This article introduces the paper "Aluminum High Pressure Vacuum Die Casting Applications for the Multi Material Lightweight Vehicle Program (MMLV) Body Structure".
1. Overview:
- Title: Aluminum High Pressure Vacuum Die Casting Applications for the Multi Material Lightweight Vehicle Program (MMLV) Body Structure
- Authors: Randy Beals¹, Jeff Conklin¹, Tim Skszek¹, Matt Zaluzec², David Wagner²
- Year of Publication: 2015
- Journal/Conference: Light Metals 2015, TMS (The Minerals, Metals & Materials Society)
- Keywords: Aluminum, high pressure vacuum die castings, body structure
2. Research Background:
This research stemmed from the Multi-Material Lightweight Vehicle (MMLV) project, a collaborative effort initiated in 2012 by Magna International, the U.S. Department of Energy, and Ford Motor Company. The societal impetus was the need for improved fuel efficiency and reduced emissions through vehicle weight reduction. The research addressed limitations of existing single-material (steel, high-strength steel, or aluminum) body-in-white (BIW) designs, specifically their high cost, incompatibility with existing manufacturing processes, and limited global production capacity. While previous studies focused on monolithic material solutions, multi-material approaches were largely confined to component-level integration.
3. Research Objectives and Questions:
- Research Objective: To evaluate the weight reduction and performance benefits of aluminum high-pressure vacuum die casting (hpvdc) components within the lightweight BIW architecture of a C/D segment vehicle.
- Key Research Questions: How much weight reduction does a multi-material BIW structure incorporating aluminum hpvdc components achieve compared to a baseline vehicle? How does this design maintain stiffness, durability, and crash performance requirements?
- Research Hypothesis: Strategic use of aluminum hpvdc components would lead to significant weight reduction compared to a steel-intensive BIW, while improving crash performance and assembly cost (part count reduction).
4. Research Methodology:
- Research Design: An empirical study utilizing data from the MMLV project prototype vehicle to analyze the weight reduction and performance characteristics of aluminum hpvdc components within the BIW.
- Data Collection Methods: Data collected included MMLV BIW design specifications, manufacturing processes, and performance test results (stiffness, durability, crashworthiness).
- Analytical Methods: Quantitative analysis of the MMLV BIW's weight, stiffness, durability, and crash performance, compared to a baseline vehicle. MAGMASOFT® software was used for casting simulation and process optimization.
- Study Population and Scope: The study focused on the MMLV prototype vehicle's BIW, comprising eight hpvdc aluminum castings, six aluminum extrusions, twelve major steel stampings, and numerous aluminum stampings.
5. Main Research Findings:
- Key Findings: The MMLV vehicle achieved a 23.5% weight reduction (1170 kg vs 1559 kg) compared to the 2013 Ford Fusion production model. This reduction was significantly attributed to the incorporation of aluminum hpvdc components.
- Quantitative/Qualitative Analysis Results: The MMLV BIW comprised 63% aluminum and 37% steel. The use of eight hpvdc components resulted in a 32-piece part count reduction and improved stiffness. Crash simulations demonstrated improved crashworthiness compared to the baseline vehicle.
- Data Interpretation: Aluminum hpvdc casting technology facilitated weight reduction, part consolidation, and simplified assembly processes. Low-pressure precision sand casting was employed for seven of the eight castings to mimic hpvdc performance due to tooling cost considerations for low-volume production. A variety of joining techniques (SPR, CMT welding, adhesives) were used to successfully integrate the multi-material BIW structure.
- Figure List:
- Figure 1. MMLV concept vehicle
- Figure 2. MMLV BIW Design
- Figure 3. MMLV BIW concept prototype
- Figure 4. MMLV BIW showing hpvdc castings
- Figure 5. MMLV vacuum die cast shock tower casting x-ray
- Figure 6. MMLV kick down rail, Magmasoft Casting Fill Simulation
- Figure 7. MMLV aluminum shock tower casting
- Figure 8. MMLV aluminum shock tower casting joined to the front end assembly by SPR and CMT methods
- Figure 9. MMLV kick down rail
- Figure 10. MMLV Frontal 40% off-set impact FEA with improved intrusion over baseline
- Figure 11. MMLV hinge pillar
- Figure 12. MMLV hinge pillar casting one sided joining with flow drill screws
- Figure 13. MMLV mid rear rail
- Figure 14. MMLV mid rear rail assembly
- Figure 15. SPR of MMLV shock tower casting to front rail
- Figure 16. MMLV cast aluminum hinge pillar to cast aluminum extruded rail TIG weld.
- Figure 17. MMLV TIG weld detail
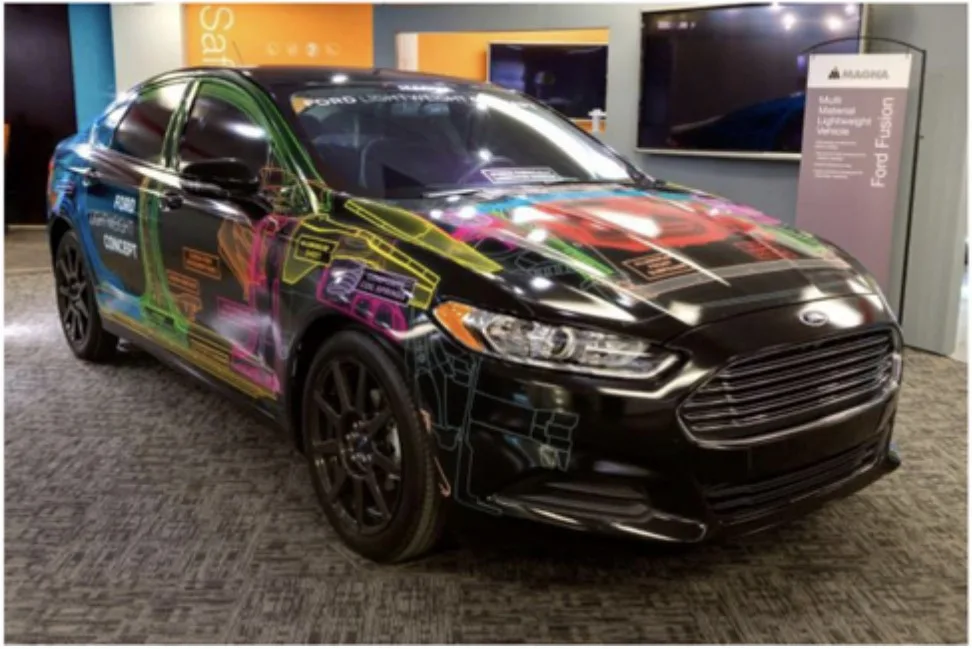
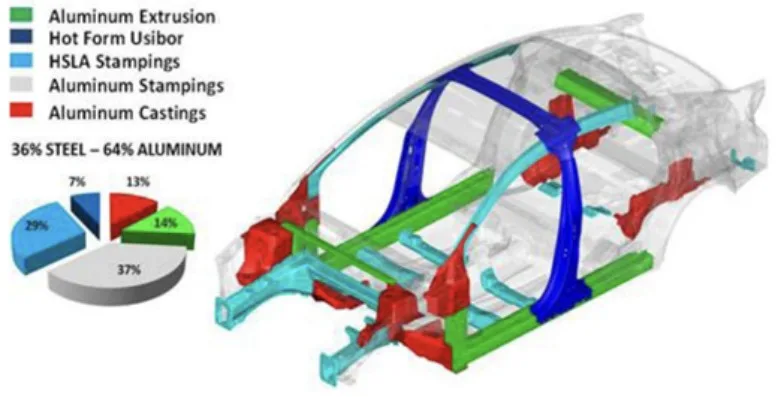
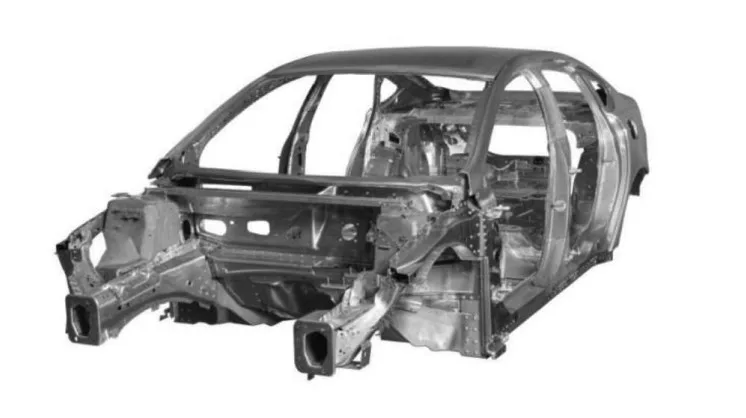
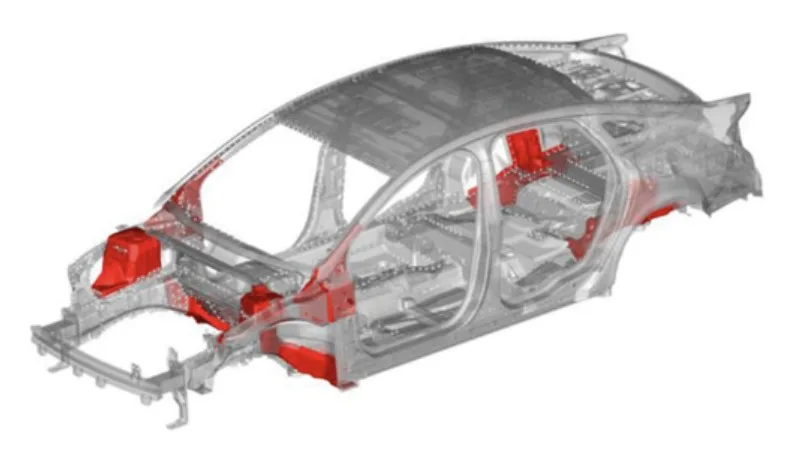
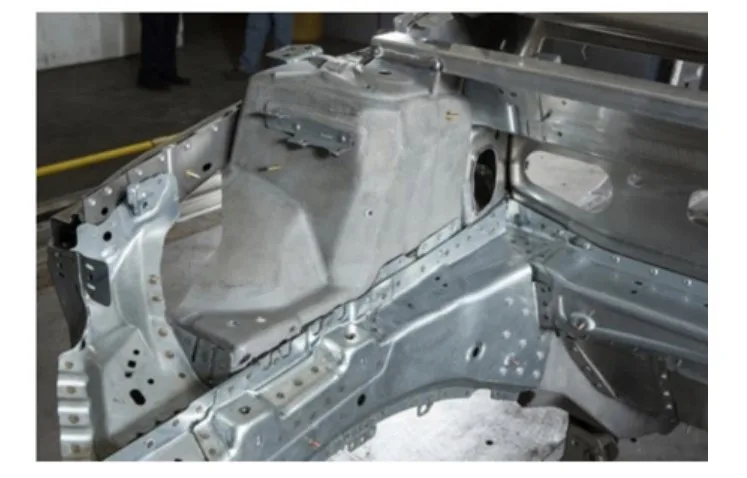
6. Conclusions and Discussion:
The MMLV project successfully demonstrated the effectiveness of a multi-material BIW design incorporating aluminum hpvdc components. Significant weight reduction was achieved while maintaining or exceeding performance targets for stiffness, durability, and crashworthiness. Cost reduction was realized through part consolidation and simplified assembly. However, the use of low-pressure sand casting for a majority of the components and the cost implications of low-volume production warrant further investigation.
7. Future Research Directions:
Further research is needed to explore the integration of aluminum hpvdc technology with high-strength steel and other advanced materials. Optimization of manufacturing processes for high-volume production is crucial. A more comprehensive analysis of different joining techniques, considering both performance and cost-effectiveness, is also warranted. Finally, further research should focus on expanding the application of this multi-material approach to a wider range of vehicle platforms and sizes.
8. References: (Insert the reference list from the original paper)
Copyright: This document summarizes the research presented in [Randy Beals¹, Jeff Conklin¹, Tim Skszek¹, Matt Zaluzec², David Wagner²]'s paper: "Aluminum High Pressure Vacuum Die Casting Applications for the Multi Material Lightweight".
This summary is for informational purposes only and may not be used for commercial purposes without permission.
Copyright © 2025 CASTMAN. All rights reserved.