This article introduces the paper "AUTOMOTIVE APPLICATIONS OF MAGNESIUM AND ITS ALLOYS".
1. Overview:
- Title: AUTOMOTIVE APPLICATIONS OF MAGNESIUM AND ITS ALLOYS
- Authors: C. Blawert, N. Hort, K.U. Kainer
- Publication Year: August 2004
- Journal/Conference: Trans. Indian Inst. Met., Vol.57, No. 4, pp. 397-408
- Keywords: Magnesium alloys, Automotive applications, Lightweight construction, Die casting, Corrosion resistance, High temperature strength, Joining technology, Surface treatment
2. Research Background:
- There is increasing interest in lightweight construction as the automotive industry is committed to achieving "a 25% reduction in average fuel consumption for all new cars by the year 2005 (compared to levels in 1990)."
- Magnesium alloys are attractive structural materials due to "the combination of high strength properties and low density" in applications where weight savings are crucial.
- In automotive applications, weight reduction improves vehicle performance by "reducing the rolling resistance and energy of acceleration, thus reducing the fuel consumption and moreover a reduction of the greenhouse gas CO₂ can be achieved."
- Magnesium has "a long history in automotive applications," but its use decreased in the seventies due to "prize volatility and also to lack of knowledge."
- "Stricter legislative rules (CAFE) and voluntary commitments to reduce the average fuel consumption have nowadays revived the interest in magnesium."
- Magnesium "shows high potential to substitute conventional materials" where "low mass and high specific properties are required." Magnesium alloys exhibit "similar or even better values than aluminium and many commercial steels (Fig. 1)" in terms of specific Young's modulus and high specific strength.
- "With the increasing use of magnesium the cost per tonne is coming down, which makes it more competitive from the economic point of view too."
- "The consumption of primary magnesium shows a broad increase in the last 20 years whereas North America is the main consumer followed by the western part of Europe and Japan 1."
- "Most of the available magnesium (40%) is still used for alloying aluminium and only about 34% is directly used for magnesium parts, which can be divided into casting applications (33.5%) and wrought materials (0.5%)2."
- "It was estimated that the market for magnesium die castings will grow from 105 tons in 2000 to twice this amount in 2006." Approximately "80 % of this market is expected to go towards die casting automotive parts1."
- The widespread use of magnesium is limited by "some poor property profiles" such as "low creep resistance, high coefficient of thermal expansion (CTE), low Young's modulus, insufficient ductility and crash energy consumption in car body structures, low fatigue stability, low corrosion and wear resistance."
3. Research Objectives and Research Questions:
- Research Objective: To give "an overview on the actual status of the development of magnesium alloys and technologies for application in the automotive industries." The paper discusses "the development of new cast or wrought alloys and the optimisation of existing or new processes for the production of magnesium parts."
- Core Research Question: What is the current status of magnesium alloy and technology development for automotive applications, and what are the future potentials and challenges?
- Research Hypothesis: This paper is an overview and does not explicitly state a research hypothesis to be tested.
4. Research Methodology:
- Research Design: This paper is an overview study that analyzes the trends and development status of magnesium alloys in automotive applications.
- Data Collection Methods: The research is based on a review of existing literature, industry reports, technical data, and expert opinions.
- Analysis Methods: The collected data is analyzed to provide an overview of alloy development, manufacturing processes (casting, forming, joining, surface treatment), automotive component applications, and market trends for magnesium alloys. The analysis identifies technical challenges and future prospects.
- Research Scope and Range: This study comprehensively covers material technology, manufacturing process technology, component application technology, and related industry trends of magnesium alloys for lightweighting in the automotive industry.
5. Main Research Findings:
- Core Findings:
- The introduction of high purity alloys was "the major step for improving the corrosion resistance of magnesium alloys."
- New high temperature resistant alloys are "under further development and testing." Some alloys are already available like "MRI, modified AE and AJ alloy systems" 12,13.
- Mg-Al-Si, Mg-Al-RE, Mg-Al-Ca, Mg-Al-Sr and quaternary combinations are "very promising new systems for high pressure die casting" 14.
- An oil pan made from the new magnesium MRI153M alloy performed "similar and had the better damping properties 15" compared to aluminium A380 alloy.
- Using alloy AZ91, "thin walled castings with wall thicknesses less than 1 mm can be obtained easily."
- "The deep drawing potential of AZ31 sheet was successfully demonstrated 11." At 225°C, "the limiting draw ratio of AZ31 is 2.6," higher than deep drawing Al and steel 16.
- Extrusion can be "successfully combined with a subsequent bending step to produce bended extrusion profiles 19."
- Friction stir welding (FSW) is "a more recent development suitable for joining materials that are more difficult to weld or even for joining dissimilar materials like magnesium or aluminium alloys 24."
- Chemical conversion coatings are "state-of-the-art for corrosion protection of magnesium" as primers. Chromating showed "the best results" but chrome-free alternatives are required 22. Keronite is a new high voltage electrolytic plasma anodizing treatment addressing wear and corrosion resistance 31.
- "Magnesium and its alloys are the most machinable of all structural materials 25."
- Statistical/Qualitative Analysis Results:
- "It was estimated that the market for magnesium die castings will grow from 105 tons in 2000 to twice this amount in 2006."
- "Approximately 80 % of this market is expected to go towards die casting automotive parts1."
- The average weight of magnesium in European cars is "about 2.5 kg" and is predicted to double within ten years 3.
- In Europe, nearly "85% of which are made of magnesium alloys 3" for steering wheels.
- At 225°C, "the limiting draw ratio of AZ31 is 2.6 16."
- Keronite has reached "a deposition rate of 5 µm/min 31."
- Data Interpretation:
- Magnesium alloys are promising materials for lightweighting in the automotive industry, especially with advancements in die casting technology enabling complex shapes.
- Improvements in corrosion resistance, high-temperature strength, joining, and surface treatment technologies are expanding the application areas of magnesium alloys.
- The magnesium market has high growth potential, particularly driven by increasing demand in the automotive sector.
- Figure Name List:
- Fig. 1: Comparison of specific Young's modulus and strength of different materials
- Fig. 2: Creep/strength performance versus temperature requirements for some automotive drivetrain applications 12
- Fig. 3: Directions of alloy development to improve the performance of magnesium components
- Fig. 4: Robotic friction stir welding of an AM60 component
- Fig. 5: Magnesium instrument panel for the Rolls-Royce Phantom: casting in the die 43
- Fig. 6: Inner door frame of the Daimler-Chrysler SL Roadster [Courtsey Jo Wilkens, HydroMagnesium Marketing GmbH, Brussels, Belgium]
- Fig. 7: World's first composite magnesium/aluminium crankcase for a water-cooled engine developed by BMW automated removal of the crankcase from the die casting maschine 43
- Fig. 8: Currently used magnesium and prediction of potential use of magnesium in VW/Audi vehicles 11
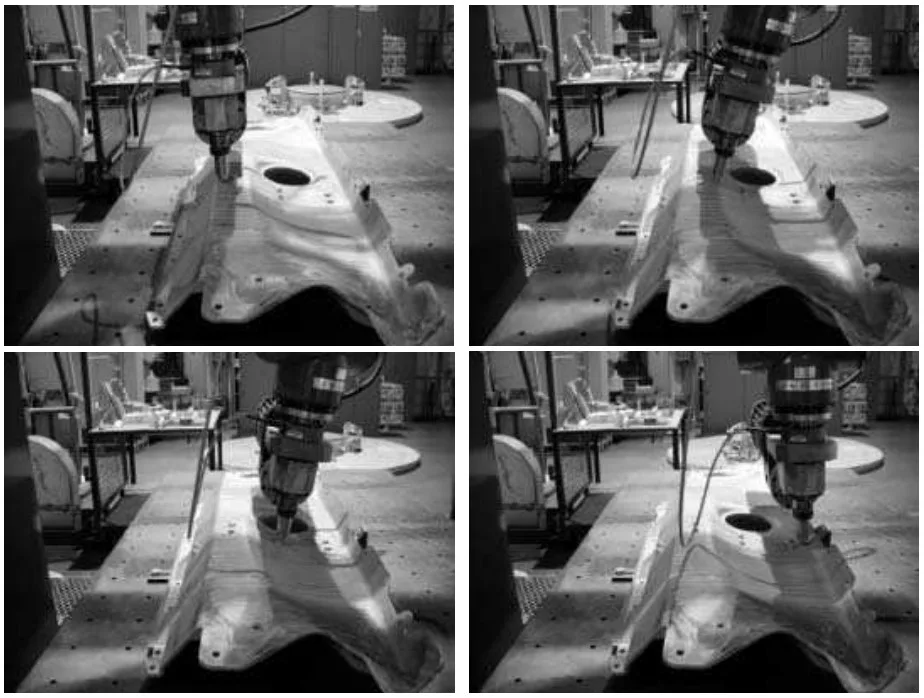
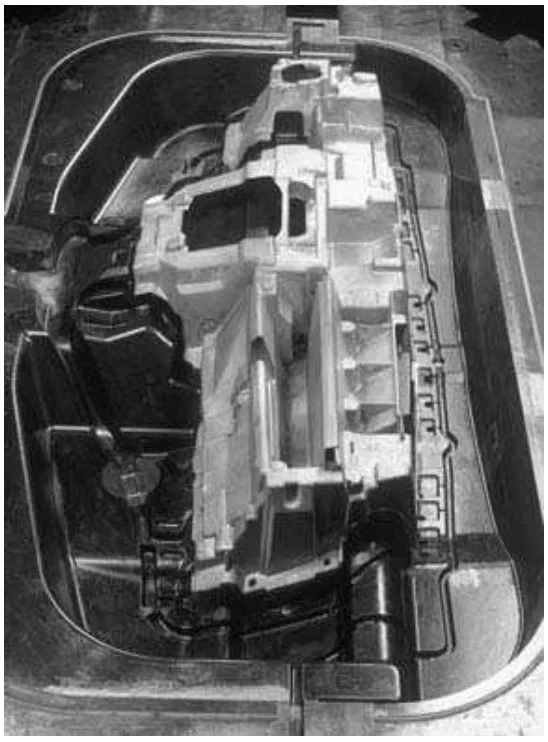
6. Conclusion and Discussion:
- Summary of Main Results: Magnesium alloys have significant potential in automotive applications due to the increasing demand for lightweighting and fuel efficiency. Advancements in alloy development, casting, joining, and surface treatment technologies are facilitating broader applications of magnesium.
- Academic Significance of Research: This overview provides a comprehensive understanding of the current technological status and future potential of magnesium alloys in the automotive industry, expanding the knowledge base in related research fields.
- Practical Implications: The research offers valuable technical information and development directions for automotive manufacturers and component suppliers, contributing to the development and production strategies for lightweight automotive components.
- Limitations of Research: As an overview study based on existing literature and technical data rather than specific experimental data analysis, the depth of analysis and validation for specific applications may be limited.
7. Future Research Directions:
- Future research should focus on:
- Development of new magnesium alloys that maintain superior mechanical properties at high temperatures.
- Development of surface treatment technologies providing further improved corrosion and wear resistance.
- Development of cost-reduction and recycling technologies for magnesium components.
- Optimization and reliability evaluation of various joining technologies.
- Development of forming technologies to improve the formability of magnesium wrought materials.
- Expanding the application of magnesium alloys to automotive body structural components and powertrain components.
8. References:
- Int. Magnesium Association: (annual Report 2001)
- Kammer C, in: C. Kammer (ed.): Magnesium Taschenbuch (Aluminium-Verlag, Germany 2001), p. 1
- Light Metals News, No. 47.03, 23.11.03, PP.2-4
- Polmear I J, in: M.M. Avedesian and H. Baker (ed.): Magnesium and Magnesium Alloys (ASM International, USA 1999), p. 3
- http://www.automotive-online.com, Automotive Online News and Information, Magnesium in automotive manufacturing – 05/07/2002 and Homepage www.magnesium.com
- Company report, 1909-1939 - 30 Jahre Elektron und neuere Leichtmetallegierungen der I.G. Farbenindustrie Aktiengesellschaft, I.G. Farbenindustrie Aktiengesellschaft Abt. Elektronmetall Bitterfeld, 1939
- Eigenfeld K., Gießerei-Rundschau, 43 (1996) 15
- Beck A, Magnesium und seine Legierungen, Springer Verlag, Berlin 1939
- Bolstad J A, dt. Verband für Materialforschung und – prüfung, Korrosion an Fahrzeugen, DVM-Tag, (1995), PP.319-324
- Schnell R, Hönes R and Käumle F, dt. Verband für Materialforschung und –prüfung, Korrosion an Fahrzeugen, DVM-Tag, (1995) PP.175-190
- Friedrich H and Schumann S, Mat.wiss. u. Werkstofftechn., 32 (2001) 6
- Bakke P and Westengen H, Proceedings of the 6th International Conference Magnesium Alloys and Their Applications, Ed. K.U. Kainer, Wiley-VCH, (2003) PP31-36
- Bronfin B, Aghion E, von Buch F, Schumann S and Friedrich H, Proceedings of the 6th International Conference Magnesium Alloys and Their Applications, Ed. K.U. Kainer, Wiley-VCH, (2003) PP 55-61.
- Pekguleryuz M O and Kaya A A, Proceedings of the 6th International Conference Magnesium Alloys and Their Applications, Ed. K.U. Kainer, Wiley-VCH, (2003), PP.74-93
- Vert P, Niu X P, Aghion E and Stickler A, Proceedings of the 6th International Conference Magnesium Alloys and Their Applications, Ed. K.U. Kainer, Wiley-VCH, (2003), PP.943-948
- Moll F, Mekkaoui M, Schumann S and Friedrich H, Proceedings of the 6th International Conference Magnesium Alloys and Their Applications, Ed. K.U. Kainer, Wiley-VCH, (2003), PP.936-942
- Gradinger R, Brandecker, Kilian H and Wahlen A, Proceedings of the 6th International Conference Magnesium Alloys and Their Applications, Ed. K.U. Kainer, Wiley-VCH, (2003), PP.313-317
- Stalmann A, Sebastian W, Friedrich H, Schuhmann S and Dröder K, Advanced Engineering Materials, 3 (2001) 969
- Homepage Universität Dortmund, Lehrstuhl für Umformtechnik, http://www.lfu.mb.uni-dortmund.de
- Weissert W, Mat.-wiss. U. Werkstofftechn, 32 (2001) 81
- Budde L, Fügeverfahren zur Realisierung von innovativen Leichtbaukonzepten, (1999), PP225-238
- Kötting G, Mechanisches Fügen und Kleben. 7. Paderborner Symposium Fügetechnik, (2000) PP 147- 164
- Doege E, Dröder K and Elend L-E, Fortschritte mit Magnesium im Automobilbau, (2000) PP.123-141
- Draugelates U, Schram A and Kettler Ch: Prozessführung und Gestaltungskonzepte für das Fügen komplexer Bauteile (manufacturing report SFB 390, Germany 1998)
- Busk R S, Magnesium Products Design, Marcel Dekker, NY, 1987
- Murray R W and Hillis J E, Magnesium Finishing - Chemical Treatment and Coating Practices, SAE Technical Paper No. 900791, Detroit, 1990
- Schreckenberger H, Korrosion und Korrosionsschutz von Magnesiumwerkstoffen für den Automobilbau – Korrosion und Korrosionsschutz von Magnesiumwerkstoffen für den Automobilbau – Problematik der Kontaktkorrosion, Fortschr.-Ber. VDI Reihe 5, Nr. 613, VDI Verlag, Düsseldorf, 2001
- Schreckenberger H and Laudien G, Fortschritte mit Magnesium im Automobilbau, Bad Nauheim, (2000), PP.41-50
- Walter M, Proceedings of the 6th International Conference Magnesium Alloys and Their Applications, Ed. K.U. Kainer, Wiley-VCH, (2003), PP.529-533
- Hillis J E, Proc. of 40th Annual Conf. of Metallurgists of CIM, (2001), PP.3-26
- Wilkes S, Materials World, December 2003, PP.18-19
- Gregg P, Proceedings of the 6th International Conference Magnesium Alloys and Their Applications, Ed. K.U. Kainer, Wiley-VCH, (2003), PP.524-528
- Hydro Magnesium Firmenschrift: Korrosionsschutz und Oberflächenbehandlung von Magnesiumlegierungen
- Reinhold B and Brettmann M, Metalloberfläche, 54 (2000) 26
- Reinhold B, Klose S G and Strobl C, Materials and Corrosion, 50 (1999) 517
- Boese E, Göllner J, Heyn A, Strunz J, Chr. Baierl and H. Schreckenberger, Materials and Corrosion, 52 (2001)247
- Skar J I and Albright D, Magnesium Technology 2002, TMS, (2002) PP. 255-261
- Lehmkuhl H, Mehler K, Reinhold B, Bongard H and Tesche B, Advanced Engineering Materials, 3 (2001) 412
- Skar J I, Materials and Corrosion, 50 (1999)2
- Schultz R A and Haupricht W J, Light Metals Age, 2 (1999)108
- Luo A A, JOM, 2 (2002)42
- Vasilash G S, Almost famous: magnesium, automotive design & production, http://www.autofieldguide.com
- BMW Group Press, 7/2003, PP.10-15
- Vollrath K, Konstruktion, 11/12 (2003), IW3-IW4
9. Copyright:
This material is based on the paper: AUTOMOTIVE APPLICATIONS OF MAGNESIUM AND ITS ALLOYS by C. Blawert, N. Hort, K.U. Kainer.
Paper Source: Trans. Indian Inst. Met., Vol.57, No. 4, August 2004, pp. 397-408
This material is a summary based on the above paper, and unauthorized use for commercial purposes is prohibited.
Copyright © 2025 CASTMAN. All rights reserved.