This introductory paper is the research content of the paper ["Development of a New High Fluidity Zinc Die Casting Alloy"] published by [Conference Paper September 2010].
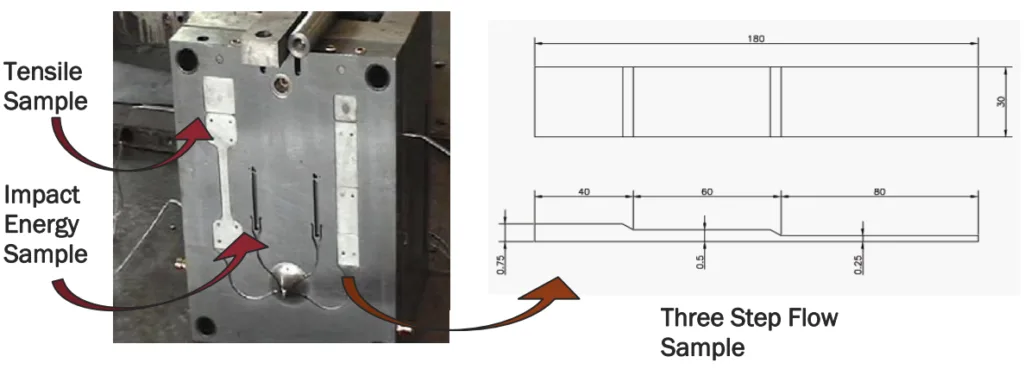
![Figure 9: Aluminum extruded 2D heat sinks (top left), aluminum machined heat sink (top
right), zinc cast heat sinks (bottom left) [8], and new generation zinc cast heat sink (bottom
right).](https://castman.co.kr/wp-content/uploads/image-1396-png.webp)
1. Overview:
- Title: Development of a New High Fluidity Zinc Die Casting Alloy
- Author: Artur .B. Filc, Y.H. Liu, K. Zhang, N.-Y. Tang, Frank E. Goodwin
- Publication Year: 2010
- Publishing Journal/Academic Society: Conference Paper
- Keywords: Zinc die casting alloy, High fluidity, Thin wall, Corrosion resistance, Mechanical properties
2. Abstracts / Introduction
ABSTRACT
A new hot chamber zinc die casting alloy containing 4.5%AI, 0.01%Mg and 0.03%Cu was developed at Teck's Product Technology Centre (PTC) in Mississauga, Ontario. It was found that this alloy possesses superior fluidity and mechanical properties comparable to those of Alloy 7. This high fluidity (HF) alloy was especially tested for intergranular corrosion in humid environment and corrosion resistance using the ASTM B117 salt spray procedure. It was demonstrated that this alloy could be used in many thin wall applications. The HF alloy can replace aluminum and magnesium die casting alloys in some applications and is creating new applications where ultra thin walls are required. The HF alloy is currently being tested for creep strength.
INTRODUCTION
In 1929, the New Jersey Zinc Company developed ZAMAK Alloy 7 which was designed for use in the casting of thin wall parts. Until now, only Alloy 7 was available for designers when a high fluidity zinc alloy was required. A constantly increasing market for thin wall applications and the necessity to conserve energy initiated a research program at Teck's Product Technology Centre (PTC) to develop a new ultra high fluidity zinc alloy. The Department of Energy (DOE) Cast Metals Coalition and, more recently, the North American Die Casting Association (NADCA) sponsored the project in which an alloy containing 4.5%Al, 0.01%Mg and 0.03%Cu was developed. Subsequent industrial trials have proven the excellent casting properties of this high fluidity (HF) alloy. It has been shown that this alloy produces sound castings with 0.3 mm (0.012 in.) wall thickness and surface quality adequate for electroplating. Increased amounts of aluminum in the HF alloy compared to other ZAMAK alloys brought its composition closer to the eutectic, therefore necessitating rigorous testing of its mechanical properties. A range of alloys with different amounts of aluminum was tested to establish a correlation between aluminum content and mechanical properties.
Magnesium is added to zinc alloys to increase corrosion resistance. Low magnesium content and a lack of nickel in the HF alloy required testing of its corrosion resistance. The HF alloy was evaluated for intergranular corrosion in particular and its resistance to corrosion, using the ASTM B117 salt sprays procedure. Both tests proved an adequate corrosion resistance when compared to Alloys 3 and 5. The HF alloy has recently been specified for the production of thin wall parts. The new alloy is currently being tested for its creep properties.
3. Research Background:
Background of the Research Topic:
The research was initiated due to the "constantly increasing market for thin wall applications and the necessity to conserve energy". The existing alloy, ZAMAK Alloy 7, developed in 1929, was the only available option for high fluidity zinc alloy, highlighting a technological gap in meeting contemporary demands.
Status of Existing Research:
Prior to this study, "only Alloy 7 was available for designers when a high fluidity zinc alloy was required." This indicates a limited selection of materials for applications demanding high fluidity in zinc die casting.
Necessity of the Research:
The research was necessary to address the "constantly increasing market for thin wall applications" and the "necessity to conserve energy". Developing a new ultra-high fluidity zinc alloy was crucial to overcome the limitations of existing materials and meet evolving industrial needs.
4. Research Purpose and Research Questions:
Research Purpose:
The primary research purpose was "to develop a new ultra high fluidity zinc alloy" at Teck's Product Technology Centre (PTC). This objective was driven by the market demand for thin-wall applications and energy conservation.
Key Research:
The key research areas included:
- Fluidity: Evaluating and enhancing the fluidity of the new alloy to enable casting of thin-wall parts.
- Mechanical Properties: Rigorous testing of mechanical properties due to the increased aluminum content in the new High Fluidity (HF) alloy, bringing its composition closer to the eutectic point.
- Corrosion Resistance: Testing the corrosion resistance, particularly intergranular corrosion, due to the low magnesium content and absence of nickel in the HF alloy.
- Creep Properties: Ongoing testing of creep properties to fully characterize the new alloy's performance.
5. Research Methodology
Research Design:
The research employed an experimental design focused on alloy development and performance evaluation. This involved formulating a new zinc die casting alloy composition and subjecting it to a series of laboratory tests and industrial trials.
Data Collection Method:
- Fluidity Test: A "Ragone Fluidity Tester" was used to measure the flow distance of molten alloys, quantifying their fluidity.
- Chemical Composition Analysis: The chemical compositions of tested alloys were determined and verified using Optical Emission Spectroscopy (OES) and Inductively Coupled Plasma (ICP) techniques.
- Mechanical Property Tests: Standard tensile and impact energy tests were conducted on samples cast in a four-cavity ILZRO die. Hardness was measured using a Brinell hardness tester.
- Corrosion Tests: Intergranular corrosion testing in a humid environment and corrosion resistance testing using the ASTM B117 salt spray procedure were performed.
- Dimensional Stability Test: Blister tests and weight measurements were conducted to assess dimensional stability and blistering behavior after heat treatment.
- Stress Simulation: Mechanical stress simulation using SolidWorks 2009 Simulation Xpress was used to evaluate the structural integrity of a component cast with the HF alloy.
Analysis Method:
The collected data were analyzed through comparative methods.
- Fluidity Comparison: Flow distances of the HF alloy were compared to those of Alloy 7 and other alloys to assess the improvement in fluidity.
- Mechanical Property Comparison: Mechanical properties of the HF alloy were compared to Alloys 3 and 7 to evaluate its performance against existing alloys.
- Corrosion Resistance Comparison: Weight loss and visual inspection were used to compare the corrosion resistance of the HF alloy to Alloys 3 and 5.
- Statistical Analysis: Average weight loss in corrosion tests and weight consistency in blister tests were used to quantify and compare alloy performance.
- Simulation Results Analysis: Stress simulation results were analyzed to determine the load-bearing capacity and deformation characteristics of components cast with the HF alloy.
Research Subjects and Scope:
The research focused on the development and testing of a new high fluidity zinc die casting alloy. The scope included:
- Alloy Composition: Development of a zinc alloy containing 4.5%Al, 0.01%Mg, and 0.03%Cu.
- Comparative Alloys: Testing and comparison with existing alloys, including Alloy 3, Alloy 7, and Alloy 5, as well as A360 aluminum alloy.
- Application Focus: Emphasis on thin-wall die casting applications and potential applications in heat sinks and electronic component housings.
6. Main Research Results:
Key Research Results:
- Development of HF Alloy: A new hot chamber zinc die casting alloy with the composition 4.5%Al, 0.01%Mg, and 0.03%Cu was successfully developed.
- Superior Fluidity: The HF alloy demonstrated significantly improved fluidity, exhibiting "40% better fluidity than Alloy 7" in Ragone Fluidity Tester experiments.
- Comparable Mechanical Properties: The HF alloy showed mechanical properties "comparable to those of Alloys 3 and 7", with the exception of impact strength at higher aluminum levels. Specifically, tensile and yield strength were maintained, while impact strength was observed to decrease slightly at 4.6%Al.
- Adequate Corrosion Resistance: Corrosion tests, including ASTM B117 salt spray and humid environment exposure, indicated "adequate corrosion resistance when compared to Alloys 3 and 5."
- Thin Wall Casting Capability: Industrial trials confirmed the HF alloy's ability to produce "sound castings with 0.3 mm (0.012 in.) wall thickness" and surface quality suitable for electroplating.
- Dimensional Stability: Blister tests indicated that parts cast with the HF alloy exhibited "more consistent weight" and less surface blistering compared to Alloy 5 after heat treatment.
- Application Potential: The HF alloy was successfully applied in the production of thin-wall components, including cellular phone covers and heat sinks, demonstrating its practical applicability.
Analysis of presented data:
- Fluidity Tests (Figure 2): Alloy II (4.48%Al, 0.006%Mg and 0.013%Cu) showed the highest average flow distance (443.5 mm), indicating superior fluidity compared to Alloy 7 (315.7 mm) and other tested alloys.
- Mechanical Properties (Table 4): The HF alloy exhibited a tensile strength of 40 ksi (276 MPa) in as-cast condition and 34 ksi (234 MPa) in aged condition. Yield strength was 35 ksi (241 MPa) as-cast and 29 ksi (200 MPa) aged. Impact energy was 28 ft-lb (38 Joules) as-cast and 21 ft-lb (28 Joules) aged.
- Corrosion Resistance (Table 6): Weight loss in salt spray tests for HF alloys (4.41%Al and 4.54%Al) was slightly higher than Alloy 3, but still within acceptable limits, indicating adequate corrosion resistance.
- Stress Simulation (Figure 7): Simulation results showed that a force of 1112 N (250 lb) would cause permanent deformation in a Communion host dispenser made from the HF alloy, providing data for structural design considerations.
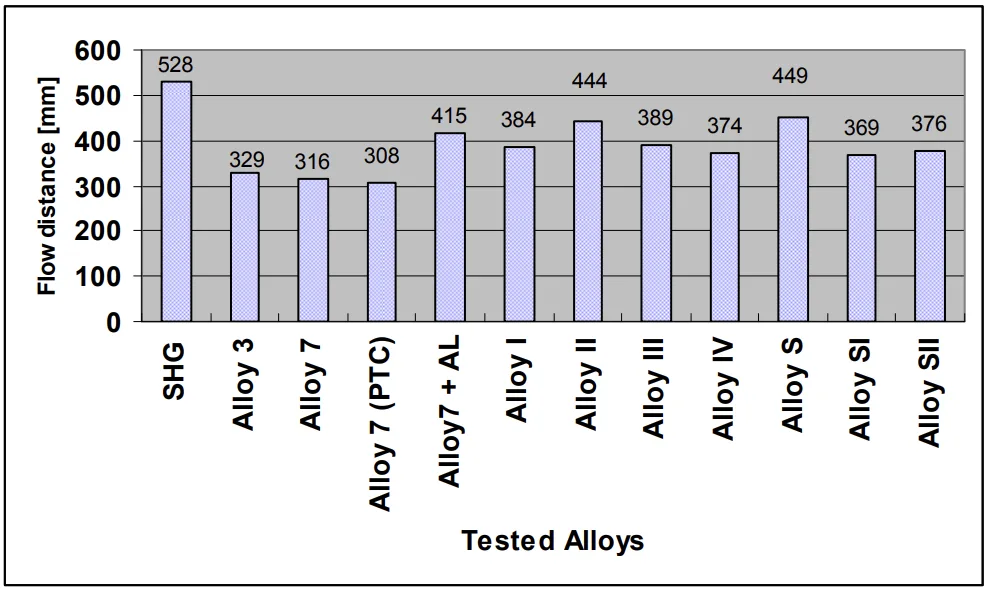
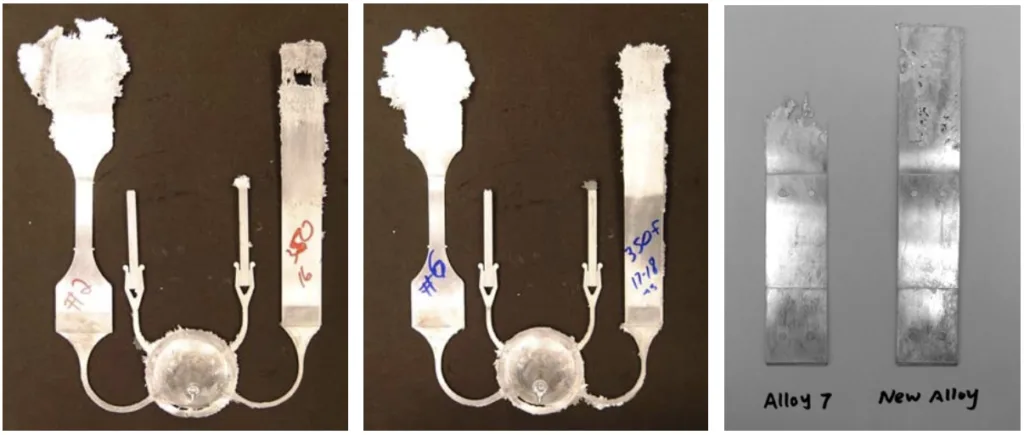
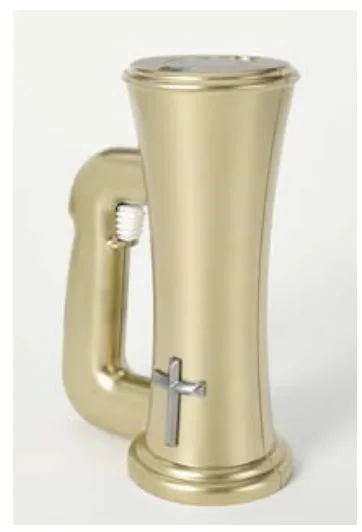
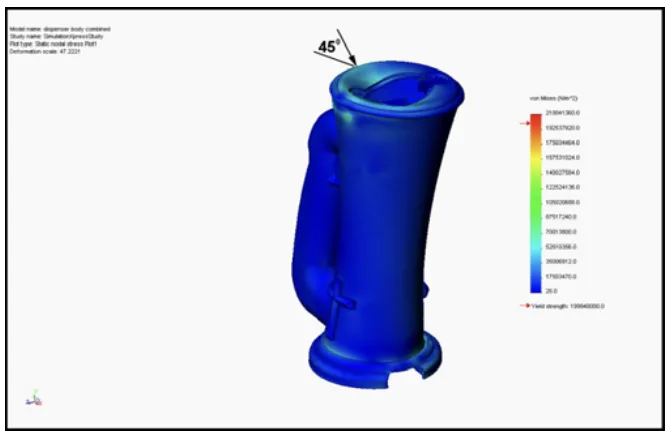
Figure Name List:
- Figure 1: Schematic of the Ragone Fluidity Tester and the experimental setup.
- Figure 2: Flow distances of tested alloys.
- Figure 3: Four-cavity ILZRO die.
- Figure 4: Typical full shots and flow samples: HF Alloy (left), Alloy 7 (centre) and flow samples (right).
- Figure 5: Parts after blister test.
- Figure 6: Communalabra™™ germ free Communion host dispenser.
- Figure 7: Illustration of the stress simulation and permanent deformation.
- Figure 8: Flow simulation showing gas pressure inside the die cavity at the end of the shot.
- Figure 9: Aluminum extruded 2D heat sinks (top left), aluminum machined heat sink (top right), zinc cast heat sinks (bottom left) [8], and new generation zinc cast heat sink (bottom right).
- Figure 10: Cellular telephone enclosures and electrical connector housings.
- Figure 11: Cellular telephone enclosure and business card holder.
7. Conclusion:
Summary of Key Findings:
The study successfully developed a new High Fluidity (HF) zinc die casting alloy with a composition of 4.5%Al, 0.01%Mg, and 0.03%Cu. This alloy exhibits superior fluidity compared to Alloy 7, while maintaining comparable mechanical properties and adequate corrosion resistance. The HF alloy is particularly suitable for thin-wall die casting applications and demonstrates potential for replacing aluminum and magnesium alloys in certain applications.
Academic Significance of the Study:
This research contributes to the field of materials science and die casting by introducing a novel zinc alloy with enhanced fluidity. The study provides valuable data on the alloy's properties, processing characteristics, and application potential, expanding the knowledge base for high-performance zinc die casting alloys.
Practical Implications:
The development of the HF alloy offers significant practical benefits for the die casting industry. Its superior fluidity enables the production of complex, thin-walled parts with improved surface quality and reduced material consumption. The alloy's potential to replace aluminum and magnesium in specific applications provides cost-saving and performance advantages. Applications in electronic equipment, such as heat sinks and EMI shielding components, are particularly promising.
Limitations of the Study and Areas for Future Research:
The study acknowledges that the impact strength of the HF alloy may be lower at higher aluminum levels and recommends further investigation in this area. Additionally, while creep strength testing is ongoing, further research is needed to fully characterize the long-term performance of the HF alloy under various service conditions. Further optimization of alloy composition and processing parameters could also be explored to further enhance its properties and expand its application range.
8. References:
- [1] Zhang, K., ILZRO Research Report No. 1 for Program ZCA-17, ILZRO, Research Triangle Park, NC, April 13, 2006.
- [2] Filc, A.B., ILZRO Research Report No. 3 for Program ZCA-17, ILZRO, Research Triangle Park, NC, August 25, 2008.
- [3] Goodwin, F.E., Filc, A.B., Lehenbauer, B., “New High Fluidity Zinc Die Casting Alloy“, Die Casting Engineer, March 2009.
- [4] Porot, P.A., Ventham, N., Jones, R.D., Spittle, J.A., "Structural Variation in Near-Eutectic Zinc-Aluminum Alloys”, Metallography 20, 1987, pp181-197.
- [5] Filc, A.B., ILZRO Research Report No. 4 for Program ZCA-17, ILZRO, Research Triangle Park, NC, March 5, 2009.
- [6] Soule, C.A., “Future Trends in Heat Sink Design", Electronics Cooling Journal, February 1, 2001.
- [7] Keller, P.K., “Cast Heat Sink Design Advantages”, Dept. of Computer Science, University of North Carolina, Chapel Hill, NC 27599-3175, USA.
- [8] U.S. Department of Energy, Office of Energy Efficiency and Renewable Energy, Industrial Technologies Programs, “Development of Thin-Section Zinc Die Casting Technology" http://www.e-smarrt.org/factsheets/thin section.pdf.
9. Copyright:
- This material is "Artur .B. Filc, Y.H. Liu, K. Zhang, N.-Y. Tang, Frank E. Goodwin"'s paper: Based on "Development of a New High Fluidity Zinc Die Casting Alloy".
- Paper Source: https://www.researchgate.net/publication/343774436
This material was created to introduce the above paper, and unauthorized use for commercial purposes is prohibited.
Copyright © 2025 CASTMAN. All rights reserved.