This article introduces the paper "Correlation Between Microstructure and Mechanical Properties of Al-Si Diecast Engine Blocks"
1. Overview:
- Title: Correlation between microstructure and mechanical properties of Al-Si diecast engine blocks
- Authors: Fabio Grosselle, Giulio Timelli, Franco Bonollo, Roberto Molina
- Publication Year: 2009
- Published Journal/Conference: Metallurgical Science and Technology
- Keywords:
- Aluminium alloys
- EN-AC 46000
- High-pressure die-casting
- SDAS
- Eutectic Si
- Microstructure
- Engine block
2. Research Background:
- Social/Academic Context of the Research Topic:
- In passenger vehicles, cylinder blocks are the heaviest components, significantly impacting fuel efficiency and vehicle drivability.
- Aluminum alloy castings are increasingly used in modern passenger cars to reduce weight and emissions.
- Replacing cast iron with aluminum alloys in cylinder blocks can reduce weight by up to 45% for gasoline engines.
- Aluminum alloys offer higher thermal conductivity, enabling engines to deliver more power per cylinder size due to better temperature control.
- High-pressure die-casting (HPDC) is widely used for mass-produced engine blocks due to its ability to create complex shapes with thin walls at high production rates, reducing costs.
- Hypoeutectic secondary Al-Si alloys are commonly used in HPDC due to their excellent castability, good mechanical properties, and low cost.
- Limitations of Existing Research:
- HPDC parts can have defects like shrinkage cavities, cold fills, oxide films, dross, and entrapped air bubbles due to the complexity of casting shapes and process parameter variability.
- Microstructure in Al-Si castings, including the distribution, morphology, and dimensions of primary α-Al and eutectic Si particles, is influenced by cooling conditions and solidification history.
- Moving from the die wall to the center of a casting, the microstructure becomes coarser, and defects can form more easily due to filling dynamics and longer solidification times.
- The presence of Cu, Mg, and tramp elements can lead to the formation of other phases, including strengthening precipitates and iron-rich intermetallics.
- Necessity of the Research:
- Understanding the correlation between microstructure and mechanical properties is crucial for optimizing the performance and reliability of Al-Si die-cast engine blocks.
- Process parameters, microstructure features, and defects all contribute to the final mechanical properties of aluminum alloys.
- In defect-free components, fracture initiates by cleavage of brittle intermetallic or eutectic Si particles and propagates along grain boundaries or cell boundaries depending on SDAS values.
- Defects can decrease mechanical properties by affecting fracture initiation and propagation.
- There is a need to analyze the relationship between microstructural features like SDAS, eutectic Si particle size and morphology, and mechanical properties in HPDC engine blocks.
3. Research Objectives and Research Questions:
- Research Objective:
- To analyze the correlation between microstructure and mechanical properties of a HPDC engine block.
- Specifically, to correlate mechanical properties with microstructural features such as Secondary Dendrite Arm Spacing (SDAS), size, and morphology of eutectic Si particles.
- Core Research Questions:
- How do microstructural features (SDAS, eutectic Si particle size and morphology) in a HPDC Al-Si alloy engine block correlate with mechanical properties (UTS and elongation to fracture)?
- What is the effect of solidification rate and cooling conditions on the microstructure and mechanical properties of the engine block?
- Can a quantitative relationship be established between microstructural parameters and mechanical properties in these die-cast components?
- Research Hypothesis:
- Mechanical properties, particularly UTS and elongation to fracture, are significantly influenced by the microstructure of the Al-Si die-cast engine block.
- Finer microstructures, characterized by low SDAS values and small, compact eutectic Si particles, will exhibit superior mechanical properties.
- A linear correlation exists between UTS and the product of SDAS, equivalent diameter, and aspect ratio of Si particles, while elongation to fracture shows an exponential trend with microstructural variations.
4. Research Methodology:
- Research Design:
- Exhaustive analysis of a HPDC 4-cylinder-in-line engine block made of secondary AlSi9Cu3 foundry alloy (EN AC-46000-UNI EN 1706 alloy).
- Correlation study between mechanical properties and microstructural features across different locations within the engine block casting.
- Data Collection Methods:
- Chemical Composition Analysis: Measured on separately poured samples using unspecified methods (Table 1).
- Thermal Analysis: Liquidus temperature (Tliq = 585°C) determined by thermal analysis.
- Radiographic Inspection: Carried out to detect macrodefects throughout the castings.
- Mechanical Testing:
- Tensile tests using flat tensile test bars machined from different locations of sectioned engine blocks, according to ASTM-B577.
- Yield Stress (YS), Ultimate Tensile Strength (UTS), and Elongation to Fracture (Sf) were measured using a computer-controlled tensile testing machine MTS 810 with a crosshead speed of 2 mm/min (strain rate ~10⁻³ s⁻¹).
- Vickers microhardness measurements on ground and polished samples using loads of 0.2 kgf and a 30-second dwell period, according to ASTM E-384.
- Microstructural Analysis:
- Optical microscopy and Scanning Electron Microscopy (SEM) with Energy-Dispersive Spectrometer (EDS).
- Quantitative image analysis using an image analyzer to measure:
- Secondary Dendrite Arm Spacing (SDAS) using the linear intercept method.
- Eutectic silicon particle size (equivalent circle diameter, d) and aspect ratio (α).
- Analysis Methods:
- Statistical analysis of experimental data, averaging best values to minimize effects of casting defects.
- Correlation analysis to determine the relationship between microstructural parameters (SDAS, eutectic Si particle size and aspect ratio) and mechanical properties (UTS, Sf, Microhardness).
- Regression analysis to establish the type of correlation (linear, exponential) and calculate the coefficient of determination (R²) to assess the quality of fit.
- Research Subjects and Scope:
- HPDC 4-cylinder-in-line engine blocks produced using a cold chamber die-casting machine with dynamic shot control and vacuum system.
- Material: Secondary AlSi9Cu3 alloy (EN AC-46000-UNI EN 1706 alloy).
- Focus on correlating microstructure and mechanical properties within different regions of the engine block casting, considering variations in solidification conditions.
5. Key Research Findings:
- Core Research Results:
- Mechanical properties of the HPDC engine block are significantly affected by microstructure.
- Finer microstructures, achieved with higher solidification rates (e.g., near casting walls and in thin sections), exhibit higher UTS and elongation to fracture.
- Coarser microstructures, resulting from slower solidification (e.g., in thicker sections and bulkhead supports), show lower mechanical properties and increased presence of defects.
- UTS and elongation to fracture decrease with increasing SDAS and eutectic Si particle size.
- A linear correlation was found between UTS and the product of SDAS, equivalent diameter, and aspect ratio of eutectic Si particles.
- Elongation to fracture shows an exponential decrease with increasing SDAS and eutectic Si particle size, indicating a higher sensitivity to microstructural variations compared to UTS.
- Statistical/Qualitative Analysis Results:
- Radiographic inspection showed good casting integrity with minimal critical defects, attributed to the vacuum system. Small macroporosity was observed in circular sections, bulkhead supports, and beneath liners, especially near the vacuum line.
- Microstructure varied across the casting:
- Near the wall: finer, porosity-free microstructure.
- Towards the center: coarser microstructure, larger α-Al phase, coarser eutectic Si particles, and more defects.
- α-Al phase morphology: equiaxed globular near the wall, dendritic towards the center.
- Eutectic Si morphology: fibrous and fine near the wall, coarse plate-like in thicker sections.
- Microhardness decreased from the edge towards the center of the casting section.
- YS values showed no significant variation across different zones.
- UTS and elongation to fracture values were higher in regions between cast iron liners (UTS: 274±10MPa, Elongation: 2.5±0.4%) compared to zones underneath liners and bulkhead supports (UTS: 236 MPa, Elongation: 1.4%).
- Coefficient of determination (R²) for the correlation between UTS and SDAS, and elongation to fracture and SDAS was 0.52.
- R² for the correlation between UTS and eutectic Si particle size, and elongation to fracture and eutectic Si particle size were 0.83 and 0.89 respectively.
- R² for the correlation between UTS and the combined parameter (SDAS x Eq. diameter x Asp. Ratio) was 0.50, and for elongation to fracture was 0.55.
- Data Interpretation:
- Solidification rate and cooling conditions are primary factors influencing microstructure and consequently mechanical properties.
- Finer microstructure, achieved through rapid solidification, enhances mechanical strength and ductility.
- Eutectic Si particle size and morphology have a more pronounced effect on elongation to fracture than UTS.
- Combined effect of SDAS and eutectic Si particle characteristics provides a comprehensive understanding of their influence on mechanical properties.
- Figure Name List:
- Fig. 1: Illustration of engine block with 6 ingates and the vacuum channels.
- Fig. 2: Position from which tensile specimens were machined.
- Fig. 3: Radiographic image of the bulkhead support showing the presence of porosity.
- Fig. 4: Microstructure in correspondence of a thick section.
- Fig. 5: Eutectic silicon particles with (a) fibrous and (b) lamellar shape in the zones with high and low cooling rates respectively.
- Fig. 6: Average diameter and aspect ratio of the eutectic Si particles as a function of SDAS.
- Fig. 7: Microstructure of die-cast AlSi9Cu3 engine block.
- Fig. 8: Vickers microharness measured along the cross section of a specimen.
- Fig. 9: (a) Oxide inclusions and films, (b) porosities and (c) cold shots observed in diecastings.
- Fig. 10: Segregation bands of eutectic silicon in regions with low solidification rate.
- Fig. 11: UTS and elongation to fracture as function of SDAS.
- Fig. 12: UTS and elongation to fracture as function of equivalent diameter of the eutectic Si particles.
- Fig. 13: UTS and elongation values as function of the combined parameter SDAS x Equivalent diameter x Aspect ratio of eutectic Si particles.
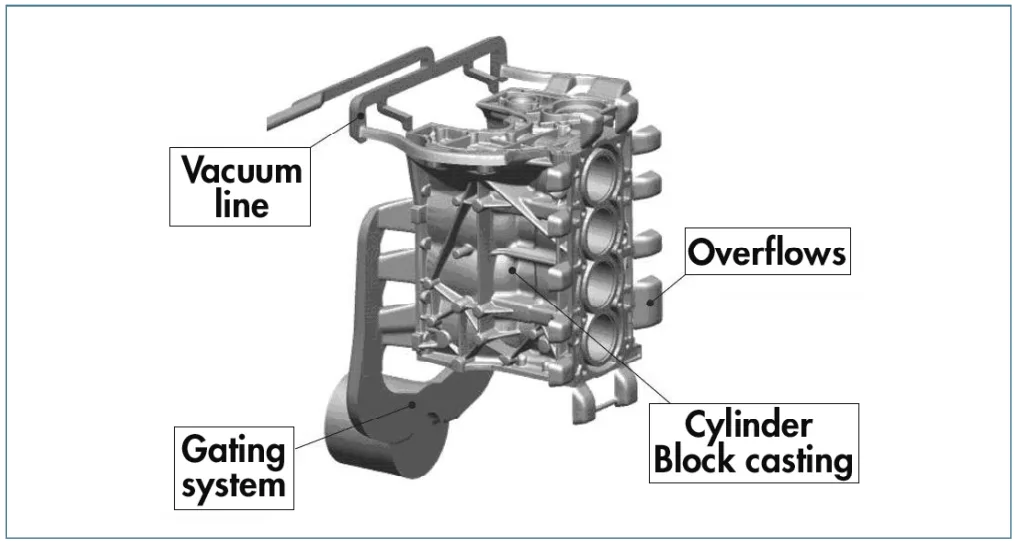
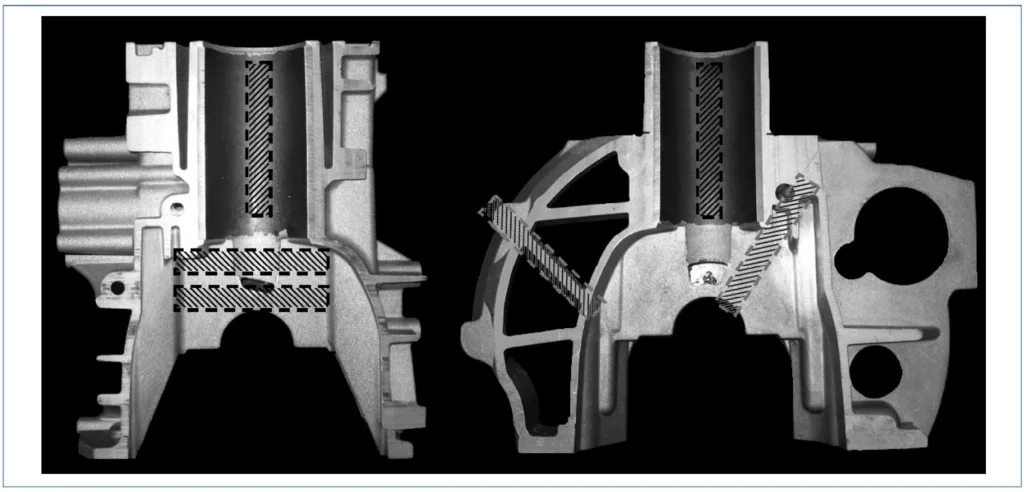
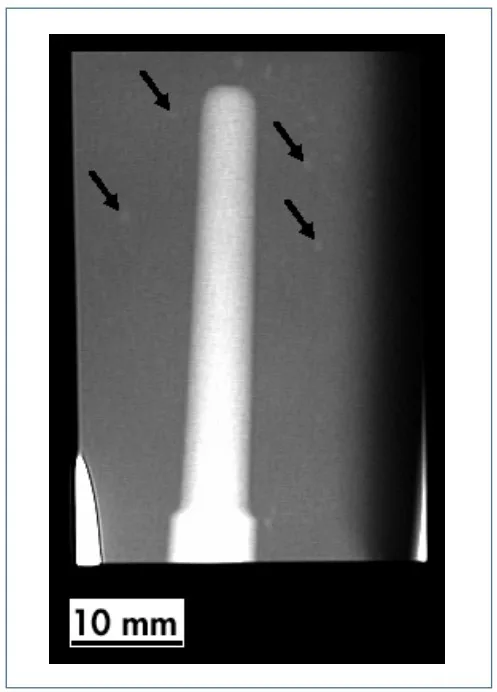
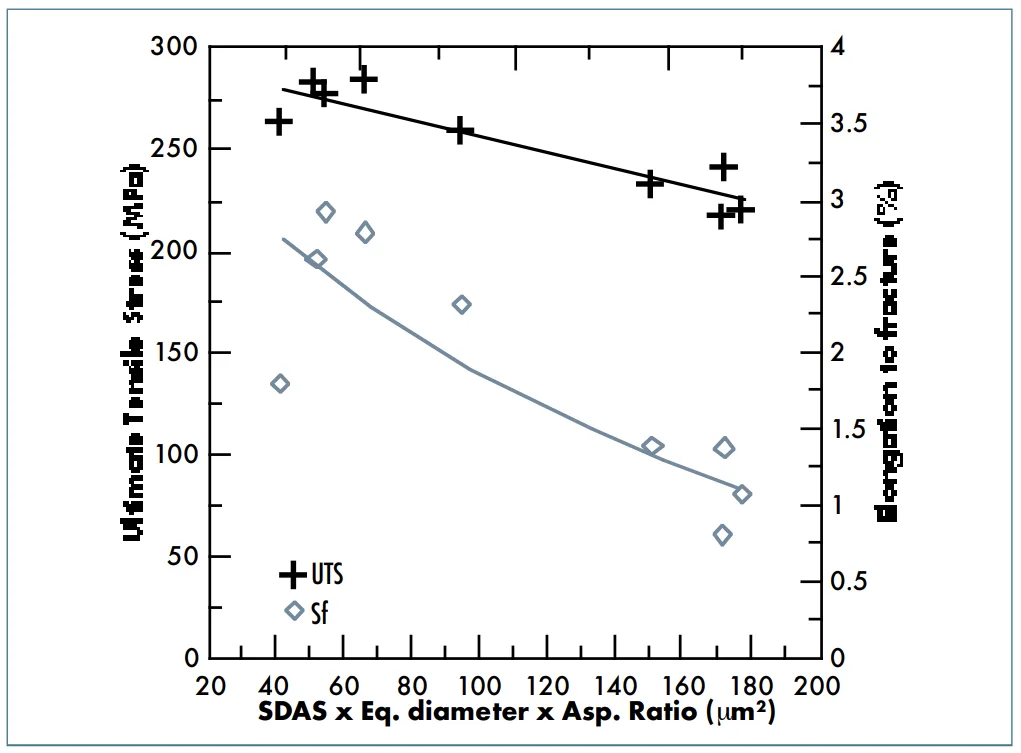
6. Conclusion and Discussion:
- Summary of Main Findings:
- Microstructure and mechanical properties of a HPDC 4-cylinder-in-line cylinder block are strongly correlated.
- Higher solidification rates lead to finer microstructures and improved mechanical properties (UTS and elongation to fracture).
- Increased solidification time results in coarser microstructures with larger SDAS, coarser eutectic Si particles, and a higher fraction of blocky-like α-Al(Mn, Fe, Cr)Si phase, leading to reduced mechanical properties.
- Mechanical properties are affected by microstructure, with best UTS and elongation values obtained for low SDAS and small, compact eutectic Si particles.
- A coarser microstructure and higher defect amount decrease alloy strength and promote fracture nucleation.
- A linear correlation exists between UTS and the combined parameter of SDAS, eutectic Si particle size and aspect ratio, while elongation to fracture shows an exponential sensitivity to these microstructural variations.
- Academic Significance of the Research:
- The study provides quantitative data and correlations between key microstructural features (SDAS, eutectic Si particle characteristics) and mechanical properties (UTS, elongation to fracture) in HPDC Al-Si alloy engine blocks.
- It enhances the understanding of how solidification conditions and microstructure influence the performance of die-cast aluminum components.
- The research highlights the importance of controlling solidification rate and microstructure to optimize mechanical properties in HPDC parts.
- Practical Implications:
- The findings can guide the optimization of HPDC process parameters (e.g., die temperature, injection speed, cooling strategies) to achieve desired microstructures and mechanical properties in engine blocks and similar components.
- Controlling SDAS and eutectic Si particle characteristics through process control can improve the reliability and performance of Al-Si die-cast engine blocks.
- The established correlations can be used for quality control and prediction of mechanical properties based on microstructural analysis.
- Limitations of the Research:
- The study focused on a specific HPDC engine block design and alloy composition.
- The correlation analysis, while significant, shows some scatter in data, possibly due to inherent defects in HPDC components and the complexity of isolating individual microstructural effects.
- The study primarily considered SDAS and eutectic Si particles, while other microstructural features and defects may also contribute to mechanical property variations.
7. Future Research Directions:
- Directions for Future Research:
- Further investigation into the influence of other microstructural features, such as porosity, intermetallic phases, and grain size, on mechanical properties.
- Detailed analysis of the effect of specific HPDC process parameters on microstructure evolution and mechanical property variations.
- Development of predictive models linking process parameters, microstructure, and mechanical performance for HPDC Al-Si alloys.
- Exploration of advanced microstructure characterization techniques and non-destructive testing methods for quality assessment of die-cast components.
- Investigation of fatigue and fracture behavior in relation to microstructure in HPDC engine blocks.
- Areas for Further Exploration:
- The role of different alloying elements and their impact on microstructure and mechanical properties in HPDC Al-Si alloys.
- Optimization of alloy composition and heat treatment strategies to further enhance the performance of die-cast engine blocks.
- Application of these findings to other complex HPDC components and industries.
8. References:
[1] Colás, R., A. Rodríguez, J. Talamantes, and S. Valtierra. Solidification analysis of aluminium engine block. Int. J. Cast Metals Res., 17 (2004), 332-338.
[2] Verran, G.O., R.P.K. Mendes and M.A. Rossi. Influence of injection parameters on defects formation in die casting Al12Si1,3Cu alloy: experimental results and numeric simulation. J. Mater. Process Technol., 179 (2006), 190-195.
[3] Avalle, M., G. Bellingardi, M.P. Cavatorta and R. Doglione. Casting defects and fatigue strength of a die cast aluminium alloy: a comparison between standard specimens and production components. Int. J. Fatigue 24 (2002), 1-9.
[4] Timelli, G. and F. Bonollo. Quality mapping of aluminium alloy diecastings. Metal. Sci. Tech., 26 (2008), 2-8.
[5] Shabestari, S.G. and F. Shari. Influence of modification, solidification conditions and heat treatment on the microstructure and mechanical properties of A356 aluminum alloy. J. Mater. Sci., 39 (2004), 2023-2032.
[6] Viswanathan, S., A.J. Duncan, S.A. Sabau, Q. Han, W.D. Porter and B.W. Riemer. Modeling of Solidification and Porosity in Aluminum Alloy Castings. AFS Transactions, 98-103 (1998), 411-417.
[7] Rontó, V. and A. Roósz. The effect of the cooling rate or the local solidification time and composition on the secondary dendrite arm spacing during solidification Part II: Al-Mg-Si alloys. Int. J. Cast Metals Res., 13 (2001), 337-342.
[8] Grosselle, F., G. Timelli, F. Bonollo, A. Tiziani and E. Della Corte. Correlation between microstructure and mechanical properties of Al-Si cast alloys. Metall. Ital., 6 (2009), 25-32.
[9] Chen, Z.W. Skin solidification during high pressure die casting of Al-11 Si-2 Cu-1Fe alloy. Mater. Sci. Eng., A348 (2003), 145-153.
[10] Ye, H. An overview of the development of Al-Si alloy based material for engine applications. J. Mater. Eng. Perf., 12(3) (2003), 288-297.
[11] Samuel, F.H., A.M. Samuel and H.W. Doty. Factors controlling the type and morphology of Cu-containing phases in 319 Al alloy. AFS Trans., 104 (1996), 893-901.
[12] Νίυ, Χ.P, B.H. Hu and S.W. Hao. Effect of iron on the microstructure and mechanical properties of Al die-casting alloys. J. Mater. Sci. Letters, 17 (1998), 1727-1729
[13] Wang, Q.G. and C.H. Cáceres. Fracture mode in Al-Si-Mg casting alloys. Mater. Sci. Eng, A241 (1998), 72-82
[14] Wang, Q.G., C.H. Cáceres and J.R. Griffiths. Damage by eutectic particle cracking in aluminum casting alloys A356/357. Metall. Mater. Trans. A, 34 (2003), 2901-2912
[15] Cáceres, C.H. and J.R. Griffiths. Damage by the cracking of silicon particles in an Al-7Si-0.4Mg casting alloy. Acta Mater. 44 (1996), 25-33.
[16] Cáceres, C.H. and B.I. Selling. Casting defects and the tensile properties of an Al-Si-Mg alloy. Mater. Sci. Eng., A220 (1996), 109-116.
[17] Gokhale, A.M. and G.R. Patel. Origins of Variability in the fracture related mechanical properties of a tilt-pour-permanent-mold cast Al-alloy. Scripta Mater., 52 (2004), 237-241.
[18] Shankar, S. and D. Apelian. Die soldering: Mechanism of the interface reaction between molten aluminum alloy and tool steel. Mater. Trans., 33B (2002), 465-476.
[19] Jorstad, J.L. Understanding "Sludge". Die Casting Eng., November/December (1986), 30-36.
[20] Ghomashchi, M.R. Intermetallic compounds in an Al-Si Alloy used in high pressure diecasting. Z. Metallkunde, 78 (1987), 784-787.
[21] Seifeddine, S., T. Sjögren and I.L. Svensson. Variations in microstructure and mechanical properties of cast aluminium EN AC 43100 alloy. Proc. High Tech Die Casting, AIM, (2006), Vicenza.
[22] Zovi, A. and F. Casarotto. Silafont-36, the low iron ductile die casting alloy development and applications. Metall. Ital. 6 (2007), vol., 33-38.
[23] Asensio-Lozano, J. and B. Suárez-Peña. Microstructure-properties correlation of pressure die cast eutectic aluminum-silicon alloys for escalator steps (Part I). Mater. Characterization, 56 (2006), 169-177.
[24] Mondolfo, L.F. Manganese in Aluminum Alloys. The Manganese Center, (1978).
[25] Μο, Α., M. M'Handi and H.I. Laukly. Modelling defect bend formation in Al-Si die casting. Proc. High Tech Die Casting, AIM, (2006), Vicenza.
9. Copyright:
- This material is summarized based on the paper: Magnesium 2021: Proceedings of the 12th International Conference on Magnesium Alloys and their Applications.
- Source of Paper: https://www.metallurgical.org.rs/uploads/editor/files/Metals_and_Technology/Vol_27_2/Grosselle.pdf
This summary is prepared based on the above paper and is intended for informational purposes only. Unauthorized commercial use is prohibited.
Copyright © 2025 CASTMAN. All rights reserved.