This article introduces the paper ["Combining Structural Optimization and Process Assurance in Implicit Modelling for Casting Parts"] published by [MDPI Materials].
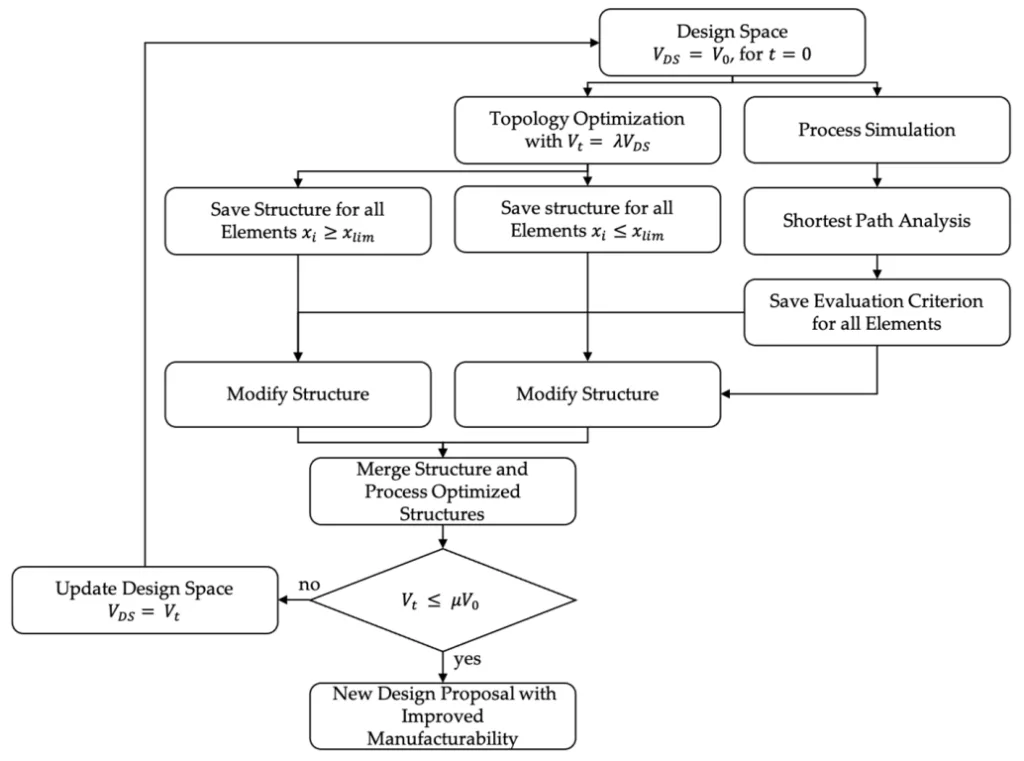
1. Overview:
- Title: Combining Structural Optimization and Process Assurance in Implicit Modelling for Casting Parts
- Author: Tobias Rosnitschek, Maximilian Erber, Christoph Hartmann, Wolfram Volk, Frank Rieg, and Stephan Tremmel
- Publication Year: 2021
- Publishing Journal/Academic Society: Materials
- Keywords: die casting; implicit modeling; process assurance; structural optimization; virtual product development
2. Abstracts or Introduction
The structural optimization of manufacturable casting parts remains a challenging and time-consuming task. Current methods involve topology optimization followed by manual reconstruction and process assurance simulation, leading to iterative refinements. This paper introduces a method to automatically combine structural optimization and process assurance results for structure- and process-optimized die casting parts using implicit geometry modeling. Evaluation criteria are developed to assess design proposals and quantify manufacturability improvements. A cantilever beam example demonstrates the method, comparing it to manual designs and direct optimization for mechanical performance and manufacturability. The automated combination of topology optimization (TO) and process assurance (PA) significantly enhances manual reconstruction. The improved manufacturability is comparable to existing methods but with reduced computational effort, highlighting the need for metamodels to shorten iteration times.
3. Research Background:
Background of the Research Topic:
Product development today demands short time-to-market and error-minimized designs. Optimizing parts structurally and for process is crucial for reducing manufacturing costs and scrap rates. However, these optimizations are time-consuming, require expert knowledge, and involve manual steps, indicating a potential for digital engineering to combine structural optimization and process assurance for casting parts.
Status of Existing Research:
Current optimization processes for structure and process are often divided between specialized departments, requiring iterative part transfers and manual redesigns based on optimization results. Existing research in structural optimization of casting parts includes topology optimization (TO) with manufacturing constraints like minimum feature size, symmetry, and extrusion. Process simulation is used to optimize mold or ingate systems for known geometries. While process knowledge is incorporated into commercial TO through manufacturing restrictions, deeper integration of process knowledge into TO is limited. Existing works incorporating full-scale casting process simulations into TO are computationally expensive due to high iteration times.
Necessity of the Research:
There is a gap in literature for geometry-linked evaluation criteria for High Pressure Die Casting (HPDC) and Low Pressure Die Casting (LPDC) that could potentially reduce the need for process simulation during TO while still providing sufficient manufacturability information. Further research is needed to investigate evaluation criteria for modifying design geometry and to automate the entire process for full autonomy. This article focuses on modifying part geometry, excluding ingate system modifications.
4. Research Purpose and Research Questions:
Research Purpose:
This research aims to present a new workflow for automatically combining TO and PA results to create structure- and process-optimized design proposals. Based on casting process-based criteria, structurally optimized geometry is modified via implicit modeling to enhance manufacturability. The long-term goal is to replace casting process simulation with a metamodel for evaluating the developed criterion.
Key Research:
The key research focuses on developing and proving the functionality of a geometry-linked evaluation criterion for casting processes. The workflow integrates process knowledge into TO of cast components, using implicit modeling to combine TO and PA results. For PA, a CFD-based process simulation followed by shortest path analysis and evaluation criterion calculation is used.
Research Hypotheses:
The proposed workflow will result in new design proposals that demonstrate increased manufacturability compared to standard TO parts. The combination of TO and PA will lead to structure- and process-optimized parts.
5. Research Methodology
Research Design:
The research employs a workflow that parallel conducts TO and PA, then uses implicit modeling to combine the best aspects of each. It distinguishes between a One-Step optimization and an iterative optimization approach. The workflow is tested for both HPDC and LPDC processes.
Data Collection Method:
For TO, nTopology software (Version 3.0.4) and a density-based TO method with SIMP are used. Process simulation is performed using Flow-3D (v5.0 Update 4) software, employing the Finite-Volume Method (FVM) and Volume of Fluid (VOF) method. A cantilever beam is used as a benchmark example.
Analysis Method:
Manufacturability is evaluated using geometry-linked evaluation criteria derived from process simulation results. For HPDC, a modified quotient (QuotHPDC) of time of first fluid arrival (tffa) and theoretical shortest path time (tsp) is used. For LPDC, a logarithmic quotient (QuotLPDC) of solidification time (tsol) and distance to the ingate level (h) is used. Structural performance is evaluated by relative-volume-related stiffness (SVR) from finite element analysis. The median of the evaluation criterion and the number of manufacturable elements are analyzed.
Research Subjects and Scope:
The research focuses on die casting parts, specifically using HPDC and LPDC processes. A cantilever beam geometry is used as a test case. The study investigates One-Step and Iterative Optimization approaches, comparing them to solely TO and manually redesigned parts.
6. Main Research Results:
Key Research Results:
- The proposed workflow successfully combines TO and PA for both HPDC and LPDC processes.
- The automated postprocessing workflow using implicit modeling effectively modifies the TO geometry based on process assurance criteria.
- For HPDC, the One-Step Optimization (HPDC-OS) achieved a manufacturability increase of 159% compared to the initial design space, and the Iterative Optimization (HPDC-IT) showed a 68% increase.
- For LPDC, both One-Step (LPDC-OS) and Iterative Optimization (LPDC-IT) approaches resulted in design proposals with directed solidification paths and improved manufacturability compared to solely TO designs.
- The HPDC-OS design proposal showed comparable manufacturability to manually designed HPDC-50 and outperformed solely topology optimized configurations in structural performance.
- For LPDC, both optimization approaches achieved similar relative-volume-related stiffness to TO configurations.
Analysis of presented data:
- Figure 17 shows the median of QuotHPDC for HPDC designs, indicating that HPDC-OS achieves the lowest median, suggesting better manufacturability compared to HPDC-IT and reference designs.
- Figure 18 evaluates the manufacturability of HPDC designs, showing HPDC-OS with the highest percentage increase in manufacturable elements compared to the initial design space.
- Figure 21 presents the median of QuotLPDC for LPDC designs, showing similar median values for iterative and one-step approaches, but lower values for TO designs.
- Figure 22 evaluates the manufacturability of LPDC designs, indicating that TO configurations have a significantly lower number of manufacturable elements compared to the proposed approaches.
- Figure 23 shows volume-related stiffness for HPDC designs, demonstrating that TO designs outperform One-Step and Iterative approaches, while HPDC-OS is comparable to manually designed HPDC-50.
- Figure 24 presents volume-related stiffness for LPDC designs, showing similar stiffness for all approaches, including TO configurations.
Figure Name List:
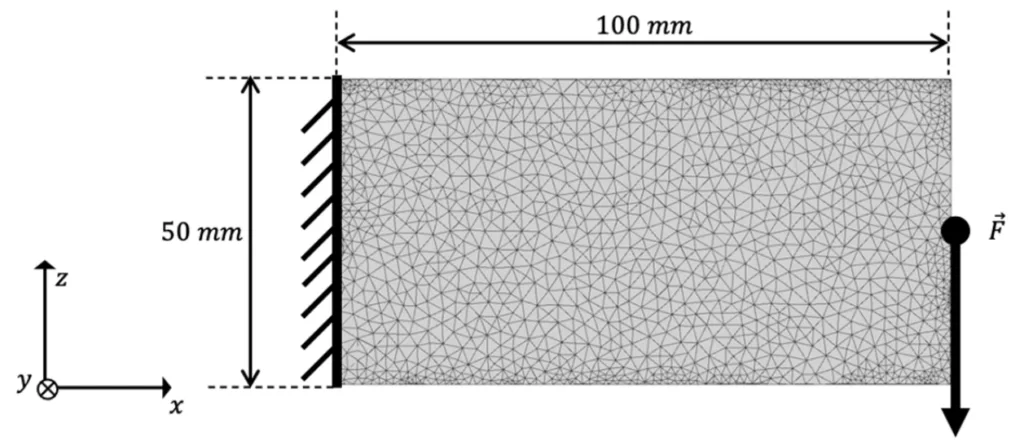
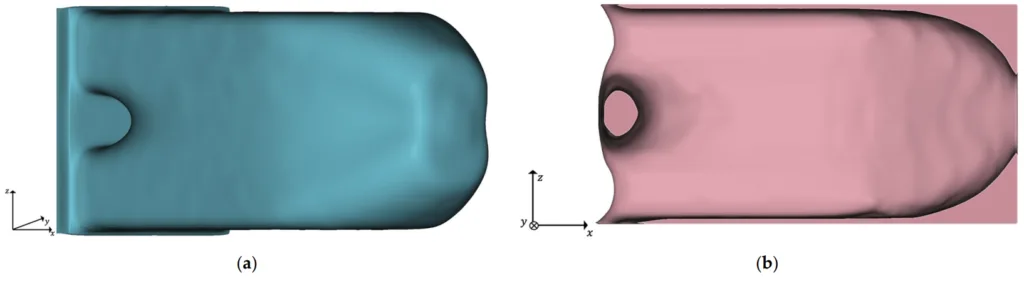
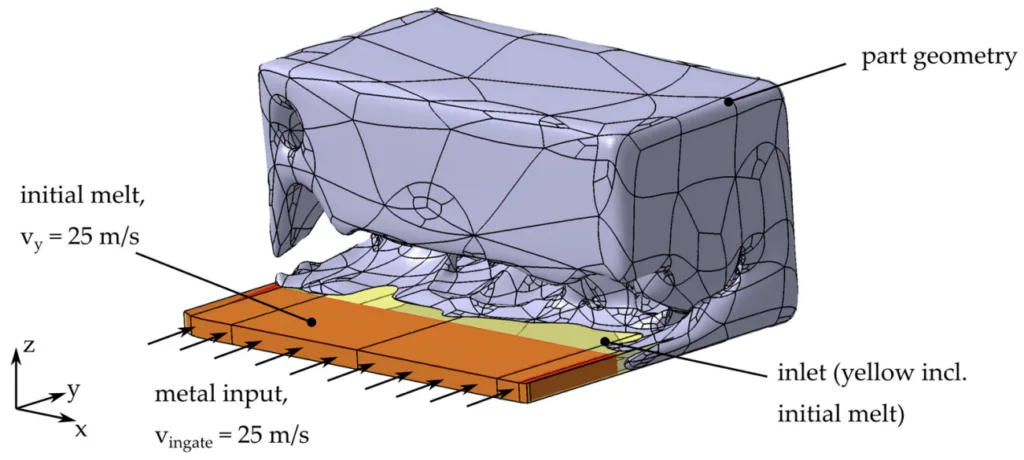
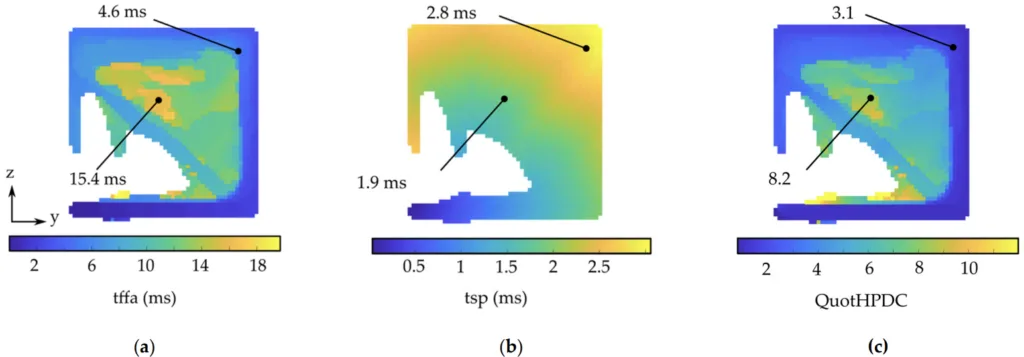
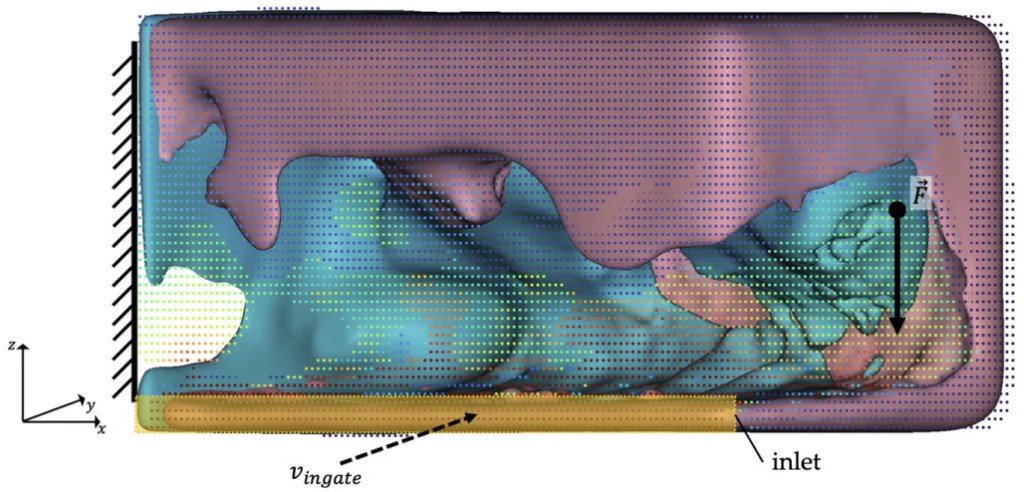
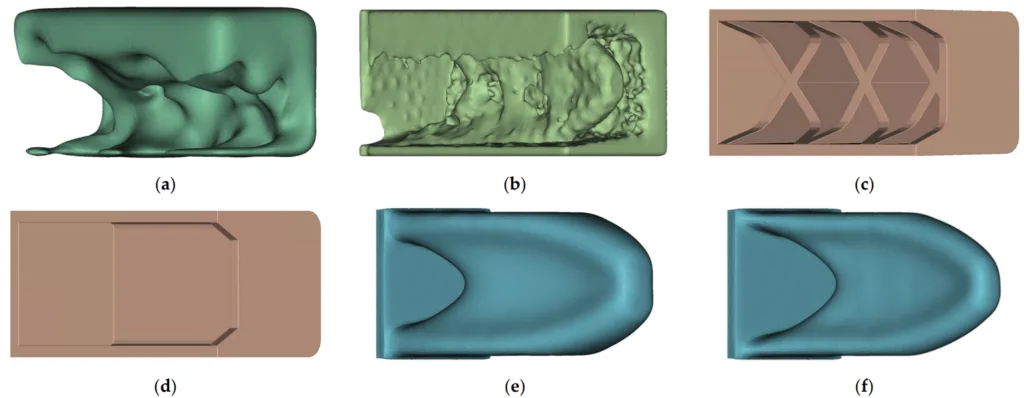
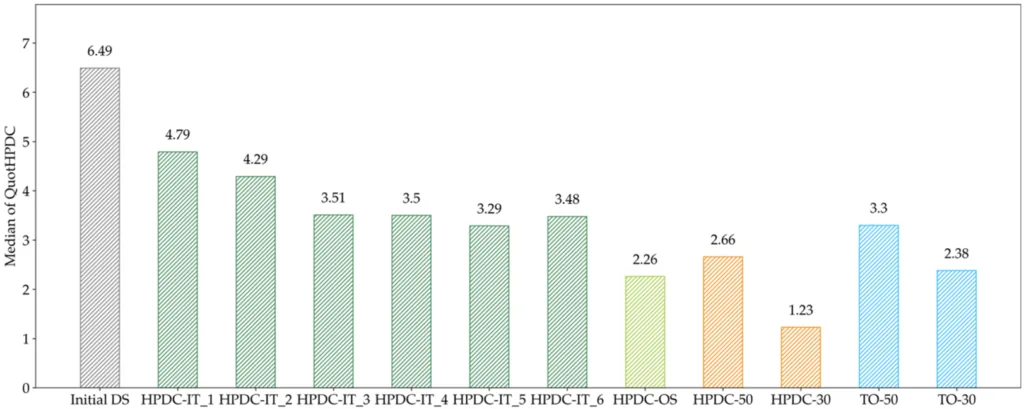
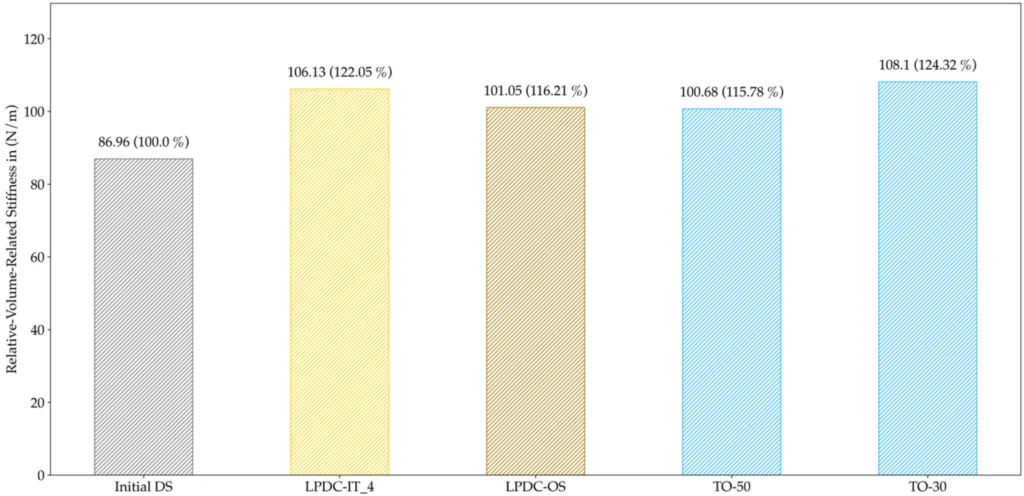
- Figure 1. Proposed workflow of the optimization for the combination of topology optimization and process assurance.
- Figure 2. Setup of the cantilever beam used as benchmark example.
- Figure 3. Results of the initial TO with λ = 0.2 and xlim = 0.6: (a) Implicit geometry of the optimized structure; (b) Cross-section of the implicit geometry of the TO-margin.
- Figure 4. Simulation setup for HPDC, exemplarily shown for iteration t = 2.
- Figure 5. Evaluation of the filling simulation of the HPDC process.
- Figure 6. Simulation setup for LPDC, exemplarily shown for iteration t = 4.
- Figure 7. Postprocessing Workflow.
- Figure 8. Exemplary point map for the QuotHPDC in iterative high-pressure die casting simulation, iteration t = 2.
- Figure 9. Creation of adapted meshes of the TO-margin by example of iterative HPDC optimization, iteration t = 5.
- Figure 10. Implicit volume mesh of the TO-margin before smoothing by example of iterative high-pressure casting optimization, iteration t = 5.
- Figure 11. Final result of the postprocessing workflow by example of iterative high-pressure casting optimization, iteration t = 5.
- Figure 12. Result of the HPDC-OS Optimization, with a volume of 50% compared to the initial design space.
- Figure 13. Result of the LPDC-OS Optimization, with a volume of 49% compared to the initial design space.
- Figure 14. Result of each iteration of the Iterative Optimization of HPDC parts for λ = 0.2.
- Figure 15. Result of each iteration of the Iterative Optimization of LPDC parts for λ = 0.2.
- Figure 16. Comparison of all HPDC and TO design proposals.
- Figure 17. Evaluation of the median of QuotHPDC for all optimized geometries.
- Figure 18. Evaluation of the manufacturability of HPDC design proposals.
- Figure 19. Comparison of all LPDC and TO design proposals: (a) LPDC-IT_4; (b) LPDC-OS; (c) TO-50; (d) TO-30.
- Figure 20. Solidification time for a cross section along the mid-plane.
- Figure 21. Evaluation of the median of QuotLPDC for all investigated geometries in the LPDC process.
- Figure 22. Evaluation of the manufacturability of LPDC design proposals.
- Figure 23. Volume-related stiffness for all HPDC configurations.
- Figure 24. Volume-related stiffness for all LPDC configurations.
7. Conclusion:
Summary of Key Findings:
This study presented a method combining TO and PA using implicit modeling and geometry-based evaluation criteria, automating the reconstruction of design proposals and accelerating the development of cast parts. The approach was validated for HPDC and LPDC processes on a cantilever beam, demonstrating improved manufacturability compared to solely TO designs. The One-Step Optimization approach showed particularly promising results for HPDC in terms of manufacturability and structural performance. For LPDC, the method facilitated directed solidification paths.
Academic Significance of the Study:
The research contributes a novel workflow for integrating process knowledge into topology optimization, addressing the gap in literature for geometry-linked evaluation criteria. The automated combination of TO and PA results and the use of implicit modeling represent advancements in design optimization for casting. The developed evaluation criteria (QuotHPDC and QuotLPDC) offer quantitative measures for manufacturability assessment.
Practical Implications:
The automated workflow significantly reduces manual redesign efforts and time in developing optimized casting parts. The method enables designers to generate structure- and process-optimized designs ready for process assurance, saving time in iterative design cycles. The approach is applicable to commercial TO software and adaptable to various casting processes.
Limitations of the Study and Areas for Future Research:
The study identified the step-length and design space as critical parameters influencing the optimization outcome, requiring further investigation. The smoothing parameters and ramp settings in postprocessing also warrant future research. The need for metamodels to replace time-consuming process simulations is highlighted as a crucial area for future development to enhance the efficiency of parameter studies and overall workflow performance. Future work should also focus on developing methods to describe desired solidification axes for complex LPDC parts and explore the trade-off between manufacturability and structural performance in multi-objective optimization.
8. References:
- [1] Hautsch, S.; Heilmeier, F.; Rieg, F.; Volk, W. Effiziente Entwicklung von prozessoptimalen druckgussbauteilen durch kombination von topologieoptimierung und prozesssimulation. In Stuttgarter Symposium für Produktentwicklung SSP17; Binz, H., Bertsche, B., Spath, D., Roth, D., Eds.; Fraunhofer-Institut für Arbeitswirtschaft und Organisation IAO: Stuttgart, Germany, 2017.
- [2] Heilmeier, F.; Goller, D.; Opritescu, D.; Thoma, C.; Rieg, F.; Volk, W. Support for Ingate Design by Analysing the Geometry of High Pressure Die Cast Geometries Using Dijkstra's Shortest Path Algorithm. Adv. Mater. Res. 2016, 1140, 400-407. [CrossRef]
- [3] Franke, T.; Fiebig, S.; Paul, K.; Vietor, T.; Sellschopp, J. Topology optimization with integrated casting simulation and parallel manufacturing process improvement. In Advances in Structural and Multidisciplinary Optimization; Schumacher, A., Vietor, T., Fiebig, S., Bletzinger, K.-U., Maute, K., Eds.; Springer International Publishing: Basel, Switzerland, 2018; ISBN 978-3-319-67987-7.
- [4] Franke, T.; Fiebig, S.; Bartz, R.; Vietor, T.; Hage, J.; vom Hofe, A. Adaptive Topology and Shape Optimization with Integrated Casting Simulation. In EngOpt 2018, Proceedings of the 6th International Conference on Engineering Optimization, Braunschweig, Germany, 5–9 June 2017; Rodrigues, H.C., Herskovits, J., Mota Soares, C.M., Araújo, A.L., Guedes, J.M., Folgado, J.O., Moleiro, F., Madeira, J.F.A., Eds.; Springer International Publishing: Basel, Switzerland, 2019; ISBN 978-3-319-97772-0.
- [5] Glamsch, J.; Deese, K.; Rieg, F. Methods for Increased Efficiency of FEM-Based Topology Optimization. Int. J. Simul. Model. 2019, 18, 453-463. [CrossRef]
- [6] Harzheim, L. Strukturoptimierung Grundlagen und Anwendung, 3rd ed.; Europa-Lehrmittel: Haan-Gruiten, Germany, 2019.
- [7] Rosnitschek, T.; Hentschel, R.; Siegel, T.; Kleinschrodt, C.; Zimmermann, M.; Alber-Laukant, B.; Rieg, F. Optimized One-Click Development for Topology-Optimized Structures. Appl. Sci. 2021, 11, 2400. [CrossRef]
- [8] Harzheim, L.; Graf, G. A Review of Optimization of Cast Parts Using Topology Optimization: I—Topology Optimization without Manufacturing Constraints. Struct. Multidisc. Optim. 2005, 30, 491-497. [CrossRef]
- [9] Harzheim, L.; Graf, G. A Review of Optimization of Cast Parts Using Topology Optimization: II—Topology Optimization with Manufacturing Constraints. Struct. Multidisc. Optim. 2006, 31, 388-399. [CrossRef]
- [10] Vatanabe, S.L.; Lippi, T.N.; de Lima, C.R.; Paulino, G.H.; Silva, E.C.N. Topology Optimization with Manufacturing Constraints: A Unified Projection-Based Approach. Adv. Eng. Softw. 2016, 100, 97-112. [CrossRef]
- [11] Gersborg, A.R.; Andreasen, C.S. An Explicit Parameterization for Casting Constraints in Gradient Driven Topology Optimization. Struct. Multidisc. Optim. 2011, 44, 875-881. [CrossRef]
- [12] Sato, Y.; Yamada, T.; Izui, K.; Nishiwaki, S. Manufacturability Evaluation for Molded Parts Using Fictitious Physical Models, and Its Application in Topology Optimization. Int. J. Adv. Manuf. Technol. 2017, 92, 1391-1409. [CrossRef]
- [13] Li, Q.; Chen, W.; Liu, S.; Fan, H. Topology Optimization Design of Cast Parts Based on Virtual Temperature Method. Comput. Aided Des. 2018, 94, 28-40. [CrossRef]
- [14] Wang, Y.; Kang, Z. Structural Shape and Topology Optimization of Cast Parts Using Level Set Method: Structural Shape and Topology Optimization of Cast Parts Using Level Set Method. Int. J. Numer. Meth. Eng. 2017, 111, 1252–1273. [CrossRef]
- [15] Xu, B.; Han, Y.S.; Zhao, L.; Xie, Y.M. Topology Optimization of Continuum Structures for Natural Frequencies Considering Casting Constraints. Eng. Optim. 2019, 51, 941-960. [CrossRef]
- [16] Nogowizin, B. Theorie und Praxis des Druckgusses; Schiele & Schön: Berlin, Germany, 2011.
- [17] Cuesta, R.; Delgado, A.; Maroto, A.; Mozo, D. Numerically modeling oxide entrainment in the filling of castings: The effect of the webber number. J. Oper. Manag. 2006, 58, 62–65. [CrossRef]
- [18] Kwon, H.-J.; Kwon, H.-K. Computer Aided Engineering (CAE) Simulation for the Design Optimization of Gate System on High Pressure Die Casting (HPDC) Process. Robot. Comput. Integr. Manuf. 2019, 55, 147-153. [CrossRef]
- [19] Dou, K.; Lordan, E.; Zhang, Y.J.; Jacot, A.; Fan, Z.Y. A Complete Computer Aided Engineering (CAE) Modelling and Optimization of High Pressure Die Casting (HPDC) Process. J. Manuf. Process. 2020, 60, 435-446. [CrossRef]
- [20] Mehtedi, M.E.; Mancia, T.; Buonadonna, P.; Guzzini, L.; Santini, E.; Forcellese, A. Design Optimization of Gate System on High Pressure Die Casting of AlSi13Fe Alloy by Means of Finite Element Simulations. Procedia CIRP 2020, 88, 509-514. [CrossRef]
- [21] Shahane, S.; Aluru, N.; Ferreira, P.; Kapoor, S.G.; Vanka, S.P. Finite Volume Simulation Framework for Die Casting with Uncertainty Quantification. Appl. Math. Model. 2019, 74, 132-150. [CrossRef]
- [22] Hirt, C.W.; Nichols, B.D. Volume of fluid (VOF) method for the dynamics of free boundaries. J. Comput. Phys. 1981, 39, 201-225. [CrossRef]
- [23] Cleary, P.; Ha, J.; Alguine, V.; Nguyen, T. Flow modelling in casting processes. Appl. Math. Model. 2002, 26, 171-190. [CrossRef]
- [24] Dabade, U.A.; Bhedasgaonkar, R.C. Casting Defect Analysis using Design of Experiments (DoE) and Computer Aided Casting Simulation Technique. Procedia CIRP 2013, 7, 616-621. [CrossRef]
- [25] Hahn, I.; Sturm, J. Von der Simulation zur gießtechnischen Optimierung. Giesserei 2015, 102, 86–100.
- [26] Hahn, I.; Sturm, J. Autonomous optimization of casting processes and designs. In Proceedings of the World Foundry Congress, Hangzhou, China, 16–20 October 2010; pp. 16-20.
- [27] Jadhav, A.R.; Hujare, D.P.; Hujare, P.P. Design and Optimization of Gating System, Modification of Cooling System Position and Flow Simulation for Cold Chamber High Pressure Die Casting Machine. Mater. Today Proc. 2021, S2214785320389598. [CrossRef]
- [28] Pinto, H.A.; Silva, F.J.G.; Martinho, R.P.; Campilho, R.D.S.G.; Pinto, A.G. Improvement and Validation of Zamak Die Casting Moulds. Procedia Manuf. 2019, 38, 1547–1557. [CrossRef]
- [29] Shahane, S.; Aluru, N.; Ferreira, P.; Kapoor, S.G.; Vanka, S.P. Optimization of Solidification in Die Casting Using Numerical Simulations and Machine Learning. J. Manuf. Process. 2020, 51, 130-141. [CrossRef]
- [30] Liu, J.; Ma, Y. A Survey of Manufacturing Oriented Topology Optimization Methods. Adv. Eng. Softw. 2016, 100, 161–175. [CrossRef]
- [31] Dijkstra, E.W. A note on two problems in connexion with graphs. Numer. Math. 1959, 1, 269-271. [CrossRef]
- [32] OPTIMAT: Entwicklung und Validierung von Softwaretools zur Simulation des Betriebsverhaltens von Werkstoffen in thermisch und Mechanisch Hoch Belasteten Komponenten, Arbeitsanteil NEMAK Wernigerode GmbH: Abschlussbericht, Berichtszeitraum: 1 May 2007–31 October 2010. Werkstoffinnovation für Industrie und Gesellschaft—WING: 2010. Available online: https://www.tib.eu/de/suchen?tx_tibsearch_search%5Baction%5D=download&tx_tibsearch_search%5Bcontroller%5D=Download&tx_tibsearch_search%5Bdocid%5D=TIBKAT%3A717891933&cHash=74e07aebe8553baac3ac1f2580585d68#download-mark (accessed on 1 July 2021).
- [33] Majernik, J.; Gaspar, S.; Kmec, J.; Karkova, M.; Mascenik, J. Possibility of Utilization of Gate Geometry to Modify the Mechanical and Structural Properties of Castings on the Al-Si Basis. Materials 2020, 13, 3539. [CrossRef]
- [34] nTopology's Implicit Modeling Technology. Available online: https://ntopology.com/resources/whitepaper-implicit-modeling-technology/ (accessed on 25 April 2021).
9. Copyright:
- This material is "Copyright: 2021 by the authors." 's paper: Based on "Combining Structural Optimization and Process Assurance in Implicit Modelling for Casting Parts".
- Paper Source: https://doi.org/10.3390/ma14133715
This material was created to introduce the above paper, and unauthorized use for commercial purposes is prohibited.
Copyright © 2025 CASTMAN. All rights reserved.