This article introduces the paper ['Advances in Metal Casting Technology: A Review of State of the Art, Challenges and Trends—Part I: Changing Markets, Changing Products'] presented at the ['Metals']
1. Overview:
- Title: Advances in Metal Casting Technology: A Review of State of the Art, Challenges and Trends—Part I: Changing Markets, Changing Products
- Author: Dirk Lehmhus
- Publication Year: 2022
- Publishing Journal/Academic Society: Metals, MDPI
- Keywords
Metal casting technology, changing markets, changing products, industry challenges, industry trends, e-mobility, structural castings, additive manufacturing, environmental issues.
![Figure 2. “The fundamental interconnectedness of all things” [14]: In the words of my namesake, a visual guide through this present text (PART I in the diagram), and the following, second part (PART II) to be published in a few months’ time—four colors, four main chapters, four subsections and some selected links between them.](https://castman.co.kr/wp-content/uploads/image-591-1024x501.webp)
2. Research Background:
Background of the Research Topic:
Metal casting is identified as one of the "oldest primary shaping processes known to humanity". The paper highlights the historical significance of metal casting, tracing its origins back to "several thousand years ago" with "copper-based alloys" and "two-part stone or ceramic molds". It mentions "lost wax casting" as a precursor to "modern investment casting" appearing as early as "6000 years ago". The evolution of metal casting is linked to historical periods, noting "bronze castings of Greek antiquity" and the impact of the "industrial revolution" which introduced "iron and steel in large amounts" and "permanent molds as well as casting machinery". The advent of "light alloys aluminum, magnesium and later also titanium" is also recognized as a significant advancement. The "increasingly broad introduction of automobiles" from the "turn of the 19th century onwards" is presented as a "major turning point" for new products and high productivity processes.
Status of Existing Research:
The paper positions itself as an introduction to a Special Issue of Metals on “Advances in Metal Casting Technology”, aiming to provide an overview of "selected technological developments in metal casting" and "current trends in markets and boundary conditions". It acknowledges the "diversity of the casting industry" and states that the selection of topics will "necessarily reflect the author's personal perspective", with a potential focus on "high-pressure die casting, specifically of aluminum alloys". The paper refers to the ongoing "fourth industrial revolution" and its impact on the casting industry through "digitalization, advanced simulation approaches such as the digital twin concept adapted to its processes, and the extended use of artificial intelligence techniques."
Necessity of the Research:
The research is deemed necessary to understand the "fundamental interconnectedness" of changing markets and technological advancements in the metal casting industry. The paper emphasizes the need to analyze current trends, challenges, and future directions in the field, especially in the context of evolving market demands, technological disruptions, and global economic shifts. It highlights the importance of reviewing the "global metal casting markets" and the "link between the individual contributions in this Special Issue to these fields". The paper also points out the need to consider the impact of events like the "COVID-19 pandemic" and the "Russian Federation's war of aggression against Ukraine" on the casting industry.
3. Research Purpose and Research Questions:
Research Purpose:
The primary purpose of this paper is to provide "an introduction to a Special Issue of Metals on “Advances in Metal Casting Technology”". It aims to "cast spotlights on selected technological developments in metal casting" while also "considering current trends in markets and boundary conditions". The paper intends to offer "background information" including "an overview of the global metal casting markets" and to highlight "the link between the individual contributions in this Special Issue to these fields".
Key Research:
The key research areas explored in this paper are:
- Analysis of the global casting industry's facts and figures, including production volume by country and material class.
- Examination of changing markets and products, focusing on challenges and trends in the metal casting industry.
- Discussion of current development directions, particularly in e-mobility and automotive structural castings.
- Consideration of additive manufacturing as a competing or complementary technology.
- Assessment of environmental issues and sustainability in metal casting.
Research Hypotheses:
Not applicable for this review paper.
4. Research Methodology
Research Design:
This paper employs a review-based research design. It synthesizes existing data, industry reports, and literature to provide an overview of the state-of-the-art, challenges, and trends in metal casting technology. The approach is descriptive and analytical, aiming to identify patterns, challenges, and future directions within the industry.
Data Collection Method:
The data presented in this paper is primarily collected from:
- "World Foundry Organization (WFO) annual census [15-27]" for global casting production figures.
- Data collected and evaluated by Büchner [28,29] for future projections of the casting industry.
- "German Foundry Industry Association (BDG)" prognosis for market developments [29].
- Industry reports and publications, as cited throughout the text.
Analysis Method:
The analysis methods used in this paper include:
- Descriptive statistics to present global casting production data (Tables 1 and 2, Figures 3 and 4).
- Trend analysis to identify patterns and changes in market shares and material usage.
- Comparative analysis to assess different casting processes and technologies.
- Qualitative analysis of industry challenges, trends, and future directions based on literature review and expert perspectives.
Research Subjects and Scope:
The research subjects are the global metal casting industry, encompassing all materials and processes. The scope of the paper is broad, covering:
- Global market analysis of casting production volume and trends.
- Technological developments in metal casting processes.
- Impact of changing markets, particularly the automotive industry's shift towards e-mobility and structural castings.
- Challenges and opportunities related to additive manufacturing and environmental sustainability in the casting industry.
- Geographical focus includes global regions with specific emphasis on China, Europe, NAFTA, and Asia.
5. Main Research Results:
Key Research Results:
- Global Casting Industry Trends: The global casting industry experienced "a constant rise in output" until 2018, with China dominating production. However, a tonnage drop was observed in 2019, potentially influenced by factors beyond the COVID-19 pandemic. "China has increased its share of global casting production from 28.1% in 2004 to 44.7% in 2019".
- Material Class Developments: "Global casting production is dominated by the three material classes cast iron, steel and aluminum". Projections suggest an "increase in production of aluminum castings and a parallel decline in cast iron almost equal in volume". There's a shift in China towards "higher grades exemplified by the proportions of grey cast iron, which steadily declined" and "ductile iron (nodular and vermicular), which rose".
- E-mobility Impact: E-mobility is significantly impacting the casting industry, leading to a reduction in cast weight in automotive powertrains. "Depending on vehicle size class, reductions between 35 and 52% on a weight basis are observed" when comparing ICE and BEV powertrains. This necessitates new approaches like "structural castings" and innovations in casting components for electric powertrains, such as "housings for electric motors, power electronics and battery packs" with integrated cooling solutions.
- Automotive Structural Castings and Gigacasting: There is a strong trend towards "automotive structural castings", exemplified by "Tesla's Gigacasting approach". This involves large single-piece castings for vehicle bodies, requiring "HPDC machines of hitherto unknown dimensions" with locking forces up to "92,000 kN". China is leading in the adoption of Gigacasting technology.
- Additive Manufacturing (AM): AM is considered more "complementary" to casting rather than a direct replacement, especially for "geometries accessible to casting either not at all or only with great effort". AM can benefit casting through "3D-printed sand molds and cores" and "integration, by means of compound casting processes, of inserts that profit from the extreme geometrical flexibility of the AM process".
- Environmental Issues: Environmental concerns are increasingly important, driving the need for "green casting" practices. Key areas include "energy consumption, direct emissions and waste". Solutions involve "use of inorganic binders", "reclamation and reuse of foundry sand", "microspraying", and adapting furnaces for "green-hydrogen" or electric systems.
Data Interpretation:
- The data indicates a shift in the global casting industry landscape, with China's dominance and evolving material preferences.
- E-mobility is a disruptive force, requiring adaptation and innovation in casting technologies and materials.
- Structural castings and Gigacasting represent a significant trend, particularly in the automotive sector, but also pose challenges in terms of equipment, tooling, and process control.
- AM offers both competition and opportunities for collaboration with casting, particularly in mold and core production and functional integration.
- Environmental sustainability is becoming a critical factor, necessitating process optimization and adoption of greener technologies.
Figure Name List:
- Figure 1. Bronze art representing the history of casting across millennia and cultures, clockwise from top left: a Chinese Ding ritual cauldron of the late Shang Dynasty, 18–11th century BC [5]; the Dancing Girl of Mohenjo-Daro, Indus civilization, approx. 2300–1750 BC [6]; the Amitābha Buddha at Kamakura, Japan, allegedly cast in 1252 AD [7]; the bronze age Sun Chariot of Trundholm, Denmark, now at Nationalmuseet, Copenhagen, dating back to 1400 BC [8]; the Artemision Bronze, a classic Greek sculpture of either Poseidon or Zeus, cast in the 5th century BC [9]; the equestrian statue or Roman emperor Marcus Aurelius, 165–166 AD [10].
- Figure 2. "The fundamental interconnectedness of all things" [14]: In the words of my namesake, a visual guide through this present text (PART I in the diagram), and the following, second part (PART II) to be published in a few months' time—four colors, four main chapters, four subsections and some selected links between them.
- Figure 3. Graphical representation of the development of the relative importance of cast materials between 2004 and 2017 based on WFO data, as summarized in Table 2, (a) in absolute and (b) in relative numbers.
- Figure 4. Prognosis regarding future development of the casting industry until 2025 based on data presented by Büchner [28], covering (a,b) cast iron and (c,d) aluminum alloys in terms of absolute (a,c) and relative (b,d) figures. See Table 3 for production data per material class, including others.
- Figure 5. Projected development of the casting in industry according to the German Foundry Industry Association [29]: (a) Europe and (b) Asia, both with NAFTA data for comparison. Note the difference in the scale of the y-axis between (a,b).
- Figure 6. E-mobility's impact on the weight of castings in the automotive powertrain; (a) subcompact cars, (b) compact cars and (c) mid-size cars [35,36].
- Figure 7. Electric motor housing demonstrator cast at ae group using the MH Technologies ZLeak Tube® concept for realization of cooling channels: left, CAD image showing geometry and position of the tubes (tube length is approx. 1400 mm, outer diameter 14 mm, wall thickness 2 mm); center, CAD image of casting with runner, overflows, etc. with parts of the mold; right, photograph of an actual casting [44].
- Figure 8. The pitfalls of rotor casting made visible via advanced CT techniques by Yxlon in cooperation with Fraunhofer IFAM: photograph of the actual rotor (top left), 3D high-energy CT image highlighting porosity in short-circuit rings and conductor bars (top right), 2D conventional (bottom left) and high-energy CT image (bottom right), with the latter clearly showing the differences in discernability of features within the cast material (images courtesy of Yxlon and Fraunhofer IFAM [50]).
- Figure 9. State of the art and the shape and size of things to come: (a) Bühler's Carat 610 high-pressure die casting machine with a locking force of 61,000 kN—the person standing beside it may serve as an indication for the sheer size of this device, as does (b) the car in the rendering of the Carat 840 machine. The casting for the latter's movable die half's mounting plate alone weighs 99.5 tons (images provided by Bühler AG).
- Figure 10. Overview of global orders for HPDC machines with locking forces of 4000 t and above, as compiled by Gärtner and Zhou [73]. Note that there is some ambiguity in the data: nine smaller HPDC machines in the "unknown" category are linked to Tesla—here, it is not clear with which Giga Factory they are associated. Similarly, a batch of 8 machines of 5500 tons purportedly ordered by Tesla from IDRA for Grünheide and Fremont has been evenly shared between USA and Germany here.
- Figure 11. More promise than threat: binder jetting additive manufacturing used to produce molds and cores for sand casting. (a) Engine block core printed using an inorganic binder system, (b) water jacket core package printed with furan-based organic (black) and inorganic binders (Picture kindly provided by ExOne; copyright: ExOne).
![Figure 1. Bronze art representing the history of casting across millennia and cultures, clockwise from top left: a Chinese Ding ritual cauldron of the late Shang Dynasty, 18–11th century BC [5]; the Dancing Girl of Mohenjo-Daro, Indus civilization, approx. 2300–1750 BC [6]; the Amitabha Buddha at ¯ Kamakura, Japan, allegedly cast in 1252 AD [7]; the bronze age Sun Chariot of Trundholm, Denmark, now at Nationalmuseet, Copenhagen, dating back to 1400 BC [8]; the Artemision Bronze, a classic Greek sculpture of either Poseidon or Zeus, cast in the 5th century BC [9]; the equestrian statue or Roman emperor Marcus Aurelius, 165–166 AD [10]](https://castman.co.kr/wp-content/uploads/image-592-1024x791.webp)
![Figure 2. "The fundamental interconnectedness of all things" [14]: In the words of my namesake, a visual guide through this present text (PART I in the diagram), and the following, second part (PART II) to be published in a few months' time—four colors, four main chapters, four subsections and some selected links between them.](https://castman.co.kr/wp-content/uploads/image-593-678x1024.webp)
![Figure 4. Prognosis regarding future development of the casting industry until 2025 based on data presented by Büchner [28], covering (a,b) cast iron and (c,d) aluminum alloys in terms of absolute (a,c) and relative (b,d) figures. See Table 3 for production data per material class, including others.](https://castman.co.kr/wp-content/uploads/image-594-1024x708.webp)
![Figure 7. Electric motor housing demonstrator cast at ae group using the MH Technologies ZLeak Tube® concept for realization of cooling channels: left, CAD image showing geometry and position of the tubes (tube length is approx. 1400 mm, outer diameter 14 mm, wall thickness 2 mm); center, CAD image of casting with runner, overflows, etc. with parts of the mold; right, photograph of an actual casting [44].](https://castman.co.kr/wp-content/uploads/image-595-png.webp)
![Figure 8. The pitfalls of rotor casting made visible via advanced CT techniques by Yxlon in cooperation with Fraunhofer IFAM: photograph of the actual rotor (top left), 3D high-energy CT image highlighting porosity in short-circuit rings and conductor bars (top right), 2D conventional (bottom left) and highenergy CT image (bottom right), with the latter clearly showing the differences in discernability of features within the cast material (images courtesy of Yxlon and Fraunhofer IFAM [50]).](https://castman.co.kr/wp-content/uploads/image-596-png.webp)
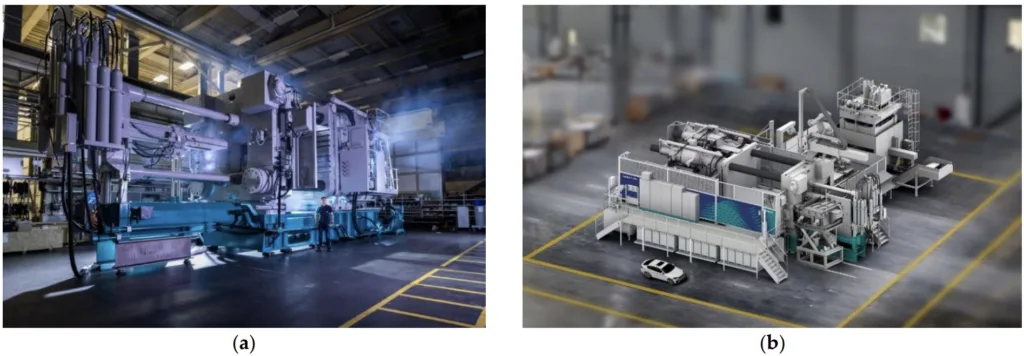
6. Conclusion:
Summary of Main Results:
The metal casting industry is undergoing significant transformations driven by changing markets, technological advancements, and global events. Key trends include the shift towards e-mobility and structural castings, the rise of Gigacasting, the evolving role of additive manufacturing, and increasing environmental concerns. While facing challenges, the industry demonstrates adaptability and innovation, particularly in adopting new technologies and addressing sustainability demands. The global landscape is dynamic, with China playing a dominant role and new production and consumption patterns emerging.
Academic Significance of the Research:
This review provides a comprehensive overview of the current state and future directions of the metal casting industry. It synthesizes data from various sources to offer insights into market trends, technological developments, and key challenges. The paper serves as a valuable resource for researchers and experts seeking to understand the broad landscape of metal casting and identify areas for further investigation and innovation. It also sets the stage for the Special Issue by highlighting the interconnectedness of various aspects within the field.
Practical Implications:
The findings of this review have significant practical implications for stakeholders in the metal casting industry:
- Strategic Adaptation: Casting companies need to adapt their strategies to address the changing demands of e-mobility and structural castings, investing in new technologies and materials.
- Technological Innovation: Continued innovation in casting processes, materials, and digitalization is crucial for maintaining competitiveness and addressing new application requirements.
- Sustainability Focus: Adopting sustainable practices and technologies is becoming increasingly important due to environmental regulations and customer demands.
- Market Awareness: Understanding global market trends and regional dynamics is essential for strategic decision-making and market positioning.
- Workforce Development: Addressing the challenge of sourcing qualified personnel is critical for the industry's future, requiring efforts to enhance the attractiveness of casting careers.
Limitations of the Research
The paper acknowledges that the selection of topics "can naturally not be complete and will necessarily reflect the author's personal perspective". It also mentions that "topics linked to high-pressure die casting, specifically of aluminum alloys, may receive more attention than some readers might consider justified". Furthermore, the analysis of future projections may be limited by unforeseen events such as the "disrupting impact of the COVID-19 pandemic" and the "economic consequences of the recent, deliberate breach of international law represented by the Russian Federation's war of aggression against Ukraine".
7. Future Follow-up Research:
- Directions for Follow-up Research
The paper explicitly mentions a "second part, subtitled “Technologies New and Revived", will be published soon after the present one". This Part II will delve into "new and emerging technologies such as semi-solid processes, hybrid as well as compound casting, smart castings as well as other Industry 4.0 aspects such as advanced simulation techniques and data analytics". - Areas Requiring Further Exploration
The paper implicitly suggests several areas requiring further exploration: - The long-term impact of the COVID-19 pandemic and geopolitical events on the global casting industry.
- Deeper investigation into the "vulnerability of Chinese-centered supply chains" and potential shifts in global casting production distribution.
- Further research and development of "new structural alloys that fulfill the respective requirement" for structural castings, particularly those that eliminate the need for heat treatment.
- Continued investigation into the "competitiveness of AM" in relation to casting and the synergistic opportunities between these technologies.
- More comprehensive life cycle assessments (LCA) of different casting processes and structural casting applications to guide sustainability efforts.
- Strategies to address the "problem of sourcing qualified personnel" in the casting industry.
8. References:
- [1] Davey, C.J. The early history of lost-wax casting. In Metallurgy and Civilisation: Eurasia and Beyond; Mei, J., Rehren, T., Eds.; Archetype Books: London, UK, 2009; pp. 147-154.
- [2] Craddock, P.T. The Metal Casting Traditions of South Asia: Continuity and Innovation. Indian J. Hist. Sci. 2014, 50, 55–82. [CrossRef]
- [3] Mattusch, C.C. The Berlin Foundry Cup: The Casting of Greek Bronze Statuary in the Early Fifth Century B.C. Am. J. Archaeol. 1980, 84, 435-444. [CrossRef]
- [4] Mattusch, C.C. Greek Bronze Statuary: From the beginnings through the 5th Century B.C; Cornell University Press: Ithaca, NY, USA, 1988.
- [5] Mountain, Photograph of a Chinese Ding Ritual Cauldron, CC BY-SA 3.0. Available online: https://commons.wikimedia.org/w/index.php?curid=602198 (accessed on 26 October 2022).
- [6] Available online: http://www.columbia.edu/itc/mealac/pritchett/00routesdata/bce_500back/indusvalley/dancer/dancer.html (accessed on 26 October 2022).
- [7] Beyer, D. Photograph of Amitabha Buddha at Kamakura, Japan, CC BY-SA 3.0. Available online: https://commons.wikimedia.org/w/index.php?curid=230799 (accessed on 26 October 2022).
- [8] Nationalmuseet Copenhagen, Photograph of the Sun Chariot of Trundholm, CC BY-SA 3.0. Available online: https://commons.wikimedia.org/w/index.php?curid=90400464 (accessed on 26 October 2022).
- [9] Frantz, R.A. Photograph of the Sculpture of Zeus or Poseidon of Cape Artemision, CC BY-SA 3.0. Available online: https://commons.wikimedia.org/w/index.php?curid=2959518 (accessed on 26 October 2022).
- [10] Grandmont, J.-P. Photograph of Equestrian Sculpture of Marc Aurel, CC BY-SA 3.0. Available online: https://commons.wikimedia.org/w/index.php?curid=25800464 (accessed on 26 October 2022).
- [11] Murray, M.T. High pressure die casting of aluminium alloys. In Fundamentals of Aluminium Metallurgy: Production, Processing and Applications; Lumley, R., Ed.; Woodhead Publishing: Philadelphia, PA, USA, 2011.
- [12] Tripsas, M. Surviving Radical Technological Change through Dynamic Capability: Evidence from the Typesetter Industry. Ind. Corp. Chang. 1997, 6, 341-377. [CrossRef]
- [13] Leng, J.; Sha, W.; Wang, B.; Zheng, P.; Zhuang, C.; Liu, Q.; Wuest, T.; Mourtzis, D.; Wang, L. Industry 5.0: Prospect and retrospect. J. Manuf. Syst. 2022, 65, 279–295. [CrossRef]
- [14] Adams, D. Dirk Gently's Holistic Detective Agency; William Heinemann Ltd.: London, UK, 1987.
- [15] Available online: http://www.thewfo.com/contentfiles/downloads/51.pdf (accessed on 26 October 2022).
- [16] Available online: http://www.thewfo.com/contentfiles/downloads/7.pdf (accessed on 26 October 2022).
- [17] Available online: http://www.thewfo.com/contentfiles/downloads/6.pdf (accessed on 26 October 2022).
- [18] Available online: http://www.thewfo.com/contentfiles/downloads/5.pdf (accessed on 26 October 2022).
- [19] Available online: http://www.thewfo.com/contentfiles/downloads/4.pdf (accessed on 26 October 2022).
- [20] Available online: http://www.thewfo.com/contentfiles/downloads/3.pdf (accessed on 26 October 2022).
- [21] Available online: http://www.thewfo.com/contentfiles/downloads/2.pdf (accessed on 26 October 2022).
- [22] Available online: http://www.thewfo.com/contentfiles/downloads/1.pdf (accessed on 26 October 2022).
- [23] Available online: http://www.thewfo.com/contentfiles/downloads/31.pdf (accessed on 26 October 2022).
- [24] Available online: http://www.thewfo.com/contentfiles/downloads/35.pdf (accessed on 26 October 2022).
- [25] Available online: http://www.thewfo.com/contentfiles/downloads/41.pdf (accessed on 26 October 2022).
- [26] Available online: http://www.thewfo.com/contentfiles/downloads/44.pdf (accessed on 26 October 2022).
- [27] Available online: http://www.thewfo.com/contentfiles/downloads/49.pdf (accessed on 26 October 2022).
- [28] Büchner, H.-J. Forecast 2025 for the global Foundry Industry. In Proceedings of the Presentation at GIFA 2019, 14th International Casting Trade Fair, Düsseldorf, Germany, 25-29 June 2020.
- [29] Mettler, S.; Schmitz-Cohnen, K. Guss 2035—Neue Perspektiven für Die Gießereiindustrie. Bundesverband der Deutschen Gießereiindustrie (BDG): Düsseldorf, DE, 2022. Available online: https://www.guss.de/fileadmin/user_upload/leitfaeden_und_broschueren/studie_guss_2035.pdf (accessed on 8 October 2022).
- [30] Spada, A. Revitalization of North American Metalcasting. Available online: https://www.diecasting.org/docs/statistics/NorthAmerica.pdf (accessed on 26 October 2022).
- [31] Available online: https://www.guss.de/organisation/bdg/branche (accessed on 8 October 2022).
- [32] Available online: https://www.guss.de/organisation/presseinformation/ukraine-umfrage (accessed on 26 October 2022).
- [33] Bonollo, F.; Gramegna, N.; Timelli, G. High-Pressure Die-Casting: Contradictions and Challenges. JOM 2015, 67, 901-908. [CrossRef]
- [34] Messer, J. The 4 Challenges in Aluminum HPDC—Aluminum Foundry Industry Is Changing. Johannes Messer Consulting GmbH, 14 January 2019. Available online: https://johannes-messer-consulting.de/pdf/the_4_challenges_in_aluminum_hpdc.pdf (accessed on 26 October 2022).
- [35] Wilhelm, C.; Kallien, L.H. Einfluss der Elektromobilität auf die Gussproduktion In der deutschen Gießereiindustrie—Influence of electromobility on the German casting industry. Prozesswärme 2018, 7, 35–40.
- [36] Wilhelm, C.; Kallien, L.H.; Görgün, V. Einfluss der Elektromobilität auf die Gussproduktion in der deutschen Gießereiindustrie (Teil 2)-Influence of electromobility on the German casting industry (Part 2). Prozesswärme 2019, 1, 39–46.
- [37] Chong, Y.C.; Staton, D.; Gai, Y.; Adam, H.; Popescu, M. Review of Advanced Cooling Systems of Modern Electric Machines for EMobility Application. In Proceedings of the 2021 IEEE Workshop on Electrical Machines Design, Control and Diagnosis (WEMDCD 2021), Modena, Italy, 8-9 April 2021. [CrossRef]
- [38] Scherer, H.; Bek, M.; Kilian, S. ZF New 8-speed Automatic Transmission 8HP70—Basic Design and Hybridization. SAE Int. J. Engines 2009, 2, 314-326. [CrossRef]
- [39] Lahaye-Geusen, M. Leichtes und Kompaktes Gehäuse für Achtgang-Automatikgetriebe-Viel Funktion auf Wenig Raum. Available online: https://automobilkonstruktion.industrie.de/allgemein/viel-funktion-auf-wenigraum/ (accessed on 19 July 2021).
- [40] Lehmhus, D.; Pille, C.; Rahn, T.; Struss, A.; Gromzig, P.; Seibel, A.; Wischeropp, T.; Becker, H.; Diefenthal, F. Druckgießen und Additive Fertigung: Durch strategische Kombination das Beste aus zwei Welten nutzen. Giesserei 2021, 108, 36-43.
- [41] Rupp, S.; Heppes, F. Combicore—Giesskerne für den Druckguss. Giess. Erfahr. 2013, 3, 6–9.
- [42] Jelinek, P.; Adamkova, E.; Miksovsky, F.; Beno, J. Advances in Technology of Soluble Cores for Die Castings. Arch. Foundry Eng. 2015, 15, 29-34. [CrossRef]
- [43] Kim, J.S.; Yoo, J. High Pressure Die Casting Core and Preparation Method of High Pressure Die Casting Core. Korean Patent KR101965669B1, 4 April 2019.
- [44] Lehmhus, D.; Pille, C.; Borheck, D.; Bumbu, F.; Schwegler, T.; Lee, J.; Yoo, J.; Lutze, P.; Vomhof, R.; Weiss, K. Leckagefreie Kühlkanäle für Druckguss-Gehäusekomponenten. Giesserei 2021, 108, 40–49.
- [45] Feikus, F.J.; Bernsteiner, P.; Gutiérrez, R.F.; Luszczak, M. Further Development of Electric Motor Housings. MTZ Worldw. 2020, 81, 38-43. [CrossRef]
- [46] Jin, Y.; Song, Y.; Liu, Y.; Cui, W.; Sun, C. Design of low-pressure sand casting process for water-cooled motor shell in electric vehicles. J. Phys. Conf. Ser. 2021, 2102, 012052. [CrossRef]
- [47] Chen, H.; Yang, L.; Long, J. First-principles investigation of the elastic, Vickers hardness and thermodynamic properties of Al-Cu intermetallic compounds. Superlattices Microstruct. 2015, 79, 156-165. [CrossRef]
- [48] Kim, K.; Kim, D.; Park, K.; Cho, M.; Cho, S.; Kwon, H. Effect of Intermetallic Compounds on the Thermal and Mechanical Properties of Al-Cu Composite Materials Fabricated by Spark Plasma Sintering. Materials 2019, 12, 1546. [CrossRef]
- [49] Kim, D.; Kim, K.; Kwon, H. Interdiffusion and Intermetallic Compounds at Al/Cu Interfaces in Al-50vol.%Cu Composite Prepared by Solid-State Sintering. Materials 2021, 14, 4307. [CrossRef]
- [50] Pille, C.; Mäurer, G. A Look into the hidden—The First Complete CT of Cast Rotors in Electric Asynchronous Motors. Insp. Int. 2020, 2, 12-13.
- [51] Yun, J.; Lee, S.B. Influence of Aluminum Die-Cast Rotor Porosity on the Efficiency of Induction Machines. IEEE Trans. Magn. 2018, 54, 8104905. [CrossRef]
- [52] Jeong, M.; Yun, J.; Park, Y.; Lee, S.B.; Gyftakis, K. Quality Assurance Testing for Screening Defective Aluminum Die-Cast Rotors of Squirrel Cage Induction Machines. IEEE Trans. Ind. Appl. 2018, 54, 2246–2254. [CrossRef]
- [53] Lee, C.-Y.; Huang, K.-Y.; Jen, L.-Y.; Zhuo, G.-L. Diagnosis of Defective Rotor Bars in Induction Motors. Symmetry 2020, 12, 1753. [CrossRef]
- [54] Khaliq, A.; Rhamdhani, M.A.; Brooks, G.A.; Grandfield, J. Proceedings in Light Metals 2011; Lindsay, S.J., Ed.; Springer: Cham, Switzerland, 2011; pp. 751–756.
- [55] Rhamdhani, M.A.; Grandfield, J.F.; Khaliq, A.; Brooks, G. Light Metals 2013; Sadler, B.A., Ed.; Springer: Cham, Switzerland, 2013; pp. 33-38.
- [56] Kotiadis, S.; Zimmer, A.; Elsayed, A.; Vandersluis, E.; Ravindran, C. High Electrical and Thermal Conductivity Cast Al-Fe-Mg-Si alloys with Ni Additions. Metall. Mater. Trans. A 2020, 51A, 4195-4214. [CrossRef]
- [57] Kim, C.-W.; Cho, J.-I.; Choi, S.-W.; Kim, Y.-C. The effect of alloying elements on thermal conductivity of aluminum alloys in high pressure die casting. Adv. Mater. Res. 2013, 813, 175-178. [CrossRef]
- [58] Abdo, H.S.; Seikh, A.H.; Mohammed, J.A.; Soliman, M.S. Alloying Elements Effects on Electrical Conductivity and Mechanical Properties of Newly Fabricated Al Based Alloys Produced by Conventional Casting Processes. Materials 2021, 14, 3971. [CrossRef] [PubMed]
- [59] Kim, J.-M.; Yun, H.-S.; Shin, J.-S.; Kim, K.-T.; Ko, S.-H. Mold filling ability and hot cracking susceptibility of Al-Fe-Ni alloys for high conductivity applications. J. Teknol. 2015, 75, 71-77. [CrossRef]
- [60] Li, K.; Zhang, J.; Chen, X.; Yin, Y.; He, Y.; Zhou, Z.; Guan, R. Microstructure evolution of eutectic Si in Al-7Si binary alloy by heat treatment and its effect on enhancing thermal conductivity. J. Mater. Res. Technol. 2020, 9, 8780-8786. [CrossRef]
- [61] Vandersluis, E.; Lombardi, A.; Ravindran, C.; Bois-Brochu, A.; Chiesa, F.; MacKay, R. Factors influencing thermal conductivity and mechanical properties in 319 Al alloy cylinder heads. Mater. Sci. Eng. A 2015, 648, 401-411. [CrossRef]
- [62] Vandersluis, E.; Ravindran, C. The Role of Porosity in Reducing the Thermal Conductivity of B319 Al Alloy with Decreasing Solidification Rate. JOM 2019, 71, 2072–2077. [CrossRef]
- [63] Vandersluis, E.; Ravindran, C. Influence of solidification rate on the microstructure, mechanical properties, and thermal conductivity of cast A319 Al alloy. J. Mater. Sci. 2019, 54, 4325-4339. [CrossRef]
- [64] Visnic, B. Tesla Casts a New Strategy for Lightweight Structures. Automot. Eng. 2020, 6, 12–14. Available online: https://www.nxtbook.com/nxtbooks/sae/20AUTP06/index.php#/p/12 (accessed on 4 January 2021).
- [65] Tesla's Switch to Giga Press Die Castings for Model 3 Eliminates 370 Parts. Available online: https://www.designnews.com/automotive-engineering/teslas-switch-giga-press-die-castings-model-3-eliminates-370-parts (accessed on 4 January 2022).
- [66] Kallas, M.K. Multi-Directional Unibody Casting Machine for a Vehicle Frame and Associated Methods. US Patent Application US 2019/0217380 A1, 18 July 2019.
- [67] Available online: https://www.buhlergroup.com/content/buhlergroup/global/en/products/carat_die-castingmachine.html (accessed on 4 January 2022).
- [68] Available online: https://www.teslarati.com/idra-9000-ton-giga-press/ (accessed on 8 October 2022).
- [69] Stegmaier, G. Alu-Guss Statt nur Schwedenstahl: Volvo Investiert 1 Milliarde in Tesla-Trick. Available online: https://www.auto-motor-und-sport.de/tech-zukunft/volvo-mega-casting-alu-elektroauto-produktion-nachhaltigkeit-neue-e-auto-plattformen/ (accessed on 10 February 2022).
- [70] Kacher, G.; Johannsen, F. Aus einem Guss. In der Neuen Trinity-Fabrik von Volkswagen Sollen Karosserien Nicht Mehr Geschweißt Werden—Tesla dient als Vorbild; Automobilwoche: Weßling, Germany, 2022.
- [71] Available online: https://www.lk.world/us/news_detail.php?type=&nid=455 (accessed on 10 February 2022).
- [72] Available online: https://www.laitimes.com/en/article/3kycy_41ndm.html (accessed on 8 October 2022).
- [73] Gärtner, J.; Zhou, Y. Realized & Planned Installment Of GIGA-/MEGA-Presses “By Whom-When-Where-Why” Insights & Prospects. In Proceedings of the 3rd VDI-Fachkonferenz Gießtechnik und E-Mobilität, Bremen, Germany, 18–19 October 2022.
- [74] Rai, A.; Sawant, S.S.; Winberg, P.; Burgess, M.; Spencer, T.; Kornmayer, P.; Pattinson, G.; Edwards, P.D.; Rinaldi, C.; Reikher, A.; et al. Integrated Energy Absorbing Castings. Patent Publication Number WO/2022/031991, 5 August 2021.
- [75] Tayal, R.K.; Singh, V.; Kumar, S.; Garg, R. Compound Casting-A Literature Review. In Proceedings of the National Conference on Trends and Advances in Mechanical Engineering, Faridabad, India, 19–20 October 2012; pp. 501–510.
- [76] Lehmhus, D.; von Hehl, A.; Hausmann, J.; Kayvantash, K.; Alderliesten, R.; Hohe, J. New Materials and Processes for Transport Applications: Going Hybrid and Beyond. Adv. Eng. Mater. 2019, 21, 1900056. [CrossRef]
- [77] Yurko, J.A.; Martinez, R.A.; Flemings, M.C. The Use of Semi-Solid Rheocasting (SSR) for Aluminum Automotive Castings. SAE Trans. J. Mater. Manuf. 2003, 112, 119–123.
- [78] Roos, H.J.; Lagler, M.; Quintana, L. Whitepaper: Die Zukunft von Strukturbauteilen für Druckgusslösungen. Bühler AG, 2019. Available online: https://assetcdn.buhlergroup.com/asset/874601345621/86bd505f19e643b2b3ce79957169681c (accessed on 24 February 2022).
- [79] Sigworth, G.K.; Donahue, R.J. The Metallurgy of Aluminum Alloys for Structural High Pressure Die Castings. Int. J. Met. 2021, 15, 1031-1046. [CrossRef]
- [80] Kang, J.W.; Ma, Q.-X. The role and impact of 3D printing technologies in casting. China Foundry 2017, 14, 157-168. [CrossRef]
- [81] Roth, C.C.; Tancogne-Dejean, T.; Mohr, D. Plasticity and fracture of cast and SLM AlSi10Mg: High throughput testing and modelling. Addit. Manuf. 2021, 43, 101998. [CrossRef]
- [82] Lehmhus, D.; Busse, M. Structural Health Monitoring. In Material-Integrated Intelligent Systems—Technology and Applications; Bosse, S., Lehmhus, D., Lang, W., Busse, M., Eds.; Wiley-VCH Verlag: Weinheim, Germany, 2018; pp. 531-594.
- [83] Lores, A.; Azurmendi, N.; Agote, I.; Zuza, E. A review on recent developments in binder jetting metal additive manufacturing: Materials and process characteristics. Powder Metall. 2019, 62, 267-296. [CrossRef]
- [84] Li, M.; Du, W.; Elwany, A.; Pei, Z.; Ma, C. Metal binder jetting additive manufacturing: A literature review. J. Manuf. Sci. Eng. 2020, 142, 090810. [CrossRef]
- [85] Mostafaei, A.; Elliott, A.M.; Barnes, J.E.; Li, F.; Tan, W.; Cramer, C.L.; Nandwana, P.; Chmielus, M. Binder jet 3D printing—Process parameters, materials, properties, modeling, and challenges. Prog. Mater. Sci. 2021, 119, 100707. [CrossRef]
- [86] Williams, S.W.; Martina, F.; Addison, A.C.; Ding, J.; Pardal, G.; Colegrove, P. Wire + Arc Additive Manufacturing. Mater. Sci. Technol. 2016, 32, 641-647. [CrossRef]
- [87] Lehmhus, D.; Busse, M. Sensor Integration in Additive Manufacturing. In Material-Integrated Intelligent Systems—Technology and Applications; Bosse, S., Lehmhus, D., Lang, W., Busse, M., Eds.; Wiley-VCH Verlag: Weinheim, Germany, 2018; pp. 217–256.
9. Copyright:
- This material is "Dirk Lehmhus"'s paper: Based on "Advances in Metal Casting Technology: A Review of State of the Art, Challenges and Trends—Part I: Changing Markets, Changing Products".
- Paper Source: https://doi.org/10.3390/met12111959
This material was summarized based on the above paper, and unauthorized use for commercial purposes is prohibited.
Copyright © 2025 CASTMAN. All rights reserved.