This introductory paper is the research content of the paper "Hohl- und Verbundguss von Druckgussbauteilen – Numerische Auslegungsmethoden und experimentelle Verifikation" published by [Fakultät Energie-, Verfahrens- und Biotechnik der Universität Stuttgart ].
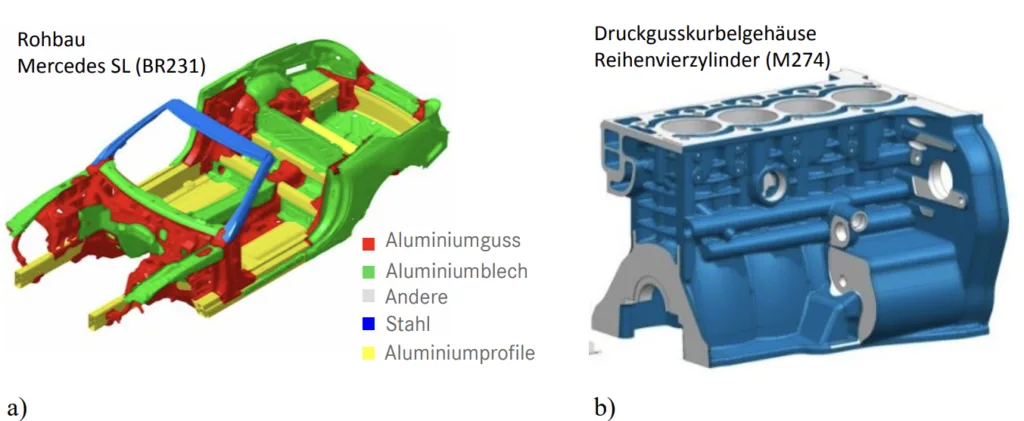
1. Overview:
- Title: Hohl- und Verbundguss von Druckgussbauteilen – Numerische Auslegungsmethoden und experimentelle Verifikation (Cavity and Composite Casting of Die Casting Components – Numerical Design Methods and Experimental Verification)
- Author: Paul Fickel
- Publication Year: 2017
- Published Journal/Society: Fakultät Energie-, Verfahrens- und Biotechnik der Universität Stuttgart (Faculty of Energy, Process Engineering and Biotechnology at the University of Stuttgart)
- Keywords: Hinterschnitten (undercuts), Druckguss (die casting), Salzkerne (salt cores), St-Al-Verbunde (steel-aluminum composites), Numerische Auslegungsmethoden (numerical design methods), experimentelle Verifikation (experimental verification)
2. Abstract
According to the state oft the art the manufacturing processes of aluminum high pressure die casting (HPDC) parts with undercuts is only possible by using complex sliders, integrated in the HPDC-tool. Known systems like sandcores, fluid injection, glass cores, metallic melting cores or pressed salt cores are only usable with restrictions in the HPDC process. Therefore, only salt cores, manufactured from the liquid phase as well as metallic inserts currently have the potential to be used successfully in HPDC. Casted salt cores achieve high levels of bending and compression strength and can be removed residue-free for example with water jet cutting after the aluminum casting process. Steel inserts which remain in the aluminium casting reinforce the part. This work presents some basic research to enable the manufacturing of casted salt cores. In preliminary investigations a salt alloy within a sodiumcloride-sodiumcarbonate phase diagram will be choosen for further investigations. Based on a priciple test specimen the dependence of the process parameters and the resulting strength and the hot cracking tendency will be demonstrated. For the mechanical characterization a bending, tensile and compression test will be performed at room temperature and temperatures up to 500 °C. An approach for the numerical simulation of the salt core casting process is presented and verified by experimental results. In addition to salt cores, steel inserts have been investigted and the aluminium-steel compound structure has been charactarized. Force-, form-, and chemical bonding have been considered. For a better chemical bonding between the steel insert and aluminium casting different coatings were applied and graded. Mechanical pull-, push-, shear- and adhesive tensile tests as wells as light and scanning electron microscope investigations were performed to characterize the connection quality. On this basis, numerical simulation methods were developed. The viability and fracture behaviour of the salt cores and steel inserts during the HPDC process were investigated. Therefore, a numerical method was introduced and verified with experimental results to predict the core viability. Both technologies were transfered on application examples.
3. Research Background:
Background of the research topic:
The production of aluminum structural components with undercuts, using sliders, sand systems, gas injection processes, glass cores, metallic melt-out cores, or pressed salt cores, is subject to restrictions in the die casting process. Currently, only salt cores produced from the liquid phase and permanent metallic inserts offer potential for use in die casting.
Status of previous research:
Previous research, as detailed in Chapter 2, explored various methods for creating undercuts in die casting, including:
- Process-related approaches: Slider technology (Schiebertechnologie) and gas injection (Gasinjektion).
- Permanent inserts: Metal foams (Metallschäume), steel and light metal inserts (Stahl- und Leichtmetalleinleger), and Combicore insert tubes (Combicore Einlegerohre).
- Lost core technology: Current approaches for lost cores in the die casting process (Verlorene Kerntechnologie), and specifically, salt cores for producing undercuts in die casting (Salzkerne zur Herstellung von Hinterschnitten im Druckguss).
- Numerical modeling of inserts in die casting.
Need for research:
The need exists to develop current casting processes and materials to enable lightweight construction. Specifically, the development of pressure-resistant lost cores (ceramic or salt) and the optimization of the die casting process through the use of metal inserts with higher strength.
4. Research purpose and research question:
Research purpose:
The overall goal is to develop the necessary data for the numerical design of force-fit, form-fit, and integrally bonded steel-aluminum connections and complex hollow castings, using cast salt cores. The study will investigate St-Al-Verbundguss (steel-aluminum composite casting) and the use of Salzkerne (salt cores).
Core research:
- Investigate experimentaly and numerically the basics for producing cast salt cores.
- Select a salt alloy from the sodium chloride-sodium carbonate phase diagram.
- Establishing simulation methods for the salt core manufacturing process, verified by experimental studies.
- Investigate steel inserts in die casting.
- Apply and evaluate different coatings for improvement of chemical bonding of the steel insert and aluminium casting.
- Characterization by mechanical testing and metallographic techniques.
- Developing and applying simulation methods for the connections(force-, form-, and integrally bonded).
- Investigate core loading and damage behavior in die-casting tests.
5. Research Methodology
The research employs both experimental and numerical methods:
- Experimental: Principle geometries and test specimens, tool designs, and testing environments are created. Salt alloy variations are planned and materials characterized using mechanical and metallographic techniques. Material models will be adjusted using bending bar and spiral casting tests. The process of casting is also examined using experiments.
- Numerical: Simulation models are developed for the salt core manufacturing process, heat crack prediction, representation of the enveloping process. Simulations are conducted to predict salt core and insert loading, as well as to characterize and numerically represent the steel-aluminum compound. Methods for modeling cohesive connections are also developed.
- Analysis method Finite-Difference-Method(FDM),Finite-Element-Method(FEM)
6. Key research results:
Key research results and presented data analysis:
The project combines experimental investigations with the development of verified simulation methods. The study focuses on understanding the processes of salt core production, core and insert loading during die casting, and characterizing/simulating the resulting steel-aluminum composites. Salt composition and casting parameters significantly influenced the formation of defects such as hot cracks.
List of figure names:
![[2] HENNING, F.; MOELLER, E.: Handbuch Leichtbau Methoden, Werkstoffe, Fertigung. Carl Hanser Verlag München Wien, 2011, ISBN 978-3-446-42267-4](https://castman.co.kr/wp-content/uploads/image-1547-1024x355.webp)
![[3] KLEIN, B.: Leichtbau-Konstruktion Berechnungsgrundlagen und Gestaltung. 10. Auflage Springer Fachmedien Wiesbaden, 2013, ISBN 978-3-658-02271-6](https://castman.co.kr/wp-content/uploads/image-1548-1024x379.webp)
![[4] OSTERMANN, F.: Anwendungstechnologie Aluminium. 2. Auflage Springer-Verlag Berlin Heidelberg, 2007, ISBN 978-3-540-71196-4](https://castman.co.kr/wp-content/uploads/image-1549-1024x286.webp)
![[8] ILSCHNER, B.; SINGER, R.F: Werkstoffwissenschaften und Fertigungstechnik – Eigenschaften, Vorgänge, Technologien. 5. Auflage Springer-Verlag Berlin Heidelberg, 2010, ISBN 978-3-642-01733-9](https://castman.co.kr/wp-content/uploads/image-1550-1024x359.webp)
![Abbildung 2.9: Salzkerne für Gießanwendungen: a) oben: Geschossener Salzkern; unten: Im Druckgussverfahren hergestellter Salzkern [12], b) gepresste und gesinterte Salzkerne der Fa. Emil-Müller-GmbH / CeramTec AG [48]](https://castman.co.kr/wp-content/uploads/image-1551-1024x553.webp)
![Abbildung 2.11: Bühler Pilotbauteil [54]: a) Salzkern Pilotbauteil, b) Schnitt durch Pilotbauteil
mit sichtbarem Salzkern, c) Schnitt durch Pilotbauteil entkernt](https://castman.co.kr/wp-content/uploads/image-1552-1024x328.webp)
![Abbildung 2.12: Phasendiagramm für NaCl+Na2CO3 [62] mit eingezeichneten Gitterstrukturänderungen und dazugehörigen Gittertypen](https://castman.co.kr/wp-content/uploads/image-1553-1024x731.webp)
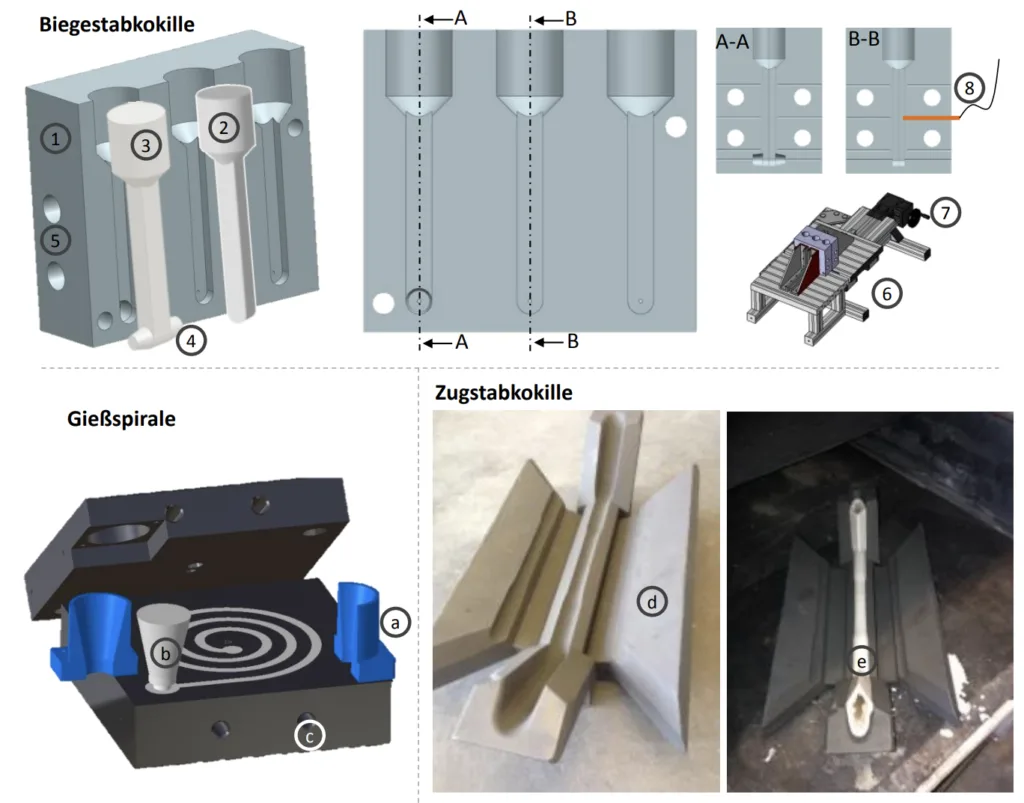
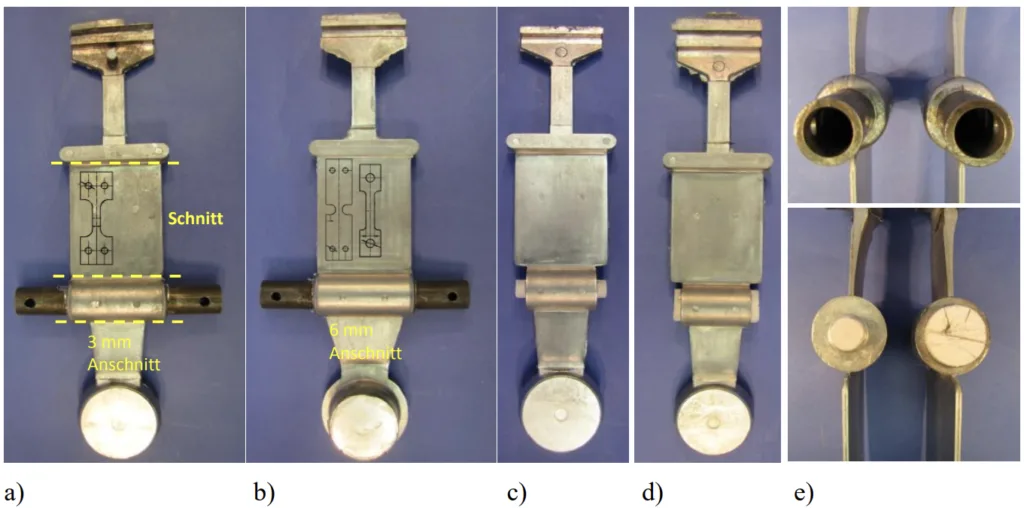
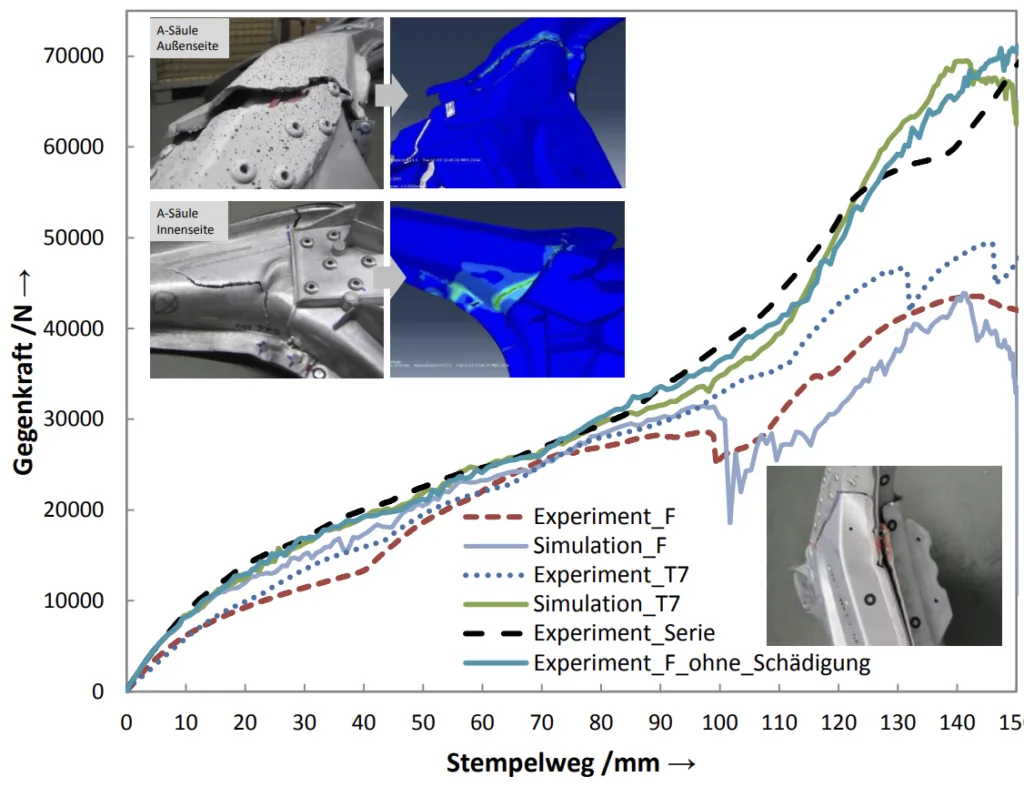
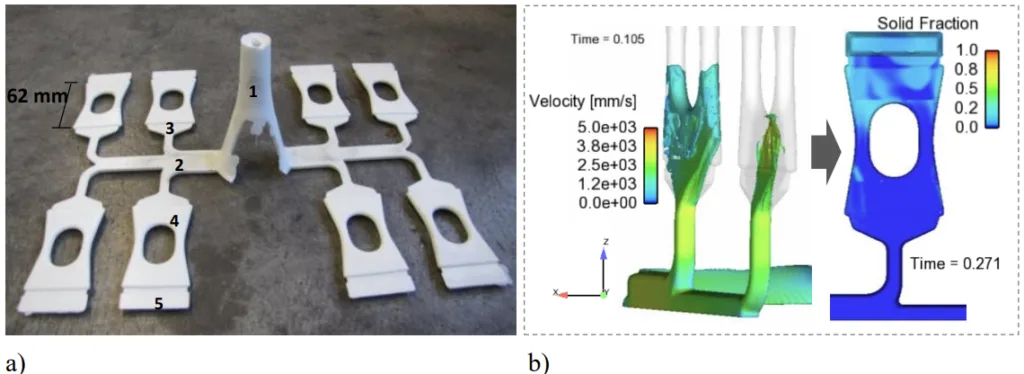
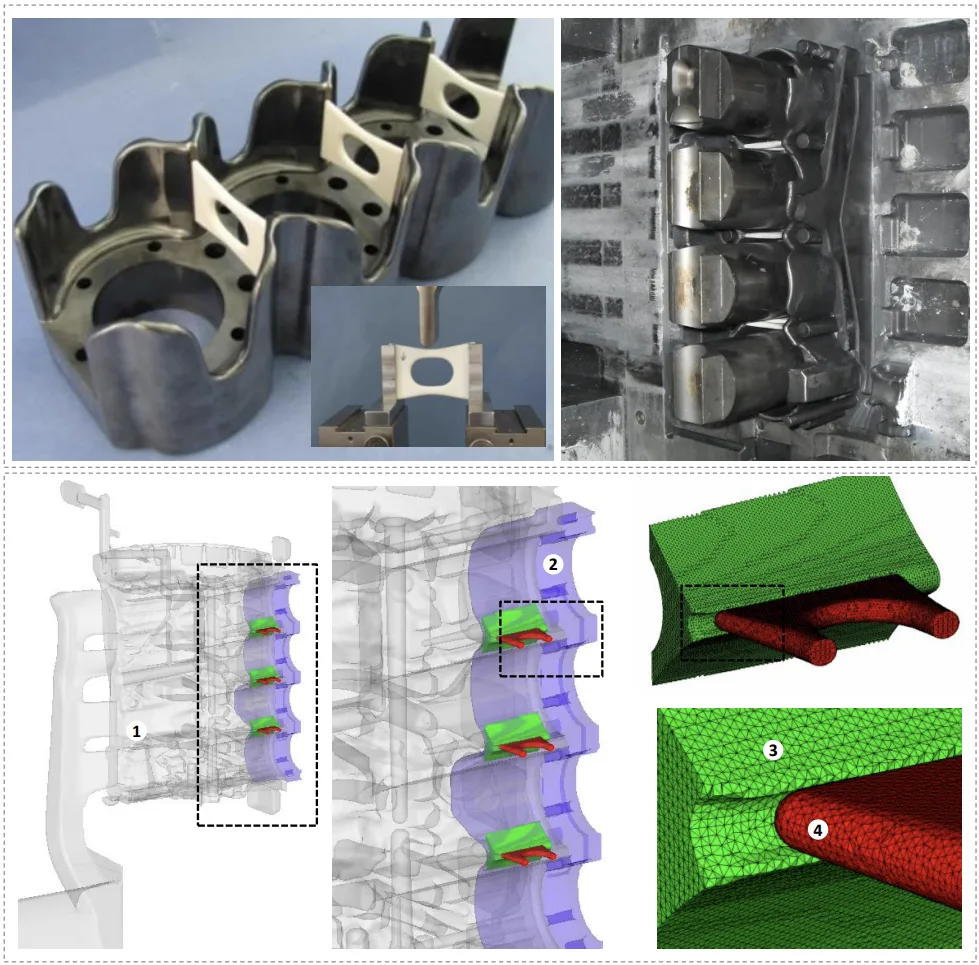
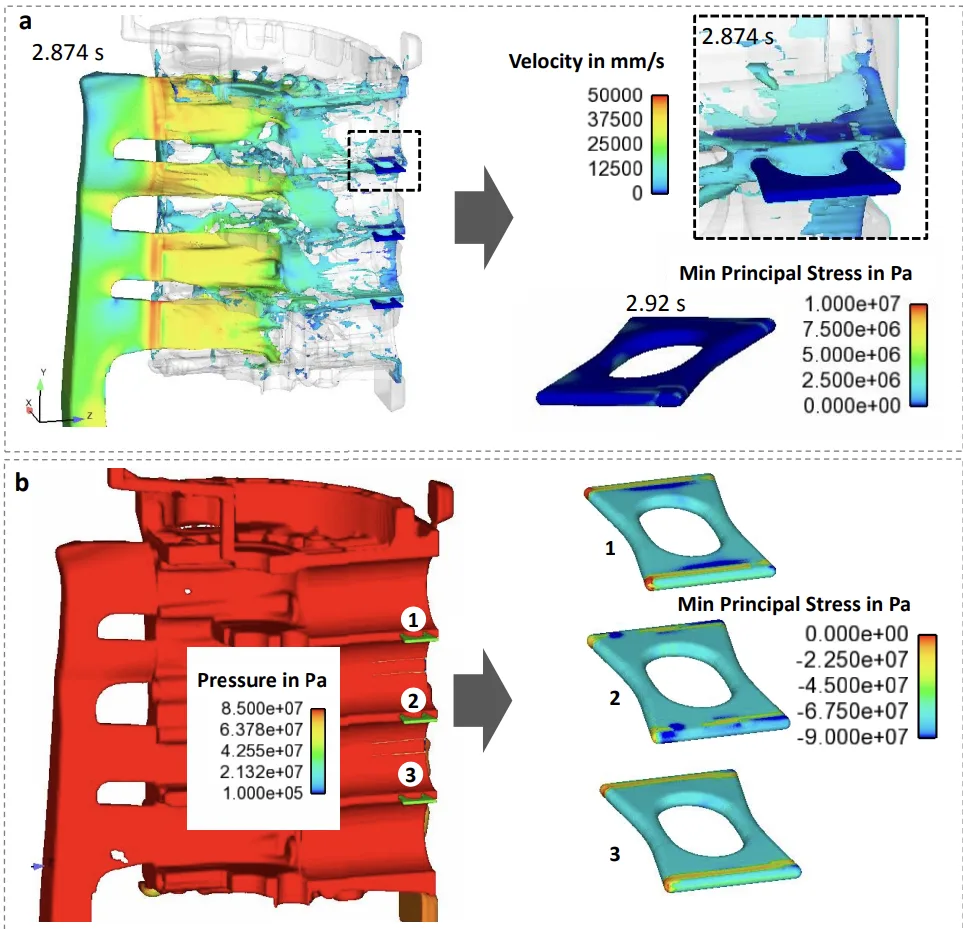
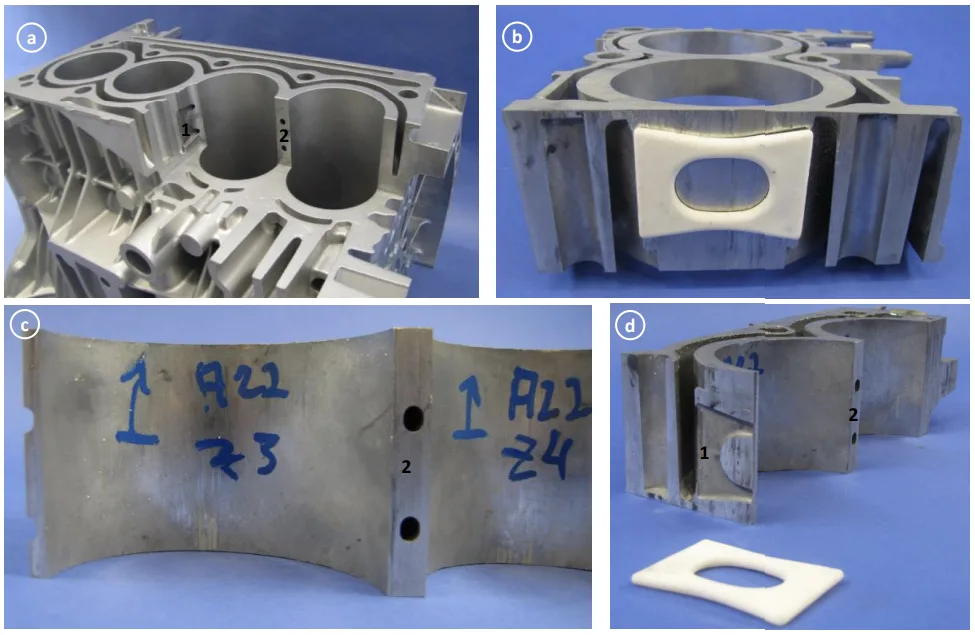
- Abbildung 1.1: a) Rohbau des Mercedes SL (BR231) inkl. Angabe der verwendeten Materialien, b) Druckgusskurbelgehäuse am Beispiel eines Reihenvierzylinders M274
- Abbildung 2.1: a) Fluidmanagementmodul mit sieben Schiebern [9], b) Druckgusswerkzeug mit komplexem Schieber (1), Schieberkulisse (2) und Hydraulikaggregat (3) [10][11]
- Abbildung 2.2: Ölfiltergehäuse mit dreidimensional verlaufenden medienführenden Kanälen [9] a) Gussbauteil, b) Röntgenaufnahme des Gussbauteils, c) Schnitt der Hohlgeometrie
- Abbildung 2.3: Demonstratorbauteil mit umgossenem Schaumkern [13], a) Demonstrator in der Ansicht von oben und im Schnitt, b) Ausschnitt aus umgossener Schaumplatte
- Abbildung 2.4: Beispiel für eine Verbundgussanwendung a) Variostruct®-Hybrid Stahl-Aluminium mit Anschnitten und Überlauf [17], b) Prinzipgeometrie ausgeführt als Formschlussprobe [17], c) Dachquerträger als SADH (Stahlblech-Aluminiumdruckguss-Hybrid) [17][21]
- Abbildung 2.5: Beispiele für einen Verbundgussdemonstrator [22] sowie die Bildung von intermetallischen Phasen im Benetzungs- und Tauchversuch zwischen Stahlblechen und Aluminiumlegierungen: a) Eine kraft-und formschlüssige Stahl-Aluminium Verbindung, hergestellt im Squeezecasting-Verfahren, b) Benetzungsprobe Stahl-Al99,98 [24], c) oben: Al-Al-Verbindung nicht behandelt; unten: Al-Substrat behandelt mit 3-stufigem Prozess [25]
- Abbildung 2.6: Combicore-Einlegerrohre[38]; a) Darstellung verschiedener Einlegerrohre zur Realisierung verschiedener Kanalgeometrien, b) Schnitt durch ein umgossenes Combicore-Rohr, c) Teilschnitt eines Combicore-Rohr inkl. eingebetteter Drahtwendel
- Abbildung 2.7: Darstellung von Hohlräumen mit Sand- und metallischen Ausschmelz-kernen: a) Druckgussbauteil mit Sandkern, oben: Längsschnitt durch Umgussbauteil, unten: entkerntes Bauteil [6], b) Druckgussbauteil mit Ausschmelzkern, oben: Längsschnitt durch Umgussbauteil, unten: aufschmelzendes metallisches Kernmaterial [6]
- Abbildung 2.8: Darstellung von Hohlräumen mittels Glas- und Keramikkernen: a) Glaskern und dazugehöriges Umgussbauteil für ein Pumpengehäuse [44], b) Prototyp eines Einzylinder-motorblocks, hergestellt mittels Keramikkern [44]
- Abbildung 2.9: Salzkerne für Gießanwendungen: a) oben: Geschossener Salzkern; unten: Im Druckgussverfahren hergestellter Salzkern [12], b) gepresste und gesinterte Salzkerne der Fa. Emil-Müller-GmbH / CeramTec AG [48]
- Abbildung 2.10: Gepresste Salzkerne und Druckgussumguss a) links: gepresster Salzbiege-riegel und Umgussbauteil; rechts: CT-Aufnahme des Umgussbauteils [10], b) entkerntes verripptes Hohlgussbauteil, hergestellt mit einem gepressten Salzkern [52]
- Abbildung 2.11: Bühler Pilotbauteil [54]: a) Salzkern Pilotbauteil, b) Schnitt durch Pilotbauteil mit sichtbarem Salzkern, c) Schnitt durch Pilotbauteil entkernt
- Abbildung 2.12: Phasendiagramm für NaCl+Na2CO3 [62] mit eingezeichneten Gitterstruktur-änderungen und dazugehörigen Gittertypen
- Abbildung 2.13: Schematische Abbildung der Kristallstruktur und des Risswachtstums für verschiedene Salzzusammensetzungen, a u. b : Eutektische Zusammen-setzung, c u. d: Reinsalz, e u. f: Zusammensetzung zwischen Eutektikum und Reinsalz [56]
- Abbildung 2.14: Diskretisierung eines Kreisbogens im Beispiel mit a) der Finite-Differenzen-Methode und Viereckselementen und b) der Finite-Element-Methode und unstrukturierten Dreickeckselementen, nach [72]
- Abbildung 2.15: Belastungssimulation für Salzkerne im Druckguss: a) Darstellung mean iso stress der Bühler Salzkerne bei Anschnittgeschwindigkeit 80 m/s oben und 120 m/s unten [86]
- b) Belastung für gepresste Salzkerne bei Anschnitt-geschwindigkeit 15 m/s oben und 35 m/s unten [10]
- Abbildung 3.1: Vorgehensweise und Arbeitspakete der vorliegenden Arbeit
- Abbildung 4.1: Darstellung der Biegestab-, Gießspiralen- und Zugstabkokille für die Salzkernprinzipuntersuchungen
- Abbildung 4.2: Skizzierter, nicht maßstabsgetreuer Versuchsaufbau für die Prinzip-untersuchungen mit der Biegestab- und Spiralkokille
- Abbildung 4.3: a) Aufbau des 3-Punkt-Biegeversuchs für die Ermittlung der Biegefestig-keiten von Salzkernen; b) Aufbau der Druckprüfung inkl. Probenabbildung zur Ermittlung der Druck-festigkeiten von Salzkernen; c) Prüfaufbau für die Zugprüfung
- Abbildung 4.4: Na2Cl-Na2CO3 Phasendiagramm inkl. eigezeichneter molarer Zusammen-setzungen für die Voruntersuchungen und Bereiche mit den zu erwartenden höchsten mechanischen Festigkeiten
- Abbildung 4.5: a) Gegenüberstellung der gemittelten Abkühlkurven für die Salzlegierungen Nr. 1 bis Nr. 7. b) Exemplarische Ergebnisdarstellung der stark untereutektischen, der unter-eutektischen und der stark übereutektischen Salzlegierungen für die Voruntersuchungen zur Auswahl einer geeigneten Salzlegierungsmischung
- Abbildung 4.6: a) Darstellung der Abkühlkurven im Mehrfachkokillen Gießexperiment für die Prozessparameterkombination =720 °C/ = 300 °C, =700 °C/ = 200 °C und = 680 °C/ = 100 °C b) Vorgehen zur Ermittlung der Abkühlraten im Biegestäbchen-gießversuch exemplarisch dargestellt an dem Prozessparameter TS =720 °C, TK =300 °C
- Abbildung 4.7: Darstellung der Gießspiralen bei den Prozessparametern = 720 °C/ = 300 °C, =700 °C/ = 200 °C und =680 °C/ = 100 °C
- Abbildung 4.8: Übersicht der Rissentstehung in der Warmrissprobe bei = 700 °C, die Ergebnisse sind tabellarisch dargestellt bei = 100 °C, 200 °C und 300 °C sowie der Ausformzeit von 15 s, 30 s, 45 s und 60 s inkl. Beispiel für die Rissgruppeneinteilung
- Abbildung 4.9: Simulationsmodell für die Mehrfachkokille in Flow3D, Darstellung der Ver-netzung, der Einfüllöffnung und der History Probes zur Aufzeichnung der Temperaturkurven
- Abbildung 4.10: Netzrandbedingungen und Oberflächentemperaturen im Mehrfachkokillen-modell dargestellt für = 100 °C, = 200 °C und = 300 °C
- Abbildung 4.11: a) Gießspiralemodell in Flow3D mit Darstellung der Schmelzeinitiierung (1) und der Vernetzung der Spirale (2 u. 3), b) Oberflächentemperaturen der Spiralkokille bei 100 °C, 200 °C und 300 °C Kokillentemperatur
- Abbildung 4.12: a) FDM-Vernetzung der Rissprobengeometrie, b) FEM-Vernetzung der Rissprobengeometrie, c) FEM Vernetzung der Mehrfachkokille zur Realisierung der Festkörperinteraktion zwischen Kokille und erstarrender Schmelze
- Abbildung 4.13: Darstellung des Temperaturfeldes im Verlauf der Erstarrung im Längschnitt bei der Rissprobengeometrie für das FDM-Netz (oben) und FEM-Netz (unten)
- Abbildung 4.14: a) Prinzipgeometrie für Verbundgussuntersuchungen inkl. Angabe des Umguss- und Einlegermaterials und Darstellung der Zugprobenentnahme-bereiche; b) Einleger-variation im Druckgussversuch, 1: geteiltes Rohr für Auszugversuche, 2: 30 mm Salzkern für Aluminiumcharakterisierung, 3: 17 mm Salzkern zur Darstellung der Einlegerbelastung
- Abbildung 4.15: a) Modulares Werkzeugkonzept für die Druckgussuntersuchungen. Gekennzeichnet sind der Formrahmen, die Entlüftung, der Werkzeugeinsatz und der 6 mm sowie 3mm Anschnitt, b) Schematische Darstellung des Druckgussumgussprozesses mit dem 6mm Anschnittsystems und prozesstechnischer Abfolge (1-3). In 2.1 – 2.3. sind zudem die neben dem Stahlrohr alternativen Einleger dargestellt.
- Abbildung 4.16: Darstellung der Versuchsergebnisse aus den Druckgussumgussversuchen, a) Verbundgussgeometrie mit 3mm-Anschnitt mit eingezeichneten Trennebenen und Zugprobenentnahmeposition, b) Verbundgussgeometrie mit 6mm-Anschnitt, c) Umguss-geometrie mit ∅ 17 Salzkern, d) Umgussgeometrie mit ∅ 30 Salzkern, e) Darstellung der Abbildungen a - d in den Seitenansicht
- Abbildung 4.17: Darstellung des Niederdruckgussprozesses für die Herstellung der Verbundgussgeometrie als CAD-Geometrie und Realbauteil. Dargestellt sind die Einlegertechnik (1) und (2) sowie die Formpakete (3) und das zentrale Anschnittsystem
- Abbildung 4.18: Darstellung der Versuchsabgüsse im Niederdruckguss: a) Darstellung der ∅ 17 und ∅ 30 Salzkerne und der Thermoelementpositionen (1) an den Stahlrohren, b) Gussrohling der Niederdruckgussversuche, c) Verputzte Versuchsgeometrie mit eingezeichneter Schnittebene
- Abbildung 4.19: a) Flow3D Modell für die Abbildung der Druckgussexperimente; Dargestellt sind die charakteristischen Modellinhalte 1-7 sowie der Übergang an der Vernetzung (8) mit unterschiedlicher Netzgröße, b) Darstellung der FEM-Vernetzung der Einlegerhülsen mit Salzkern sowie des Stahlrohrs und der Kavität
- Abbildung 4.20: Prozessablauf eines Druckgussumgussversuchs, dargestellt an dem Kolben-druck und der Kolbengeschwindigkeit über der Prozesszeit sowie an charakteristischen Zeitpunkten aus der Füllsimulation
- Abbildung 4.21: Darstellung der von Mises-Spannung im Salzkern und der Schmelze-geschwindigkeit für drei charakteristischer Zeitpunkte im Füllprozess der Umgussprinzip-geometrie, a) Umschaltpunkt von erster zur zweiten Phase, b) erstes Auftreffen der Schmelze auf den Salzkern, c) Nachdruckphase
- Abbildung 4.22: Vorgehen beim Auszugversuch zur Charakterisierung der Anbindungsqualität zwischen Stahleinleger und Aluminiumumguss, a) ungeprüfte Auszugprobe und Prüfaufnahme, b) Versuchsaufbau im CAD-Schnitt und Realbauteil, c) teilgeprüfte Probe nach 15 mm Traversenverfahrweg, d) vollständig ausgezogene Probe im CAD-Schnitt und Realbauteil
- Abbildung 4.23: a) Ausdruckversuch zur Charakterisierung der Anbindung zwischen Einleger und Umgussmaterial und Darstellung der Ringbeschriftung, b) Aufbau für die Haftzugprüfung an der geteilten Verbundguss-Ringgeometrie, exemplarisch dargestellt für eine feuerverzinkte Probe
- Abbildung 4.24: a) Schwerzugversuch für die Charakterisierung der Anbindung auf Scherung, b) exemplarische Darstellung einer geprüften Haftzug- bzw. Scherzugprobe am Beispiel eines feuerverzinkten Stahleinlegers
- Abbildung 4.25: Stahl-Aluminiumverbundgussbauteil mit Zink-Zwischenschicht, hergestellt im Druckguss: a) Lichtmikroskop-, b) Rasterelektronenmikroskopaufnahme
- Abbildung 4.26: a) Technische Zeichnung der Miniflachzugprobe mit einer Wandstärke von 2mm, b) Fließkurvenapproximation am Beispiel AlSi9MgMn-T6
- Abbildung 4.27: Auswertung der Härtemessung nach Brinell für die Zugprobe und die Umgussgeometrie mit einer linearen Ausgleichsgerade, für beide Härtewertkurven
- Abbildung 4.28: Darstellung der gemessenen Fließkurven bis 30 % plastischer Dehnung für AlSi9MgMn-F mit der Endung –a; Die approximierten Kurven nach dem Hocket-Sherby-Model sind mit der Endung –g bezeichnet
- Abbildung 4.29: Temperaturaufzeichnungen der Schmelzetemperaturen an der Rohraußen-fläche und Rohrinnenfläche mittig in axialer Richtung aus dem Druckgussumgussversuch für Schussnummer 12 und 13
- Abbildung 4.30: a) FEM-Modell für die Abkühl- und Auszugsimulation in ABAQUS dargestellt im 34 Schnittmodell und im 2D-Model, b) Schematische Darstellung der theoretischen Berechnungsvorgehensweise zur Abkühl- und Auszugsimulation in ABAQUS
- Abbildung 4.31: a) Darstellung der maximalen Auszugskraft in Abhängigkeit verschiedener Kontaktdefinitionen einer Importberechnung in Abaqus, b) Einfluss des Penalty Scale Faktors auf die maximale Auszugskraft
- Abbildung 4.32: a) Darstellung des Abkühlmodells im 34 -Schnitt für die Ausdruck-simulation, b) Ausdruckmodell im 34 -Schnitt mit Halter und Stempel, c) 2D-Darstellung des Ausdruck-modells, d) Vernetzung und Spalte an den Kontaktflächen zwischen Stahlring und Stempel sowie Aluminium und Halter
- Abbildung 4.33: a) Schematische Darstellung der Funktionsweise von kohäsiven Elementen und kohäsiven Kontaktflächen, b) Schädigungstheorie zur Beschreibung von kohäsiven Elementen und kohäsiven Flächen in Abaqus 6.13 [113]
- Abbildung 4.34: a) Darstellung eines feuerverzinkten Stahlrings nach dem Ausdruckversuch mit geschädigter intermetallischer Phase, b) Kraft- und Stoffschlussbereich im 3D-Ausdruck-modell aufgezeigt am Aluminiumumgussbereich
- Abbildung 4.35: a) Darstellung eines feuerverzinkten Stahlrings nach dem Haftzugversuch mit eingezeichneter geschädigter intermetallischer Phase, b) Darstellung des numerischen Modells zur Abbildung des Haftzugversuchs inkl. Rand-bedingungen und getrenntem Zustand
- Abbildung 4.36: a) Darstellung eines Spannungs-Dehnungs-Diagramms mit der Beschreibung eines Schadenfortschrittes und Verringerung der Elastizität ab Initiierung; Abbildung einer Kurve mit und ohne Schädigung [113], b) Abbildung der fünf verschiedenen Spannungs-zustände mit beispielhaften Probengeometrien für die Ermittlung der Triaxialitäts-zustände η von -0,666 bis + 0,666
- Abbildung 4.37: Proben zur Ermittlung des Verhaltes unter verschiedenen Spannungs-zuständen a) Druckprobe, b) Kerbzug R4, c) Scherzug 0°, d) Scherzug 45°
- Abbildung 4.38: Iterativ ermittelte Kraft-Weg-Kurven in ABAQUS für die Legierung AlSi7Mg0,15-F am Beispiel des Zug- und Kerbzugversuchs sowie der beiden Scherzugversuche bei 0° und 45. Zudem ist der jeweilige Vergleich zwischen der optischen Aramis-Messung (links) und der numerischen Simulation (rechts) dargestellt. Als Skala wird die Vergleichs-dehnung nach von Mises verwendet
- Abbildung 4.39: a) Versuchsaufbau für die Druckprüfung inkl. Darstellung der Druckprobe im Ausgangszustand und nach Ende der Verfahrweges für die AlSi7Mg0,15-Legierung im F- und T7-Zustand; b) Vergleich der numerischen Simulation und des experimentellen Kraft-Weg-Verlaufs im Druckversuch exemplarisch für AlSi7Mg0,15-T7
- Abbildung 4.40: Exemplarische Darstellung der wahren plastischen Dehnung bei Versagen über der Triaxialität η inklusive Triaxialitätsverlauf und Mittelwert bis zum Versagen im kritischen Element für die Legierung AlSi7Mg0,15-F
- Abbildung 4.41: Schematische Darstellung des zeitlichen Verlaufs der Dehnung ε und der Dehnrate ε̇ , verursacht durch primäres (1), sekundäres (2) und tertiäres (3) Kriechen bei metallischen Werkstoffen bis zum Bruch [117]
- Abbildung 4.42: a) Technische Zeichnung der Zeitstandprobe für die Untersuchung des Kriechverhaltens der verwendeten Aluminiumlegierungen, b) Versuchs-aufbau für die Zeitstandversuche
- Abbildung 4.43: Darstellung der Zugfestigkeit (a) und Streckgrenze (b) für die Aluminium-legierung AlSi7Mg0,15 über Temperatur
- Abbildung 4.44: Darstellung der Stufenzeitstandversuche für die Legierung AlSi7Mg0,15-F für a) bei der Temperatur 350 °C und b) bei der Temperatur 400 °C
- Abbildung 4.45: Ermittlung der Dehnrate ε̇ cr für die Stufenzeitstandversuche der Aluminium-legierung AlSi7Mg0,15-F a) bei der Temperatur 350 °C und b) bei der Temperatur 400 °C
- Abbildung 4.46: Parameterermittlung für das Kriechmodel nach Norton für AlSi7Mg0,15-F
- Abbildung 4.47: Vergleich zwischen der numerischen Simulation und den experimentellen Versuchen für die Stufenzeitstandversuche der Aluminiumlegierung AlSi7Mg0,15-F für a) bei der Temperatur 350 °C und b) bei der Temperatur 400 °C
- Abbildung 5.1: a) Darstellung der ermittelten 3-Punkt-Biegefestigkeiten in Abhängigkeit der Zusammensetzung; Zudem die Darstellung der ermittelten Festigkeiten nach Yaokawa [56], b) Darstellung des Bruchzeitpunkts bei der Warmrissprobe und der Randfaserdehnung in der Drei-Punkt-Biege-Prüfung in Abhängigkeit der Salzkernzusammensetzung
- Abbildung 5.2: a) Darstellung der Temperatur bei Bruch und der Zeit bis zum Erreichen der 400 °C Grenze für die untersuchten Legierungen Nr. 2 bis Nr. 7, b) Darstellung der Abkühl-raten für die Salzmischung Nr. 2, Nr. 5, Nr. 6 und Nr. 7 für den Bereich 1: Messpunkt 1 – Liquidus, Bereich 2: Liquidus – Solidus und Solidus – 400 °C
- Abbildung 5.3: Gefüge der DoE5 mittig und im Randbereich mit x300 Vergrößerung
- Abbildung 5.4: Vergleich der Abkühlraten mit der Erstarrungsmorphologie der DoE-Gießserien. Dargestellt sind drei charakteristische Proben mit den minimalen, mittleren sowie maximalen errechneten Abkühlraten.
- Abbildung 5.5: a) Gegenüberstellung der 3-Punkt-Biege-, Zug- und Druckfestigkeiten sowie des E-Moduls der ausgewählten Salzkernlegierung bei Raumtemperatur bis 400 °C, b) Darstellung der gemessenen Dehnung im 3-Punkt-Biegeversuch und Zugversuch in Abhängigkeit der Temperatur
- Abbildung 5.6: Mittlere 3-Punkt-Biegefestigkeit der mechanisch bearbeiteten Salzproben inkl. Standardabweichung und Auflageposition im Biegeversuch. Schematisch sind in der Biegeprobe im Längsquerschnitt der Ursprungsquerschnitt, die Trennebene und der durch Bearbeitung erzeugten Prüfquerschnitt eingezeichnet.
- Abbildung 5.7: Simulationsergebnis aus der Formfüll- und Erstarrungssimulation in Flow3D; dargestellt wird die Temperaturverteilung der Kokille vor dem Gießvorgang bis hin zum Zeitpunkt der Entformung des Biegestäbchens nach 90 s
- Abbildung 5.8: Darstellung des Temperatur-Zeit-Verlaufs für die Schmelzetemperatur in der Kavität und der Wandtemperatur nahe der Kavität für das Experiment und die numerische Berechnung sowie der Festkörperanteil (Solid Fraction) während des Füllvorganges bis 1,8 s Prozesszeit.
- Abbildung 5.9: Vergleich der experimentell und numerisch ermittelten Temperaturkurven; Dargestellt wird der Temperaturverlauf in der Mitte des Salzbiegestäbchens während des Gießprozesses. Als numerisches Materialmodell wird der iterativ bestimmte, finale Datensatz SFQ9V3 zugrunde gelegt.
- Abbildung 5.10: Füllvorgang beim Spiral-Kokillenguss dargestellt in acht Schritten
- Abbildung 5.11: Vergleich der Spirallängen zwischen Experiment und numerischer Simulation. Dargstellt werden der Zentralpunkt, zwei weitere Prozessparameterkombinationen mit Angabe der Gießlängen sowie einer schematischen Darstellung in der Gießspirale.
- Abbildungsqualität von Gussphänomenen in der Biegestab- und Gießspiralkokille
- Abbildung 5.14: Auswertung der Rissentstehung nach Gießtemperatur (links) und Kokillen-temperatur (rechts); Unterteilt werden die Risse in vier Kategorien.
- Abbildung 5.15: Auswertung der Rissentstehung über die Temperaturdifferenz zwischen Kokillentemperatur und Gießtemperatur; Unterteilt werden die entstehenden Risse in vier Kategorien.
- Abbildung 5.16: Darstellung der zwei Extrempunkte der Salzkerngießversuche zur Untersuchung der Warmrissfähigkeit; Worst Case: =720°C und =100°C mit dem höchsten ∆ zwischen Kokille und Schmelze; Best Case: =680°C und =300°C mit dem geringsten ∆ zwischen Kokille und Schmelze
- Abbildung 5.17: Darstellung der ersten Hauptspannung im Verlauf der Abkühlung in der Salzkernwarmrissprobe mit Schwindungsbehinderung für die Variante 1: =720°C/ =100°C und Variante 2: =680°C/ =300°C
- Abbildung 5.18: Verlauf der ersten Hauptspannung in der Randschale der Probenmitte und im Speiserübergangsbereich zur Stabkontur für die Variante 1: =720°C/ =100°C und Variante 2: =680°C/ =300°C
- Abbildung 5.19: Darstellung der ersten Hauptspannung in der Randschale der Probenmitte und im Speiserübergangsbereich zur Stabkontur für die Variante 1: =720°C/ =100°C und Variante 2: =680°C/ =300°C über der Temperatur; Zudem ist die maximal ertragbare Spannung, basierend auf den durchgeführten Zugversuchen im Diagramm, eingezeichnet.
- Abbildung 5.20: Schematische Darstellung der Funktionsweise des angepassten Solvers in Flow3D zur Darstellung der beiden Skalare „Hot Crack“ und „Hot Crack Duration“
- Abbildung 5.21: Darstellung des Hot Crack Criterions und der Hot Crack Duration für den Fall =680°C/ =300°C und =720°C/ =100°C; Abgebildet sind die Ergebnisse bei 15 s, 30 s, 45 s und 60 s Abkühlzeit.
- Abbildung 5.22: Darstellung der charakteristischen Schusskurven inkl. des dazugehörigen Bruchverhaltens der Salzkerne nach dem Druckgussumgussprozess
- Abbildung 5.23: Abbildung der von-Mises-Spannung im Salzkern und Schmelze-geschwindigkeit kurz nach dem Auftreffen der Aluminiumschmelze für die Kolbengeschwindigkeit a) 0,7 s , b) 1,0 s und c) 4,0 s
- Abbildung 5.24: Darstellung der ersten und zweiten Hauptspannung an der Zug- und Druckseite über die Prozesszeit inkl. Markierung der experimentell ermittelten Zug- und Biegefestigkeit für den Belastungfall mit der höchsten Kolbengeschwindigkeit von 4,0 s
- Abbildung 5.25: Abbildung des Kolbendrucks, der ersten drei Hauptspannungen in der Randschale des Salzkerns während des Umgussprozesses am Ende der zweiten Phase mit Übergang zur dritten Phase
- Abbildung 5.26: a) Temperaturverteilung in der Kavität und im Salzkern während der dritten Phase des Druckgussprozesses, b) Druckverteilung in der Kavität und Spannung im Salzkern während der Nachdruckphase
- Abbildung 5.27: Exemplarische Darstellung des Füllvorgangs beim Umguss des Stahleinlegers mit 1,5 mm Wandstärke mit von-Mises-Spannung im Rohr und der Geschwindigkeit der Aluminiumschmelze in der Kavität sowie der Nachdruckphase mit 480 bar und 800 bar Nachdruck
- Abbildung 5.28: Übersicht der verwendeten Stahlrohre (inkl. Wandstärke) und der Ergebnisse der Umgussversuche bei der Kolbengeschwindigkeit 2,8 ms-1 mit und ohne dem Nachdruck; Gegenüberstellung der von-Mises-Spannungen für das 1,5 mm und 2 mm Stahlrohr bei einem Nachdruck von 500 bar sowie für das 2 mm und 2,5 mm Stahlrohr bei einem Nachdruck von 780 bar
- Abbildung 5.29: Gegenüberstellung der ermittelten Maximalspannungen für die unterschiedlichen Stahleinleger, umgossen im Aluminiumdruckguss und geprüft im Ausdruckversuch
- Abbildung 5.30: Gegenüberstellung der gemittelten Energieaufnahme für die unterschiedlichen Stahleinleger, umgossen im Aluminiumdruckguss und geprüft im Ausdruckversuch
- Abbildung 5.31: Betrachtung der a) Maximalspannung und b) Energie der unbeschichteten, profilierten Einleger im Ausdruckversuch, aufgetragen über den taktil gemessenen Rz-Wert
- Abbildung 5.32: REM-Aufnahmen des feuerverzinkten Stahleinlegers, eingelegt bei Raum-temperatur und 680 °C Schmelzetemperatur; Abbgebildet ist der Anguss (Bereich1), die erste Abnahme der stoffschlüssigen Anbindung (Bereich2), das Ende der stoffschlüssigen Anbindung (Bereich3) sowie der Überlauf, der keinerlei stoffschlüssige Anbindung aufweist (Bereich4).
- Abbildung 5.33: Darstellung des Einflusses von Einlegertemperatur und Schmelzetemperatur sowie der T6-Wärmebehandlung auf die Maximalspannung und Ausdrückenergie am Beispiel des feuerverzinkten Einlegers; Die Erhöhung der Schmelzetemperatur ist von 680°C auf 700°C gewählt, die vorgewärmten Einleger sind bei 250 °C gewählt.
- Abbildung 5.34: Darstellung der a) Scherzugfestigkeit und b) Haftzugfestigkeit für ausgewählte Stahl-Aluminiumverbindungen mit stoffschlüssigen Anteilen
- Abbildung 5.35: a) Darstellung eines feuerverzinkten Stahlrings nach dem Haftzugversuch mit eingezeichneter geschädigter intermetallischer Phase, b) Darstellung des numerischen Modells zur Abbildung des Haftzugversuchs inkl. Rand-bedingungen und getrenntem Zustand
- Abbildung 5.36: Darstellung der Auszugberechnung in 20-facher Überhöhung in radialer Richtung mit Darstellung der von-Mises-Spannung
- Abbildung 5.37: a) Gegenüberstellung der Kraft-Weg-Verläufe der Auszugprüfung aus dem Experiment, der rein impliziten Simulation mit Haftreibkoeffizient und der Implizit-Explizit-Import-Simulation mit Berücksichtigung des Wechsels von Haft- auf Gleitreibung, b) Innenradius der rotationssymmetrischen Berechnung und taktilen Vermessung an drei ausgewählten Winkeln in Abhängigkeit der axialen Richtung
- Abbildung 5.38: a) Darstellung der Kontaktspannung in radialer Richtung am Distanzring mit Angabe der Maximalspannung der „direct“ und „penalty“ Kontakt-formulierung aus ABAQUS mit und ohne Kriechmodell, b) Übersicht der Spannungsverteilung in radialer Richtung über das gesamte Bauteil, c) Innenradius nach dem Auszug für die beiden Kontaktformulierungen mit und ohne Kriechmodell
- Abbildung 5.39: a) Spannungen in radialer Richtung nach dem Abkühlvorgang des Ausdruckmodells, b) Spannungszustand im ersten Inkrement der expliziten Import-Ausdruckberechnung, c) Spannungszustand am Ende des Kontaktfindungsschrittes
- Abbildung 5.40: Vergleich zwischen Experiment und numerischer Simulation im Ausdruckversuch, a) Kraft-Weg-Verlauf des 2D Ausdruckverlaufs, b) Kraft-Weg-Verlauf des 3D-Ausdruckversuchs
- Abbildung 5.41: Entstehung der radialen Spannungen 11, dargestellt in einem zylindrischen Koordinatensystem, während des Abkühlvorgangs im 3D-Verbundgussmodell
- Abbildung 5.42: Darstellung der Spannungen 11 in radialer Richtung im zylindrischen Koordinatensystem und der Kontaktspannung im Stahl-Aluminiuminterface mittig, in Umfangsrichtung zu Beginn und am Ende des Trennvorgangs
- Abbildung 5.43: Vergleich der experimentellen und numerischen Kraft-Weg-Kurve im a) Haftzugversuch und b) Scherzugversuch einer feuerverzinkten und mit AlSI10MgMn umgossenen Stahlprobe
- Abbildung 5.44: Gegenüberstellung der numerischen Kraft-Weg-Kurven mit und ohne thermischer Importberechnung für a) den Haftzugversuch und b) den Scherzugversuch
- Abbildung 5.45: Darstellung der Größe CPRESS und CSHEAR für die Simulation mit Abkühlvorgang (oben) und ohne (unten) für den Fall a) nach dem Trennvorgang, am Ende des Kontaktfindungsschrittes und für den Fall b) kurz vor dem Versagen der kohäsiven Schicht
- Abbildung 5.46: a) Darstellung des experimentell ermittelten Rz-Werts und des numerischen statischen Reibkoeffizienten über die experimentell und numerisch ermittelte maximale Ausdruckspannung, b) Gegenüberstellung des experimentellen und numerischen Kraft-Weg-Verlaufs aus dem Ausdruckversuch einer charakteristischen feuerverzinkten Verbundgussprobe
- Abbildung 5.47: Schematische Darstellung der wirkenden Parameter im FEM-Modell einer Stahl-Aluminium-Verbundgussprobe vor und nach der Schädigung der kohäsiven Schicht
- Abbildung 5.48: Vergleich zwischen numerischer Berechnung und Experiment unter Annahme erhöhter Werte für die kohäsive Schicht
- Abbildung 5.49: Schematische Darstellung der Funktionsweise der verwendeten Subroutine zur Abbildung kombinierter stoff- und kraftschlüssiger Stahl-Aluminium-Verbunde mit der ABAQUS Kontaktdefinition
- Abbildung 5.50: Aufbau der Kontaktspannung, dargestellt durch die Größe CPRESS in dem Stahl-Aluminium-Kontakt mit und ohne der Subroutine VUINTER; Der Bereich der Subroutine ist mit einer roten gestrichelten Linie verdeutlicht.
- Abbildung 5.51: a) Vergleich der Kraft-Weg-Kurve von Experiment und der numerischen Berechnung unter Verwendung der Subroutine, b) Darstellung der Größe CSHEAR2 im Zeitschritt vor und nach der Schädigung der Schicht
- Abbildung 6.1: a) Verbundguss-A-Säulenkonzept mit Darstellung der zwei verwendeten Stahlrohre, des Stahlblechs und des Aluminiumumgussbereichs; b) Sandform und Sandkern; c) Gussrohling der Verbundgusssäule mit Angusssystem und Speisern
- Abbildung 6.2: a) Realaufnahmen des Prüfaufbaus zur Umsetzung des A-Säulenersatzlastfalls mit Dateilaufnahmen der Fixierungen 1-3, b) FEM-Modell für den Roof-Crush-Test der Verbundguss-A-Säule inkl. Stempel
- Abbildung 6.3: Vergleich des Kraft-Weg-Verlaufs für den Ersatzlastfall des Dacheindrück-tests zwischen Experiment und numerischer Simulation; Dokumentiert ist der Verlauf aus dem Experiment im Gusszustand und im T7-Zustand sowie der dazugehörige Verlauf aus der numerischen Berechnung mit Schädigungsmodell. Ergänzend sind die Ergebnisse der Seriengeometrie und einer Berechnung ohne Schädigungsmodell eingezeichnet.
- Abbildung 6.4: a) Rohteil des 8-fach-Abgusses und; b) Darstellung der Füllung und Schmelze-geschwindigkeit nach 0,105 sowie der Erstarrung der Salzkernstegkü
7. Conclusion:
Summary of key findings:
Both technologies examined, composite casting and cast salt cores, are fundamentally recommended for an application.
-Salt cores casting with liquid phase have the most potential for create holes.
-With steel inserts which stay in the cast part, it's recommend to use a force and form closure connection.
Possible areas for future expansion research:
- Further investigation of salt core compositions, particularly the promising hypereutectic alloy.
- Development of a method to predict the formation of intermetallic phases in composite casting.
- Investigation of the influence of different cooling rates on material properties.
- Investigation of creep behavior influence.
8. References:
- [1] HARTER C.: Abschlussbericht CO2-Emissionsreduktion bei Pkw und leichten Nutzfahrzeugen nach 2020. Projektnummer 123320, Im Auftrag des Bundesministeriums für Wirtschaft und Energie (BMWi), Institut für Kraftfahrzeuge (ika), RWTH Aachen, 2014
- [2] HENNING, F.; MOELLER, E.: Handbuch Leichtbau Methoden, Werkstoffe, Fertigung. Carl Hanser Verlag München Wien, 2011, ISBN 978-3-446-42267-4
- [3] KLEIN, B.: Leichtbau-Konstruktion Berechnungsgrundlagen und Gestaltung. 10. Auflage Springer Fachmedien Wiesbaden, 2013, ISBN 978-3-658-02271-6
- [4] OSTERMANN, F.: Anwendungstechnologie Aluminium. 2. Auflage Springer-Verlag Berlin Heidelberg, 2007, ISBN 978-3-540-71196-4
- [5] HERMANN, C.; PRIES, H.; HARTMANN, G.: Energie- und ressourceneffiziente Produktion von Aluminiumdruckguss. Springer-Verlag Berlin Heidelberg, 2013, ISBN 978-3-642-39852-0
- [6] KUGEL, A; BÜHRIG-POLACZEK, A.: Entwicklung einer neuen Kerntechnologie für das Druckgussverfahren. Giesserei Rundschau 49, 2002, S.38-42
- [7] FRITZ, A.H.; SCHULZE, G.: Fertigungstechnik. Springer-Verlag Berlin Heidelberg, 2010, ISBN 978-3-642-12878-3
- [8] ILSCHNER, B.; SINGER, R.F: Werkstoffwissenschaften und Fertigungstechnik – Eigenschaften, Vorgänge, Technologien. 5. Auflage Springer-Verlag Berlin Heidelberg, 2010, ISBN 978-3-642-01733-9
- [9] BÖHNLEIN, C.: Darstellung 3-dimensionaler, funktionaler Hohlstrukturen im Druckguss durch Gasinjektion. Dissertation, Technische Universität Claustahl, 2013
- [10] FUCHS, B.: Simulationsgestützte Vorhersage der Überlebenswahrscheinlichkeit verlorener Salzkerne im Leichtmetall-Druckguss. Aalener Gießereikolloquium, 2013
- [11] FUCHS, B.: Salzkerntechnologie für Hohlgussbauteile im Druckguss. Dissertation, Cuvillier Verlag Göttingen, 2014, ISBN 978-3-95404-758-1
- [12] KALLIEN, L.H.: Hohle Strukturen im Druckguss durch Gasinjektion und Salzkerne. Gießerei Kolloquium, 2013 XLIX
- [13] HEINRICH, F.: Encasing of Al-Foams by Die Casting as Manufacturing Process for Light Weight Composites. Dissertation, FAU Erlangen-Nürnberg, 2003, URN urn:nbn:de:bvb:29-opus-447
- [14] HIRSCHMANN, M.: Manufacturing technology and properties of injection molded magnesium integral foam parts. Dissertation, FAU Erlangen-Nürnberg, 2007, urn:nbn:de:bvb:29-opus-6950
- [15] KERBER, K.: Verfahren zum Verbundguss der Leichtmetalle Aluminium und Magnesium durch den Druckguss. Dissertation, Gottfried Wilhelm Leibniz Universität Hannover, PZH Produktionstechnisches Zentrum GmbH, 2011, ISBN 978-3-943104-04-2
- [16] CESPEDES-GONZALES, G.E.: Aluminium-Stahl-Verbundguss als strukturgebendes Fügeverfahren für attraktive Fahrwerkskomponenten – Darlegung der Prozesskette. Dissertation, Technische Universität Bergakademie Freiberg, 2012, ISBN 978-3-86012-440-6
- [17] OBERSCHELP, C.: Hybride Leichtbaustrukturen für den Karosseriebau – Gusswerkstofforientierte Anwendungsuntersuchung für das Druckgießen. Dissertation, RWTH Aachen, 2012
- [18] LAO, B.: Druckgegossene Metallhybridstrukturen für den Leichtbau-Prozess, Werkstoffe und Gefüge der Metallhybriden. Dissertation, Aachen, 2013
- [19] BÜHRIG-POLACZEK, A.; RÖTH, T.; BAUMEISTER, E; ET AL.: Hybride Leichtbaustrukturen in Stahlblech-Leichtmetall Verbundguss. Internationaler Expertenpreis Automobil-leichtbau, 15. Europäische AutomobilLeichtbaukonferenz, 2006
- [20] NOWACK, N.; OBERSCHELP, C.; LAO, B.; ET AL.: Gute Perspektiven für StahlAluminium-Hybride im Automotivebereich. Gießerei 96, 2009, S. 110-122
- [21] PASLIGH, N.: Hybride formschlüssige Strukturverbindungen in Leichtbaustrukturen aus Stahlblech und Aluminiumdruckguss. Dissertation, RWTH Aachen, 2010
- [22] BITSCHE, R.D.: Design and Computational Analysis of Compound Castings and other Mult-Material. Dissertation, Fortschr.-Ber. VDI Reihe 18 Nr. 324. Düsseldorf:VDI Verlag, 2009, ISBN 978-3-18-332418-7
- [23] WASMUTH, U.: Orts- und zeitabhängige Analyse von Eigenspannungen im Verbundguss. Dissertation, utg – Forschungsberichte Band 50, 2009, ISBN 978- 3-8-89791-400-1
- [24] FRAGNER, W.; SONNLEITNER, R.: Investigation of the Interface Formation and its Properties for Al Compound Casting. 5th European Metallurgical conference, Vol 4, 2009 L
- [25] FRAGNER, W.; PAPIS, K.; WOSIK, J.; ET AL.: Herausforderungen und Lösungsmöglichkeiten bei der Herstellung von Verbundgussbauteilen. 5.Ranshofer Leichtmetalltage, Vortragstexte, 2008, ISBN-13: 978-3-902092-05-2
- [26] ZHANG, N.; WOSIK, J.; FRAGNER, W.; ET AL.: Three-dimensional analysis of the growth of intermetallics phases between solid steel and molten aluminium. Intermetallics 18, 2010, S. 221-225
- [27] PAN, J.; YOSHIDA, M.; SASAKI, G.; ET AL.: Ultrasonic Insert Casting of Aluminium Alloy. Scripta mater. 43 (2000), S.155-159
- [28] DEZELLUS, O.; DIGONNET, B.; SACERDOTE-PERONNET, M.; ET AL.: Mechanical testing of steel/aluminium-silicon interfaces by pushout. International Journal of Adhesion & Adhesives 27 (2007), S. 417-421
- [29] DEZELLUS, O.; ZHE, M.; BOSSELET, F; ET AL.: Mechanical testing of titanium/aluminium-silicon interface: Effect of T6 heat treatment. Materials Science and Engieering A 528, 2011, S. 2795-2803
- [30] PAPIS, K.J.M; HALLSTEDT, B.; UGGOWITZER, P.J.: Light metal compound casting. Science in China Series E: Technological Sciences 52 no.1, 2009, S. 46-51
- [31] PAPIS, K.J.M; LÖFFLER, J.F; UGGOWITZER, P.J.: Interface formation between liquid and solid Mg alloys – An approach to continuously metallurgic joining of magnesium parts. Material Science and Engineering A 527, 2010, S. 2274-2279
- [32] PAPIS, K.J.M; HALLSTEDT, B.; LÖFFLER, J.F.; ET AL.: Interface formation in aluminium-aluminium compound casting. Acta Materialia 56, 2008, S. 3036- 3043
- [33] HAJJARI, E.; DIVANDARI, M.; RAZAVI, S.H.; ET AL.: Dissimilar Joining of AlMg light metals by compound casting process. Journal of Material Science 46, 2011, S. 6491-6499
- [34] HAJJARI, E.; DIVANDARI, M.; RAZAVI, S.H.; ET AL.: Intermetallic compounds and antiphase domains in Al/Mg compound casting. Intermetallics 23, 2012, S. 182- 186
- [35] RÜBNER, M.; GÜNZL, M.; KÖRNER, C.; SINGER, R.F.: Aluminium-aluminium compound fabrication by high pressure die casting. Materials Science and Engineering A 528 (2011), S. 7024-7029
- [36] KOERNER, C.; SCHWANKL, M.; HIMMLER, D.: Aluminum-aluminum compound castings by electroless deposited zinc layers. Journal of Materials Processing Technology 214, 2014, S.1094-1101
- [37] WEDLER, J.; SCHWANKL, M.; KOERNER, C.: Al-Al-Verbundguss mit höherfesten Knetlegierungen, Gießerei 102, 07/2015, S.46-53 LI
- [38] DINGER, P.; HEPPES, F.; RUPP, S.: Stabile Einlegerrohre für Gießereien. Giesserei 99, 02/2012, S. 22-27
- [39] DINGER, P.; HEPPES, F.; RUPP, S.: Stabile Aluminium-Einlegerrohre für Druckguss und andere Gießverfahren – Innovative Anwendungen mit integrierten Kanälen aus einem Guss. Druckguss 10/2012, S. 445-452
- [40] KUGEL, A; BÜHRIG-POLACZEK, A.: Möglichkeiten zur Erzeugung von Hohlräumen in Druckgussteilen. Giessereiforschung 56, 2004, S. 14-22
- [41] RAAB, M; HÜLSENBERGER, D.: Säurelösliche Hohlglaskerne für den Aluminiumguss Teilprojekt 2: Hohle Gießkerne aus Glas. TU Ilmenau, Schlussbericht, 2005
- [42] RAAB, M; HARTMANN, K.; HÜLSENBERGER, D.: Entwicklung einer Schmelztechnologie Teilprojekt 2: Lösliche Gießkerne aus Glas. TU Ilmenau, Schlussbericht, 2003
- [43] GIEGOLD, M.: Stampi con Anima per Veicoli Effecienti (SAVE) – Druckgusswerkzeuge mit Kernen für effektive Automobile. Gießereikolloquium Aalen, 2013
- [44] MOSCHINI, R.: Production of hollow components in HPDC through the use ofceramic lost cores. Congressi di Fonderia ASSOFOND, 2012
- [45] BÜNCK, M.: Entwicklung einer optimierten Vormaterialherstellung für den Einsatz verlorener Kerne beim Druckgießen teilerstarrter Materialsuspensionen. Dissertation, RWTH Aachen, 2010
- [46] MICHELS, H; BÜNCK, M.; Bührig-Polaczek, A.: Suitability of lost cores in rheocasting process. Transactions of Nonferrous Metals Society of China 20, 2010, S. 948-953
- [47] KALLIEN, L.; BÖHNLEIN, C.; DWOROG, A.; MÜLLER, B.: Ergebnisse aus dem Forschungsprojekt 3-D-Freiform – medienführende Kanäle im Druckguss. Gießerei, Ausgabe 12/2013, S. 36-42
- [48] SCHEYDECKER, M.: Innovationspotential Salzkerne – Herausforderungen für die Serienanwendung im Aluminium-Guss. VDI Wissensforum, 2014
- [49] FUCHS, B.; HEID, R.; THOMA, C.; DILGER, K.: Angepasste Wärmebehandlung von druckgegossenen Aluminiumstrukturbauteilen mit verlorenem Salzkern. Giesserei 101 06/2014, S. 52-59
- [50] FUCHS, B.; KÖRNER, C.: Dwell pressure induced compression of lost salt cores in high pressure die casting. International Foundry Research 65, 2013, No.3 ,S. 18- 23 LII
- [51] FUCHS, B.; EIBISCH, H., KÖRNER, C.: Core Viability simulation for salt core Technology in high-pressure diecasting. International Journal of Metalcasting, 2013. S.39-44
- [52] EIBISCH, H.: Studien zu Kerntechnologien hohlgegossener Druckgussbauteile. Aalener Gießerei Kolloquim, 2014, Vortrag
- [53] ASCHMANN, A.: Salzkerne – neue Perspektiven für den Druckguss. Aalener Giesserei Kolloquium, 2013
- [54] FABBRONI, M.: Lost Core – Ein industrieller Prozesspfad für hochwertige Salzkerne. Druckguss, Ausgabe 10/2013, S. 446-447
- [55] HABEL, G..: Wirtschaftlichkeit beim Salzkern Verfahren im Aluminium Druckguss. Aalener Giesserei Kolloquium, 2013
- [56] YAOKAWA, J.; DAISUKE, M.; KOICHI, A.; ET AL.: Strength of Salt Core Composed of Alkali Carbonate and Alkali Chloride Mixtures Made by Casting Technique. Materials Transactions, Vol. 48, No. 5 (2007), S.1034-1041
- [57] YAMADA, Y.; YAOKAWA, J.; YOSHII, H; ET AL.: Developments and Application of Expendable Salt Core Materials for High Pressure Die Casting to Apply ClosedDeck Type Cylinder Block. SAE-Paper 2007-32-0084, 2007
- [58] OHLE, M.: Für den Druckguss entwickelt: Gegossene Salzkerne mit geometrischer Gestaltungsfreiheit. Frauenhofer IFAM, Presseinfo., 2013
- [59] LATSCHA, H.A.; KLEIN, H.P.: Anorganische Chemie – Chemie-Basiswissen 1. 9.Auflage, Springer Berlin Heidelberg New York, 2007, ISBN: 978-3-540- 69863-0
- [60] SCHWISTER, K.: Taschenbuch der Chemie. Carl Hanser Verlag, München, 2010, ISBN: 978-3-446-42211-7
- [61] MÜLLER, U.: Anorganische Strukturchemie. 6. aktualisierte Auflage, GWV Fachverlage GmbH, 2008, ISBN 978-3-8348-0626-0
- [62] http://www.crct.polymtl.ca/fact/documentation/FTsalt/FTsalt_Figs.htm.: FactSage Datenbank für Salze, Zugriff 18.08.2015
- [63] PEREZ, N.: Fracture mechanics. Kluwer Academic Publishers Boston, 2004, ISBN 1-4020-7861-7
- [64] RÖßLER, J.; HARDERS, H.; BÄKER, M.: Mechanisches Verhalten der Werkstoffe. 3. Auflage, Vieweg Verlag, 2008, ISBN 978-3-8351-0240-8
- [65] FABER, K.T.; EVANS, A.G.: Crack deflection processes – 1. Theory. Acta metal. Vol 31, No.4, pp. 565-576, 1983
- [66] FABER, K.T.; EVANS, A.G.: Crack deflection processes – 2. Experiment. Acta metal. Vol 31, No.4, pp. 577-584, 1983 LIII
- [67] HIRZ, M.; DIETRICH, W.; GFRERRER, A.; LANG, J: Integrated Computer-Aided Design in Automotive Development - Development Processes, Geometric Fundamentals, Methods of CAD, Knowledge-Based Engineering Data Management. Springer-Verlag berlin Heidelberg 2013, ISBN: 978-3-642-11939- 2
- [68] KASCHNITZ, E.: Der Einsatz der Formfüllungs- und Erstarrungssimulation in österreichischen Gießereien. Giesserei-Rundschau 49, Heft 7/8, 2002, S. 106-107
- [69] KASCHNITZ, E.; MAYER, H.P.: Der Einfluss der Formfüllungs- und Erstarrungssimulation auf die Bauteilgestaltung von Gussteilen. GiessereiRundschau 51, Heft 1/2, 2004, S. 7-10
- [70] RAVI, B.: Casting Simulation – Best Practices. Transactions of 58th IFC, Ahmedabad, 2010, S.19-29
- [71] BÜHRIG-POLACZEK, A.; MICHAELI, W.; SPUR, G.: Handbuch Urformen – Edition, Handbuch der Fertigungstechnik. Carls Hanser Verlag, München, 2014, ISBN: 978-3-446-42035-9
- [72] FENT, A.: Einfluss der Wärmebehandlung auf den Eigenspannungszustand von Aluminiumgussteilenrts. Dissertation, utg – Forschungsberichte Band 15, 2002, ISBN 3-89791-253-8
- [73] FISH, J.; BELYTSCHKO, T.: A First Course in Finite Elements. John Wiley & Sons Ltd, 2007, ISBN: 978-0-470-03580-1
- [74] BELYTSCHKO, T.; LIU, W.K.; MORAN, B.; ELKHODARY, K.I.: Nonlinear Finite Elements for Continua and Structures. John Wiley & Sons Ltd, 2014
- [75] KLEIN, B.: Grundlagen und Anwendungen der Finite-Element-Methode im Maschinen-und Fahrzeugbau. 9. Auflage Wieweg+Teubner Verlag, 2012, ISBN 978-3-8348-1603-0
- [76] STEINKE, P.: Finite-Elemente-Methode – Rechnergeestützte Einführung. 3.Auflage Springer-Verlag Berlin Heidelberg, 2010, ISBN 978-3-624-11204-1
- [77] BUCALEM, L. M.; BATHE, K.J.: The Mechanics of Solids and Structures – Hierarchical Modeling and the Finite element Solution. Springer-Verlag Berlin Heidelberg, 2011, ISBN 978-3-540-26331-9
- [78] STEFANESCU, D.M.: Science and Engineering of Casting Solidification. Second Edition, Springer Science + Business Media, 2009, ISBN 978-0-387-74609-8
- [79] HATTEL, J.H.: Fundamentals of Numerical Modelling of Casting Processes. Polyteknisk Forlag, 2005, ISBN ISBN 8750209698 LIV
- [80] BUNGARTZ, H.J; SCHÄFER, M.: Fluid-Structure Interaction – Modelling, Simulation, Optimization. Lecture Notes in Computational Science and Engineering 53, Springer-Verlag Berlin Heidelberg, 2006, ISBN-10 3-540- 34595-7
- [81] AHUETT-GARZA, H.; MILLER, R.A.: The effects of heat released during fill on the deflections of die casting dies. Journal of Materials Processing Technology 142, 2003, S. 648-658
- [82] VERRAN, C.O; MENDES, R.P.K.; ROSSI, M.A.: Influence of injection parameters on defects formation in die casting Al12Si1,3Cu alloy: Experimental results and numeric simulation. Journal of Materials Processing Technology 179, 2006, S. 190-195
- [83] SUN, Z.; HU, H.; CHEN, X.: Numerical optimization of gating system paramters for a magnesium alloy casting with multiple performance characteristics. Journal of Materials Processing Technology 199, 2008, S. 256-264
- [84] DOMKIN, K.; HATTEL, J.H.; THORBORG, J.: Modelling of high temperature- and diffusion-controlled die soldering in aluminum high pressure die casting. Journal of Materials Processing Technology 209, 2009, S. 4051-4061
- [85] HELENIUS, R.; LOHNE, O.; ARNBERG, L.; LAUKLI, H.I.: The heat transfer during filling of a high-pressure die-casting shot sleeve. Materials Science and Engineering A 413-414, 2005, S. 52-55
- [86] LAGLER, M.: Use of Simulation to Predict the Viability of Salt Cores in the HPDC Process – Shot Curve as a Decisive Criterion. Die Casting Engineer, July 2013, S. 16-17
- [87] LAGLER, M.: Simulation – Possibilities for Lost Core Technology. Bühler Lost Core Symposium, 2012, S. 28-42
- [88] DI SABATINO, M.: Fluidity of Aluminium Foundry Alloys. Dissertation, Norwegian University of Science and Technology (NTNU), 2005, IMT-Report 2005:76
- [89] BÜHRIG-POLACZEK, A.; HENNINGS, A.; AGUILAR, J.: Untersuchung der Fließeigenschaften von Magnesium-Legierungen im flüssigen und teilflüssigen Zustand. Gießerei-Rundschau 51 (2004) Heft 3/4, S. 54-58
- [90] GUGISCH, M.; BÄHR, R.; BEHM, I.; POLIANSKA, O.: Kausalzusammenhang „Gießtechnologische Legierungseigenschaften – Erstarrungsgefüge“ bei Aluminiumlegierungen. Gießerei-Rundschau 56 (2009) Heft 3/4, S. 50-54
- [91] DANZER, R.; LUBE, T.: Werkstoffprüfung keramischer Werkstoffe – ein Überblick. Tagungsband Werkstoffprüfung, S. 245-254. Deutsche Gesellschaft für Materialkunde, 2004 LV
- [92] DIN EN 843-1: Hochleistungskeramik – Mechanische Eigenschaften monolithischer Keramik bei Raumtemperatur – Teil1: Bestimmung der Biegefestigkeit. Deutsche Fassung EN 843-1:2006
- [93] LEMMENS, J.W.: Dynamic Materials Testing – Referenzhandbuch. GrindoSonic MK5 “Industrial“.
- [94] SIEBERT, J.; BEBBER D.; HOCHKIRCHEN, T.: Statistische Versuchsplanung Design of Experiments (DoE). Springer-Verlag Berlin Heidelberg, 2010, ISBN 978-3- 642-0549-1
- [95] ALLEN, T.T.: Introduction to Engineering Statistics and Six Sigma Statistical Quality Control and Design of Experiments and Systems. Springer-Verlag London Limited, 2006, ISBN 1-85233-955-1
- [96] HIRT, C.W.; NICHOLS, B.D: Volume of fluid (VOF) Method for the Dynamics of Free Boundries. Journal of computational Physics 39, S. 201-225, 1981
- [97] NETZSCH HANDBUCH: Analysieren & Prüfen: Laser Flash Analysis – LFA – Method, Application
- [98] NETZSCH HANBUCH: Analysieren & Prüfen: Dilatometrie – Methode, Geräte, Applikation – von 180 °C bis 2800 °C
- [99] NETZSCH HANDBUCH: Analysieren & Prüfen: Dynamische DifferenzKalometrie - Methode, Technik Applikation
- [100] JANZ, G.J.; TOMKINS, R.P.T.: Additional Single and Multi-Component Salt Systems Electrical Conductance, Density, Viscosity and Surface Tension Data. Molten Salts: Volume 5, Part 2. J. Phys. Chem. Ref. Data, Vol. 12, No.3, 1983
- [101] BRETHOUR, J.M.; ISFAHANI, A.H.G: The Fluid-Structure Interaction and Thermal Stress Evolution Models in Flow-3D. Flow Science, Inc., Santa Fe, NM USA 87505, FSI-11-TN90, July 2011
- [102] DIN EN 10305-3.: Präzisionsstahlrohre – Technische Lieferbedingungen-Teil 3: Geschweißte maßgewalzte Rohre. Deutsche Fassung EN 10305-3:2010
- [103] CARTER, M.C.; PALIT, S.; LITTLER, M.: Characterizing Flow Losses Occuring in Air Vents and Ejector Pins in High Pressure Die Castings. NADCA Transactions, 2010
- [104] WEI, G.: A Fixed-Mesh Method for General Moving Objects. Flow Science, Inc, 2005
- [105] THOMAS, S.: Konstitutive Gleichungen und numerische Verfahren zur Beschreibung von Verformung und Schädigung. Dissertation, TU Darmstadt, 2001 LVI
- [106] MÜLDERS, B.: Modellierung der Verfestigung technischer Aluminiumlegierungen. Dissertation, RWTH Aachen, 2001
- [107] LAROUR, P.: Strain rate sensitivity of automotive sheet steels: influence of plastic strain, strain rate, temperature, microstructure, bake hardening and pre-strain. Dissertation, RWTH Aachen, 2010
- [108] DEMIRKOL, M.; KISAKÜREK, S. E.: On the Relations between Ball Indentation Hardness Measurements and the Tensile Flow Behaviour of Some Ferrous and Non-ferrous Metals. Materials Science and Engineering 59, 1983, S. 197-205
- [109] TABOR, D.: A Simple theory of static and dynamic hardness. The Royal Society Publishing. 1948, DOI: 10.1098/rspa.1948.0008
- [110] BARRIE, S.S.: A Simple Procedure for Calculating Rockwell Hardness Conversion Relationships for Metallic Alloys. Materials Science and Engineering 95, 1987, S. 209-216
- [111] COLLEY, L.J.: Microstructure-Property Models for Heat Treatment of A356 Aluminum Alloy. Dissertation, University of British Columbia Vancouver, 2011
- [112] TIRYAKIOGLU, M.; ROBINSON, J. S.; SALAZAR-GUAPURICHE, M.A.; ET AL.: Hardness-strenght Relationships in the aluminium alloy 7010. Material Science and Engineering A, Author’s Accepted Manuscript, 2015, DOI: http://dx.doi.org/10.1016/j.msea.2015.02.049
- [113] Abaqus 6.13 Manuel
- [114] BASARAN, M.: Stress-State Dependent Modeling with a Focus on the Lode Angle Influence. Dissertation, RWTH Aachen, 2011
- [115] SUN, D.Z..: Werkstoffcharakterisierung und numerische Simulation zur Bewertung des Crashverhaltens dickwandiger Al-Profile im Schienenfahrzeugbau. Schlussbericht AiF-Förderkennzeichen: 16640 N, 2013
- [116] EFFELSBERG, J.; HAUFE, A.; FEUCHT, M.; NEUKAMM, F.; DU BOIS, P.: On parameter identification for the GISSMO damage model. 12th International LSDYNA® User Conference, Metal Forming(3): 16640 N, 2011
- [117] THOMA, C.: Simulationsgestützte Optimierung der Maßhaltigkeit in der Prozesskette Druckguss. Dissertation, Audi-Dissertationsreihe, Band 107, Cuvillier Verlag, Göttingen 2015, ISBN: 9783736990098
- [118] MICHELFEIT, S.: Werkstoffgesetze einer AlSi-Gusslegierung unter Hochtemperaturbeanspruchung in Abhängigkeit des Werkstoffzustandes. Dissertation, TU Darmstadt, 2012
- [119] SCHEMMEL, J.: Beschreibung des Verformungs-, Festigkeits- und Versagensverhaltens von Komponenten im Kriechbereich unter instationärer Beanspruchung mit einem elastisch-viskoplastischen Werkstoffmodell. Dissertation, MPA Universität Stuttgart, 2003
- [120] KLIEMT, C.: Thermo-Mechanical Fatigue of Cast Aluminium Alloys For Engine Applications under Severe Conditions. Dissertation, Heriot-Watt University School of Engineering and Physical Sciences, 2012
- [121] KOJIC M., J.; BATHE K.J.: Inelastic Analysis of Solids and Structures. SpringerVerlag Berlin Heidelberg, 2005, ISBN: 3-540-22793-8
- [122] HASSE, S.: Guß- und Gefügefehler. Erkennung, Deutung und Vermeidung von Guß- und Gefügefehlern bei der Erzeugung von gegossenen Komponenten. Berlin, Schiele & Schön, 2., aktualisierte und erw. Auflage, 2003
- [123] POPOV V.L.: Kontaktmechanik und Reibung – Von der Nanotribologie bis zur Erdbebendynamik. 2. Überarbeitete Auflage, Springer-Verlag Berlin Heidelberg, 2010, ISBN 978-3-642-13301-5
- [124] SELI, H.; ISMAEL, A.I.MD; RACHMANN, E.; ET AL.: Mechanical evaluation and thermal modelling of friction welding of mild steel and aluminium. Journal of Material Processing Technology, 210 (2010). S. 1209-1216
- [125] BORRISUTTHEKUL, R.; YACHI, T.; MIYASHITA, Y., ET AL.: Suppression of intermetallic reaction layer formation by controlling heat flow in dissimilar joining of steel and aluminum alloy. Materials Science and Engineering A 467 (2007), S. 108-113
- [126] TREITLER, R.: Vom Gießprozess zur Festigkeitsberechnung am Beispiel einer Aluminium-Magnesium-Druckgusslegierung. Dissertation, Universitätsverlag Karlsruhe (TH), 2005, ISBN 3-937300-94-5
- [127] REHM, W.: Virtuelle Entwicklung von Gussbauteilen unter Einbeziehung des Herstellprozesses am Beispiel von Gusseisen mit VermicularGrafit. Dissertation, IMWF Stuttgart, 2005
- [128] TODTE, M.: Prognose der mechanischen Eigenschaften von Aluminium-Gußteilen durch numerische Simulation des Erstarrungsprozesses. Dissertation, Universität Magdeburg, 2003
- [129] THOMA, C.; VOLK, W.: Simulation der Prozesskette Druckguss – Schlüssel für verzugsminimierte Strukturbauteile. VDI Berichte Nr. 2217 (2014), S. 129-141
- [130] THOMA, C.; VOLK, W.; BRANNER, G.; EIBISCH, H.: Simulationsgestützte Optimierung der Maßhaltigkeit von dünnwandigen Strukturbauteilen in der Prozesskette Aluminium-Druckguss. Druckguss 7-8/2013, S. 332-335 I
- [131] EGNER-WALTER, A.: Simulation des Entstehens von Eigenspannungen in Gußteilen. Dissertation, Shaker Verlag, 1998, ISBN 3-8265-3623-1
- [132] DEMIREL, C.: Experimentelle Untersuchung und Simulation des Abschreckprozesses von bauteilähnlichen Geometrien aus G-AlSi7Mg. Dissertation, Technische Universität Berlin, Fakultät 3, D 83, 2009
- [133] CARHS: Dacheindrücktest – Roof Crush. Saftey Wissen – Passive Sicherheit, S.41
- [134] OFFICE OF VEHICLE SAFETY COMPLIANCE (OVSC): Laboratory Test Procedure for FMVSS 216, U.S. DEPARTMENT OF TRANSPORTATION NATIONAL HIGHWAY TRAFFIC SAFETY ADMINISTRATION, TP-216-05, 2006
- [135] GATILAO, F., ROESSER, G., REAUME, B.: An Overview of FMVSS 216a – Roof Crush Resitance Testing. SAE International, 2010
9. Copyright:
- This material is a paper by "Fakultät Energie-, Verfahrens- und Biotechnik der Universität Stuttgartl": Based on "Hohl- und Verbundguss von Druckgussbauteilen – Numerische Auslegungsmethoden und experimentelle Verifikation".
- Source of paper: https://core.ac.uk/download/pdf/147556253.pdf
This material was created to introduce the above paper, and unauthorized use for commercial purposes is prohibited. Copyright © 2025 CASTMAN. All rights reserved.