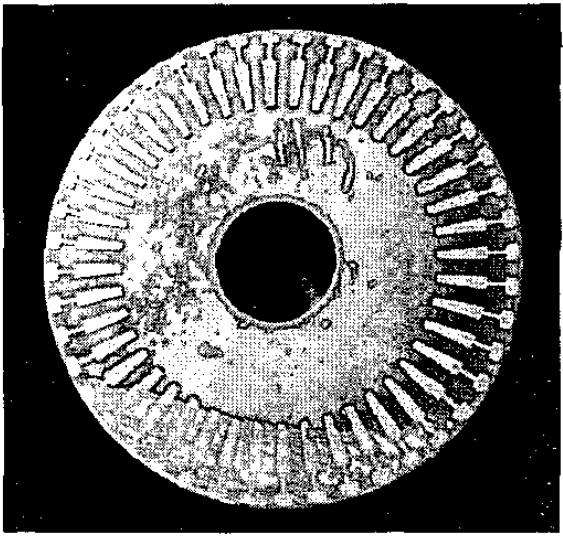
- IEEE Keywords
- INSPEC: Controlled Indexing
- INSPEC: Non-Controlled Indexing
References
1.D. T. Peters, J. G. Cowie, E. F. Brush, Jr. and S. P. Midson, "Advances in Pressure Die Casting of Electrical Grade Copper," Amer. Foundry Society 2002 Congress Paper No. 02-002, Kansas City, Mo.
Show in Context Google Scholar
2.D. T. Peters, J. G. Cowie, E. F. Brush, Jr. and S. P. Midson, "Use of High Temperature Die Materials and Hot Dies for High Pressure Die Casting Pure Copper and Copper Alloys," Trans. of the North Amer. Die Casting Assoc. 2002 Die Casting Congress, Rosemont, Il.
Show in Context Google Scholar
3.DOE/CS-0147 - U. S. Department of Energy, Classification and Evaluation of Electric Motors and Pumps, February, 1980.
Show in Context Google Scholar
4.J. C. Benedyk, D. J. Moracz, and J. F. Wallace, "Thermal Fatigue Behavior of Die Materials for Aluminum Die Castings," Trans. of SDCE, Paper No. 111, 1970.
Show in Context Google Scholar
5.E. A. Herman, J. F. Wallace and A. A. Machonis, Copper Alloy Pressure Die Casting, p 52, International Copper Research Assoc., Inc. 1975.
Show in Context Google Scholar
6.H. H. Doehler, Die Casting, pp 163-165, New York: McGraw-Hill Book Co., Inc. 1951.
Show in Context Google Scholar