This article introduces the paper ['Advancements in surface treatments for aluminum alloys in sports equipment'] presented at the ['Reviews on Advanced Materials Science']
1. Overview:
- Title: Advancements in surface treatments for aluminum alloys in sports equipment
- Author: Shaozhou Chen
- Publication Year: 2024
- Publishing Journal/Academic Society: Reviews on Advanced Materials Science
- Keywords: surface modification, corrosion protection, eco-friendly coatings, microstructural refinement, mechanical performance
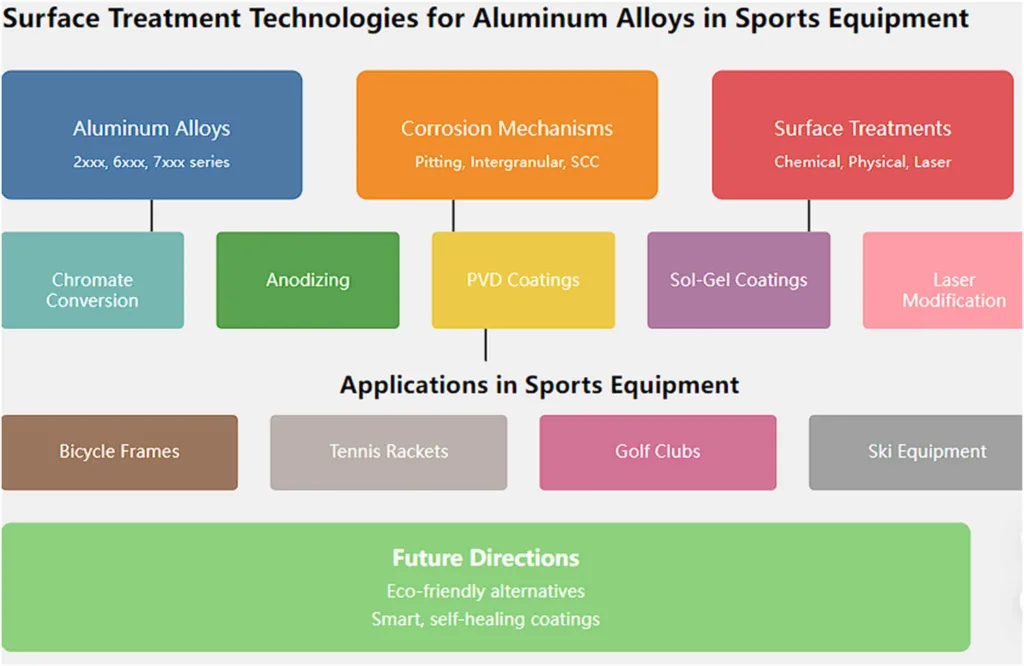
2. Research Background:
Background of the Research Topic:
Aluminum alloys are widely used in sports equipment due to their "exceptional properties, such as a high strength-to-weight ratio, good formability, and excellent corrosion resistance". However, the surfaces of aluminum alloys in sports equipment are "subject to various forms of deterioration depending on the specific application and usage conditions". Surface treatment technologies are crucial to "enhance the corrosion resistance and overall performance of aluminum alloys used in sports equipment".
Status of Existing Research:
Existing research has explored various surface treatment methods for aluminum alloys, including "chemical conversion coatings, anodizing, physical vapor deposition (PVD) coatings, and sol-gel coatings". Among these, "chemical conversion coatings have been widely used in the sports equipment industry due to their cost-effectiveness, ease of application, and ability to provide excellent corrosion protection". However, "the use of hexavalent chromium in CCCs has raised environmental and health concerns", driving the development of eco-friendly alternatives like "trivalent chromium conversion (TCC) coatings and other chromium-free conversion coatings based on molybdenum, zirconium, titanium, and rare-earth elements". Recent studies have shown "promising results in developing nano-engineered coatings that offer superior performance".
Necessity of the Research:
Despite advancements, challenges remain in surface treatments for aluminum alloys in sports equipment. These include "achieving uniform coating thickness on complex geometries", ensuring treatments "withstand the dynamic stresses experienced by sports equipment during use", and "balancing functional improvements with aesthetic appeal". Furthermore, "the industrial implementation of advanced surface treatments poses economic challenges". Therefore, continued research and development are necessary to overcome these challenges and improve the performance, sustainability, and cost-effectiveness of surface treatments for aluminum alloys in sports equipment.
3. Research Purpose and Research Questions:
Research Purpose:
This review aims to "examine recent advancements in surface treatment technologies for aluminum alloys used in sports equipment". It assesses and evaluates these advancements, discussing "conventional methods like chemical conversion coatings and anodizing, as well as emerging techniques such as plasma electrolytic oxidation, physical vapor deposition, and laser surface modification". The review also addresses "the replacement of toxic hexavalent chromium with eco-friendly alternatives" and "explore the potential of smart, self-healing coatings to extend equipment lifespan".
Key Research:
The key research questions addressed in this review include:
- What are the recent advancements in surface treatment technologies for aluminum alloys in sports equipment?
- How do conventional and emerging surface treatment methods compare in terms of working principles, corrosion protection mechanisms, and recent developments?
- What are the environmental and health aspects of these surface treatments, particularly regarding the replacement of hexavalent chromium?
- What are the future directions and challenges in the field, including the industrial implementation of advanced surface treatment technologies?
Research Hypotheses:
This review does not explicitly state research hypotheses but implicitly suggests that:
- Emerging surface treatment technologies offer improved performance and address limitations of conventional methods for aluminum alloys in sports equipment.
- Eco-friendly alternatives can effectively replace toxic hexavalent chromium in surface treatments without compromising performance.
- Smart, self-healing coatings have the potential to significantly extend the lifespan and enhance the durability of aluminum sports equipment.
4. Research Methodology
Research Design:
This paper is a review article. It adopts a descriptive and analytical approach to summarize and evaluate the current state of surface treatment technologies for aluminum alloys in sports equipment.
Data Collection Method:
The data collection method involves a comprehensive literature review of "recent advancements in surface treatment technologies for aluminum alloys used in sports equipment". The review gathers information from academic papers, research articles, and potentially industry reports related to the topic.
Analysis Method:
The analysis method is qualitative and involves:
- Descriptive Summary: Summarizing various surface treatment methods, their principles, and applications.
- Comparative Analysis: Evaluating the advantages and disadvantages of different methods, including conventional and emerging techniques.
- Thematic Analysis: Identifying key trends and challenges in the field, such as the development of eco-friendly alternatives and smart coatings.
- Visual Summary: Using "Figure 1" to provide a "visual summary of the key aspects of surface treatment technologies for aluminum alloys in sports equipment".
Research Subjects and Scope:
The research subject is surface treatment technologies for aluminum alloys. The scope is limited to the application of these technologies in "sports equipment". The review focuses on "aluminum alloys used in sports equipment belong to the 2xxx, 6xxx, and 7xxx series", as well as cast aluminum alloys like "A356, A357, and ADC12".
5. Main Research Results:
Key Research Results:
- Aluminum Alloys in Sports Equipment: The review identifies commonly used aluminum alloys (2xxx, 6xxx, 7xxx series and cast alloys) and their applications in sports equipment, highlighting the importance of surface treatments due to corrosion factors.
- Corrosion Mechanisms: It details sport-specific corrosion factors (Table 3) and general corrosion mechanisms (pitting, intergranular corrosion) affecting aluminum alloys in sports equipment.
- Surface Treatment Technologies: The paper comprehensively reviews various surface treatment technologies:
- Chemical Conversion Coatings (CCCs): Discusses traditional chromate coatings and eco-friendly alternatives (TCCs).
- Anodizing: Covers conventional (SAA, CAA) and advanced (PEO) anodizing processes.
- PVD Coatings: Highlights their barrier protection and application in sports equipment.
- Sol-gel Coatings: Emphasizes their versatility, eco-friendliness, and functionalization potential.
- Laser Surface Modification (LSM, LSA): Showcases their ability to improve surface properties.
- Sublimation Coating: Introduces this technology for aesthetic and functional enhancements.
- Commercial Treatments: Lists notable commercial surface treatments used in the sports equipment industry (Table 5).
- Full Protection Systems: Describes multi-layer systems combining conversion coatings and organic layers for enhanced protection.
- Painting Methods: Outlines painting methods and paint types used for aluminum sports equipment.
- Comparative Analysis: Categorizes and compares surface treatments (chemical, electrochemical, physical) based on advantages, limitations, and applications (Table 7).
- Eco-friendly Alternatives: Evaluates eco-friendly alternatives to hexavalent chromium (Table 8).
- Emerging Trends: Highlights trends in self-healing coatings, nanotechnology integration, and sustainable treatments.
Data Interpretation:
The review interprets the data by:
- Categorizing and comparing different surface treatment methods based on their mechanisms, advantages, and limitations.
- Analyzing the effectiveness of each method in enhancing corrosion resistance, wear resistance, and other relevant properties.
- Highlighting the trade-offs between performance, cost, environmental impact, and industrial applicability of different technologies.
- Identifying trends and future directions in the field, emphasizing the shift towards eco-friendly and high-performance solutions.
Figure Name List:
- Figure 1: Overview of surface treatment technologies for aluminum alloys in sports equipment.
- Figure 2: Die dimension design of bicycle pedal forming and the final product [34].
- Figure 3: Microstructures of A7075 composites with different Ni@Al2O3(p) contents [45]. (a) 0 wt%, (b) 0.5 wt%, (c) 1.5 wt%, and (d) 2.5 wt%.
- Figure 4: Microstructure of semi-solid A356 (a) before and (b) after ultrasonic vibration [46].
- Figure 5: Typical morphologies of anodized layers grown in H2SO4 (a), cross-section observations for aluminum alloys 1050 (b), 7175 (c) and (d), and 2618 (e) and (f) [90].
- Figure 6: Scheme for the corrosion mechanism of the coating [100].
- Figure 7: A growth and 3D structure model of the PEO coating at different stages: (a) breakdown of dielectric film under plasma discharges; (b) formation of PEO coating with open pores; (c) initial formation of three-layer structure; and (d) further evolution of three-layer structure [102].
- Figure 8: SEM images of coatings cross-section for coating chemical composition: (a) AlCrN PVD coating; (b) AITIN/Si3N4 PVD nanocomposite; and (c) AICrN/Si3N4 PVD nanocomposite coating [104].
- Figure 9: Chemical interaction of the sol-gel coating and SBA-15-NH2 nanostructure [109].
- Figure 10: Schematic of laser transformation hardening [111].
- Figure 11: Manufacturing sequence of aluminum extrusions for sports applications.
![Figure 2
Die dimension design of bicycle pedal forming and the final product [34].](https://castman.co.kr/wp-content/uploads/image-526-1024x353.webp)
![Figure 3
Microstructures of A7075 composites with different Ni@Al2O3(p) contents [45]. (a) 0 wt%, (b) 0.5 wt%, (c) 1.5 wt%, and (d) 2.5 wt%.](https://castman.co.kr/wp-content/uploads/image-527-1024x910.webp)
![Figure 4
Microstructure of semi-solid A356 (a) before and (b) after ultrasonic vibration [46].](https://castman.co.kr/wp-content/uploads/image-528-1024x369.webp)
![Figure 5
Typical morphologies of anodized layers grown in H2SO4 (a), cross-section observations for aluminum alloys 1050 (b), 7175 (c) and (d), and 2618 (e) and (f) [90].](https://castman.co.kr/wp-content/uploads/image-529-884x1024.webp)
![Figure 6
Scheme for the corrosion mechanism of the coating [100].](https://castman.co.kr/wp-content/uploads/image-530-771x1024.webp)
![Figure 7
A growth and 3D structure model of the PEO coating at different stages: (a) breakdown of dielectric film under plasma discharges; (b) formation of PEO coating with open pores; (c) initial formation of three-layer structure; and (d) further evolution of three-layer structure [102].](https://castman.co.kr/wp-content/uploads/image-531-1024x751.webp)
![Figure 8
SEM images of coatings cross-section for coating chemical composition: (a) AlCrN PVD coating; (b) AlTiN/Si3N4 PVD nanocomposite; and (c) AlCrN/Si3N4 PVD nanocomposite coating [104].](https://castman.co.kr/wp-content/uploads/image-532-1024x277.webp)
![Figure 9
Chemical interaction of the sol–gel coating and SBA-15-NH2 nanostructure [109].](https://castman.co.kr/wp-content/uploads/image-533-1024x608.webp)
![Figure 10
Schematic of laser transformation hardening [111].](https://castman.co.kr/wp-content/uploads/image-534-png.webp)

6. Conclusion:
Summary of Main Results:
The review concludes that significant advancements have been made in surface treatment technologies for aluminum alloys in sports equipment. Eco-friendly alternatives to hexavalent chromium CCCs, advanced anodizing techniques like PEO, PVD coatings, sol-gel coatings, and laser surface modification show great promise. Multi-layer protection systems and specialized commercial treatments are also effective. However, challenges remain in long-term durability, scalability, cost-effectiveness, and industrial implementation of advanced treatments.
Academic Significance of the Research:
This review provides a comprehensive overview of the current state of surface treatment technologies for aluminum alloys in sports equipment. It synthesizes findings from diverse research areas, offering valuable insights into the mechanisms, performance, and trends in this field. The categorization and comparative analysis of different treatment methods contribute to a deeper understanding of their relative merits and limitations.
Practical Implications:
The review offers practical guidance for sports equipment manufacturers in selecting appropriate surface treatments for aluminum alloys. It highlights the availability of eco-friendly alternatives and advanced technologies that can enhance the performance, durability, and sustainability of sports equipment. The discussion of commercial treatments and full protection systems provides insights into industrially relevant solutions.
Limitations of the Research
As a review article, this paper is limited by the scope of the reviewed literature. It relies on existing research and does not present new experimental data. The depth of analysis for each technology is necessarily limited by the breadth of the review. The review also acknowledges the ongoing challenges in industrial implementation and cost-effectiveness, suggesting areas where further research and development are needed.
7. Future Follow-up Research:
- Directions for Follow-up Research
Future research should focus on:- Development and optimization of "smart and self-healing coatings" to enhance durability and extend equipment lifespan.
- Further optimization of surface treatment processes to improve "corrosion resistance and mechanical properties".
- Industrial implementation of advanced technologies in a "cost-effective and sustainable manner".
- Improving the "performance of eco-friendly alternatives" to hexavalent chromium and optimizing their "production processes for large-scale industrial implementation".
- Areas Requiring Further Exploration
Further exploration is needed in:- Long-term performance and durability testing of advanced surface treatments in real-world sports environments.
- Scalability and cost-effectiveness analysis of emerging technologies for industrial production.
- Environmental impact assessment of different surface treatment processes and materials.
- Development of standardized testing methods for evaluating the performance of surface treatments for sports equipment.
8. References:
- [1] Kumari, P. and M. Lavanya. Plant extracts as corrosion inhibitors for aluminum alloy in NaCL environment - recent review. Journal of the Chilean Chemical Society, Vol. 67, No. 2, 2022 Jun, pp. 5490-5495.
- [2] Peltier, F. and D. Thierry. Review of Cr-free coatings for the corrosion protection of aluminum aerospace alloys. Coatings, Vol. 12, No. 4, 2022, id. 518.
- [3] Chen, J. Surface engineered light alloys for sports equipment. Surface engineering of light alloys, Elsevier, Cambridge, 2010, pp. 549-567.
- [4] Cicero, S., R. Lacalle, R. Cicero, D. Fernández, and D. Méndez. Analysis of the cracking causes in an aluminium alloy bike frame. Engineering Failure Analysis, Vol. 18, No. 1, 2011 Jan 1, pp. 36-46.
- [5] Cartner, J. L., W. O. Haggard, J. L. Ong, and J. D. Bumgardner. Stress corrosion cracking of an aluminum alloy used in external fixation devices. Journal of Biomedical Materials Research Part B: Applied Biomaterials, Vol. 86B, No. 2, 2008, pp. 430-437.
- [6] Kuchariková, L., T. Liptáková, E. Tillová, D. Kajánek, and E. Schmidová. Role of chemical composition in corrosion of aluminum alloys. Metals, Vol. 8, No. 8, 2018 Aug, id. 581.
- [7] Adams, F. V., S. O. Akinwamide, B. Obadele, and P. A. Olubambi. Comparison study on the corrosion behavior of aluminum alloys in different acidic media. Materials Today: Proceedings, Vol. 38, 2021 Jan, pp. 1040-1043.
- [8] Saleema, N., D. K. Sarkar, R. W. Paynter, D. Gallant, and M. Eskandarian. A simple surface treatment and characterization of AA 6061 aluminum alloy surface for adhesive bonding applications. Applied Surface Science, Vol. 261, 2012 Nov, pp. 742-748.
- [9] Wagner, L. Mechanical surface treatments on titanium, aluminum and magnesium alloys. Materials Science and Engineering: A, Vol. 263, No. 2, 1999 May, pp. 210-216.
- [10] Mansfeld, F. and Y. Wang. Development of "stainless" aluminum alloys by surface modification. Materials Science and Engineering: A, Vol. 198, No. 1, 1995 Jul, pp. 51-61.
- [11] Wu, Y., J. Lin, B. E. Carlson, P. Lu, M. P. Balogh, N. P. Irish, et al. Effect of laser ablation surface treatment on performance of adhesive-bonded aluminum alloys. Surface and Coatings Technology, Vol. 304, 2016 Oct, pp. 340-347.
- [12] Feng, J., Y. Wang, X. Lin, M. Bian, and Y. Wei. SECM in situ investigation of corrosion and self-healing behavior of trivalent chromium conversion coating on the zinc. Surface and Coatings Technology, Vol. 459, 2023 Apr, id. 129411.
- [13] Sun, W., G. Bian, L. Jia, J. Pai, Z. Ye, N. Wang, et al. Study of trivalent chromium conversion coating formation at solution - metal interface. Metals, Vol. 13, No. 1, 2023, id. 93.
- [14] Paz Martínez-Viademonte, M., S. T. Abrahami, T. Hack, M. Burchardt, and H. Terryn. A review on anodizing of aerospace aluminum alloys for corrosion protection. Coatings, Vol. 10, No. 11, 2020, id. 1106.
- [15] Wang, S., X. Liu, X. Yin, and N. Du. Influence of electrolyte components on the microstructure and growth mechanism of plasma electrolytic oxidation coatings on 1060 aluminum alloy. Surface and Coatings Technology, Vol. 381, 2020 Jan, id. 125214.
- [16] Liu, N., J. Gao, S. Tong, L. Xu, Y. Wan, and H. Sun. Improvement in corrosion resistance of micro-arc oxidation coating on PVD Ti-coated aluminum alloy 7075. International Journal of Applied Ceramic Technology, Vol. 19, No. 5, 2022, pp. 2556-2565.
- [17] Zhang, Z., F. Xue, W. Bai, X. Shi, Y. Liu, and L. Feng. Superhydrophobic surface on Al alloy with robust durability and excellent self-healing performance. Surface and Coatings Technology, Vol. 410, 2021 Mar, id. 126952.
- [18] Xavier, J. R. Experimental investigation of the hybrid epoxy-silane coating for enhanced protection against the corrosion of aluminum alloy AA7075 frame in solar cells. Macromolecular Research, Vol. 28, No. 5, 2020 May, pp. 501-509.
- [19] Xavier, J. R. and S. Srinivasan. Multilayer epoxy/GO/silane/Nb2C nanocomposite: a promising coating material for the aerospace applications. Journal of Adhesion Science and Technology, Vol. 38, No. 1, 2024, pp. 44-69.
- [20] Jeeva, N., K. Thirunavukkarasu, and J. R. Xavier. Multilayer functional polyurethane nanocomposite coating containing graphene oxide and silanized zirconium nitride for the protection of aluminum alloy structures in aerospace industries. Journal of Materials Engineering and Performance, 2024 Mar 22 [cited 2024 Jul 26].
- [21] Xavier, J. R., S. P. Vinodhini, and R. Ganesan. Innovative nanocomposite coating for aluminum alloy: superior corrosion resistance, flame retardancy, and mechanical strength for aerospace applications. Journal of Materials Science, Vol. 59, No. 27, 2024 Jul, pp. 12830-12861.
- [22] Alavala, C. R. Micromechanics of thermoelastic behavior of AA2024/MgO metal matrix composites. International Journal of Advanced Technology in Engineering and Science, Vol. 4, No. 1, 2016, pp. 33-40.
- [23] Muthusamy, S. and G. Pandi. Investigation of mechanical and corrosion properties of AA2024-B4C-TiC hybrid metal matrix composites. Surface Review and Letters, Vol. 25, No. 5, 2018 Jul, id. 1850109.
- [24] Fan, Y. Review on plastic deformation of 2024 aluminum alloy for sports equipment. Aging and Application of Synthetic Materials, Vol. 50, No. 4, 2021 Aug, pp. 189-192.
- [25] Choi, J. S., Y. G. Jin, H. C. Lee, and Y. T. Im. High strength bolt manufacturing of ultra-fine grained aluminium alloy 6061. Materials Transactions, Vol. 52, No. 2, 2011, pp. 173-178.
- [26] Leng, B., Y. Xue, J. Li, J. Qi, A. Yi, and Q. Zhao. A critical review of anti-corrosion chemical surface treatment of aluminum alloys used for sports equipment. Crystals, Vol. 14, No. 1, 2024, id. 101.
- [27] Iskandar, R., D. Sawitri, R. Hantoro, I. R. Zulkifli, and Y. Pratama. Analysis of dynamics mechanical properties of electric bike frames using finite element analysis (FEA). AIP Conference Proceedings, Vol. 2384, No. 1, 2021 Dec, id. 070005.
- [28] Harvey, T. G. Cerium-based conversion coatings on aluminium alloys: a process review. Corrosion Engineering, Science and Technology, Vol. 48, No. 4, 2013 Jun, pp. 248-269.
- [29] Wibowo, H., M. Mujiyono, R. Asnawi, F. Arifin, and T. Tafakur. Finite element simulation of A356 and A6061 aluminum combination bicycle elements to optimize weight of frame, AIP Publishing, Yogyakarta, 2023.
- [30] Suyitno, S. and U. A. Salim. Fabrication of bicycle frame of A356 aluminum alloys by using sand casting. Applied Mechanics and Materials, Vol. 758, 2015, pp. 131-135.
- [31] Rosso, M., I. Peter, and F. Calosso. Development and setting of a new system for advanced rheocast components. American Institute of Physics, Belfast, 2011, pp. 1470-1475.
- [32] Hollaus, B., J. C. Volmer, and T. Fleischmann. Cadence detection in road cycling using saddle tube motion and machine learning. Sensors, Vol. 22, No. 16, 2022, id. 6140.
- [33] Bansal, R. and B. Altaf. Lightweight, cost-effective, and environmentally friendly materials for a mountain bicycle frame during high-impact riding: A comparative analysis of traditional aluminum, aluminum 6013, and a BioMid Fiber™™ composite. Material Science, Vol. 5, No. 2, 2023, id. 22.
- [34] Chen, D. C., J. G. Lin, W. H. Ku, and J. R. Shiu. Optimal process conditions for the manufacture of aluminum alloy bicycle pedals. Advances in Mechanical Engineering, Vol. 6, 2014 Jan, id. 601253.
- [35] Wang, Z. and D. Yu. Application of aluminum in sports equipment in China. Aluminium Fabrication, Vol. 1, 2018 Jan, pp. 4-8.
- [36] Bajer, J., S. Zaunschirm, B. Plank, M. Šlapáková, L. Bajtošová, M. Cieslar, et al. Kirkendall effect in twin-roll cast AA 3003 aluminum alloy. Crystals, Vol. 12, No. 5, 2022 May, id. 607.
- [37] Bao, S., A. Kvithyld, G. A. Bjørlykke, and K. Sandaunet. Recycling of aluminum from aluminum food tubes. In: Light metals, S. Broek, ed., Springer Nature Switzerland, Cham, 2023, pp. 960-966.
- [38] Stahl, T., S. Falk, A. Rohrbeck, S. Georgii, C. Herzog, A. Wiegand, et al. Migration of aluminum from food contact materials to food – a health risk for consumers? Part I of III: exposure to aluminum, release of aluminum, tolerable weekly intake (TWI), toxicological effects of aluminum, study design, and methods. Environmental Sciences Europe, Vol. 29, No. 1, 2017 Dec, pp. 1-8.
- [39] Soni, M. G., S. M. White, W. G. Flamm, and G. A. Burdock. Safety evaluation of dietary aluminum. Regulatory Toxicology and Pharmacology, Vol. 33, No. 1, 2001 Feb, pp. 66-79.
- [40] Stahl, T., S. Falk, H. Taschan, B. Boschek, and H. Brunn. Evaluation of human exposure to aluminum from food and food contact materials. European Food Research and Technology, Vol. 244, No. 12, 2018 Dec, pp. 2077-2084.
- [41] Majeed, T., Y. Mehta, and A. N. Siddiquee. Precipitation-dependent corrosion analysis of heat treatable aluminum alloys via friction stir welding, a review. Proceedings of the Institution of Mechanical Engineers, Part C: Journal of Mechanical Engineering Science, Vol. 235, No. 24, 2021 Dec, pp. 7600-7626.
- [42] Maniam, K. K. and S. Paul. A review on the electrodeposition of aluminum and aluminum alloys in ionic liquids. Coatings, Vol. 11, No. 1, 2021 Jan, id. 80.
- [43] Dai, Y., L. Yan, and J. Hao. Review on micro-alloying and preparation method of 7xxx series aluminum alloys: progresses and prospects. Materials, Vol. 15, No. 3, 2022 Jan, id. 1216.
- [44] Huang, H., J. Niu, X. Xing, Q. Lin, H. Chen, and Y. Qiao. Effects of the shot peening process on corrosion resistance of aluminum alloy: a review. Coatings, Vol. 12, No. 5, 2022 May, id. 629.
- [45] Zhao, P. Microstructure and properties of coated particle reinforced aluminum matrix composites used in sports equipment. Casting, Vol. 71, No. 7, 2022, pp. 878-882.
- [46] Lu, C. and C. Liu. Study on microstructure and tensile properties of aluminum alloy for semi-solid sports equipment prepared by ultrasonic vibration. Casting, Vol. 70, No. 4, 2021 Apr, pp. 449-453.
- [47] Qu, H., G. Li, W. Jiang, Y. Yu, and H. Wei. Effect of Mg content on microstructure and properties of Al-6Zn-xMg-0.5Cu-0.1Zr cast aluminum alloy for sports equipment. Foundry, Vol. 71, No. 10, 2022 Oct, pp. 1256-1261.
- [48] Xusheng, L. Effect of Y content on microstructure and mechanical properties of aluminum alloy used in sports equipment. Casting Technology, Vol. 36, No. 10, 2015 Oct, pp. 2454-2456.
- [49] Zhang, J., M. Klasky, and B. C. Letellier. The aluminum chemistry and corrosion in alkaline solutions. Journal of Nuclear Materials, Vol. 384, No. 2, 2009 Feb, pp. 175-189.
- [50] Park, S. W., G. D. Han, H. J. Choi, F. B. Prinz, and J. H. Shim. Evaluation of atomic layer deposited alumina as a protective layer for domestic silver articles: Anti-corrosion test in artificial sweat. Applied Surface Science, Vol. 441, 2018 May, pp. 718-723.
- [51] Fekry, A. M., A. A. Ghoneim, and M. A. Ameer. Electrochemical impedance spectroscopy of chitosan coated magnesium alloys in a synthetic sweat medium. Surface and Coatings Technology, Vol. 238, 2014 Jan, pp. 126-132.
- [52] Wu, F., S. Zhang, and Z. Tao. Corrosion behavior of 3C magnesium alloys in simulated sweat solution. Materials and Corrosion, Vol. 62, No. 3, 2011 Mar, pp. 234-239.
- [53] Naser, S. A., A. A. Hameed, and M. A. Hussein. Corrosion behavior of some jewelries in artificial sweat. AIP Conference Proceedings, Vol. 2213, No. 1, 2020 Mar, id. 020030.
- [54] Zaid, B., D. Saidi, A. Benzaid, and S. Hadji. Effects of pH and chloride concentration on pitting corrosion of AA6061 aluminum alloy. Corrosion Science, Vol. 50, No. 7, 2008 Jul, pp. 1841-1847.
- [55] Loto, R. T. and A. Adeleke. Corrosion of aluminum alloy metal matrix composites in neutral chloride solutions. Journal of Failure Analysis and Prevention, Vol. 16, No. 5, 2016 Oct 1, pp. 874-885.
- [56] Mishra, A. K. and R. Balasubramaniam. Corrosion inhibition of aluminum alloy AA 2014 by rare earth chlorides. Corrosion Science, Vol. 49, No. 3, 2007 Mar, pp. 1027-1044.
- [57] Luo, C., S. P. Albu, X. Zhou, Z. Sun, X. Zhang, Z. Tang, et al. Continuous and discontinuous localized corrosion of a 2xxx aluminum-copper-lithium alloy in sodium chloride solution. Journal of Alloys and Compounds, Vol. 658, 2016 Feb, pp. 61-70.
- [58] Deflorian, F., S. Rossi, B. Tancon, and P. L. Bonora. Corrosion behaviour of steel ropes for snow and rockfall barriers. Corrosion Engineering, Science and Technology, Vol. 39, No. 3, 2004 Sep, pp. 250-254.
- [59] Huttunen-Saarivirta, E., V. T. Kuokkala, J. Kokkonen, and H. Paajanen. Corrosion effects of runway de-icing chemicals on aircraft alloys and coatings. Materials Chemistry and Physics, Vol. 126, No. 1, 2011 Mar, pp. 138-151.
- [60] Schoukens, I., F. Cavezza, J. Cerezo, V. Vandenberghe, V. C. Gudla, and R. Ambat. Influence of de-icing salt chemistry on the corrosion behavior of AA6016. Materials and Corrosion, Vol. 69, No. 7, 2018, pp. 881-887.
- [61] Huang, I. W., B. L. Hurley, F. Yang, and R. G. Buchheit. Dependence on temperature, pH, and Cl- in the uniform corrosion of aluminum alloys 2024-T3, 6061-T6, and 7075-T6. Electrochimica Acta, Vol. 199, 2016 May, pp. 242-253.
- [62] Xavier, J. R., S. P. Vinodhini, and B. Ramesh. Optimizing aluminum alloy performance for marine superstructures: Advanced nanocomposite coating for enhanced corrosion resistance, flame retardancy, and mechanical strength. Polymer Degradation and Stability, Vol. 227, 2024 Sep, id. 110847.
- [63] Shen, Y., Y. Dong, Y. Yang, Q. Li, H. Zhu, W. Zhang, et al. Study of pitting corrosion inhibition effect on aluminum alloy in seawater by biomineralized film. Bioelectrochemistry, Vol. 132, 2020 Apr, id. 107408.
- [64] Wan, Y., L. Li, Y. Jin, Y. Li, and X. Zhu. Pitting corrosion behavior and mechanism of 5083 aluminum alloy based on dry-wet cycle exposure. Materials and Corrosion, Vol. 74, No. 4, 2023, pp. 608-621.
- [65] Berlanga-Labari, C., M. V. Biezma-Moraleda, and P. J. Rivero. Corrosion of cast aluminum alloys: a review. Metals, Vol. 10, No. 10, 2020, id. 1384.
- [66] Qin, J., Z. Li, M. Y. Ma, D. Q. Yi, and B. Wang. Diversity of intergranular corrosion and stress corrosion cracking for 5083 Al alloy with different grain sizes. Transactions of Nonferrous Metals Society of China, Vol. 32, No. 3, 2022 Mar, pp. 765-777.
- [67] Mondou, E., A. Proietti, C. Charvillat, C. Berziou, X. Feaugas, D. Sinopoli, et al. Understanding the mechanisms of intergranular corrosion in 2024 Al alloy at the polycrystal scale. Corrosion Science, Vol. 221, 2023 Aug, id. 111338.
- [68] Peng, C., G. Cao, T. Gu, C. Wang, Z. Wang, and C. Sun. The corrosion behavior of the 6061 Al alloy in simulated Nansha marine atmosphere. Journal of Materials Research and Technology, Vol. 19, 2022 Jul, pp. 709-721.
- [69] Fujii, T., T. Sawada, and Y. Shimamura. Nucleation of stress corrosion cracking in aluminum alloy 6061 in sodium chloride solution: Mechanical and microstructural aspects. Journal of Alloys and Compounds, Vol. 938, 2023 Mar, id. 168583.
- [70] Srinivasan, P. B., W. Dietzel, R. Zettler, J. F. dos Santos, and V. Sivan. Stress corrosion cracking susceptibility of friction stir welded AA7075-AA6056 dissimilar joint. Materials Science and Engineering: A, Vol. 392, No. 1, 2005 Feb, pp. 292-300.
- [71] Dwivedi, P., A. N. Siddiquee, and S. Maheshwari. Issues and requirements for aluminum alloys used in aircraft components: state of the art. Russian Journal of Non-Ferrous Metals, Vol. 62, No. 2, 2021 Mar, pp. 212-225.
- [72] Samuel, A. U., A. O. Araoyinbo, R. R. Elewa, and M. B. Biodun. Effect of machining of aluminium alloys with emphasis on aluminium 6061 alloy - A review. IOP Conference Series: Materials Science and Engineering, Vol. 1107, No. 1, 2021 Apr, id. 012157.
- [73] Khan, H. M., G. Özer, M. S. Yilmaz, and E. Koc. Corrosion of additively manufactured metallic components: A review. Arabian Journal for Science and Engineering, Vol. 47, No. 5, 2022 May, pp. 5465-5490.
- [74] Renner, P., S. Jha, Y. Chen, A. Raut, S. G. Mehta, and H. Liang. A review on corrosion and wear of additively manufactured alloys. Journal of Tribology, Vol. 143, 2021 Apr [cited 2024 Jun 25], id. 050802.
- [75] Liew, Y., C. Örnek, J. Pan, D. Thierry, S. Wijesinghe, and D. J. Blackwood. Towards understanding micro-galvanic activities in localised corrosion of AA2099 aluminium alloy. Electrochimica Acta, Vol. 392, 2021 Oct, id. 139005.
- [76] Tian, W., B. Chao, X. Xiong, and Z. Li. Effect of surface roughness on pitting corrosion of 2A12 aluminum alloy. International Journal of Electrochemical Science, Vol. 13, No. 3, 2018 Mar, pp. 3107-3123.
- [77] Ly, R., K. T. Hartwig, and H. Castaneda. Effects of strain localization on the corrosion behavior of ultra-fine grained aluminum alloy AA6061. Corrosion Science, Vol. 139, 2018 Jul, pp. 47-57.
- [78] Zhao, Z., J. Liu, and A. Siddiq. Plastic softening induced by high-frequency vibrations accompanying uniaxial tension in aluminum. Nanomaterials, Vol. 12, No. 7, 2022 Jan, id. 1239.
- [79] Zhang, L., W. Bian, K. Fu, X. Dai, H. Wang, and J. Wang. Improvement of mechanical properties and microstructure of wire arc additive manufactured 2319 aluminum alloy by mechanical vibration acceleration. Materials Characterization, Vol. 208, 2024 Feb, id. 113672.
- [80] Pathak, S. S., M. D. Blanton, S. K. Mendon, and J. W. Rawlins. Investigation on dual corrosion performance of magnesium-rich primer for aluminum alloys under salt spray test (ASTM B117) and natural exposure. Corrosion Science, Vol. 52, No. 4, 2010 Apr, pp. 1453-1463.
- [81] Akande, I. G., M. A. Fajobi, O. A. Odunlami, and O. O. Oluwole. Exploitation of composite materials as vibration isolator and damper in machine tools and other mechanical systems: A review. Materials Today: Proceedings, Vol. 43, 2021 Jan, pp. 1465-1470.
- [82] Meng, X. K., H. Wang, W. S. Tan, J. Cai, J. Z. Zhou, and L. Liu. Gradient microstructure and vibration fatigue properties of 2024-T351 aluminium alloy treated by laser shock peening. Surface and Coatings Technology, Vol. 391, 2020 Jun, id. 125698.
- [83] Qi, J., J. Światowska, P. Skeldon, and P. Marcus. Chromium valence change in trivalent chromium conversion coatings on aluminium deposited under applied potentials. Corrosion Science, Vol. 167, 2020 May, id. 108482.
- [84] Kim, M., L. N. Brewer, and G. W. Kubacki. Microstructure and corrosion resistance of chromate conversion coating on cold sprayed aluminum alloy 2024. Surface and Coatings Technology, Vol. 460, 2023 May, id. 129423.
- [85] Oki, M., A. A. Adediran, P. P. Ikubanni, O. S. Adesina, A. A. Adeleke, S. A. Akintola, et al. Corrosion rates of green novel hybrid conversion coating on aluminium 6061. Results in Engineering, Vol. 7, 2020 Sep, id. 100159.
- [86] Quarto, F. D., M. Santamaria, N. Mallandrino, V. Laget, R. Buchheit, and K. Shimizu. Structural analysis and photocurrent spectroscopy of CCCs on 99.99% aluminum. Journal of the Electrochemical Society, Vol. 150, No. 10, 2003 Aug, id. B462.
- [87] Campestrini, P., H. Terryn, J. Vereecken, and J. H. W. de Wit. Chromate conversion coating on aluminum alloys: III. Corrosion protection. Journal of the Electrochemical Society, Vol. 151, No. 6, 2004 May 6, id. B370.
- [88] Janaki, G. B. and J. R. Xavier. Evaluation of bi-functionalized alumina-epoxy nanocomposite coatings for improved barrier and mechanical properties. Surface and Coatings Technology, Vol. 405, 2021 Jan, id. 126549.
- [89] Zhang, J. S., X. H. Zhao, Y. Zuo, and J. P. Xiong. The bonding strength and corrosion resistance of aluminum alloy by anodizing treatment in a phosphoric acid modified boric acid/sulfuric acid bath. Surface and Coatings Technology, Vol. 202, No. 14, 2008 Apr, pp. 3149-3156.
- [90] Veys-Renaux, D., N. Chahboun, and E. Rocca. Anodizing of multiphase aluminium alloys in sulfuric acid: in-situ electrochemical behaviour and oxide properties. Electrochimica Acta, Vol. 211, 2016 Sep, pp. 1056-1065.
- [91] Xavier, J. R. Investigation of anticorrosion, flame retardant and mechanical properties of polyurethane/GO nanocomposites coated AJ62 Mg alloy for aerospace/automobile components. Diamond and Related Materials, Vol. 136, 2023 Jun, id. 110025.
- [92] Lin, M. Y., P. S. Hsiao, H. H. Sheu, C. C. Chang, M. Tsai, D. S. Wuu, et al. Improving the corrosion resistance of 6061 aluminum alloy using anodization and Nickel-Cobalt based sealing treatment. International Journal of Electrochemical Science, Vol. 16, No. 10, 2021 Oct, id. 211053.
- [93] Karagianni, B. and I. Tsangaraki-Kaplanoglou. N-heterocyclic organic compounds as additives in the AC coloring of anodized aluminum from Nickel sulfate solutions - Part I: Effect on color intensity & uniformity of the probes. Plating and Surface Finishing, Vol. 83, 1996, pp. 73-76.
- [94] Giles, C. H. Dyeing anodized aluminium: A review. Transactions of the IMF, Vol. 57, No. 1, 1979 Jan, pp. 48-52.
- [95] Akolkar, R., Y. M. Wang, and H. H. (Harry) Kuo. Kinetics of the electrolytic coloring process on anodized aluminum. Journal of Applied Electrochemistry, Vol. 37, No. 2, 2007 Feb 1, pp. 291-296.
- [96] Critchlow, G. W., K. A. Yendall, D. Bahrani, A. Quinn, and F. Andrews. Strategies for the replacement of chromic acid anodising for the structural bonding of aluminium alloys.
9. Copyright:
- This material is "Shaozhou Chen"'s paper: Based on "Advancements in surface treatments for aluminum alloys in sports equipment".
- Paper Source: https://doi.org/10.1515/rams-2024-0065
This material was summarized based on the above paper, and unauthorized use for commercial purposes is prohibited.
Copyright © 2025 CASTMAN. All rights reserved.