A Comprehensive Guide to FSW: Understanding the Process, Parameters, and Potential for High-Strength Joints
This technical brief is based on the academic paper "A Critical Review of Friction Stir Welding Process" by Verma, S. M. & Misra, J.P., published in DAAAM International Scientific Book 2015. It is summarized and analyzed for manufacturing and design professionals by the experts at CASTMAN.
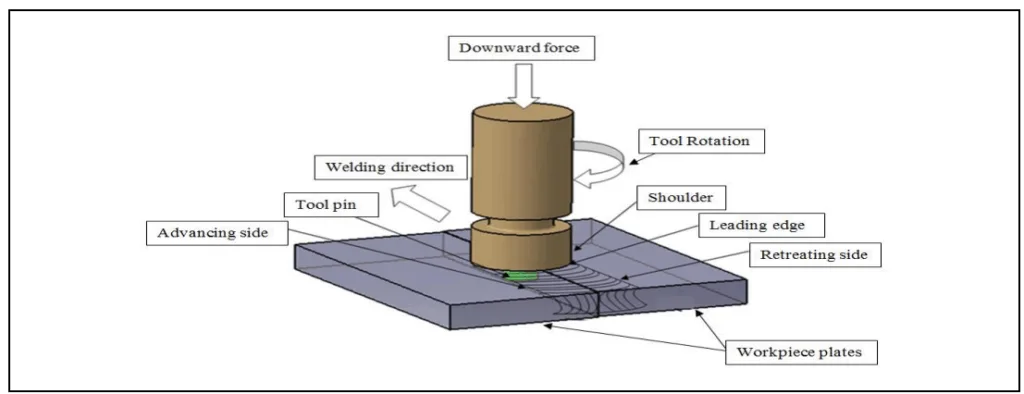
Keywords
- Primary Keyword: Friction Stir Welding (FSW) Process
- Secondary Keywords: Solid-state welding, FSW process parameters, FSW tool geometry, FSW aluminum alloys, Dissimilar metal welding, FSW applications, Heat Affected Zone (HAZ)
Executive Summary
- The Challenge: Traditional fusion welding methods for high-strength alloys (like aluminum) often introduce defects such as porosity, distortion, and large, weakened heat-affected zones (HAZ), compromising joint integrity.
- The Method: This paper provides a critical review of Friction Stir Welding (FSW), a solid-state joining process that avoids melting the material. It analyzes extensive research on FSW principles, process parameters, and applications across various materials.
- The Key Breakthrough: FSW consistently produces high-quality, low-defect joints with superior mechanical properties compared to fusion welding. The process is highly dependent on controllable factors like tool geometry, welding speed, and rotational speed.
- The Bottom Line: FSW is an established, eco-friendly, and efficient alternative for joining a wide range of materials, including dissimilar metals, with significant advantages in the aerospace, automotive, and marine industries.
The Challenge: Why This Research Matters for HPDC Professionals
In modern manufacturing, the demand for lightweight, high-strength components is ever-increasing. However, joining advanced materials like aluminum and magnesium alloys using conventional fusion welding techniques presents significant challenges. High energy density leads to wide heat-affected zones (HAZ), solidification defects, reduced mechanical properties, and distortion (Lohwasser and Chen, 2010). These drawbacks necessitate the exploration of advanced joining techniques.
Friction Stir Welding (FSW), invented by The Welding Institute (TWI) in 1991, emerged as a revolutionary solution. As a solid-state process, it joins materials below their melting point, eliminating many of the issues associated with fusion welding. This review consolidates years of research to provide a clear understanding of why FSW has become a "green technology" and a go-to process for critical applications.
The Approach: Unpacking the Methodology
This paper conducts a comprehensive literature review, critically evaluating the key aspects of the FSW process. The authors synthesized findings from numerous studies to provide a holistic overview. The core of the FSW technique involves a non-consumable rotating tool with a specially designed pin and shoulder, as depicted in Fig. 1.
The process works as follows:
1. The rotating tool is plunged into the interface of the two workpieces to be joined.
2. Friction between the tool and the workpieces generates intense, localized heat, softening the material without melting it.
3. The tool then travels along the joint line, stirring the plasticized material together.
4. This thermomechanical action creates a solid-state, recrystallized joint with a fine-grained microstructure upon cooling.
The review examines how different parameters—grouped into tooling, machine, and other factors (Fig. 3)—influence the final weld quality.
The Breakthrough: Key Findings & Data
The review highlights several critical findings from the collective body of research on FSW.
Superior Microstructure and Properties: FSW joints exhibit distinct microstructural regions (Fig. 2), including a fine-grained, fully recrystallized "nugget zone." This refined structure often leads to enhanced tensile strength, ductility, and fatigue properties compared to the parent material or fusion welds. For example, studies on aluminum alloys show FSW can increase joint strength by 30% to 50% (Lohwasser and Chen, 2010).
Tool Geometry is Crucial: The design of the tool pin and shoulder is one of the most vital elements. Different pin profiles (cylindrical, tapered, threaded) and shoulder designs (concave, scroll) directly influence material flow, heat generation, and the final weld integrity (Fig. 4). For instance, Elangovan et al. (2008) found that a square pin profile produces defect-free welds with high tensile strength in 6061 aluminum alloy.
Broad Material Applicability: While 76% of research focuses on aluminum (Fig. 5), FSW has been successfully applied to a wide range of materials:
- Steel: Produces joints with superior ductility and refined grain structures compared to fusion welding (Reynolds et al., 2003).
- Copper: Overcomes the challenges of high thermal diffusivity, resulting in welds with higher strength than electron beam welding (Lee and Jung, 2004).
- Dissimilar Metals: FSW can effectively join dissimilar materials like aluminum to steel or aluminum to copper, which is extremely difficult with fusion processes (Takehiko et al., 2006).
Process Enhancements: The review also covers advanced FSW variations:
- Nanoparticle Inclusion: Adding ceramic particles (e.g., SiC, ZrB₂) can further enhance joint strength by acting as barriers to recrystallization (Bahrami et al., 2014).
- Preheating: Preheating the workpiece softens the material, improving material flow, reducing tool wear, and increasing joint strength by up to 8% (Sinclair et al., 2010).
Practical Implications for Your HPDC Operations
The comprehensive findings presented in this review have direct, actionable implications for engineering, design, and manufacturing operations. Understanding these principles is essential for process optimization, whether through physical trials or advanced thermomechanical simulations.
For Process Engineers: The detailed analysis of process parameters (tool rotation, travel speed, tilt angle) provides a clear roadmap for process optimization. The cause-and-effect diagram (Fig. 3) serves as an excellent starting point for designing experiments to eliminate defects and maximize joint strength. The findings suggest that precise control over heat input is key to managing the final microstructure.
For Tooling and Design Engineers: This review underscores that tool design is not a one-size-fits-all problem. The choice of pin profile and shoulder geometry (Fig. 4) must be tailored to the specific material and joint configuration. This knowledge is critical for designing robust and efficient FSW tools and can significantly reduce the trial-and-error phase of development.
For Simulation and R&D Teams: The complex material flow, severe plastic deformation, and heat generation in FSW are ideal candidates for modeling with advanced simulation software (FEA/CFD). This paper provides the foundational physics and key influencing factors required to build accurate simulation models. Modeling the effects of tool geometry or preheating can predict weld quality, minimize defects, and drastically cut down on physical prototyping costs.
Paper Details
A Critical Review of Friction Stir Welding Process
1. Overview:
- Title: A Critical Review of Friction Stir Welding Process
- Author: Verma, S. M. & Misra, J.P.
- Year of publication: 2015
- Journal/academic society of publication: DAAAM International Scientific Book 2015
- Keywords: Solid-state welding, friction stir welding, preheating, quenching, nano-particle inclusion
2. Abstract:
Friction stir welding (FSW) is a permanent type solid state joining process which is increasing rapidly for joining different metal alloys and non-metals in manufacturing industries especially aerospace, marine, spacecraft, automotive, etc. In present scenario the welding of metal alloys are replaced by FSW owing to its unique features over fusion welding processes, i.e. reduced porosity defect, reduced heat affected zone (HAZ), no requirement of shielding gas, ecofriendly, reduced distortion, etc. In this chapter, a critical evaluation of critical aspects of friction stir welding namely process principle, metallurgical and mechanical aspects; effect of preheating and nano-particle inclusion have been discussed. Difficulties and other issues related to FSW are also addressed to provide a guideline to global research community to carry out extensive research in this field.
3. Introduction:
In the present scenario, joining process industries are growing rapidly. Traditional fusion welding techniques, while established, suffer from high energy density, wide heat-affected zones (HAZ), and solidification defects like distortion and reduced mechanical properties. While advanced techniques like plasma and laser welding offer improvements, they are not suitable for reactive elements like aluminum and magnesium. This necessitates the exploration of solid-state welding techniques. FSW was invented in 1991 by TWI as a novel solid-state process that produces joints that are over 90% defect-free without melting the workpiece. Its eco-friendly and energy-efficient nature has established it as a green technology with significant cost and time savings in industries like aerospace.
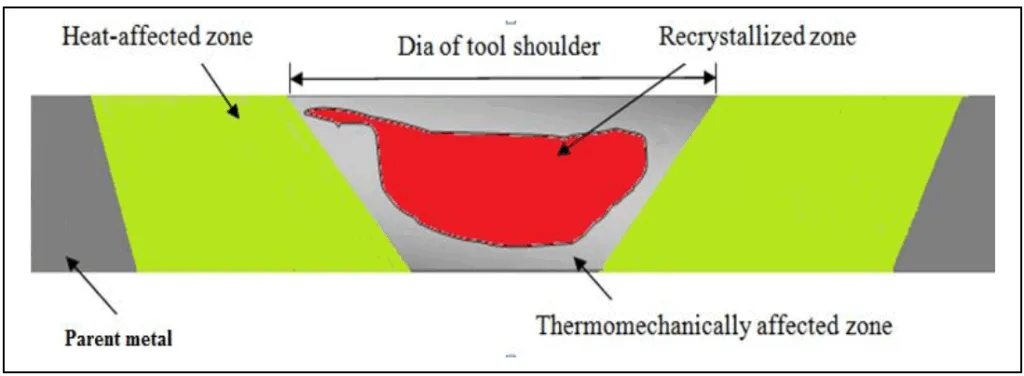
4. Summary of the study:
Background of the research topic:
The study is set against the backdrop of increasing demand for high-strength, lightweight metal alloys in critical industries like aerospace and automotive. Joining these materials effectively is a major concern, as traditional fusion welding methods often introduce defects and degrade material properties. FSW presents itself as a powerful alternative due to its solid-state nature.
Status of previous research:
The paper summarizes a vast body of existing research. It notes that while FSW is capable of joining a wide variety of materials (aluminum, magnesium, copper, steel, etc.), the bulk of published work (76%) has focused on aluminum alloys due to their industrial importance and the difficulties in fusion welding them. The review covers foundational work from the invention of the process (Thomas et al., 1991) to detailed studies on microstructure (Sato et al., 1999), tool geometry (Elangovan et al., 2008), and process enhancements like preheating and nanoparticle inclusion.
Purpose of the study:
The purpose is to provide a critical review and a consolidated summary of the work already carried out on FSW. The authors aim to present the major findings in one place, discuss critical aspects of the process (principle, metallurgy, mechanics), and address difficulties and outstanding issues to provide a guideline for future research in the field.
Core study:
The core of the paper is a literature review that systematically examines the FSW process. It covers:
1. The principle of FSW: Explaining how the tool generates frictional heat and mechanically stirs the material to form a solid-state bond.
2. Process parameters: Classifying and illustrating the influence of tooling, machine, and other parameters on weld quality.
3. FSW of different materials: Reviewing specific findings for aluminum, steel, copper, and other materials like titanium, brass, and polymers.
4. FSW of dissimilar metals: Discussing the unique capabilities and challenges of joining different metals.
5. Advanced techniques: Investigating the effects of nanoparticle inclusions, preheating, and quenching on joint properties.
5. Research Methodology
Research Design:
The research design is a comprehensive literature review. The authors have gathered, synthesized, and critically evaluated a wide range of academic papers, articles, and patents related to Friction Stir Welding.
Data Collection and Analysis Methods:
Data was collected from existing published research. The analysis involves comparing and contrasting the findings of different researchers on various aspects of FSW, such as the effect of process parameters on mechanical properties, microstructural evolution in different materials, and the efficacy of process variations. The paper uses this synthesized information to draw broad conclusions and identify gaps in the current body of knowledge.
Research Topics and Scope:
The scope is broad, covering the entire FSW field. Key topics include:
- Fundamental principles and microstructural regions of an FSW joint.
- The influence of a wide array of process parameters.
- Application of FSW to similar and dissimilar ferrous and non-ferrous alloys, as well as non-metals.
- The effects of preheating, quenching, and nanoparticle reinforcement.
- Identification of areas requiring further research, such as material flow mechanisms, tool wear, and the development of predictive models.
6. Key Results:
Key Results:
- FSW is a superior alternative to fusion welding for many alloys, offering benefits like low distortion, no porosity, a smaller HAZ, and no need for shielding gas or filler metal.
- Process parameters, particularly tool rotation rate, traverse speed, and tool geometry, are crucial for producing a sound, defect-free weld.
- Tool design (both pin and shoulder) has a significant influence on material stirring and heat generation, directly impacting the final mechanical properties of the joint. For example, conical shoulder tools result in different precipitate structures and elongation compared to scroll shoulder tools (Rodrigues et al., 2009).
- FSW is highly effective for aluminum alloys, which constitute the majority of research. It is also feasible and beneficial for steels, coppers, titanium, and even polymers.
- The process can be enhanced with preheating to improve material flow and with nanoparticle inclusions to create composite-like joints with significantly improved strength.
- Gaps in research exist, particularly in the areas of material flow mechanisms, tool wear, corrosion behavior, and the development of mathematical models to predict process outcomes.
Figure Name List:
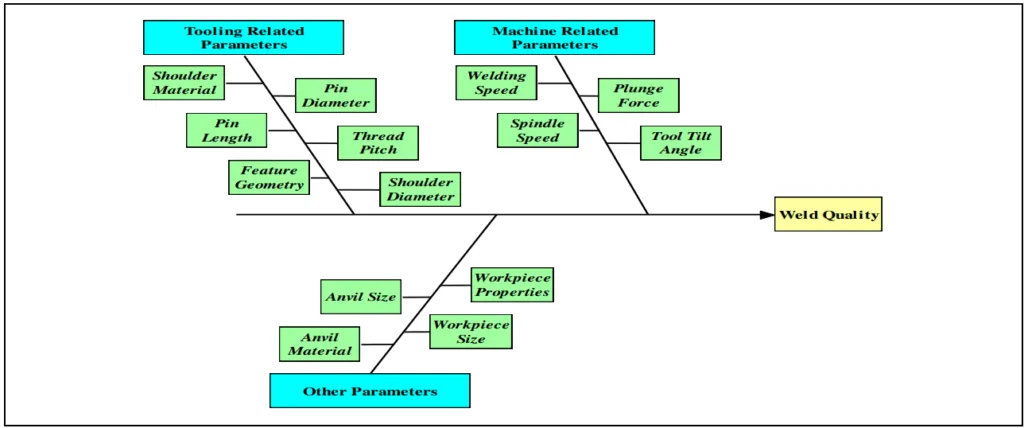
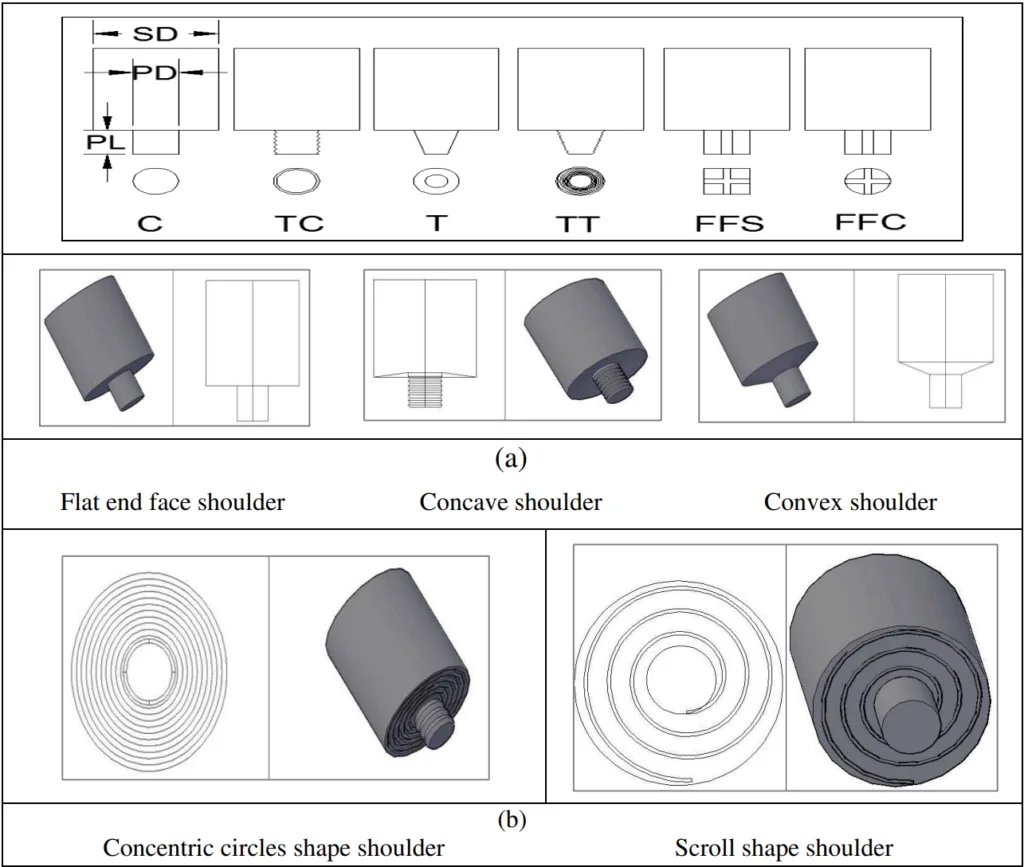
- Fig. 1. Principle of friction stir welding (Backer and Bolmsjo, 2014)
- Fig. 2. Microstructural regions of friction stir welding (Mahoney et al., 1998)
- Fig. 3. Cause and effect diagram for friction stir welding process
- Fig. 4. (a) FSW tool with different pin geometry (C: Cylindrical; TC: Threaded cylindrical; T: Tapered; TT: Threaded taper; FFS: Four flute square; FFC: Four flute cylindrical)(b) FSW tools with different shoulder geometry
- Fig. 5. Comparative study of published research work on FSW
7. Conclusion:
The paper concludes that FSW is a proven and highly advantageous joining process for a wide range of similar and dissimilar materials. Its unique characteristics result in joints with significantly enhanced mechanical properties compared to those made by fusion welding. The quality of the weld is critically dependent on process parameters, with tool geometry being a deciding factor. Despite considerable research, the authors highlight several areas that require further investigation. These include a more in-depth study of the interaction effects of process parameters, the mechanism of material flow, tool wear, and the tribological and corrosion behavior of FSW joints. Finally, there is a need for robust mathematical or theoretical models to help select input parameters to achieve a desired output, which would further accelerate the industrial adoption of the technology.
8. References:
- Backer, J. D. & Bolmsjö, G. (2014).Temperature control of robotic friction stir welding using the thermoelectric effect. Int. J. of Adv. Manuf. Technol., 70, 375-383.
- Elangovan, K.; Balasubramanian, V. & Valliappan, M. (2008). Influences of tool pin profile and axial force on the formation of friction stir processing zone in AA6061 aluminium alloy. Int. J. Adv. Manuf. Technol, 38, 285-295
- Lohwasser, D. & Chen, Z. (2010). Friction stir welding: from basics to applications, Woodhead Publishing limited, New Delhi
- Mahoney, M. W.; Rohdes, C. G.; Flintoff, J. G.; Surling,R. A. & Bingel, W. H. (1998). Properties of friction-stir-welded 7075 T651 aluminum. Metallurgical and Materials Transactions, 29,1955-1964
- Reynolds, A. P.; Tang, W.; Gnaupel-Herold, T. & Prask, H. (2003). Structure, properties, and residual stress of 304L stainless steel friction stir welds. Scripta Materialia, 48, 1289-1294
- Rodrigues, D. M.; Loureiro, A.; Leitao, C.; Leal, R. M.; Chaparro, B. M. &Vilaça, P. (2009). Influence of friction stir welding parameters on the microstructural and mechanical properties of AA 6016-T4 thin welds. Materials & Design, 30
- Sinclair, P. C.; Longhurst, W. R.; Cox, C. D.; Lammlein, D. H.; Alvin, M. & Cook, G.E. (2010). Materials and manufacturing processes heated friction stir welding: an experimental and theoretical investigation into how preheating influences process
- Takehiko, W.; Hirofumi, T. & Yanagisawa, A. (2006). Joining of aluminum alloy to steel by friction stir welding. Science and Technology of Welding and Joining, 4, 365-372
- Thomas, W. M.; Nicholas, E. D.; Needham, J. C.; Murch, M. G.; Templesmith, P. & Dawes, C. J. (1991). Patent 9125978.8
Conclusion & Next Steps
This research provides a valuable roadmap for enhancing component joining through Friction Stir Welding. The findings offer a clear, data-driven path toward improving quality, reducing defects, and optimizing production for a variety of materials.
STI C&D is committed to applying cutting-edge industry research to solve our customers’ most challenging technical problems. If the challenges discussed in this paper align with your goals, please contact our engineering team to discuss how we can help you apply advanced simulation principles to your FSW process development.
Expert Q&A:
Q1: What are the main advantages of Friction Stir Welding (FSW) over traditional fusion welding?
A1: According to the paper, FSW offers several unique advantages, including low distortion and shrinkage, no need for filler metal or shielding gas, a reduced heat-affected zone (HAZ), and freedom from porosity defects. This makes it an eco-friendly and highly effective alternative for joining materials like aluminum, magnesium, and copper. (Source: "A Critical Review of Friction Stir Welding Process", Abstract & Section 4).Q2: How important is the FSW tool design for the quality of the weld?
A2: The tool design is a deciding factor for obtaining sound welds. The paper states that the FSW tool, specifically the geometry of the pin and shoulder, regulates the amount of material stirred and the frictional heat generated. Different geometries, as shown in Fig. 4, directly impact material flow and the final mechanical and metallurgical properties of the joint. (Source: "A Critical Review of Friction Stir Welding Process", Section 4 & Section 2).Q3: Can FSW be used to join dissimilar materials, like aluminum and steel?
A3: Yes, the review indicates that FSW is capable of joining dissimilar metals, which is a significant challenge for fusion welding. For example, Takehiko et al. (2006) successfully joined aluminum alloy to steel, finding that joint strength was optimized when the tool pin was slightly offset toward the steel side. This capability makes FSW highly valuable for many industrial applications. (Source: "A Critical Review of Friction Stir Welding Process", Section 3.5).Q4: What are the key process parameters that need to be controlled in FSW?
A4: The paper identifies three broad categories of parameters, as shown in the cause-and-effect diagram in Fig. 3. The most critical machine-related parameters are tool rotational speed, welding (traverse) speed, plunge force/depth, and tool tilt angle. These parameters directly influence the heat input, material flow, and ultimately, the final weld quality. (Source: "A Critical Review of Friction Stir Welding Process", Section 1.2).Q5: Does adding nanoparticles to the joint improve the FSW process?
A5: Yes, the inclusion of hard ceramic nanoparticles (like SiC or ZrB₂) into the joint can significantly enhance the mechanical properties of FSW joints. The paper notes that these particles act as barriers against recrystallization during the process, leading to improved strength. In some cases, the joint becomes so strong that fracture during testing occurs in the base metal, not the weld. (Source: "A Critical Review of Friction Stir Welding Process", Section 3.6).Q6: What are the main areas where more research on FSW is needed?
A6: The review concludes by identifying several areas for future research. These include a deeper understanding of the material flow mechanism, tool geometry design and wear, the corrosion behavior of FSW joints, and the effect of process enhancements like preheating and quenching. Crucially, the paper calls for the development of mathematical/theoretical models to predict weld performance based on input parameters. (Source: "A Critical Review of Friction Stir Welding Process", Section 4).
Copyright
- This material is an analysis of the paper "A Critical Review of Friction Stir Welding Process" by Verma, S. M. & Misra, J.P.
- Source of the paper: DOI: 10.2507/daaam.scibook.2015.22
- This material is for informational purposes only. Unauthorized commercial use is prohibited.
- Copyright © 2025 STI C&D. All rights reserved.