This introductory paper is the research content of the paper ["Design and Development of Rotor Quality Test System for Die-Cast Copper Rotors"] published by [IEEE].
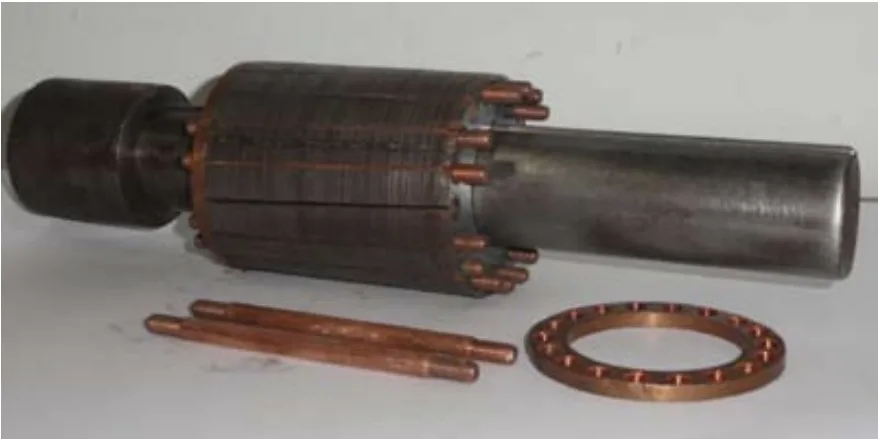
1. Overview:
- Title: Design and Development of Rotor Quality Test System for Die-Cast Copper Rotors
- Author: Soby T. Varghese, K. R. Rajagopal and Bhim Singh, Fellow, IEEE
- Publication Year: 2018
- Publishing Journal/Academic Society: IEEE Transactions on Industry Applications
- Keywords: Induction motor, die-cast copper rotor, rotor tester, rotor faults, fault detection, diagnostics, signal analysis.
2. Abstracts / Introduction
In this paper, common faults in copper die-cast processing are identified and sufficient monitoring methods are suggested in a three stage inspection. The final stage consists of a rotor quality test system, which detects most of the problems found in copper die-cast rotors.
This rotor quality test system analysis, helps to optimize the rotor manufacturing process and avoid the circumstances of fitting an inferior rotor in the motor assembly. As global interest in EV (Electric Vehicle) has been extended to a larger scale, the automotive engineers are in search of special materials for the manufacturing of the motor. Recently, the interest in die- cast copper rotor motor has increased due to concerns about the scanty availability of rare earth materials and magnet performance at elevated temperatures in permanent magnet motors.
The copper rotor induction motor appears to be the viable choice for parallel hybrid electric vehicles in terms of compactness, high-power density, overall system, efficiency and durability [1]. High pressure die-casting is the most economical process for the manufacturing of die-cast rotors. Replacing the aluminium with the copper in die-cast rotor bars in the squirrel cage induction motor has enormous benefit in terms of reduction in rotor I2R loss that ultimately provides improved efficiency and energy savings.
Though, the copper die-cast process is identical to aluminium die-cast process, additional manufacturing challenges of increased temperature and pressures make copper die-cast rotor production difficult.
3. Research Background:
Background of the Research Topic:
The background of this research is rooted in the increasing adoption of Electric Vehicles (EVs) and the demand for high-efficiency motors. Copper rotor motors offer superior efficiency and temperature handling capabilities compared to traditional motors, making them suitable for EV applications. However, manufacturing die-cast copper rotors presents challenges, leading to potential defects that can compromise motor performance and reliability.
Status of Existing Research:
Existing research includes methods for detecting rotor faults in assembled motors, such as Motor Current Signature Analysis (MCSA) [8]-[9]. MCSA detects rotor faults from the relative differences of frequency components received from stator windings [8]. However, these methods are limited as they require the motor to be in an assembled and operational state, and the results can be influenced by other motor components. Disassembled detection methods like growler test, tap test, dye penetrant test, temperature indicating paints, ultra sonic testing, high current excitation and resistance test [8] exist, but they may not provide a complete evaluation of electric, magnetic, insulational and structural properties of the rotor stack simultaneously.
Necessity of the Research:
There is a necessity for a direct, non-destructive testing method for die-cast copper rotors that can be implemented in the production field, independent of other motor components. Conventional fault detection methods in disassembled motor and online methods have limitations in accurately evaluating the quality level of die-cast copper rotors during manufacturing. The paper points out that "during the manufacturing process of the die-cast rotor, the rotor can't be locked up until it is fully assembled and powered for test." and "results obtained from these tests are naturally influenced by the condition of the other motor components". Therefore, a dedicated rotor quality test system is needed to address these limitations and ensure the production of high-quality copper rotors.
4. Research Purpose and Research Questions:
Research Purpose:
The research purpose is to design and develop a Rotor Quality Test System (RQTS) for die-cast copper rotors. This system aims to detect common faults arising from the copper die-casting process, optimize the rotor manufacturing process, and prevent the assembly of inferior rotors into motors.
Key Research:
The key research focuses on:
- Identifying common faults in copper die-cast rotors.
- Suggesting monitoring methods for a three-stage inspection process.
- Developing a rotor quality test system (RQTS) as the final stage of inspection.
- Analyzing the RQTS data to optimize the rotor manufacturing process.
- Evaluating the effectiveness of the RQTS in detecting rotor faults.
5. Research Methodology
Research Design:
The research employs a design and development approach, creating a novel Rotor Quality Test System (RQTS) based on electro-magnet induction. The RQTS is designed for implementation in a manufacturing setting for direct rotor testing. A three-stage quality monitoring test is formulated, including weight test, flaw detection test on end rings using ultrasonic tester and Rotor Quality Tester.
Data Collection Method:
The RQTS utilizes an electromagnet sensor to induce a voltage in the rotor bars as it rotates within a magnetic field. A pick-up coil detects changes in the magnetic field due to rotor bar current. The induced voltage waveform from the pick-up coil is acquired by a Data Acquisition System (DAQ), specifically the National Instruments PCI-5922 digitizer board. A proximity sensor provides rotor speed data.
Analysis Method:
The acquired voltage waveforms are analyzed in both time and frequency domains using software developed in NI LabVIEW. The software performs FFT analysis to examine the frequency spectrum of the rotor bar waveform. Quality assessment is based on statistical comparison of waveform characteristics, including FFT frequency and amplitude, against pre-defined quality levels.
Research Subjects and Scope:
The research focuses on die-cast copper rotors for induction motors. The developed RQTS is designed to be adaptable for testing rotors of various sizes and weights through adjustable chuck and tailstock assembly. A prototype rotor with intentionally introduced faults (broken bar, inter-laminar short) was fabricated to validate the RQTS and inspection procedure.
6. Main Research Results:
Key Research Results:
The main research result is the successful design and development of a functional Rotor Quality Test System (RQTS). The RQTS effectively detects various faults in die-cast copper rotors, including blow holes, porosity, inter-laminar shorting, bad skewing, lower conductivity, eccentric rotor cage, and lamination property changes. The system provides qualitative results, indicating the degree of problems in faulty rotors and enabling pass/fail decisions based on standard quality levels. "All the seven rotor problems mentioned earlier can be detected by this rotor quality test."
Analysis of presented data:
- Weight Test: A primary level check for detecting "larger unacceptable voids" by comparing rotor stack weight before and after casting. (Fig. 3)
- Flaw Detection Test (Ultrasonic): Used to verify porosity levels in end rings, with "peaks in ultrasonic tester" indicating flaws. (Fig. 4)
- Rotor Quality Tester (RQTS): Based on Faraday's law of induction, the RQTS generates waveforms reflecting rotor bar condition. Deviations from a "single frequency sine waveform repeated for the number of rotor bars having the same peak amplitude" indicate faults. (Fig. 5, Fig. 9, Fig. 17, Fig. 20, Fig. 21)
- Software Analysis: LabVIEW software analyzes waveforms in time and frequency domains, using FFT to identify frequency and amplitude deviations indicative of faults. (Fig. 15, Fig. 16, Fig. 17)
- Prototype Rotor Testing: Testing with prototype rotors containing intentional faults validated the RQTS's ability to detect and differentiate various rotor defects, producing characteristic waveforms for each fault type. (Fig. 18, Fig. 19, Fig. 20, Fig. 21)
- Fig. 1 Manufacturing process flow of die-cast copper rotor
- Fig. 2 Three stage quality monitoring test for copper die-cast rotor
- Fig. 3 Weight test to identify the blow holes
- Fig. 4 Flaw detection on end rings using ultrasonic tester
- Fig. 5 Conceptual design of rotor quality tester
- Fig. 6 Hardware set up of rotor quality test system
- Fig. 7 Parts of rotor quality test system
- Fig. 8 Model of electromagnet sensor arrangement with rotor
- Fig. 9 AC and DC flux lines and waveforms (top) in EM sensor
- Fig. 10 Development stages of electromagnet sensor
- Fig. 11 Aluminium sheets used for insulation in model (left) and sensor (right)
- Fig. 12 Gauss meter testing of electromagnet sensor
- Fig. 13 Electromagnet sensor with height and skew angle adjuster
- Fig. 14 Digitizer board connectivity with EM sensor and speed sensor
- Fig. 15 Rotor quality tester front panel created in NI LabVIEW software
- Fig. 16 Rotor quality test program sequence
- Fig. 17 Rotor fault inspection using FFT
- Fig. 18 Prototype rotor for testing RQTS
- Fig. 19 Prototype rotor with (a) no fault (b) broken bar (c) inter-laminar shor
- Fig. 20 Waveforms obtained in RQTS for various rotor faults
- Fig. 21 Inspection waveform chart of RQTS
7. Conclusion:
Summary of Key Findings:
The study successfully designed and implemented a Rotor Quality Test System (RQTS) for die-cast copper rotors. The RQTS, based on electro-magnetic induction and advanced signal processing, effectively detects a range of manufacturing defects in copper rotors through a three-stage inspection process. The system utilizes weight testing, ultrasonic flaw detection, and a dedicated rotor quality tester with FFT-based waveform analysis. Prototype testing validated the RQTS's capability to identify and classify various rotor faults, providing a comprehensive quality assessment.
Academic Significance of the Study:
This study contributes to the field of electrical motor manufacturing and quality control by providing a detailed methodology for non-destructive testing of die-cast copper rotors. It introduces a novel RQTS and signal analysis technique that can be used to evaluate rotor integrity directly in the production line. The research highlights the importance of dedicated testing systems for ensuring the quality and reliability of high-efficiency copper rotor motors, crucial for EV and industrial applications.
Practical Implications:
The developed RQTS has significant practical implications for die-cast copper rotor manufacturers. Implementing the three-stage inspection process, particularly the RQTS, can optimize manufacturing processes, reduce rotor rejection rates, and prevent the assembly of faulty rotors into motors. The RQTS serves as an "automatic accept/reject tester" and "is instrumental in diagnosing several manufacturing problems in the production line", enhancing the overall quality and reliability of copper rotor motors and reducing manufacturing costs associated with defects and failures.
Limitations of the Study and Areas for Future Research:
The paper does not explicitly detail limitations or future research areas within the conclusion section. However, based on the paper's content, potential limitations and future research directions could include:
- Further refinement and automation of the RQTS software and hardware for industrial-scale deployment.
- Expanding the RQTS capabilities to detect and quantify the severity of specific fault types more precisely.
- Investigating the correlation between RQTS test results and motor performance metrics to establish more definitive quality thresholds.
- Exploring the application of RQTS to other types of rotors and motor designs.
- Integrating the RQTS data with manufacturing process control systems for real-time process optimization and defect prevention.
8. References:
- [1] J.L. Kirtley, F. Schiferl, Dale T. Peters. and E.F. Brush, "The case for induction motors with die-cast copper rotors for high efficiency traction motors," in Proc. SAE International, 2009.
- [2] Dale T. Peters, "The die-cast copper motor rotor a new copper market opportunity," [online] Available: https://www.copper.org/environment /sustainable-energy/electric-motors/education/motor-rotor/pdf/die- cast _copper.pdf..
- [3] John G. Cowie, Dale T. Peters and David T. Brender, "Die-cast copper rotors for improved motor performance," Conf. Rec. 49th IEEE IAS Pulp and Paper Conference, Charleston, SC, June 2003.
- [4] Dale T.Peters, S.P. Midson, W.G. Walkington, E.F. Brush Jr. and J.G. Cowie, "Porosity control in copper rotor die castings," Trans. the North Amer. Die Casting Assoc. Congress, Indianapolis, 2003.
- [5] L.C. Packer, "Die-cast rotors for induction motors," AIEE Trans., vol. 68, 1949.
- [6] Dale T. Peters, J.G. Cowie, E.F. Brush and M. Doppelbauer, "Performance of motors with die-cast copper rotors in industrial and agricultural pumping applications," in Proc. IEEE Int. Conf. on Electric Machines and Drives, 2005.
- [7] M. Thieman, R. Kamm and J. Jorstad, "Copper motor rotors energy saving efficiency, now also economic feasibility," Electrical Insulation Conference and Electrical Manufacturing Expo, 2007.
- [8] Tom Bishop, "Squirrel cage rotor testing," in Proc. EASA Conv., San Francisco, CA, USA, Jun. 2003.
- [9] A. Bellini, F. Filippetti, C. Tassoni, and G. A. Capolino, "Advances in diagnostic techniques for induction machines," IEEE Trans. Industrial Electronics, vol. 55, no. 12, pp. 4109-4126, Dec. 2008.
- [10] R. Puche-Panadero, M. Pineda-Sanchez, M. Riera-Guasp, J. Roger-Folch, E. Hurtado-Perez, and J. Perez-Cruz, "Improved resolution of the MCSA method via Hilbert transform, enabling the diagnosis of rotor asymmetries at very low slip," IEEE Trans. Energy Conversion, vol. 24, no. 1, pp. 52-59, March 2009.
- [11] T. Ilamparithi and S. Nandi, "Detection of eccentricity faults in three phase reluctance synchronous motor," IEEE Trans. Industry Applications, vol. 48, no. 4, pp. 1307-1317, 2012.
- [12] Scott W. Clark and Daniel Stevens, "Induction motor rotor bar damage evaluation with magnetic field analysis," IEEE Trans. Industry Applications, vol. 52, no. 2, pp. 1469-1476, March/April 2016.
- [13] Sebastiao Lauro Nau, Daniel Schmitz and Waldiberto de Lima Pires, "Methods to evaluate the quality of stator and rotor of electric motors," in Proc. IEEE 10th Int. Symp. Diagn. Elect. Mach. Power Electron. Drives (SDEMPED), pp. 64–70, Sep. 1-4, 2015.
- [14] Soby T. Varghese, Bhim Singh and K. R. Rajagopal, "Fault investigations on die-cast copper rotors," in Proc. IEEE Int. Conf. PEDES, Trivandrum, Dec. 2016.
- [15] Soby T. Varghese, K.R. Rajagopal. "Design and development of rotor quality test system for die-cast copper rotors," in Proc. 1st IEEE Int. Conf. on Power Electronics, Intelligent Control and Energy Systems (ICPEICES), Delhi, July 2016.
9. Copyright:
- This material is "Soby T. Varghese, K. R. Rajagopal and Bhim Singh"'s paper: Based on "Design and Development of Rotor Quality Test System for Die-Cast Copper Rotors".
- Paper Source: DOI 10.1109/ΤΙΑ.2018.2792418
This material was created to introduce the above paper, and unauthorized use for commercial purposes is prohibited.
Copyright © 2025 CASTMAN. All rights reserved.