- Technical Paper
- Open access
- Published: 17 May 2024
- Cite this article
You have full access to thisopen accessarticle
International Journal of MetalcastingAims and scopeSubmit manuscript
- Lukas Bruckmeier ORCID:orcid.org/0009-0001-9741-95311,
- Aron Ringel2,
- Marvin Erck3,
- David Bailly2,
- Kirsten Bobzin3,
- Hendrik Heinemann3 &
- Andreas Bührig-Polaczek1
- 205 Accesses
- Explore all metrics
Abstract
Lightweight design can reduce CO2 emissions and improve energy efficiency, especially in the fuel-intensive transportation sector. Multi-material design approaches can combine specific properties of materials for effective lightweight design. A multi-material component made from two metals used widely in industry could combine the exceptionally lightweight properties of aluminum with the strength and structural integrity of steel. However, joining aluminum and steel is a challenge due to their different thermo-physical properties and the possible formation of brittle intermetallic phases. In hybrid casting, aluminum is cast around a steel sheet insert in a high-pressure die casting process to produce complex parts. In a first approach, a cold gas sprayed aluminum coating on the insert was tested as a bonding agent between the steel substrate and the molten aluminum. The joint was achieved by a combination of metallurgical bonding and micro-clamping. As a second option, surface structures with undercuts were applied to the steel sheet by modified cold rolling, which allowed the molten aluminum to flow into the channels and interlock with the solid steel. Different orientations of the structure on the insert were tested. In addition, the combination of both approaches was used to potentially enhance the positive effect of the pretreatment techniques. Given the critical importance of joint strength, the quality of these approaches was tested by static tensile tests and dynamic fatigue tests. The results show that the joint by coatings is strongly influenced by the process temperature. The improvement of the joint by the surface structure depends on its orientation to the melt flow.
Similar content being viewed by others
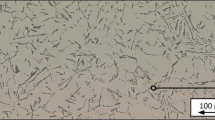
Influence of solidification rates and heat treatment on the mechanical performance and joinability of the cast aluminium alloy AlSi10Mg
Article Open access 23 January 2022
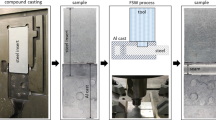
Hybrid joining of cast aluminum and steel by compound casting and friction stir welding
Article 16 January 2023
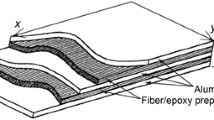
Process Design for Hybrid Sheet Metal Components
Article 12 December 2015
Use our pre-submission checklist
Avoid common mistakes on your manuscript.
Introduction
To meet the requirements for energy efficient innovations in the aerospace and automotive industries, significant weight reduction is essential. Lightweight design can reduce CO2 emissions or increase the range of vehicles. One way to achieve lightweight design is to develop multi-material components.1 Such components combine the advantageous properties of different materials. A common application is multi-material components made of versatile steel and aluminum used in car bodies or aircrafts. The combination of the strength and ductility of steel with the low density of aluminum offers great potential for lightweight design. The dissimilar thermo-physical and metallurgical properties and the formation of brittle intermetallic phases of aluminum and steel do not allow the use of common joining techniques such as fusion welding.2 Therefore, multi-material components made of steel and aluminum require new joining techniques,3 which enable a reliable connection with a gap free joint.
State of the Art
Joining of dissimilar materials is often achieved by forming processes, which can be divided into metallurgical and mechanical joining processes.4 Processes such as cold or friction stir welding allow metallurgical joining without the problems of conventional fusion welding. In processes such as clinching, riveting or hemming, the materials are deformed to produce a mechanical interlock. However, these processes are usually limited in their design flexibility or provide only localized connections. For complex geometries of the composite part, hybrid casting with metals offers great potential.5 Known from hybrid molding with polymers6 the process usually consists of two steps: a pretreatment of the solid insert and an assembly with the liquid component. A connection can be reached by a mechanical interlock, which requires a surface structuring of the insert. This includes subtractive processes such as micromachining,7 perforations,8 stamping,9 or electron and laser beam sculpturing10 and additive processes like selective laser melting to create ball-head pins11 or nanospikes12 on the insert surface. Additionally, hybrid casting offers the possibility for metallurgical bonding. By the use of different coatings on the steel insert a shear bond strength of 7.7 MPa was achieved to an aluminum cast.13
In this work, a high-pressure die casting (HPDC) process was used to produce structural components by inserting formed parts made of steel sheet directly into the casting mold and casting around them with molten aluminum.14 The short solidification times in the die casting process14 and the different expansion behavior of aluminum and steel15 complicate the joining process. On the other hand, the risk of formation of intermetallic phases is negligible due to the short process times. In order to create a large-area joint instead of local joints, thermally sprayed (TS)16 coatings and surface structures with undercuts17 have been investigated.
Surface-brazed Cu coatings and cold gas sprayed (CGS) EN AW-7075 coatings have been investigated as an approach to increase the bond adhesion in composite casting applications.16,18 In this work, a comprehensive analysis of the coating morphology and properties was performed and it was found, that TS is well suited to apply coatings for HPDC applications. For coatings made of EN AW-7075, bonding to the steel substrate was achieved by mechanical micro-clamping. It was shown that heat treatment of the investigated coatings can lead to a significant increase in ductility.19 Finally, the metallurgical bonding of the aluminum die casting with the coating is achieved by diffusion processes between liquid metal and solid coating. In this way, the joining of steel and aluminum die casting is made possible. Laboratory-scale tests were carried out on the production of composite castings and the composite zone was observed in cross section. First results already indicated a high potential of these coatings. In,20 the wetting behavior of the aluminum die casting alloy was investigated on the uncoated and the coated component. Due to the coating, a significantly smaller wetting angle could be achieved, which is a positive effect for HPDC applications.
In the alternative multi-pass rolling process, a profiled roller imprints a rectangular channel structure in the first pass (Fig. 1). In the consecutive pass, the ribs are flattened by a flat roller. The rib tips spread out horizontally, thus creating the undercut for interlocking with the die cast melt.17
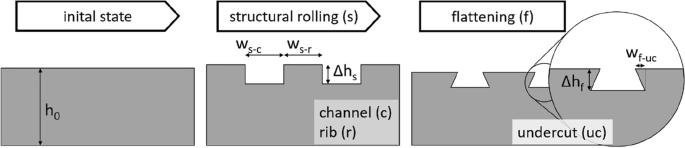
The die cast metal can flow into the channels and an interlocking connection is established as soon as it solidifies. In addition, the interlocking can counteract the shrinkage of the aluminum melt.16 The resulting joint strength is decisively depending on the undercut width \({w}_{f-uc}\). The results of shear tests on laboratory-scale specimens have shown a maximum bond strength of 45 MPa.21 Furthermore, the formability of cold sprayed EN AW-7075 coatings has been investigated by cold rolling, where thickness reductions of up to 16% have been reached.22
For the transfer and further investigation of the different joining processes in hybrid casting, an industry-oriented demonstrator part for the high-pressure die casting process was developed by the Foundry Institute (GI) (Figure 2e).8 In the present work, the focus is on a reliable and gap-free joint between steel and aluminum using two different pretreatment approaches for the demonstrator part. The strength properties of the composite castings are of great importance for use in car body structures. Therefore, the hybrid components with coated and structured steel sheet inserts were tested for their tensile strength and dynamic load capacity (Figure 2a,b). On the one hand, coatings of EN AW-7075 alloy were applied to the steel inserts using CGS. In order to investigate the temperature influence on the metallurgical bond between melt and coating, variations of melt and die temperature were carried out. On the other hand, surface structuring was carried out by a cold rolling process to enable a mechanical interlocking. It is assumed, that the size of the surface structure is linearly correlated with the tensile strength. Therefore, a wider structure was tested (Figure 2c). Furthermore, it is unknown whether the orientation of the structure (longitudinal or transversal to the main filling direction) affects the compound strength and load-bearing capacity (Figure 2d). Moreover, the combination of both approaches was tested to possibly enhance the positive effect of the pretreatment techniques (Figure 2e).
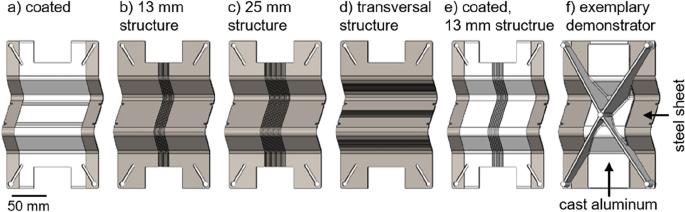
Materials and Methods
Materials
For the use case of the demonstrator part, a strong and ductile base material is required. Since the focus of the study is on the compound strength and not on the overall load-bearing capacity of the component, a 2 mm thick DC04 sheet with favorable formability was chosen for the steel sheet insert. Nevertheless, the intention is to allow the applicability of this approach to different high strength steels as well. The unbent steel sheet inserts had an outer contour of 203.5 mm length and 109 mm width (Figure 3). A high-strength aluminum alloy EN AW-7075 was used for the coating.23 The powder from Eckart TLS GmbH, Bitterfeld-Wolfen, Germany, had a grain fraction of +63 -20 µm. The coating was applied by the CGS process, which provides high density and homogeneity as well as good mechanical properties. The primary aluminum alloy EN AC-4350024 was used for the die casting, which has good strength and low density but low ductility without heat treatment.
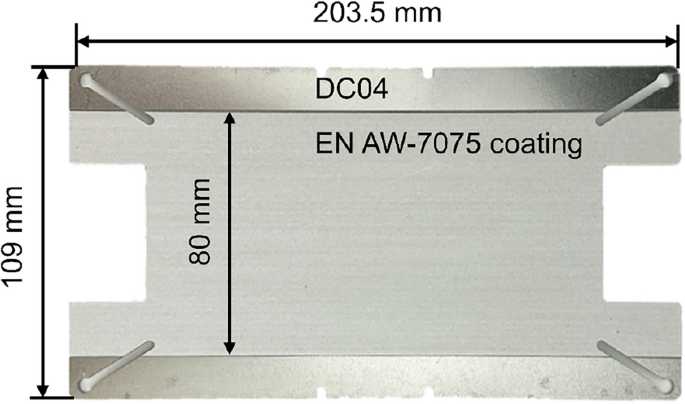
Cold Gas Spraying of Steel Sheets
For preparation, the sheet was sandblasted from both sides with F20 grain corundum at a pressure of p = 6 bar and then cleaned with ethanol. This process is necessary to minimize the influence of oxides and impurities on the surface. At the same time, the surface is roughened, which enables stronger adhesion of the aluminum coating by mechanical clamping into the resulting roughness. The EN AW-7075 coating was then applied to the steel sheet by CGS. This process is characterized by high particle velocities and low temperatures, resulting in coatings with low oxide content and high density. To further reduce the influence of newly forming oxides, the coating was applied shortly after the surface activation. The parameters used for the coating process are shown in Table 1.Table 1 Process Parameters of the Thermal Spray Process CGS
The Kinetics 8000 Cold Spray System from Oerlikon Metco, Pfäffikon, Switzerland was used for the CGS process. A central strip of 80 mm width is coated on both surfaces along the full length of the sheet (Figure 3). For coating, the CGS gun was moved in a meandering pattern over the steel sheets with the aid of a robot in order to apply a homogeneous and flat coating.
Production of Steel Sheet Inserts
The steel sheet insert was produced in four process steps. Uncoated and coated sheets of 160 mm width and 500 mm length were first structured by rolling. The sheets were then waterjet cut into a geometry of 203.5 mm length and 109 mm width. Afterward, the sheets were bent into the insert geometry for die casting. In an intermediate step, the edges of the insert were deburred and the surfaces cleaned in an ultrasonic bath before the inserts were processed in die casting.
Structural Rolling of Steel Sheets
Rolling was carried out on a P3.160 roll forming machine from Dreistern GmbH & Co. KG, Schopfheim, Germany. Profiled rollers with 92.5 mm radius and 13 mm structured width were used for the first pass (Figure 4). The profile is composed of seven ribs and six channels, each 1.0 mm wide and 0.5 mm deep. For wider structures, an intermediate structuring step is performed. These rollers imprinted an additional 6 mm structured width on both sides of the existing structure with the same rib and channel geometry as in the first pass. A flat roller with 93.0 mm radius is used for the flattening pass. The rolling speed is set to 5.8 m/min.
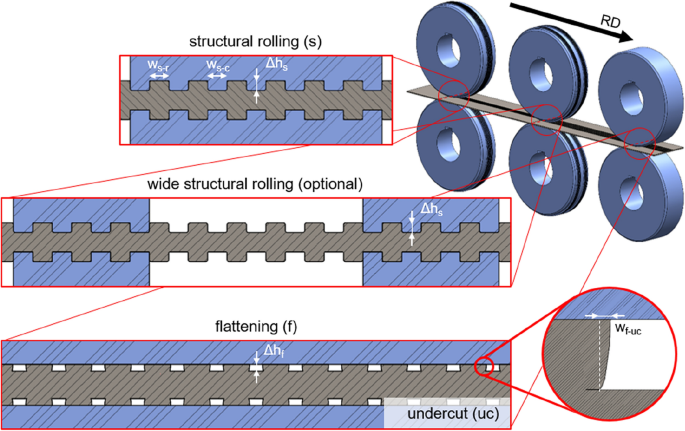
Cross-sectional samples were taken for geometry measurements, which were performed with a Keyence VHX-7000 (Osaka, Japan) digital microscope. In the first pass, channels with a depth of approx. 479 µm (\(\Delta {h}_{s}\)) were imprinted into the sheet surface. The resulting ribs were flattened, resulting in an average channel depth of \(\Delta {h}_{f}=\) 333 µm and an average undercut width of \({w}_{f-uc}=\) 58 µm. However, micrograph preparation (Figure 5a) showed that the very outer channels formed undercuts only on the inner side. Therefore, half a channel width was subtracted on each side, resulting in an effective structure width for the interlocking of 12 mm. These outer channels were formed again in the optional second structuring pass of the wider structure. However, the accuracy of the alignment of the two structural rolling passes was limited by the precision of the mill. This resulted in a transition zone between the first and second structuring pass that showed reduced undercut formation (Figure 5b). For the wider structure, an effective width of 24 mm was assumed for the upcoming compound strength analysis. Flaking of the coating was observed when the coated steel sheet was structured. Therefore, no statistically significant geometric measurements could be obtained. For the upcoming compound strength analysis, an average compound width from 50 mm coating and 12 mm structuring was calculated to be 31 mm (Figure 6).
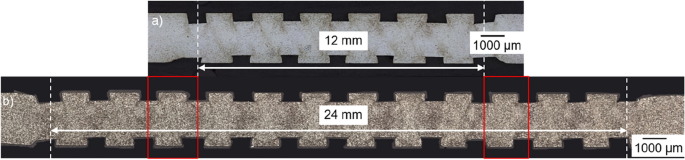
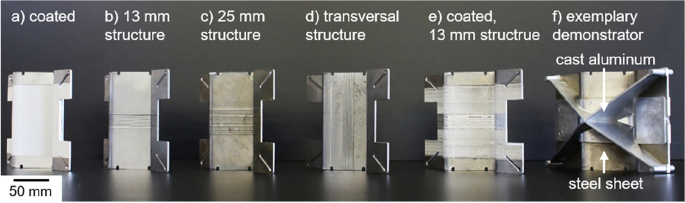
Bending of Steel Sheet Insert
The steel sheet inserts were bent on a Trumpf Trumabend V50 (Ditzingen, Germany) press brake. The geometry required four bending operations with two times of 82° and 133°. A punch with 5.0 mm radius and a die with 16 mm opening were used. After bending, the edges were deburred at the bending curvature.
High-Pressure Die Casting of Demonstrator Part
Casting trials were conducted on a Bühler H630-SC cold chamber high-pressure die casting machine with a nominal locking force of 6,900 kN. The aluminum alloy EN AC 43500, also known as AA 365 with the commercial trade names Silafont-36 and Trimal-05,18 was melted in a resistance furnace and subsequently treated by rotary degassing with argon to a density index of less than 1.0 in the vacuum density test. The chemical composition is given in Table 2.Table 2 Chemical Composition of the Cast Aluminum EN AC 43500
The inserts were placed in the die at room temperature after the release agent had been applied by a conventional high-pressure spraying process (Figure 7). This was followed by the metering process using a preheated ceramic composite ladle attached to a Wollin melt dosing unit, before casting the stiffening structures surrounding the insert for the hybrid parts.
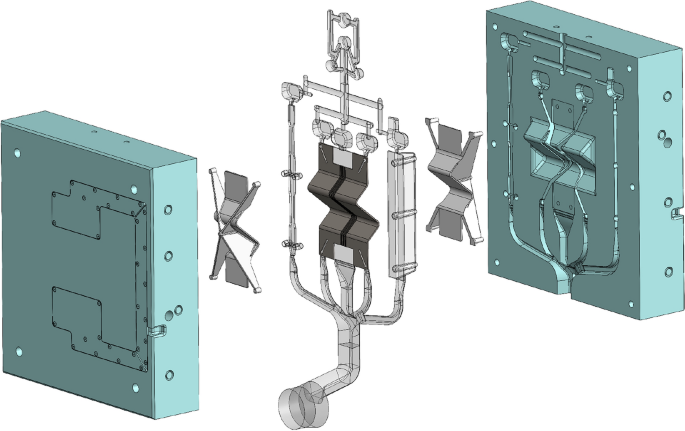
Both, the shot sleeve and the die are thermoregulated with oil as thermoregulation fluid and the temperatures were checked with built-in thermocouples. The parameters of the conducted casting trials are listed in Table 3.Table 3 Boundary Conditions for the Conducted Casting Trials
The Design of Experiments, which provides an ID for each set of parameters tested, is displayed in Table 4. ID 1 is used as a reference with no coating or surface structuring process applied. The experiments used to determine the contribution of the metallurgical bonding of the EN AW-7075 coating at different melt and tool temperatures are ID 2-4. In addition, IDs 5-7 investigate the influence of different orientations and widths of the structures. Finally, ID 8 combines both the surface coating and structuring.Table 4 Design of Experiments to Analyze the Influence of Coating and Structure
Dynamic and Static Testing of the Demonstrator Part
For the dynamic testing, the demonstrator parts were placed in a three-point bending fixture of a 250 kN servo-hydraulic machine from Schenk (Figure 8). The short sides of the specimens were placed on cylindrical bars and the dome was loaded by a punch. A central load of 16.5 kN and an amplitude of 13.5 kN at a frequency of 20 Hz. For the selected parameters, no temperature increase in the sample was observed. The number of load cycles until crack initiation detected by displacement increase is measured.
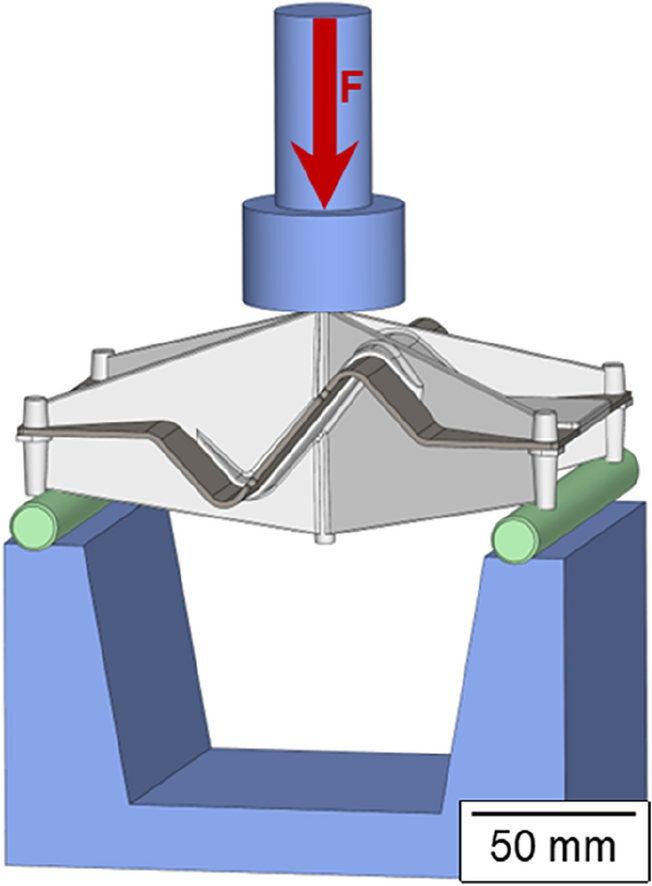
For static testing a sample was extracted from the central section of the demonstrator part (Figure 9) using a horizontal bandsaw with controlled hydraulic feed for minimum force application as previously shown in.25 Since its geometry has a planar bond area, it was possible to test the compound strength explicitly in the normal direction. Shape-matching grips were used to install the sample in a Zwick Z100 tensile testing machine. The specimens were loaded to failure, detected by force drop, and the maximum force was measured.
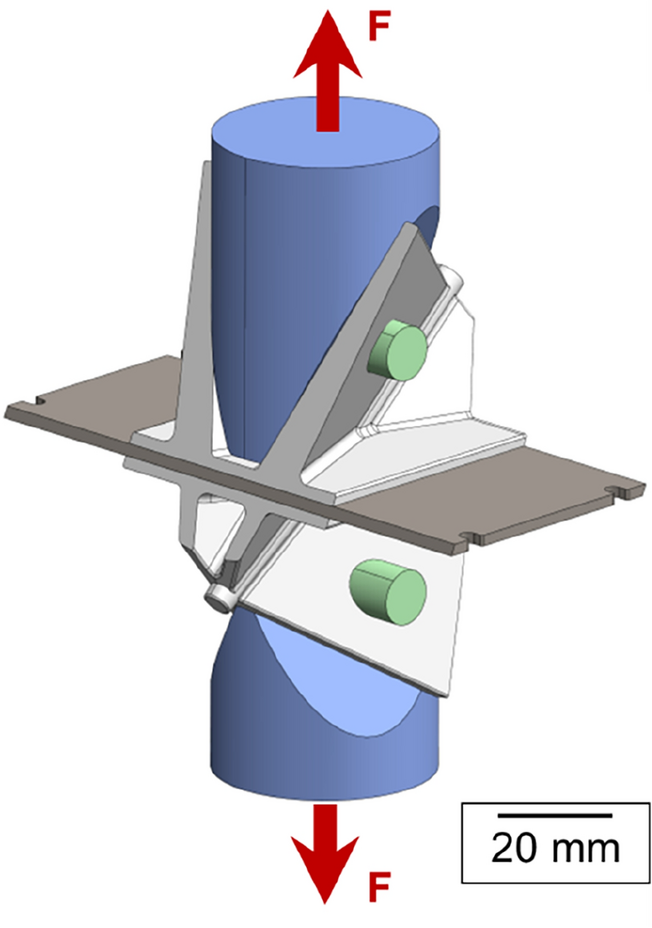
Results and Discussion
The measurement results of dynamic and static testing were evaluated. A comparison between the compound strength for the different insert variants is presented. For the static testing, the compound strength was normalized to the load bearing area of the structure to provide comparable results. For dynamic testing, the entire part was tested, making normalizing to the load bearing area impossible.
Dynamic Testing of the Demonstrator Part
Dynamic testing was performed for demonstrator parts produced at 720 °C melt and 200 °C die temperature (IDs 1, 2 and 5-8). Figure 10 shows the influence of coating, different structuring and a combination of both on the number of load cycles to failure. For each parameter set one standard deviation in positive and negative directions was added as an error bar.
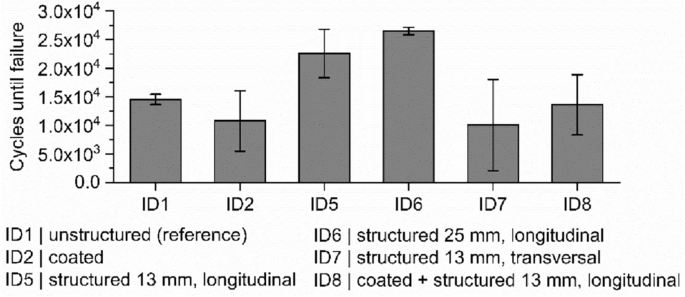
The reference parts achieved an average of 14,550 bending cycles to failure (Figure 10, ID1). It is interesting to note the reduced number of bending cycles for the coated insert (Figure 10, ID2). One hypothesis is an increased notch effect due to the high surface roughness of the cold gas sprayed coating. The 13 mm wide longitudinal structure showed a significant improvement in compound strength (Figure 10, ID5). The number of bending cycles was increased by approximately 55%. A wider structure of 25 mm (Figure 10, ID6) further improved the number of bending cycles, but to a much lesser extent of only another 17%. Compared to the longitudinal structure, the transversal structure (Figure 10, ID7) appears to have a negative effect on the load bearing capacity as it reduces the number of bending cycles by approximately 31%. The cross-sectional preparations in Figures 11 and 12 show, that the filling of the transverse channel structure is reduced. This is most likely caused due to the orthogonal orientation of the channels to the melt flow, which results in significantly worse filling of the structures undercuts (Figure 12a) and additional casting defects (Figure 12b). Another possibility is a different load path of the aluminum due to the different contact areas. The combination of the coating and structure (Figure 10, ID8) does not appear to have a beneficial effect on the compound strength, as it shows a very similar number of load cycles compared to the reference. In the structuring experiments, the coating showed a very small deformability. Flaking of the coating was observed when the undercut structure was created. It is possible that this reduces the interlocking of the compound.
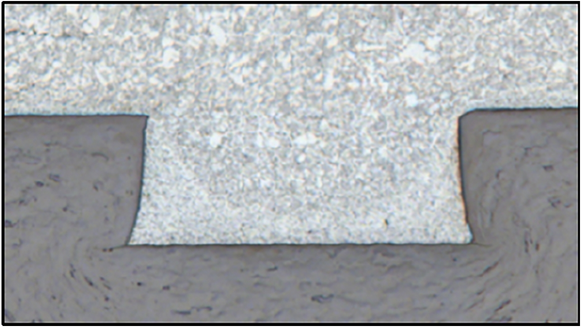
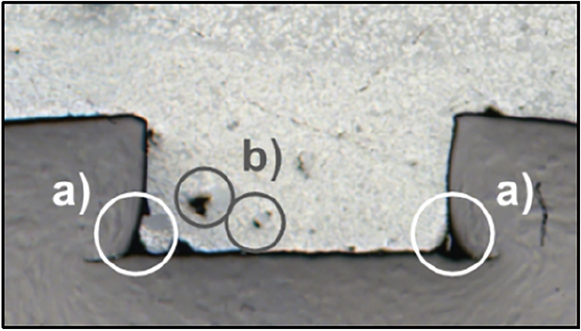
Static Testing of the Demonstrator Part
In order to compare the different insert variants in the static test, the measured mechanical load from the tensile test is converted into an equivalent stress value σeq. After sawing, the sample length was measured for each sample. It should be noted that the reference parts, which were uncoated and unstructured, already failed during cutting, which suggests that the reference stress is σ = 0 MPa. For the coated inserts, a compound width of 50 mm was chosen, as this is the width of the insert which is covered by the cast material. For the structured inserts, the effective structure width was used (Figure 5). For each specimen, an individual compound area was calculated based on the length and compound width. The equivalent stress σeq was then calculated as the ratio of the tensile force measured and the individual compound area.
Casting Temperature for Joining with Coated Surfaces
In a first study, the influence of the melt and cavity temperature was tested on compounds with coated inserts (Figure 13). The results show, that higher temperatures improve the strength of the compound.
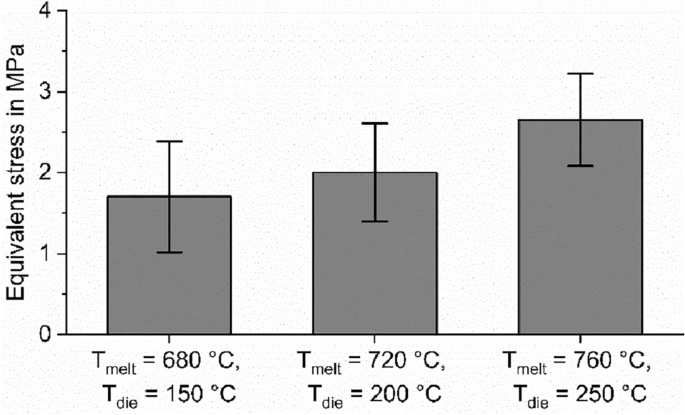
As SEM analysis of the specimens (Figure 14) showed, the higher melt and tool temperatures allowed the melt to penetrate the oxide layer at the coatings surface more easily, which contributed to an improved metallurgical bond. Correspondingly, higher temperatures could lead to an increase in local melting and bonding areas. Similar effects have been observed in16 with an AlSiMn9 alloy. It is clear that, compared to the reference, a metallurgical connection between the steel insert and the die cast aluminum can be achieved, which is capable of transmitting load.
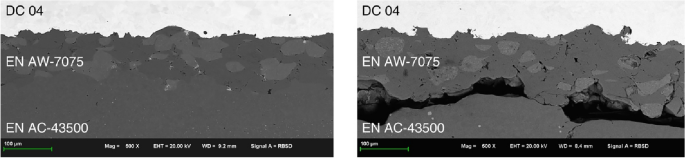
Influences of Channel Structure
For inserts with channel structures, a maximum equivalent stress of 6.9 MPa was obtained for the 13 mm wide longitudinal structure (Figure 15). As indicated by the dynamic tests, the transversal structure results in a reduced strength. Since the joints strength is normalized by the compound area and the load conditions are comparable, the difference in compound strength needs to be a result of the filling conditions. The channels with transverse orientation to the melt flow resulted in significantly worse filling of the structures. The 25 mm longitudinal structure achieves an equivalent stress of 5.1 MPa. This reduction compared to the 13 mm structure was also found in the dynamic tests. This may be due to the transition zone between the first and second structuring passes. Reduced undercut formation was observed in this zone (Figure 5).
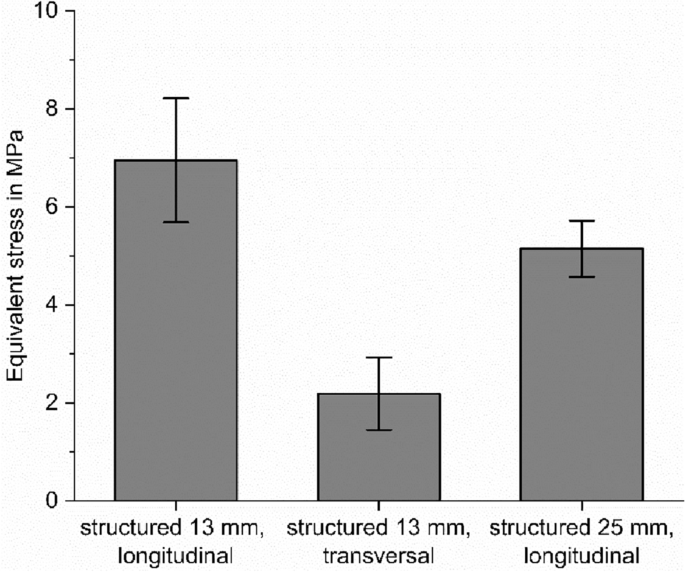
Coating, Structure and Combination in Comparison
Figure 16 shows a comparison of the coated insert and the insert with 13 mm structure in longitudinal direction. Based on the area of the compound, the inserts with channel structures allow higher loads per area of the joint compared to the coated insert. A combination of coating and structuring does not improve of the joint strength.
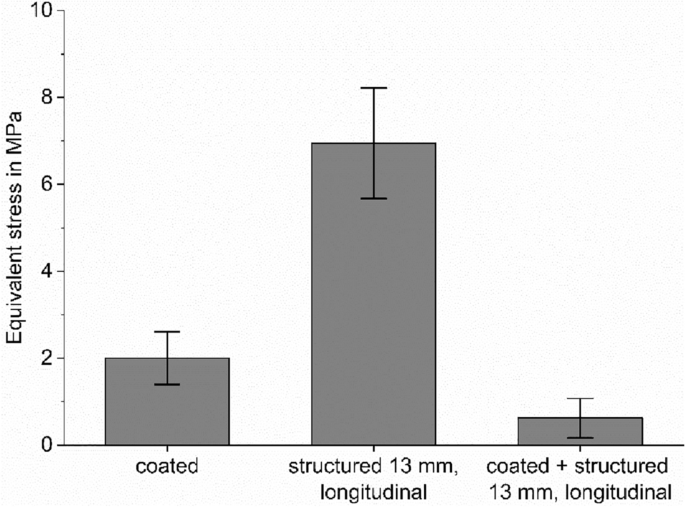
The mechanism leading to lower joint strength in the parts with the combination of coating and structuring is shown in Figure 17. The coating layer c filled the undercut of the steel insert a. Therefore, the cast aluminum b can only interact with the structured and thus deformed coating layer, but cannot form a mechanical interlocking with the steel sheet to transfer the load. The premature failure between the coating and the steel substrate material then results in a failure of the compound.
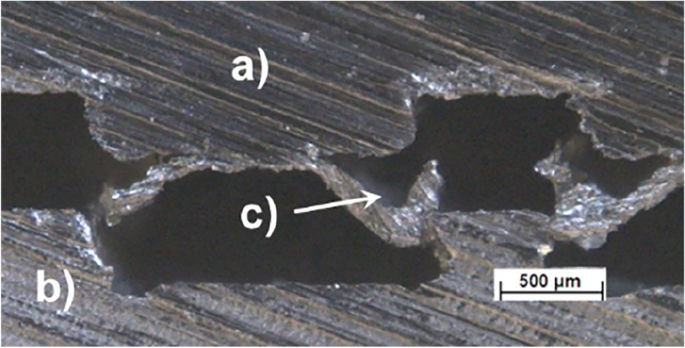
Conclusion and Outlook
In this study, different pretreatment methods for steel sheet inserts for hybrid components made by high-pressure die casting of aluminum were analyzed. On the one hand, cold gas spraying was used to apply an aluminum coating for metallurgical bonding with the die-cast aluminum. On the other hand, undercut surface structures were imprinted into the steel sheet insert for mechanical interlocking with the die cast. The resulting compound strength of the die castings was tested dynamically and statically. The following conclusions were drawn:
- Sheet metal inserts with cold-sprayed coatings can form a mechanically resilient bond with die-cast aluminum in a close to serial production high-pressure die casting process. The cold gas spray process provides micro clamping to the steel sheet and a metallurgical bonding to the aluminum cast.
- Higher temperatures of the melt and die are beneficial for increasing the compound strength between aluminum die-cast and steel when using EN AW-7075 coating.
- Inserts with channel structures running along the melt flow improve the compound strength. Up to 6.9 MPa equivalent stress was measured in static tests.
- Wider structures improve the absolute strength, but the equivalent stress was reduced for the given tests. The reason might be a reduced accuracy of the structure geometry due to the transition between the two structure rolling passes.
- The alignment between the channel structure and the melt flow is crucial in the design of the die casting process, as channels transversal to the melt flow showed significantly reduced strength.
- A combination of coating and structure led to no improvement under the given circumstances.
To further improve the adhesion of the coating to the die cast, mechanical pretreatments such as grinding can be investigated. For wider structured areas, modifications of the rolling process could enhance the accuracy of the structure geometry and lead to constant joint strength. A combined approach between coating and structuring might be achieved by changing the process chain. Structuring before coating would lead to no flaking of the coating. Yet unclear is, how this would affect the joining with the aluminum melt.
References
- Bundesministerium für Wirtschaft und Energie (2021) Leichtbaustrategie für den Industriestandort Deutschland, Bundesministerium für Wirtschaft und Energie (BMWi), Berlin.
- G. Meschut, V. Janzen, T. Olfermann, Innovative and highly productive joining technologies for multi-material lightweight car body structures. J. Mater. Eng. Perform. 23(5), 1515–1523 (2014). https://doi.org/10.1007/s11665-014-0962-3Article CAS Google Scholar
- K. Mori, Y. Abe, A review on mechanical joining of aluminium and high strength steel sheets by plastic deformation. Int. J. Lightweight Mater. Manuf. 1(1), 1–11 (2018). https://doi.org/10.1016/j.ijlmm.2018.02.002Article Google Scholar
- K. Mori, N. Bay, L. Fratini, F. Micari, A.E. Tekkaya, Joining by plastic deformation. CIRP Ann. Manuf. Technol. 62(2), 673–694 (2013). https://doi.org/10.1016/j.cirp.2013.05.004Article Google Scholar
- T. Noguchi, K. Asano, S. Hiratsuka, H. Miyahara, Trends of composite casting technology and joining technology for castings in Japan. Int. J. Cast Met. Res. 21(1–4), 219–225 (2008). https://doi.org/10.1179/136404608X361981Article CAS Google Scholar
- E.E. Feistauer, J.F. dos Santos, S.T. Amancio-Filho, A review on direct assembly of through-the-thickness reinforced metal–polymer composite hybrid structures. Polym. Eng. Sci. 59(4), 661–674 (2019). https://doi.org/10.1002/pen.25022Article CAS Google Scholar
- Y. Ma, G. Zhang, S. Cao, Z. Huo, J. Han, S. Ma, Z. Huang, A review of advances in fabrication methods and assistive technologies of micro-structured surfaces. Processes 11(5), 1337 (2023). https://doi.org/10.3390/pr11051337Article CAS Google Scholar
- D. Joop, Präzisionsbestimmende Faktoren bei der Herstellung blechverstärkter Hybridstrukturen im Druckguss: Grenzflächenanalyse und Verzugsoptimierung (Gießerei-Institut, RWTH Aachen University, Diss., 2018)Google Scholar
- S. Müller, M. Brand, K. Dröder, D. Meiners, Increasing the structural integrity of hybrid plastics-metal parts by an innovative mechanical interlocking effect. Mater. Sci. Forum 825–826, 417–424 (2015). https://doi.org/10.4028/www.scientific.net/MSF.825-826.417Article Google Scholar
- A.L. Buxton, A. Ferhati, R.J. Glen, B.G. Dance, D. Mullen, T. Karayiannis, EB surface engineering for high performance heat exchangers. Proc. FIEBWC. 17, 1 (2009)Google Scholar
- S. Ucsnik, R. Gradinger, A. Becirovic, A. Waldhör, Enhanced performance of steel-aluminium cast nodes through cold metal transfer. Mater. Sci. Forum 765, 736–740 (2013). https://doi.org/10.4028/www.scientific.net/MSF.765.736Article CAS Google Scholar
- H. Abe, J.C. Chung, T. Mori, A. Hosoi, K.M. Jespersen, H. Kawada, The effect of nanospike structures on direct bonding strength properties between aluminum and carbon fiber reinforced thermoplastics. Compos. B Eng. 172, 26–32 (2019). https://doi.org/10.1016/j.compositesb.2019.05.025Article CAS Google Scholar
- X. Fang, J. Gundlach, J.J. Schipperges, X. Jiang, On the steel-aluminum hybrid casting by sand casting. J. Mater. Eng. Perform. 27(12), 6415–6425 (2018). https://doi.org/10.1007/s11665-018-3717-8Article CAS Google Scholar
- Oberschelp, C (2012) Hybride Leichtbaustrukturen für den Karosseriebau Gusswerkstofforientierte Anwendungsuntersuchungen für das Druckgießen. Diss., Hochschulbibliothek Rheinisch-Westfälische Technische Hochschule; Gießerei-Inst, Aachen, pp 294.
- Lao, B (2013) Druckgegossene Metallhybridstrukturen für den Leichtbau-Prozess, Werkstoffe und Gefüge der Metallhybriden. Diss., Hochschulbibliothek der Rheinisch-Westfälischen Technischen Hochschule Aachen, Aachen.
- K. Bobzin, M. Öte, S. Wiesner, L. Gerdt, Analysis of coatings deposited by brazing and cold spraying for casting aluminum/steel hybrids. Proceed. Int. Brazing Solder. Conf. 2018, 229–233 (2018)Google Scholar
- S. Senge, J. Brachmann, G. Hirt, A. Bührig-Polaczek Interlocking multi-material components made of structured steel sheets and high-pressure die cast aluminium, in: ESAFORM. Proceedings of the 20th International ESAFORM Conference on Material Forming, Dublin, Ireland. 26-28, p 190007 (2017)
- K. Bobzin, M. Öte, S. Wiesner, L. Gerdt, S. Senge, G. Hirt, Investigation on the cold rolling and structuring of cold sprayed copper-coated steel sheets. IOP Conf. Ser. Mater. Sci. Eng. 181, 12028 (2017). https://doi.org/10.1088/1757-899X/181/1/012028Article Google Scholar
- K. Bobzin, W. Wietheger, J. Hebing, L. Gerdt, Softening behavior of cold-sprayed aluminum-based coatings AA1200 and AA7075 during annealing. J. Therm. Spray Technol. 30(1–2), 358–370 (2021). https://doi.org/10.1007/s11666-020-01121-7Article CAS Google Scholar
- K. Bobzin, H. Heinemann, M. Erck, J. Körner Thermal sprayed coatings as a solution for joining steel/Al composite castings (accepted). Thermal Spray Bull. (2023)
- S. Senge, J. Brachmann, G. Hirt, A. Bührig-Polaczek Evaluation of interlocking bond strength between structured 1.0338 steel sheets and high pressure die cast AlMg5Si2, in: ESAFORM. Proceedings of the 21st International ESAFORM Conference on Material Forming, Palermo, Italy. 23–25 April 2018, p 40019 (2018)
- S. Senge, L. Gerdt, S. Wiesner, M. Öte, K. Bobzin, G. Hirt Cold rolling of coated steel sheets as pretreatment for hybrid components, in: 3. International Konferenz Hybrid—Materials and Structures, Bremen. 18.-19.04.2019, pp 290–295 (2019).
- E.V. DIN Deutsches Institut für Normung DIN EN 573-3, Aluminium and aluminium alloys—Chemical composition and form of wrought products—Part 3: Chemical composition and form of products, Beuth Verlag GmbH, Berlin (2022)
- E.V. DIN Deutsches Institut für Normung DIN EN 1706:2020-06, Aluminium and aluminium alloys—Castings—Chemical composition and mechanical properties, Beuth Verlag GmbH, Berlin (2021)
- L. Bruckmeier, A. Ringel, U. Vroomen, D. Bailly, A. Bührig-Polaczek, Influence of high-pressure die casting process parameters on the compound strength of hybrid components with undercut sheet metal. Metals 13(10), 1717 (2023). https://doi.org/10.3390/met13101717Article CAS Google Scholar
Acknowledgements
Funded by the Deutsche Forschungsgemeinschaft (DFG, German Research Foundation)—Project-ID 245566034. Special thanks to Niklas Fehlemann, Manuel Henrich and Marc Grümmer for the dynamic fatigue testing at IEHK.
Funding
Open Access funding enabled and organized by Projekt DEAL.
Author information
Authors and Affiliations
- Foundry Institute (GI), RWTH Aachen University, Intzestraße 5, 52072, Aachen, GermanyLukas Bruckmeier & Andreas Bührig-Polaczek
- Institute of Metal Forming (IBF), RWTH Aachen University, Intzestraße 10, 52072, Aachen, GermanyAron Ringel & David Bailly
- Surface Engineering Institute (IOT), RWTH Aachen University, Kackertstraße 15, 52072, Aachen, GermanyMarvin Erck, Kirsten Bobzin & Hendrik Heinemann
Authors
- Lukas BruckmeierView author publicationsYou can also search for this author inPubMedGoogle Scholar
- Aron RingelView author publicationsYou can also search for this author inPubMedGoogle Scholar
- Marvin ErckView author publicationsYou can also search for this author inPubMedGoogle Scholar
- David BaillyView author publicationsYou can also search for this author inPubMedGoogle Scholar
- Kirsten BobzinView author publicationsYou can also search for this author inPubMedGoogle Scholar
- Hendrik HeinemannView author publicationsYou can also search for this author inPubMedGoogle Scholar
- Andreas Bührig-PolaczekView author publicationsYou can also search for this author inPubMedGoogle Scholar
Corresponding author
Additional information
Publisher's Note
Springer Nature remains neutral with regard to jurisdictional claims in published maps and institutional affiliations.
Rights and permissions
Open Access This article is licensed under a Creative Commons Attribution 4.0 International License, which permits use, sharing, adaptation, distribution and reproduction in any medium or format, as long as you give appropriate credit to the original author(s) and the source, provide a link to the Creative Commons licence, and indicate if changes were made. The images or other third party material in this article are included in the article's Creative Commons licence, unless indicated otherwise in a credit line to the material. If material is not included in the article's Creative Commons licence and your intended use is not permitted by statutory regulation or exceeds the permitted use, you will need to obtain permission directly from the copyright holder. To view a copy of this licence, visit http://creativecommons.org/licenses/by/4.0/.
About this article
Cite this article
Bruckmeier, L., Ringel, A., Erck, M. et al. Investigation of the Compound Strength of Hybrid Casting Components with Different Variations of Coated and Undercut Sheet Metal. Inter Metalcast (2024). https://doi.org/10.1007/s40962-024-01359-9
- Received17 August 2023
- Accepted15 April 2024
- Published17 May 2024
- DOIhttps://doi.org/10.1007/s40962-024-01359-9
Keywords
- interlocking
- multi-material components
- cold gas spraying
- structured cold rolling
- high-pressure die casting