This introduction paper is based on the paper "DESIGN OF A NEW CASTING ALLOYS CONTAINING LI OR TI+ZR AND OPTIMIZATION OF ITS HEAT TREATMENT" published by "METAL 2014".
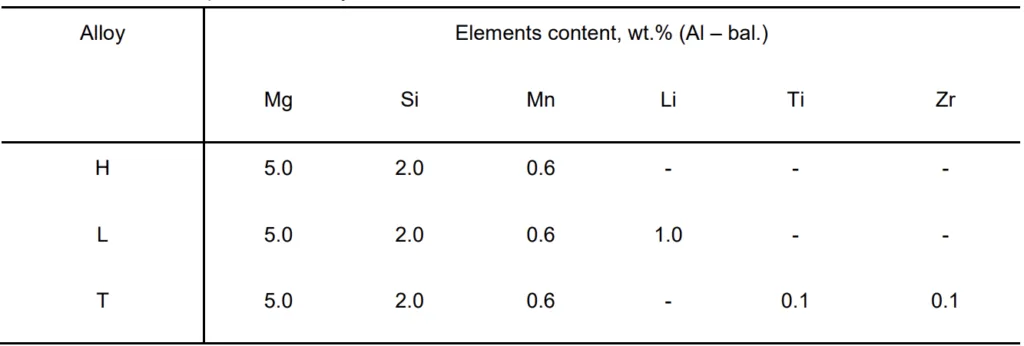
1. Overview:
- Title: DESIGN OF A NEW CASTING ALLOYS CONTAINING LI OR TI+ZR AND OPTIMIZATION OF ITS HEAT TREATMENT
- Author: Oleksandr TRUDONOSHYN, Olena PRACH, Viktoriya BOYKO, Maxim PUCHNIN, Kostiantyn MYKHALENKOV
- Year of publication: 2014
- Journal/academic society of publication: METAL 2014
- Keywords: aluminum, casting alloys, eutectic, microstructure, automated ball indentation, elastic modulus.
2. Abstract:
In this paper was proposed to design new casting alloys on the base of the Al-Mg-Si system using Li addition to achieve precipitation strengthening effect and alloying by Ti+Zr to achieve saturation of solid solution and grain refinement effect.
The as-cast and heat treated structure of permanent mould casting of AlMg5Si2Mn containing 1.0 wt.% Li and 0.1 wt.% Ti+0.1 wt.% Zr alloys was investigated by differential scanning calorimetry, microhardness measurements, scanning and transmission electron microscopy and energy dispersive X-ray analysis. Mechanical properties of these alloys were investigated with modern automated ball indentation method. This method showed good convergence with standard tensile tests and allows to determine hardness, yield stress and elastic modulus of tested alloys.
It was observed that addition of Li causes modification of (Al)+(Mg2Si) eutectic lamellas making them thinner and interlamella distance becomes larger. Ti+Zr addition does not change eutectic morphology but strongly reduces the size of α-Al dendrites, also, it produces the nucleation particles for primary Mg2Si crystals.
Homogenization of studied alloys at 570 C results in disintegration of Mg2Si lamellas and this process takes 30 min to transform plate like lamellas to fine spheres. It was established that hardness and microhardness both of Li and Ti+Zr containing alloys decrease at the same time. Further heating does not produce remarkable changes of hardness. Artificial aging leads to the increasing of hardness and microhardness.
Obtained results showed that heat treatment of AlMg5Si2Mn improves its mechanical properties with Li and Ti+Zr assist precipitation hardening and solid solution strengthening effects.
3. Introduction:
Automotive and aerospace industries from year to year are strongly interested in development of new alloys for production of light weight constructions. In this context alloys of the Al-Mg-Si system are considered as promising candidate for production of sheets and extruded parts using wrought alloys (6061, 6005, etc) and thin wall casting using AlMg5Si2Mn alloy. Today is established that Al-Mg-Si casting alloys possesses good corrosion resistance, weldability, high surface finishing and, in particular, good mechanical properties.
Considering additional alloying and heat treatment of AlMg5Si2Mn the data on the possibility to improve mechanical properties by alloying with Cu, Zn, Cr, Ti, Zr, Sc+Zr, Li, and heat treatment is rather limited and controversial [1-4]. According to Lenczowski [1] AlMg3Si1 containing Sc+Zr in T5 state shows ultimate tensile strength (UTS) of 270 MPa at room temperature and 265 MPa at 250°C. From the work of Petkow et al. [2] can be seen that the AlMg5Si2Mn alloy, cast into permanent mold, shows only a slight increase of tensile and ultimate tensile strength after T6 treatment together with a dramatically low fracture elongation of about 2.5% for temper F, decreasing down to 1.4% after artificial aging.
Author's data and literature information, such as [5] show that the UTS of commercial A356 T6 may reach a level up to 300 MPa and an elongation to fracture of 6.0%. Comparable to A356 is the permanent mold cast AlMg5Si2Mn [6], where the ultimate tensile strength varies from 255 to 298 MPa and the elongation is in the range between 1.2 and 3.2%. The elongation is one order lower than that of AlMg5Si2Mn+0.2 wt.% Ti alloy subjected to high pressure die casting (HPDC), where it can reach 15% [3] in as-cast state.
It is known that Al-Mg-Si belong to the group of age hardenable alloys and can be heat treated to achieve necessary combination of properties especially. However, the optimal solution treatment temperature and time as well as temperature and time for artificial aging are not established yet.
Similarly to heat treatment the effect of additional alloying of AlMg5Si2Mn alloy by, for example, Li or Ti+Zr, on the structure formation and properties are not yet satisfactory considered. From the early work of Fridlyander et al. [7] it is clear that addition of Li to Al-Cu or Al-Mg alloys can significantly enhance their properties simultaneously with decreasing density.
Last years showed strong advance in development of Al-Cu-Li and Al-Mg-Li wrought alloys. But, there is no one Li-containing casting alloy is designed yet. It was proposed to use AlMg5Si2Mn casting alloy as the base material to design Li-containing casting alloy. The idea is based on the composition of α-Al solid solution in AlMg5Si2Mn alloy which consists of 2.4 wt.% Mg, (0.3 - 0.4) wt.% Mn and no Si was detected. Subsequently, the solution grain would be similar to Al-Mg alloy and addition of Li may enhance mechanical properties of the material.
Thus, the purpose of the present paper is to establish the effect of Li and Ti+Zr additions on the microstructure and mechanical properties of Al-Mg-Si-Mn casting alloy in as cast state and after heat treatment.
4. Summary of the study:
Background of the research topic:
The automotive and aerospace industries require lightweight materials. Al-Mg-Si alloys are promising candidates, particularly the AlMg5Si2Mn alloy for thin-wall castings due to its good corrosion resistance, weldability, surface finish, and mechanical properties.
Status of previous research:
Data on improving AlMg5Si2Mn properties through alloying (e.g., Cu, Zn, Cr, Ti, Zr, Sc+Zr, Li) and heat treatment is limited and sometimes contradictory. While Li additions are known to enhance properties in Al-Cu and Al-Mg wrought alloys, specific Li-containing Al-Mg-Si casting alloys have not been well-developed. Optimal heat treatment parameters (solution treatment, artificial aging) for these modified alloys are not fully established.
Purpose of the study:
To establish the effect of Li and Ti+Zr additions on the microstructure and mechanical properties of Al-Mg-Si-Mn casting alloy (specifically AlMg5Si2Mn base) in the as-cast state and after heat treatment.
Core study:
The study involved designing new casting alloys based on AlMg5Si2Mn by adding either 1.0 wt.% Li (Alloy L) or 0.1 wt.% Ti + 0.1 wt.% Zr (Alloy T). The microstructure of these alloys and a base alloy (H) was investigated in the as-cast and heat-treated (solution treatment at 570°C, T6 treatment with aging at 175°C) conditions using microscopy (SEM, TEM mentioned in abstract) and EDS. Mechanical properties including hardness (Brinell, microhardness) and tensile properties (yield stress, elastic modulus) were measured using standard tensile tests and the automated ball indentation (ABI) method. The effects of the additions on eutectic morphology, grain size, phase composition, and the response to heat treatment (homogenization, solution treatment, artificial aging) were analyzed.
5. Research Methodology
Research Design:
Three alloys based on Al5Mg2Si0.6Mn were prepared: a base alloy (H), one with 1.0 wt.% Li (L), and one with 0.1 wt.% Ti + 0.1 wt.% Zr (T). Alloys were prepared in an electric resistance furnace using master alloys and high purity aluminum, melted, degassed under argon, and cast into permanent moulds (implied from abstract). Two types of heat treatment were applied: 1) Solution treatment at 570°C for varying times (30 min, 1h, 1.5h) followed by water quenching. 2) T6 treatment, combining solution treatment (570°C), water quenching, and artificial aging at 175°C for different times.
Data Collection and Analysis Methods:
- Microstructure: Scanning Electron Microscopy (SEM), Energy Dispersive X-ray analysis (EDS/EDX). (Differential Scanning Calorimetry and Transmission Electron Microscopy mentioned in abstract but details not provided in methods/results).
- Mechanical Properties:
- Brinell Hardness (HB): 2.5 mm ball, 62.5 kg load, 10 sec loading time.
- Microhardness (HV0.05): Duramin-2 tester, standard indentation time.
- Tensile Tests: INSTRON 5582 machine, according to ČSN EN ISO 6892-1 standard.
- Automated Ball Indentation (ABI): Continuous recording of load and indentation depth (max load 2.5 kN) to determine hardness, yield stress (calculated), and elastic modulus.
Research Topics and Scope:
The research focused on the AlMg5Si2Mn alloy system with specific additions of Li or Ti+Zr. The scope included:
- Characterization of as-cast microstructure (phases, morphology).
- Investigation of microstructural changes during solution treatment (homogenization) and T6 heat treatment.
- Evaluation of the effect of Li and Ti+Zr additions on microstructure (eutectic modification, grain refinement).
- Measurement and comparison of mechanical properties (hardness, microhardness, tensile properties via standard tests and ABI) in as-cast and heat-treated states.
- Analysis of the relationship between microstructure, heat treatment, and mechanical properties.
6. Key Results:
Key Results:
- As-cast Microstructure: All alloys (H, L, T) showed an equiaxed grain structure consisting of α-Al solid solution dendrites, (Al)+(Mg2Si) eutectic, primary Mg2Si crystals, and Al(Mn,Fe)Si phase (Fig. 1). The (Al)+(Mg2Si) eutectic was lamellar.
- Effect of Additions: Li addition (Alloy L) modified the (Al)+(Mg2Si) eutectic, making lamellas thinner and increasing interlamellar spacing. Ti+Zr addition (Alloy T) did not significantly change eutectic morphology but caused a slight grain refinement effect (smaller α-Al dendrite arms) and provided nucleation sites for primary Mg2Si crystals (Fig. 1).
- Phase Composition: EDS analysis confirmed Mg (approx. 2.3-2.6 wt.%) and Mn (approx. 0.45 wt.%) in the α-Al solid solution (Table 2).
- Heat Treatment Effects:
- Homogenization (570°C): Resulted in the disintegration of Mg2Si lamellas, transforming into fine spheres within 30 minutes.
- Solution Treatment: Caused a significant decrease in Brinell hardness (HB) and microhardness (HV0.05) due to eutectic spheroidization and dissolution of precipitates (Fig. 2). Mg content in α-Al initially decreased (to 1.6 wt.% after 30 min) and then gradually increased with longer heating (up to 1.8 wt.%).
- Artificial Aging (175°C): Led to an increase in hardness and microhardness for all alloys. Optimal hardness for L and T alloys was reached after 90 minutes of aging, followed by a slight decrease (overaging) with prolonged aging up to 1800 min (Fig. 2).
- Mechanical Properties:
- The Automated Ball Indentation (ABI) method showed good correlation with standard tensile tests for hardness and elastic modulus (Table 3, Fig. 3). Elastic modulus values (74-79 GPa) were within the typical range for aluminum alloys.
- Yield strength (Rp0.2) calculated from ABI hardness (using Rp0.2 = 2.5 × HB) showed the same trend as values obtained from standard tensile tests, indicating ABI's potential for rapid property estimation (Table 3).
- Heat treatment improved mechanical properties, attributed to precipitation hardening and solid solution strengthening effects assisted by Li and Ti+Zr additions.
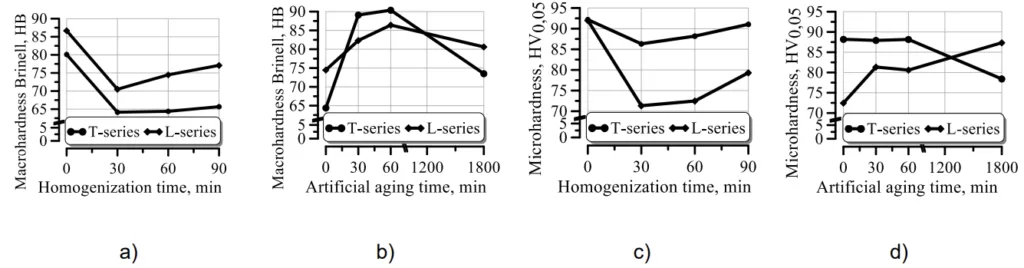
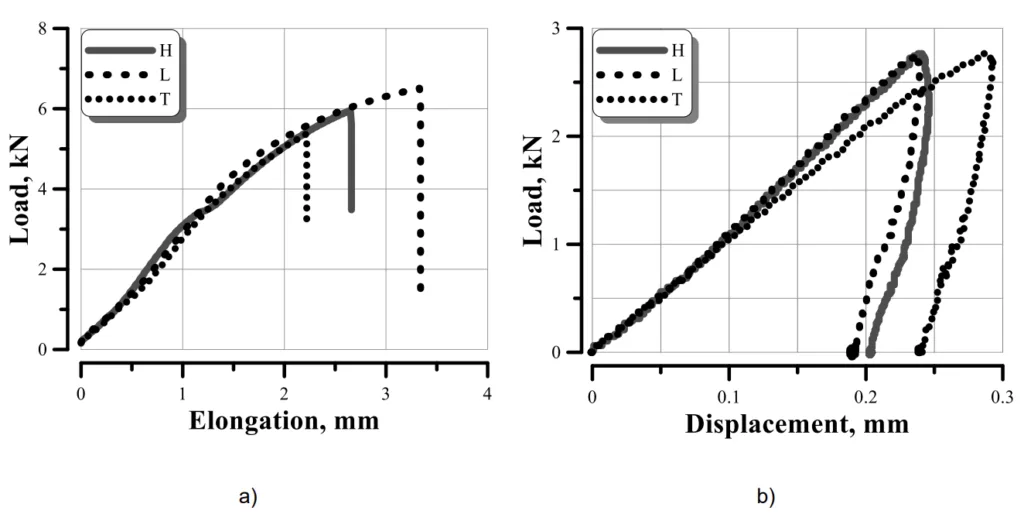
Figure Name List:
- Fig. 1 Microstructure of H (a), L (b), T (c) alloys in as-cast state.
- Fig. 2 Changes of Brinell hardness (a, b) and microhardness (c, d) of L, T alloys.
- Fig. 3 Tensile curves of standard tensile test (a) and ABI (b)
7. Conclusion:
- In as-cast state the microstructure of Al-Mg-Si-Mn alloy consists of three phase: α-Al solid solution grains, (Al)+(Mg2Si) eutectic and Mg2Si primary crystals. α-Al exhibits dendrites morphology with well developed arms. Eutectic has plate-shaped morphology of lamellas and Mg2Si primary crystals.
- Both alloys of AlMg5Si2Mn+Li and AlMg5Si2Mn+(Ti+Zr) showed the similar results of macro- and microhardness tests. Mechanical tests prove that solution treatment reduces the hardness of investigated alloys due to the disintegration of the Mg2Si lamellas, decreases the content of alloying elements in solid solution.
- Artificial aging leads to increase of the alloy hardness. Optimal values of macro- and microhardness was achieved after 30-60 minutes of aging time. Overaging of evaluated alloys was monitored after the 60 minutes of artificial aging indicated by extremely decrease of hardness.
- Automated ball indentation test shows that this method allows rapid orientation in mechanical properties of tested materials. Obtained values using ABI method may effectively facilitate modification of parameters of heat treatment and content of alloying elements. Yield stress calculated using equation Rp0.2 = 2.5 x HB has the same trend as tensile values. More accurate correlations between values of yield stress, which were obtained by tensile tests and ABI, require more data for statistic. Calculation given in this paper shows that this trend is quite promising.
8. References:
- [1] EIGENFELD, K., FRANKE, A., KLAN, S., KOCH, H., LENZCOWSKI, B., PFLEGE, B. New developments in heat resistant aluminum casting materials, Casting plant and Technology International, Vol. 4, 2004, p. 4-9.
- [2] PETKOV, T., KUNSTNER, D., PABEL, T., KNEIBL, C., SCHUMACHER, P. Optimizing the Heat Treatment of a ductile AlMgSi-alloy, Giesserei-Rundschau, Vol. 59, 2012, p. 194-200.
- [3] JI, S., WATSON, D., FAN, Z., WHITE, M. Development of a super ductile die cast Al-Mg-Si alloy, Materials Science and Engineering, Vol. 556, October 2012, p. 824-833.
- [4] WUTH, M. C., KOCH, H., FRANKE, A. J. Production of steering wheel frames with an AlMg5Si2Mn alloy, Casting Plant and Technology International, Vol.16, No. 1, 2000р. 12-24.
- [5] SHABESTARI, S. G., SHAHRI, F., Influence of modification, solidification conditions and heat treatment on the microstructure and mechanical properties of A356 aluminum alloy, Journal of Material Science, Vol. 39, 2004, p. 2023-2032.
- [6] PIRŠ, J., ZALAR, A. Investigations of the distribution of elements in phases present in G-AlMg5Si cast alloy with EDX/WDX spectrometers and AES, Microchimica Acta, Vol. 101, No.1-6, 1990, p. 295-304.
- [7] FRIDLYANDER, J. N., BRATUKHIN, A. G., DAVYDOV, V. G. Soviet Al-Li Alloys of Aerospace Application, Aluminum-Lithium, Proceedings of the Sixth International Aluminum-Lithium Conference in Garmisch-Partenkirchen, PETERS, M. and WINKLER, P.-J. eds., Germany, Vol. 1, 1991, p. 35-42.
- [8] OLIVER, W. C., PHARR, G. M. Measurement of hardness and elastic modulus by instrumented indentation: Advances in understanding and refinements to methodology, Journal of Materials Research, Vol. 19, No. 1, 2004, p. 3-20.
- [9] ISO 14577-4:2007, Metallic materials - Instrumented indentation test for hardness and materials parameters - Part 4: Test method for metallic and non-metallic coatings, Switzerland, 2007.
- [10] ASTM WK381, Standard Test Methods for Automated Ball Indentation Testing of Metallic Samples and Structures to Determine Stress - Strain Curves and Ductility at Various Test Temperatures, USA.
- [11] TRET'JAKOV, A., TROFIMOV, G.; GUR'JANOVA, M. M Mechanical properties of steel and alloys during plastic deformation, Moscow „Mashinostroenie", 1971. 64 p. UDK 621.7.011.
9. Copyright:
- This material is a paper by "Oleksandr TRUDONOSHYN, Olena PRACH, Viktoriya BOYKO, Maxim PUCHNIN, Kostiantyn MYKHALENKOV". Based on "DESIGN OF A NEW CASTING ALLOYS CONTAINING LI OR TI+ZR AND OPTIMIZATION OF ITS HEAT TREATMENT".
- Source of the paper: [DOI not provided in the paper]
This material is summarized based on the above paper, and unauthorized use for commercial purposes is prohibited.
Copyright © 2025 CASTMAN. All rights reserved.