This article introduces the paper "Cradle-to-Gate Impact Assessment of a High-Pressure Die-Casting Safety-Relevant Automotive Component".
1. Overview:
- Title: Cradle-to-Gate Impact Assessment of a High-Pressure Die-Casting Safety-Relevant Automotive Component
- Authors:
- Silvia Cecchel
- Giovanna Cornacchia
- Andrea Panvini
- Publication Year: 2016
- Journal/Conference: JOM (The Minerals, Metals & Materials Society)
- Keywords:
- Life cycle assessment (LCA)
- High-pressure die casting (HPDC)
- Aluminum
- Automotive component
- Energy analysis
2. Research Background:
- Social/Academic Context of the Research Topic:
- Lightweighting of automotive components has become increasingly important for economic and environmental reasons.
- Reducing vehicle mass directly improves fuel consumption and reduces emissions.
- There is a growing trend to adopt low-density materials like aluminum alloys in vehicles, replacing conventional steel and cast iron parts.
- The automotive industry has exponentially increased the use of aluminum alloys, and this trend is expected to continue.
- Aluminum automotive components are mainly produced in wrought or cast forms, with high-pressure die casting (HPDC) being the most prevalent process for high-volume production.
- HPDC efficiently manufactures near-net shape lightweight aluminum parts, achieving a 30% to 50% weight reduction compared to steel.
- To evaluate the real environmental benefit, a proper life cycle assessment (LCA) considering the entire product lifecycle is necessary.
- Life cycle analysis (LCA) is a tool to study the environmental burden of products at all stages, from resource extraction to disposal, including manufacturing, use, and end-of-life.
- One of the key roles of LCA is to support correct eco-design.
- While using aluminum reduces vehicle weight and fuel consumption, aluminum alloy component production may require more energy.
- Limitations of Existing Research:
- While many LCA studies exist for automotive components, few detail the real parts' production processes.
- Dalquist et al. (16) provided general information based on aggregate national data and representative machines, lacking accuracy for specific component production evaluation.
- Singh et al. (17) developed a model for die-casting part sustainability at the design stage, but analyzed only a small part of manufacturing (melting and holding) based on theoretical equations.
- Gunasegaram et al. (18) compared aluminum and magnesium production for a small component (converter housing, ~3 kg), which is not applicable to larger, safety-relevant automotive components like the one in this study (~15 kg) that require different process parameters and tooling.
- Necessity of Research:
- Aluminum HPDC process involves energy-intensive manufacturing phases requiring step-by-step evaluation.
- Accurate environmental impact assessment of automotive components requires in-depth analysis based on real data.
- Environmental impact assessment of critical components like safety-relevant automotive parts is particularly important.
3. Research Objectives and Research Questions:
- Research Objective:
- To assess the cradle-to-gate environmental impact of producing a safety-relevant aluminum high-pressure die-casting component (suspension cross-beam) for commercial vehicles.
- To develop and apply an LCA model evaluating environmental impact in terms of energy use.
- To analyze the environmental benefits of aluminum recycling.
- Core Research Questions:
- What is the energy consumption of each stage in the production of a safety-relevant aluminum HPDC automotive component?
- What is the impact of aluminum recycling on the overall energy consumption?
- What are the potential improvements to reduce the environmental burden of aluminum HPDC component production?
- Research Hypotheses:
- The primary aluminum production stage will be the most energy-intensive phase in aluminum HPDC component production.
- Aluminum recycling will significantly reduce overall energy consumption.
4. Research Methodology:
- Research Design:
- Cradle-to-gate LCA methodology, following ISO 14040:2006 standard.
- Cumulative energy use assessment method.
- Development and application of a new LCA model.
- Data Collection Methods:
- Primary data collected from actual production sites through collaborations with automotive supplier companies.
- EAA (European Aluminium Association) data for raw material extraction to primary aluminum ingot stages.
- Literature review and industry databases.
- Analysis Methods:
- LCA model construction based on collected data.
- Calculation and analysis of energy consumption for each stage.
- Aluminum recycling scenario analysis.
- Comparison of energy consumption (with and without recycling).
- Research Subjects and Scope:
- Target component: Aluminum HPDC suspension cross-beam for commercial vehicles (safety-relevant).
- Functional unit: Production batch of 250 units of HPDC aluminum suspension beams.
- System boundary: Cradle-to-gate (raw material extraction, primary aluminum ingot realization, component casting, finishing, recycling).
- Process stages:
- Raw material extraction to primary aluminum ingot: Bauxite mining, alumina production (Bayer process), aluminum electrolysis (Hall-Héroult process), cast house.
- Primary aluminum ingot to component casting: Melting, holding, casting (HPDC).
- Finishing: 5-axis machining.
- Recycling: Aluminum scrap recycling.
5. Key Research Findings:
- Core Research Findings:
- Primary aluminum production stage accounts for the largest share of total energy consumption (Table I, Fig. 2).
- Component casting stage is the second largest energy-consuming stage (Table I, Fig. 2).
- Energy contribution of the finishing operation is negligible (Table I, Fig. 2).
- Aluminum recycling (EOL stage) recovers approximately 42% of the total energy consumption (Table I, Fig. 3, Fig. 4).
- Statistical/Qualitative Analysis Results:
- Table I. Energy by life cycle stages:
- Primary aluminum: 68,211 kWh
- Casting: 15,005 kWh
- Finishing: 800 kWh
- EOL: -47,751 kWh
- Total: 84,016 kWh
- Total EOL: 36,265 kWh
- High energy consumption in primary aluminum production is closely related to the liquid aluminum electrolysis process.
- The casting stage accounts for about 18% of the total energy, demonstrating the energy intensity of the casting process.
- Aluminum recycling significantly contributes to energy recovery.
- Table I. Energy by life cycle stages:
- Data Interpretation:
- Environmental impact of aluminum HPDC components is mainly driven by the primary aluminum production stage.
- The casting process also has significant energy consumption, requiring efforts to improve process efficiency.
- Increasing aluminum recycling rates is highly effective in reducing environmental impact.
- Figure Name List:
- Fig. 1. Life cycle assessment flow-chart.
- Fig. 2. Energy by life cycle stages without EOL.
- Fig. 3. Energy by life cycle stages with EOL.
- Fig. 4. Total energy comparison.
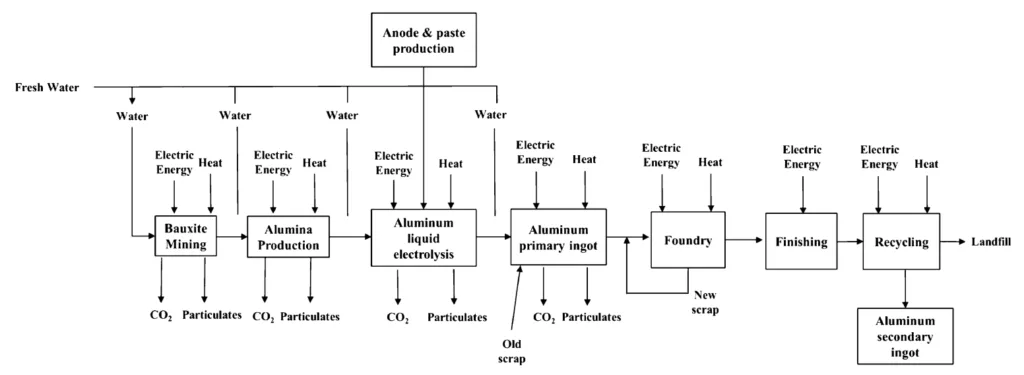
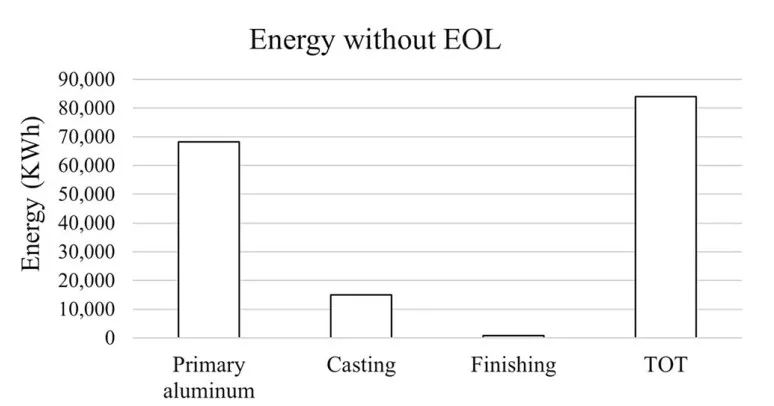
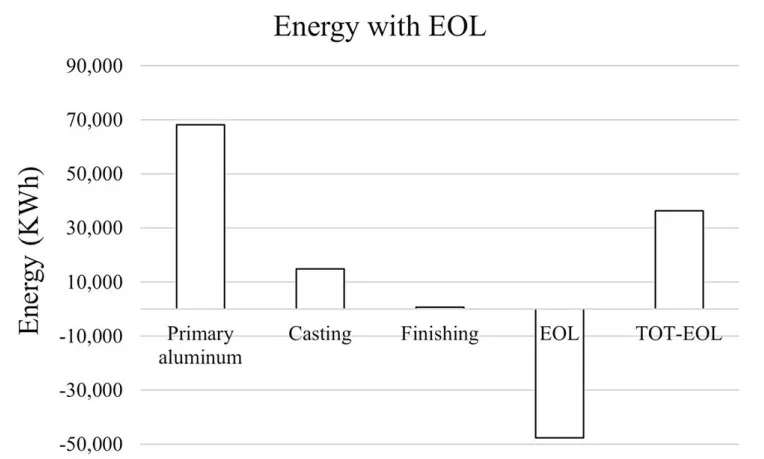
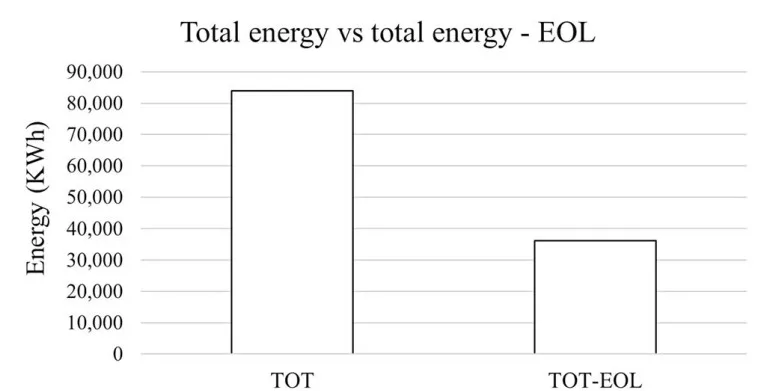
6. Conclusion and Discussion:
- Summary of Main Findings:
- This study performed a cradle-to-gate LCA of an aluminum HPDC suspension cross-beam for commercial vehicles, analyzing energy consumption.
- Primary aluminum production is the most energy-intensive stage, followed by the component casting stage.
- Energy consumption of the finishing stage is negligible.
- Aluminum recycling recovers a significant portion of total energy consumption, providing environmental benefits.
- Academic Significance of the Research:
- Provides an in-depth analysis of the environmental impact of the aluminum HPDC process.
- Presents a case study of developing and applying an LCA model based on real industry data.
- Quantitatively demonstrates the importance of aluminum recycling.
- Practical Implications:
- Increasing aluminum recycling rates is crucial to reduce the environmental impact of aluminum HPDC component production.
- Technology development and application to improve the energy efficiency of the casting process are needed.
- LCA results should be considered from the product design stage to promote eco-friendly design.
- Limitations of the Research:
- This study is a case study for a specific aluminum HPDC component, and generalization to other components or processes may be limited.
- LCA model data is based on data from a specific time and company, and results may vary with temporal and regional changes.
- This study only evaluated environmental impact in terms of energy consumption, and other environmental impact categories (e.g., global warming, resource depletion) were not considered.
7. Future Follow-up Research:
- Directions for Future Research:
- Expand LCA research to various types of aluminum HPDC components and processes.
- Conduct LCA evaluations including other environmental impact categories beyond energy consumption.
- Develop energy efficiency improvement technologies for the casting process and evaluate them based on LCA.
- Study methods to improve the efficiency of aluminum recycling systems.
- Comparative environmental impact studies between aluminum HPDC and other manufacturing methods (e.g., steel press forming) (as mentioned in the paper for future works).
- Areas Requiring Further Exploration:
- Optimization of aluminum HPDC process and energy-saving technologies.
- Policies and technology development to increase aluminum recycling rates.
- Continuous improvement of LCA methodology and expansion of databases.
8. References:
- H. Helms and U. Lambrecht, Int. J. LCA (2006). doi:10. 1065/lca2006.07258.
- S. Das, JOM 52, 41 (2000).
- J. Hirsch, Mater. Forum 28, 15 (2004).
- J. Kasai, JSAE Rev. 20, 387 (1999).
- G.S. Cole and A.M. Sherman, Mater. Charact. 35, 3 (1995).
- S.W. Hadley, S. Das, and J.W. Mille, Oak Ridge National Laboratory (2000). doi:10.2172/814613.
- A.A. Luo, A.K. Sachdev and B.R. Powell, China Foundry 7, 463 (2010).
- D.R. Gunasegaram and A. Tharumarajah, Metal. Trans. B 40, 605 (2009).
- J.B. Guine´e, Int. J. Life Cycle Assess. 7, 311 (2002).
- International Standard Organisation (ISO), ISO14040: Environmental Management—Life Cycle Assessment: Principles and Framework (Geneva: ISO, 2006), pp. 1–20.
- J. Green, Aluminum Recycling and Processing for Energy Conservation and Sustainability (Novelty, OH: ASM International, 2007), pp. 1–14.
- H.C. Kim and T.J. Wallington, Environ. Sci. Technol. 47, 6089 (2013).
- H. Kim, C. McMillan, G.A. Keoleian and S.J. Skerlos, J. Ind. Ecol. 14, 929 (2010).
- C. Wagner, J. Provo, and C. Koffler, Comparative Life Cycle assessment of Aluminum and Steel Truck Wheels (Alcoa, 2012). http://www.alcoawheels.com/alcoawheels/north_ america/en/pdf/Alcoa_Comparative_LCA_of_Truck_ Wheels_with_CR_statement.pdf. Accessed 20 Sept 2012.
- C.A. Ungureanu, S. Das and I.S. Jawahir, in Aluminum Alloys Transport, Package, Aerospace. Other Applications, Proceedings Symposium, ed. S.K. Das and W. Yin (Warrendale, PA: TMS, 2007), pp. 11–24.
- S. Dalquist and T. Gutowski, Life Cycle Analysis of Conventional Manufacturing Techniques: Die Casting (Massachusetts Institute of Technology, Paper no. LMPMIT-TGG-03-12-09-2004). http://web.mit.edu/ebm/Publica tions/Die%20Casting%20Dalquist%20Gutowski.pdf. Accessed 8 June 2014.
- R. Singh, C.D. Singh and S. Singh Sidhu, IJMDEBM 1, 21 (2013).
- D.R. Gunasegaram and A. Tharumarajah, Metal. Trans. B 40B, 605 (2009).
- F. Mathieux and D. Brissaud, Resour. Conserv. Recycl. 55, 92 (2010).
- European Aluminium Association, Environmental Profile Report for the European Aluminium Industry (European Aluminum Association, 2013). http://european-aluminium. eu/media/1329/environmental-profile-report-for-the-eur opean-aluminium-industry.pdf. Accessed Apr 2013.
- C. Panseri, Manuale di fonderia dell’alluminio (Milan, IT: Hoelpi, 1966), p. 439.
- S. Nagendra Parashar and R.K. Mittal, in Elements of Manufacturing Processes (New Delhi, IN: Prentice-Hall of India Private Limited, 2006), p. 233.
- H. Bakemeyer, Report No. E-902 (NADCA, Arlington Heights, IL, 2008).
- M. Bertram, M. Hryniuk, G. Kirchner and F. Pruvost, Aluminium Recycling in Europe (Brussels, BL: EAA/OEA Recycling Division), p. 1.
- R. Dhingra and S. Das, J. Clean. Prod. 85, 347 (2014).
9. Copyright:
- This material is based on the paper: Cradle-to-Gate Impact Assessment of a High-Pressure Die-Casting Safety-Relevant Automotive Component by Silvia Cecchel, Giovanna Cornacchia, and Andrea Panvini.
- Paper Source: DOI: 10.1007/s11837-016-2046-3
This material is a summary based on the above paper, and unauthorized use for commercial purposes is prohibited.
Copyright © 2025 CASTMAN. All rights reserved.
Cradle-to-Gate Impact Assessment of a High-Pressure Die-Casting Safety-Relevant Automotive ComponentDownload