This article introduces the paper "Combined defect prediction for large-area die-cast components using high-resolution multi-phase simulation".
1. Overview
- Title: Combined defect prediction for large-area die-cast components using high-resolution multi-phase simulation
- Authors: J. Jakumeit, Η Behnken, R Laqua, J. Gänz, L. Becker, M. Fehlbier, O. Middelmann
- Publication Year: 2023
- Publishing Journal/Academic Society: IOP Conference Series: Materials Science and Engineering
- Keywords: high pressure die casting process (HPDC), multi-phase simulation, casting defects, porosity, air entrainment, solidification, validation
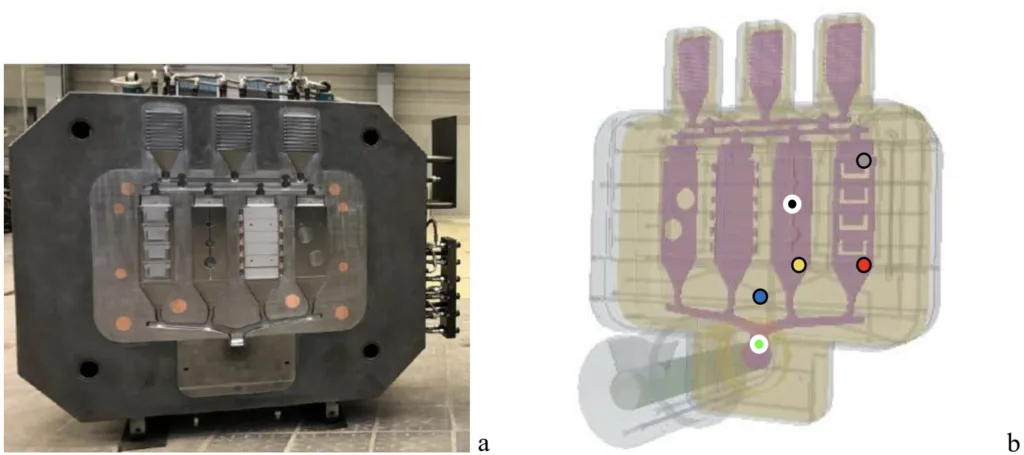
2. Research Background
- Social/Academic Context of the Research Topic:
- In the automotive industry, there is a growing trend towards manufacturing large components using high-pressure die casting (HPDC) to replace multiple welded parts, aiming to reduce costs and energy consumption.
- For large HPDC components, incipient solidification during mold filling is a significant concern.
- Casting defects such as cold running, air pockets, and porosity are interconnected and influence each other both spatially and temporally.
- Limitations of Existing Research:
- Traditional simulation models for die casting often employ approximations to reduce computational time.
- Phenomena like air influence and melt solidification arrest are often simplified in these models.
- Thin-walled areas can be challenging to analyze accurately due to mesh cell limitations.
- Existing porosity models, such as the Niyama criterion, have been found unsuitable for porosity prediction in HPDC applications.
- Previous models tended to simplify the complex interactions between gas and shrinkage porosity.
- Necessity of the Research:
- A more realistic simulation of the casting process is needed to accurately depict the interactions between various casting defects.
- There is a need for a multi-phase approach that can treat air as a compressible gas, account for solidification-induced melt flow reduction, and handle porosity formation due to volume shrinkage in a coupled manner.
- Validating such a multi-phase approach through actual casting trials and industrial applications is crucial for its practical utilization.
3. Research Purpose and Research Questions
- Research Purpose:
- To develop and validate a coupled porosity model for high-pressure die casting (HPDC) applications that comprehensively predicts both air entrainment and shrinkage porosity formation using high-resolution multi-phase simulation.
- Key Research Questions:
- Can a multi-phase simulation approach, treating air as a compressible gas and melt solidification using a porous media approach, accurately predict casting defects in large-area die-cast components?
- How can air entrainment and shrinkage porosity formation be coupled in a simulation model for HPDC to account for their interactions effectively?
- Can a coupled porosity model, based on pressure calculation and melt compressibility, predict porosity formation in regions where melt feeding is limited by solidification?
- How well does the developed multi-phase approach and coupled porosity model align with experimental casting trials and industrial applications?
- Research Hypotheses:
- A multi-phase simulation approach, incorporating compressible air, solidification effects, and a coupled porosity model, will provide a more realistic prediction of casting defects in HPDC compared to simplified models.
- The coupled porosity model, considering pressure changes due to solidification and gas evaporation, will accurately predict shrinkage porosity formation in regions with limited melt feeding.
- Simulation results using the developed model will correlate well with experimental casting trials and industrial case studies, demonstrating the model's validity for HPDC applications.
4. Research Methodology
- Research Design:
- Development of a multi-phase simulation approach for the HPDC process using the flow solver STAR-CCM+.
- Implementation of a coupled porosity model that considers both air entrainment and shrinkage porosity.
- Validation of the simulation approach through casting trials using a specially designed test geometry.
- Application of the validated model to an industrial casting component.
- Data Collection Method:
- Experimental casting trials were conducted on a GTK cold chamber die casting machine (Bühler Carat 1400 t) using AlSi9Cu3 alloy.
- Temperature measurements were collected using six thermocouples placed within the test geometry during casting cycles.
- Porosity levels in castings were analyzed using CT scans for industrial application validation.
- Analysis Method:
- Comparison of calculated temperature curves from simulations with measured temperature data to validate thermal settings.
- Qualitative comparison of predicted porosity locations with observed porosity in experimental castings and industrial parts.
- Analysis of velocity, air distribution, pressure, solid fraction, and pore gas distribution from simulation results to understand defect formation mechanisms.
- Research Subjects and Scope:
- A specially designed HPDC test geometry with four test cases (two-holes, steps, three-cam, and U-profiles) to investigate misrun, gas entrainment, and porosity.
- A simplified three-cam geometry extracted from the test geometry for detailed porosity simulation.
- An industrial structural part from KSM Castings Group GmbH for industrial application validation.
- Focus on aluminum HPDC applications and validation using AlSi9Cu3 alloy.
5. Main Research Results
- Key Research Results:
- A multi-phase simulation approach for HPDC was developed, treating air and melt as compressible fluids, employing the Volume of Fluid (VoF) method and High-Resolution-Interface-Capturing (HRIC) scheme in STAR-CCM+ to capture sharp interfaces.
- A coupled porosity model was implemented, considering pressure build-up, solidification, and gas evaporation to predict both air entrainment and shrinkage porosity.
- The simulation approach was validated by comparing calculated temperature curves with measured data from casting trials, showing good agreement. "Figure 2a compares the calculated temperature curves at the thermocouple position with the measurement results."
- High-resolution simulation of the three-cam geometry using the coupled porosity model predicted porosity formation in the middle of the cams, consistent with experimental findings. "Figure 7 shows the final porosity distribution after all 4 steps. The pure thermal porosity model gives pores close to the middle of the cams…" and "Along with the pore gas distribution figure 7 gives the porosity found in the real casting. The porosity prediction by the coupled porosity model agrees well with the experimental findings…"
- Application to an industrial casting part showed that the simulation could predict shrinkage porosity in locations identified by CT scans, although some discrepancies were observed. "Shrinkage porosity was identified at two locations (C5, B2, see figure 9a and 9b) by CT-scans (figure 9c and 9d). Simulation was so far not able to predict these porosity locations." and later "Shrinkage porosity was indeed indicated by the pure thermal porosity model at the end of step 4 at the two locations C5 and B2 (figure 9e and 9f)."
- Simulation results indicated that shrinkage porosity dominates over porosity due to entrained air in well-designed gating systems. "Looking at the porosity prediction for the test cases and the industrial application, the shrinkage porosity dominates the porosity due to entrained air."
- Statistical/Qualitative Analysis Results:
- Qualitative agreement between simulated and measured temperature curves was observed (Figure 2a).
- Qualitative agreement between predicted porosity locations and experimentally observed porosity in the three-cam geometry (Figure 7 and Figure 9).
- Qualitative comparison of porosity locations in industrial casting between CT scans and simulation results (Figure 9).
- Data Interpretation:
- The validated multi-phase simulation approach and coupled porosity model can effectively predict temperature distribution and porosity formation in HPDC processes.
- The coupled porosity model captures the complex interplay between air entrainment and shrinkage porosity, improving the accuracy of defect prediction compared to traditional models.
- High-resolution multi-phase simulation methodology provides a valuable tool for understanding and optimizing HPDC processes, particularly for large and complex components.
- While the model shows good agreement with experiments, further refinement may be needed to improve the accuracy of porosity prediction in industrial applications, particularly regarding the hypersensitivity of the model and factors not addressed by current porosity models.
- Figure Name List:
- Figure 1: Inner side of the moving die (a) and the geometry with four test cases two-holes, steps, three-can and u-profiles (b) and the shown in a)
- Figure 2: Comparison of measured and calculated temperature curves at the 6 measurement points (a) (see figure 1b) and the calibrated temperature dependent HTC (b)
- Figure 3: Three cam test geometry with simple inlet and outlet (a) and the high resolution mesh with 2.4 Mio cells, 1.8 Mio in part region. 3 prism layer at the melt/mold interface were used for a high resolution of the velocity and temperature gradients.
- Figure 4: Velocity (a) and entrained air (b) distribution after 0.055 s at the end of the filling step.
- Figure 5: Velocity (a) and entrained air (b) distribution after 0.1 s at the end of the intensification step.
- Figure 6: Fraction solid (a), velocity (b), pressure (c) and porosity (d) distributions after 1.1 s at the end of the coupled flow and solidification step.
- Figure 7: Comparison of the porosity prediction by the coupled porosity model and the experimental findings.
- Figure 8: Geometry a), polyhedral mesh b), temperature and melt distribution during filling after 0.75 s c) and the air entrainment after complete filling and pressure intensification d).
- Figure 9: Industrial HPDC application showing porosity at two positions C5 (a) and B2 (b) of the casting revealed by CT-analysis (c) and (d) and the porosity prediction by the coupled simulation model for the position C5 (e) and B2 (f).
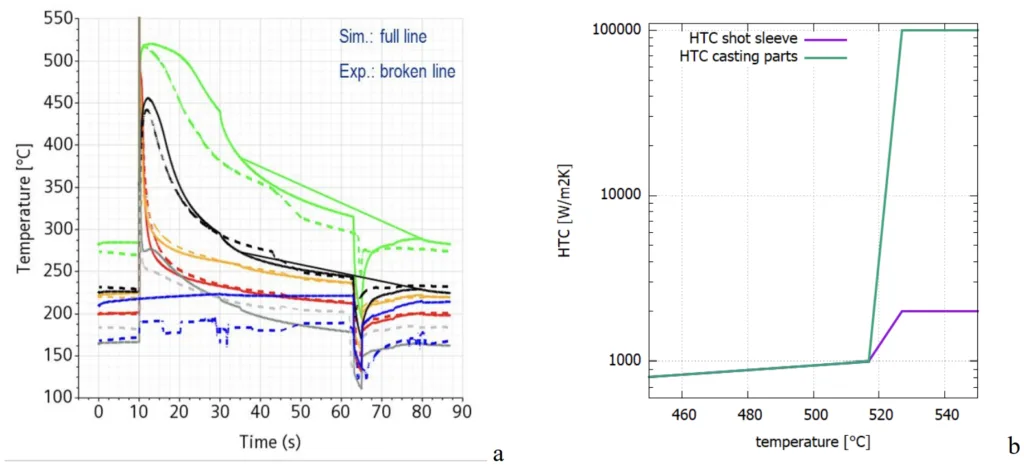
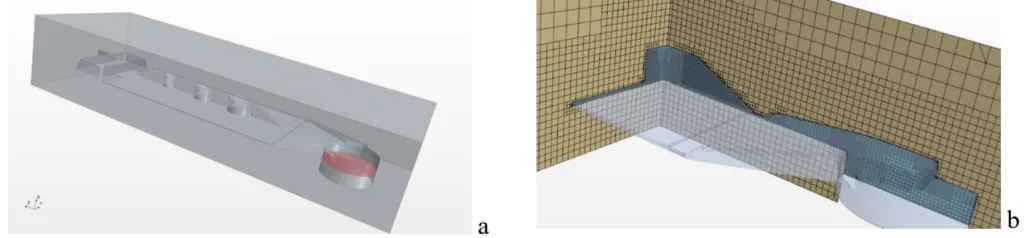
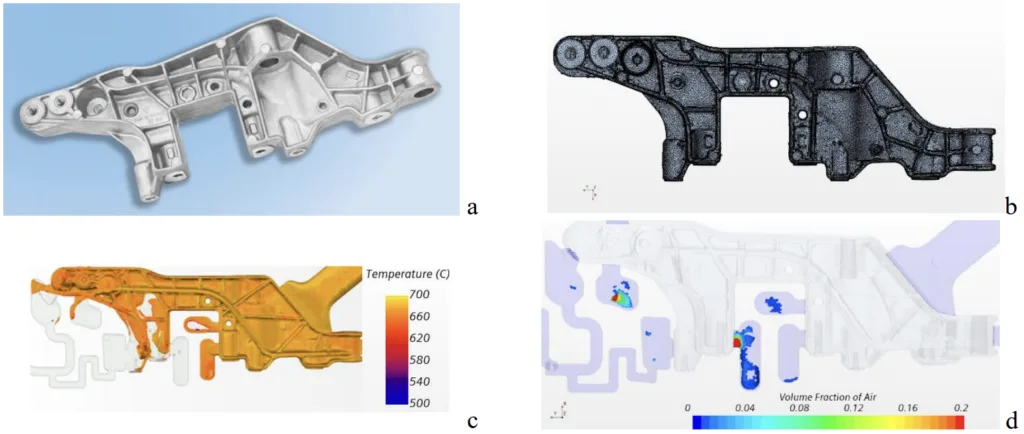
6. Conclusion and Discussion
- Summary of Main Results:
- The research successfully developed and validated a multi-phase flow and solidification simulation approach for HPDC, incorporating a coupled porosity model for predicting air entrainment and shrinkage porosity.
- The model treats liquid melt and gas as compressible fluids, accounts for solidification effects on melt flow using temperature-dependent viscosity and porous media approach, and simulates porosity formation based on pressure changes and gas evaporation.
- Validation against experimental casting trials and industrial application demonstrated the model's capability to predict temperature distribution and porosity formation in HPDC components.
- Academic Significance of the Research:
- This research contributes to the advancement of die casting simulation technology by providing a more realistic and comprehensive approach to predict casting defects.
- The coupled porosity model addresses the complex interplay between air entrainment and shrinkage porosity, improving the accuracy of defect prediction compared to traditional models.
- The high-resolution multi-phase simulation methodology provides a valuable tool for understanding and optimizing HPDC processes, particularly for large and complex components.
- Practical Implications:
- The validated simulation approach can be used by die casting engineers to optimize process parameters, mold design, and gating systems to minimize casting defects and improve component quality.
- By accurately predicting porosity and other defects, the model can help reduce scrap rates, shorten process development time, and improve the overall efficiency of HPDC manufacturing.
- The industrial application demonstrates the potential of the model for solving real-world casting problems and improving the production of high-quality die-cast components.
- Limitations of the Research:
- While the model shows good agreement with experimental data, there are still discrepancies in predicting porosity in industrial applications, suggesting room for further refinement.
- The model might be hypersensitive to certain parameters, leading to potential over-prediction of porosity in some cases.
- Factors not explicitly addressed in the current porosity models, as mentioned by Beckermann [13], could contribute to differences between simulation predictions and real casting results.
7. Future Follow-up Research
- Directions for Follow-up Research:
- Further refinement of the coupled porosity model to improve its accuracy and robustness for industrial applications.
- Investigation of the hypersensitivity of the model and potential calibration or adjustment of model parameters.
- Incorporation of additional factors that influence porosity formation in HPDC, as identified by Beckermann [13] and others, into the model.
- Further validation of the model with a wider range of casting geometries, alloys, and process conditions.
- Development of more efficient computational methods to reduce simulation time, enabling wider adoption of high-resolution multi-phase simulation in industrial practice.
- Areas Requiring Further Exploration:
- Detailed investigation of the critical pressure level for gas evaporation and its dependence on material properties and process conditions.
- Study of the influence of dissolved hydrogen or air in the melt on porosity formation and gas evaporation.
- Exploration of advanced turbulence models and interface capturing techniques to further improve the accuracy of multi-phase flow simulation in HPDC.
- Development of user-friendly simulation tools and guidelines to facilitate the application of the coupled porosity model by die casting engineers.
8. References
- [1] Duan H Z, Shen J N, & Li Y P (2012). Comparative analysis of HPDC process of an auto part with ProCAST and FLOW-3D. In Applied Mechanics and Materials (Vol. 184, pp. 90-94). Trans Tech Publications Ltd.
- [2] Bodhayana M R and Ramesha N 2014 Int. J. Research in Engineering and Technology 03 (11) 1163
- [3] Aghion E, Moscovitch N and Arnon A (2007). The correlation between wall thickness and properties of HPDC Magnesium alloys. Materials Science and Engineering: A, 447(1-2), 341-346.
- [4] Wang T, Huang J, Fu H, Yu K and Yao S (2022). Influence of Process Parameters on Filling and Feeding Capacity during High-Pressure Die-Casting Process. Applied Sciences, 12(9), 4757.
- [5] Simcenter STAR-CCM+: https://www.plm.automation.siemens.com/global/de/products/simcenter/STAR-CCM.html
- [6] Jana S, Kättlitz O, Hediger F, Jakumeit J and Aguilar J (2012). MCWASP XIII, IOP Publishing, IOP Conf. Series: Materials Science and Engineering.
- [7] Stefanescu, D. M. (2005). Computer simulation of shrinkage related defects in metal castings-a review. International Journal of Cast Metals Research, 18(3), 129-143.
- [8] Beech J, Barkhudarov M, Changands K, Chin B (1998) in ‘Modelling of casting, welding and advanced solidificationprocesses VIII', (ed. B. G. Thomas and C. Beckerman), 1071; Warrendale, PA, TMS.
- [9] Jakumeit J, Behnken H, Laqua R, Mbewou S, Fehlbier M, Gänz J, & Becker, L. (2021). Coupled Modeling of Misrun, Cold Shut, Air Entrainment, and Porosity for High-Pressure Die Casting Applications. In Light Metals 2021 (pp. 865-870). Springer, Cham.
- [10] Niyama T, Uchida M, Morika W A, Saito S (1982) Int. cast metals journal 7:52-63
- [11] Carlson K D and Beckermann C (2009). Metallurgical and Materials Transactions A, 40(1), 163-175.
- [12] Jakumeit, J., Jana, S., Böttger, B., Laqua, R., Jouani, M. Y., & Bührig-Polaczek, A. (2012, January). In IOP Conference Series: Materials Science and Engineering (27, No. 1, p. 012066). IOP Publishing.
- [13] Beckermann C and Monroe A 2009 Porosity simulation for high pressure die castings Die Casting Engineer (The North American Die Casting Association) ISSN 0012-25JX
- [14] Carlson K D, Lin Z and Beckermann C (2007). Modeling the effect of finite-rate hydrogen diffusion on porosity formation in aluminum alloys. Metallurgical and Materials Transactions B, 38(4), 541-555.
- [15] Khalajzadeh V, Goettsch, D D and Beckermann C (2016). In Shape Casting: 6th International Symposium (pp. 35-42). Springer, Cham
- [16] Khalajzadeh V and Beckermann C (2020). Simulation of shrinkage porosity formation during alloy solidification. Metallurgical and Materials Transactions A, 51(5), 2239-2254.
- [17] Ferziger J H and Peric M (ed) 2002 Computational Methods for Fluid Dynamics (McGraw-Hill) ISBN 2-540-42074-6
- [18] Teskeredzic A, Demirdzic I and Muzaferija S 2002 Num. Heat Trans. B 42 43
- [19] Demirdzic I and Muzaferija S 1995 Computer Methods in Appl. Mech. and Eng. 125 235-255.
- [20] Muzaferija S and Peric M 1999 Computation of free surface flows using interface-tracking and interface-capturing methods. Nonlinear Water Wave Interaction, ed O Mahrenholtz and M. Markiewicz, (Southampton: WIP Press) 59-100
- [21] Sabau S and Viswanath S 2002 Met. Mat. Trans. B 33B 131
- [22] Poirier D R (1987). Permeability for flow of interdendritic liquid in columnar-dendritic alloys. Metallurgical Transactions B, 18(1), 245-255.Poirier D R, Yeum K and Mapples A L 1987 Metall. Mater. Trans. A 18 1979
- [23] Jakumeit, J., Subasic, E., & Bünck, M. (2016). Prediction of misruns in thin wall castings using computational simulation. In Shape Casting: 5th International Symposium 2014 (pp. 253-260). Springer International Publishing.
9. Copyright
- This material is based on the paper by J. Jakumeit, Η Behnken, R Laqua, J. Gänz, L. Becker, M. Fehlbier, O. Middelmann: Combined defect prediction for large-area die-cast components using high-resolution multi-phase simulation.
- Paper Source: http://dx.doi.org/10.1088/1757-899X/1281/1/012027
This material was summarized based on the above paper, and unauthorized use for commercial purposes is prohibited.
Copyright © 2025 CASTMAN. All rights reserved.