Tülay Hançerlioğlu 1*
1 R&D Department Nemak İzmir Döküm San.A.Ş.
- tulay.hancerlioglu@nemak.com
- Orcid: 0000-0003-2373-4405
Received: 6 December 2021
Accepted: 1 June 2022
DOI: 10.18466/cbayarfbe.1033177
Abstract
For creating complex geometric shapes in the cast part, salt was used to produce core instead of sand
which is thermo-chemical or chemical process using resin as a binder. In salt core casting, the efficiency
will be increased by reducing the core gas-induced errors in the part. The harmful effect on the
environment will be reduced with the absence of odor and smoke from the core gas. Using water in salt
core breaking instead of mechanical impact and vibration during sand core breaking will bring benefits
such as eliminating the noise source and using less energy. By eliminating the dust generated during sand
core breaking, its harmful effects on the environment will be reduced. Since the salt core can be dissolved
in water and removed from the piece without any residue, there will be no problem of sand remaining in
the sand core from time to time.
주조 부품에 복잡한 기하학적 모양을 만들기 위해 열화학 또는 수지를 바인더로 사용하는 화학 공정인 모래 대신 소금을 사용하여 코어를 생성했습니다. 염심 주조에서 부품의 코어 가스로 인한 오류를 줄임으로써 효율성이 증가합니다. 코어 가스에서 냄새와 연기가 없어 환경에 대한 유해한 영향이 줄어듭니다. 샌드 코어 파쇄 시 기계적 충격 및 진동 대신 염심 파쇄에 물을 사용하면 소음원을 제거하고 에너지를 덜 사용하는 등의 이점이 있습니다. 샌드 코어 파쇄시 발생하는 먼지를 제거하여 환경에 대한 유해한 영향을 줄입니다. 염심은 물에 용해되어 잔류물 없이 조각에서 제거될 수 있으므로 때때로 모래심에 모래가 남아 있는 문제가 없습니다.
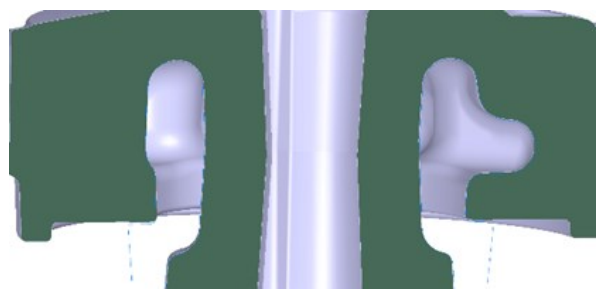
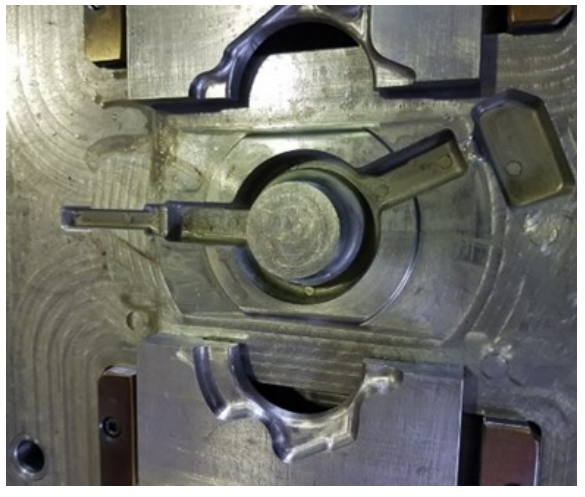
for salt core.
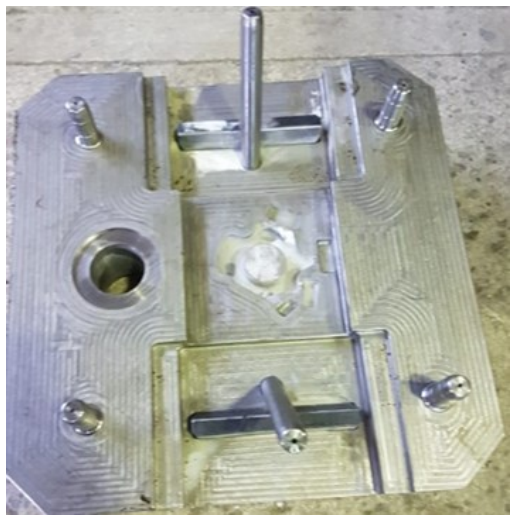
manufactured for salt core
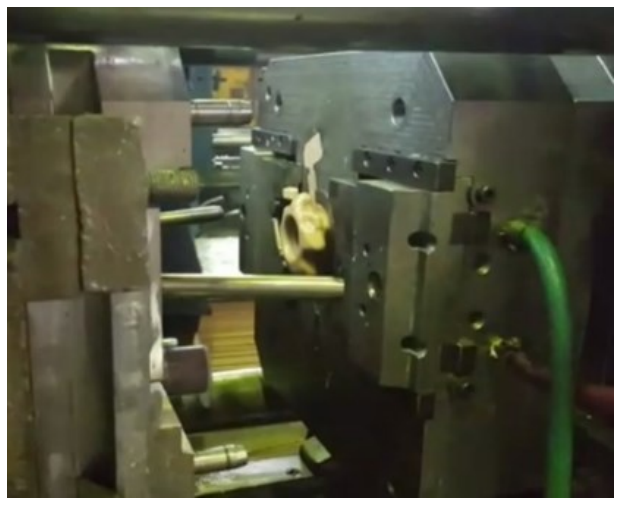
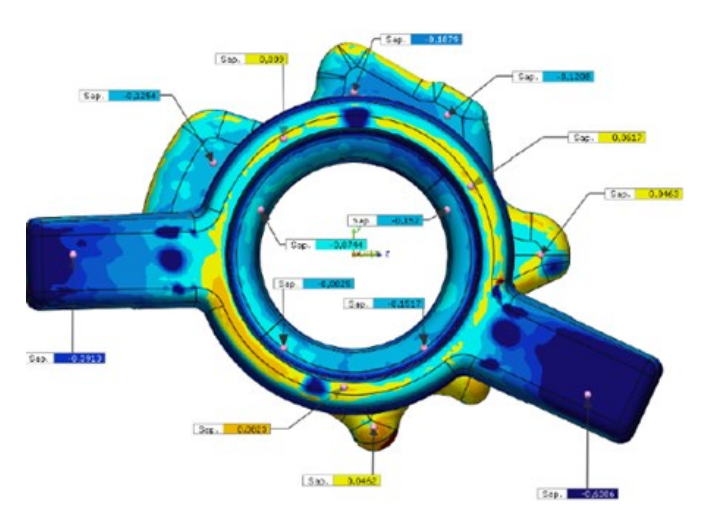
data model.
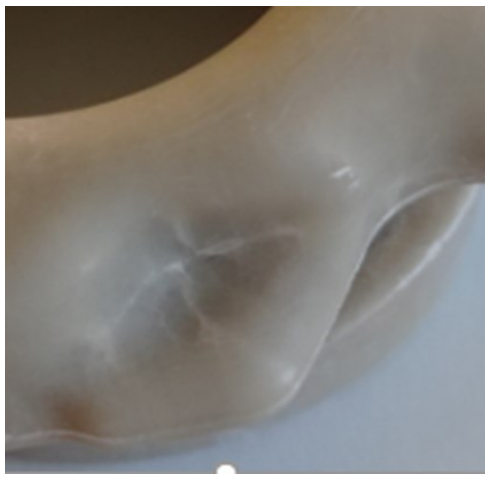
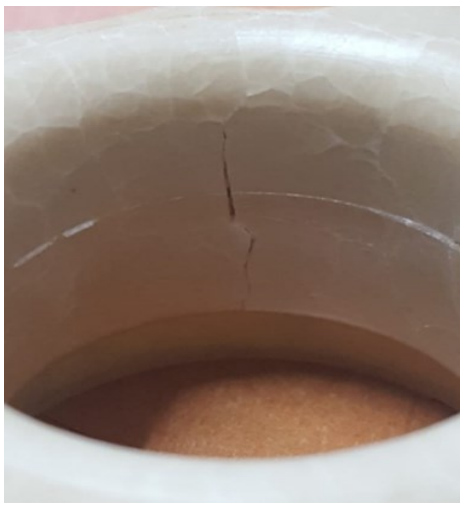
visible with eye control.
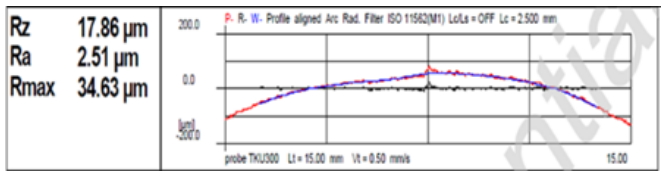
part with a salt core.
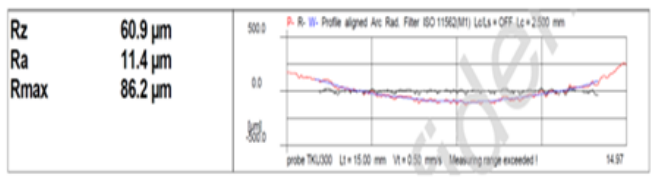
part with a 60 AFS sand core.
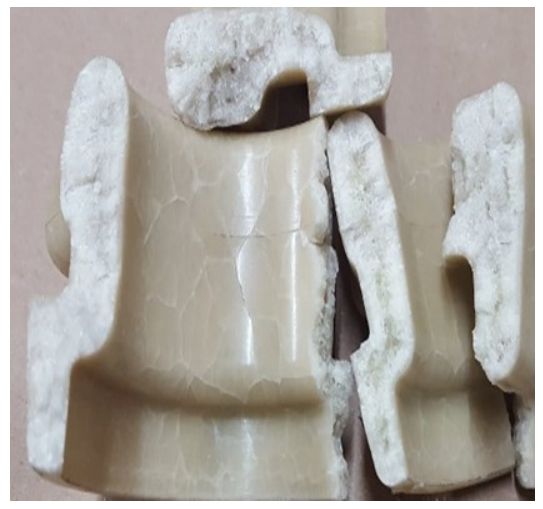
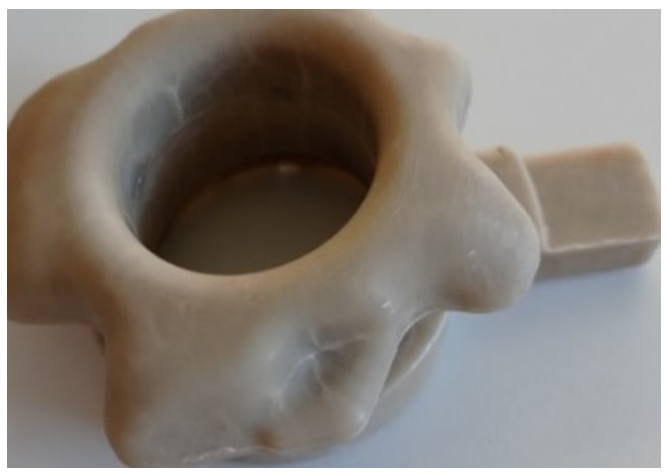
and short time.
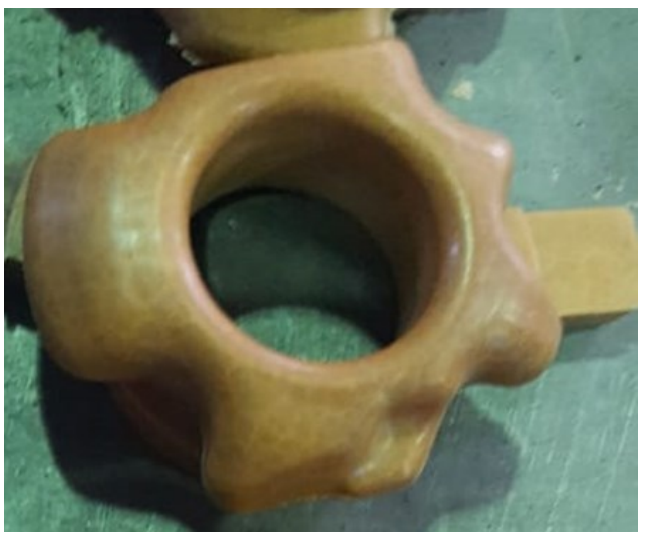
and long time.
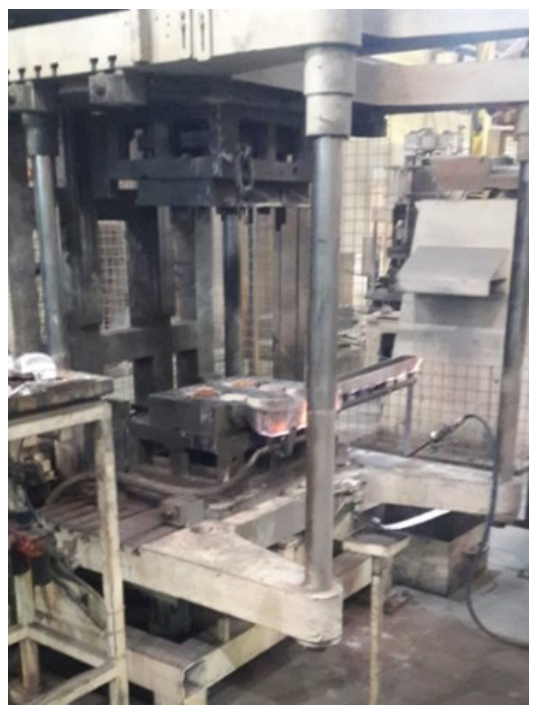
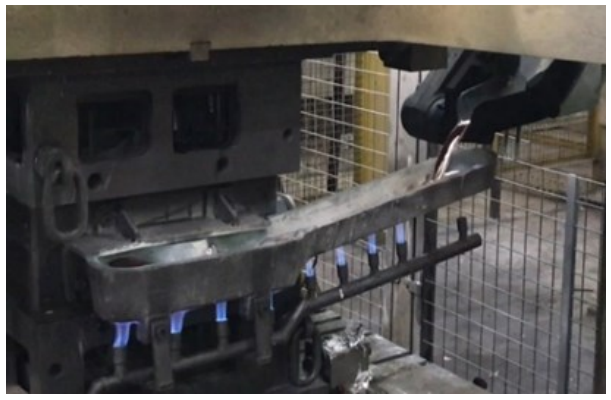
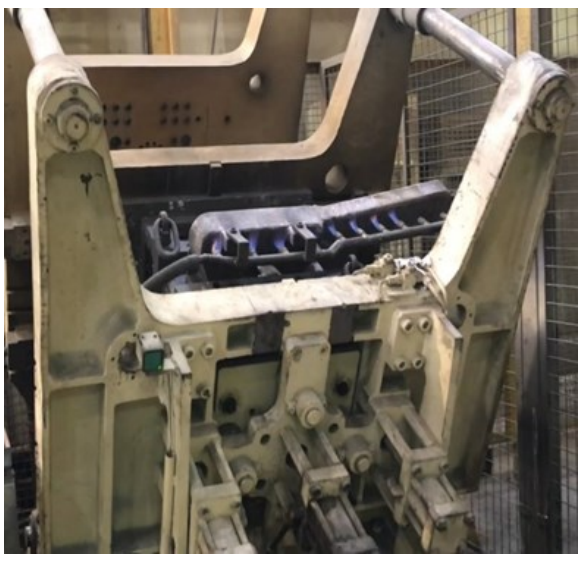
degrees.

out of the casting mold.
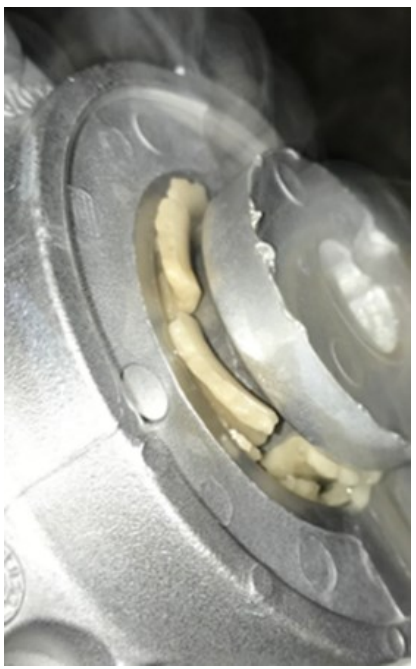
the cast part.
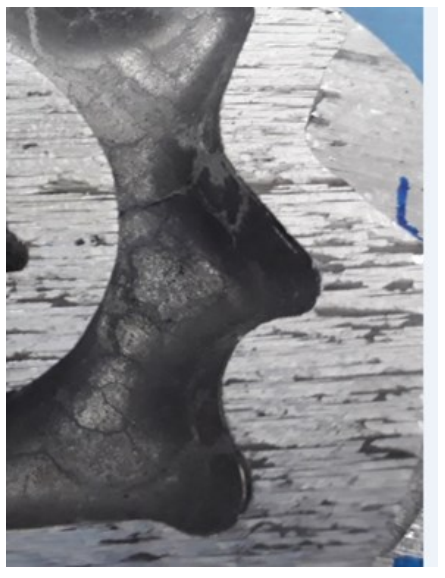
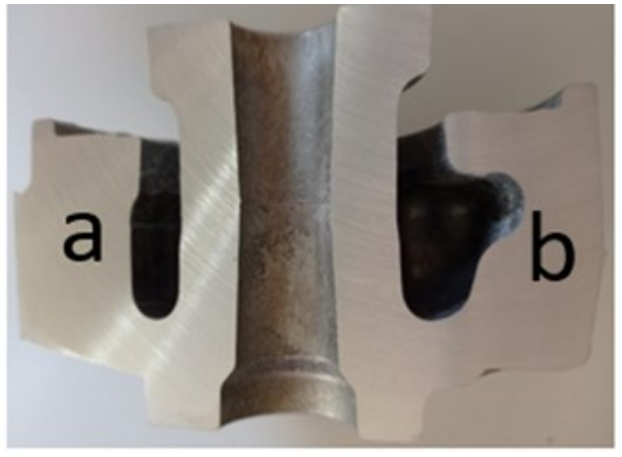
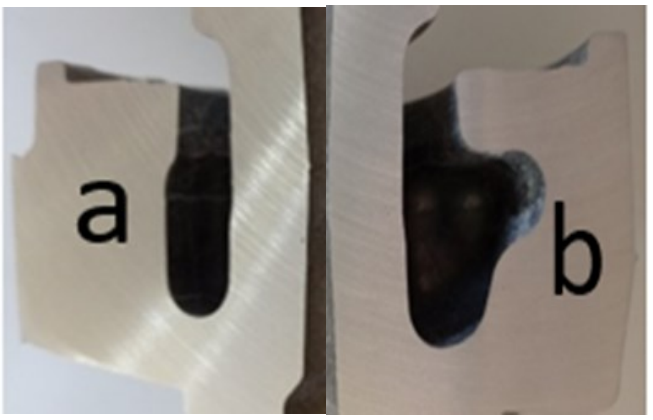
References
[1]. Brůna, M., Sládek, A. & Kucharčík, L. (2012). Formation of
porosity in Al-Si alloys. Archives of Foundry Engineering. 12(1), 5-
- DOI: 10.2478/v10266-012-0001-5.
[2]. Lichý, P., Bednářová, V. & Elbel, T. (2012). Casting routes for
porous metals production. Archives of Foundry Engineering. 12(1),
71-74. DOI: 10.2478/v10266-012-0014-0.
[3]. Dańko, J., Dańko, R. (2009). Theoretical and technological
aspects of the production processes of foundry cores blown In 50.
Konferencji i Krystalizacja Metali (pp. 71-86). Katowice – Gliwice,
Poland: Polska ademia Nauk, Komisja Odlewnictwa. ISBN: 978-
83-929266-0-3. (in Polish).
[4]. Fuchs, B., Eibisch, H. & Körner, C. (2013). Core viability
simulation for salt core technology in high – pressure die casting.
International Journal of Metalcasting. 7(3), 39-45. ISSN: 1939-5981
[5]. Stingl, P., & Shiller, G. (2009). Gichte und rückstandfreie
Entkernung – Salzkerne für den Aluminiumguss. GiessereiErfahrungsaustausch. 6, 4-8.
[6]. Adámková, E., Jelínek, P., & Študentová, S. (2013).
Application of cooking salts in manufacture of water soluble cores
for high pressure die.Materials and technology. 61(11-12), 689-693.
ISSN: 1580-2949, 1580-3414.
[7]. P. Jelínek, E. Adámková “ Lost Cores for High-Pressure Die
Casting” Department of Metallurgy and Foundry Engineering,
VŠB-Technical University of Ostrava DOI:10.2478/afe-2014-0045.
[8]. P. Jelínek, E. Adámková , F. Mikšovský, J. Beňo Advance in
Technology of Soluble Cores for Die Castings, Department of
Metallurgy and Foundry, VŠB – Technical University of Ostrava
ISSN (1897-3310) Volume 15 Issue 2/2015 29-34.
[9]. Eliska Adámková, Petr Jelínek, Jaroslav Beòo Frantiek
Mik{ovský, Water-Soluble Cores-Verifying Development Trends,
V[B-Technical University of Ostrava, Faculty of Metallurgy and
Materials Engineering, Department of Metallurgy and Foundry,
ISSN 1580-2949 MTAEC9,49(1)61(2015).
Celal Bayar University Journal of Science
Volume 18, Issue 2, 2022, p 141-147
Doi: 10.18466/cbayarfbe.1033177 T. Hançerlioğlu
147
[10]. Mr. Vijaykumar A. Radadiya, Dr. Komal G. Dave, Mr.
Kalpeshkumar R. Patel, Design and Analysis of Salt Core for a
Casting of Alüminium Alloys Core casting, International Journal
Of Advance Engineering and Research Development, Volume
2,Issue 3-2015.
[11]. Jun Yaoka wa, Daisuke Miura, Koichi Anzai1, Youji Ya mada
and Hiroshi Yoshii, “Strength of Salt Core Composed of Alkali
Carbonate and Alkali Chloride Mixtu res Made by Casting” Journal
of Technique Mate rials Transactions, Vol. 48, No. 5 (2007) pp.
1034 to 1041,Japan Foundry Engineering Society.
[12]. Petr Jelinek, Frantisek Miksovsky, Jaroslav Beoo, Eliska
Adamkova, “ Development of Foundry Cores Based On Inorganic
Salts” MTAEC9, 47(6)689(2013), ISSN 1580-2949.
[13]. Bühler AG: Lost Core - An Industrial Process Path for HighQuality Salt Cores. https://www.foundry-planet.com (Date of
access: 25.06.2021)