This article introduces the paper "Thin-walled and large-sized magnesium alloy die castings for passenger car cockpit: Application, materials, and manufacture".
1. Overview:
- Title: Thin-walled and large-sized magnesium alloy die castings for passenger car cockpit: Application, materials, and manufacture
- Authors: Lei Zhan, Yu-meng Sun, Yang Song, Chun-hua Kong, **Kai Ma, Bai-xin Dong, Hong-yu Yang, Shi-li Shu, and *Feng Qiu
- Publication Year: 2024
- Journal/Conference: CHINA FOUNDRY Vol. 21 No. 5 September 2024
- Keywords: Mg alloys; thin wall; large size; automotive part; die casting
2. Research Background:
- Social/Academic Context of Research Topic: In order to effectively reduce energy consumption and increase range mile, new energy vehicles represented by Tesla have greatly aroused the application of integrated magnesium (Mg) alloy die casting technology in automobiles. Previously, the application of Mg alloys in automobiles, especially in automotive cockpit components, is quite extensive, while it has almost disappeared for a period of time due to its relatively high cost, causing a certain degree of information loss in the application technology of Mg alloy parts in automobiles. The rapid development of automotive technology has led to a higher requirement for the automotive components compared with those traditional one. Therefore, whatever the components themselves, or the Mg alloy materials and die casting process have to face an increasing challenge, needing to be upgraded. In addition, owing to its high integration characteristics, the application of Mg alloy die casting technology in large-sized and thin-walled automotive parts has inherent advantages and needs to be expanded urgently. Indeed, it necessitates exploring advance Mg alloys and new product structures and optimizing die casting processes.
- Limitations of Existing Research: While the paper doesn't explicitly state limitations of existing research, it implies a gap in current knowledge by mentioning "causing a certain degree of information loss in the application technology of Mg alloy parts in automobiles" in the introduction.
- Necessity of Research: This article summarizes and analyzes the development status of thin-walled and large-sized die casting Mg alloy parts in passenger car cockpit and corresponding material selection methods, die casting processes as well as mold design techniques. Furthermore, this work will aid researchers in establishing a comprehensive understanding of the manufacture of thin-walled and large-sized die casting Mg alloy parts in automobile cockpit. It will also assist them in developing new Mg alloys with improved comprehensive performance and new processes to meet the high requirements for die casting automotive components.
3. Research Objectives and Research Questions:
- Research Objective: The objective of this research is to summarize and analyze the development status of thin-walled and large-sized die casting Mg alloy parts in passenger car cockpits, along with corresponding material selection methods, die casting processes, and mold design techniques. Ultimately, it aims to provide researchers with a comprehensive understanding of the field and support the development of new Mg alloys and processes that meet the high-performance die casting requirements for automotive components in the future.
- Core Research Questions: While the paper doesn't explicitly list research questions, based on the research objectives, we can infer the following core questions:
- Which components in passenger car cockpits are suitable for thin-walled and large-sized Mg alloy die casting, and what is the application status of each component?
- What material properties are required for thin-walled and large-sized Mg alloy die casting parts, and which commercial Mg alloys are suitable?
- What are the appropriate die casting processes and conditions for manufacturing thin-walled and large-sized Mg alloy die casting parts?
- What are the mold design considerations for ensuring the quality of thin-walled and large-sized Mg alloy die casting parts?
- Research Hypothesis: There is no explicit research hypothesis stated in the paper.
4. Research Methodology
- Research Design: This research adopts a review article format rather than a specific research design. It comprehensively analyzes existing literature and research data to analyze the technological trends and key issues of thin-walled and large-sized Mg alloy die casting parts.
- Data Collection Methods: The research primarily collects and analyzes publicly available literature information, including academic papers, technical reports, and industry data. It does not involve specific experimental data collection or surveys.
- Analysis Methods: Based on the collected literature information, the research conducts technology trend analysis, material property comparison analysis, process technology analysis, and mold design technology analysis. The focus is on analyzing, comparing, and summarizing technical content rather than quantitative data analysis.
- Research Subjects and Scope: The research focuses on thin-walled and large-sized Mg alloy die casting parts among passenger car cockpit components. Specifically, it includes components such as seat frames, CCB (cross car beam), center console frames, and door inners. The research scope covers material selection, die casting processes, mold design, and surface treatment technologies.
5. Key Research Findings:
- Core Findings:
- Thin-walled and large-sized Mg alloy die casting parts are an effective solution for lightweighting passenger car cockpits, and their importance is increasing, especially in the field of new energy vehicles.
- Among passenger car cockpit components, seat frames, CCBs, and center console frames have relatively mature Mg alloy die casting technology applications, and the application scope is expanding to door inner and rear tailgate components.
- AM series alloys (AM50, AM60) are currently the most widely used materials for automotive cockpit die casting parts, but there is a growing demand for Mg alloys with higher mechanical properties. Mg-RE series alloys have excellent high-temperature properties, but their high cost is a disadvantage.
- Die casting process conditions and mold design have a significant impact on the quality of thin-walled and large-sized Mg alloy die casting parts, and optimized design and process control are crucial. In particular, thin-walled parts are prone to defects, requiring meticulous process management.
- Vacuum-assisted HPDC is an effective method to reduce porosity in Mg alloy die casting parts and improve mechanical properties.
- Surface treatment is essential to ensure the corrosion resistance of Mg alloy parts, and various surface treatment technologies (chemical conversion coating, anodizing, etc.) can be applied.
- Statistical/Qualitative Analysis Results:
- Comparative analysis of material properties (YS, UTS, Elongation) of various commercial Mg alloys (AZ91, AM50, AM60, WE43, WE54) is performed to present the advantages and disadvantages of each alloy and their application fields (Table 1, 2, 3).
- Analysis of the influence of die casting process variables (injection speed, mold temperature, pressure, etc.) on part quality, emphasizing the importance of setting optimal process conditions.
- Analysis of the influence of mold design elements (die cavity, gating system, runner, gate, rib, etc.) on part formability and quality, and presentation of optimal mold design solutions.
- Comparative analysis of pore distribution and mechanical properties of LA42 alloy castings between vacuum die casting and conventional HPDC to demonstrate the effectiveness of vacuum die casting (Fig. 11).
- Data Interpretation:
- Mg alloys have excellent properties such as lightweightness, rigidity, and strength, contributing to the lightweighting of automotive parts, but also have disadvantages such as low elongation, corrosion resistance, and high cost.
- Successful manufacturing of thin-walled and large-sized Mg alloy die casting parts requires comprehensive consideration of all factors, including material selection, process optimization, mold design, and surface treatment.
- It is expected that the application range of Mg alloy die casting parts in automobiles can be further expanded through technology development and cost reduction.
- Figure Name List:
- Fig. 1: First high-volume one-piece die cast Mg alloy CCB
- Fig. 2: Exploded view of the center console with conventional structure
- Fig. 3: Application of Mg alloys center console frame in automobile
- Fig. 4: Traditional seat back frame structure
- Fig. 5: Traditional seat cushion frame structure
- Fig. 6: Seat frame consisting of 5 Mg die casting parts
- Fig. 7: Images showing Mg alloy seat frame applications in 2015 Mercedes-Benz SLK seat
- Fig. 8: Typical Mg alloy seat back frame
- Fig. 9: Prototype of Mg alloy door inner die casting
- Fig. 10: Schematic of a cold chamber die-casting machine
- Fig. 11: Comparison of the LA42 alloy casting of HPDC and vacuum-assisted HPDC
- Fig. 12: Typical redundant materials on the part of Mg alloy die casting
- Fig. 13: Surface treatment process flow for Mg alloy die casting parts
- Fig. 14: Surface morphologies of AZ31 Mg alloy after anodizing at 3 V (a), 10 V (b), 20 V (c), 70 V (d), 80 V (e), and 100 V (f)
- Fig. 15: Typical surface defects of thin wall Mg alloy parts
- Fig. 16: Suggestions for the design of the die casting parts with uniform wall thickness
- Fig. 17: Some suggestions about how to layout the ribs on the die casting parts
- Fig. 18: Gating system of Mg alloy die castings
- Fig. 19: Different runner designs of Mg alloy die casting dies and their impact on filling process
- Fig. 20: Different gate system designs of Mg alloy die casting seat frame
![Fig. 1: First high-volume one-piece die cast Mg alloy CCB: (a) 3D data [18]; (b) CCB for GMC Savana and Chevrolet Express; (c) CCB for Buick LaCrosse [19]](https://castman.co.kr/wp-content/uploads/Fig.-1-First-high-volume-one-piece-die-cast-Mg-alloy-CCB-a-3D-data-18-b-CCB-for-GMC-Savana-and-Chevrolet-Express-c-CCB-for-Buick-LaCrosse-19-1024x334.webp)
![Fig. 2: Exploded view of the center console with conventional structure: (a) the shell itself is outer skin; (b) with a structural component inside [21]](https://castman.co.kr/wp-content/uploads/Fig.-2-Exploded-view-of-the-center-console-with-conventional-structure-a-the-shell-itself-is-outer-skin-b-with-a-structural-component-inside-21-1024x508.webp)
![Fig. 3: Application of Mg alloys center console frame in automobile: (a) Porsche [6]; (b) Volvo; (c) Hongqi](https://castman.co.kr/wp-content/uploads/Fig.-3-Application-of-Mg-alloys-center-console-frame-in-automobile-1024x648.webp)
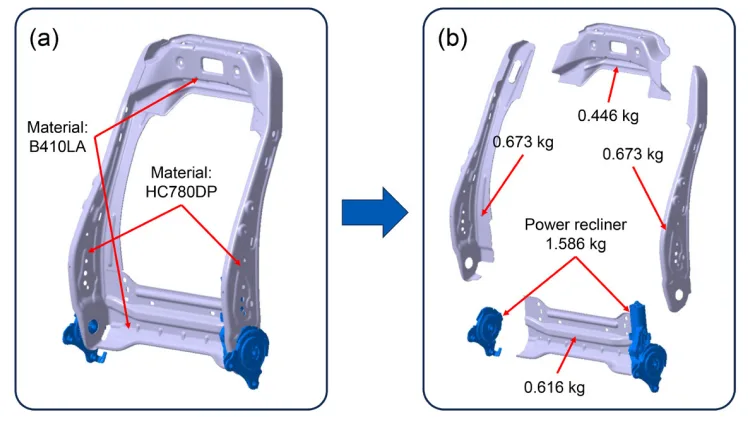
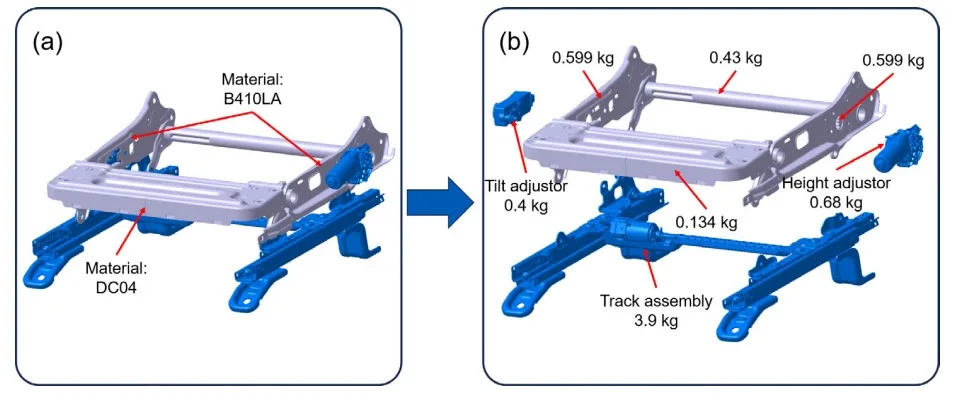
![Fig. 6: Seat frame consisting of 5 Mg die casting parts: (a) backrest; (b) cushion; (c) assembly [11]](https://castman.co.kr/wp-content/uploads/Fig.-6-Seat-frame-consisting-of-5-Mg-die-casting-parts-a-backrest-b-cushion-c-assembly-11.webp)
![Fig. 10: Schematic of a cold chamber die-casting machine (a), and stages of the shot profile for die casting process showing changes of melt pressure and plunger displacement versus time (b) [91]](https://castman.co.kr/wp-content/uploads/Fig.-10-Schematic-of-a-cold-chamber-die-casting-machine-a-and-stages-of-the-shot-profile-for-die-casting-process-showing-changes-of-melt-pressure-and-plunger-displacement-versus-time-b-91-1024x425.webp)
![Fig. 17: Some suggestions about how to layout the ribs on the die casting parts [127]](https://castman.co.kr/wp-content/uploads/Fig.-17-Some-suggestions-about-how-to-layout-the-ribs-on-the-die-casting-parts-127-1024x607.webp)
![Fig. 19: Different runner designs of Mg alloy die casting dies and their impact on filling process: (a) Y shape runner; (b) T shape runner; (c) radiation shape runner; (d) tracer particles during the filling simulation of the Y shape runner; (e) tracer particles during the filling simulation of the T shape runner [125]](https://castman.co.kr/wp-content/uploads/Fig.-19-Different-runner-designs-of-Mg-alloy-die-casting-dies-and-their-impact-on-filling-process-1024x606.webp)
![Fig. 20: Different gate system designs of Mg alloy die casting seat frame: (a) [134] and (b) [29] for backrest; (c) and (d) for cushion [25]](https://castman.co.kr/wp-content/uploads/Fig.-20-Different-gate-system-designs-of-Mg-alloy-die-casting-seat-frame.webp)
6. Conclusion and Discussion:
- Summary of Main Findings: The popularization of new energy vehicles has greatly promoted the development of lightweight technology, and the application of Mg alloys die casting is desirable in many lightweight technologies. Due to its relatively high integration, die casting technology is more suitable for the integrating of numerous small parts to form the thin-walled and large-sized parts, making a significant effect on the components lightweight. Technically, the suitable components, selection of Mg alloy materials, die casting process, and the design of die casting molds will greatly impact the quality of the final parts. Through the related research, following conclusions could be obtained: (The conclusions are the same as in the Korean summary, already provided in section 5. Key Research Findings - Core Findings)
- Academic Significance of Research: This study provides a comprehensive technical trend analysis of the application of thin-walled and large-sized Mg alloy die casting parts in automobile cockpits, and can contribute to setting the direction for future research and development. In particular, it enhances academic value by presenting technical challenges and solutions from various aspects such as materials, processes, and mold design.
- Practical Implications: This study provides useful information on the application of Mg alloy die casting technology to practitioners in the field of automotive part design and manufacturing. In particular, it increases the feasibility of practical application by presenting specific guidelines for thin-walled and large-sized part design, material selection, process condition setting, and mold design.
- Limitations of Research: This research is a review paper based on literature research, and lacks in-depth experimental verification for specific alloys or processes. In addition, analysis related to economic aspects such as cost, productivity, and recyclability is insufficient. Future research needs to address these limitations through in-depth studies.
7. Future Follow-up Research:
- Future Follow-up Research:
- Research on the development of low-cost and high-strength Mg-RE alloys
- Research on improving the performance of thin-walled and large-sized Mg alloy die casting parts (strength, elongation, corrosion resistance, fatigue properties, etc.)
- Research on die casting process optimization and elucidation of defect generation mechanisms (porosity, ESC, etc.)
- Research on integrated design and manufacturing technology for Mg alloy die casting parts (reduction of part count, simplification of assembly process)
- Research on recycling technology for Mg alloy die casting parts
- Areas Requiring Further Exploration:
- Evaluation of fatigue properties and durability of Mg alloy die casting parts
- Evaluation of creep properties and high-temperature reliability of Mg alloy die casting parts
- Evaluation of impact properties and safety of Mg alloy die casting parts
- LCA (Life Cycle Assessment) analysis and development of environmentally friendly manufacturing processes for Mg alloy die casting parts
8. References:
- [1] Polmear I J. Magnesium alloys and applications. Materials Science and Technology, 1994, 10(1): 1-16. https://doi. org/10.1179/mst.1994.10.1.1.
- [2] Eliezer D, Aghion E, Froes F H. Magnesium science, technology and applications. Advanced Performance Materials, 1998, 5: 201-212. https://doi.org/10.1023/A:1008682415141.
- [3] Wang G G, Weiler J P. Recent developments in highpressure die-cast magnesium alloys for automotive and future applications. Journal of Magnesium and Alloys, 2023, 11(1): 78-87. https://doi.org/10.1016/j.jma.2022.10.001.
- [4] Tan J, Ramakrishna S. Applications of magnesium and its alloys: A review. Applied Science, 2021, 11(5): 6861. https://doi. org/10.3390/app11156861.
- [5] Luo A A. Applications: Aerospace, automotive and other structural applications of magnesium. In: Fundamentals of Magnesium Alloy Metallurgy, Elsevier: Amsterdam, The Netherlands, 2013: 266-316. https://doi.org/10.1533/9780857097293.266.
- [6] Liu B, Yang J, Zhang X Y, et al. Development and application of magnesium alloy parts for automotive OEMs: A review. Journal of Magnesium and Alloys, 2023,11(1): 15-47. https://doi. org/10.1016/j.jma.2022.12.015.
- [7] Westengen H, Rashed H M M A. Magnesium alloys: Properties and applications. Reference Module in Materials Science and Materials Engineering, 2016: 1-9. 10.1016/B978-0-12-803581- 8.02568-6.
- [8] Kim S K, Yoo H J, Kim Y J. Research strategy for AM60 magnesium steering wheel. Magnesium Technology 2002, 2002: 247-254.
- [9] Kawase Y, Shinto H. Development of magnesium steering wheel. SAE: International Congress and Exposition, Detroit, Michigan, USA, 1991: 910549. https://doi.org/10.4271/910549.
- [10] Abate M, Willman M. Use of cast magnesium back frames in automotive seating. 2005 SAE World Congress, Detroit, Michigan, USA, 2005: 2005-1-0723. https://doi. org/10.4271/2005-01-0723.
- [11] Hector B, Heiss W. Magnesium die castings as structural members in the integral seat of the new Mercedes-Benz roadster. 1990 SAE International Congress and Exposition, Detroit, Michigan, USA, 1990: 900798. https://doi. org/10.4271/900798.
- [12] Cui X P, Zhang Y X, Liu H F, et al. Development and application of magnesium alloy seat back for passenger cars. Foundry, 2022, 71(5): 637-644. (In Chinese)
- [13] Gao Y K, Gao D W, Gao Y H. A study on magnesium alloy substitution design and analysis for automotive seat back frame. Advanced Materials Research, 2011, 156-157: 245-251. https://doi.org/10.4028/www.scientific.net/AMR.156-157.245.
- [14] Li N Y, Chen X M, Hubbert T, et al. 2005 Ford GT magnesium instrument panel cross car beam. 2005 SAE World Congress, Detroit, Michigan, USA, 2005: 2005-01-0341. https://doi. org/10.4271/2005-01-0341.
- [15] Fan S, Wang X, Wang G G, et al. Applications of high-pressure die casting (HPDC) magnesium alloys in industry. Magnesium Alloys-processing, Potential and Applications, IntechOpen, 2023: 15. http://dx.doi.org/10.5772/intechopen.110494.
- [16] Kulekci M K. Magnesium and its alloys applications in automotive industry. International Journal of Advance Manufacture Technology, 2008, 39: 851-865. https://doi.org/10.1007/s00170- 007-1279-2.
- [17] Ma Q. Study of numerical simulation and design of die casting mould for magnesium vehicle parts. Master’s Dissertation, Harbin: Harbin University of Science and Technology, 2005. (In Chinese)
- [18] Luo A A. Magnesium casting technology for structural applications. Journal of Magnesium and Alloys, 2013, 1(1): 2-22. https:// doi.org/10.1016/j.jma.2013.02.002.
- [19] Nehan M, Maloney R. Magnesium AM60B instrument panel structure for crashworthiness FMVSS 204 and 208 compliance. 1996 SAE international Congress & Exposition, Detroit, Michigan, USA, 1996: 960419. https://doi.org/10.4271/960419.
- [20] Jiang J. Design and analysis of Mg-Al alloy beam. Commercial Vehicle, 2022, 12: 84-85+100. https://doi.org/10.20042/ j.cnki.1009-4903.2022.12.003. (In Chinese)
- [21] Schmiedel I, Winklbauer D M, Pfeufer L. Interior concept with light centre console. ATZ Worldwide, 2015, 117: 24-27. https:// doi.org/10.1007/s38311-015-0169-8.
- [22] Powell B R, Luo A A. Krajewski P E. 7-magnesium alloys for lightweight powertrains and automotive bodies. Advanced Materials in Automotive Engineering, 2012: 150-209. https://doi. org/10.1533/9780857095466.150.
- [23] Li W, Kang S L, Wang H M. Based on the lightweight design of an electric vehicle console. Auto Sci-Tech., 2020, 3: 76-83. https://doi.org/10.3969/j.issn.1005-2550.2020.03.015. (In Chinese)
- [24] D’Errico F, Tauber M, Just M. Magnesium alloys for sustainable weight-saving approach: A brief market overview, new trends, and perspectives. Current Trends in Magnesium (Mg) Research, 2022: 1-33. https://doi.org/10.5772/intechopen.102777.
- [25] Ko Y J, Kim J J, Park S C, et al. Module design concept for lightweight automotive seats. Magnesium: Proceedings of the 6th International Conference Magnesium Alloys and Their Applications, Shenyang, China, 2005: 924-929. https://doi. org/10.1002/3527603565.ch143.
- [26] Ren W, Li D P, Wang Z W, et al. Design of magnesium alloy seating riser. In: Proc. 2023 Chongqing Foundry Annual Conference, Chongqing, China, 2023: 367-370. https://doi. org/10.26914/c.cnkihy.2023.009736. (In Chinese)
- [27] Polavarapu S. Topology and free-size optimization with multiple loading conditions for light weight design of die cast automotive backrest frame. Master’s Dissertation, Clemson, South Carolina, USA: Clemson University, 2008: 414. https://open.clemson.edu/ all_theses/414.
- [28] Fantetti N, Szczesniak M. High ductility magnesium seat back structure. 1994 SAE International Congress & Exposition, Detroit, Michigan, USA, 1994: 940404. https://doi.org/10.4271/940404.
- [29] Long Z G, Zhang L, Xing X L. Magnesium alloy frame for car seat. SAECCE2020, 2020, 2: 51-54. https://doi.org/10.26914/ c.cnkihy.2020.023532. (In Chinese)
- [30] Brambilla S, Perotti P. Die casted magnesium front seat frame: An application for small and medium size cars. 1997 SAE International Congress and Exposition, Detroit Michigan, USA, 1997: 970323. https://doi.org/10.4271/970323.
- [31] Weiler J P, Sweet C, Adams A, et al. Next generation magnesium liftgate-utilizing advanced technologies to maximize mass reduction in a high volume vehicle application. In: Proceedings of the 2016 IMA World Magnesium Conference, Rome, Italy, 2016.
- [32] Blanchard P J, Bretz G T, Subramanian S, et al. The application of magnesium die casting to vehicle closures. 2005 SAE World Congress, Detroit Michigan, USA, 2005: 2005-01-0338. https:// doi.org/10.4271/2005-01-0338.
- [33] Weiler J J. A review of magnesium die-castings for closure application. Journal of Magnesium and Alloys, 2019, 7: 297-304. https://doi.org/10.1016/j.jma.2019.02.005.
- [34] Jekl J, Auld J, Sweet C, et al. Development of a thin-wall magnesium side door inner panel for automobiles. In: Proceedings of the 2015 IMA World Magnesium Conference, Detroit Michigan, USA, 2015.
- [35] Jonason P, Nilsson P, Isacsson M. MAGDOOR-magnesium in structural application. SAE International Body Engineering Conference and Exposition, Detroit Michigan, USA, 1999: 1999- 01-3198. https://doi.org/10.4271/1999-01-3198.
- [36] Pan F S, Yang M B, Chen X H. A review on casting magnesium alloys: Modification of commercial alloys and development of new alloys. Journal of Materials Science & Technology, 2016, 32(12): 1211-1221. http://dx.doi.org/10.1016/j.jmst.2016.07.001.
- [37] Kubásek J, Dvorský D, Čavojský M, et al. WE43 magnesium alloy-material for challenging applications. Kovove Material, 2019, 57(3): 159-165. https://doi.org/10.4149/km_2019_3_159.
- [38] Maltais A, Dube D, Fiset M, et al. Improvements in the metallography of as-cast AZ91 alloy. Materials Characterization, 2004, 52(2): 103-119. https://doi.org/10.1016/j.matchar.2004.04.002.
- [39] Kiełbus A, Rzychoń T, Cibis R. Microstructure of AM50 die casting magnesium alloy. Journal of Achievements in Materials and Manufacturing Engineering, 2006, 18(1-2): 135-138.
- [40] Chadha G, Allison J E, Jones J W. The role of microstructure on ductility of die-cast AM50 and AM60 magnesium alloys. Metallurgical and Materials Transactions: A, 2007, 38A: 286- 297. https://doi.org/10.1007/s11661-006-9027-z.
- [41] Wang G G, Weiler J P. Recent developments in high-pressure die-cast magnesium alloys for automotive and future applications. Journal of Magnesium and Alloys, 2023, 11(1): 78-87. https:// doi.org/10.1016/j.jma.2022.10.001.
- [42] Park S S, Park Y S, Kim N J. Microstructure and properties of strip cast AZ91 Mg alloy. Metals and Materials International, 2002, 8(6): 551-554. https://doi.org/10.1007/BF03178256.
- [43] Zhao H L, Guan S K, Zheng F Y. Effects of Sr and B addition on microstructure and mechanical properties of AZ91 magnesium alloy. Journal of Material Research, 2007, 22(9): 2423-2429. https://doi.org/10.1557/JMR.2007.0331.
- [44] Candan S, Unal M, Koc E, et al. Effects of titanium addition on mechanical and corrosion behaviours of AZ91 magnesium alloy. Journal of Alloys and Compounds, 2011, 509(5): 1958-1963. https://doi.org/10.1016/j.jallcom.2010.10.100.
- [45] Afsharnaderi A, Malekan M, Emamy M, et al. Microstructure evolution and mechanical properties of the AZ91 magnesium alloy with Sr and Ti additions in the as-cast and as-aged conditions. Journal of Materials Engineering and Performance, 2019, 28: 6853–6863. https://doi.org/10.1007/s11665-019- 04396-2.
- [46] Khomamizadeh F, Naml B, Khoshkhooel S. Effect of rare-earth element additions on high-temperature mechanical properties of AZ91 magnesium alloy. Metallurgical and Materials Transactions: A, 2005, 36A: 3489-3494. https://doi.org/10.1007/s11661-005- 0022-6.
- [47] Cížek L, Greger M, Pawlica L, et al. Study of selected properties of magnesium alloy AZ91 after heat treatment and forming. Journal of Materials Processing Technology, 2004, 157-158: 466-471. https://doi.org/10.1016/j.jmatprotec.2004.07.149.
- [48] Zhu Y L, Liu F Y, Xin R L, et al. Improving mechanical properties of an AZ91 alloy by properly combining aging treatment and torsion deformation. Materials Science & Engineering: A, 2020, 779: 139156. https://doi.org/10.1016/j.msea.2020.139156.
- [49] Ma Y L, Chen Q J, Wang Y, et al. Research progress in casting magnesium alloys of AM family. Materials Reports, 2007, 8: 84-87. (In Chinese)
- [50] Tian Z, Song B, Liu Y B. Application and development of AM magnesium alloy in automobile industry. Automobile Technology & Material, 2004, 7: 21-23. (In Chinese)
- [51] Luo A A, Sachdev A K. 12-Applications of magnesium alloys in automotive engineering. Advances in Wrought Magnesium Alloys, 2012, 4: 393-426. https://doi.org/10.1533/9780857093844.3.39.
- [52] Luo A A, Renaud J, Nakatsugawa I, et al. Magnesium castings for automotive applications. JOM, 1995, 47: 28-31. https://doi. org/10.1007/BF03221226.
- [53] He F, Li J P, Yang Z. The microstructure and mechanical properties of as cast AM60-Ti magnesium alloy. Special Casting & Nonferrous Alloys, 2008, 3: 227-229. (In Chinese)
- [54] Zhang S, Song J F, Liao H X, et al. Effect of boron on the grain refinement and mechanical properties of as-cast Mg alloy AM50. Materials, 2019, 12: 1100. https://doi.org/10.3390/ma12071100.
- [55] Mert F, Özdemir A, Kainer K U, et al. Influence of Ce addition on microstructure and mechanical properties of high pressure die cast AM50 magnesium alloy. Transactions of Nonferrous Metals Society of China, 2013, 23(1): 66-72. https://doi.org/10.1016/ S1003-6326(13)62430-9.
- [56] Zhou G B. Effect of Y, Sb and Cd on microstructure and properties of AM50 magnesium alloy. Master’s Dissertation, Nanjing: Nanjing University of Aeronautics and Astronautics, 2012. (In Chinese)
- [57] Sevik H, Acikgoz S, Kurnaz S C. The effect of tin addition on the microstructure and mechanical properties of squeeze cast AM60 alloy. Journal of Alloys and Compounds, 2010, 508(1): 110-114. https://doi.org/10.1016/j.jallcom.2010.07.185.
- [58] Su G H, Zhang L, Cheng L R, et al. Microstructure and mechanical properties of Mg-6Al-0.3Mn-xY alloys prepared by casting and hot rolling. Transactions of Nonferrous Metals Society of China, 2010, 20(3): 383-389. https://doi.org/10.1016/ S1003-6326(09)60150-3.
- [59] Mao Z L, Huang X F, Chuang H J. Effect of neodymium on structure and mechanical properties of AM60 magnesium alloys. China Foundry Machinery & Technology, 2008, 1: 15-17. (In Chinese)
- [60] Wang L G, Zhang B F, Guan S K, et al. Effects of RE, B on microstructure and properties of AM60 alloy. Rare Metal Materials and Engineering, 2007, 36: 59-62. (In Chinese)
- [61] Zander D, Schnatterer C, Kuhnt C. Influence of heat treatments and Ca additions on the passivation behaviour of high-pressure die cast AM50. Materials and Corrosion, 2016, 66(12): 1519- 1528. https://doi.org/10.1002/maco.201508273.
- [62] Hoseini S M B, Malekan M, Emamy M, et al. Microstructure, tensile and bending behaviour of the as-cast AM50 alloy modified with different antimony and copper additions. Materials Science and Technology, 2021, 37(1): 86-102. https://doi.org/10. 1080/02670836.2020.1866847.
- [63] Mert F, Blawert C, Kainer K U, et al. Influence of cerium additions on the corrosion behaviour of high pressure die cast AM50 alloy. Corrosion Science, 2012, 65: 145-151. https://doi. org/10.1016/j.corsci.2012.08.011.
- [64] Itoh D, Terada Y, Sato T. Effect of calcium additions on creep properties of a die-cast AM50 magnesium alloy. Materials Transactions, 2008, 49(9): 1957-1962. https://doi.org/10.2320/ matertrans.MAW200830.
- [65] Teimoory F S, Emamy M, Malekan M. Effect of Pr on the grain refinement and mechanical properties of AM50 alloy in as-cast condition. AIP Conference Proceedings, Kish Island, Iran, 2018, 1920(1): 020016. https://doi.org/10.1063/1.5018948.
- [66] Yang M, Liu Y H, Song Y L. Corrosion and mechanical properties of AM50 magnesium alloy after being modified by 1 wt.% rare earth element gadolinium. Journal of Rare Earths, 2014, 32(6): 558-563. https://doi.org/10.1016/S1002-0721(14)60108-3.
- [67] Zhao P, Wang Q, Zhai C, et al. Effects of strontium and titanium on the microstructure, tensile properties and creep behavior of AM50 alloys. Materials Science and Engineering: A, 2007, 444(1-2): 318-326. https://doi.org/10.1016/j.msea.2006.08.111.
- [68] Fechner D, Maier P, Hort N, et al. Development of a magnesium recycling alloy based on AM50. Materials Science Forum, 2007, 539-543: 108-113. https://doi.org/10.4028/www.scientific.net/ MSF.539-543.108.
- [69] Matsubara H, Ichige Y, Fujita K, et al. Effect of impurity Fe on corrosion behavior of AM50 and AM60 magnesium alloys. Corrosion Science, 2013, 66: 203-210. https:// doi.org/10.1016/ j.corsci.2012.09.021.
- [70] Yang M, Liu Y H, Liu J A, et al. Effect of T6 heat treatment on corrosion resistance and mechanical properties of AM50 magnesium alloy. Materials Research Innovations, 2015, 19: S10-259-S10-264. https:// doi.org/10.1179/143289171 5Z.0000000002160.
- [71] Qiu X, Yang Q, Guan K, et al. Microstructures and tensile properties of Mg-Zn-(Gd)-Zr alloys extruded at various temperatures. Rare Metals, 2017, 36(12): 962-970. https://doi. org/10.1007/s12598-017-0966-x.
- [72] Wang G, Guo C X, Pang S J. Thermal stability, mechanical properties and corrosion behavior of a Mg-Cu-Ag-Gd metallic glass with Nd addition. Rare Metals, 2017, 3: 183-187. https:// doi.org/10.1007/s12598-017-0885-x.
- [73] Jiang H S, Qiao X G, Zheng M Y, et al. The partial substitution of Y with Gd on microstructures and mechanical properties of as-cast and as-extruded Mg-10Zn-6Y-0.5Zr alloy. Materials Characterization, 2018, 135: 96-103. https://doi.org/10.1016/ j.matchar.2017.11.025.
- [74] Yu H H, Li C Z, Xin Y C, et al. The mechanism for the high dependence of the Hall-Petch slope for twinning/slip on texture in Mg alloys. Acta Materialia, 2017, 128: 313-326. https://doi. org/10.1016/j.actamat.2017.02.044.
- [75] Li Y F, Zhang A, Li C M, et al. Recent advances of high strength Mg-RE alloys: Alloy development, forming and application. Journal of Materials Research and Technology, 2023, 26: 2919- 2940. https://doi.org/10.1016/j.jmrt.2023.08.055.
- [76] King J F. Development of practical high temperature magnesium casting alloys. Magnesium Alloys and their Applications, WileyVCH Verlag GmbH & Co. KGaA, 2006: 14-22. https://doi. org/10.1002/3527607552.ch3.
- [77] Nie J F. Precipitation and hardening in magnesium alloys. Metallurgical and Materials Transactions: A, 2012, 43: 3891- 3939. https://doi.org/10.1007/s11661-012-1217-2.
- [78] Kang Y H, Huang Z H, Wang S C, et al. Effect of pre-deformation on microstructure and mechanical properties of WE43 magnesium alloy II: Aging at 250 and 300 °C. Journal of Magnesium and Alloys, 2020, 8(1): 103-110. https://doi.org/10.1016/ j.jma.2019.11.012.
- [79] Li J L, Chen R S, Ma Y Q, et al. Effect of Zr modification on solidification behavior and mechanical properties of Mg-Y-RE (WE54) alloy. Journal of Magnesium and Alloys, 2013, 1(4): 346-351. https:// doi.org/10.1016/j.jma.2013.12.001.
- [80] Gui Y W, Li Q A, Chen J. Effects of Sm content on microstructures and mechanical properties of casting Mg-Y-Nd-Sm-Zr alloys. Materials Research Express, 2018, 5(7): 076515. https:// iopscience.iop.org/article/10.1088/2053-1591/aad07e.
- [81] Li J L, Ma Y Q, Chen R S, et al. Effects of shrinkage porosity on mechanical properties of a sand cast Mg-Y-RE (WE54) alloy. Materials Science Forum, 2013, 747-748: 390-397. https://doi. org/10.4028/www.scientific.net/MSF.747-748.390.
- [82] Zhan L, Sun J, He J G, et al. Research status on the lightweight of the automotive seat. Automobile Parts, 2015, 11: 68-73. 10.19466/j.cnki.1674-1986.2015.11.019. (In Chinese)
- [83] Lee H S, Kim J H, Kang G S, et al. Development of seat side frame by sheet forming of DP980 with die compensation. International Journal of Precision Engineering and Manufacturing, 2017, 18: 115-120. https://doi.org/10.1007/s12541-017-0014-7.
- [84] Oh W J, Lee C M. A study on the sheet forming of the lower seat rail using 1180 TRIP steel. International Journal of Precision Engineering and Manufacturing, 2018, 19: 299-302. https://doi. org/10.1007/s12541-018-0036-9.
- [85] Forsmark J H, Boileau J, Houston D, et al. A microstructural and mechanical property study of an AM50 HPDC magnesium alloy. International Journal of Metalcasting, 2012, 6: 15-26. https://doi. org/10.1007/BF03355474.
- [86] Wang X J, Zhu S M, Easton M A, et al. Heat treatment of vacuum high pressure die cast magnesium alloy AZ91. International Journal of Cast Metals Research, 2014, 27(3): 161-166. https://doi.org/10.1179/1743133613Y.0000000091.
- [87] Suman C. Heat treatment of magnesium die casting alloys AZ91D and AM60B. 1989 SAE International Congress and Exposition, Detroit, Michigan, USA, 1989: 890207. https://doi. org/10.4271/890207.
- [88] Tański1 T, Dobrzański L A, Čížek L. Influence of heat treatment on structure and properties of the cast magnesium alloys. Advanced Materials Research, 2007, 15-17: 491-496. https:// doi.org/10.4028/www.scientific.net/AMR.15-17.491.
- [89] Fu P H, Luo A A, Jiang H Y, et al. Low-pressure die casting of magnesium alloy AM50: Response to process parameters. Journal of Materials Processing Technology, 2008, 205(1-3): 224-234. https://doi.org/10.1016/j.jmatprotec.2007.11.111.
- [90] Luo A A, Sachdev A K, Powell B R. Advanced casting technologies for lightweight automotive applications. China Foundry, 2010, 7(4): 248-254.
- [91] Czerwinski F. Magnesium injection molding. Springer New York, NY, 2008. https://doi.org/10.1007/978-0-387-72528-4.
- [92] Vinarcik E J. High integrity die casting processes. John Wiley & Sons, Inc., New York, 2003.
- [93] Vanli A S, Akdogan A, Sonmez H. Investigation the effects of process parameters on product quality in cold chamber high pressure die casting of magnesium alloys. International Journal of Arts and Sciences, 2010, 3(9): 320-325.
- [94] ASM Handbook Committee. Properties and selection: Nonferrous alloys and special purpose materials. ASM Handbook, 1990, Volume 2. https://doi.org/10.31399/asm. hb.v02.9781627081627
- [95] Aghion E, Moscovitch N, Arnon A. The correlation between wall thickness and properties of HPDC magnesium alloys. Materials Science and Engineering: A, 2007, 447(1-2): 341-346. https:// doi.org/10.1016/j.msea.2006.10.065.
- [96] Woo S H, Han B S, Yoo H J, et al. Development of magnesium seat frames using the vacuum die casting process. Journal of Korean Society for Precision Engineering, 2009, 26: 88-97.
- [97] Uchida M. Development of vacuum die casting process. China Foundry, 2009, 6(2): 137-144.
- [98] Li Z X, Zhang W C, Li D J, et al. Effect of vacuum-assisted die casting on the thermal conductivity and mechanical properties of LA42 magnesium alloy. Special Casting & Nonferrous Alloys, 2023, 43: 590-595. https://doi.org/10.15980/j.tzzz.2023.05.003. (In Chinese)
- [99] Brown Z, Luo A A, Musser M, et al. Development of supervacuum die casting process for magnesium alloys. North American Die Casting Association Transactions, 2009, T09-043: 723-729.
- [100] Yuan J, Zhao B H. Effects of post treatment on deformation of die casting generator bracket. Special Casting & Nonferrous Alloys, 2010, 30: 645-648. (In Chinese)
- [101] Liang C S, Yu L L, Xie Y J. Discussion on the application of trimming die in die casting products. In: Proc. 2023 Chongqing Foundry Annual Conference, Chongqing, 2011: 291-292. https://doi.org/10.26914/c.cnkihy.2023.009736. (In Chinese)
- [102] Sayak R B E E. Investigation of flash-free die casting by overflow design optimization. Master’s Dissertation, Columbus, Ohio, USA: The Ohio State University, 2014.
- [103] Wu W, Huang Z L. The ways to reduce the flashes and improve the accuracy of die casting. Special Casting & Nonferrous Alloys, 1998(Supplement): 43-45. (In Chinese)
- [104] Wu L P, Zhao J J, Xie Y P, et al. Progress of electroplating and electroless plating on magnesium alloy. Transactions of Nonferrous Metals Society of China 2010, 20(supplement 2): s630-s637. https://doi.org/10.1016/S1003-6326(10)60552-3.
- [105] Seifzadeh D, Rajabalizadeh Z. Environmentally-friendly method for electroless Ni-P plating on magnesium alloy. Surface and Coatings Technology, 2013, 218: 119-126. https://doi. org/10.1016/j.surfcoat.2012.12.039.
- [106] Wang Z C, Jia F, Yu L, et al. Direct electroless nickel-boron plating on AZ91D magnesium alloy. Surface & Coatings Technology, 2012, 206(17): 3676-3685. https://doi.org/10.1016/ j.surfcoat.2012.03.020.
- [107] Saji V S. Review of rare-earth-based conversion coatings for magnesium and its alloys. Journal of Materials Research and Technology, 2019, 8(5): 5012-5035. https://doi.org/10.1016/ j.jmrt.2019.08.013.
- [108] Pommiers B S, Frayret J, Uhart A, et al. Determination of the chemical mechanism of chromate conversion coating on magnesium alloys EV31A. Applied Surface Science, 2014, 298: 199–207. https://doi.org/10.1016/j.apsusc.2014.01.162.
- [109] Guo Y, Frankel G S. Characterization of trivalent chromium process coating on AA2024-T3. Surface and Coatings Technology, 2012, 206(19-20): 3895-3902. https://doi. org/10.1016/j.surfcoat.2012.03.046.
- [110] Ogle K, Tomandl A, Meddahi N, et al. The alkaline stability of phosphate coatings I: ICP atomic emission spectroelectrochemistry. Corrosion Science, 2004, 46(4): 979- 995. https://doi.org/10.1016/S0010-938X(03)00182-3.
- [111] Jiang L, Wolpers M, Volovitch P, et al. The degradation of phosphate conversion coatings by electrochemically generated hydroxide. Corrosion Science, 2012, 55: 76-89. https://doi. org/10.1016/j.corsci.2011.10.004.
- [112] Jian S Y, Chu Y R, Lin C S. Permanganate conversion coating on AZ31 magnesium alloys with enhanced corrosion resistance. Corrosion Science, 2015, 93: 301-309. https://doi. org/10.1016/j.corsci.2015.01.040.
- [113] Liang C S, Lv Z F, Zhu Y L, et al. Protection of aluminium foil AA8021 by molybdate-based conversion coatings. Applied Surface Science, 2014, 288: 497-502. https://doi.org/10.1016/ j.apsusc.2013.10.060.
- [114] Dabalà M, Armelao L, Buchberger A, et al. Cerium-based conversion layers on aluminum alloys. Applied Surface Science, 2001, 172: 312-322. https://doi.org/10.1016/S0169- 4332(00)00873-4.
- [115] Rudd A L, Breslin C B, Mansfeld F. The corrosion protection afforded by rare earth conversion coatings applied to magnesium. Corrosion Science, 2000, 42(2): 275-288. https:// doi.org/10.1016/S0010-938X(99)00076-1.
- [116] Rocca E, Juers C, Steinmetz J. Corrosion behavior of chemical conversion treatments on as-cast Mg-Al alloys: Electrochemical and non-electrochemical methods. Corrosion Science, 2010, 52(6): 2172-2178. https://doi.org/10.1016/j.corsci.2010.02.036.
- [117] Zhou W Q, Shan D Y, Han E H, et al. Structure and formation mechanism of phosphate conversion coating on die cast AZ91D magnesium alloy. Corrosion Science, 2008, 50(2): 329-337. https://doi.org/10.1016/j.corsci.2007.08.007.
- [118] Hawke D, Albright A. A phosphate-permanganate conversion coating for magnesium. Metal Finishing, 1995, 93(10): 34-38. https://doi.org/10.1016/0026-0576(96)80428-4.
- [119] Salman S A, Okido M. 8-anodization of magnesium (Mg) alloys to improve corrosion resistance. Corrosion Prevention of Magnesium Alloys, 2013: 197-231. https://doi.org/10.1533/978 0857098962.2.197.
- [120] Blawert C, Dietzel W, Ghali E, et al. Anodizing treatments for magnesium alloys and their effect on corrosion resistance in various environments. Advanced Engineering Materials, 2006, 8(6): 511-533. https://doi.org/10.1002/adem.200500257.
- [121] Salman S A, Mori R, Ichino R, et al. Effect of anodizing potential on the surface morphology and corrosion property of AZ31 magnesium alloy. Materials Transactions, 2010, 51(6): 1109-1113. https://doi.org/10.2320/matertrans.M2009380.
- [122] Wu C S, Zhang Z, Cao F H, et al. Study on the anodizing of AZ31 magnesium alloys in alkaline borate solutions. Applied Surface Science, 2007, 253: 3893-3898. https://doi. org/10.1016/j.apsusc.2006.08.020.
- [123] Chen R S, Lu G D. Design key points and material selection of the magnesium alloy die casting mold. MW Metal Forming, 2011, 3: 26-27. (In Chinese)
- [124] Friedrich H E, Mordike B L. 6 technology of magnesium and magnesium alloys. In: Magnesium Technology, Springer, Berlin, Heidelberg, 2006: 219-430. https://doi.org/10.1007/3-540- 30812-1_6.
- [125] Timelli G, Capuzzi S, Bonollo F. Optimization of a permanent step mold design for Mg alloy castings. Metallurgical and Materials Transactions: B, 2015, 46: 473-484. https://doi. org/10.1007/s11663-014-0197-6.
- [126] Wang J D, Lu C, Ding W J. Key technologies for the design of Mg alloy die casting and die. Special Casting & Nonferrous Alloys, 2002, 2: 24-26+2. https://doi.org/10.15980/ j.tzzz.2002.02.011. (In Chinese)
- [127] Tan G Y. Structure design principles of die-casts for automobile use. Special Purpose Vehicle, 2000, 3: 40-41+47. (In Chinese)
- [128] Renner F, Zenner H. Fatigue strength of die-cast magnesium components. Fatigue & Fracture of Engineering Materials & Structures, 2002, 25: 1157-1168. https://doi.org/10.1046/ j.1460-2695.2002.00607.x.
- [129] Shawki G S A, Kandeil A Y. A review of design parameters and machine performance for improved die casting quality. Journal of Mechanical Working Technology, 1988, 16(3): 315-333. https://doi.org/10.1016/0378-3804(88)90059-9.
- [130] Chavan R, Kulkarni P S. Die design and optimization of cooling channel position for cold chamber high pressure die casting machine. IOP Conference Series: Materials Science and Engineering, 2020, 810: 012017. https://doi.org/10.1088/1757- 899X/810/1/012017.
- [131] Zhao K P. Simulation and optimization of gating system of die casting die for magnesium alloy AM60B part. Die & Mould Industry, 2008, 1: 53-56. https://doi.org/10.16787/ j.cnki.1001-2168.dmi.2008.01.015. (In Chinese)
- [132] Zhang Y W, Cheng T S. Automobile weight lightening and Mg-alloy mold. Automobile Technology & Material, 2003, 11: 1-4. (In Chinese)
- [133] Jadhav A R, Hujare D P, Hujare P P. Design and optimization of gating system, modification of cooling system position and flow simulation for cold chamber high pressure die casting machine. Materials Today: Proceedings, 2021, 46(17): 7175-7181. https://doi.org/10.1016/j.matpr.2020.11.346.
- [134] Han J L. Numerical design of Mg seat frame and its die-casting process optimization. Master’s Dissertation, Chongqing: Chongqing University, 2008. (In Chinese)
9. Copyright:
This material is based on Feng Qiu's paper: Thin-walled and large-sized magnesium alloy die castings for passenger car cockpit: Application, materials, and manufacture.
Paper Source: https://doi.org/10.1007/s41230-024-4100-z
This material is a summarized version of the above paper, and unauthorized use for commercial purposes is prohibited.
Copyright © 2025 CASTMAN. All rights reserved.
Thin-walled and large-sized magnesium alloy die castings for passenger car cockpit-Application, materials, and manufactureDownload