This article introduces the paper "Development of a bus armrest fabrication process with a high-vacuum, high-pressure die-casting process using the AM60 alloy".
1. Overview:
- Title: Development of a bus armrest fabrication process with a high-vacuum, high-pressure die-casting process using the AM60 alloy
- Authors: MyeongHan Yoo, JoonHyuk Song, JeHa Oh, ShinJae Kang, KwangSeok Kim, SungMo Yang, MinSeok Moon
- Publication Year: 2018
- Publishing Journal: Robotics and Computer–Integrated Manufacturing
- Keywords: light-weight vehicle, magnesium alloy, vacuum die-casting, AM60 alloy, bus armrest
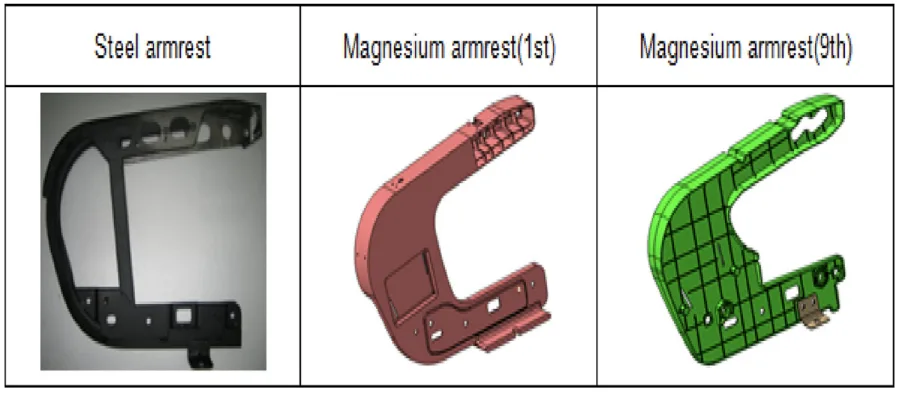
2. Research Background:
- Social/Academic Context: The increasing global focus on environmental concerns, particularly pollution and global warming, has led to stricter environmental regulations in developed countries. Automobile manufacturers are actively seeking ways to meet these enhanced standards. Lightweight vehicle design is a key area of focus to improve fuel economy and reduce CO2 emissions from automobiles.
- Limitations of Existing Research: While lightweight materials are being adopted across vehicle types, buses, despite their larger size and passenger capacity compared to passenger cars, still primarily utilize aluminum alloys in certain components. Magnesium alloys, known for their superior lightness and performance compared to other commercial metallic materials, are not yet commonly used in bus manufacturing.
- Necessity of the Research: This research addresses the need to develop lightweight vehicle parts, specifically for buses, using magnesium die-casting. Replacing heavier materials with magnesium alloys in bus components like armrests offers a significant opportunity for weight reduction, contributing to improved fuel efficiency and reduced environmental impact.
3. Research Purpose and Research Questions:
- Research Purpose: The primary purpose of this study is to develop and evaluate a bus armrest made from lightweight magnesium alloy AM60. This is achieved through a high-vacuum, high-pressure die-casting process, encompassing design, simulation, mold making, and process development.
- Key Research Questions:
- Can a bus armrest be effectively fabricated using AM60 magnesium alloy and a high-vacuum, high-pressure die-casting process?
- Will the magnesium alloy armrest meet the necessary mechanical property requirements and durability standards for bus applications?
- Research Hypotheses: The research hypothesizes that a magnesium alloy bus armrest, manufactured using high-vacuum, high-pressure die-casting, will be significantly lighter than a traditional steel armrest while still fulfilling the required structural and functional performance criteria.
4. Research Methodology:
- Research Design: This research employs a development and experimental approach. It involves a series of stages, starting from part design and simulation, progressing through mold making and die-casting process development, and culminating in mechanical property and durability testing.
- Data Collection Method: Data was collected through:
- Simulation Results: Structural simulations were performed using Nastran FX (ver. 2.0), and fluidity and solidification simulations were conducted using Anycasting (ver. 7.0).
- Mechanical Property Test Data: Tensile tests were performed according to ASTM-E8M standards to evaluate the mechanical properties of the magnesium alloy armrest.
- Vertical Fracture Load Test Data: Vertical fracture load tests were conducted to assess the armrest's structural integrity under load, following ES88001-50 specifications.
- Fatigue Test Data: Fatigue tests were performed to evaluate the armrest's durability under cyclic loading, also according to ES88001-50 specifications.
- Analysis Method: The collected data was analyzed through:
- Structural and Solidification Simulation Analysis: Simulation results were used to optimize the armrest design and die-casting process parameters.
- Mechanical Property Analysis: Tensile test data was analyzed to determine key mechanical properties like yield strength and ultimate tensile strength.
- Vertical Fracture Load and Fatigue Test Analysis: Test results were compared against the ES88001-50 specification requirements to evaluate the structural performance and durability of the magnesium armrest. Comparison was made between the performance of the magnesium armrest and a steel armrest based on simulation and experimental results.
- Research Subjects and Scope: The research focuses on the development of a bus armrest component made from AM60 magnesium alloy. The scope includes the entire fabrication process, from initial design to final performance testing, using high-vacuum, high-pressure die-casting. The performance of the magnesium armrest is evaluated in comparison to a conventional steel armrest.
5. Main Research Results:
- Key Research Results: The study successfully developed a magnesium alloy bus armrest using a high-vacuum, high-pressure die-casting process. The resulting armrest achieved significant weight reduction compared to steel, while meeting the required mechanical properties and durability standards. The design was also optimized for manufacturing efficiency by creating a single part usable for both left and right sides of the bus.
- Statistical/Qualitative Analysis Results:
- Weight Reduction: The final magnesium armrest design achieved a 35% weight reduction compared to the existing steel armrest. The weight of the affected part was reduced by 36%.
- Vertical Fracture Load Test: At a vertical load of 150 kgf (approximately 1471 N), the displacement of the magnesium armrest was measured at 6.99 mm. This is well within the ES88001-50 specification limit of 20 mm.
- Fatigue Test: The magnesium armrest successfully passed the fatigue test, exceeding the target of 65,000 cycles as per ES88001-50 requirements.
- Yield Strength: The yield strength of the AM60 magnesium alloy armrest was confirmed to be over 130 MPa.
- Deformation Simulation: Vertical load simulation showed a deformation of 5.80 mm for the steel armrest. The initial magnesium armrest design showed a higher deformation of 13.4 mm. However, after design optimization, the final magnesium armrest design exhibited a significantly reduced deformation of only 2.34 mm.
- Data Interpretation: The results demonstrate that AM60 magnesium alloy, processed using high-vacuum, high-pressure die-casting, is a viable material for manufacturing bus armrests. The magnesium armrest not only achieves significant weight reduction but also meets and exceeds the required structural performance and durability standards. The improved deformation performance in the final design compared to the initial magnesium design and even the steel design highlights the effectiveness of the design optimization process.
- Figure Name List:
- Fig. 1. Design comparison with steel armrest and magnesium armrest design.
- Fig. 2. Result of vertical fracture load simulation with each material.
- Fig. 3. Simulation condition of the magnesium armrest solidification.
- Fig. 4. Oxide trapping on the mold during filling.
- Fig. 5. Mold base and final mold.
- Fig. 6. Mechanical property specimen and results summary.
- Fig. 7. Armrest vertical fracture load evaluation.
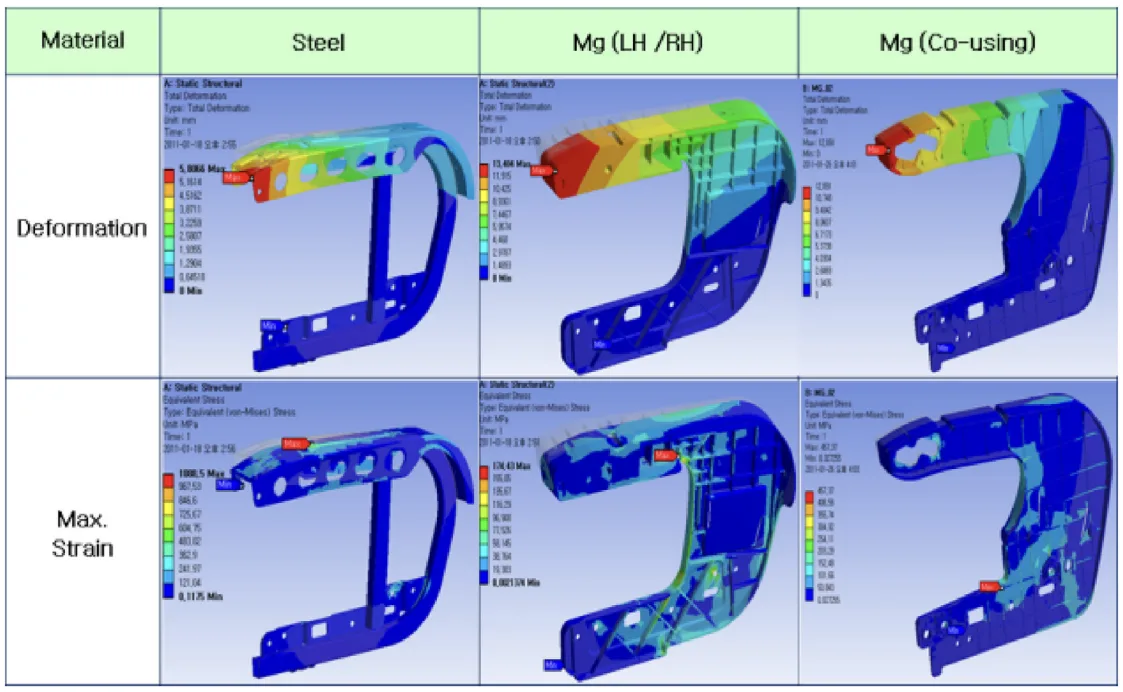
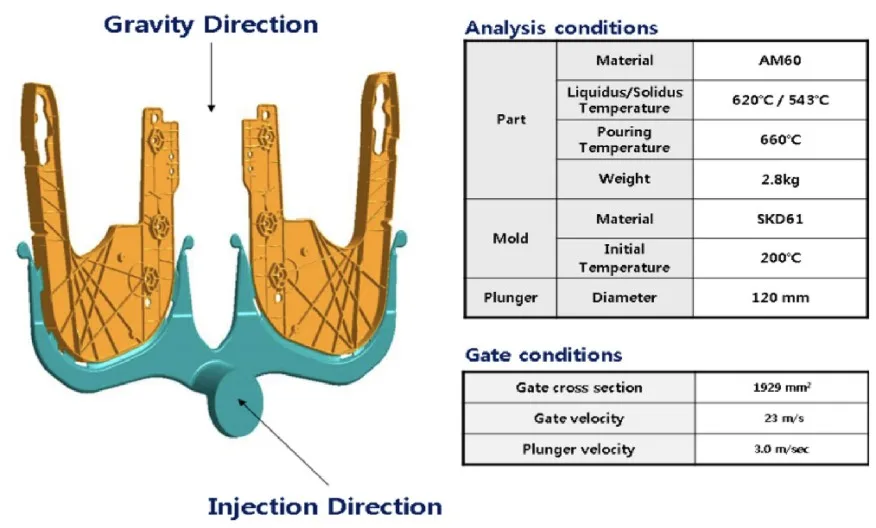
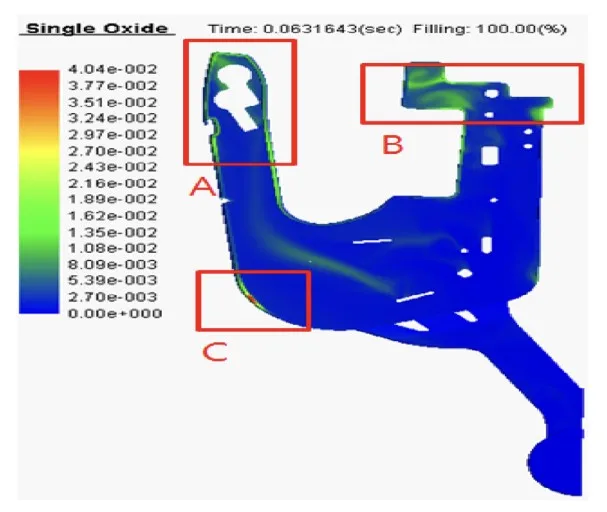
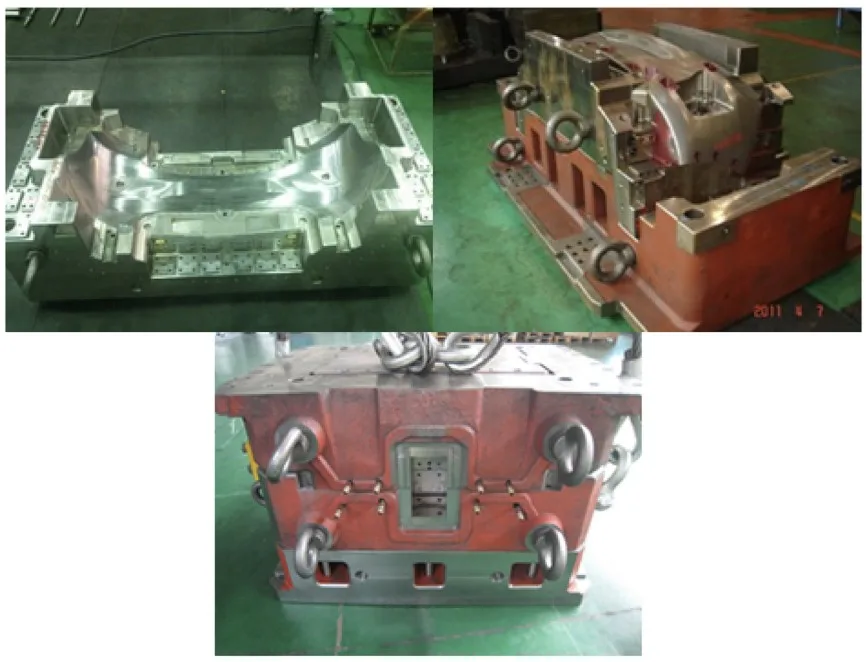
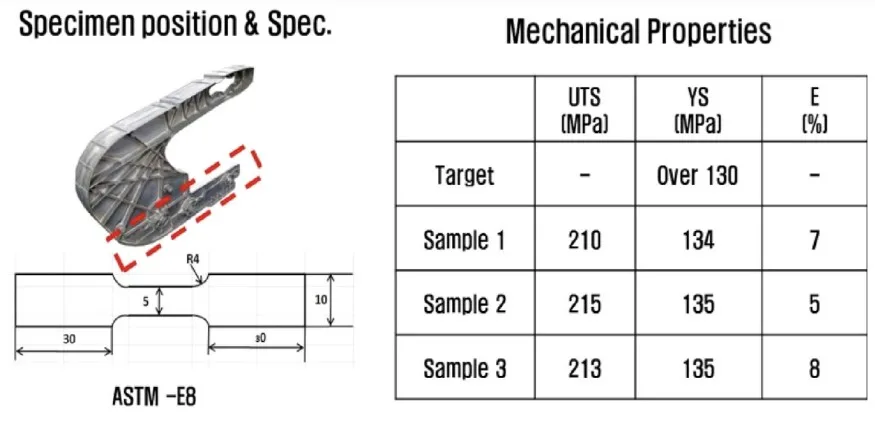
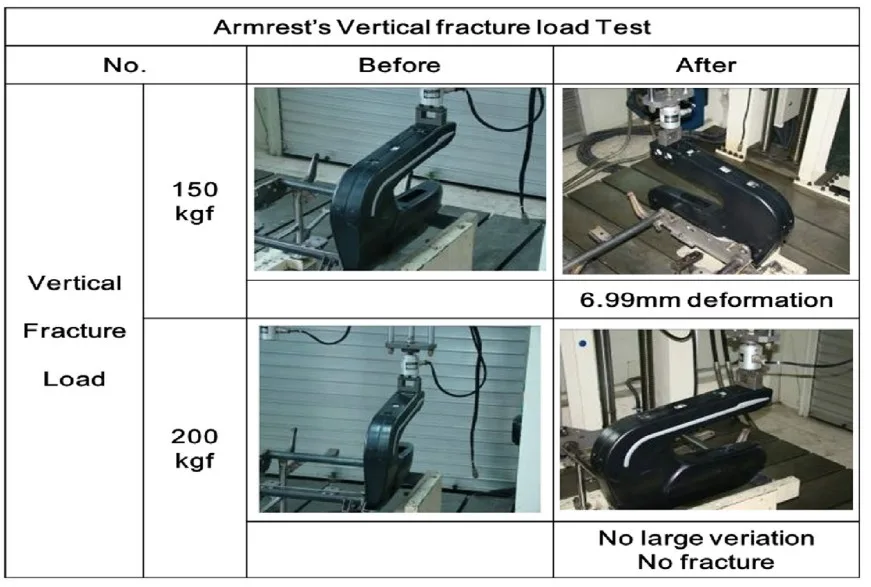
6. Conclusion and Discussion:
- Summary of Main Results: This research successfully developed a lightweight bus armrest by replacing steel with magnesium alloy AM60 and utilizing a high-vacuum die-casting process. The magnesium armrest achieved significant weight reduction, reduced the number of manufacturing parts from 5 to 2, and successfully met the vertical fracture load, fatigue test, and yield strength requirements.
- Academic Significance of the Research: This study provides valuable insights into the application of magnesium alloy AM60 and high-vacuum die-casting for manufacturing complex automotive components. It demonstrates the feasibility of using magnesium alloys to replace heavier materials like steel in structural parts, contributing to lightweight vehicle design principles.
- Practical Implications: The successful development of a lightweight magnesium bus armrest has significant practical implications for the automotive industry, particularly for bus and commercial vehicle manufacturing. The weight reduction achieved translates to potential fuel savings and reduced emissions. The all-in-one design for both right and left sides also streamlines manufacturing processes, potentially reducing production costs and improving inventory management. The findings suggest a pathway for wider adoption of magnesium alloys in vehicle components to meet increasingly stringent environmental regulations and improve vehicle efficiency.
- Limitations of the Research: While the paper demonstrates the successful development of the magnesium armrest, it primarily focuses on a specific component and alloy. Further research may be needed to assess the generalizability of these findings to other vehicle parts and different magnesium alloys. Long-term durability in real-world operating conditions and a comprehensive cost analysis for mass production are also areas that warrant further investigation.
7. Future Follow-up Research:
- Directions for Follow-up Research: Future research should focus on the development of commercial vehicle seat modules utilizing magnesium alloy and high-vacuum high-pressure die-casting. This includes expanding the application to other components within the seat module and exploring the adoption of these lightweight solutions in buses, trucks, and electric vehicles.
- Areas Requiring Further Exploration: Further research should explore:
- Optimization of the die-casting process for mass production and cost-effectiveness.
- Investigation of other magnesium alloys with potentially enhanced properties or cost advantages.
- Long-term durability and performance evaluation of magnesium armrests in real-world bus operating environments.
- Detailed cost-benefit analysis for large-scale implementation of magnesium alloy components in commercial vehicles.
8. References:
- [1] M.S. Moon, K.D. Woo, S.J. Kang, J.H. Song, J.H. Oh, S.M. Yang, A study of the corrosive behavior of STS304 and STS430, depending on surface pre-treatment conditions, in PEMFC while in operation, Int. J. Precis. Eng. Man. 15 (6) (2014) 1201–1205.
- [2] K. Pettersen, P. Bakke, D. Albright, Magnesium Die Casting Alloy Design, Proceedings of 132nd TMS Conference Magnesium Technology 2002 as Held at the 2002 TMS Annual Meeting 240–246.
- [3] P. Bakke, K. Pettersen, S. Guldberg, S. Sannes, The impact of metal cleanliness on mechanical properties of die cast magnesium alloy AM50, in: K.U. Kainer (Ed.), Magnesium Alloys and Their Applications, Wiley-VCH Verlag GmbH, Germany, 2006, pp. 739–745.
- [4] H.W. Shin, B.S. Han, H.J. Yoo, H.H. Jung, Development of magnesium seat frames using the vacuum die casting process, J. KSPE 26 (3) (2009) 88–97.
- [5] P. Bakke, K. Pettersen, H. Westengen, Improving the strength and ductility of magnesium die-casting alloys via rare-earth addition, JOM 55 (11) (2003) 46–51.
- [6] G. Gu, S. Lin, Y Xia, Q Zhou, Experimental study on influence of section thickness on mechanical behavior of die-cast AM60 magnesium alloy, Mater. Des. 38 (2012) 124–132.
- [7] A. Kiełbus, T. Rzychoń, R. Cibis, Microstructure of AM50 die casting magnesium alloy, J. Achiev. Mater. Manuf. Eng. 18 (1-2) (2006) 135–138.
- [8] J.H. Seo, S.K. Kim, Mechanical properties of 0.25-0.65wt% CaO added AM60B Eco-Mg diecastings at room and elevated temperatures, J. Korea Foundry Soc. 31 (1) (2011) 11–17.
- [9] O. Unal, M. Tiryakioğlu, On the ductility potential and assessment of structural quality in Mg alloy castings, Mater. Sci. Eng. A 643 (2015) 51–54.
- [10] K. Máthis, F. Chmelík, M. Janeček, B. Hadzima, Z. Trojanová, P. Lukác, Investigating deformation processes in AM60 magnesium alloy using the acoustic emission technique, Acta Mater. 54 (2006) 5361–5366.
9. Copyright:
- This material is MyeongHan Yoo et al.'s paper: Based on Development of a bus armrest fabrication process with a high-vacuum, high-pressure die-casting process using the AM60 alloy.
- Paper Source: https://doi.org/10.1016/j.rcim.2018.01.004
This material was summarized based on the above paper, and unauthorized use for commercial purposes is prohibited.
Copyright © 2025 CASTMAN. All rights reserved.