This article introduces the paper "Advanced casting technologies for lightweight automotive applications".
1. Overview:
- Title: Advanced casting technologies for lightweight automotive applications
- Authors: Alan A. Luo, Anil K. Sachdev, Bob R. Powell
- Publication Year: 2010
- Journal/Conference: China Foundry, Vol.7 No.4
- Keywords: lightweight, aluminum alloy, magnesium alloy, die casting
2. Background:
Lightweighting in the automotive industry is crucial for improving fuel efficiency. Aluminum and magnesium castings have been utilized for this purpose for a considerable time, gaining significant traction since the mid-1970s. Aluminum castings offer a 30-50% mass reduction compared to steel, while magnesium castings provide a 40-60% reduction. However, existing aluminum and magnesium alloys presented limitations in terms of wear resistance, creep resistance, and high strength/ductility combinations. Furthermore, conventional high-pressure die casting processes suffered from porosity issues. Therefore, advancements in alloy development and casting processes were necessary to further enhance lightweighting efforts in the automotive sector.
3. Research Objectives and Questions:
This research aims to provide a comprehensive overview of the latest alloy and process developments in aluminum and magnesium casting technologies for lightweight automotive applications. The key research questions are:
- What are the newly developed aluminum and magnesium alloys suitable for automotive applications, and what are their specific properties?
- What advanced casting processes enhance the production of high-quality lightweight components, and what are their advantages over conventional methods?
4. Methodology:
This study is based on a comprehensive literature review of recent advancements in aluminum and magnesium casting technologies. The analysis encompasses the development of novel alloys, advanced casting processes such as vacuum-assisted die casting (VADC), high-vacuum die casting (HVDC), super-vacuum die casting (SVDC), and low-pressure die casting (LPC). Real-world automotive applications of these technologies are examined to assess their practical effectiveness.
5. Main Findings:
- Aluminum Alloy Development: Near-eutectic Al-Si alloys (e.g., GM396) were developed to improve wear resistance without relying on the wear resistance of primary Si particles, thereby addressing machinability challenges associated with hypereutectic Al-Si alloys.
- Magnesium Alloy Development: High strength/ductility magnesium alloys (e.g., AM70) were developed. Furthermore, research focused on enhancing creep resistance in magnesium alloys through the addition of elements like Ca, Sr, RE, and Si. (See Fig. 1, Fig. 2)
- Casting Process Development: To mitigate porosity issues in high-pressure die casting, VADC, HVDC, and SVDC technologies were developed. (See Table 1, Fig. 4) LPC enabled the production of thick-walled, near-net-shape components with minimal porosity. (See Table 2, Table 3, Fig. 5)
- Overcasting Technology: Overcasting enabled the creation of mixed-material designs by casting one material onto a pre-existing component (e.g., casting magnesium onto a steel tube), resulting in designs with enhanced structural integrity and mass reduction. This technology found application in engine cradles and instrument panel beams. (See Fig. 6, Fig. 7)
- Figure List:
- Figure 1: Tensile properties of Mg-Al-Mn alloys in the as-cast condition (gravity permanent mold casting).
- Figure 2: TEM micrograph showing the formation of (Mg, Al)2Ca phase in AX53 (Mg-5%AI-3%Ca) alloy (high pressure die casting).
- Figure 3: Advanced simulation for high-pressure die casting (Mg cradle for Corvette Z06).
- Figure 4: Casting surfaces after T4 treatment: (a) conventional die casting; and (b) vacuum-assisted die casting.
- Figure 5: (a) Hollow aluminum casting; and (b) welded engine cradle for Cadillac CTS.
- Figure 6: Magnesium die cast instrument panel beam for Buick LaCrosse.
- Figure 7: Lightweight instrument panel beam of magnesium overcast onto a steel tube.
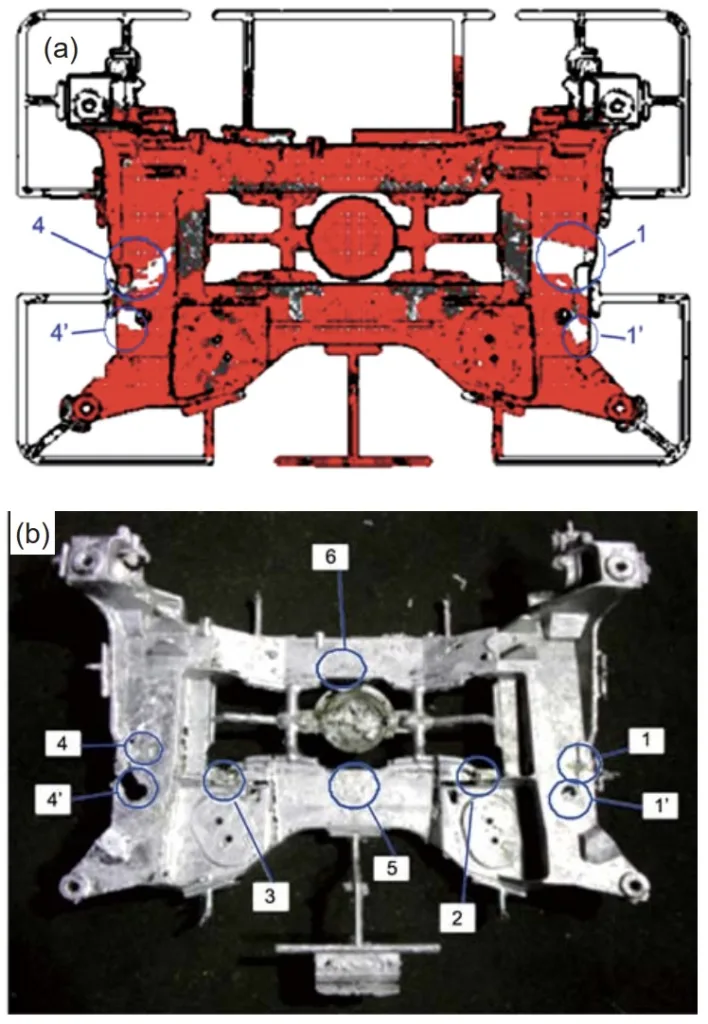
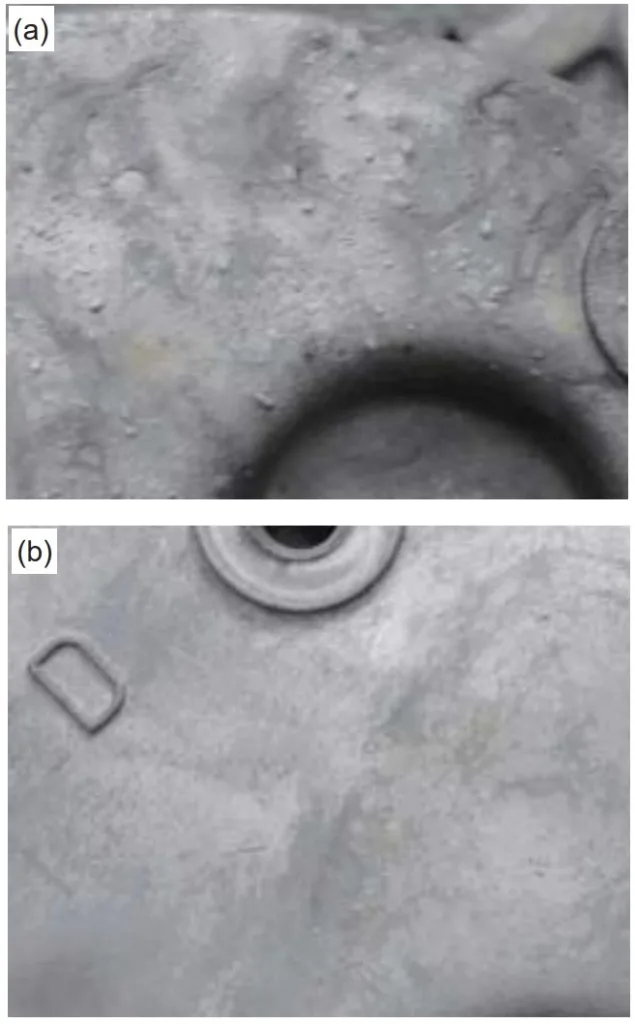
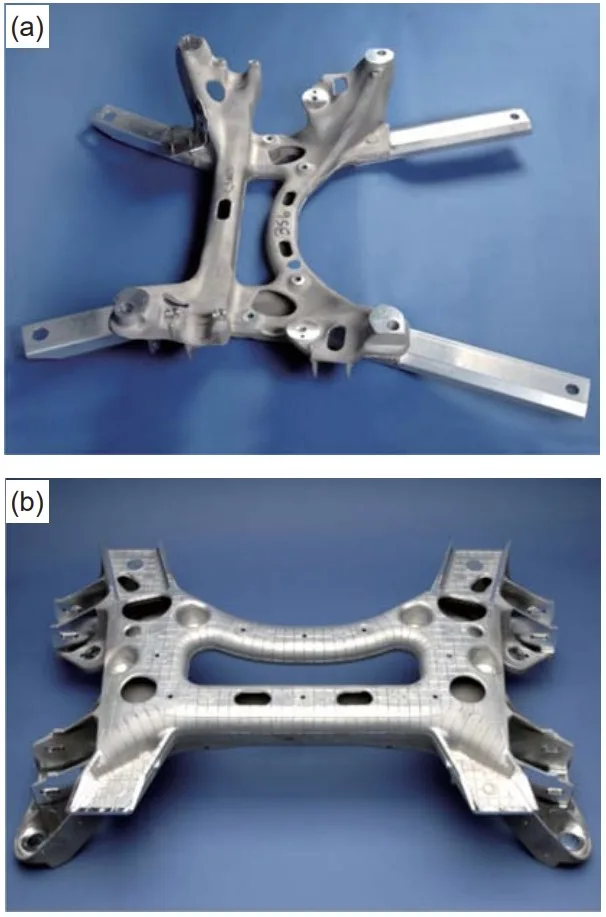
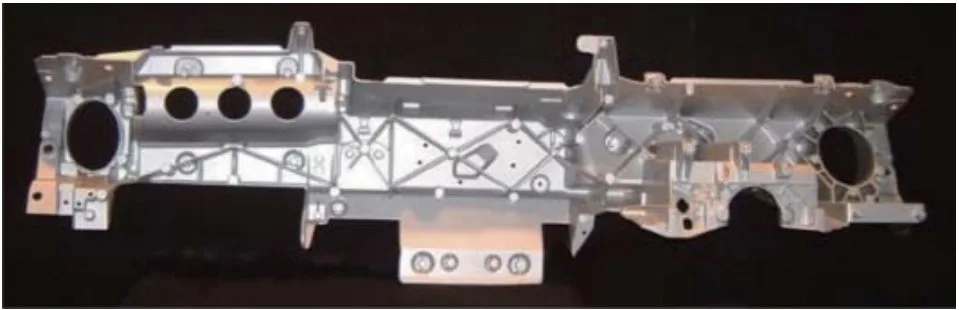
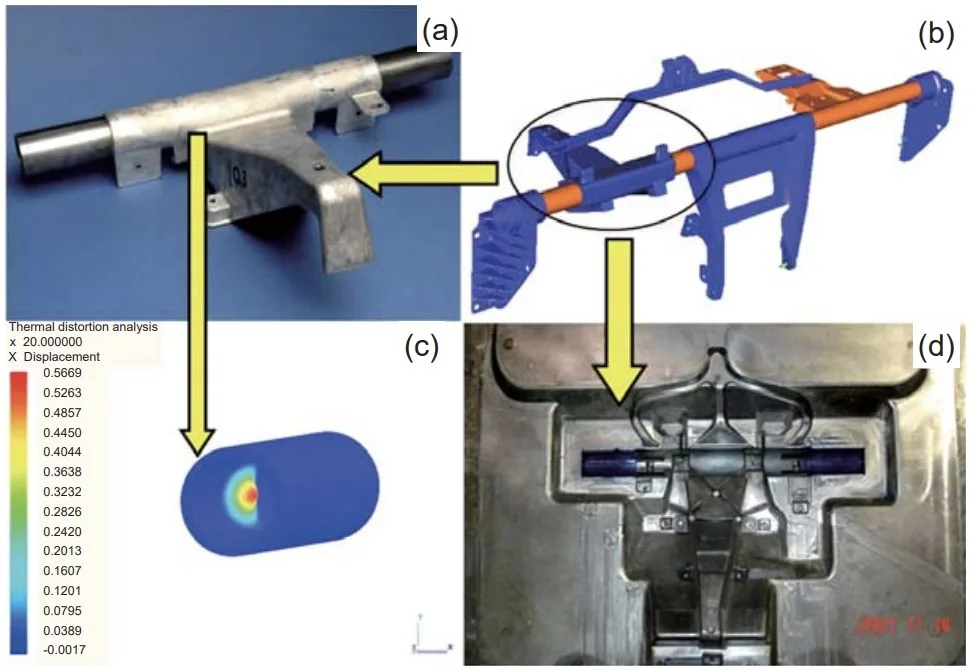
6. Conclusion and Discussion:
This research highlights significant advancements in aluminum and magnesium casting technologies for lightweight automotive applications. The development of new alloys and advanced casting processes has enabled the production of lighter, stronger, and more durable automotive components. Vacuum die casting and low-pressure die casting effectively address porosity issues, while overcast technology allows for innovative multi-material designs. However, some of these advanced techniques may entail higher costs compared to conventional methods.
7. Future Research:
- Development of alloys with further enhanced mechanical properties (strength, ductility, creep resistance).
- Cost optimization and scalability improvements in advanced casting processes.
- Expansion of overcast technology to a broader range of automotive components.
- Research into joining techniques and corrosion resistance in multi-material designs.
8. References:
- [1] Taub A I, Krajewski P E, Luo A A, and Owens J N. The Evolution of Technology for Materials Processing over the Last 50 Years: The Automotive Example. JOM, 2007, 59 (2): 48-57.
- [2] National Research Council (U.S.). Effectiveness and Impact of Corporate Average Fuel Economy (CAFE) Standards. Washington, D.C.: National Academy Press, 2001: 5A-4.
- [3] Malen D E and Reddy K. Preliminary Vehicle Mass Estimation using Empirical Subsystem Infl uence Coeffi cients. Auto Steel Partnership, May 2007 (Revised June 26, 2007), www.a-p.net.
- [4] Bjelkengren C. The Impact of Mass Decompounding on Assessing the Value of Vehicle Lightweighting. Thesis for Master of Science in Engineering Systems, MIT, June 2008.
- [5] Verbrugge M W, et al. Mass Decompounding and Vehicle Lightweighting. Materials Science Forum, 2009, 618-619: 411-418.
- [6] Kneisler F J, Martens D A, and Midgley R W. Design and Development of In-Line Overhead Camshaft 4-Cycle Engine for Vega 2300. Society of Automotive Engineers, Technical Paper No. 710147, 1971.
- [7] Das S, Perry T, and Biswas S K. Effect of Surface Etching on the Lubricated Sliding Wear of an Eutectic Aluminum-Silicon Alloy. Tribology Letters, 2006, 21(3): 193-204.
- [8] Shin J, Kim D, Hwang I, and Oh S. Casting Technology and Engine Development for Sleeveless Cylinder Block Using GM396 Material. In: Proceedings of Korean Society of Automotive Engineers Annual Meeting, Seoul, Korea, Nov. 2009.
- [9] Luo A A and Sachdev A K. Microstructure and Mechanical Properties of Mg-Al-Mn and Mg-Al-Sn Alloys. Magnesium Technology 2009, TMS, Warrendale, PA, 2009: 437-443.
- [10] Luo A A. Recent Magnesium Alloy Development for Elevated Temperature Applications. International Materials Reviews, 2004, 49(1): 13-30.
- [11] Powell B R, Rezhets V, Balogh M and Waldo R. In: Magnesium Technology 2001 (ed. Hryn J N). Warrendale, PA: The Minerals, Metals and Materials Society, 2001: 175-181.
- [12] Luo A A, Balogh M P and Powell B R. Creep and Microstructure of Magnesium-Aluminum-Calcium Based Alloys. Metall. & Mater. Trans. A, 2002, 33A: 567-574.
- [13] Pekguleryuz M O and Baril E. Development of Creep Resistant Mg-Al-Sr Alloys. Magnesium Technology 2001, TMS, Warrendale, PA, 2001: 119-125.
- [14] Greiner J, Doerr C, Nauerz H, and Graeve M. The ‘New 7G-TRONIC’ of Mercedes-Benz: Innovative Transmission Technology for Better Driving Performance, Comfort, and Fuel Economy. Society of Automotive Engineers Technical Paper No. 2004-01-0649, 2004.
- [15] Hoeschl M, Wagener W, and Wolfe J. BMW’s MagnesiumAluminum Composite Crankcase: State-of-the-Art Light Metal Casting and Manufacturing. Society of Automotive Engineers, Technical Paper No. 2006-01-0069, 2006.
- [16] Quinn J F and Powell B R. Magnesium Powertrain Cast Components Project
- [EB/OL]. http://annualmeritreview.energy. gov on May 21, 2009.
- [17] Aragones J, Goundan K, Kolp S, Osborne R, Ouimet L and Pinch W. Development of the 2006 Corvette Z06 Structural Cast Magnesium Crossmember. Society of Automotive Engineers Technical Paper No. 2005-01-0340, 2005.
- [18] Vinarcik E J. High Integrity Die Casting Processes. New York, John Wiley & Sons, Inc., 2003.
- [19] Luo A A, Fu P H, Yu Y D, Jiang H Y, Peng L M, Zhai C Q, Sachdev A K. Vacuum-Assisted High Pressure Die Casting of AZ91 Magnesium Alloy. North American Die Casting Association Transactions, T08-083, 2008.
- [20] Brown Z, Szymanowski B, Musser M, Saha D, Seaver S. Manufacturing of Thin Wall Structural Automotive Components Through High Vacuum Die Casting Technology. In: Proc. 2007 Metal Casting Congress,15-18, 2007, Houston, TX, USA.
- [21] Koch H and Franke A J. Ductile Pressure Die Castings for Automotive Application. Automotive Alloys, TMS, Warrendale, PA, 1997: 185-198.
- [22] Brown Z, Luo A A, Musser M, Ouimet L J, Sadayappan K, Zindel J, Beals R. Development of Super-Vacuum Die Casting Process for Magnesium Alloys. North American Die Casting Association Transactions, T09-043, 2009.
- [23] Sahoo M, Weiss D and Marlatt M. Factors Affecting Successful Permanent Mold Casting of Magnesium. In: Proc. International Conference on Permanent Mold Casting of Al and Mg. Dallas, Texas, USA, February 11-12, 2008.
- [24] Woycik G. Low Pressure Casting of Magnesium Alloys for Automotive Components. Presentation at the 111th Metalcasting Congress, Houston, TX, May 15-18, 2007.
- [25] Westengen H, Holta O. Low Pressure Permanent Die Casting of Magnesium – Recent Developments. Foundry Trade Journal, 1989,163(3399): 738-742.
- [26] Robison S T, Weiss D, Gegel G, Woycik G, Marlatt M and Cox B. Magnesium Casting Process Development: Designing an Engine Cradle for Magnesium Semi-Permanent Mold Casting. AFS Paper 05-217, Schaumburg, IL: American Foundry Society, 2005.
- [27] Luo A A, Fu P H, Yu Y D, Peng L M, Jiang H Y, Zhai C Q and Sachdev A K. Low Pressure Die Casting of AZ91 and AM50 Magnesium Alloys. AFS Paper 08-147, Schaumburg, IL: American Foundry Society, 2007.
- [28] Luo A A and Sachdev A K. Lightweight Hybrid Tubular/Casting Instrument Panel Beam. U.S. Patent Application, Feb 18, 2005, published on Jun 8, 2006.
- [29] Luo A A and McCune R C. Magnesium Front End Projects. US Department of Energy Automotive Lightweighting Materials, FY 2009 Progress Report.
- [30] Luo A A, Nyberg E A, Sadayappan K and Shi W. Magnesium Front End Research and Development: A Canada-ChinaUSA Collaboration. Magnesium Technology 2008, TMS, Warrendale, PA, 2008: 3-10.
Copyright:
This summary is based on the paper "Advanced casting technologies for lightweight automotive applications" by Alan A. Luo, Anil K. Sachdev, and Bob R. Powell.
Unauthorized commercial use is prohibited.
Copyright © 2025 CASTMAN. All rights reserved.