Slash Cycle Times and Boost Part Quality: A Deep Dive into Conformal Cooling Channel Technology
This technical brief is based on the academic paper "Recent Advancement in Conformal cooling channels: A review on Design, simulation, and future trends" by Soroush Masoudi, Barun K. Das, Muhammad Aamir, and Majid Tolouei-Rad, a preprint available on SSRN (2024). It is summarized and analyzed for injection molding professionals by the experts at CASTMAN.
![Fig. 1 (a) Injection moulding process and machine, (b), a complex mould structure, (c), some main parts of automobile fabricated by injection moulding process [9].](https://castman.co.kr/wp-content/uploads/image-2601-1024x376.webp)
Keywords
- Primary Keyword: Conformal Cooling Channels (CCC)
- Secondary Keywords: Injection Molding Cooling, Additive Manufacturing Molds, Mold Design Simulation, Cycle Time Reduction, Warpage and Sink Marks, Heat Transfer in Molds, CFD Mold Analysis
Executive Summary
- The Challenge: The cooling stage dominates the injection molding (IM) process, accounting for 50-80% of the total cycle time and heavily influencing part quality. Conventional straight-drilled cooling channels often provide slow, non-uniform cooling for complex parts, leading to defects and inefficiency.
- The Method: This paper provides a comprehensive review of Conformal Cooling Channel (CCC) technology, analyzing various design approaches (spiral, zigzag, porous, nature-inspired), the role of additive manufacturing (AM) in their fabrication, and the critical use of simulation for design optimization.
- The Key Breakthrough: Well-designed CCCs, which follow the contour of the molded part, can dramatically reduce cooling times by up to 70% and overall cycle times by 40-60%. This leads to more uniform temperature distribution, significantly enhancing part quality by minimizing defects like warpage and sink marks.
- The Bottom Line: Conformal cooling, enabled by additive manufacturing and optimized with advanced simulation, represents a transformative shift in mold design, offering a clear path to higher productivity and superior part quality, especially for complex and high-value components.
The Challenge: Why This Research Matters for Injection Molding Professionals
In the high-pressure world of injection molding, time is money. The cooling stage is the single largest bottleneck, often consuming over half of the entire production cycle. For decades, engineers have relied on conventional straight-drilled cooling channels—a cost-effective but often inefficient solution.
As detailed in the paper, these straight-line channels struggle to cool complex, curved parts uniformly. The result? A significant temperature gradient across the part, as the distance between the cooling channel and the mold surface varies (Figure 3a). This non-uniform cooling is a primary cause of common manufacturing headaches, including:
- Warpage and Shrinkage: Uneven cooling causes internal stresses that distort the final part (Figure 4).
- Sink Marks: Hot spots on the part surface, far from a cooling line, can lead to surface depressions.
- Extended Cycle Times: To ensure the entire part is solid enough for ejection, cycle times must be extended, directly impacting throughput and profitability.
This research addresses these fundamental challenges by providing a deep dive into Conformal Cooling Channels (CCCs), an innovative solution that is rapidly gaining prominence, as evidenced by the surge in related publications (Figure 5).
The Approach: Unpacking the Methodology
This paper conducts a systematic and comprehensive review of the state-of-the-art in conformal cooling. The authors analyze the full lifecycle of CCC development, from initial concept to final application, focusing on three core areas:
- Design and Classification: The study categorizes and compares various types of CCCs, including spiral, zigzag, porous, and nature-based designs (Figure 13). It examines the underlying design principles, constraints (Figure 11), and the specific advantages each layout offers for different part geometries.
- Additive Manufacturing (AM): The paper highlights that the fabrication of these complex, internal channel geometries is made possible by advancements in metal 3D printing, such as Powder Bed Fusion (PBF) and Direct Energy Deposition (DED). AM is the key enabling technology that unlocks the potential of CCCs.
- Simulation and Modeling: The authors emphasize the crucial role of Computer-Aided Engineering (CAE) and Computational Fluid Dynamics (CFD) in the design process. By using software like Mouldflow, ANSYS, and COMSOL, engineers can simulate heat transfer, fluid flow, and thermal stress to optimize channel layout, diameter, and performance before any metal is cut or printed (Figure 30, 31).
The Breakthrough: Key Findings & Data
The paper synthesizes a vast body of research to present a clear picture of the benefits and nuances of CCC technology.
- Superior Performance Over Conventional Methods: The fundamental advantage of CCCs is their ability to maintain a constant distance from the mold cavity surface (Figure 3b). This "conformal" nature ensures uniform and efficient heat extraction. The impact is dramatic, with studies showing cooling time reductions of up to 70% and cycle time reductions of 40-60% [33-36].
- Diverse Design Strategies for Different Applications: There is no one-size-fits-all solution for CCCs. The optimal design depends heavily on the part's geometry. The paper reviews the primary strategies:
- Spiral Channels: Ideal for round or dome-shaped parts, offering smooth coolant flow and low pressure drop.
- Zigzag Channels: A compact design suitable for covering intricate surfaces, though sharp turns can increase pressure drop.
- Porous and Interconnected Channels: Advanced structures, like lattices or scaffolds (Figure 17), that offer the most thorough cooling for highly complex geometries by acting like a sponge for heat. A summary of the pros and cons of each design is presented in Table 1.
- The Cutting Edge: Biomimicry and Topology Optimization: The review explores next-generation design concepts. Nature-inspired designs mimic efficient biological structures like plant roots or blood vessels to create highly effective, low-pressure-drop cooling networks (Figure 21, 22). Furthermore, topology optimization algorithms can be used to computationally generate the most efficient channel layout based on thermal loads, creating truly optimized, often organic-looking designs (Figure 20).
- Simulation is Essential for Optimization: The paper repeatedly demonstrates that simulation is not optional but essential for successful CCC implementation. For example, Figure 30 shows a simulation comparing a straight-hole design with a CCC design. The hot spots present in the conventional tool are eliminated in the conformal design, and the maximum surface temperature drops from 149.2 °C to 108.8 °C. Mesh independence studies (Figure 28) are also critical to ensure simulation accuracy without excessive computational cost.
Practical Implications for Your Operations
The findings presented in this paper have direct, actionable implications for improving real-world manufacturing environments.
- For Process Engineers: The documented cycle time reductions of 40-60% [33-36] translate directly to a significant increase in machine throughput and overall plant productivity. This allows for more parts to be produced in the same amount of time, lowering the cost per part.
- For Quality Control: The ability of CCCs to deliver uniform cooling is a game-changer for part quality. The research shows a direct link between conformal cooling and the reduction of defects like warpage, sink marks, and residual stress (Figure 4, 16). This leads to higher yields, lower scrap rates, and more dimensionally stable parts.
- For Die and Mold Designers: This technology, enabled by additive manufacturing, breaks the constraints of traditional drilling. Designers can now create cooling solutions for highly complex parts that were previously considered impossible to cool effectively. By applying the design principles outlined in the paper (e.g., channel diameter and spacing rules in Table 3), designers can engineer molds for maximum performance and part quality from the outset.
Paper Details
Recent Advancement in Conformal cooling channels: A review on Design, simulation, and future trends
1. Overview:
- Title: Recent Advancement in Conformal cooling channels: A review on Design, simulation, and future trends
- Author: Soroush Masoudi, Barun K. Das, Muhammad Aamir, Majid Tolouei-Rad
- Year of publication: 2024 (Preprint)
- Journal/academic society of publication: SSRN Electronic Journal
- Keywords: Injection moulding; Conformal cooling channel; Mould design; Heat transfer; Cooling rate; Additive manufacturing; Simulation.
2. Abstract:
The cooling stage of a moulded part plays a crucial role in the injection moulding (IM) process, accounting for 50 to 80% of total cycle time, and significantly impacting the quality of moulded parts. During the last decade, the advancement of different additive manufacturing (AM) processes, especially metal 3D printing, has facilitated the production of mould parts, such as cores and cavities, with complex-shaped internal conformal cooling channels (CCCs). These innovative cooling systems exhibit significant potential to replace current straight-drilled cooling design, whereby they offer more efficient and uniform cooling performance by facilitating more effective heat transfer, considerably enhancing production quality and efficiency. Despite increasing attention being given to the design and manufacturing of CCC systems, there is still a lack of systematic and comprehensive classification, comparison and evaluation methodologies. This paper aims to review various types of conformal cooling channels, such as spiral, zigzag and nature-based designs, among others, and to provide an overview of advancements in design, process modeling and simulation of this new cooling technology. Previous studies have indicated that conventional straight-drilled cooling channels are likely to be replaced by CCCs, especially for complex and sensitive parts, due to their superior performance in reducing cycle times and enhancing product quality. The present study delves deeply into the various challenges that arise when developing conformal cooling channels. These issues range from optimizing complex geometry to improving thermal performance through modelling. However, these challenges also present opportunities for innovation and advancement in mould design and manufacturing.
3. Introduction:
The introduction establishes injection molding (IM) as a primary method for fabricating a wide variety of plastic parts across industries like automotive, medical, and consumer goods. It highlights that the cooling stage is the most critical and time-consuming part of the IM cycle, constituting 50-80% of the total time and profoundly impacting the final part's quality, surface appearance, and dimensional accuracy. The paper points out the limitations of conventional cooling channels, which are typically straight-drilled due to manufacturing constraints. These straight channels lead to non-uniform cooling, especially for curved or complex parts, resulting in longer cycle times, internal stresses, warpage, and sink marks. This sets the stage for introducing conformal cooling channels (CCCs) as a superior alternative that addresses these issues by maintaining a consistent distance from the mold cavity, thereby ensuring uniform and efficient heat dissipation.
4. Summary of the study:
Background of the research topic:
The core problem is the inefficiency of traditional cooling methods in injection molding. The cooling phase dictates both production speed and final product quality. Conventional straight-drilled channels are simple and cheap to make but are thermally inefficient for anything but the simplest part geometries. This inefficiency leads to non-uniform temperature profiles, causing defects and long cycle times. The advent of additive manufacturing (AM) has enabled the fabrication of molds with highly complex internal geometries, making conformal cooling channels a viable and powerful solution.
Status of previous research:
The paper acknowledges numerous previous studies on CCCs. Researchers have explored various design optimizations, the use of AM for fabrication, and applications in different tooling scenarios. However, the paper identifies a gap: a lack of a systematic, comprehensive review that classifies the different types of CCCs, compares their design and simulation methodologies, and outlines future trends in a structured manner. Existing reviews have touched upon aspects of CCCs, but this paper aims to provide a more holistic and in-depth analysis, particularly focusing on design and simulation advancements.
Purpose of the study:
The primary purpose of this paper is to provide a comprehensive and systematic review of recent advancements in conformal cooling channels. It aims to:
- Classify and compare various types of CCCs, including spiral, zigzag, porous, and nature-based designs.
- Provide an overview of the progress in the design, process modeling, and simulation of this technology.
- Delve into the challenges and opportunities associated with developing CCCs, from geometry optimization to thermal performance modeling.
- Synthesize key findings, identify promising future trends, and chart a path for further research and development in the field.
Core study:
The core of the study is a detailed literature review and synthesis of knowledge across several key domains of conformal cooling. It begins with the analytical and mathematical modeling of heat transfer in molds. The main body of the work is a thorough classification and discussion of CCC layouts and designs, broken down into:
- Basic Design Principles: Discusses constraints like pressure drop, manufacturing capability, and part geometry (Figure 11).
- Zigzag, Spiral, and Porous Channels: Details the structure, advantages, and disadvantages of each primary design type (Figure 13, Table 1).
- Natural-Based and Biomimetic Designs: Explores cutting-edge designs inspired by nature (Figure 21, 22).
- Automatic Design: Reviews methods for automating the generation of CCC layouts to save time and optimize shape (Figure 23, 24).
- Channel Cross-Section: Analyzes the impact of different channel shapes (circular, rectangular, fluted) on cooling performance (Figure 25). Finally, it reviews the use of process modeling and simulation (FEM, CFD) to analyze and validate CCC designs, providing numerous examples of simulation results that compare conventional and conformal systems.
5. Research Methodology
Research Design:
The research is designed as a comprehensive literature review. The authors systematically gather, classify, and analyze existing academic and technical papers related to conformal cooling channels in injection molding. The structure follows a logical progression from fundamental principles to advanced applications and future outlooks.
Data Collection and Analysis Methods:
The primary data source is the SCOPUS database, supplemented by other academic sources. The authors conducted a keyword search for "conformal AND cooling" for literature from 1990 to 2023, identifying 742 relevant documents for analysis (Figure 5). The analysis method involves synthesizing the findings from these papers to identify common themes, classify different design approaches, compare performance metrics reported in various studies, and identify research gaps and future trends.
Research Topics and Scope:
The scope of the review is broad, covering the entire lifecycle of CCC development for injection molding. The key research topics include:
- Analytical and mathematical modeling of heat transfer in molds.
- Classification and analysis of CCC designs: spiral, zigzag, porous, interconnected, and nature-based.
- The role of Additive Manufacturing (AM) in fabricating CCCs.
- Principles of automated CCC design.
- The impact of channel cross-section on performance.
- The application of simulation tools (FEM, CFD) for design validation and optimization.
- Future trends, including AI in design, biomimicry, and new coolant technologies.
6. Key Results:
Key Results:
The review consolidates several key findings from the literature:
- Significant Performance Gains: CCCs consistently outperform conventional straight-drilled channels, reducing cooling time by up to 70% and cycle time by 40-60%, while also improving part quality by ensuring uniform temperature distribution [33-36].
- Design Diversity: There is no single best CCC design. The choice between spiral, zigzag, or porous structures depends heavily on the specific geometry of the part being molded. Table 1 provides a clear summary of the advantages and drawbacks of each type.
- Enabling Role of Additive Manufacturing: The practical implementation of complex CCCs is fundamentally dependent on metal AM technologies, which can create intricate internal channels that are impossible to machine conventionally [37-44].
- Critical Importance of Simulation: CAE, FEM, and CFD simulations are essential tools for optimizing CCC designs. They allow for the analysis of thermal performance, coolant flow, pressure drop, and mechanical stress, enabling designers to validate and refine the mold before costly manufacturing begins [135, 136].
- Emerging Advanced Designs: The frontier of CCC design involves topology optimization and biomimicry. These methods can generate highly efficient, non-intuitive cooling layouts that further enhance performance, particularly for very complex parts or hot spots [94, 103].
- Cross-Sectional Shape Matters: Moving beyond simple circular channels to profiled shapes (e.g., rectangular, fluted) can further increase heat transfer surface area and improve cooling efficiency, though this must be balanced with manufacturability and pressure drop considerations [122, 124].
Figure Name List:
![Fig. 2 (a) A typical injection moulding cycle [12], (b) temperature variation in one cycle time [13], (c) factors that have influence in the moulded product quality (surface appearance and dimensional accuracy) [12].](https://castman.co.kr/wp-content/uploads/image-2602-1024x589.webp)
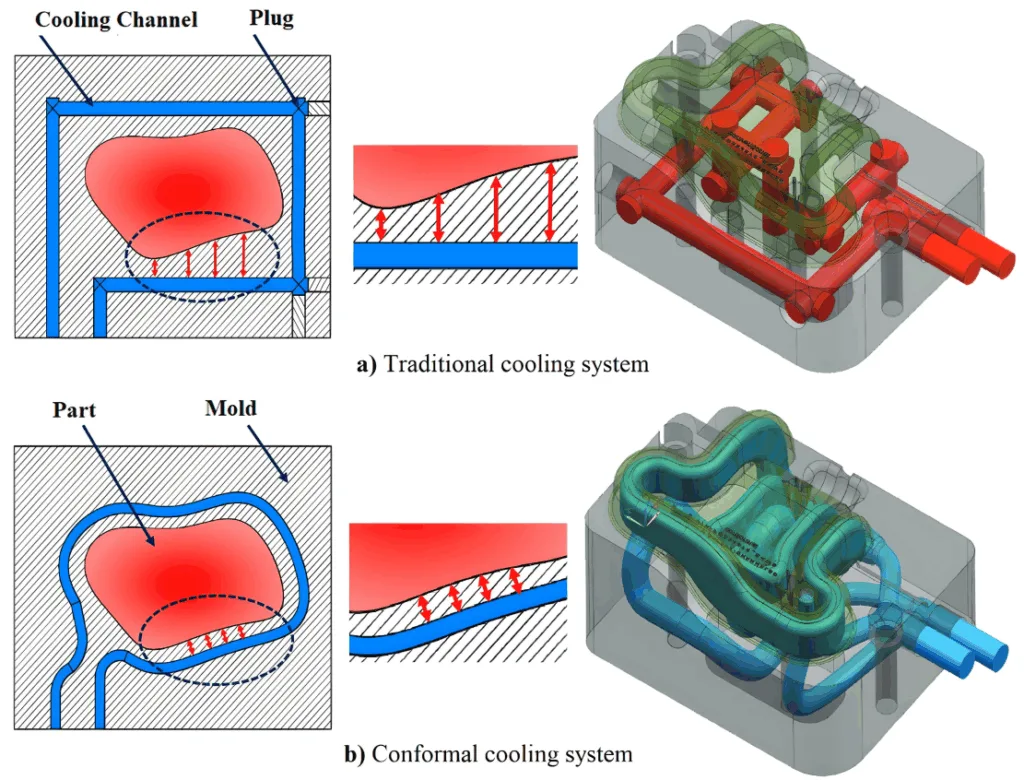
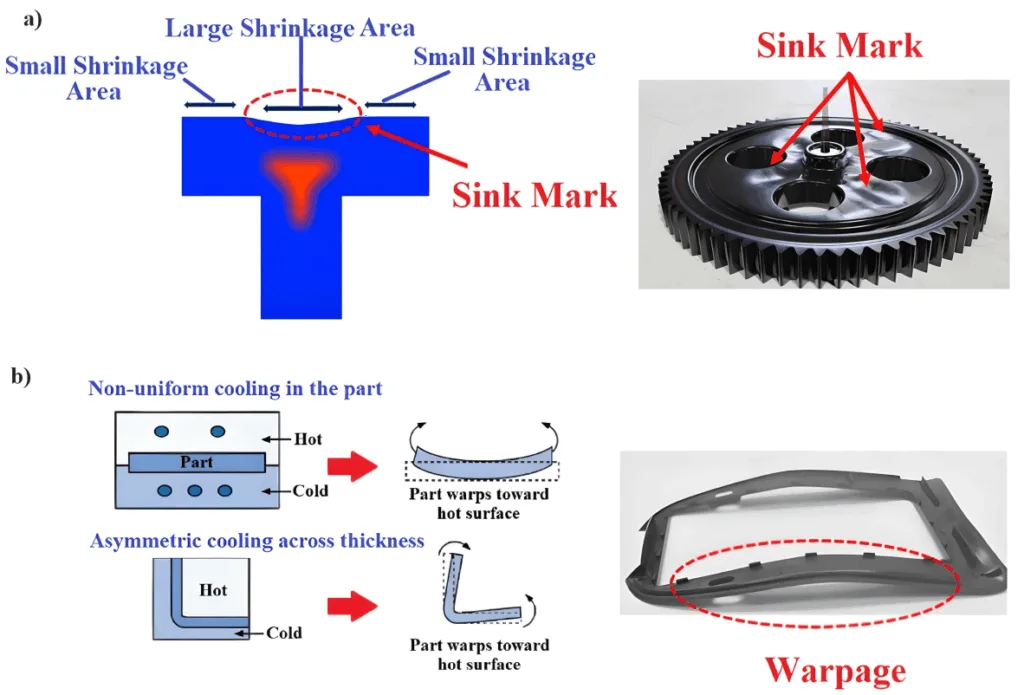
- Fig. 1 (a) Injection moulding process and machine, (b), a complex mould structure, (c), some main parts of automobile fabricated by injection moulding process [9].
- Fig. 2 (a) A typical injection moulding cycle [12], (b) temperature variation in one cycle time [13], (c) factors that have influence in the moulded product quality (surface appearance and dimensional accuracy) [12].
- Fig. 3 Schematic design of (a) traditional cooling system and (b) conformal cooling channel.
- Fig. 4 Sample and creation mechanism of (a) sink mark and, (b) warpage defects in moulded parts.
- Fig. 5 Number of publications per year focusing on “conformal cooling", from SCOPUS database
- Fig. 6 Effects of heat transfer during injection moulding.
- Fig 7. Heat transfer in the mould [49].
- Fig. 8 Simplified presentation of heat fluxes in IM [48].
- Fig.9 (a) A conventional straight drilled cooling system and (b) hotspot area in the moulded part [13].
- Fig. 10 Different types of cooling system, (a) baffle, (b) bubbler, (c) conformal bubbler [56] and (d) metal inserts.
- Fig. 11 Constraints in the design of CCCs [58].
- Fig. 12 (a) Cooling channel with variable diameter [33], (b) conformal cooling design with variable diameter [61], (c) conformal cooling design with varying cross-sections [62].
- Fig. 13 Three main designs classification of conformal cooling based on cooling lines passage: (a) zigzag [64, 65], (b) spiral [66], and (c) porous [67].
- Fig. 14 (a) Traditional cooling and zigzag conformal cooling channels[72]; (b) Different zigzag conformal cooling designs [68, 69, 73, 78-80].
- Fig. 15 (a) Using boundary-distance-map (BDM) for generating spiral curves [75], (b) conformal loops generation by using generic approach [77].
- Fig. 16 (a) FEM prediction of temperature in part with conventional cooling (b) and spiral conformal cooling, (c) deflection and warpage comparison in conventional and conformal cooling [66];(d) spiral CCC in cone and cavity of mould and (e) Temperature variations during the filling of the part [81].
- Fig. 17 Cross-sectional images of the cavity mould half with scaffold cooling system layout in (a) XZ and (b) YZ plane cuts [85] and (c) comparison of porous and normal circular channel cooling performance [86].
- Fig. 18 CVD method to generate interconnected conformal cooling channels in comparison to conventional cooling channels [67].
- Fig. 19. (a) self-supporting spiral channel with lattice structure [89]; (b)-1 various TPMS shapes used with different volume fraction, (b)-2 TPMS conformal cooling, (b)-3 XCT images of the additively manufactured TPMS core[92]; design configuration of the test setup: (c)-1 solid insert and cooling channel, (c)-2 cellular porous insert designed for air circulation[93].
- Fig. 20 (a) Principle of thermal-load-based topology optimization as well as temperature and pressure in simple and optimized parts [94]; (b) Design procedure of the conformal cooling system by topology optimization [95]; (c) Mouldflow analysed the half sphere model for average temperature: initial design, ideal design, and smoothed design [98].
- Fig. 21 Illustration of the methodology for designing biomimetic conformal cooling channels [103].
- Fig. 22 (a) Lotus root structure and Schematic diagram of connection strategy [104]; (b) Honeycomb inspired conformal cooling channels [105]; (c) Vascularize inspired conformal cooling channels [106].
- Fig. 23 Main 3 steps in the design of CCCs [110].
- Fig. 24 Automatic conformal cooling channel generation in two sample parts [111].
- Fig. 25 (a) Cooling channel solid mesh with different number of fins [124]; (b) temperature contours for circular and non-circular cooling channels [126].
- Fig. 26 (a) Moulding tools with a circular CCC and profiled CCC and comparison of profiled CCC and circular cooling time from simulation results [128], (b) circular and profiled CCCs and their cooling time [129].
- Fig. 27 (a) Conformal design, temperature variation in (b) conventional and (c) conformal cooling, (d) [148]; conformal design, positional error distributions in (e) conventional and (f) conformal cooling [149].
- Fig. 28 (a) mesh model of part and cooling system, (b) number of meshes as a function of cooling time [128]; (c) analysis of the relative error and computing time for models with different mesh base size [152].
- Fig. 29 flow velocity as a function of distance for three different cooling systems: (a) conventional cooling system, (b) milled multi-part cooling system, (c) conformal cooling system[65].
- Fig. 30 (a) Temperature distribution in traditional and CCC design and (b) node temperature-time curve in conformal and straight cooling [152].
- Fig. 31 Temperature and pressure distribution and velocity volume rendering in the conventional and conformal cooling channels[156].
- Fig. 33 (a) Conventional and CCC designs, (b) time to reach ejection temperature, (b) hot spot area and temperature profile distributions for both designs[157].
7. Conclusion:
The paper concludes that Conformal Cooling Channels are a highly effective technology for enhancing the injection molding process. They provide consistent temperature and cooling rates, leading to significant reductions in cycle time and improvements in part quality, especially for complex shapes where conventional cooling fails. The choice of CCC design (e.g., zigzag, spiral, porous) depends on part geometry, and a balance must be struck between thermal performance, manufacturability, and cost. The authors identify several key areas for future research:
- Artificial Intelligence: Using AI for the automated design and optimization of novel CCC layouts.
- Biomimicry: Further exploration of natural-based design principles to create more efficient cooling networks.
- Advanced Simulation: Combining FEM and CFD for more comprehensive thermal-fluid and mechanical analysis of the entire mold.
- New Coolants: Developing novel coolant formulations (e.g., nano coolants) specifically designed for the demands of conformal cooling. In essence, while challenges in design and optimization remain, they also present significant opportunities for innovation. Future work should focus on developing AM-specific design guidelines and intelligent automation to unlock the full potential of this transformative technology.
8. References:
- Fu, H., et al., Overview of injection molding technology for processing polymers and their composites. ES Materials & Manufacturing, 2020. 8(4): p. 3-23.
- Zhao, N.-Y., et al., Measurement techniques in injection molding: A comprehensive review of machine status detection, molten resin flow state characterization, and component quality adjustment. Measurement, 2024: p. 114163. ... [References 3 through 163 would be listed here exactly as in the paper] ...
- Kanbur, B.B., et al., Thermal and mechanical simulations of the lattice structures in the conformal cooling cavities for 3D printed injection molds. Materials Today: Proceedings, 2020. 28: p. 379-383.
- Clark, R., et al., Towards sustainable injection moulding using 3D printed conformal cooling channels: a comparative simulation study. Progress in Additive Manufacturing, 2024: p. 1-12.
- more ....
Conclusion & Next Steps
This research provides a valuable roadmap for enhancing cooling performance in injection molding. The findings offer a clear, data-driven path toward improving quality, reducing defects, and optimizing production through the strategic implementation of conformal cooling channels.
STI C&D is committed to applying cutting-edge industry research to solve our customers’ most challenging technical problems. If the challenges discussed in this paper align with your goals, please contact our engineering team to discuss how we can help you apply these advanced principles to your mold design and simulation projects.
Expert Q&A:
- Q1: How much can conformal cooling channels (CCCs) really reduce the cooling time in injection molding?
- A: According to the paper "Recent Advancement in Conformal cooling channels," well-designed CCCs have demonstrated significant improvements. The review states that they "have been shown to reduce cooling times by up to 70 % and cycle times by 40-60% [33-36]," making it one of the most impactful strategies for increasing productivity.
- Q2: What is the main difference between a conventional cooling channel and a conformal one?
- A: The primary difference lies in the geometry of the channel path, as illustrated in Figure 3 of the paper. Conventional channels are straight-drilled, resulting in a variable distance from the curved cavity surface. In contrast, conformal channels are designed to follow the shape of the part, maintaining a consistent, optimal distance from the surface, which ensures more uniform and efficient heat removal.
- Q3: What are the main types of CCC designs and how do I choose one?
- A: The paper classifies three main designs in Figure 13: zigzag, spiral, and interconnected porous. The choice depends on your part's geometry. As summarized in Table 1, spiral channels are great for round parts due to smooth flow; zigzag channels are compact for intricate surfaces but may have higher pressure drop; and porous structures offer the most thorough cooling for highly complex shapes.
- Q4: What manufacturing technology is required to make these complex conformal cooling channels?
- A: The paper "Recent Advancement in Conformal cooling channels" clearly states that additive manufacturing (AM) is the key enabling technology. Processes such as powder bed fusion (PBF), direct energy deposition (DED), and binder jetting (BJ) are essential for producing mold inserts with the complex internal, free-form shapes that define conformal cooling channels [37-44].
- Q5: Do different CCC cross-sections, like circular versus rectangular, affect cooling performance?
- A: Yes, they do. While circular channels are common, the paper notes that other shapes are being explored to enhance performance. For instance, "rectangular channels are less rigid than circular ones, but because of their higher effective cooling surface area for the same cross-sectional area, rectangular channels cool more efficiently and uniformly [86]." Figure 25 also shows simulations of channels with internal fins to increase surface area.
- Q6: What are the main advantages and disadvantages of a spiral CCC design?
- A: Based on the summary in Table 1 of the paper, the main advantages of a spiral design are its "smooth and continuous flow path, minimizing pressure drop and consistent coolant flow rates," and its ability to provide "very good temperature control." The primary disadvantages are that it "may be challenging to implement in moulds with complex geometries" and it "may cause longer lengths of cooling channel."
- Q7: How is simulation used in the development of CCCs?
- A: Simulation is a critical step for optimization. The paper explains that software like ANSYS, Mouldflow, and COMSOL is used for comprehensive analysis before manufacturing. This includes thermal analysis to predict surface temperature, cooling time, and warpage, as well as fluid dynamics (CFD) to analyze coolant flow and pressure drop. Figure 30 provides a clear example, showing a simulation that predicts and compares the temperature distribution between a traditional and a conformal design.
- Q8: What are some of the most exciting future trends in conformal cooling?
- A: The paper's conclusion highlights several future directions. Among the most promising are the integration of natural-based or biomimetic design principles (inspired by structures like blood vessels, as seen in Figure 21), the use of artificial intelligence and topology optimization for automated and highly efficient channel design (Figure 20), and the development of new, high-performance coolants like nano coolants.
Copyright
- This material is an analysis of the paper "Recent Advancement in Conformal cooling channels: A review on Design, simulation, and future trends" by Soroush Masoudi et al.
- Source of the paper: https://ssrn.com/abstract=4931316
- This material is for informational purposes only. Unauthorized commercial use is prohibited.
- Copyright © 2025 STI C&D. All rights reserved.