
Here is a list of products that are effective when manufactured using Cu (Copper) High Pressure Die Casting (HPDC). The effectiveness in terms of cost and performance can vary depending on complex interactions of factors beyond the manufacturing method, including material properties, design, application requirements, and cost considerations. However, these are the types of components where Cu HPDC can offer significant advantages.
Below is a list of components that could benefit from Cu HPDC manufacturing, considering the unique properties of copper (thermal conductivity, electrical conductivity, corrosion resistance, and mechanical properties):
- Thermal management requirements
- Electrical conductivity requirements
- Corrosion resistance requirements
- Mechanical property requirements
- Production volume considerations
- Complex geometric features
- Surface finish requirements
Potential Components Suitable for Cu HPDC Manufacturing
Thermal Management Components
Key Advantages of Manufacturing with Cu HPDC: For High Heat Dissipation Applications
Manufacturing with Cu HPDC (Copper High Pressure Die Casting) offers several key advantages, particularly for applications requiring high thermal management.
Excellent Thermal Conductivity:
- Efficient heat dissipation due to copper's high thermal conductivity (~400 W/mK).
- Approximately twice the thermal conductivity compared to aluminum (~200 W/mK).
Manufacturing Process Advantages:
- Enables the design of complex cooling channels.
- High dimensional accuracy.
- Excellent surface quality.
- High volume production capability.
Performance Advantages:
- Enables equivalent cooling performance with smaller form factors.
- Improved overall system efficiency.
- Enhanced long-term reliability.
- Superior resistance to thermal cycling.
Due to these characteristics, Cu HPDC can be a particularly effective manufacturing method for applications requiring high-performance thermal management.
- Heat sinks for power electronics
- CPU coolers and thermal modules
- LED lighting heat dissipation components
- Industrial process heat exchangers
- Automotive radiator end tanks
- Electric vehicle battery cooling plates
- Power supply cooling components
- Server cooling solutions
- Industrial chiller components
- Thermal interface blocks
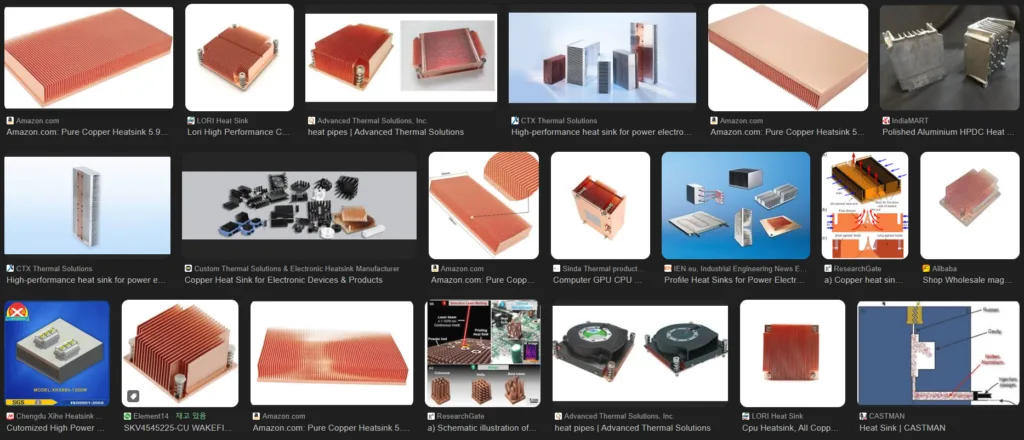
Electrical Components
Advantages of Using Copper (Cu) in Manufacturing
Copper is one of the metals with the highest electrical conductivity. This is essential for maximizing the efficiency of electrical components. Manufacturing with copper offers the following advantages:
- Low Resistance: Copper has a low resistance value, facilitating efficient current flow. This reduces power loss and enhances component efficiency.
- High Thermal Conductivity: Copper's excellent heat transfer properties allow for effective dissipation of heat generated by components. This mitigates overheating and promotes longevity.
- Excellent Machinability: Copper has excellent machinability, allowing for easy fabrication into diverse geometries. This is advantageous for manufacturing complex components.
- Good Resistance to Corrosion: Copper has good resistance to corrosion, which helps prevent performance degradation.
- High-current electrical connectors
- Bus bar components
- Circuit breaker housings
- Switchgear components
- Power distribution components
- Electric motor end shields
- Terminal blocks
- EMI/RFI shielding components
- Ground bus components
- Power converter housings
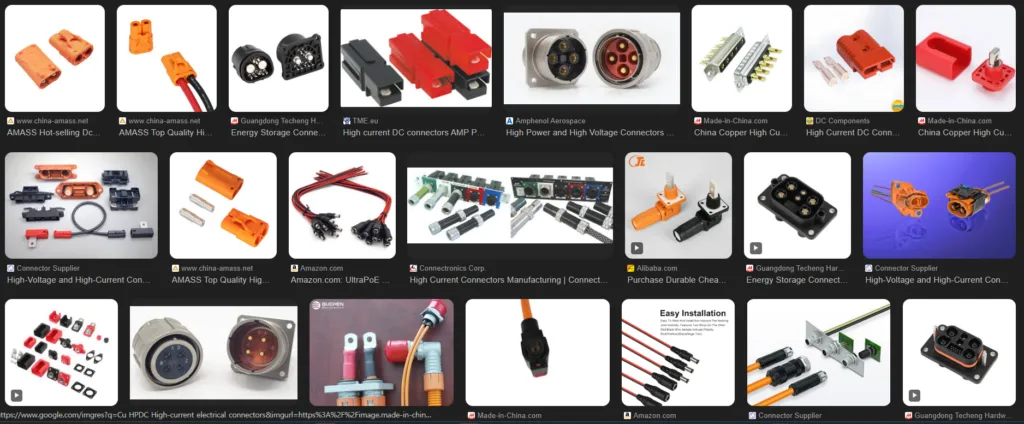
Automotive Applications
Key Advantages of Copper Die Casting
Copper offers several advantages over aluminum, especially in die casting applications.
- Superior Electrical Conductivity: Copper exhibits significantly higher electrical conductivity than aluminum. This is crucial for maximizing the efficiency of electrical components and minimizing power loss. For example, using copper in motor rotors or inverter components can lead to improved performance and miniaturization.
- Excellent Thermal Conductivity: Copper exhibits superior thermal conductivity compared to aluminum. This allows for efficient dissipation of heat generated by high-performance electrical components, extending their lifespan and mitigating performance degradation. For example, using copper in electric vehicle battery cooling systems or high-power LED lighting enables efficient thermal management.
- High Strength and Durability: Copper exhibits greater strength and durability compared to aluminum. This is beneficial for automotive components that are subjected to vibration and shock. For example, using copper in connectors and terminals can ensure reliable connections.
- Enhanced Corrosion Resistance: Copper offers enhanced corrosion resistance compared to aluminum, mitigating performance degradation due to corrosion. This is particularly important for components exposed to harsh external environments.
Examples of Copper Die Casting Applications in the Automotive Industry
- Electric Vehicle Motors and Inverters: High electrical conductivity maximizes motor efficiency and minimizes heat generation in inverters.
- Battery Connection Components and Cooling Systems: High electrical and thermal conductivity optimizes battery performance and ensures safety.
- High-Power Connectors and Terminals: High strength and durability ensure reliable electrical connections.
- LED Lighting: High thermal conductivity effectively dissipates heat generated by LEDs, extending their lifespan.
- Heat Exchangers and Radiators: High thermal conductivity maximizes cooling efficiency.
- Electric vehicle charging components
- Brake system components
- Transmission components
- Engine management system housings
- Electric motor housings
- Power steering components
- Hybrid vehicle power electronics housings
- Battery management system components
- Vehicle control unit housings
- Sensor housings
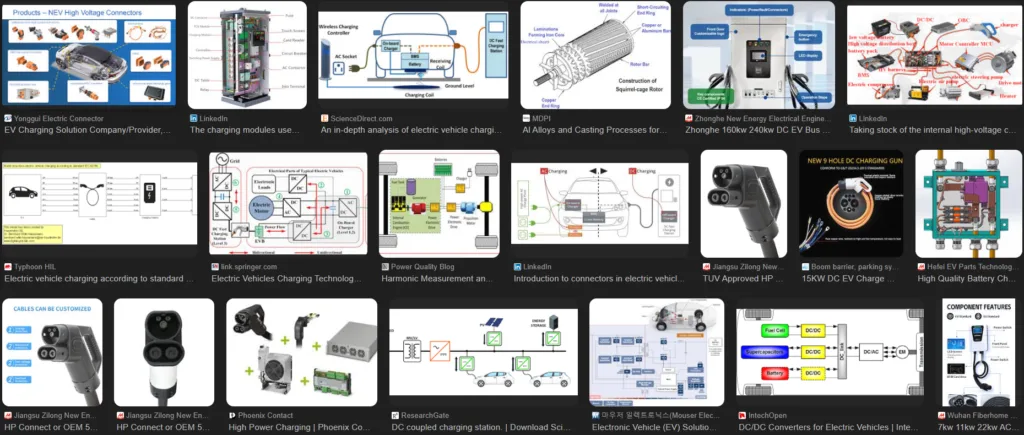
Industrial Equipment
Examples of Copper Die Casting Applications in Industrial Sectors
Copper die casting finds applications in various industrial sectors due to its advantageous properties. Here are some specific examples:
- High-Power Electric Motors and Alternators: High electrical conductivity enhances efficiency and reduces heat generation.
- Welding Equipment: High electrical and thermal conductivity improves welding performance and extends equipment lifespan.
- Transformers and Inductors: High electrical conductivity improves efficiency and allows for size reduction.
- Heat Exchangers and Cooling Systems: High thermal conductivity maximizes cooling efficiency.
- Power Transmission and Distribution Systems: High electrical conductivity minimizes power loss.
- High-Temperature Applications: High thermal conductivity prevents component overheating and extends lifespan.
- Pump housings
- Valve bodies
- Pneumatic system components
- Hydraulic system components
- Industrial robot components
- CNC machine components
- Bearing housings
- Gearbox components
- Compressor parts
- Industrial automation components
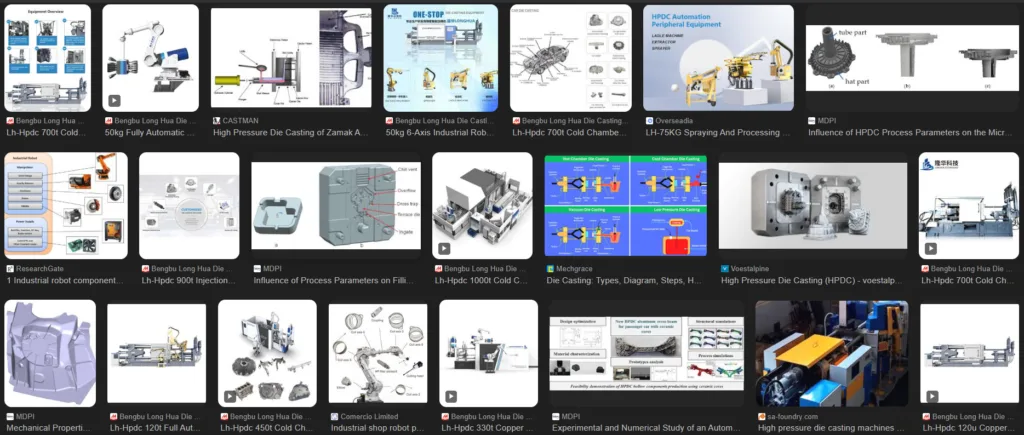
Marine and Corrosion-Resistant Applications
Examples of Copper Die Casting Applications in the Marine Sector
Copper die casting finds valuable applications in the marine sector due to its inherent properties. Here are some specific examples:
- Propellers, impellers, and other propulsion system components: Exhibits high corrosion resistance, strength, and biofouling resistance.
- Seawater valves and pumps: Ensures reliable performance in resisting saltwater corrosion.
- Marine heat exchangers and coolers: Provides high thermal conductivity and corrosion resistance.
- Submarine cable connectors: Offers high electrical conductivity and corrosion resistance.
- Components for offshore platforms and marine structures: Demonstrates high strength, durability, and corrosion resistance.
- Marine hardware components
- Underwater equipment housings
- Offshore platform components
- Ship propulsion system components
- Seawater cooling system parts
- Marine electrical enclosures
- Dock hardware components
- Marine sensor housings
- Watercraft components
- Submarine components

Aerospace and Defense
Examples of Copper Die Casting Applications in the Aerospace and Defense Sectors
Copper die casting plays a crucial role in the aerospace and defense industries due to its unique combination of properties. Here are some specific applications:
- Radar antenna components: Exhibit high electrical conductivity and shielding effectiveness.
- Components for missile guidance systems: Deliver high accuracy, strength, and durability.
- Aircraft power distribution components: Provide excellent electrical and thermal conductivity.
- Components for spacecraft thermal control systems: Ensure high thermal conductivity.
- Components for military communication systems: Provide high shielding effectiveness and robust durability.
- Aircraft cooling system components
- Avionics housings
- Radar system components
- Communication equipment housings
- Military vehicle components
- Satellite components
- Guidance system housings
- Power distribution units
- Electronic warfare components
- Aircraft structural components
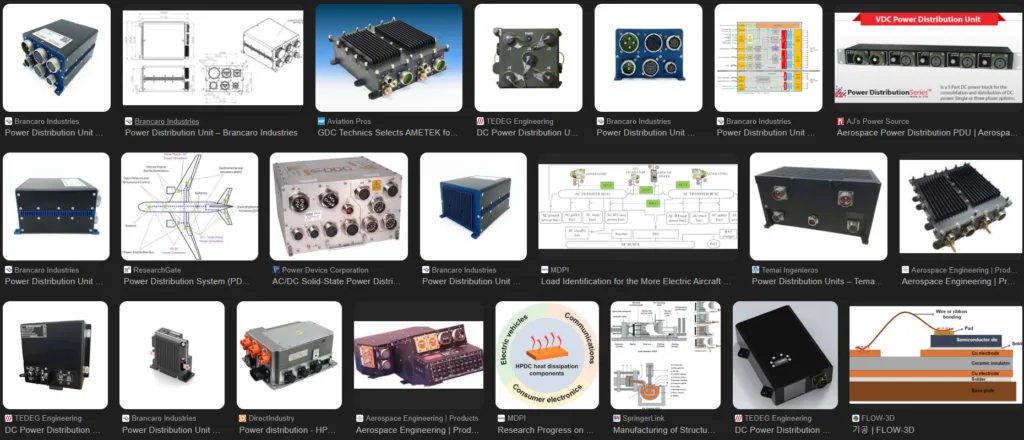
Renewable Energy
Examples of Copper Die Casting Applications in Renewable Energy
Copper die casting offers significant advantages in renewable energy applications due to its unique properties. Here are some specific examples:
- Solar panel busbars and interconnect ribbons: Maximize energy conversion efficiency due to high electrical conductivity.
- Wind turbine generator windings and power converters: Maximize power generation efficiency and minimize power losses due to high electrical conductivity.
- Geothermal power plant heat exchangers: Optimize heat transfer due to high thermal conductivity.
- Battery terminals, busbars, and thermal management systems: Enhance battery performance and ensure battery safety due to high electrical and thermal conductivity.
- Solar inverter housings
- Wind turbine components
- Fuel cell system components
- Energy storage system parts
- Power conversion equipment
- Thermal management systems
- Generator components
- Smart grid components
- Battery system components
- Power conditioning units
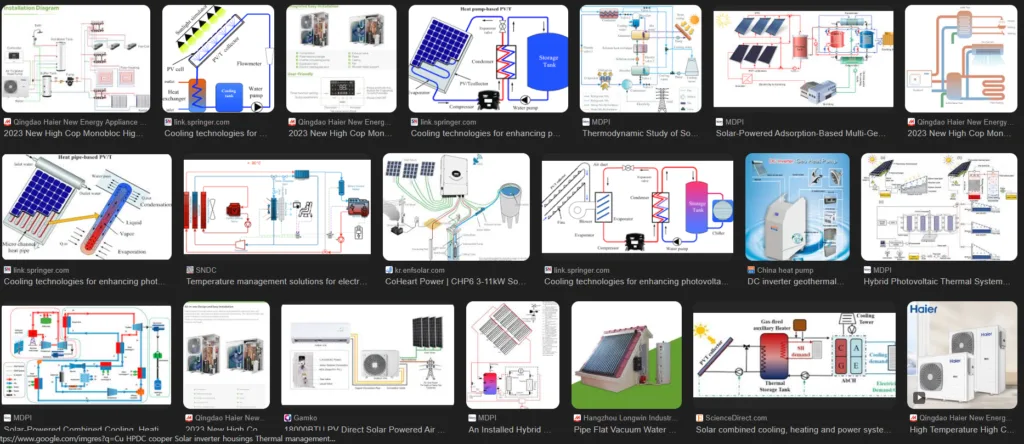
Medical Equipment
Examples of Copper Die Casting Applications in the Medical Field
Copper die casting plays a valuable role in the medical field due to its unique material characteristics. Specific applications include:
- Surgical instruments: Exhibit antimicrobial properties, high strength, and durability, contributing to sterile and reliable surgical procedures.
- Medical implants: Offer biocompatibility and corrosion resistance, essential for long-term implant performance within the human body.
- Electrodes and connectors for diagnostic equipment: Provide high electrical conductivity, ensuring accurate and reliable diagnostic measurements.
- Heat sinks for laser surgical equipment: Offer excellent thermal conductivity, effectively dissipating heat and maintaining optimal equipment performance.
- Dental instruments and equipment: Exhibit antimicrobial properties and corrosion resistance, crucial for maintaining hygiene and preventing contamination in dental practices.
- Imaging equipment components
- Surgical instrument parts
- Medical device housings
- Sterilization equipment components
- Laboratory equipment parts
- Medical cooling system components
- Diagnostic equipment housings
- Treatment delivery system components
- Medical robot components
- Patient monitoring system housings
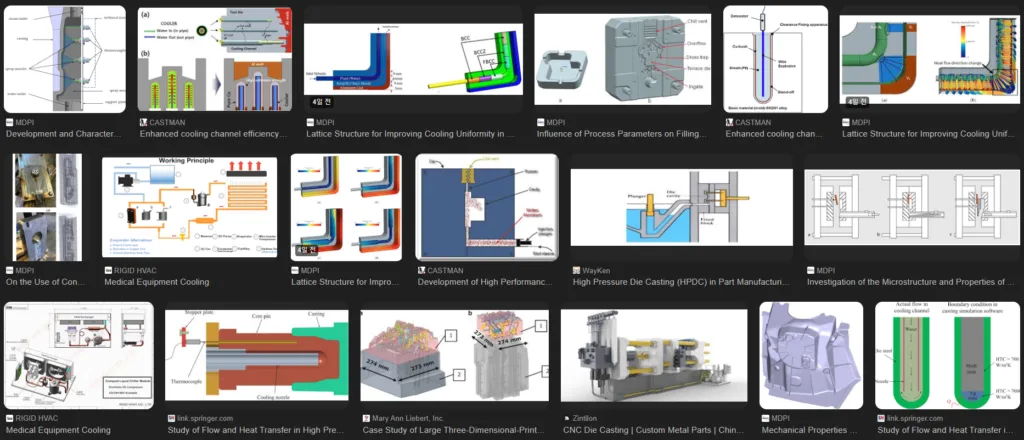
Communications Infrastructure
Examples of Copper Die Casting Applications in the Telecommunications Industry
Copper die casting plays a crucial role in the telecommunications industry, enabling the production of high-performance components. Specific applications include:
- Base station antennas and RF components: Exhibit high electrical conductivity and excellent electromagnetic shielding effectiveness, crucial for efficient high-frequency signal transmission and minimizing signal interference.
- Connectors for high-speed communication cables: Provide high electrical conductivity, minimizing signal loss and ensuring efficient data transmission.
- Heat sinks for communication equipment: Offer superior thermal conductivity, effectively dissipating heat generated by electronic components and ensuring reliable operation.
- Components for fiber optic communication equipment: Require precision machining and offer high durability, ensuring reliable performance in demanding environments.
- Base station components
- Network equipment housings
- Data center cooling components
- Antenna system parts
- Signal amplifier housings
- Router/switch housings
- Telecommunication cabinets
- Fiber optic equipment housings
- Satellite communication components
- Broadcasting equipment parts
Consumer Products
Examples of Copper Die Casting Applications in Consumer Products
Copper die casting offers a range of benefits for consumer products, leveraging its unique material properties. Specific applications include:
- Cookware: Facilitates rapid and uniform heat distribution for optimal cooking performance.
- Bathroom fixtures: Combines antimicrobial properties and corrosion resistance for hygienic and durable performance.
- Lighting fixtures: Enhance aesthetics with a premium finish while providing efficient heat dissipation.
- Watch cases and accessories: Combine a premium appearance with exceptional durability.
- Furniture hardware: Offer a premium aesthetic and exceptional strength.
- Tools: Exhibit high strength and robustness for demanding use.
- High-end appliance components
- Professional kitchen equipment
- Audio equipment heat sinks
- Gaming console cooling systems
- Professional camera components
- High-performance computer parts
- Professional tool components
- Home automation system parts
- Professional audio equipment
- High-end lighting components

Note: The suitability of Cu HPDC for these components depends on:
- Specific design requirements
- Production volumes
- Surface finish requirements
- Total manufacturing costs
- Alternative manufacturing process comparison
- End-use specific requirements
- Thermal and electrical conductivity needs
- Mechanical property requirements
- Corrosion resistance requirements
- Cost-effectiveness of the overall solution