Mingfan Qi a,∗, Yonglin Kanga, Bing Zhoua, Wanneng Liaoa, Guoming Zhua, Yangde Li b,
Weirong Li b
a School of Materials Science and Engineering, University of Science and Technology Beijing, Beijing 100083, China b Dongguan EONTEC Corporation, Ltd., Dongguan 523662, China
Abstract
A simplified process, namely forced convection stirring (FCS), was proposed to prepare four different
semisolid slurries ofAl andMg alloys.Asimple rheological high pressure die-casting (Rheo-HPDC) process
was developed by combining the FCS device with a HPDC machine. The temperature and composition
fields of the melt in the FCS process were simulated. The microstructures and mechanical properties
of the alloys formed by the FCS Rheo-HPDC were studied and compared with those formed by HPDC
and other Rheo-HPDC processes. The results showed that the FCS process can prepare slurries in which
the primary particles are fine, spherical and uniformly distributed in the matrix and the process can
effectively suppress macrosegregation. The strong convection rapidly promotes the uniformity of the
temperature and composition of the melt. Compared to HPDC and other Rheo-HPDC alloys, the alloys
formed by FCS Rheo-HPDC have an improved ultimate tensile strength, yield strength, elongation and
hardness, due to the refinement of microstructure and the decrease of porosity. Heat treatments can be
utilized to further enhance the mechanical properties of FCS Rheo-HPDC alloys.
Keywords
Forced convection stirring process, Semisolid slurries, Rheo-HPDC, Microstructure, Mechanical properties
Introduction
For the past few years, in order to provide solutions to environmental and energy issues, the importance of Al and Mg alloys as light-weight metals has been widely recognized, especially in the fields of 3C (computer, communication and consumer electronics) and automotive (Sui et al., 2015). Nowadays, high pressure die-casting (HPDC) is the process that is primarily used for manufacturing the majority of Al and Mg alloys applications, due to its low cost and high efficiency.
However, Jin et al. (2015) demonstrated that many porosities, caused by gas entrapment during the high speed mold filling, exist in HPDC parts. Cáceres and Selling (1996) showed that porosity can seriously decrease mechanical performance by serving as local strain concentration.
Porosity also causes issues during heat treatment, where heat results in the expansion of air within the pores, creating bubbling in HPDC parts. Improvement of the HPDC process to form parts with high quality and increased performance is thus of highly worthwhile. Flemings (1991) demonstrated that the Rheo-HPDC technique can be used to prepare high quality parts. Compared to traditional HPDC, Rheo-HPDC provides parts with many advantages such as low porosity, heat treatability and high performance.
In the RheoHPDC process, the liquid metal is initially turned into semisolid slurry and then the slurry is shaped directly using a HPDC machine. Various preparation processes have been developed to prepare the semisolid slurry. The twin-screw stirring process was studied by Fan et al. (2005), the gas induced semisolid (GISS) process was reported by Wannasin et al. (2006) and the serpentine channel pouring (SCP) process was used by Liu et al. (2015).
These preparation techniques have been widely studied and used in labs, and are able to prepare semisolid slurries with equiaxed microstructures. However, many drawbacks still exist, such as difficulties in cleaning up the devices and complicated disassembly and installation of the devices, which limit their extensive use for industrial applications.
In order to deal with the issues that exist in the slurry preparation, a self-developed forced convection stirring (FCS) device was designed for the preparation of semisolid slurry by Zhou et al. (2014a,b). It is an environmentally friendly device with a simple operational process and low cost, and it can run continuously without cleanup. It is convenient to combine a FCS device with HPDC machines to develop a Rheo-HPDC process and such procedure is termed as, FCS Rheo-HPDC.
In this work, the semisolid slurries of A356, A380 and 7075 Al-alloys, as such of AZ91D Mg-alloy were prepared by the FCS process and then formed by HPDC machines to four different parts or quenched by water to ingots. The effect of the FCS process on the microstructure and macrosegregation of ingots was studied.
The microstructure, porosity and mechanical properties of the FCS Rheo-HPDC alloys were studied and compared to those formed by HPDC and other Rheo-HPDC processes. Based on heat transfer and hydrodynamics, the effect of the rotation speed on temperature, composition and solid fraction were simulated by the commercial computational fluid dynamic software Flow-3D.
Experimental procedure
2.1. FCS process
The FCS device is presented in Fig. 1. It consists of a stirring system, a temperature control system and a discharge system. The stirring system contains a stirring rod equipped with a helicoid blade, and its major function is to turn the melt into high-quality semisolid slurry under the FCS action. There are huge amounts of changing interfacial areas among the solidifying melt, helicoid blade and barrel during slurry preparation. This makes the preparation process of slurry significantly efficient for fast heat dissipation. Heating cables are twined around the stainless steel barrel wall. The discharge operation is controlled by a discharge handle and a graphite blockage, which are linked using a center pin. It should be noted that a graphite lining is embedded in the stirring chamber for solving sticking problem.
2.2. Raw materials
The alloys, including commercially available cast Al-alloys A356
and A380, a commercially available wrought Al-alloy 7075, and a
commercially available cast Mg-alloy AZ91D, are used in this work.
Table 1 lists the chemical compositions and freezing ranges of the
four alloys.
2.3. Slurry preparation and FCS rheo-HPDC
The alloys were melted in top-loading resistance furnaces at the temperature of 70 ◦C above their liquidus. The melt was cooled to a pouring temperature (0–30 ◦C above their liquidus) after drossing and degassing. Then the melt was poured into the pre-heated FCS device. The detailed melt mass and FCS process parameters are listed in Table 2. After the melt was stirred to a preset time, the semisolid slurry with a certain solid fraction was prepared and was sent into the shot sleeve of a HPDC machine to form parts.
The detailed HPDC machine models and HPDC process parameters are also listed in Table 2 and the photographs of forming parts are presented in Fig. 2. For comparison, traditional HPDC parts were also prepared without FCS treatment under the same pouring temperature and HPDC parameters.
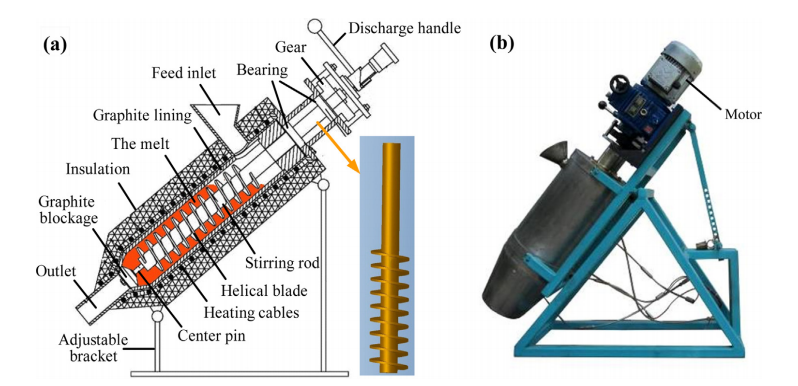
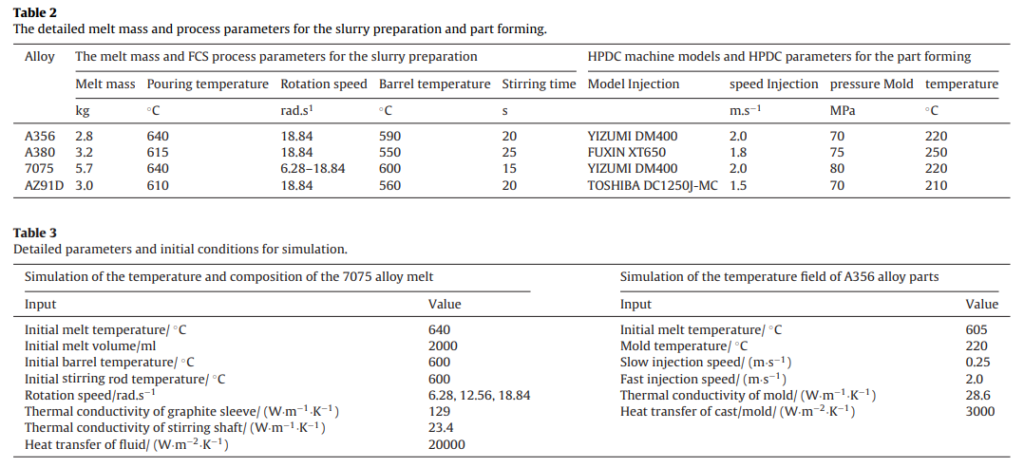
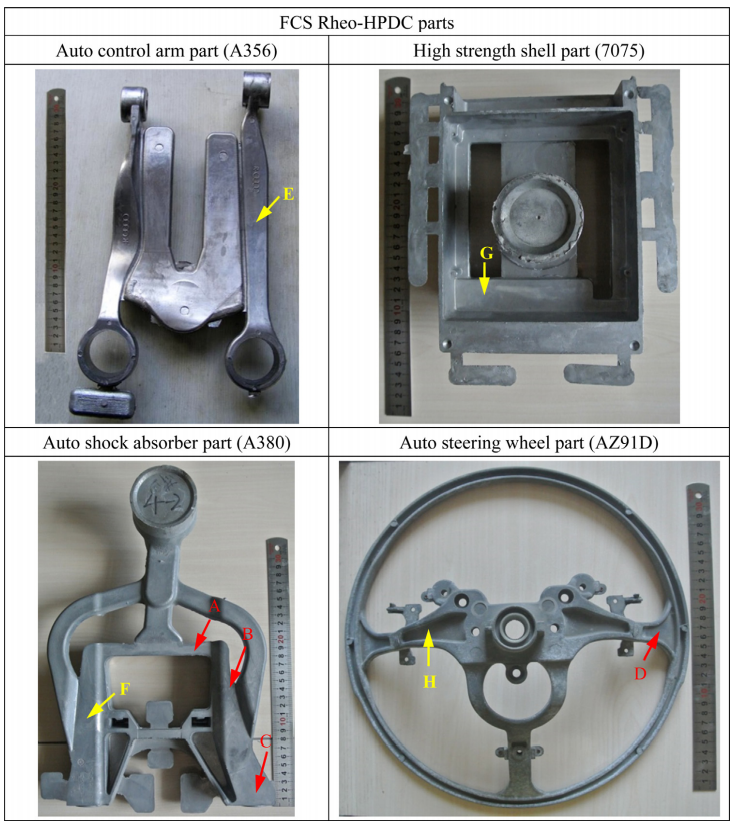
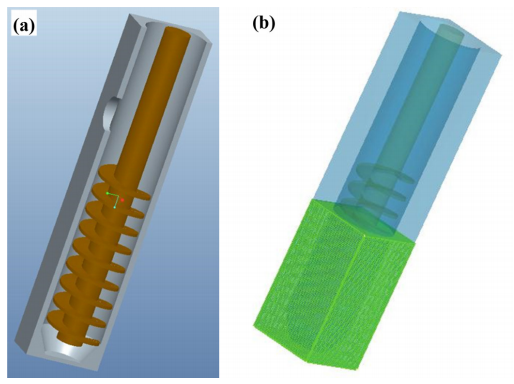
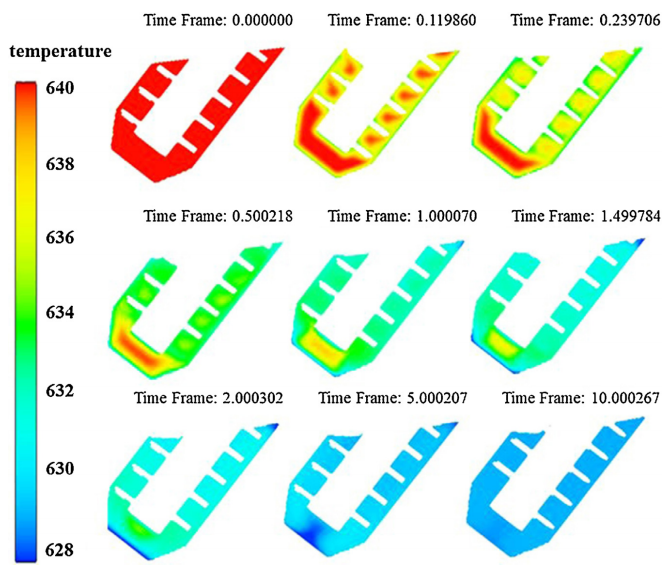
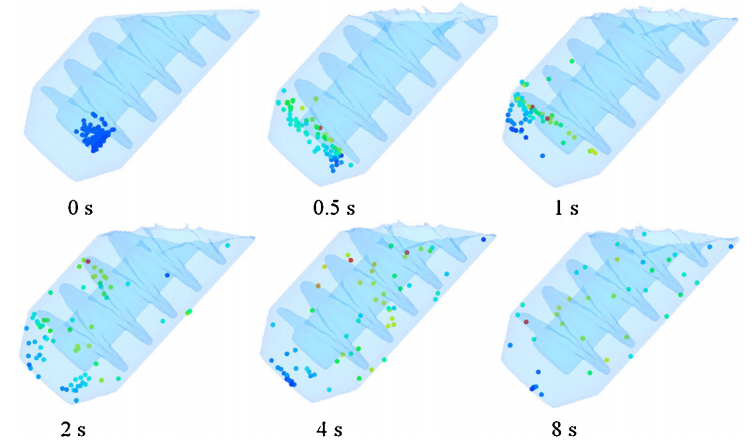
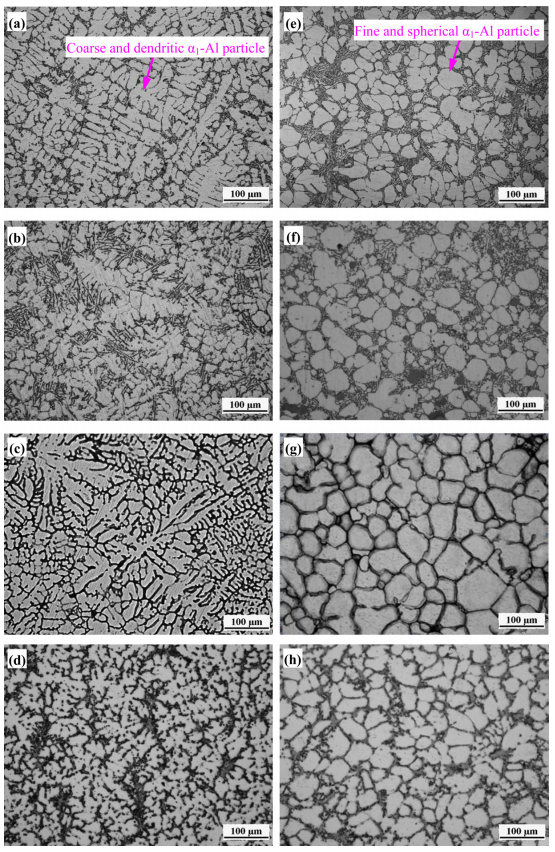
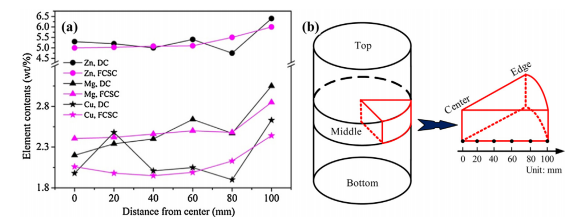
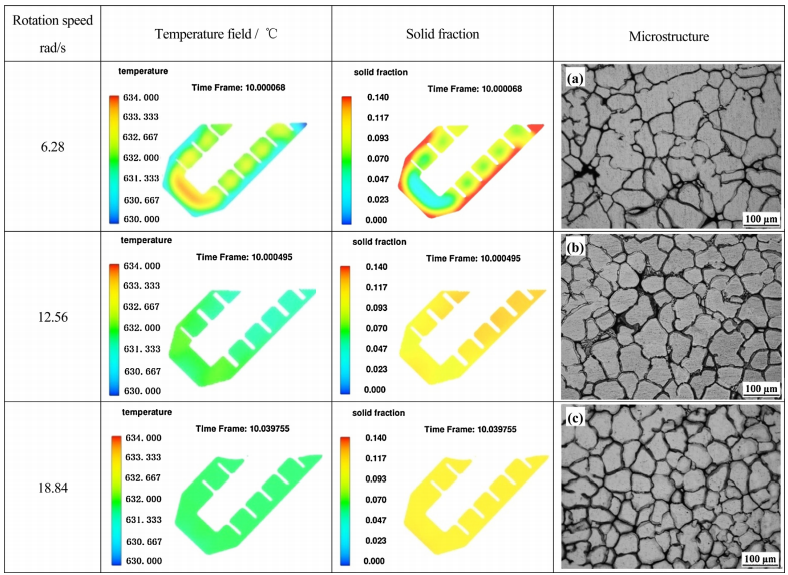
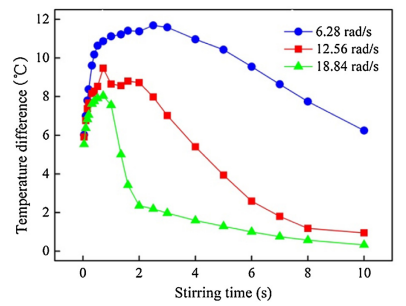
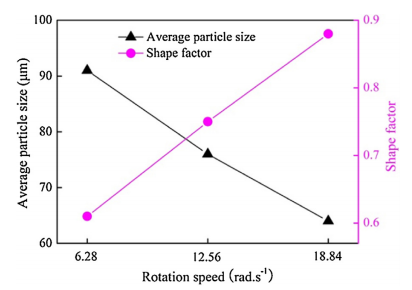
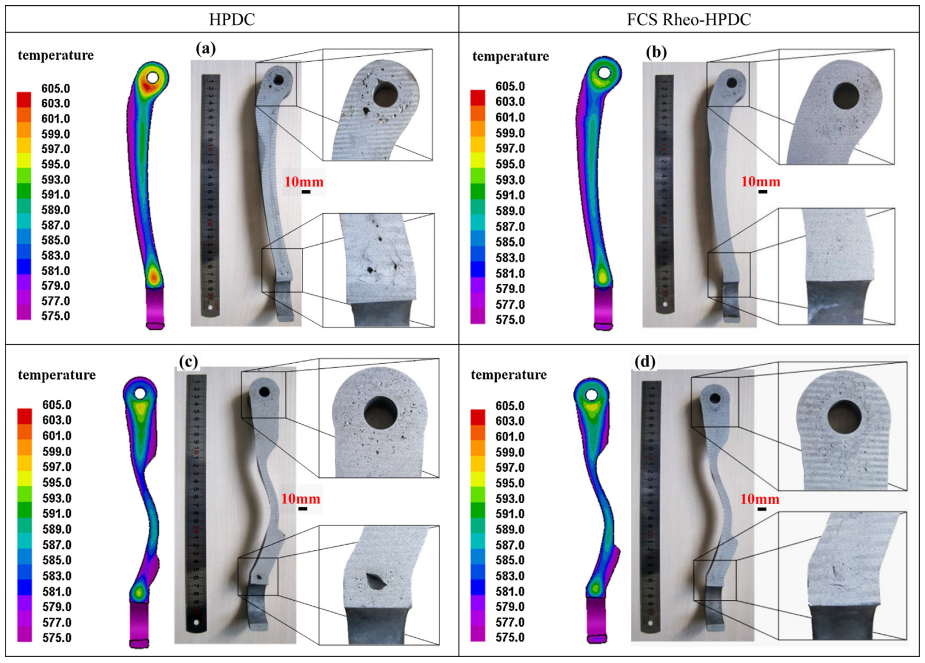
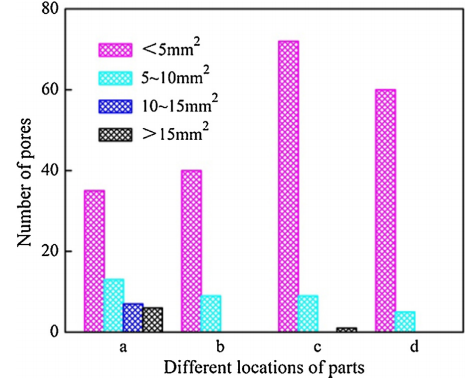
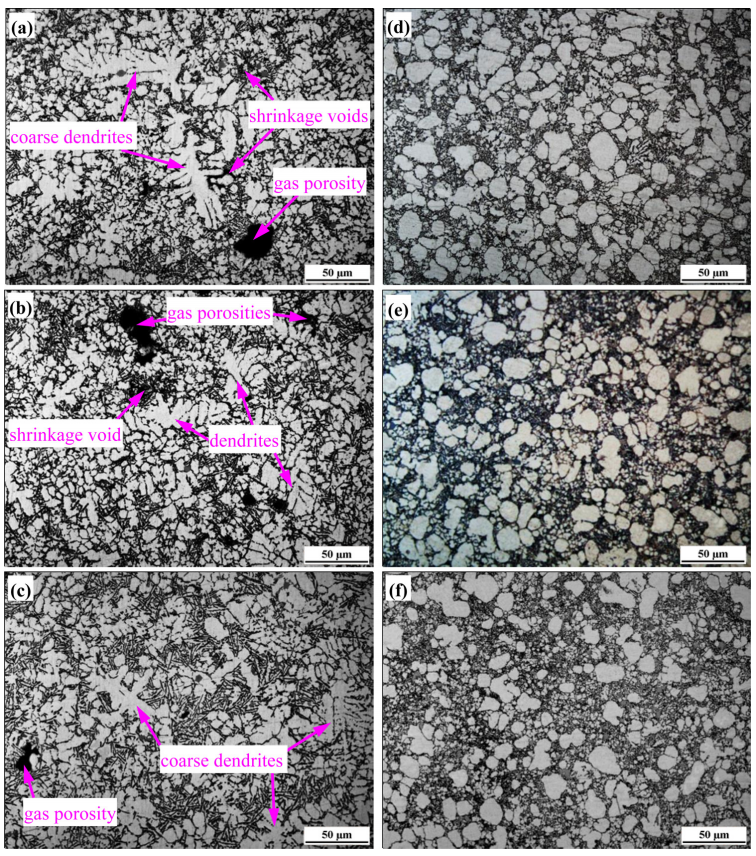
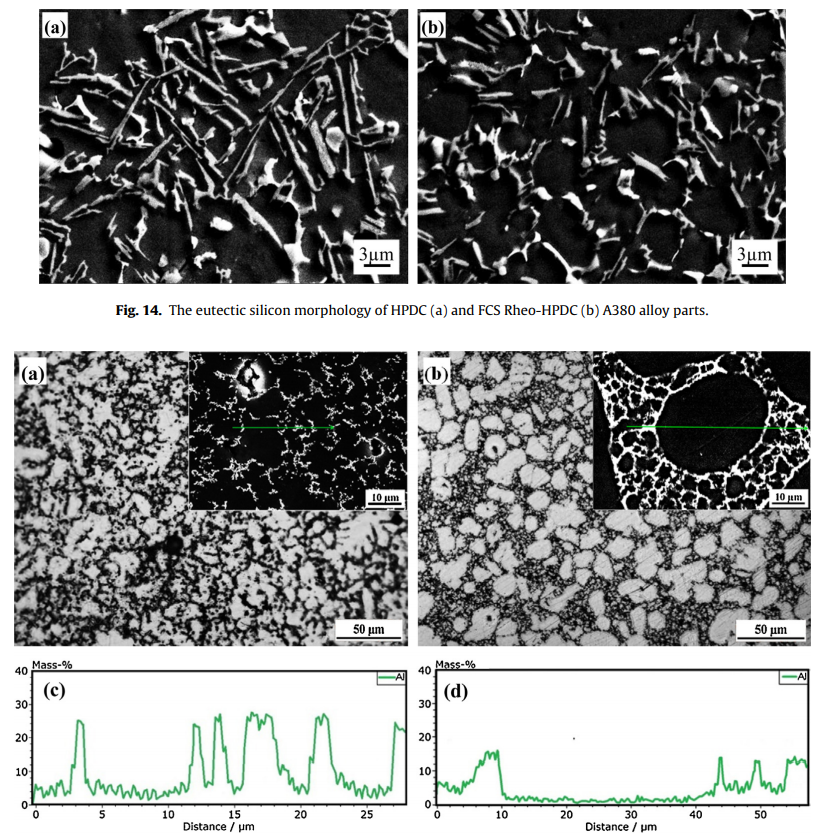
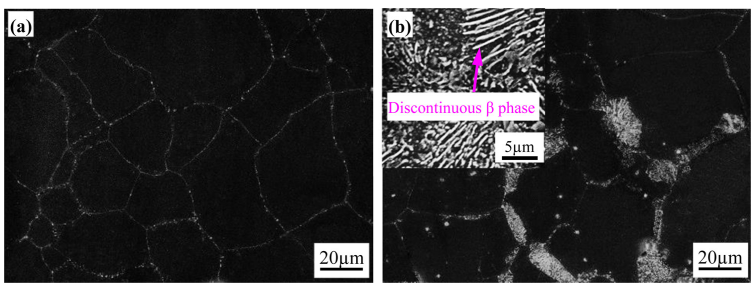
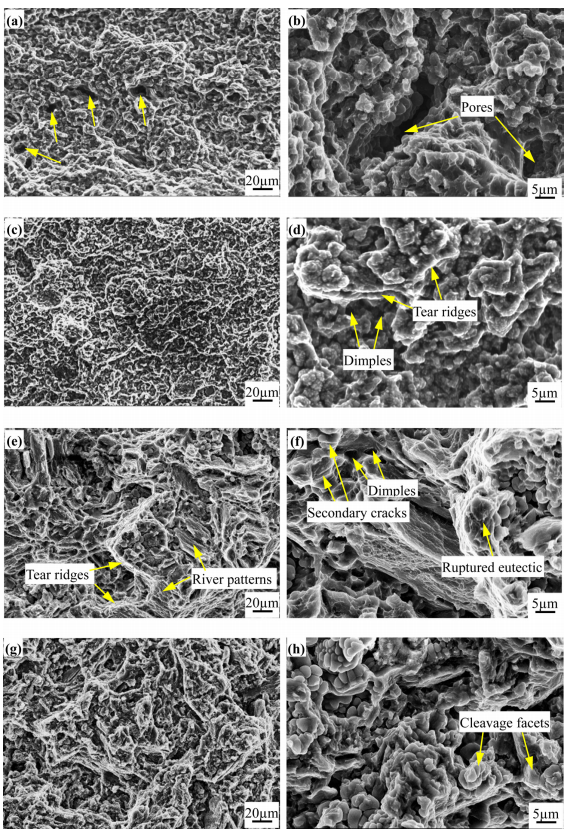
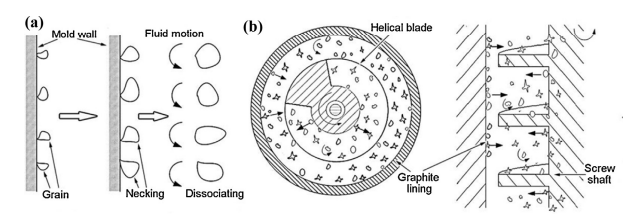
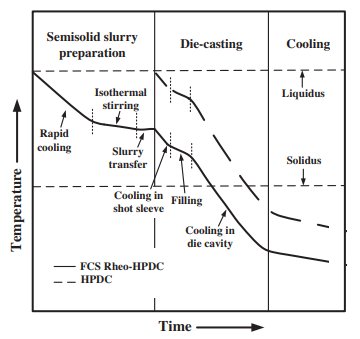
Conclusions
(1) A simplified process, namely forced convection stirring (FCS), was developed for the preparation of semisolid slurries. The FCS process can prepare slurries in which primary particles are fine, spherical and uniformly dispersed in the liquid matrix.
(2) The strong convection rapidly promotes the uniformity of the temperature and composition of the melt, which destroys the formation environment of dendrites and improves primary particles in the quantity and morphology.
(3) A simple Rheo-HPDC process is developed by combining the FCS device with a HPDC machine. The microstructures of FCS Rheo-HPDC parts at different regions are all composed of fine spherical particles and low porosity levels (0.3-0.5%). For the control arms of A356 alloy, the total pore areas of the FCS RheoHPDC parts are decreased by 3 times in comparison to that of the HPDC parts.
(4) FCS Rheo-HPDC parts show improved mechanical properties to those formed by HPDC and other Rheo-HPDC techniques, and the increasing rates of UTS, YS and elongation are over 10% in comparison to HPDC.
References
Aguilar, J., Grimming, T., Bührig-Polaczek, A., 2005. Rheo-container-process (RCP): new semisolid forming method for light metal alloys. In: Kainer, K.U. (Ed.), Magnesium: Proceedings of the 6th International Conference Magnesium Alloys and Their Applications. Wolfsburg, Germany, pp. 767–773.
Bradai, D., Kadi-Hanfi, M., Zieba, P., Kuschke, W.M., Gust, W., 1999. The kinetics of the discontinuous precipitation and dissolution in Mg-rich Al alloys. J. Mater. Sci. 34, 5331–5336.
Cáceres, C.H., Selling, B.I., 1996. Casting defects and the tensile properties of an A1-Si-mg alloy. Mater. Sci. Eng. A 220, 109–116.
Cáceres, C.H., Davidson, C.J., Griffiths, J.R., Newton, C.L., 2002. Effects of solidification rate and ageing on the microstructure and mechanical properties of AZ91 alloy. Mater. Sci. Eng. A 325, 344–355.
Chalmers, B., 1964. Principles of Solidification. John Wiley & Sons, New York.
Chen, Z.Z., Mao, W.M., Wu, Z.C., 2011. Mechanical properties and microstructures of Al alloy tensile samples produced by serpentine channel pouring rheo-diecasting process. Nonferrous Met. Soc. China 21, 1473–1479. Clark, J.B., 1968. Age hardening in a Mg-9 wt% Al alloy. Acta Metall. 16, 141–152.
Curle, U.A., Govender, G., 2010. Semisolid rheocasting of grain refined aluminum alloy 7075. Trans. Nonferrous Met. Soc. Chi. 20, 832–836. Duly, D., Simon, J.P., Brechet, Y., 1995. On the competition between continuous and discontinuous precipitations in binary Mg-al alloys. Acta metal. Mater. 43, 101–106.
Esmaily, M., Shahabi-Navid, M., Mortazavi, N., Svensson, J.E., Halvarsson, M., Wessén, M., Jarfors, A.E.W., Johansson, L.G., 2014. Microstructural characterization of the Mg-al alloy AM50 produced by a newly developed rheo-casting process. Mater. Charact. 95, 50–64.
Fan, Z., Fang, X., Ji, S., 2005. Microstructure and mechanical properties of rheo-diecast (RDC) aluminum alloys. Mater. Sci. Eng. A 412, 298–306. Fan, Z., Liu, G., Wang, Y., 2006. Microstructure and mechanical properties of rheo-diecast AZ91D magnesium alloy. J. Mater. Sci. 41, 3631–3644.
Flemings, M.C., 1991. Behavior of metal alloys in the semisolid state. Met. Trans. 22A, 957–981.
Fu, J.L., Wang, K.K., 2014. Modelling and simulation of die casting process for A356 semi-solid alloy. Proced. Eng. 81, 1565–1570.
Guo, H.M., Yang, X.J., 2008. Heat treatments and mechanical properties of YL112 aluminum alloy produced by rheo-diecasting process. Chin. J. Nonferrous Met. 18, 394–399.
Guo, H.M., Yang, X.J., Wang, J.X., 2009a. Pressurized solidification of semi-solid aluminum die casting alloy A356. J. Alloys Compd. 485, 812–816.
Guo, H.M., Yang, X.J., Luo, X.Q., 2009b. Formation of grain refined and non-dendritic microstructure of an aluminum alloy under angular oscillation. J. Alloys. Compd. 482, 412–415.
Jiang, J.F., Wang, Y., 2015. Microstructure and mechanical properties of the semisolid slurries and rheoformed component of nano-sized SiC/7075 aluminum matrix composite prepared by ultrasonic-assisted semisolid stirring. Mater. Sci. Eng. A 639, 350–358.
Jiang, J.X., Wu, Z.C., Chen, L.L., Hao, J., 2008. Numerical simulation and analysis of mould filling process in lost foam casting. Chin. Foundry 5, 175–178.
Jin, C.K., Jang, C.H., Kang, C.G., 2015. Die design method for thin plates by indirect rheo-casting process and effect of die cavity friction and punch speed on microstructures and mechanical properties. J. Mater. Process. Technol. 224, 156–168.
Kaufmann, H., Uggowitzer, P.J., 2001. Fundamentals of the new rheocasting process for magnesium alloys. Adv. Eng. Mater. 3, 963–967.
Kubota, K., Mabuchi, M., Higashi, K., 1999. Review processing and mechanical properties of fine-grained magnesium alloys. J. Mater. Sci. 34, 2255–2262.
Lü, S.L., Wu, S.S., Wan, L., An, P., 2013. Microstructure and tensile properties of wrought Al alloy 5052 produced by rheo-squeeze casting. Metall. Mater. Trans. A 44, 2735–3745.
Li, L., Zhou, R.F., Cen, Q.H., Li, Z.H., Jiang, Y.H., Zhou, R., 2011. Die casting semi-solid ZL101A alloy prepared by inclined slope cooling-transferring method and its properties. Spec. Cast. Nonferrous Alloys 31, 907–910.
Li, Y.G., Mao, W.M., Zhu, W.Z., Yang, B., 2014. Rheological behavior of semi-solid 7075 aluminum alloy at steady state. China Foundry 11, 79–84.
Lin, C., Wu, S.S., Lü, S.L., An, P., Wan, L., 2013. Microstructure and mechanical properties of rheo-diecast hypereutectic Al-si alloy with 2%Fe assisted with ultrasonic vibration process. J. Alloy. Comp. 568, 42–48.
Liu, Z.Y., Mao, W.M., Wang, W.P., Zheng, Z.K., 2015. Preparation of semi-solid A380 aluminum alloy slurry by serpentine channel. Trans. Nonferrous Met. Soc. China 25, 1419–1426.
Minkoff, I., 1986. Solidification and Cast Structure. John Wiley & Sons Ltd., Great Britain. Nemcová, ˇ A., Zapletal, J., Julis,ˇ M., Podrábsky, ´ T., 2009. Cyclic fatigue resistance of AZ91 magnesium alloy. Mater. Eng. 16, 5–10.
Ohno, A., 1987. Solidification-The Separation Theory and Its Practical Applications. Springer-Verlag Press, Germany.
Sui, Y.D., Wang, Q.D., Ye, B., Zhang, L., Jiang, H.Y., Ding, W.J., 2015. Effect of solidification sequence on the microstructure and mechanical properties of die-cast Al-11Si-2Cu-fe alloy. J. Alloys Compd. 649, 679–686.
Thanabumrungkul, S., Janudom, S., Burapa, R., Dulyapraphant, P., Wannasin, J., 2010. Industrial development of gas induced semi-solid process. Nonferrous Met. Soc. China 20, 1016–1021.
Wannasin, J., Martinez, R.A., Flemings, M.C., 2006. Grain refinement of an aluminum alloy by introducing gas bubbles during solidification. Scripta Mater. 55, 115–118.
Wu, S.S., Lü, S.S., An, P., Nakae, H., 2012. Microstructure and property of rheocasting aluminum alloy made with indirect ultrasonic vibration process. Mater. Lett. 73, 150–153.
Yang, L.Q., Kang, Y.L., Zhang, F., Xu, J., 2010. Microstructure and mechanical properties of rheo-diecasting AZ91D Mg alloy. Trans. Nonferrous Met. Soc. China 20, 862–867.
Yang, B., Mao, W.M., Song, X.J., 2013. Microstructure characteristies and mechanical properties of rheocasting 7075 aluminum alloy. China Foundry 5, 277–281.
Zhang, Y.F., Liu, Y.B., Cao, Z.Y., Zhang, Q.Q., Zhang, L., 2009. Mechanical properties of thixomolded AZ91D magnesium alloy. J. Mater. Process. Tech. 209, 1375–1384.
Zhou, B., Kang, Y.L., Qi, M.F., Zhang, H.H., Zhu, G.M., 2014a. Microstructure and property of rheo-diecasting magnesium-alloy with forced convection mixing process. Solid State Phenom 217-218, 455–460.
Zhou, B., Kang, Y.L., Qi, M.F., Zhang, H.H., Zhu, G.M., 2014b. R-hPDC process with forced convection mixing device for automotive part of A380 aluminum alloy. Materials 7, 3084–3105.