This article introduces the paper "About the impact on gravity cast salt cores in high pressure die casting and rheocasting".
1. Overview:
- Title: About the impact on gravity cast salt cores in high pressure die casting and rheocasting
- Authors: Andreas Schilling, Daniel Schmidt, Jakob Glück, Niklas Schwenke, Husam Sharabi, Martin Fehlbier
- Year: 2022
- Journal/Conference: Simulation Modelling Practice and Theory
- Keywords:
- Cast salt cores
- Lost core
- Core damage
- Rheocasting
- Flow-3D
- Simulation
- Core testing
- High pressure die casting
2. Research Background:
- Social/Academic Context:
- High pressure die casting (HPDC) accounts for 60% of aluminum castings and over half of non-ferrous castings in Germany.
- Increasing casting complexity with internal geometries, especially in e-mobility, demands new technologies beyond complex molds with sliders.
- Lost salt core technology offers an alternative to slide systems for creating internal geometries.
- Salt cores are advantageous due to water solubility, simplifying removal after casting.
- Limitations of Existing Research:
- Core viability is a decisive issue for process-safe use of salt cores.
- Core loading in die casting is mainly attributed to the flow velocity of the impinging melt.
- High mechanical demands are placed on cores due to high pressures and flow speeds in HPDC.
- Research Need:
- Explore alternative casting methods like rheocasting to lower melt temperature and potentially reduce core loading.
- Investigate the application of rheocasting technology to salt cores to improve component quality and core durability.
3. Research Objectives and Research Questions:
- Research Objective:
- To investigate whether rheocasting technology can be applied to salt cores.
- To assess if rheocasting can simultaneously improve component quality when using salt cores.
- Core Research Question:
- What is the impact of rheocasting on the durability of gravity cast salt cores in high pressure die casting compared to conventional high pressure die casting?
- Research Hypothesis:
- Salt cores used in rheocasting will experience reduced loads.
- Salt cores in rheocasting will exhibit increased core viability compared to conventional HPDC. (This is implied by the expected lower core loading in rheocasting).
4. Research Methodology:
- Research Design:
- Simulation study using Flow-3D fluid-structure-interaction (FSI) simulations.
- Experimental validation through three-point bending tests on salt cores.
- Comparison of simulation results with experimental data.
- Data Collection Method:
- Simulation: Numerical data on core loading, stress distribution, and energy transfer during mold filling in both conventional HPDC and rheocasting simulations.
- Experiment: Physical measurements of breaking strength and deformation of salt cores in three-point bending tests at 20 °C and 180 °C under different loading conditions (prism line load and area load).
- Analysis Method:
- FSI Simulation: Flow-3D Cast Version 5.0.1 was used to model mold filling and forces acting on the salt core. Rankine maximum-normal stress theory was used to predict core damage. Energy analysis was conducted to compare energy transfer to the core in different casting conditions.
- Three-point Bending Test: Modified three-point bending test was used to determine the failure-critical material data of salt cores. Tests were conducted at different temperatures and loading types to characterize core strength and deformation.
- Research Subject and Scope:
- Salt Core Geometry: A simple geometry with a total length of 60 mm, square cross-section (10 mm side length), and a middle part with a 6 mm side length and 20 mm length was used.
- Casting Processes: Conventional high pressure die casting and rheocasting were simulated and compared.
- Material: A356 (AlSi7Mg0,3) alloy and a salt mixture of 50 wt-% sodium chloride and 50 wt-% sodium carbonate for the core.
- Simulation Parameters: Piston speed of 6 m/s for conventional HPDC and 2 m/s for rheocasting. Melt temperature of 630 °C for conventional HPDC and 600 °C for rheocasting.
5. Major Research Findings:
- Core Research Findings:
- Rheocasting significantly reduces the load on salt cores compared to conventional HPDC.
- The highest core load occurs at the first impact of the melt.
- Core loads remain approximately constant during further mold filling after the initial impact.
- Salt cores in rheocasting show reduced stress levels, well below the failure limit observed in bending tests.
- Statistical/Qualitative Analysis Results:
- Bending Tests:
- Higher core temperature leads to a decreasing breaking load with triangular fin.
- Compression increases slightly at higher temperatures.
- Full load tests show higher breaking load and breaking elongation with higher variance.
- Fine-grained microstructure of the edge zone (0.8 - 1.0 mm thick) is decisive for bending strength.
- Breaking strength and compression data are presented in Fig. 5 for Prism 20°C, Prism 180°C, and Full face 20°C loading conditions.
- Simulation:
- Mesh dependency study showed that 0.5 mm mesh size for the salt core is a reasonable compromise between accuracy and computation time.
- Maximum normal stress in conventional HPDC (6 m/s piston speed) reaches up to 13 MPa immediately after melt impact (Fig. 10).
- Maximum normal stress in rheocasting (2 m/s piston speed) is significantly lower, around 2.3 MPa (Fig. 12).
- Calculated displacement in melt flow direction is 0.17 mm, comparable to bending test results.
- Energy analysis indicates lower energy transfer to the salt core in rheocasting.
- Bending Tests:
- Data Interpretation:
- Simulation results are consistent with the experimental bending test data, suggesting the simulation model is reasonably accurate.
- The significantly lower core loads in rheocasting, as indicated by simulations, suggest improved core viability compared to conventional HPDC.
- The initial melt impact is the most critical phase for core loading.
- Figure Name List:
- Fig. 1. Salt core geometry and casting die.
- Fig. 2. Modified three-point bending test.
- Fig. 3. Simulation model for the fluid structure interaction (FSI) calculation.
- Fig. 4. Detail of the core balance volume.
- Fig. 5. Breaking strength and compression resulting from three-point bending tests.
- Fig. 6. Sectional view of the salt core (6 x 6 mm) at 40x magnification.
- Fig. 7. Mesh dependency of the stresses in the salt core after the impact of the melt.
- Fig. 8. Balance volume of the salt core for energy consideration (purple).
- Fig. 9. Simulated impact of the melt on the salt core.
- Fig. 10. Stress condition on salt core surface immediately after the first impact of the melt.
- Fig. 11. Deformation of the salt core after first impact of the melt.
- Fig. 12. Stress condition on salt core surface immediately after the first impact of the semi solid melt.
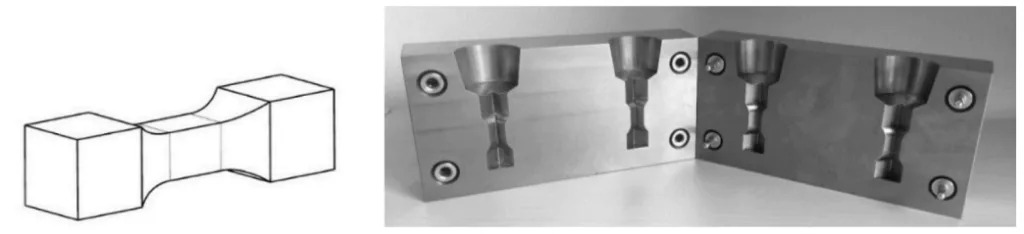
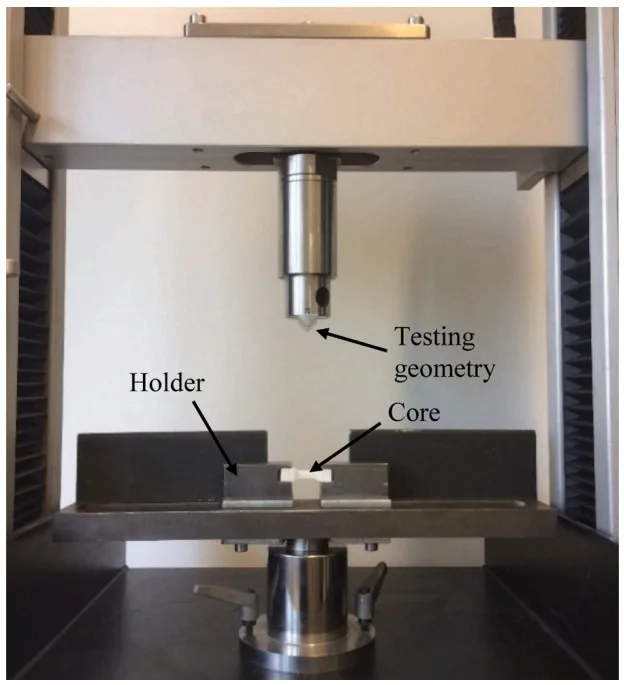
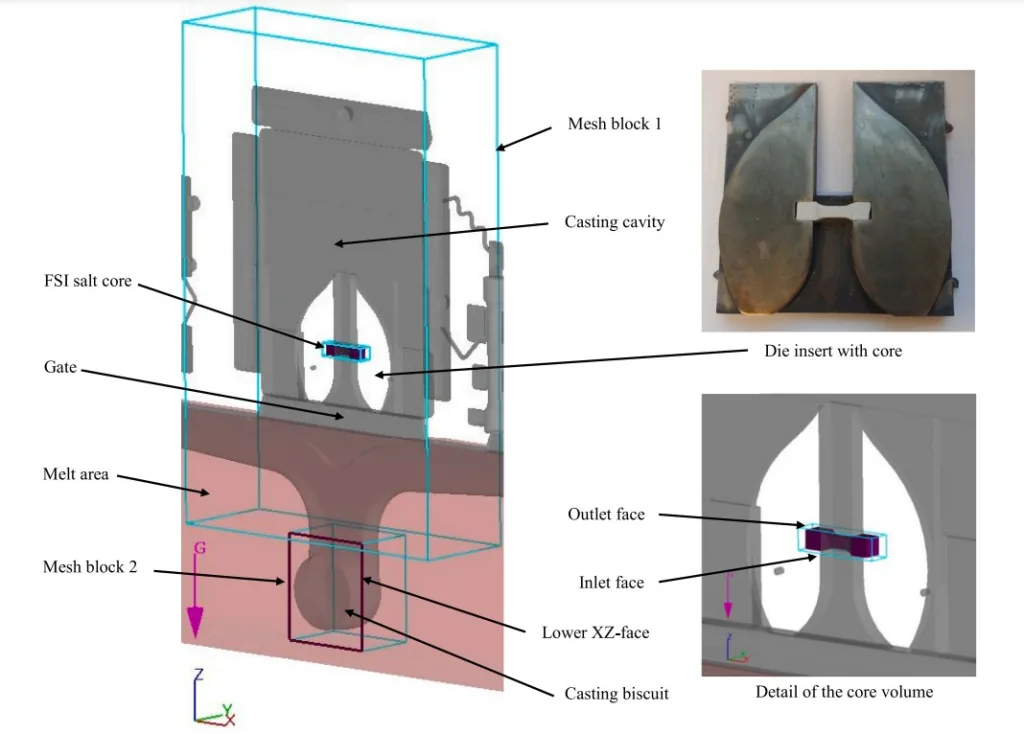
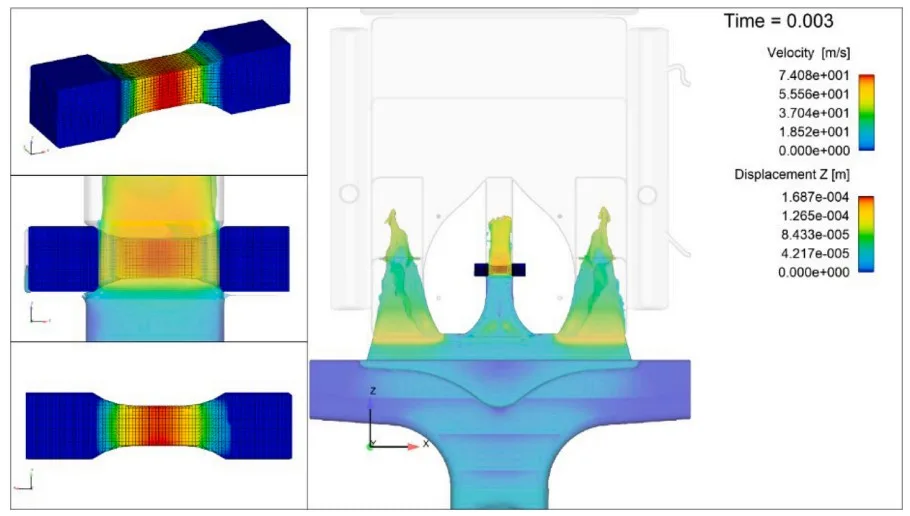
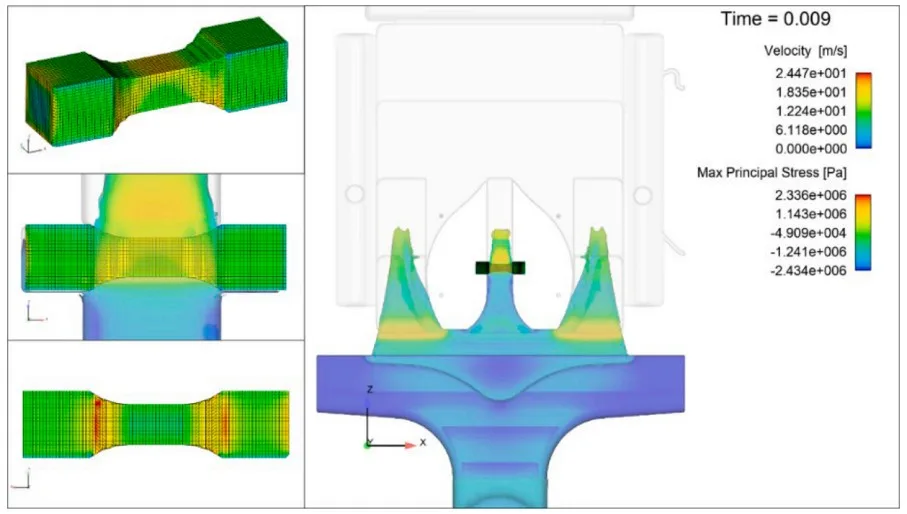
6. Conclusion and Discussion:
- Summary of Major Findings:
- Simulation results indicate that rheocasting significantly reduces the load on salt cores during die casting compared to conventional HPDC.
- The load from the impacting melt is directly related to piston speed and melt flow rate, with higher speeds leading to higher loads.
- In conventional HPDC (6 m/s piston speed), the tension on the salt core can reach around 13 MPa, exceeding the tensile strength of the salt core (11 MPa), suggesting potential core failure.
- In rheocasting (2 m/s piston speed), the maximum stress is significantly reduced to approximately 2.3 MPa, well below the tensile strength.
- Academic Significance:
- This study demonstrates the potential of rheocasting as a viable alternative to conventional HPDC for applications using lost salt core technology.
- The research provides valuable insights into the core loading mechanisms in both HPDC and rheocasting processes.
- The use of FSI simulation combined with experimental validation offers a robust methodology for analyzing and optimizing salt core die casting processes.
- Practical Implications:
- Rheocasting offers a promising approach to enhance the process safety and reliability of salt core die casting by reducing core damage.
- Lower core loads in rheocasting can potentially enable the production of more complex and delicate internal geometries using salt cores.
- The findings suggest that adjusting casting parameters, particularly piston speed and melt temperature in rheocasting, can significantly improve core viability.
- Limitations of the Research:
- The simulation model simplifies the casting process and assumes isothermal flow and homogeneous salt core material properties.
- The deformation speed in the three-point bending test (5 mm/min) is significantly slower than the deformation rate in the casting process (deformation occurs within about 0.001 s), which might affect the direct comparability of failure limits.
- Experimental verification of the simulation results in real casting trials is still needed.
7. Future Follow-up Research:
- Future Research Directions:
- Experimental validation of the simulation results through real die casting and rheocasting trials in a casting laboratory.
- Investigation of the influence of various rheocasting parameters on core loading and component quality.
- Exploration of different salt core materials and compositions to further enhance core strength and viability in rheocasting.
- Evaluation of the impact of rheocasting and salt core technology on the microstructure and overall quality of cast components.
- Areas that need further exploration:
- Detailed analysis of the solid phase formation and its influence on core loading in rheocasting.
- Optimization of salt core design and casting process parameters for rheocasting applications.
- Investigation of the long-term durability and performance of components produced using rheocasting and salt core technology.
8. References:
- [1] B. Nogowizin, Theorie Und Praxis des Druckgusses, Fachverlag Schiele&Schön, Berlin, 2011.
- [2] Jelínek, P.; Adámková, E.: Lost Cores for High-Pressure Die Casting, Archives of Foundry Engineering, 14(2) 101-104, 2014, doi:10.2478/afe-2014-0045.
- [3] B. Fuchs, Salzkerntechnologie Für Hohlgussbauteile im Druckguss, Cuvillier Verlag, PhD, Erlangen, Nürnberg, 2014.
- [4] D. Pierri, C. Beck, Lost Core-Technologie - offen für alle, Chancen und Grundlagen des Verfahrens, In: Giesserei, Jg 103 (2016), 10/2016, DVS Media GmbH, Düsseldorf.
- [5] J. Yaokawa, D. Miura, K. Anzai, Strength of Salt Core Composed of Alkali Carbonate and Alkali Chloride Mixtures Made by Casting Technique, Mater. Trans. 48 (5) (2007) 1034-1041.
- [6] Schilling, A. et al.: Approach on simulation of solidification and shrinkage of gravity cast salt cores, Simulation Modelling Practice and Theory, 107, 102231, 2021, ISSN 1569-190X, doi:10.1016/j.simpat.2020.102231.
- [7] Kohlstädt, S.; Vynnycky, M.; Goeke, S.: On the CFD Modelling of Slamming of the Metal Melt in High-Pressure Die Casting Involving Lost Cores, Metals 2021, 11 (1), 78, doi:10.3390/met11010078.
- [8] Uggowitzer, P.J.; Gullo, G.; Wahlen, A.: Metallkundliche Aspekte bei der semi-solid Formgebung von Leichtmetallen, In: Vom Werkstoff zum Bauteil, ed. H. Kaufmann und P.J. Uggowitzer, LKR-Verlag Ranshofen, 95-107, 2000.
- [9] P. Das, Rheological Characterization of Semi-Solid A356 Aluminium Alloy, In: Solid State Phenomena, Vols. 192-193, Trans Tech Publications, Switzerland, 2013, pp. 329-334.
- [10] Fickel, P.: Hohl- und Verbundguss von Druckgussbauteilen – Numerische Auslegungsmethoden und experimentelle Verifikation, PhD, Stuttgart, 2017.
- [11] R.K. Freier, Aqueous Solutions, Data Inorg. Org. Compd. 2 (1978). Supplements, Gruyter, Berlin.
9. Copyright and Source Material:
This summary is based on the paper "About the impact on gravity cast salt cores in high pressure die casting and rheocasting" by Andreas Schilling.
Paper Source: https://doi.org/10.1016/j.simpat.2022.102585
This summary is for informational purposes only and should not be used for commercial purposes without permission from the author.
Copyright © 2025 CASTMAN. All rights reserved.