This article introduces the paper "A complete computer aided engineering (CAE) modelling and optimization of high pressure die casting (HPDC) process" presented in the Journal of Manufacturing Processes.
1. Overview:
- Title: A complete computer aided engineering (CAE) modelling and optimization of high pressure die casting (HPDC) process
- Author: K. Dou, E. Lordan, Y.J. Zhang, A. Jacot, Z.Y. Fan
- Publication Year: 2020
- Publishing Journal/Academic Society: Journal of Manufacturing Processes, Elsevier Ltd. / The Society of Manufacturing Engineers
- Keywords: CAE simulation, finite element method, HPDC, Process optimization, CFD, Mechanical property
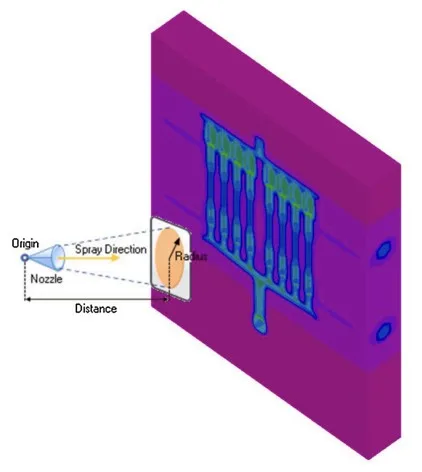
2. Research Background:
- Social/Academic Context of the Research Topic: The application of Computer Aided Engineering (CAE) in manufacturing is increasingly prevalent due to its efficiency and reliability. In the casting industry, CAE-based numerical modeling has become a standard practice, replacing traditional trial-and-error Research and Development (R&D) approaches. Advanced parallel computing and sophisticated calculation models enable detailed examination of fluid flow, heat transfer, solidification, and defect formation under various casting conditions. This facilitates component design and casting parameter optimization to achieve desired microstructural and mechanical properties. Establishing a direct correlation between process conditions, casting quality, and mechanical properties is crucial for processes like gravity die casting, High Pressure Die Casting (HPDC), and continuous casting, offering practical, economical, and energy-efficient solutions.
- Limitations of Existing Research: While numerical simulation of the HPDC process is not novel, prior research often focused on individual phenomena influencing the process. These include studies on gating system design, liquid jet optimization at the ingate, melt flow characteristics, re-oxidation processes, and the effects of shot sleeve filling. Existing studies often examined singular aspects like die casting machine parameters, plunger velocities, or runner designs in isolation. A comprehensive approach considering the entire HPDC cycle, encompassing upstream sub-processes, was lacking.
- Necessity of the Research: The paper highlights the need for a holistic simulation approach that integrates the entire HPDC process into a single mathematical model. This includes die heating, thermal die cycling, shot sleeve pre-filling, slow shot/fast shot injection, die filling/solidification, and intensification. Such a complete model is necessary to understand the complex interplay of these sub-processes and to optimize the HPDC process effectively for improved casting quality and mechanical properties. The research aims to address the limitations of fragmented studies by developing and validating a comprehensive CAE model for HPDC.
3. Research Purpose and Research Questions:
- Research Purpose: The primary research purpose is to develop and validate a complete Computer Aided Engineering (CAE) model for the High Pressure Die Casting (HPDC) process. This model aims to simulate the entire HPDC cycle, from die heating to solidification and intensification, using the ProCAST software. Ultimately, the goal is to demonstrate how this comprehensive CAE approach can be used for process optimization to improve casting quality and mechanical properties.
- Key Research Questions:
- Can a complete CAE model be developed to accurately simulate the entire HPDC process, including all relevant sub-processes and their interactions?
- How can interfacial heat transfer coefficients (iHTCs) between the melt and die/shot sleeve be accurately determined and incorporated into the CAE model?
- What is the optimum thermal die cycle number required to achieve a dynamic steady state of die temperature and ensure consistent casting quality?
- How can the piston shot profile be optimized using the CAE model to minimize defect formation during the injection phase?
- Can the optimized process parameters, derived from CAE simulations, demonstrably improve the mechanical properties of HPDC components?
- Research Hypotheses: (Implied, not explicitly stated in the paper, but can be inferred)
- A comprehensive CAE model, incorporating adjusted iHTCs and simulating the entire HPDC cycle, will accurately predict process conditions and casting quality.
- Optimizing the thermal die cycle through CAE simulation will lead to a more stable die temperature and improved casting consistency.
- Adjusting the piston shot profile based on CAE simulation will reduce defect formation (e.g., air entrapment) during die filling.
- HPDC components cast using CAE-optimized process parameters will exhibit improved mechanical properties (yield strength, ultimate tensile strength, and elongation) compared to those produced with non-optimized parameters.
4. Research Methodology:
- Research Design: The research employs a simulation-based experimental design. A complete CAE model of the HPDC process was developed using the finite element method (FEM) within the ProCAST software. The model was then used to simulate and optimize the HPDC process. Experimental validation was conducted by casting tensile bars using optimized parameters and testing their mechanical properties.
- Data Collection Method:
- Thermal Couple Measurements and Infrared Imaging: These methods were used to measure die surface temperature distribution and to adjust the interfacial heat transfer coefficients (iHTCs) within the CAE model. Time-dependent iHTCs were derived from these measurements and incorporated into the simulation.
- Mechanical Property Testing: Tensile tests were performed on cast tensile bars to evaluate yield strength, ultimate tensile strength (UTS), and elongation. These experimental results were used to assess the effectiveness of the CAE-optimized process parameters.
- Process Parameter Data: Time durations and sequences for various HPDC stages (die heating, thermal die cycling, shot sleeve pre-filling, injection, intensification, part ejection, die spraying, and air blowing) were recorded from actual HPDC experiments and used as inputs for the CAE model.
- Analysis Method:
- Finite Element Method (FEM) Simulation: The entire HPDC process was simulated using FEM within ProCAST. The Visual-Mesh, Visual-Cast, and Visual-Viewer modules were utilized for mesh generation, model calculation, and result analysis, respectively. Parallel computing techniques were employed for efficient computation.
- Governing Equations: Melt injection, die filling, and solidification were modeled using 3D FEM based on the enthalpy method. Melt turbulence was described using the standard k-ε turbulence model. The Volume of Fluid (VOF) method was used to track the melt free surface. Continuity and momentum equations were solved (simplified versions presented in the paper).
- Optimization Methodology: The HPDC process optimization was conducted in two steps:
- Thermal Die Cycle Optimization: Determining the optimum number of thermal die cycles to achieve a dynamic steady state die temperature.
- Piston Shot Profile Optimization: Adjusting the piston shot profile to minimize defect formation during injection, specifically focusing on air entrapment.
- Statistical Analysis: Mechanical property data from tensile tests were analyzed to compare the performance of castings produced with optimized and non-optimized parameters. Averages and standard deviations were calculated for Yield Strength (YS), Ultimate Tensile Strength (UTS), and Elongation (El).
- Research Subjects and Scope:
- Material: Aluminum alloy A356 was used for the simulations and experiments. Temperature-dependent material properties were obtained from the ProCAST database.
- Process: High Pressure Die Casting (HPDC) process using a cold chamber HPDC machine.
- Simulation Scope: The entire HPDC cycle, including die heating, thermal die cycling, shot sleeve pre-filling, slow/fast shot injection, die filling/solidification, and intensification.
- Experimental Scope: Casting of tensile bars using both standard and CAE-optimized piston shot profiles, followed by mechanical property testing.
5. Main Research Results:
- Key Research Results:
- Optimum Thermal Die Cycle: CAE simulation revealed that after 6-7 thermal cycles, the die surface temperature distribution reaches a quasi-steady state. Therefore, the temperature distribution after the 7th cycle was used for subsequent die filling simulations.
- Optimized Piston Shot Profile: Simulations with varying piston slow shot acceleration positions indicated that an acceleration position of 10 mm from the initial position resulted in the least and most uniform air entrapment in the casting.
- Improved Mechanical Properties: Tensile bars cast using the optimized piston shot profile (10 mm acceleration position, slow shot speed of 0.4-0.6 m/s) exhibited improved mechanical properties. Specifically, the UTS and Elongation values were highest, and standard deviations were lowest for samples produced with this optimized profile compared to other profiles tested.
- Statistical/Qualitative Analysis Results:
- Mechanical Property Data (Table 3): Tensile tests showed that the piston velocity profile of 0.4-0.6 m/s resulted in the highest average UTS and Elongation values and the lowest standard deviations for these properties, indicating improved and more consistent mechanical performance.
- Air Entrainment Simulation (Figure 17): Qualitative analysis of air entrainment distribution showed that the 10 mm piston slow shot acceleration position led to less and more uniformly distributed air entrapment compared to other positions.
- Oxide Formation Simulation (Figure 19): The oxide indicator simulation suggested that a slow shot speed of 0.4-0.6 m/s resulted in a relatively uniform oxide distribution and lower overall oxide tendency compared to other speeds.
- Data Interpretation: The results demonstrate that CAE simulation can effectively model and optimize the HPDC process. Optimizing the thermal die cycle ensures thermal stability, while adjusting the piston shot profile based on CAE insights can minimize defect formation and improve mechanical properties. The experimental validation through tensile testing supports the CAE predictions, showing a clear link between optimized process parameters and enhanced casting performance.
- Figure Name List:
- Fig. 1. Modelling workflow of the entire HPDC process.
- Fig. 2. Typical HPDC procedures during one entire cycle.
- Fig. 3. Configuration and hybrid FEM mesh used in calculation (in ½ symmetry).
- Fig. 4. A356 alloy thermophysical properties.
- Fig. 5. Time-dependent iHTCs used in this work.
- Fig. 6. Temperature distribution on the die surface after heating from atmosphere.
- Fig. 7. Temperature distribution at die surface during the 6th HPDC cycle.
- Fig. 8. Schematic illustration of spray/blow after part ejection.
- Fig. 9. Comparison of predicted die surface temperature distribution with infrared images obtained during HPDC.
- Fig. 10. Calculated temperature curves at sampling positions of die surface at multiple thermal cycles.
- Fig. 11. Flowrate curve used during shot sleeve filling.
- Fig. 12. Flow and temperature evolution of melt during filling of shot sleeve prior to piston injection, images from two viewing angles.
- Fig. 13. Distribution of externally solidified crystals along the shot sleeve.
- Fig. 14. Filling sequence of the melt and distribution of air in the die cavity.
- Fig. 15. Section cut-off for position where solidification time is below 0.7 s.
- Fig. 16. Piston shot curves with different slow shot acceleration positions.
- Fig. 17. Modelling results of air entrainment in casting with different slow shot acceleration position.
- Fig. 18. Piston shot curves with different slow shot velocities.
- Fig. 19. Comparison of modelling results with different piston slow shot velocity magnitude.
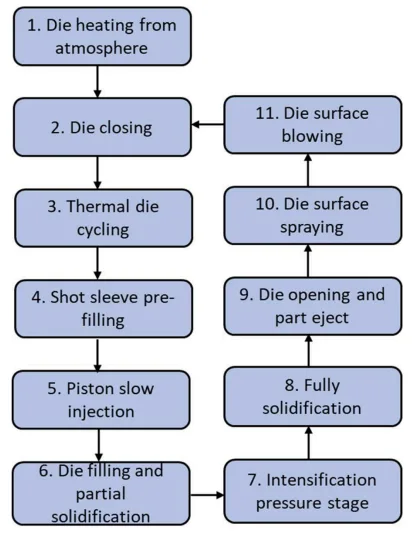
6. Conclusion and Discussion:
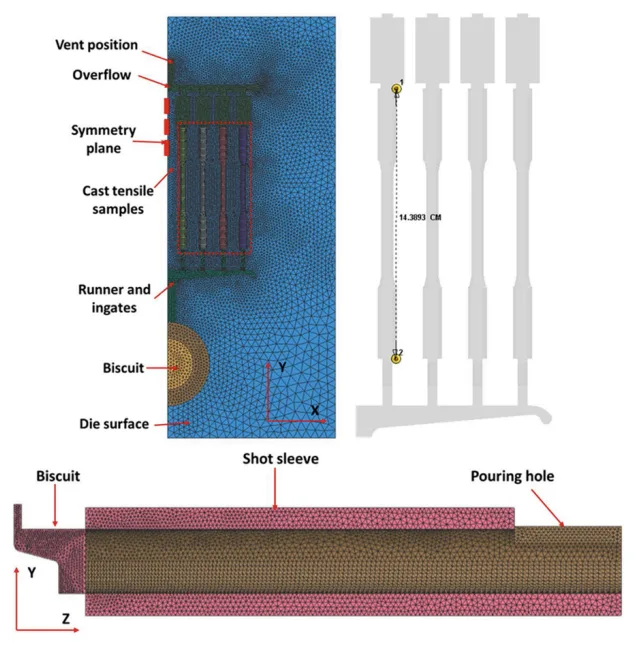
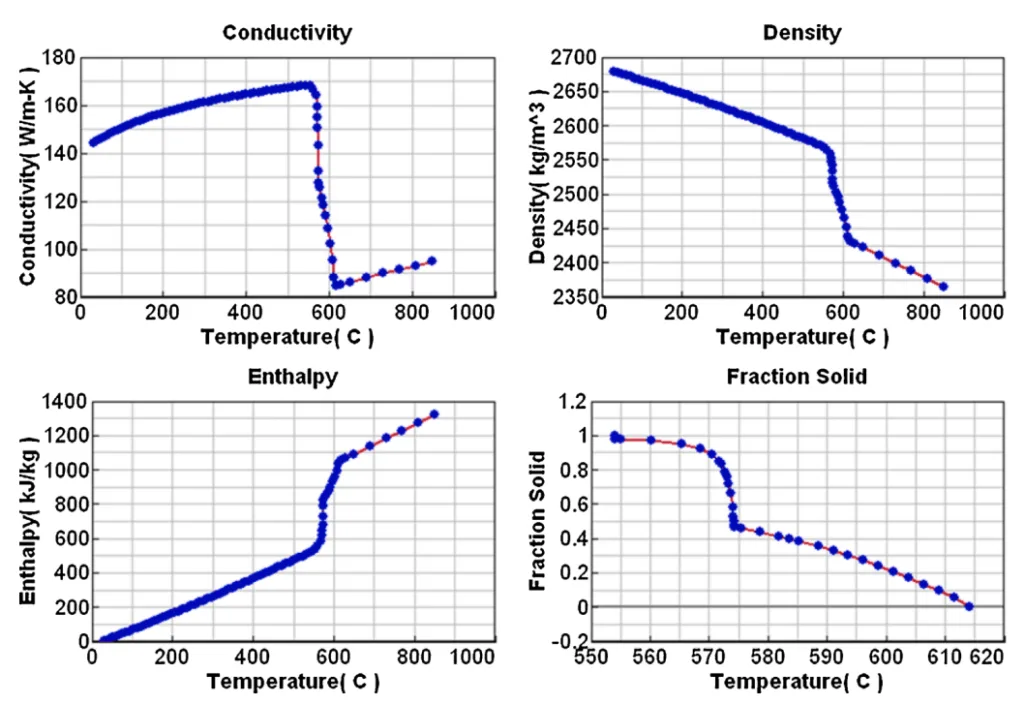
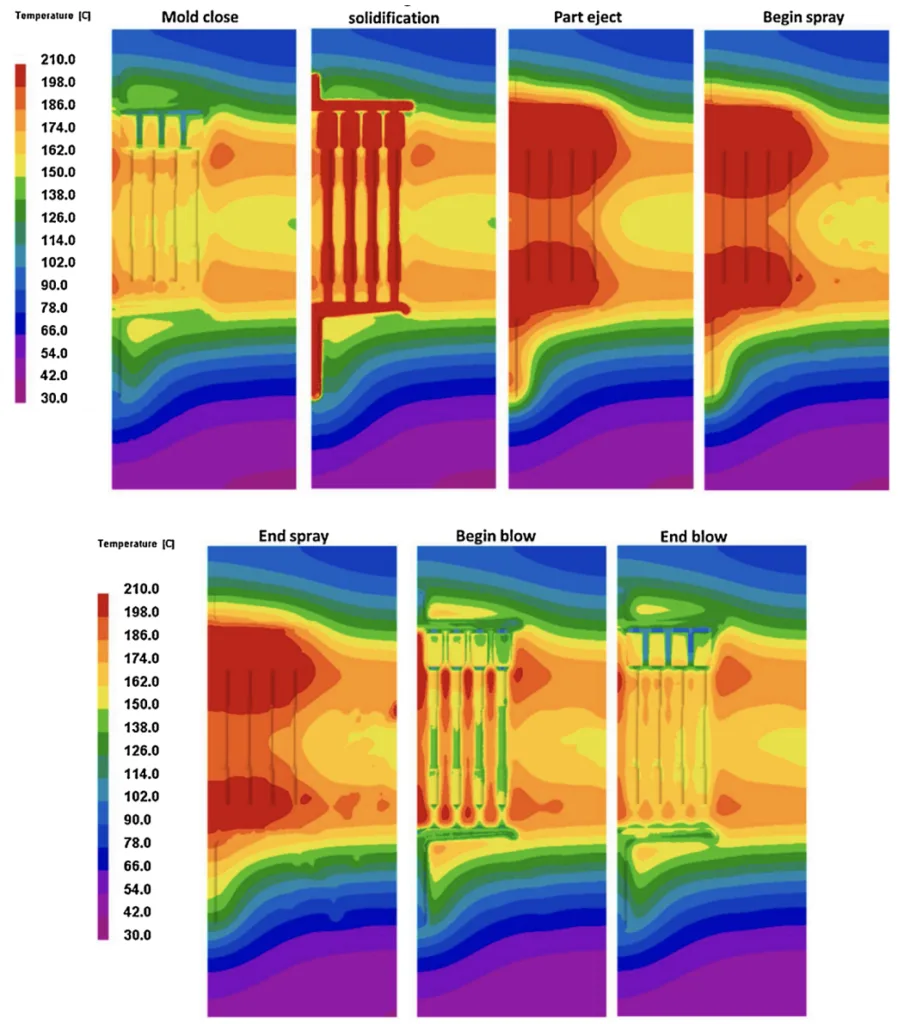
- Summary of Main Results: This research successfully established a complete CAE simulation approach for cold chamber HPDC using ProCAST. The model incorporates die heating, thermal die cycling, shot sleeve pre-filling, injection, and solidification. Optimization of the thermal die cycle and piston shot profile was achieved through simulation. Experimental validation confirmed that castings produced with CAE-optimized parameters exhibited improved mechanical properties. The optimal piston slow shot acceleration position was found to be 10 mm, and the optimal slow shot speed range was 0.4-0.6 m/s for the studied conditions.
- Academic Significance of the Research: The study provides a comprehensive methodology for simulating the entire HPDC process, addressing the limitations of previous research that focused on isolated aspects. The integration of experimental data (iHTCs) into the CAE model enhances its accuracy and predictive capability. The research demonstrates the value of a holistic CAE approach for understanding the complex interactions within the HPDC process and for optimizing process parameters.
- Practical Implications: The developed CAE methodology offers a systematic and cost-effective route for HPDC engineers to optimize casting parameters and operating conditions without extensive and costly empirical trials. By using this virtual engineering approach, manufacturers can reduce defects, improve casting quality, enhance mechanical properties, and potentially reduce material and energy consumption in HPDC processes. The findings regarding optimal piston shot profile parameters provide practical guidelines for process setup.
- Limitations of the Research: The prediction of air entrainment in ProCAST is noted as qualitative. While it provides a useful guide, it may not offer precise quantitative predictions of air entrapment levels. Further refinement and validation of the air entrainment model could be beneficial. The study focused on A356 alloy and a specific HPDC setup; the generalizability of the optimized parameters to other alloys and casting systems requires further investigation.
7. Future Follow-up Research:
- Directions for Follow-up Research:
- Further investigate the influence of various process parameters (beyond piston shot profile and thermal die cycle) on melt flow, solidification, and defect formation in HPDC using the developed CAE model.
- Explore and validate new techniques for suppressing defect formation in HPDC processes, potentially using CAE simulation to design and optimize these techniques before physical implementation.
- Conduct more detailed quantitative validation of the CAE model, particularly for defect prediction (e.g., porosity, air entrainment, oxides), comparing simulation results with experimental measurements.
- Areas Requiring Further Exploration:
- Deeper investigation into the complex interplay between melt flow characteristics, solidification behavior, and defect formation mechanisms in HPDC.
- Expanding the application of the comprehensive CAE model to a wider range of aluminum alloys and other die casting alloys (e.g., magnesium alloys).
- Developing more sophisticated and quantitatively accurate models for predicting defect formation, particularly air entrainment and oxide generation, in HPDC simulations.
- Integrating real-time process monitoring data with the CAE model for dynamic process control and optimization in HPDC.
8. References:
- [1] Zhou Y, Guo Z, Xiong SM. Effect of runner design on the externally solidified crystals in vacuum die-cast Mg-3.0Nd-0.3Zn-0.6Zr alloy. J. Mater. Process. Technol. 2019;267:366-75. https://doi.org/10.1016/j.jmatprotec.2018.12.032.
- [2] Gunasegaram DR, Givord M, O'Donnell RG, Finnin BR. Improvements engineered in UTS and elongation of aluminum alloy high pressure die castings through the alteration of runner geometry and plunger velocity. Mater. Sci. Eng. A. 2013;559: 276-86. https://doi.org/10.1016/j.msea.2012.08.09
- [3] Tsoukalas VD. The effect of die casting machine parameters on porosity of aluminium die castings. Int. J. Cast Met. Res. 2003;15:581-8. https://doi.org/ 10.1080/13640461.2003.11819544.
- [4] wu Wu M, bo Li X, peng Guo Z, mei Xiong S. Effects of process parameters on morphology and distribution of externally solidified crystals in microstructure of magnesium alloy die castings. China Foundry. 2018;15:139-44. https://doi.org/ 10.1007/s41230-018-7242-z.
- [5] Kwon HJ, Kwon HK. Computer aided engineering (CAE) simulation for the design optimization of gate system on high pressure die casting (HPDC) process. Robot. Comput. Integr. Manuf. 2019;55:147-53. https://doi.org/10.1016/j. rcim.2018.01.003.
- [6] Pereira GG, Cleary PW, Serizawa Y. Prediction of fluid flow through and jet formation from a high pressure nozzle using Smoothed Particle Hydrodynamics. Chem. Eng. Sci. 2018;178:12-26. https://doi.org/10.1016/j.ces.2017.1
- [7] Cleary PW, Ha J, Prakash M, Nguyen T. Short shots and industrial case studies: Understanding fluid flow and solidification in high pressure die casting. Appl. Math. Model. 2010. https://doi.org/10.1016/j.apm.2009.10.015.
- [8] Brůna M, Bolibruchová D, Pastirčák R. Reoxidation Processes Prediction in Gating System by Numerical Simulation for Aluminium Alloys. Arch. Foundry Eng. 2017; 17:23-6. https://doi.org/10.1515/afe-2017-0084.
- [9] Korti AIN, Abboudi S. Effects of shot sleeve filling on evolution of the free surface and solidification in the high-pressure die casting machine. Int. J. Met. 2017;11: 223-39. https://doi.org/10.1007/s40962-016-0051-5.
- [10] Dou K, Lordan E, Zhang YJ, Jacot A, Fan ZY. Numerical simulation of fluid flow, solidification and defects in high pressure die casting (HPDC) process, IOP Conf. Ser. Mater. Sci. Eng. 2019;529:012058. https://doi.org/10.1088/1757-899X/529/ 1/012058.
- [11] Gleeson J, Gourlay CM, Schaffer PL, Laukli HI. Gate microstructure in an AlSi9MgMn High-Pressure Die Casting. Proc. 12th Int. Conf. Alum. Alloy 2010: 751-6.
- [12] Cao H, Wessén M. Characteristics of microstructure and banded defects in die cast AM50 magnesium components. Int. J. Cast Met. Res. 2005;18:377-84. https://doi. org/10.1179/136404605225023216.
- [13] Hong Hai N. Effect of Pressure on Solidification Process and Mechanical Properties During Semi-Solid Casting by Computational Fluid Dynamics (CFD). Adv. Mater. 2019;7. https://doi.org/10.11648/j.am.20180702.15. 44.
- [14] Yuan Z, Guo Z, Xiong SM. Skin layer of A380 aluminium alloy die castings and its blistering during solution treatment. J. Mater. Sci. Technol. 2019;35:1906–16. https://doi.org/10.1016/j.jmst.2019.05.011.
- [15] Otarawanna S, Gourlay CM, Laukli HI, Dahle AK. Agglomeration and bending of equiaxed crystals during solidification of hypoeutectic Al and Mg alloys. Acta Mater. 2010;58:261-71. https://doi.org/10.1016/j.actamat.2009.09.002.
- [16] Wang BS, Xiong SM. Effects of shot speed and biscuit thickness on externaly solidified crystals of high-pressure diet cast AM60B magnesium alloy. Trans. Nonferrous Met. Soc. China (English Ed. 2011;21:767-72. https://doi.org/ 10.1016/S1003-6326(11)60778-4.
- [17] Jiao XY, Wang J, Liu C, Guo Z, Wang J, Wang Z, Gao J, Xiong SM. Influence of slow-shot speed on PSPs and porosity of AlSi 17 Cu 2.5 alloy during high pressure die casting. J. Mater. Process. Technol. 2019;268:63-9. https://doi.org/10.1016/j. jmatprotec.2019.01.008.
- [18] Yuan L, Xiong S, Liu B, Masayuki M, Yoshihide M, Shingo I. Numerical simulation and optimization of liquid metal flow in the shot sleeve of cold chamber die casting process. MCWASP Conf. Model. Cast. Welding, Adv. Solidif. Process. Opio, Fr. Miner. Met. Mater. Soc. 2006:111-8.
- [19] Wang QL, Xiong SM. Effect of multi-step slow shot speed on microstructure of vacuum die cast AZ91D magnesium alloy. Trans. Nonferrous Met. Soc. China (English Ed. 2015;25:375-80. https://doi.org/10.1016/S1003-6326(15)63613-5.
9. Copyright:
- This material is "K. Dou, E. Lordan, Y.J. Zhang, A. Jacot, Z.Y. Fan"'s paper: Based on "A complete computer aided engineering (CAE) modelling and optimization of high pressure die casting (HPDC) process".
- Paper Source: https://doi.org/10.1016/j.jmapro.2020.10.062
This material was summarized based on the above paper, and unauthorized use for commercial purposes is prohibited.
Copyright © 2025 CASTMAN. All rights reserved.