This article introduces the paper "Analytical cost estimation model in High Pressure Die Casting" published in Procedia Manufacturing in 2017.
1. Overview:
- Title: Analytical cost estimation model in High Pressure Die Casting
- Authors: Claudio Favi, Michele Germani, Marco Mandolini
- Publication Year: 2017
- Publishing Journal/Academic Society: Procedia Manufacturing, Elsevier B.V.
- Keywords: cost estimation, High Pressure Die Casting, analytical cost model, knowledge formalization.
2. Research Background:
- Social/Academic Context of the Research Topic:
- The paper highlights the importance of product/process-related data and information throughout the product lifecycle within the context of Intelligent Manufacturing.
- It emphasizes that during the design phase, designers significantly influence product cost, establishing up to 80% of it, including manufacturing costs.
- Process-related information sharing within an enterprise is presented as a solution to enhance manufacturing flexibility.
- The availability of big data from production plants is seen as a potential support for designers in making informed decisions regarding feasibility and cost-effectiveness.
- Limitations of Existing Research:
- Existing cost estimation methods, particularly for casting processes, are often based on parametric (rule-based) models, primarily using casting weight and shape complexity.
- While some parametric methods incorporate geometric feature recognition, literature models are deemed sufficiently accurate only for comparative cost analysis at the design phase.
- Current models lack the detail required for analytically optimizing product geometry and features based on specific process characteristics of each casting process (e.g., gravity, HPDC).
- Commercial software tools, even those following an analytical approach, operate as "black boxes," failing to provide a detailed cost breakdown based on elementary operations and hindering the identification of process criticalities by product and production engineers.
- Necessity of the Research:
- The research identifies the need for a systematic approach to cost estimation specifically for the High Pressure Die Casting (HPDC) process.
- Such an approach is expected to yield more accurate results and provide better insights into cost breakdowns compared to general methods currently in practice.
- The paper emphasizes the necessity of coupling a robust cost estimation model with Design-to-Cost (DtC) rules.
- This coupling is crucial for establishing a holistic framework for cost analysis and optimization, providing a tangible tool for daily design activities in the HPDC sector.
3. Research Purpose and Research Questions:
- Research Purpose:
- The primary purpose of this research is to define an analytical model specifically for cost estimation in the High Pressure Die Casting (HPDC) process.
- The model aims to provide a structured and detailed approach to cost estimation, moving beyond the limitations of existing methods.
- Key Research Questions:
- How can an analytical model for HPDC cost estimation be developed based on knowledge formalization and cost estimation algorithms?
- How can the analytical model (algorithms) be effectively linked to the geometrical features of the product being developed?
- What is the relationship between the geometrical features of a HPDC component and the various cost items involved in its manufacturing?
- Can establishing this relationship lead to a more accurate cost breakdown in HPDC, thereby supporting designers in applying Design-to-Cost rules?
- Research Hypotheses:
- The central hypothesis is that by establishing a clear relationship between the geometrical features of a product and the associated cost items in the HPDC process, a more accurate and detailed cost breakdown can be achieved.
- This accurate cost breakdown will empower product designers to effectively apply Design-to-Cost (DtC) rules within the HPDC sector, leading to more cost-effective product designs.
- The novelty of this approach lies in defining an analytical cost estimation model for HPDC that directly starts from the geometrical features of the product under development.
4. Research Methodology:
- Research Design:
- The research employs a design science approach, focusing on the development of an analytical cost model for HPDC.
- The model is structured around two main pillars: (i) knowledge formalization and (ii) cost estimation algorithms.
- The novelty lies in linking the analytical model to the geometrical features of the product.
- Data Collection Method:
- The analytical cost model was developed by integrating knowledge from multiple sources:
- Scientific and industrial literature on cost estimation and manufacturing processes.
- Expert knowledge gathered from skilled technicians in the industry, including cost engineers, production technologists, plant managers, and designers.
- A spreadsheet was utilized as the implementation tool for the developed cost model.
- The analytical cost model was developed by integrating knowledge from multiple sources:
- Analysis Method:
- The core analysis method is the analytical cost model itself, which is based on:
- Knowledge Formalization: Characterizing and classifying cost items involved in the HPDC process through knowledge collection and formalization from both internal company sources and explicit literature.
- Cost Estimation Algorithms: Defining algorithms and equations to predict HPDC manufacturing costs. These algorithms establish relationships between HPDC cost items and product attributes (e.g., roughness, maximum thickness).
- The model calculates the total cost (Ctot) as the sum of raw material cost (Cmat), processing cost (Cpro), accessory operations cost (Caccessory), and setup operations cost (Csetup).
- The core analysis method is the analytical cost model itself, which is based on:
- Research Subjects and Scope:
- The research focuses specifically on the High Pressure Die Casting (HPDC) process.
- The scope includes the cost estimation of HPDC components, considering various factors from raw material to processing and setup.
- To validate the model, case studies were conducted on three different HPDC components: two gas flame-spreaders (Burner and Burner 3 rings) and a Heater element. These components represent a range of dimensions, features, attributes, and properties within HPDC manufacturing.
5. Main Research Results:
- Key Research Results:
- The primary outcome is the development of a structured analytical model for cost estimation in HPDC.
- The model successfully links geometrical features of the product to specific cost items in the HPDC process.
- The model provides a detailed cost breakdown, offering insights into the contribution of different cost components.
- The model's accuracy was tested and validated through case studies on industrial components.
- Statistical/Qualitative Analysis Results:
- The validation through case studies demonstrated a maximum error of 6% in estimating the total cost (Ctot) when comparing the model's results to reference values from industry.
- For the "Burner" case study, a noticeable difference in raw material cost (Cmat) contributed to the 6% error, attributed to potentially over-dimensioned gating systems in the reference model, leading to a higher total casting weight.
- For the "Burner 3 rings" and "Heater element" case studies, the maximum error in total cost estimation was approximately 4%.
- The energy cost item (Cene) within the raw material cost was approximated based on current batch data from companies, potentially introducing minor errors in raw material cost estimation.
- The highest error in cost estimation was observed for accessory and set-up operations (approximately 50% deviation for "Burner 3 rings" and "Heater element"). However, the contribution of these costs to the total cost was low (less than 10%).
- Data Interpretation:
- The results indicate that the developed analytical cost model provides a reasonably accurate estimation of the total cost for HPDC components.
- The model's strength lies in its ability to provide a detailed cost breakdown, enabling designers to understand the cost implications of different design choices related to geometrical features.
- The relatively higher error in accessory and set-up costs, while present, has a limited impact on the overall cost estimation accuracy due to their smaller contribution to the total cost, especially in high production volumes.
- Figure Name List:
- Fig. 1. HPDC process overview. This figure illustrates the sequential steps of the High Pressure Die Casting process, from release agent application to final part operations. The steps are numbered and include:
- Release agent applied to the die surface.
- Shot sleeve filled with molten metal.
- Piston forces molten metal into the die cavity.
- Piston maintains pressure on molten metal when die cavity is filled.
- Die inserts are separated and the casting is removed (after cooling time).
- Individual cast parts are trimmed from the casting.
- Final operations performed to the cast parts.
- Fig. 2. Cost estimation results for the proposed case studies. This table presents the cost estimation results for three case studies (Burner, Burner 3 rings, Heater element), comparing the calculated values from the model with reference values. The table includes:
- Total cost - Ctot [€]
- Raw material Cost - Cmat [€]
- Processing Cost- Cpro [€]
- Accessory operations Cost - Caccessory [€]
- Set-up operations cost - Cset-up [€]
- HPDC process efficiency [%]
- Total casting weight [kg]
- Cast product weight [kg]
- Fig. 1. HPDC process overview. This figure illustrates the sequential steps of the High Pressure Die Casting process, from release agent application to final part operations. The steps are numbered and include:
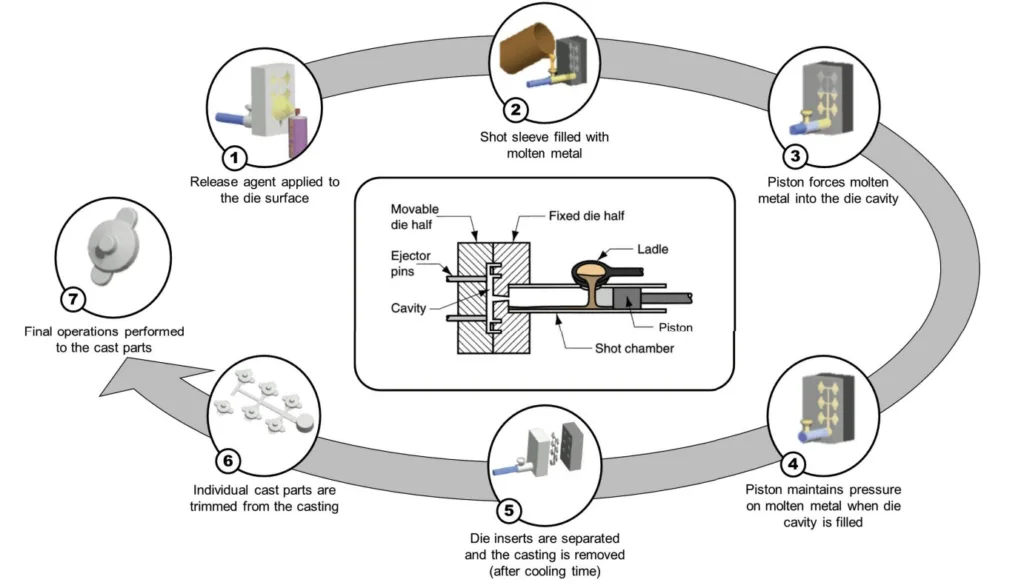
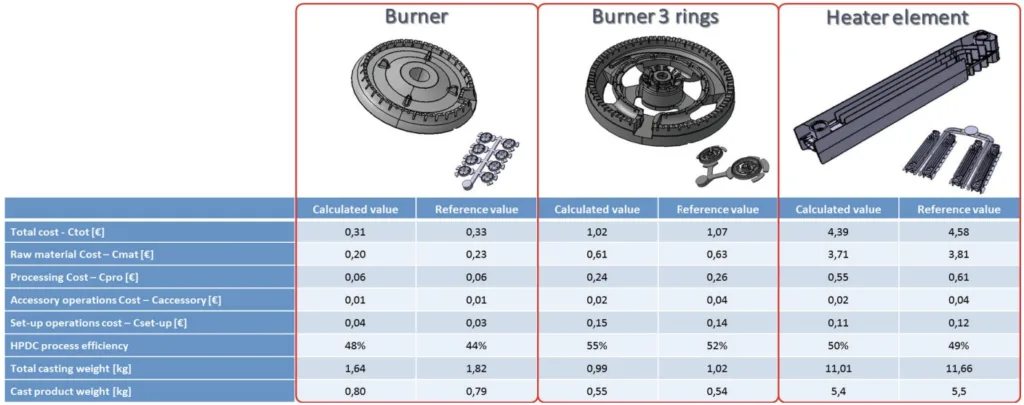
6. Conclusion and Discussion:
- Summary of Main Results:
- The paper successfully defined an analytical model for cost estimation of products manufactured using the HPDC process.
- The model effectively integrates various cost items and establishes a link between product features (geometrical, dimensional) and process parameters (batch size, cooling time).
- The relationship between geometrical features and cost items provides an accurate cost breakdown, as validated by the case studies.
- The maximum error observed in total cost estimation using the model was approximately 6%, primarily influenced by the raw material cost item and gating system weight.
- Lower accuracy was noted for accessory and set-up cost items, although their impact on the total cost is minimal, especially for high production volumes.
- Academic Significance of the Research:
- The research demonstrates the effectiveness of adopting analytical models for cost estimation in consolidated manufacturing technologies like HPDC.
- The developed model provides a valuable tool for manufacturing companies to make informed decisions regarding technology adoption and optimization for specific component geometries and features.
- This approach contributes to the body of knowledge in cost estimation methodologies for manufacturing processes, particularly in the context of die casting.
- Practical Implications:
- The analytical cost estimation model serves as a powerful tool for product designers in the HPDC sector, enabling the application of Design-to-Cost (DtC) principles.
- By providing a detailed cost breakdown linked to geometrical features, the model allows designers to evaluate the cost implications of design choices early in the design phase.
- This facilitates the design of more cost-effective HPDC components, optimizing both product performance and manufacturing cost.
- Limitations of the Research:
- The model exhibits lower accuracy in estimating accessory and set-up cost items compared to raw material and processing costs.
- The energy cost item (Cene) within the raw material cost is based on approximations, which could introduce some level of error.
- Further validation with a broader range of HPDC components and manufacturing scenarios is recommended.
7. Future Follow-up Research:
- Directions for Follow-up Research:
- Future research should focus on improving the model's accuracy, particularly for critical cost items such as accessory and set-up operations.
- Efforts should be made to reduce subjectivity in the cost estimation process, potentially through more refined algorithms and data inputs.
- Validation of the proposed model should be extended by comparing its performance against other cost models available in scientific literature and commercial software tools.
- Investigating the integration of more detailed process parameters and material properties into the model could further enhance its accuracy and applicability.
- Areas Requiring Further Exploration:
- A key area for future exploration is coupling the developed cost estimation model with the development of a comprehensive Design-to-Cost (DtC) methodology specifically tailored for HPDC.
- This would involve creating a framework that seamlessly integrates cost estimation into the design process, providing designers with real-time feedback on the cost implications of their design decisions.
- Further research could also explore the application of the model in optimizing process parameters and tooling design for HPDC, beyond just product geometry optimization.
8. References:
- [1] A.A. Luo, A.K. Sachdev, B.R. Powell, Advanced casting technologies for lightweight automotive applications, China Foundry, 7:4 (2010).
- [2] R. Raffaeli, C. Favi, F. Mandorli, Virtual prototyping in the design process of optimized mould gating system for high pressure die casting, Engineering Computations, 32:1 (2015) 102-128.
- [3] F. Bonollo, N. Gramegna, G. Timelli, High-pressure die-casting: Contradictions and challenges, Journal of the Minerals, Metals & Materials Society, 67 (2015) 901-908.
- [4] M. Mauchand, A. Siadat, A. Bernard, N. Perry, Proposal for Tool-based Method of Product Cost Estimation during Conceptual Design, Journal of Engineering Design, 19:2 (2008) 159-17.
- [5] M. Sadeghi, Optimization product parts in high pressure die casting process. Mälardalen University Press Licentiate Theses No. 197, 2015.
- [6] A.S.M. Hoque, P.K. Halder, M.S. Parvez, T. Szecsi, Integrated manufacturing features and Design-for-manufacture guidelines for reducing product cost under CAD/CAM environment. Computers & Industrial Engineering 66 (2013) 988-1003.
- [7] R.G. Chougule, B. Ravi, Casting process planning using case based reasoning. Transactions of American Foundry Society, 2003.
- [8] I.F. Weustink, E. Ten Brinke, A.H. Streppel, H.J.J. Kals, Generic framework for cost estimation and cost control in product design. J. Materials Processing Tech. 103 (2000) 141-148.
- [9] E.M. Shehab, H.S. Abdalla, Manufacturing cost modelling for concurrent product development. Robotics and Computer Integrated Manufacturing. 17 (2001) 341-353.
- [10] C. Favi, M. Germani, M. Mandolini, Design for Manufacturing and Assembly vs. Design to Cost: Toward a Multi-objective Approach for Decision-making Strategies During Conceptual Design of Complex Products, Procedia CIRP, 50 (2016) 275-280.
- [11] R.G. Chougule, B. Ravi, Casting Cost Estimation in an Integrated Product and Process Design Environment. International Journal of Computer Integrated Manufacturing. 19:7 (2006) 676-688.
- [12] T. Farineau, B. Rabenasolo, J.M. Castelain, Y. Meyer, P. Duverlie, Use of parametric models in an economic evaluation step during the design phase. International Journal of Advanced Manufacturing Technology, 17:2 (2001) 79–86.
- [13] Boothroyd and Dewhurst Inc., Design for Manufacture Concurrent Costing Software - User Manual (Boothroyd and Dewhurst Inc). 2003.
- [14] C. Blum, Early Cost Estimation of Die Cast Components, M.S. Thesis, University of Rhode Island, Kingston, 1989.
- [15] S. Bonetti, M. Perona, N. Saccani, Total Cost of Ownership for Product-Service System: Application of a Prototypal Model to Aluminum Melting Furnaces, Procedia CIRP 47 (2016) 60-65.
- [16] Depreciation guide, Document 2001D, Nationwide Publishing Company Inc., 2004.
- [17] M. Ward, Gating Manual, NADCA, USA, 2006.
- [18] M. Mandolini, M. Germani, P. Cicconi, LeanCost: knowledge-based tool for early product cost estimation', in LIBRERIA CORTINA - Padova (ed.) Proceedings of IMProVe 2011 (2011) 35-36.
- [19] P. Cicconi, M. Germani, M. Mandolini, How to support mechanical product cost estimation in the embodiment design phase', in the Proceedings of the new world situation: new directions in concurrent engineering. Cracow, (2010) 419-431.
9. Copyright:
- This material is Claudio Favi, Michele Germani, Marco Mandolini's paper: Based on Analytical cost estimation model in High Pressure Die Casting.
- Paper Source: doi:10.1016/j.promfg.2017.07.146
This material was summarized based on the above paper, and unauthorized use for commercial purposes is prohibited.
Copyright © 2025 CASTMAN. All rights reserved.